Modular Construction Timeline
Building a Better World With Modular Construction
Since the 1970s, Fluor has been one of the first engineering and construction companies to realize the benefits to clients of offsite fabrication and modular construction. Our global modular construction experience delivers lower project risk, compressed schedules and greater cost certainty.
Fluor's innovations in modular construction continue to lead the industry and raise the bar for projects to come.
1970s
Fluor begins using a modular approach to construction.
1973
Suez Oil Company offshore module installed in the Gulf of Suez
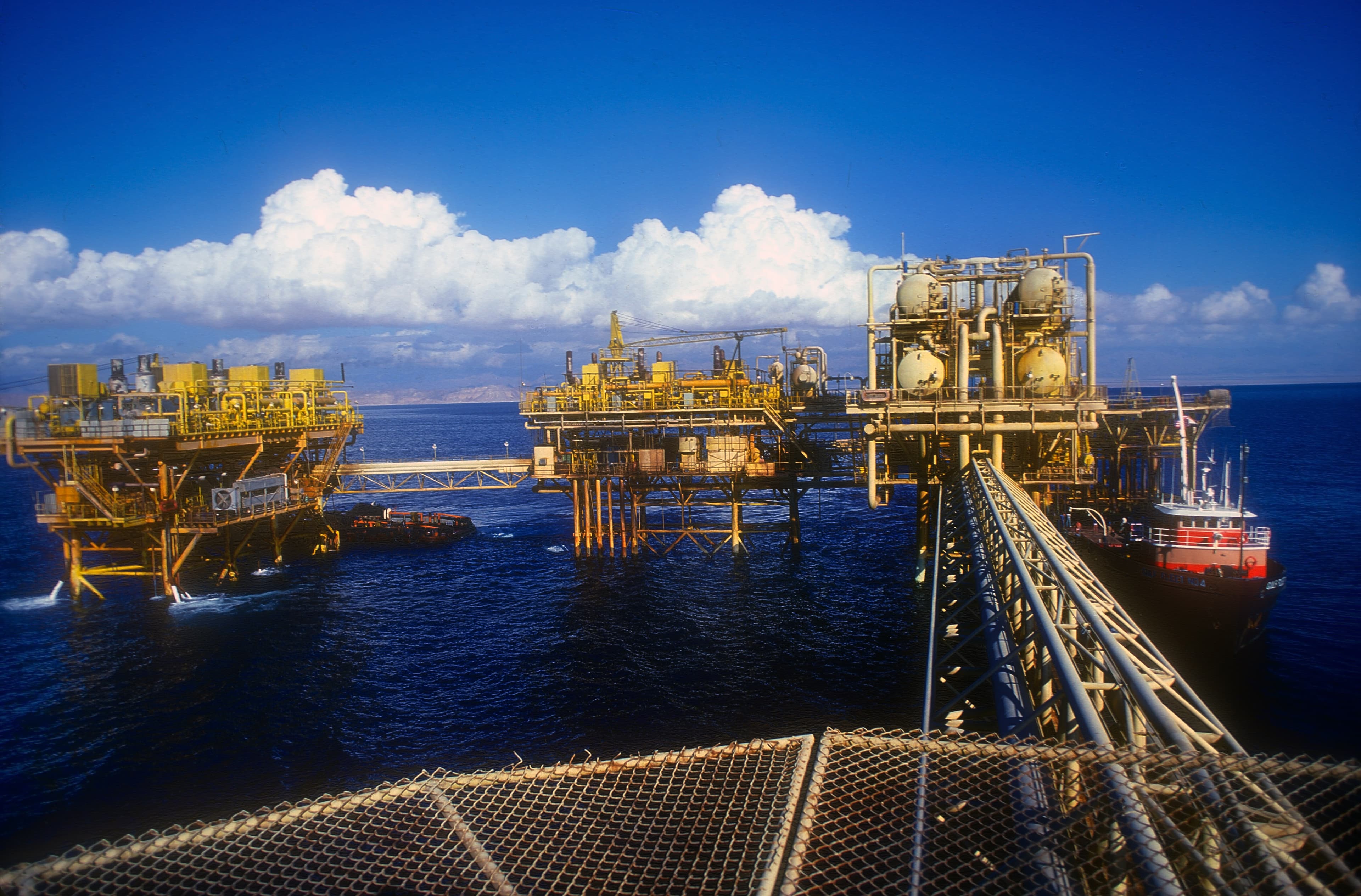
1973: Suez Oil Company offshore module installed in the Gulf of Suez
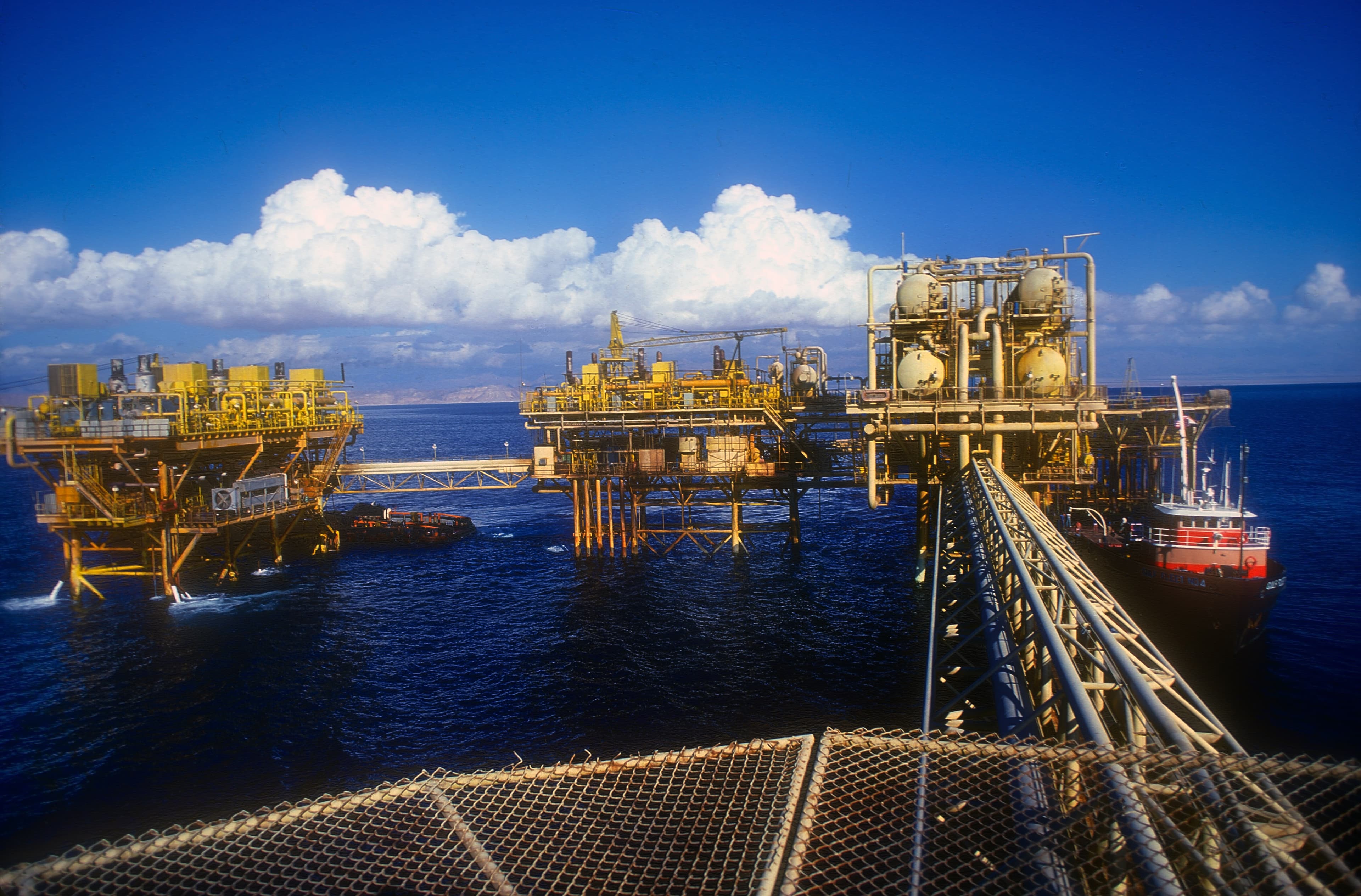
The Suez Oil Ras Fanar Field Development project was located on the west side of the Gulf of Suez and included two well-head platforms in approximately 100 feet of water, subsea pipelines, an onshore power plant, crude sweetening facilities, and export facilities. Offshore facilities, by necessity, have been constructed using modular construction. Many of the techniques developed and refined on offshore construction have been adapted to offsite construction of onshore facilities.
1974
Prefabricated single lift modules assembled at ARCO Pertamina's Ardjuna Offshore NGL Recovery Plant
&w=3840&q=75)
1974: Prefabricated single lift modules assembled at ARCO Pertamina's Ardjuna Offshore NGL Recovery Plant
&w=3840&q=75)
A plant of this size would normally require five acres on land, yet Fluor engineered it to function on only one acre of platform deck space. Fluor used modular construction of 21 prefabricated single lift modules for total plant assembly.
The modules included a refrigeration unit, five piperack modules, six air cooler modules, and a dehydrator. The outlying gas compressor stations provide 40,000 hp of natural gas compression. The plant’s turbine generators and compressors use methane fuel derived from natural gas on the job site.
1977
Valdez Crude Oil Export Terminal floating dock built as a single module
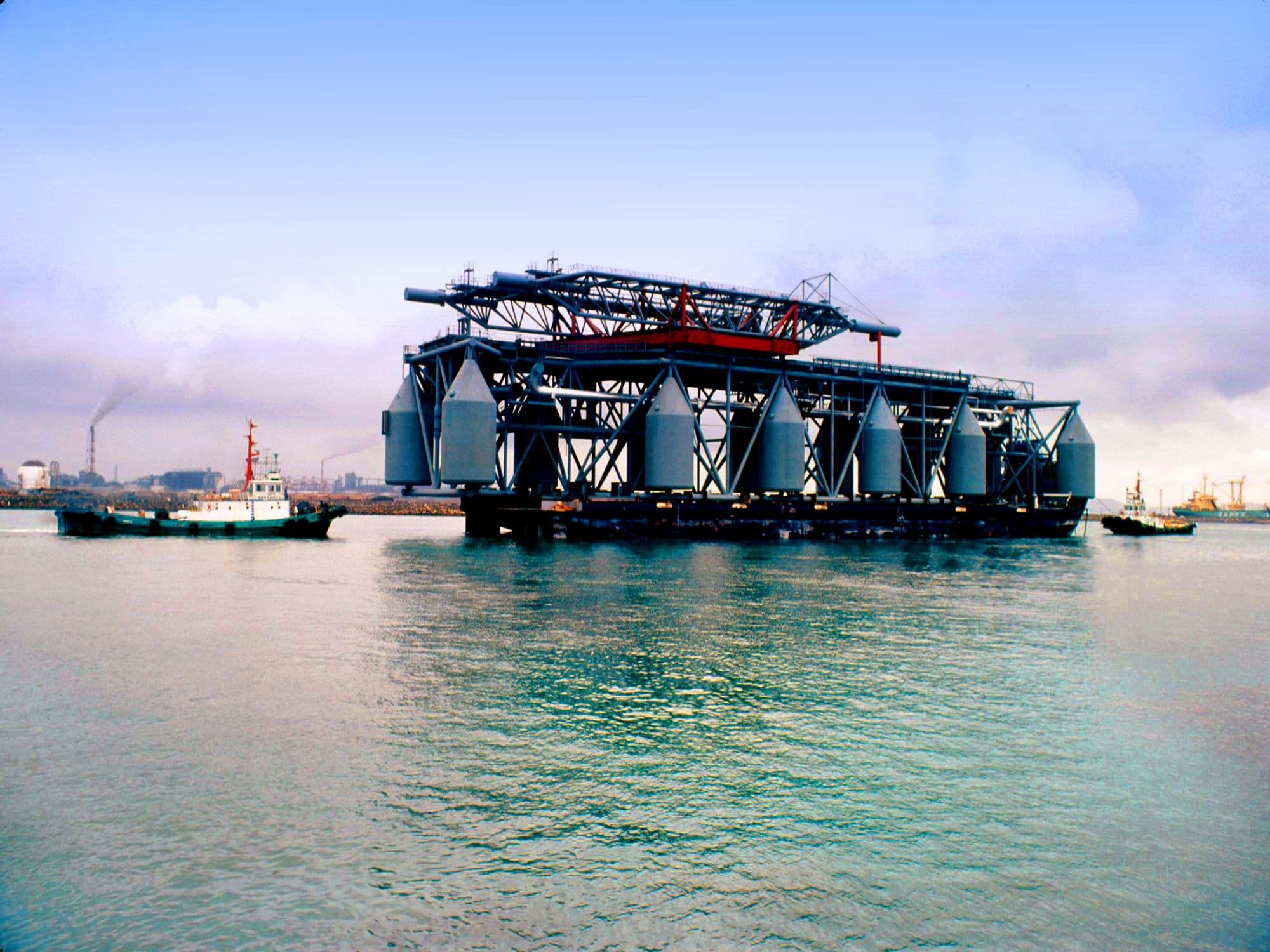
1977: Valdez Crude Oil Export Terminal floating dock built as a single module
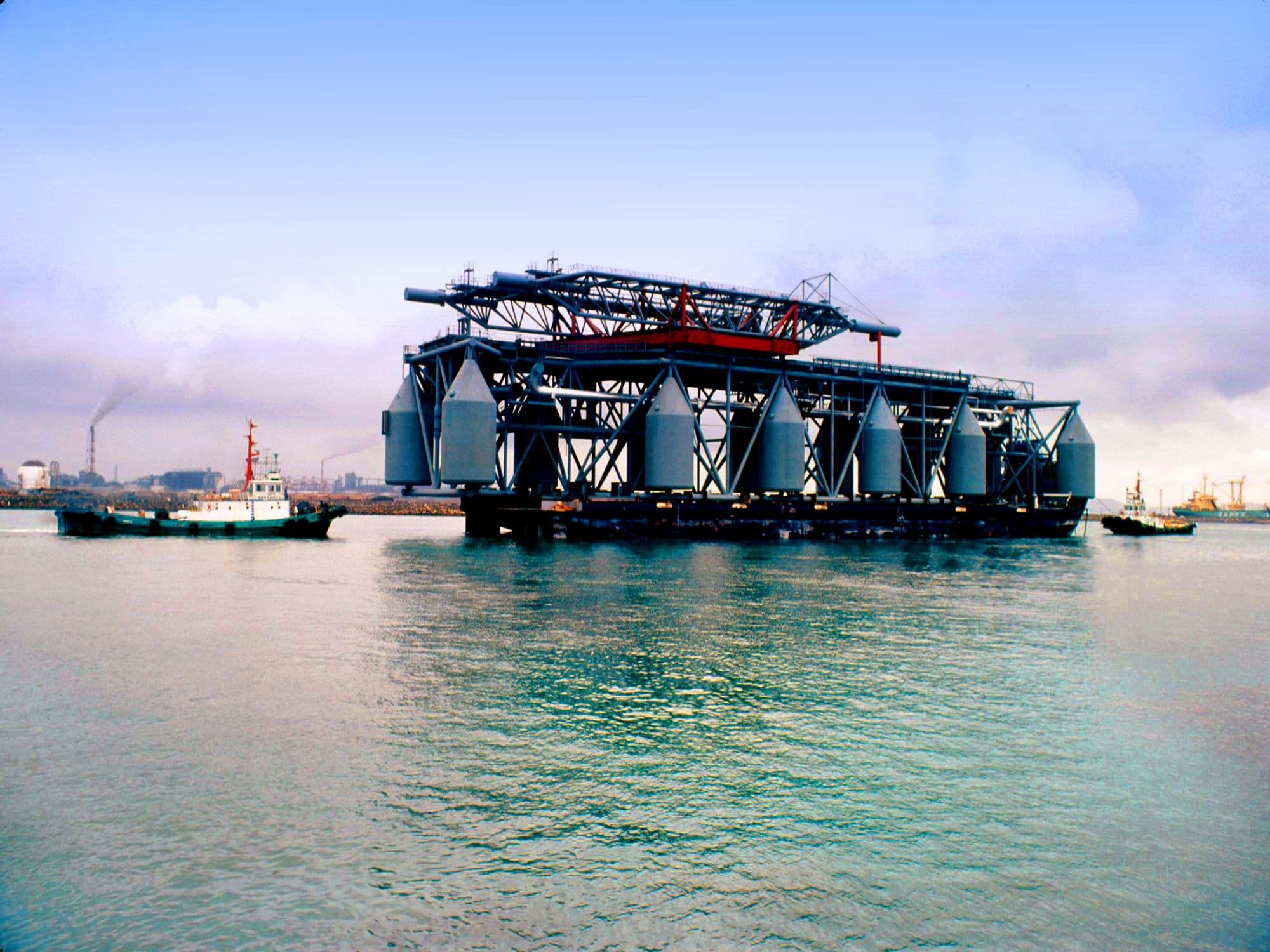
The Valdez Marine Terminal incorporated an innovative, first-of-a-kind floating dock design. At the time it was, by far, the largest crude oil tanker loading terminal in the U.S. Fluor was responsible for EPCM of the original terminal and used new technical approaches to control costs and meet aggressive budget goals. The terminal included both fixed and floating berths.
1978
United States' first deepwater port constructed using offshore modules
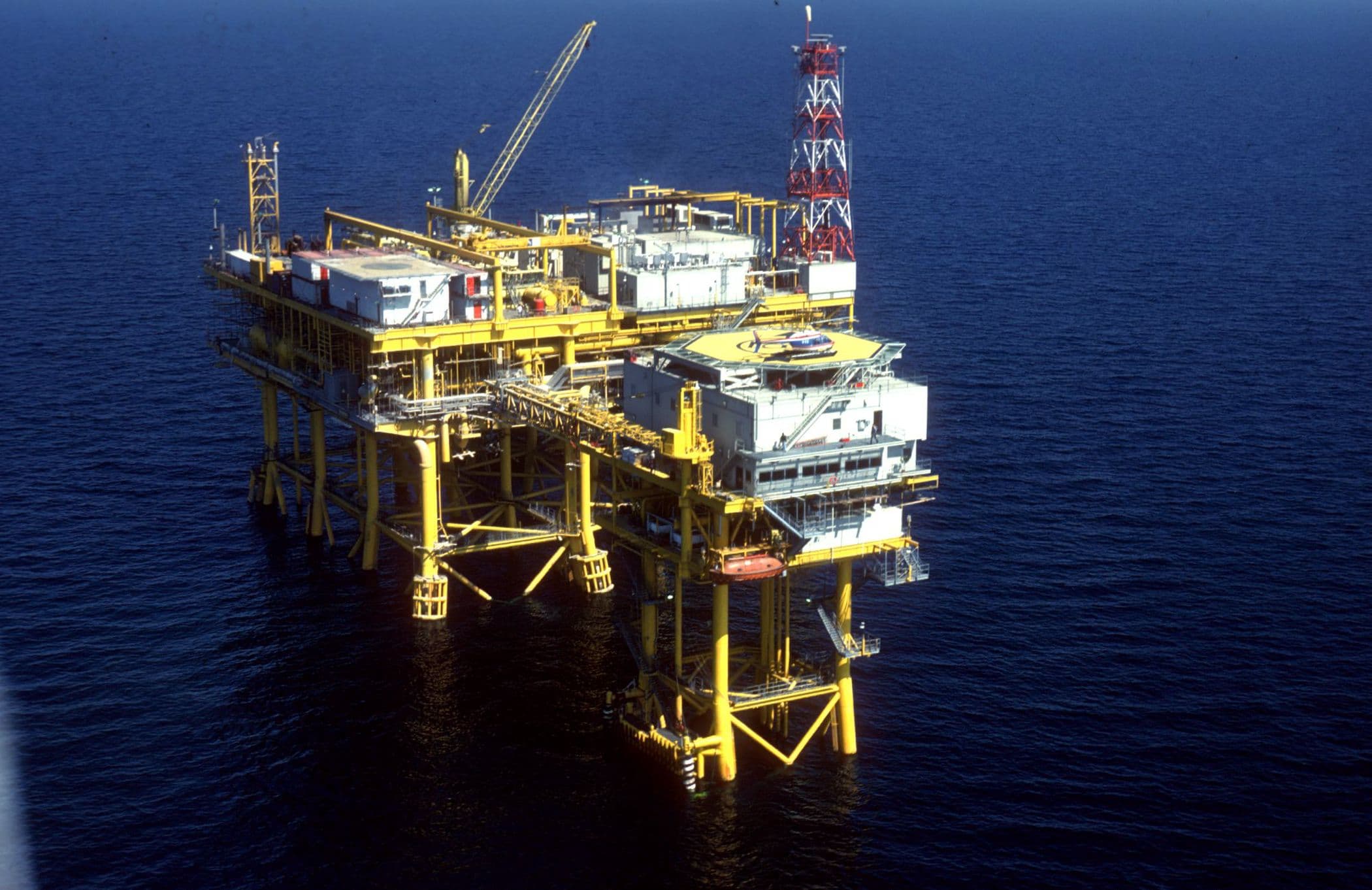
1978: United States' first deepwater port constructed using offshore modules
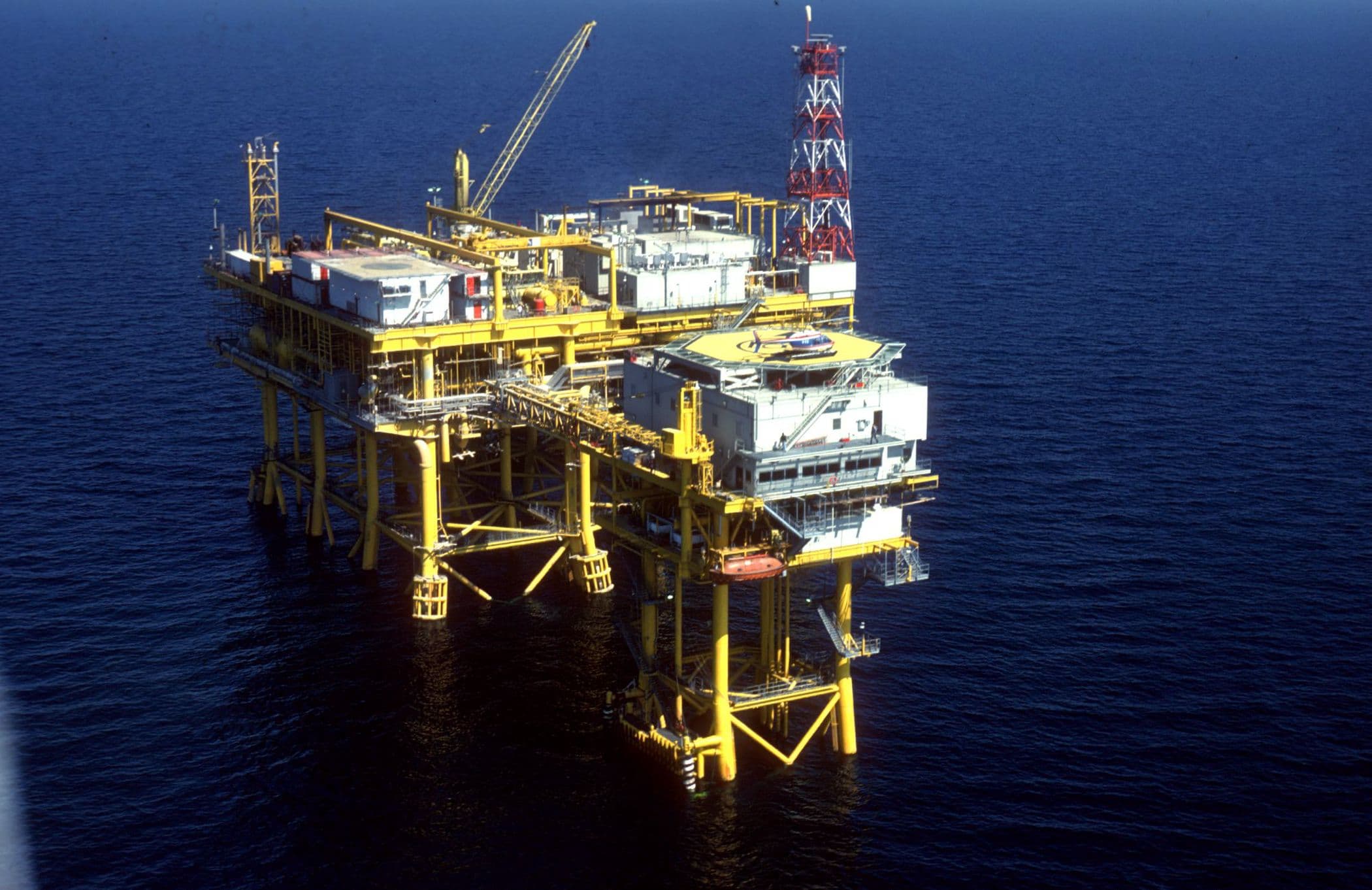
Fluor was managing contractor for the United States' only deepwater oil terminal, the Louisiana Offshore Oil Port (LOOP), which provides offloading and temporary storage for imported crude oil. In designing and constructing the terminal, Fluor set new expectations about what could be installed in the Gulf of Mexico. At the time, this was the largest import facility in the U.S.
1978
Saudi Aramco's Shedgum Gas Plant onshore modularized approach leads industry design
&w=3840&q=75)
1978: Saudi Aramco's Shedgum Gas Plant onshore modularized approach leads industry design
&w=3840&q=75)
Fluor provided engineering, procurement, and construction management for the Shedgum Gas Plant, which was part of an overall Saudi Arabian Gas Program undertaken by Saudi Aramco to utilize natural gases previously considered waste product. The design of the Shedgum Gas Plant was executed using a modular concept in order to take advantage of the similarities between the new facilities and the existing facilities. The design concepts of modularization, equipment grouping, and similarity of layout contributed to schedule and cost savings.
1979
Sonatrach Gas Plant in Algeria completed using small modules
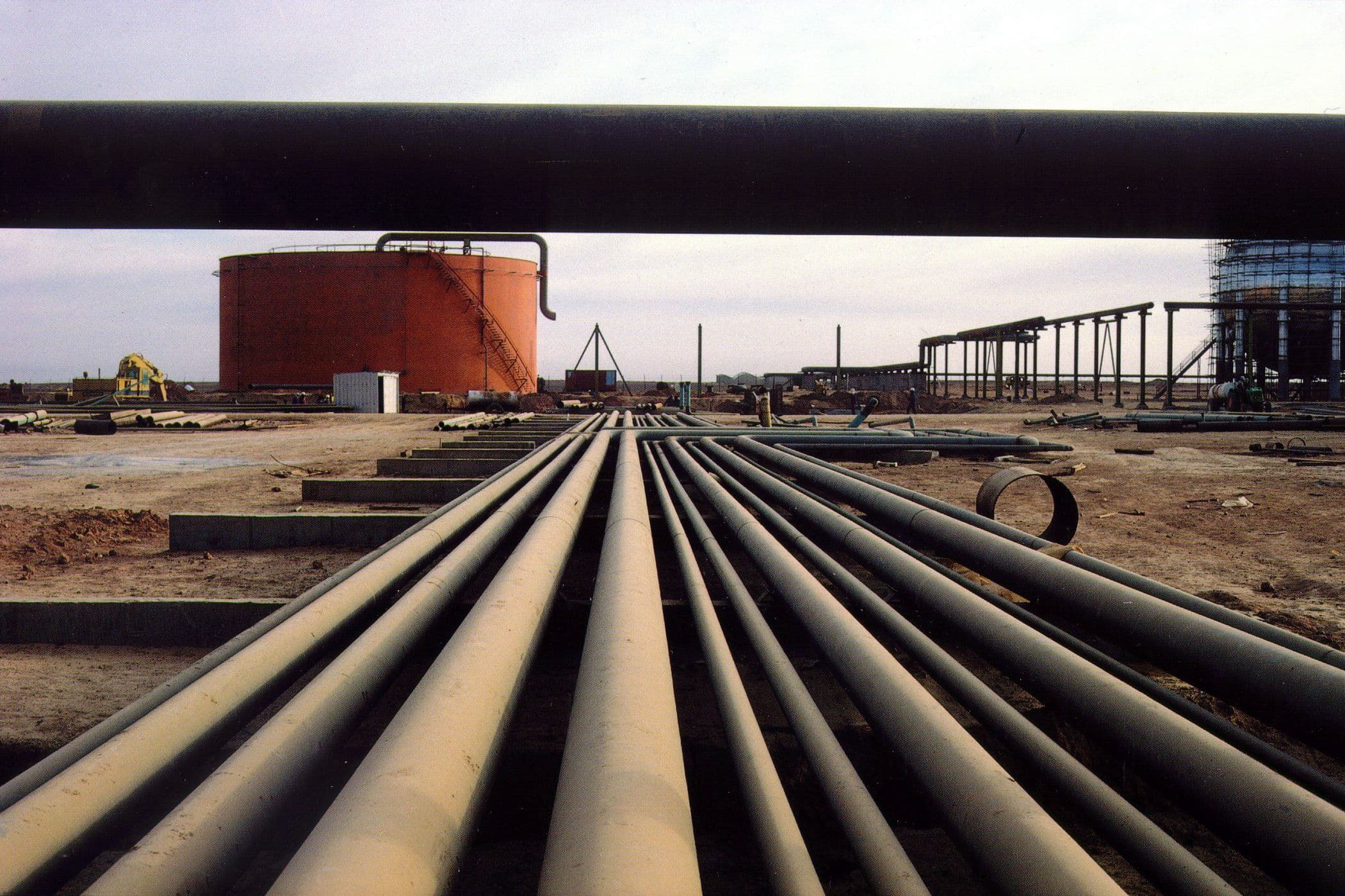
1979: Sonatrach Gas Plant in Algeria completed using small modules
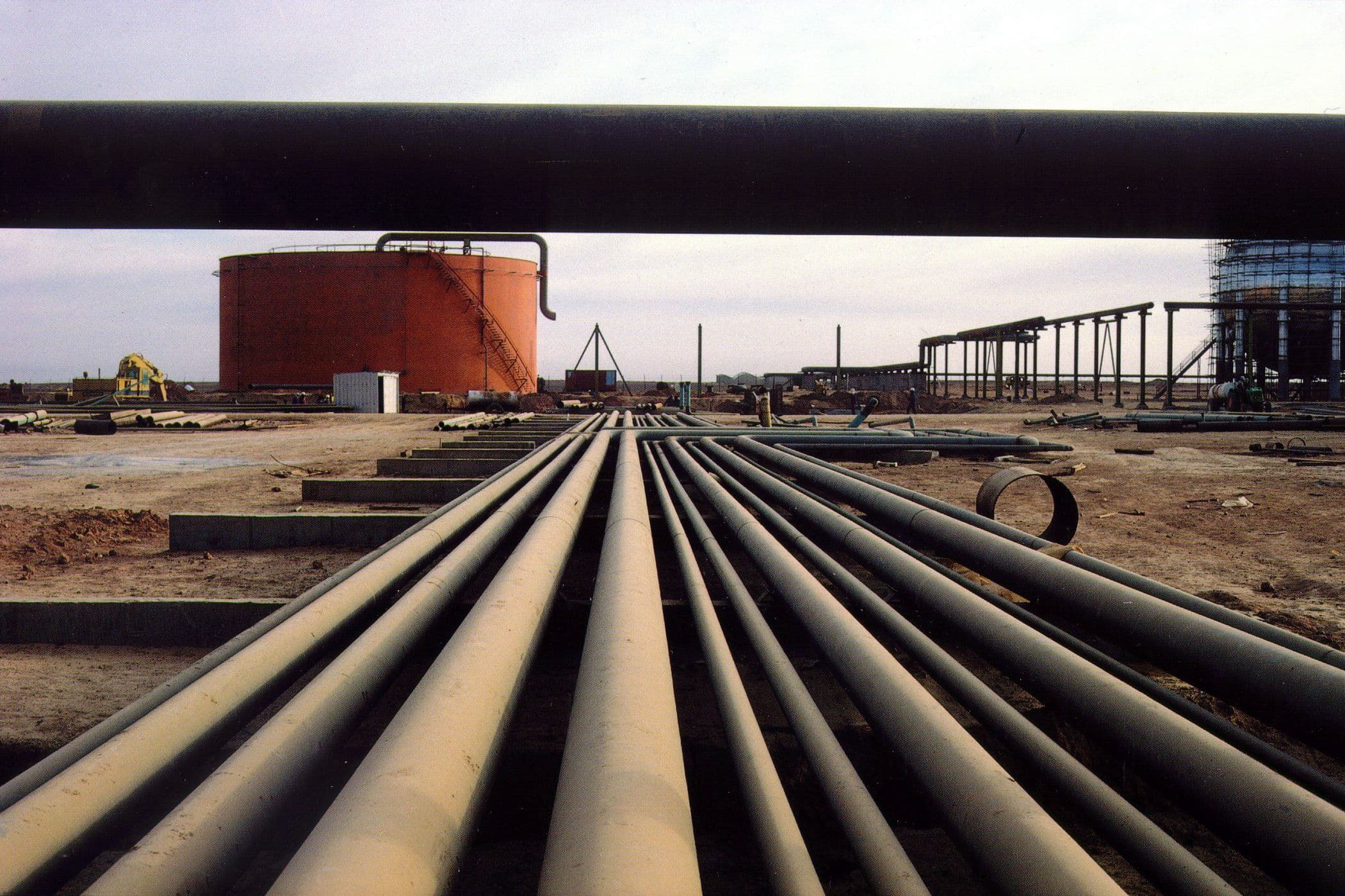
Fluor engineered and designed Sonatrach's Alrar Gas Field located in remote, eastern Algeria. Small, self contained modules were prepared offsite. The gas gathering system at the Alrar field collected gas from 22 production wells and delivered it to the treating plant battery limits. These pipeline systems then distributed the feed gas from the Alrar Gas Treating Plant to various locations.
1980s
Modular construction is used globally on some of the world's largest oil and gas projects.
1980
Fractionation modules installed at Saudi Aramco's Ju'aymah Terminal
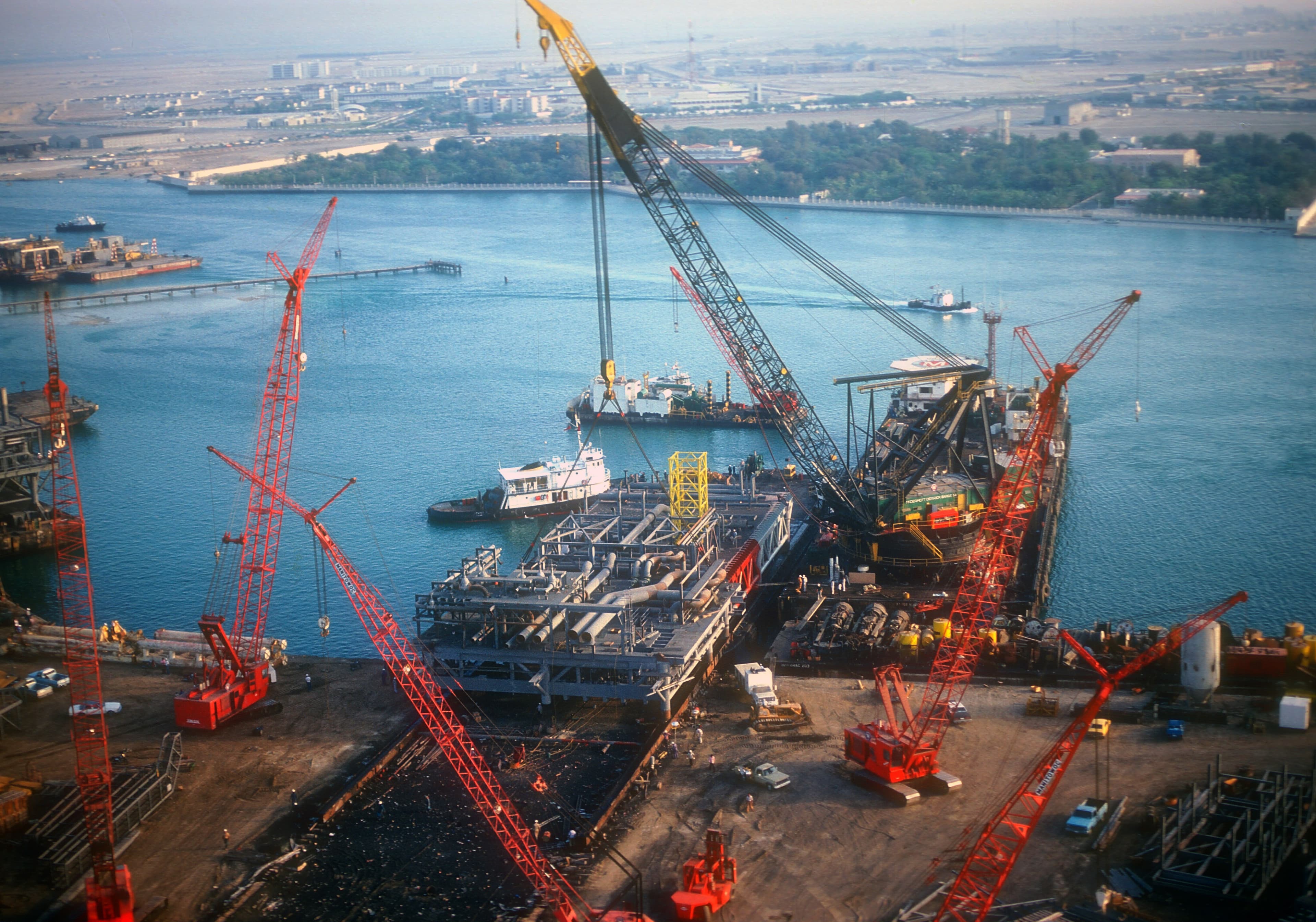
1980: Fractionation modules installed at Saudi Aramco's Ju'aymah Terminal
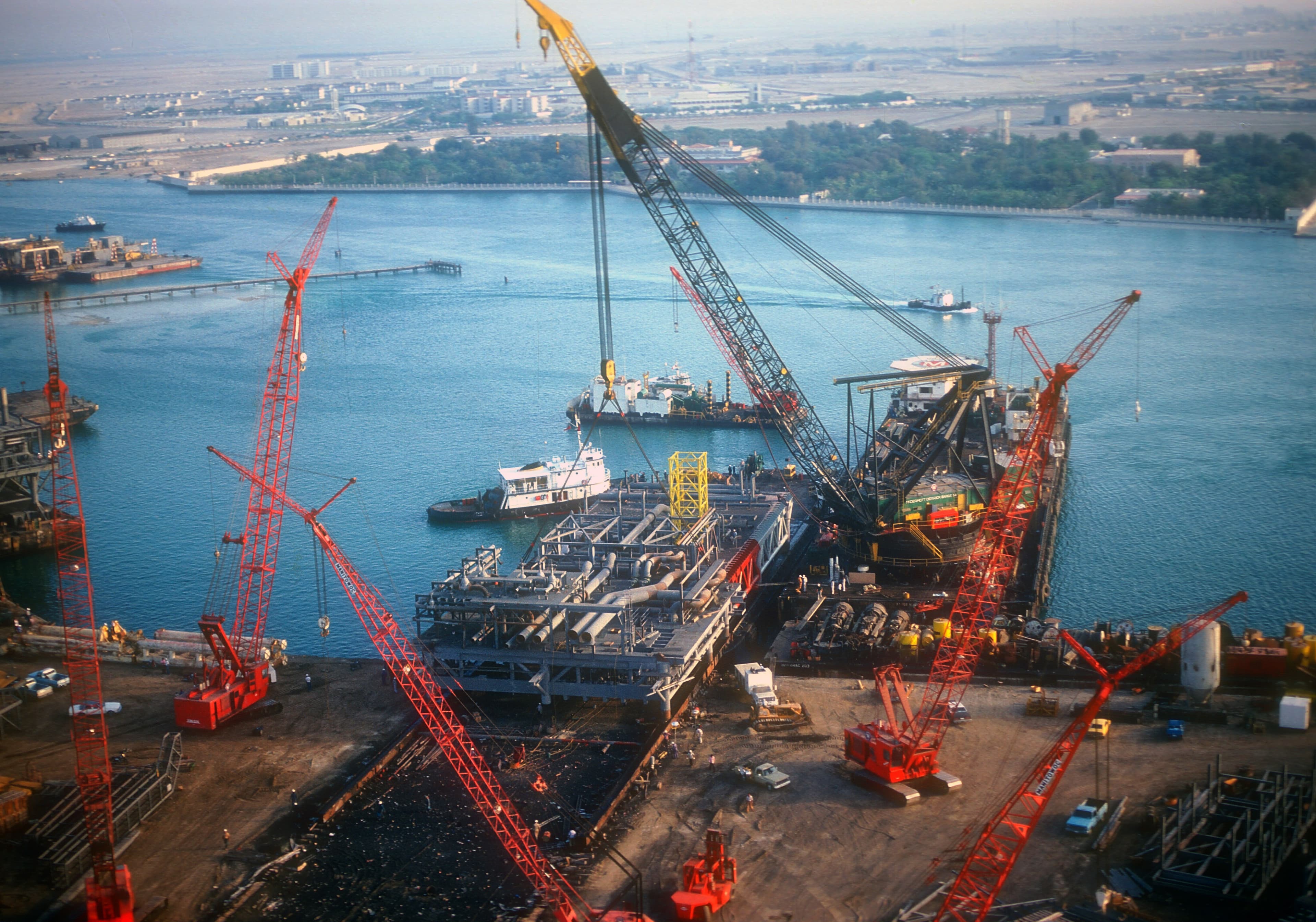
Fluor was responsible for engineering and construction management of Saudi Aramco’s Ju’aymah Terminal, one of the world’s largest crude oil storage and loading facilities at the time. The ethane-and-heavier product from the Shedgum and Uthmaniyah NGL Plants was piped to the Ju'aymah Fractionation Center for fractionation into ethane, propane, butane, and pentane-plus products. The fractionation modules included facilities for polishing the propane and butane products to meet final water and sulfur specifications.
1981
Unique modularization enhances KEMYA Polyethylene Plant construction
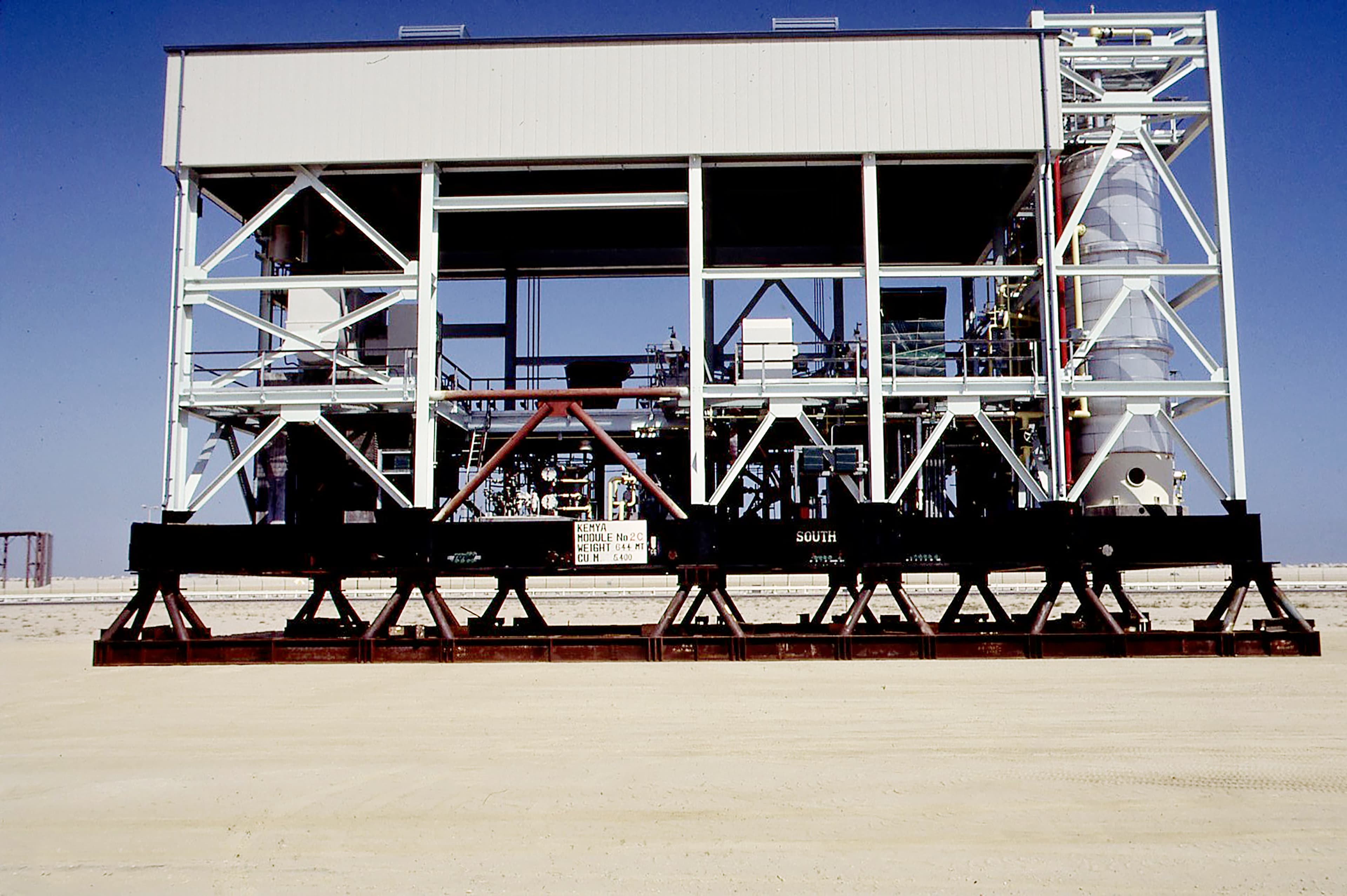
1981: Unique modularization enhances KEMYA Polyethylene Plant construction
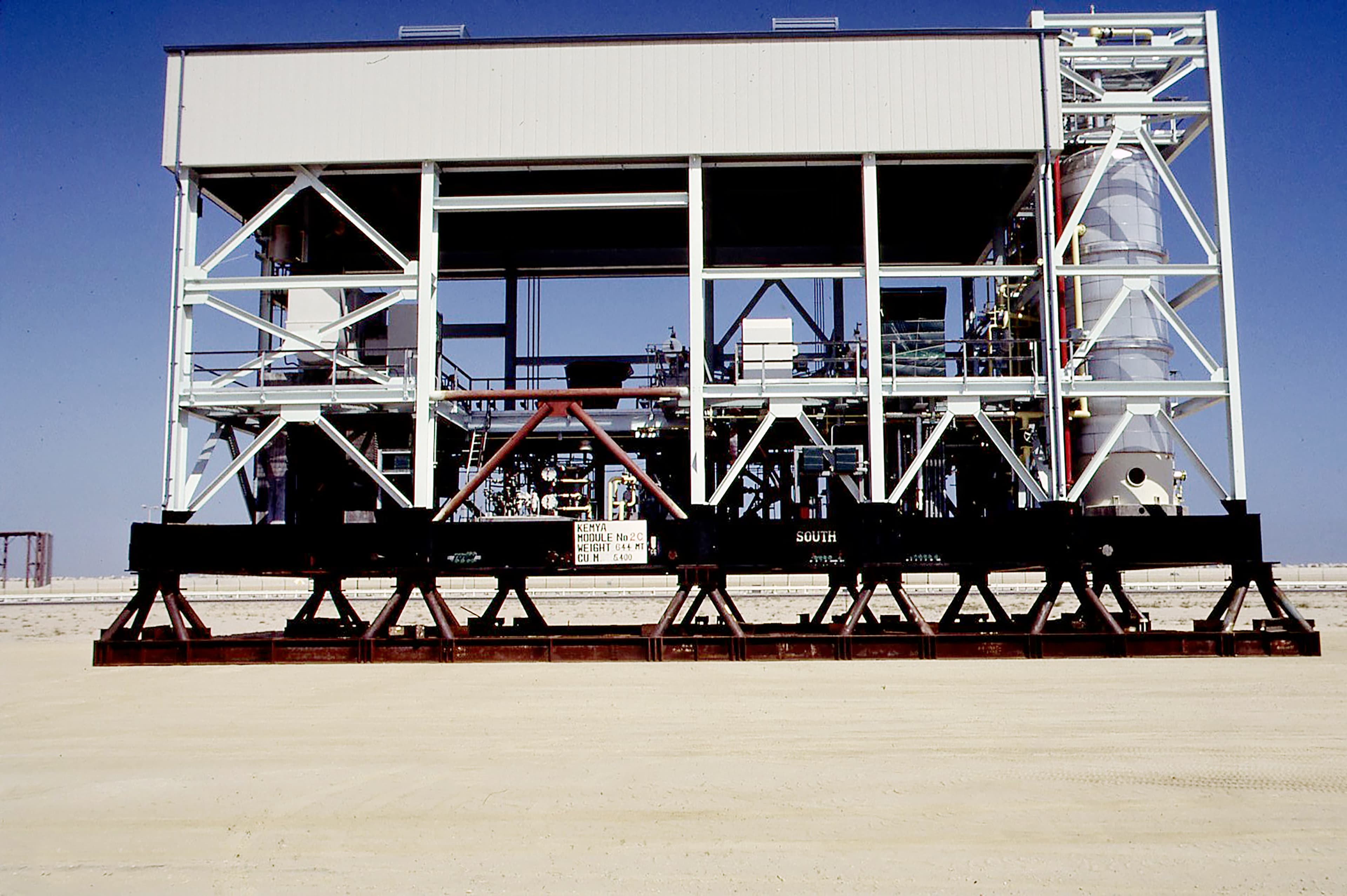
Fluor was the prime contractor for design, engineering, procurement, and construction of this major grassroots, linear, low-density polyethylene plant with a 260,000-ton-per-year nameplate capacity. Union Carbide’s Unipol process was the technology chosen by the joint-venture clients. A unique modular construction technique was used by Fluor to fabricate the process and support facilities offshore for assembly at the plant site. This approach resulted in substantial cost savings and in project completion ahead of schedule. The project required 28 modules.
1981
Phased construction at Sohio's Water Treatment Facility utilizes modular construction
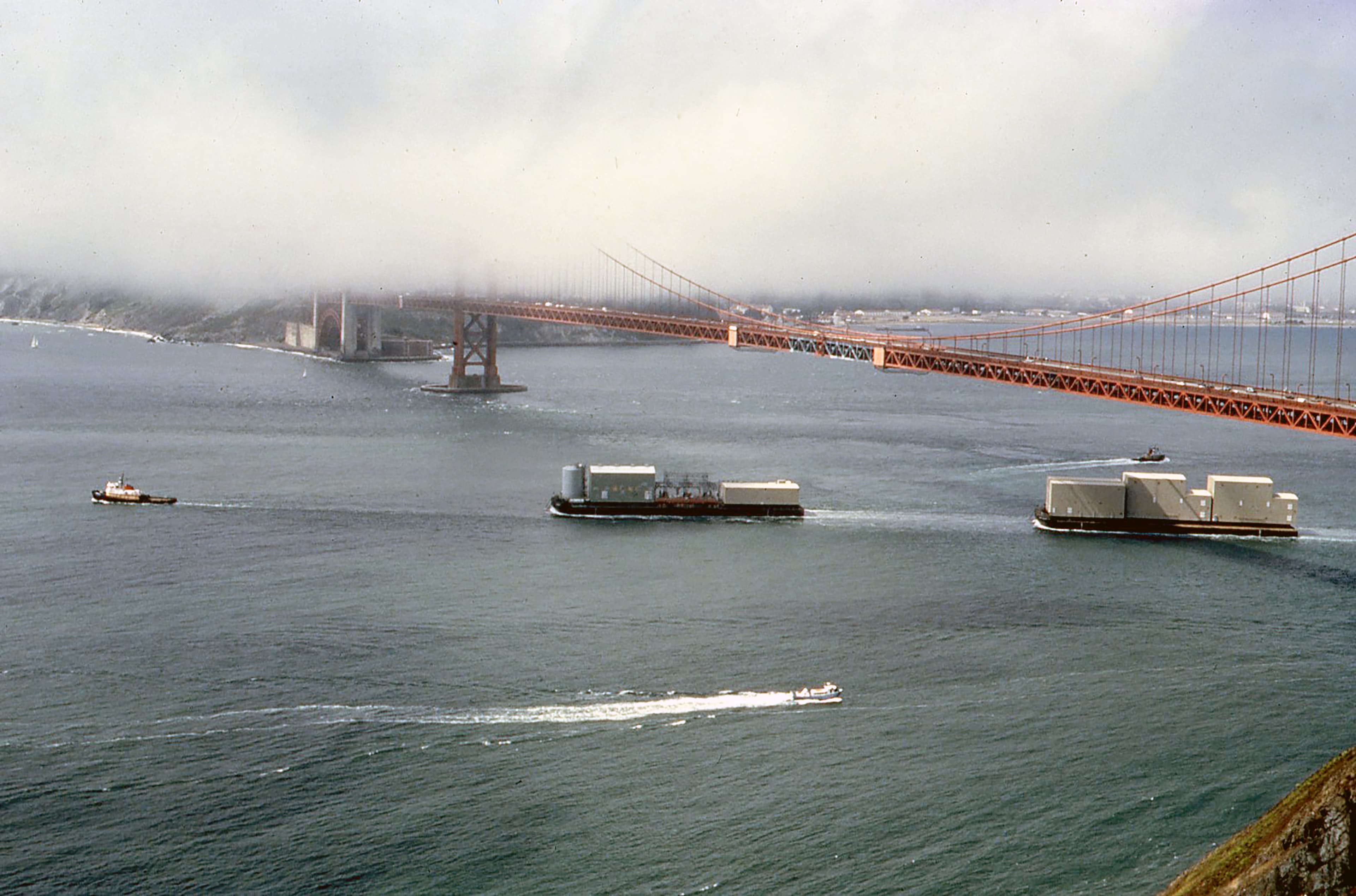
1981: Phased construction at Sohio's Water Treatment Facility utilizes modular construction
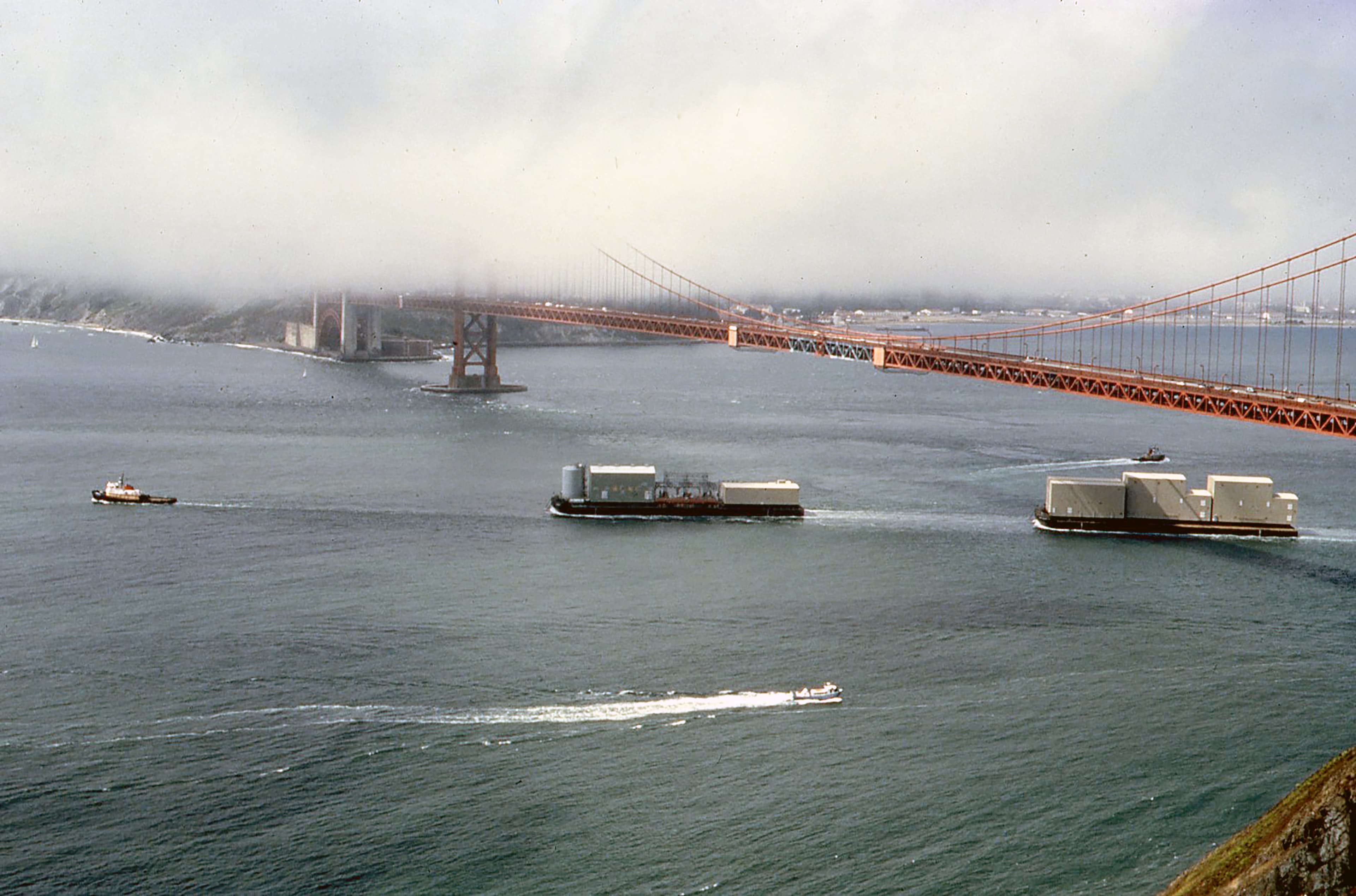
Sohio's produced water treatment and injection facilities used a modular design concept. Process, utility, and electrical equipment was installed and interconnected in six enclosed modules and five skids. The modules were 47 feet wide and ranged up to 120 feet in length. Individual modules weighed up to 750 tons. The modules and skids were sealifted by barge in the summer of 1981 and, subsequently, installed and interconnected at Prudhoe Bay, Alaska.
1983
Skid-mounted modules installed at Union Camp Paper Mill
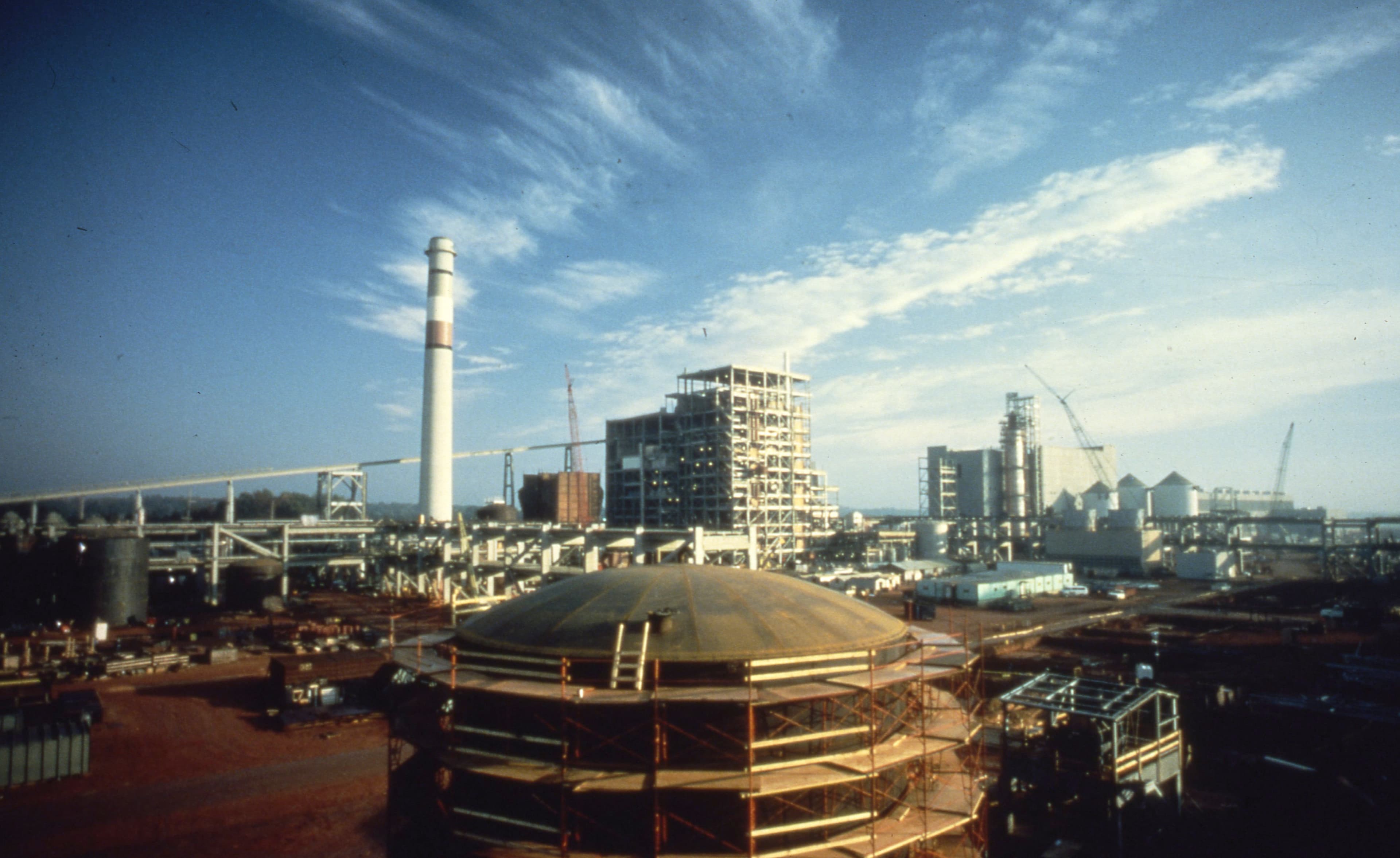
1983: Skid-mounted modules installed at Union Camp Paper Mill
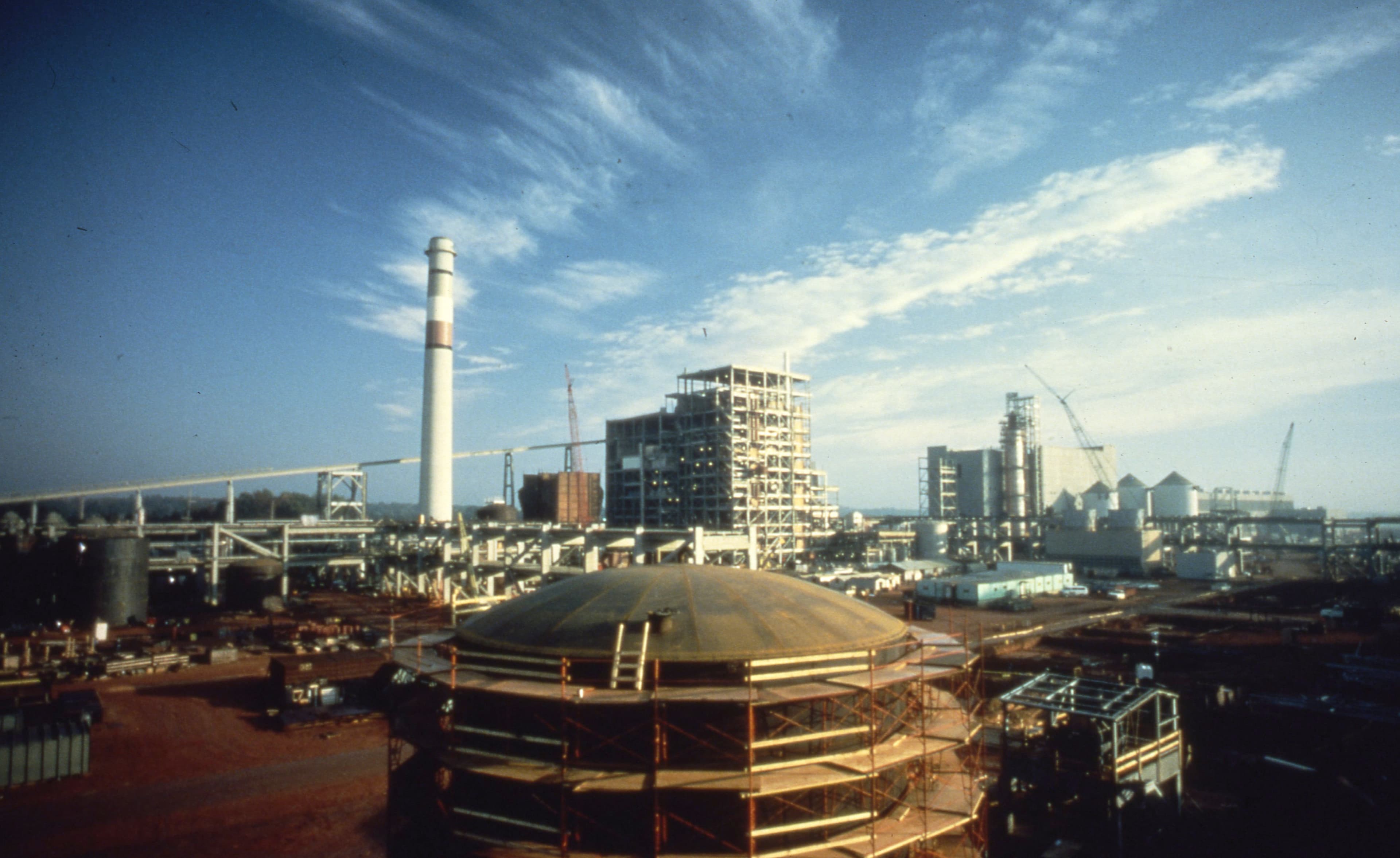
Fluor engineered, procured, and managed construction for Union Camp's grassroots paper mill. During construction, Fluor installed skid-mounted modules at the mill in Eastover South Carolina.
1983
United States' first shale facility constructed using modules for Union Oil
&w=3840&q=75)
1983: United States' first shale facility constructed using modules for Union Oil
&w=3840&q=75)
Union Oil's Shale Oil Program at Parachute Creek, Colorado was the first commercial oil shale facility in the United States. The program included a mine, an above ground retort, and an upgrading plant to convert the shale to synthetic crude oil. Fluor was responsible for the engineering and procurement of the upgrading plant and for the construction of the overall complex. Fluor utilized small and skid-mounted modules to construct the plant.
1984
Modular construction at Texaco's Convent Refinery improves schedule and reduces cost
&w=3840&q=75)
1984: Modular construction at Texaco's Convent Refinery improves schedule and reduces cost
&w=3840&q=75)
Fluor used a block construction approach to modularizing several units at Texaco’s Convent refinery. The piperack modules included offsite preassembly of fabricated structural steel and staffing of process piping, including insulation, shoes, guides, and anchors. The equipment structure included preassembly of fabricated steel, including handrails, ladders, and platform grating, and installation of equipment, pipe, and lighting. Vertical vessels were dressed out to include installation of insulation, platforms, piping, and lighting prior to erection.
The project achieved overall schedule improvement by performing out-of-sequence construction. Cost reductions were achieved by doing the assembly work at lower elevations and in less congested areas.
1985
Mechanical completion for well head module achieved for Chevron's Hermosa platform
&w=3840&q=75)
1985: Mechanical completion for well head module achieved for Chevron's Hermosa platform
&w=3840&q=75)
Beginning in the early 1980s, Fluor provided engineering design and materials management services for the Hermosa oil and gas offshore production platform in California's Santa Maria Basin. The first platform installed in the basin, it was designed to withstand storms and earthquakes while housing a large-scale drilling operation for the client, Chevron U. S. A. Module and jacket fabrication for the platform were finished in 1984. Mechanical completion and jacket installation followed in 1985.
1985
World's largest modular construction project to date completed for SADAF in Al Jubail
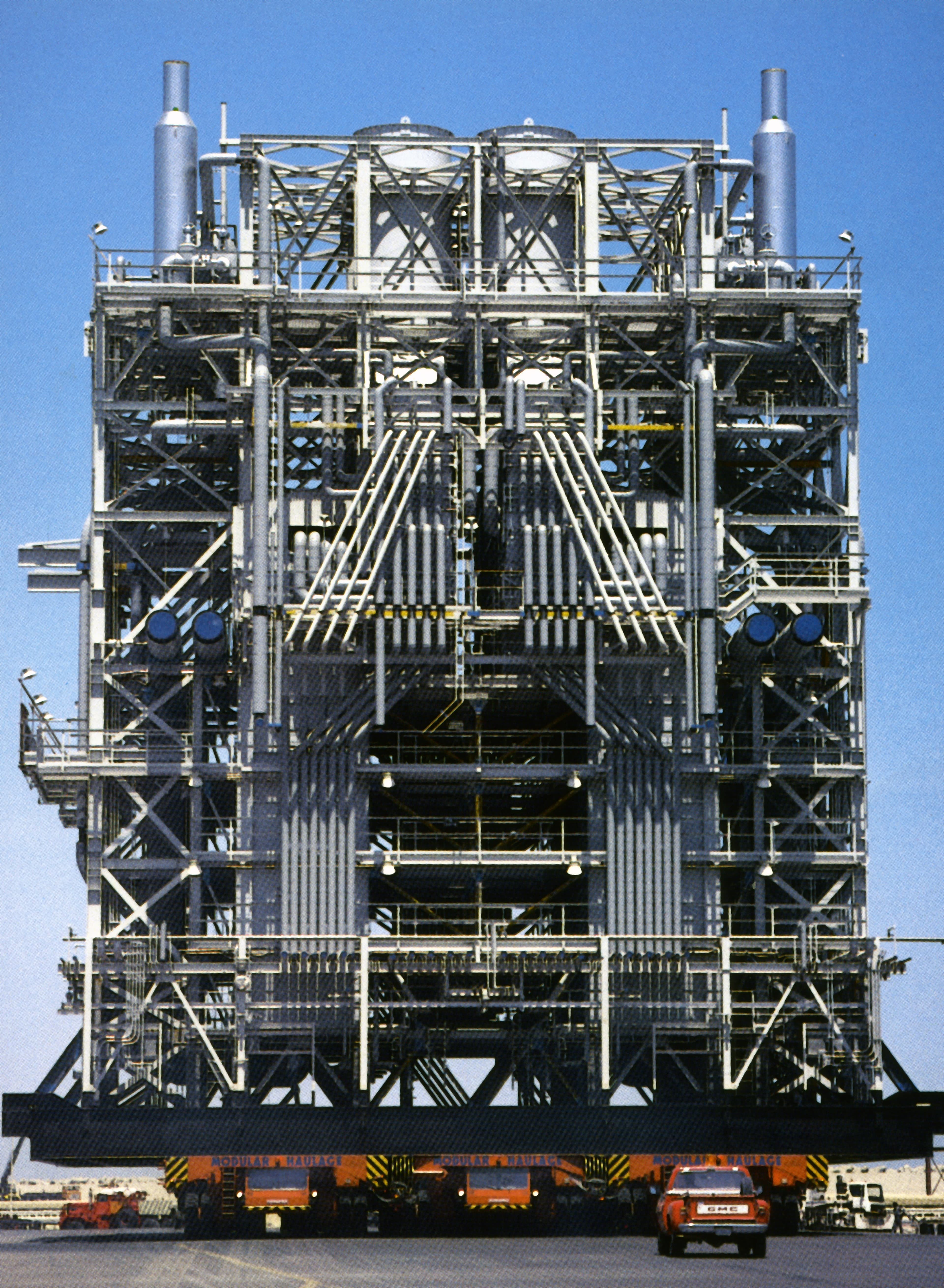
1985: World's largest modular construction project to date completed for SADAF in Al Jubail
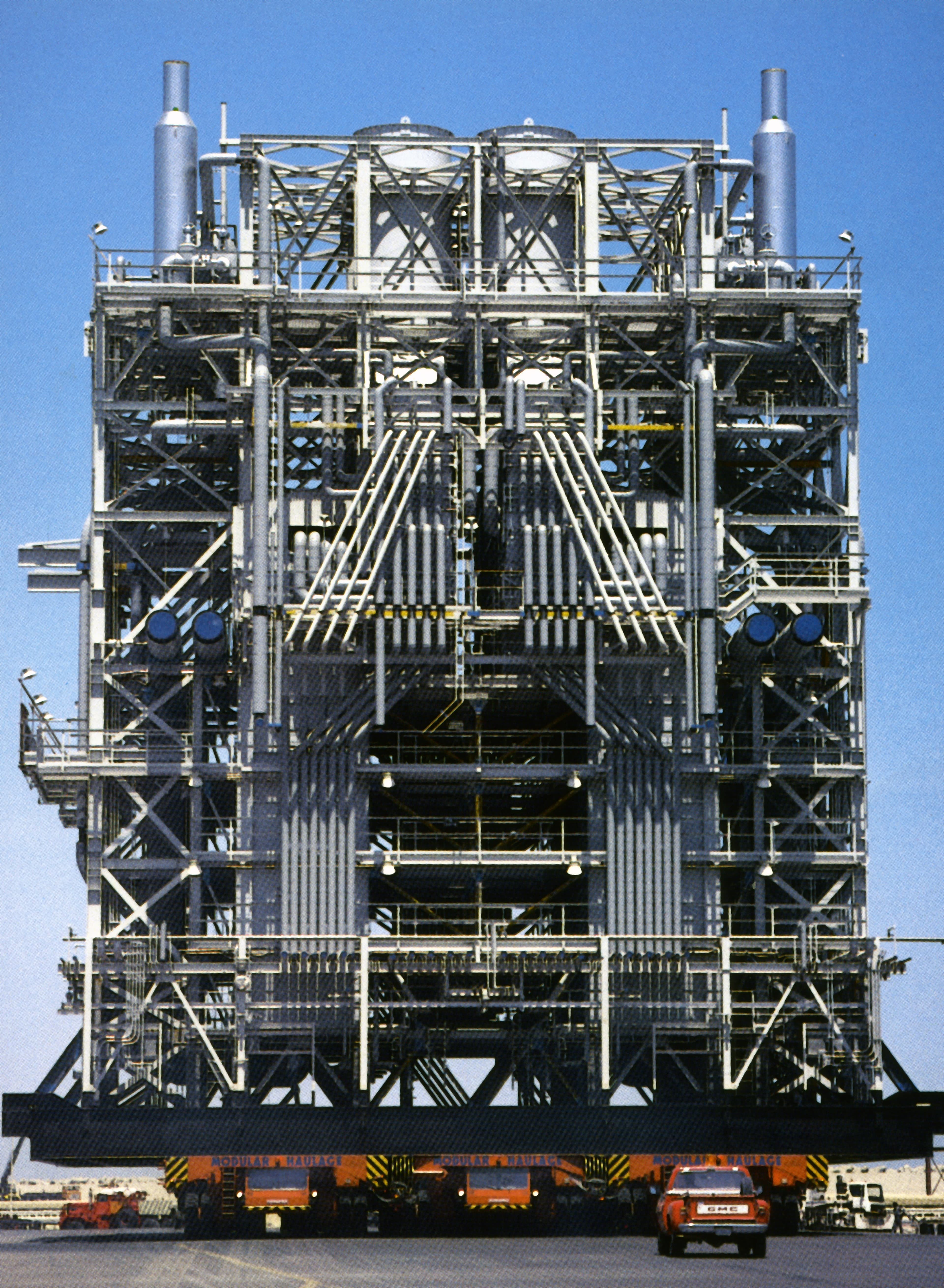
Fluor served as the managing contractor on a 500-acre grassroots ethylene-based petrochemical complex for Saudi Arabia Petrochemical Company (SADAF) at Al Jubail, Saudi Arabia. Approximately 40 percent of the complex was completed using modular construction, the largest modular construction project at the time.
1985
Modular panels used in the building of a new office space for Upjohn GmbH
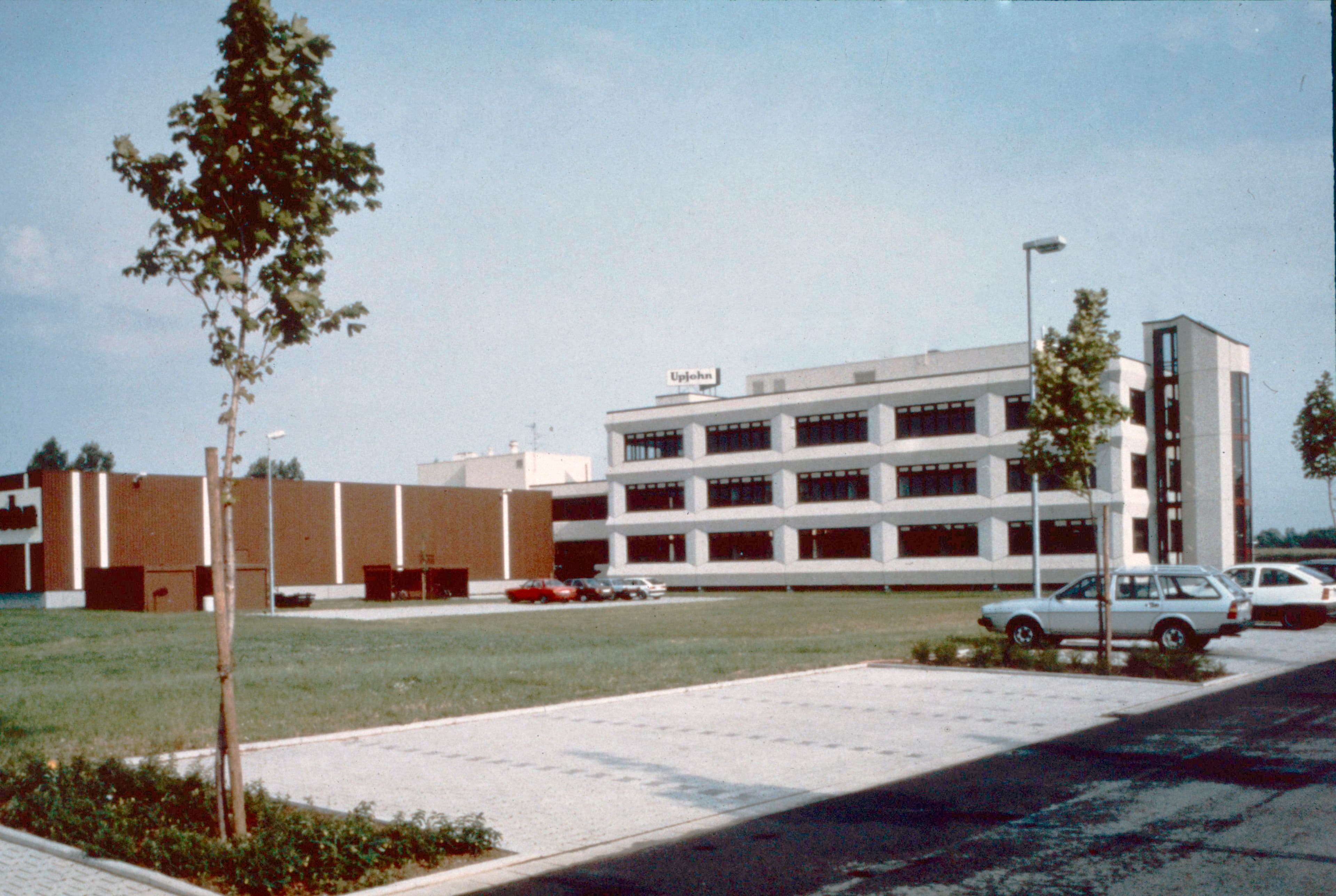
1985: Modular panels used in the building of a new office space for Upjohn GmbH
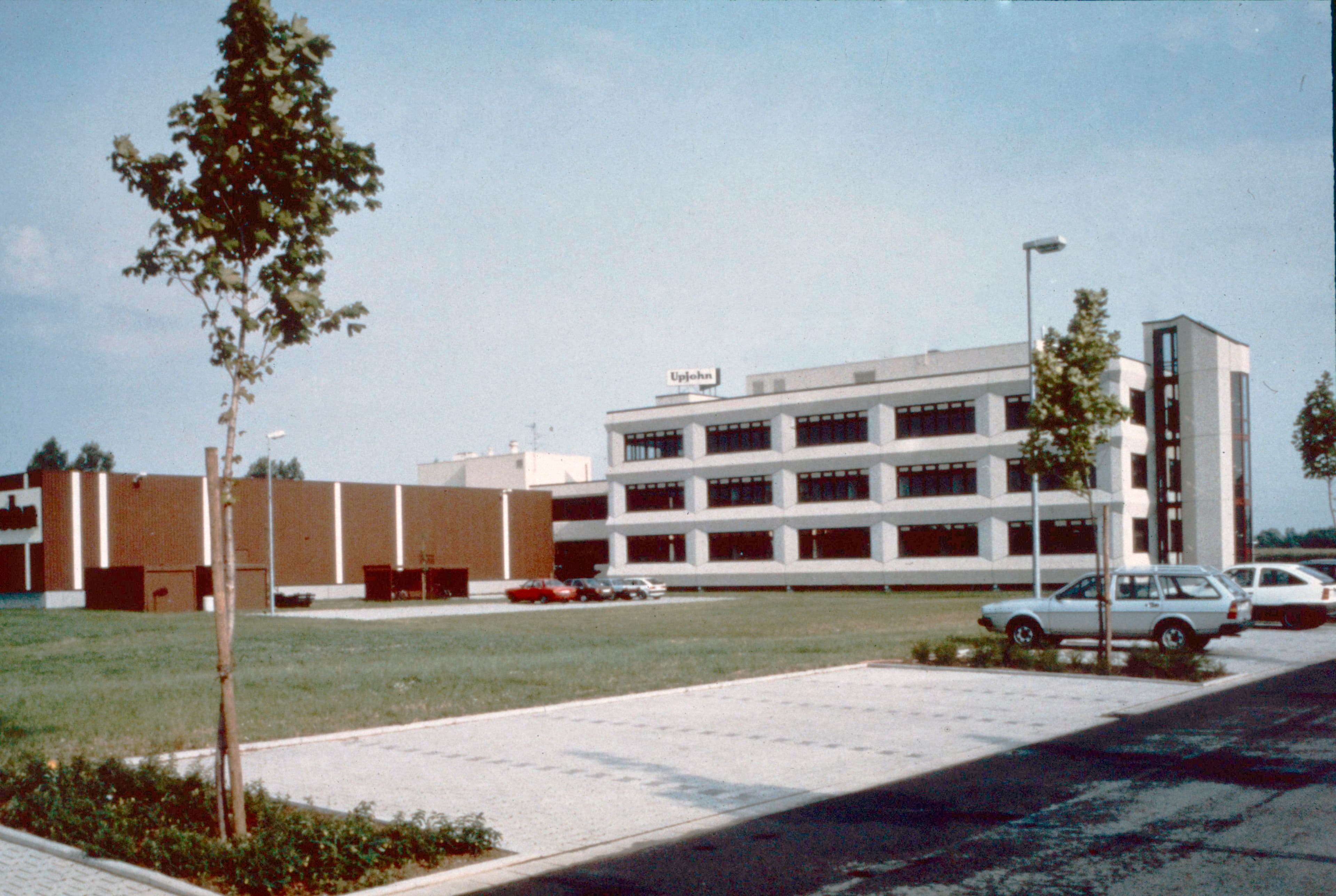
Fluor was awarded a lump-sum contract for the erection of a new office building and the remodeling of an existing warehouse by Upjohn GmbH at Heppenheim in West Germany. The total structure of the building was designed in precast concrete. The interior walls were built using high quality modular panels. The scope also included a full service kitchen designed for a work force of 150 employees. The project was completed and occupied by the client within eight months of breaking ground.
1985
Modular flowline connections innovate subsea technology at Texaco's Highlander Field
&w=3840&q=75)
1985: Modular flowline connections innovate subsea technology at Texaco's Highlander Field
&w=3840&q=75)
Texaco's Highlander Field development was a break-through in subsea technology that included universal trees and modular flowline connection concepts, a subsea slug catcher, retrievable pig launchers and receivers, and diver-friendly designs for the 420-foot water depth.
1986
GASCO NGL Extraction Plants constructed using modules
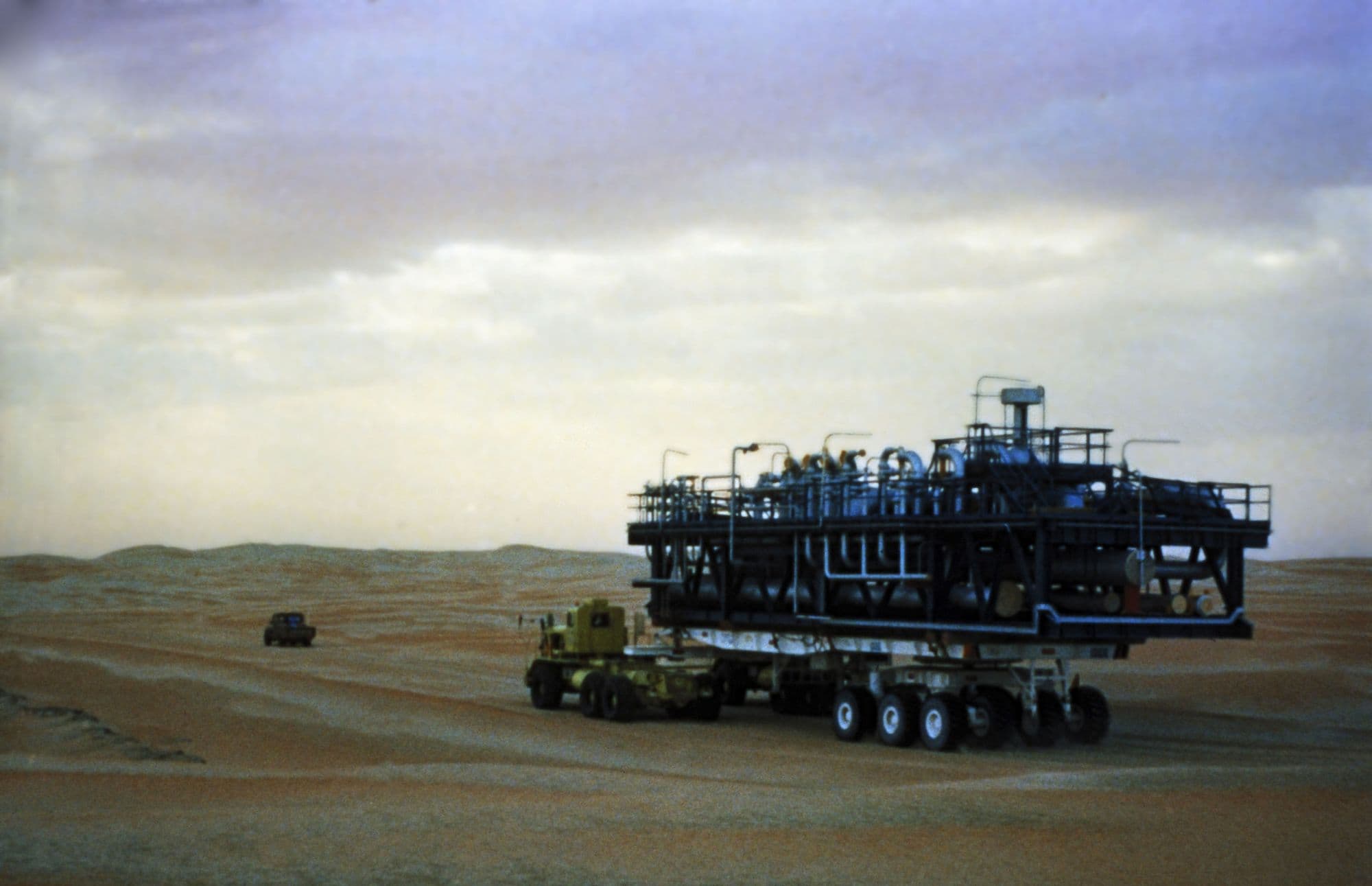
1986: GASCO NGL Extraction Plants constructed using modules
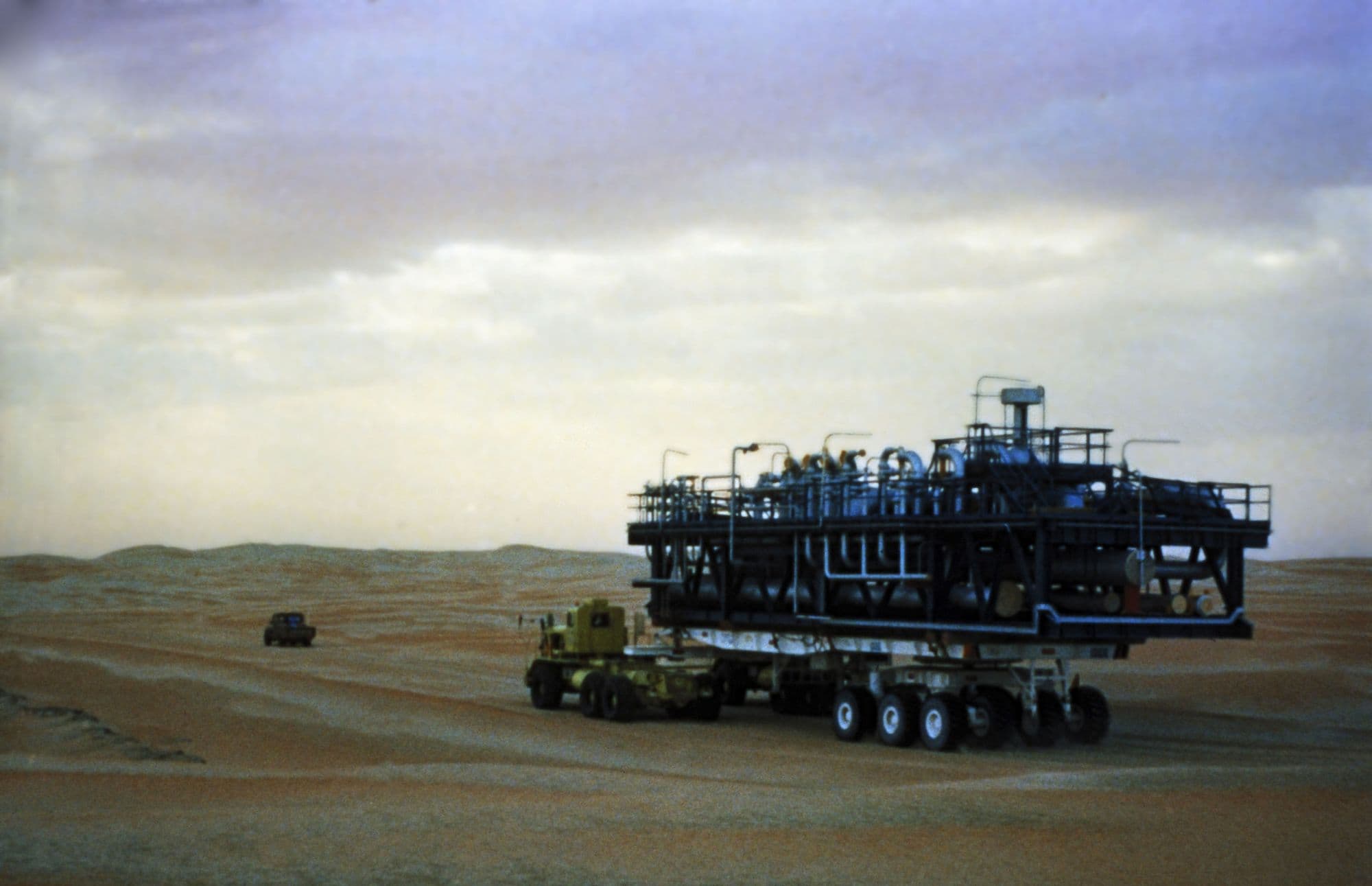
Fluor performed engineering, procurement, and construction management for the Abu Dhabi Gas Industries Limited (GASCO) natural gas liquid (NGL) extraction plants at Bab and Asab in Abu Dhabi. The remote plants required that modular construction be used and that the modules then be shipped to the site for installation. The success of this project led to subsequent work with GASCO.
1986
Saudi Aramco's Marjan offshore modules placed
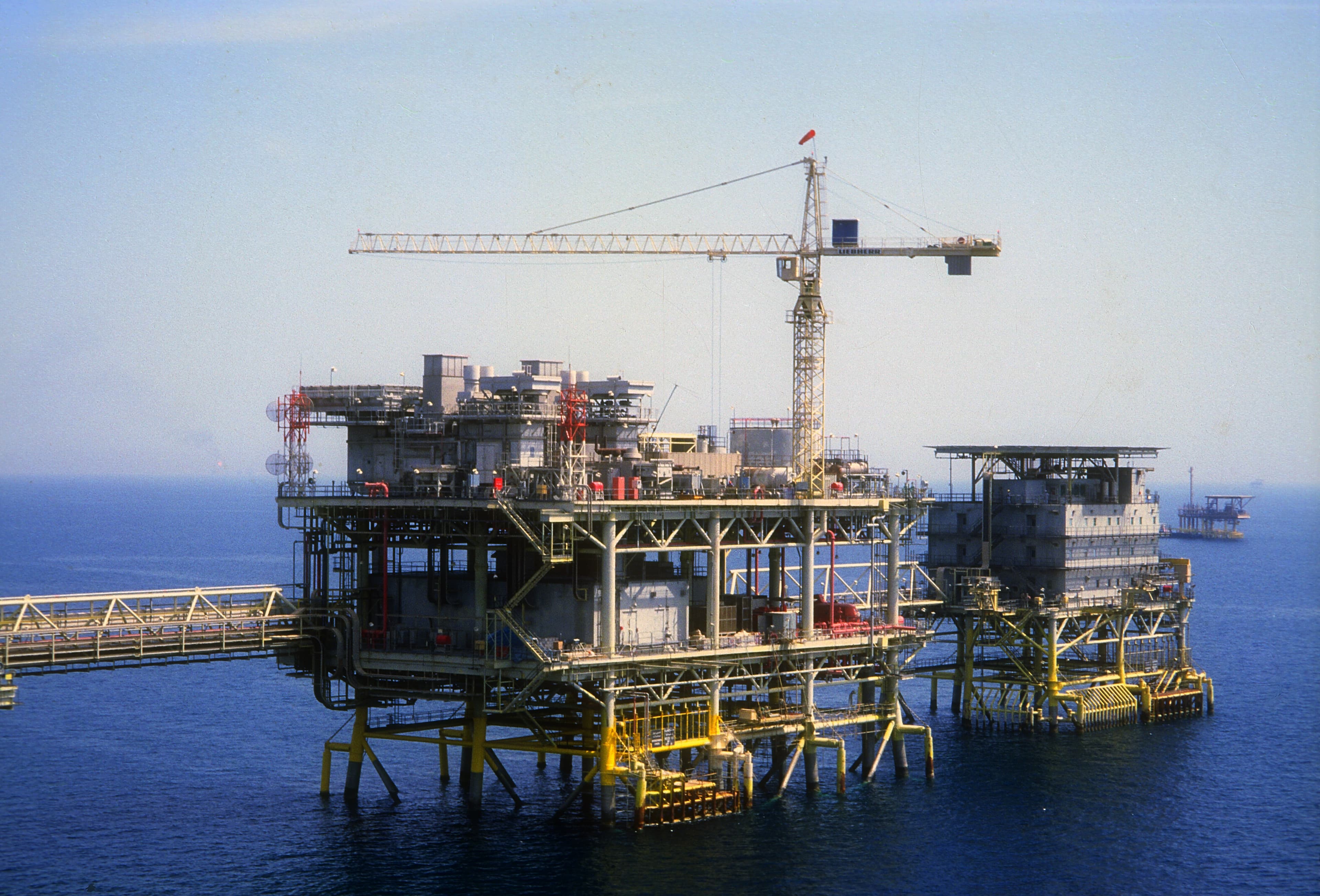
1986: Saudi Aramco's Marjan offshore modules placed
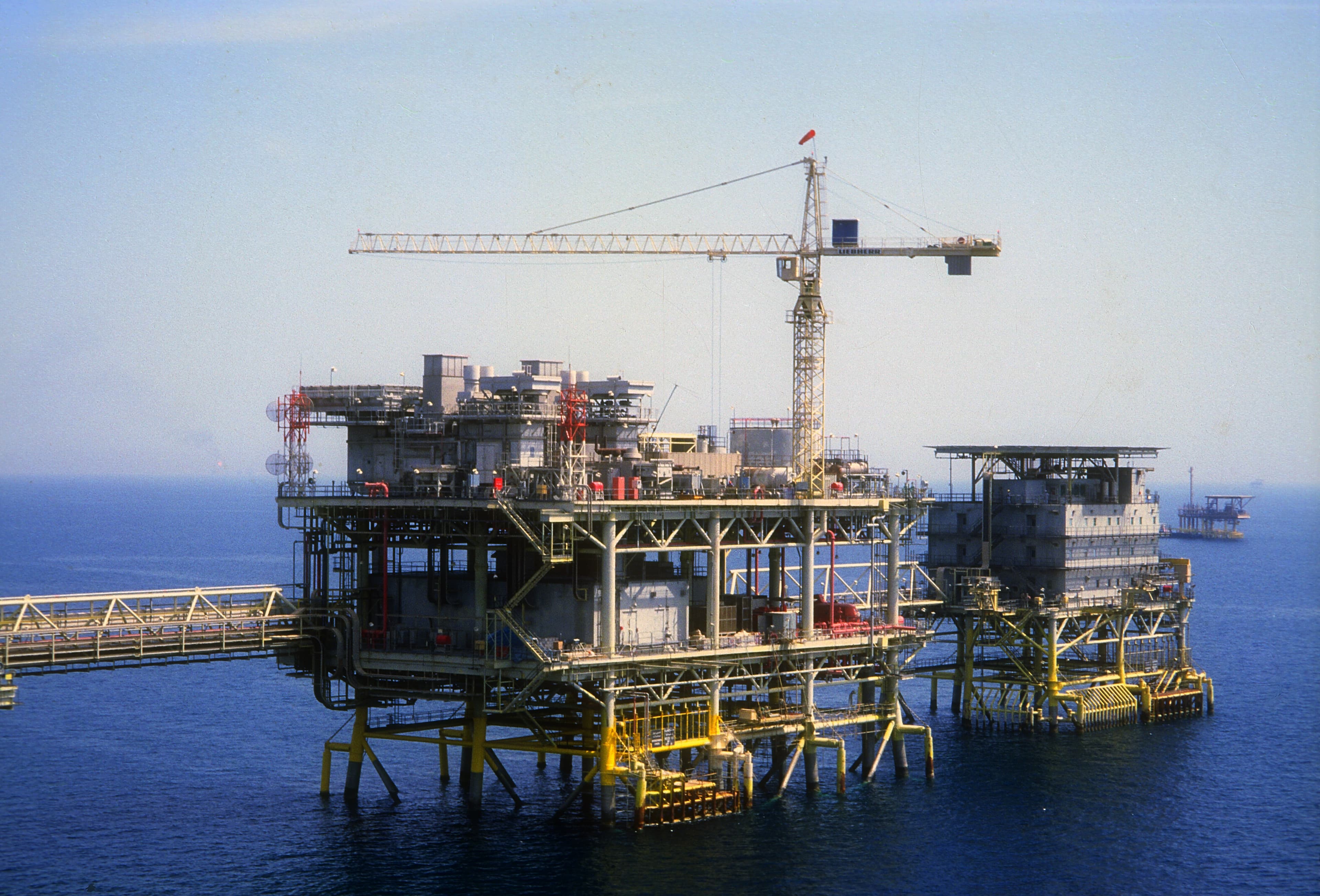
The Marjan project for Saudi Aramco consisted of two major offshore oil and gas production and separation plants. The platforms are located 50 miles offshore in the Arabian Gulf in 155 feet of water. Each of the production complexes is designed to produce 200,000 barrels per day of crude oil and 470 MMSCFD of sour gas. A total of four offshore platforms are included in each of the two complexes. Each complex consists of a quarters platform, a power generation platform, a production platform, and a pipeline manifolding riser platform. Fluor performed detailed engineering, procurement assistance, and construction management.
1987
Lisburne Field Development modules installed
&w=3840&q=75)
1987: Lisburne Field Development modules installed
&w=3840&q=75)
ARCO contracted Fluor to engineer and construct the Lisburne Facilities Project. The project was located in the Prudhoe Bay Field area and was made up of five onshore and one offshore drill sites and a central onshore production facility. Fluor developed a production center composed of seven modules. The modules included oil production, gas processing, gas injection, power generation, utilities, shop/warehouse, and living quarters.
1988
Modular control systems used at Europe's first commercial biotech facility
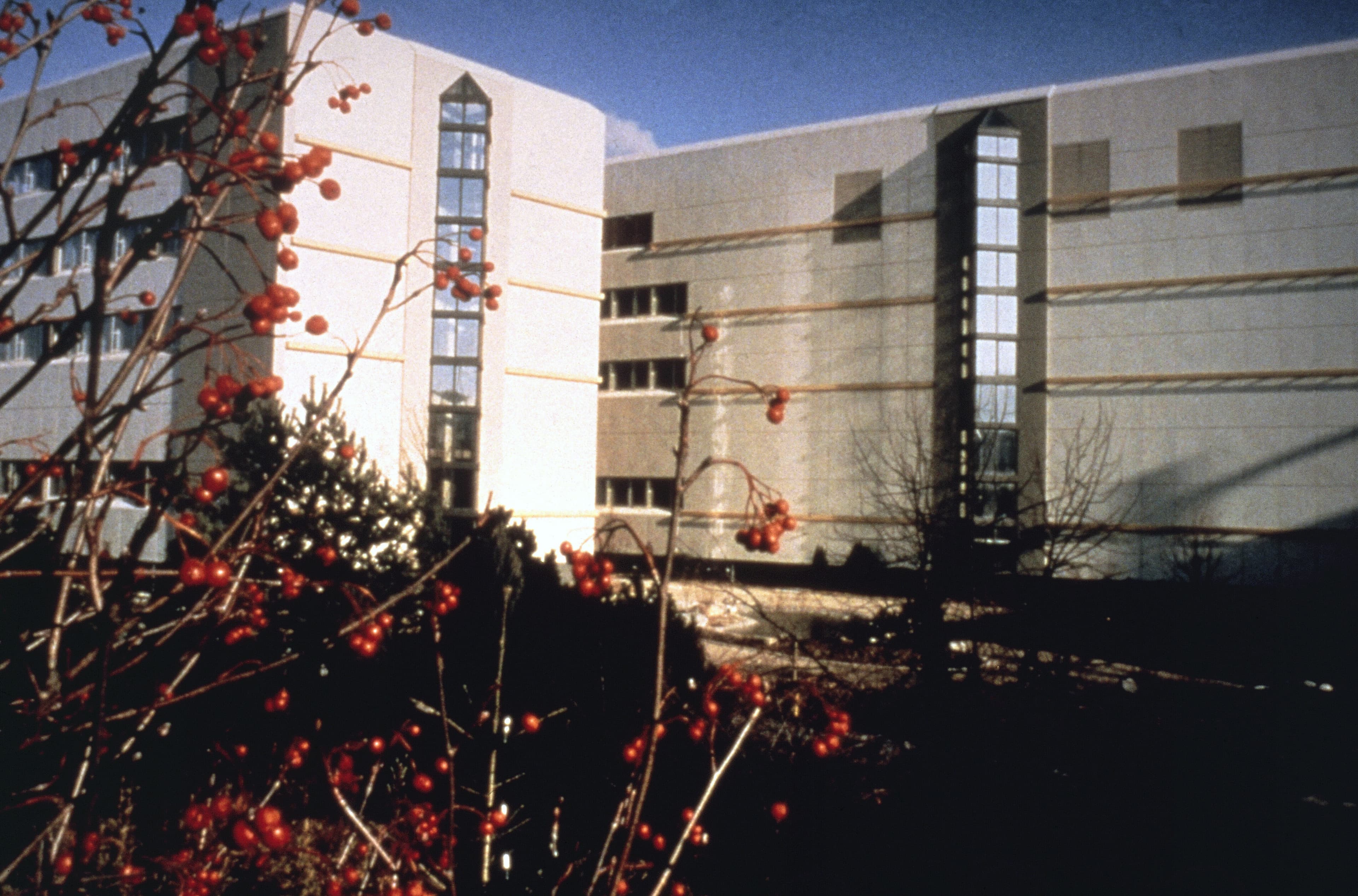
1988: Modular control systems used at Europe's first commercial biotech facility
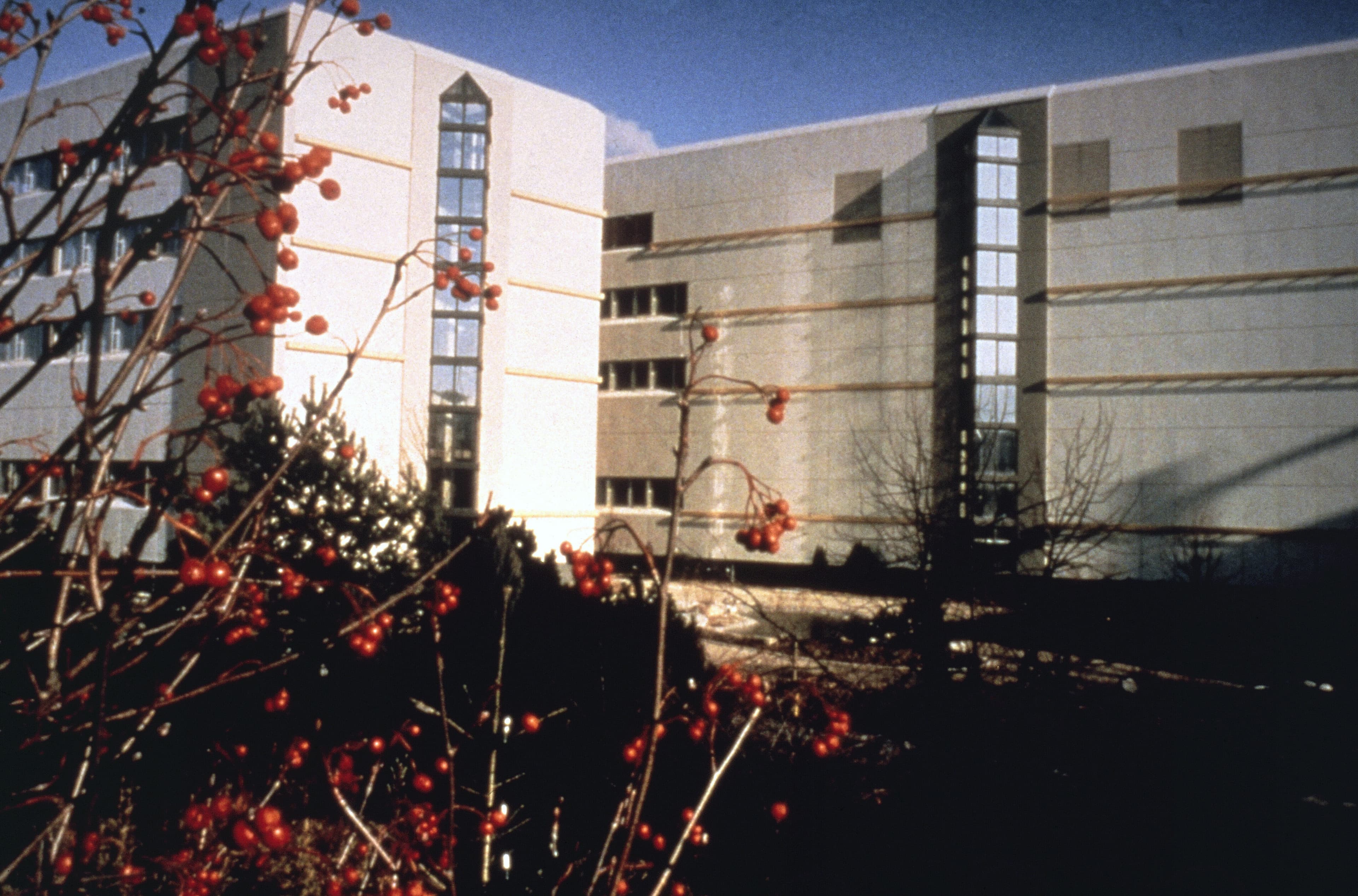
Fluor was awarded the engineering, procurement, construction management, and project management of the greenfield Thomae biotech plant in Biberach, the first European commercial biotech facility in 1986. The plant used automated modular process control systems.
1990s
Fluor's modular construction experience continues to expand.
1991
Eight-legged steel jacket structure supports three production modules off the coast of Côte d’Ivoire
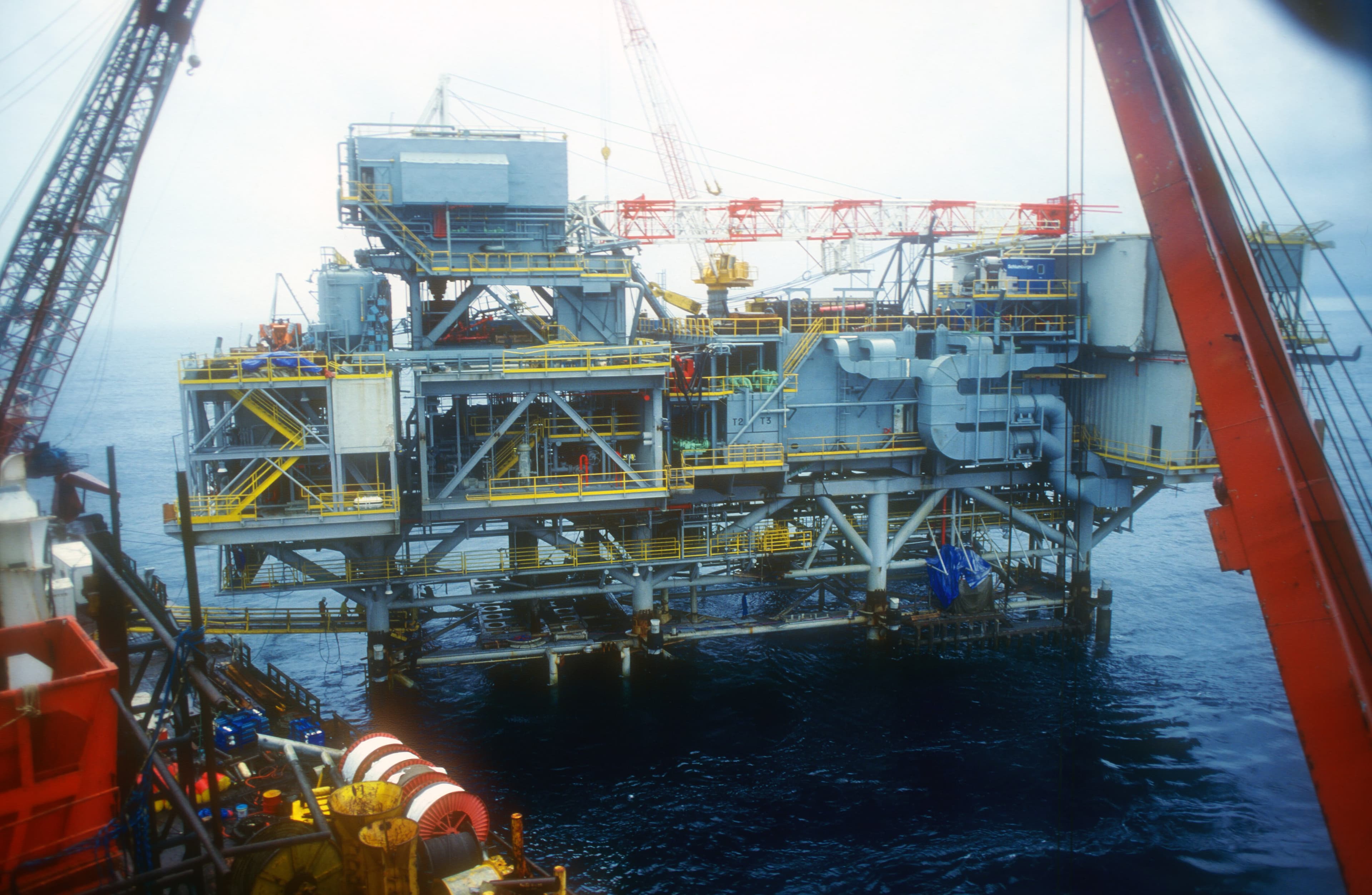
1991: Eight-legged steel jacket structure supports three production modules off the coast of Côte d’Ivoire
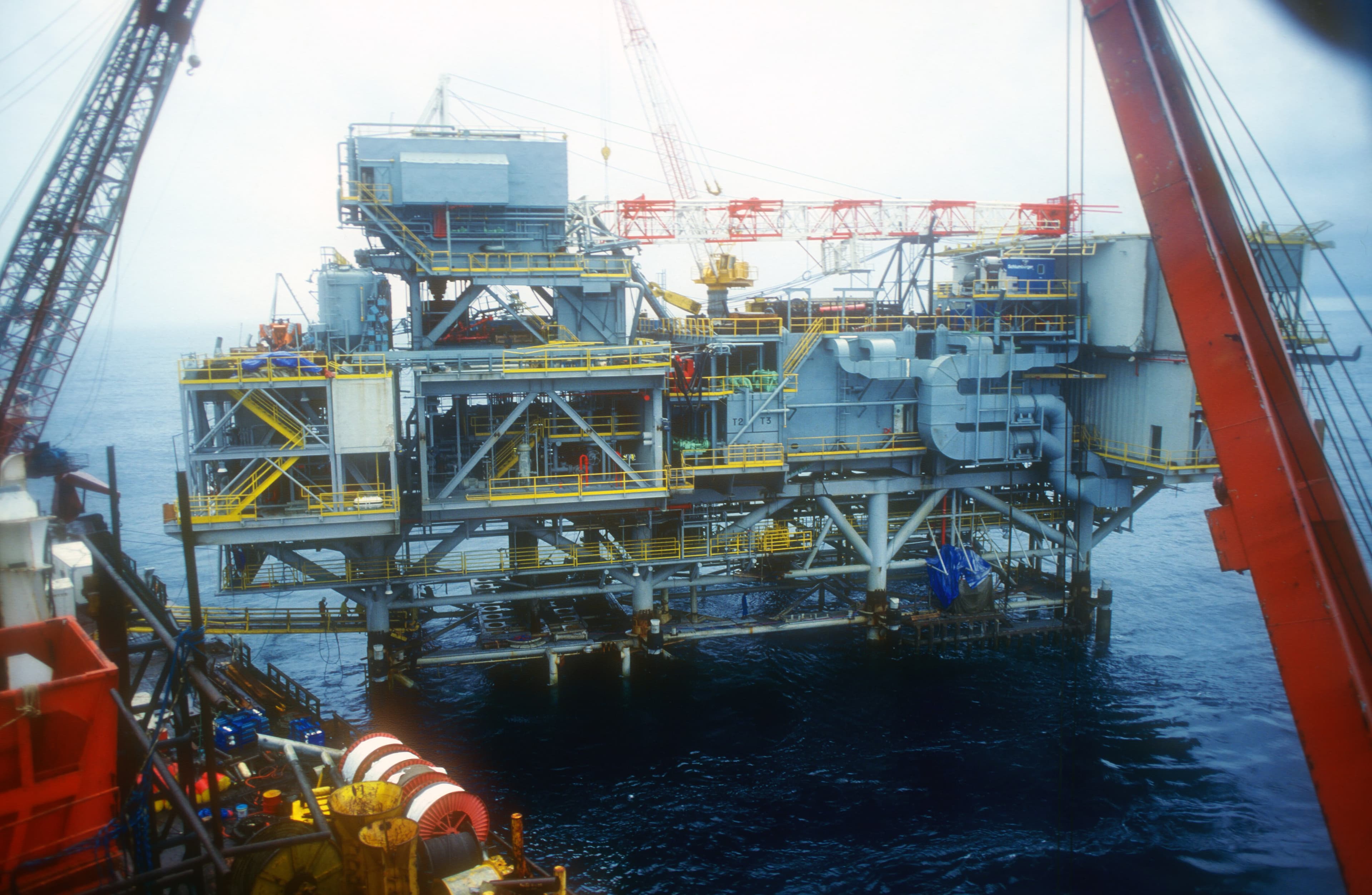
Fluor, as the managing contractor, provided engineering, procurement, and construction management to ESSO Exploration and Production Côte d’Ivoire, Inc. (ESSO). Fluor was responsible for the offshore drilling and production platform, as well as the pipeline and onshore re-separation and storage facilities. The offshore drilling and production platform includes an eight-legged steel jacket structure supporting three production modules, three drilling equipment cap bridges, and drilling rig plus living quarters and helideck.
1991
Modular approach used to fast-track the construction of North America's first MTBE Manufacturing Plant
&w=3840&q=75)
1991: Modular approach used to fast-track the construction of North America's first MTBE Manufacturing Plant
&w=3840&q=75)
Capitalizing on technology never before used anywhere in the world, Fluor performed engineering, procurement, and construction on Alberta EnviroFuels’ $360 million methyl tertiary butyl ether (MTBE) manufacturing plant. The Canadian-based plant was the first of its kind in North America. Fluor developed a fast-track execution plan using many innovations. Some of those approaches included the use of piperack modularization and erection/transport of field super modules; extensive use of precast concrete for structures; pre-dressing of major columns; shop fabrication of mall-bore piping as well as the use of 3D CAD.
1991
Fluor contracted to construct modular high temperature gas-cooled reactor fabrication facilities
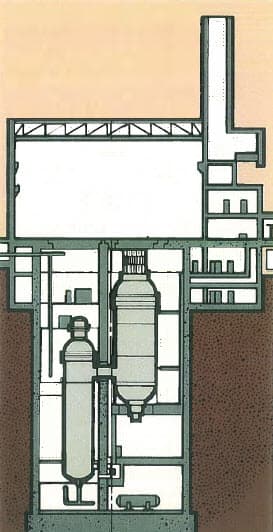
1991: Fluor contracted to construct modular high temperature gas-cooled reactor fabrication facilities
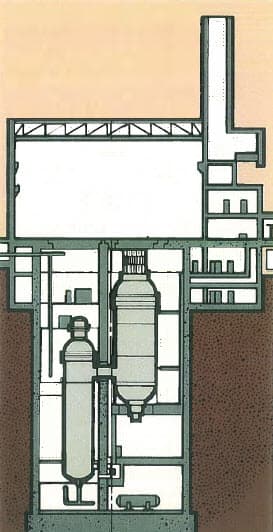
The Fuel and Target Fabrication Facilities were built to fabricate fuel and target element assemblies for use in the production of tritium via 4 modular high temperature gas-cooled reactor (MHTGR) modules. MHTGR modules were capable of providing the electrical power industry with an intrinsically safe nuclear reactor.
1993
Modular, skid mounted units installed at Valero Butane Upgrading Project in Corpus Christi, Texas
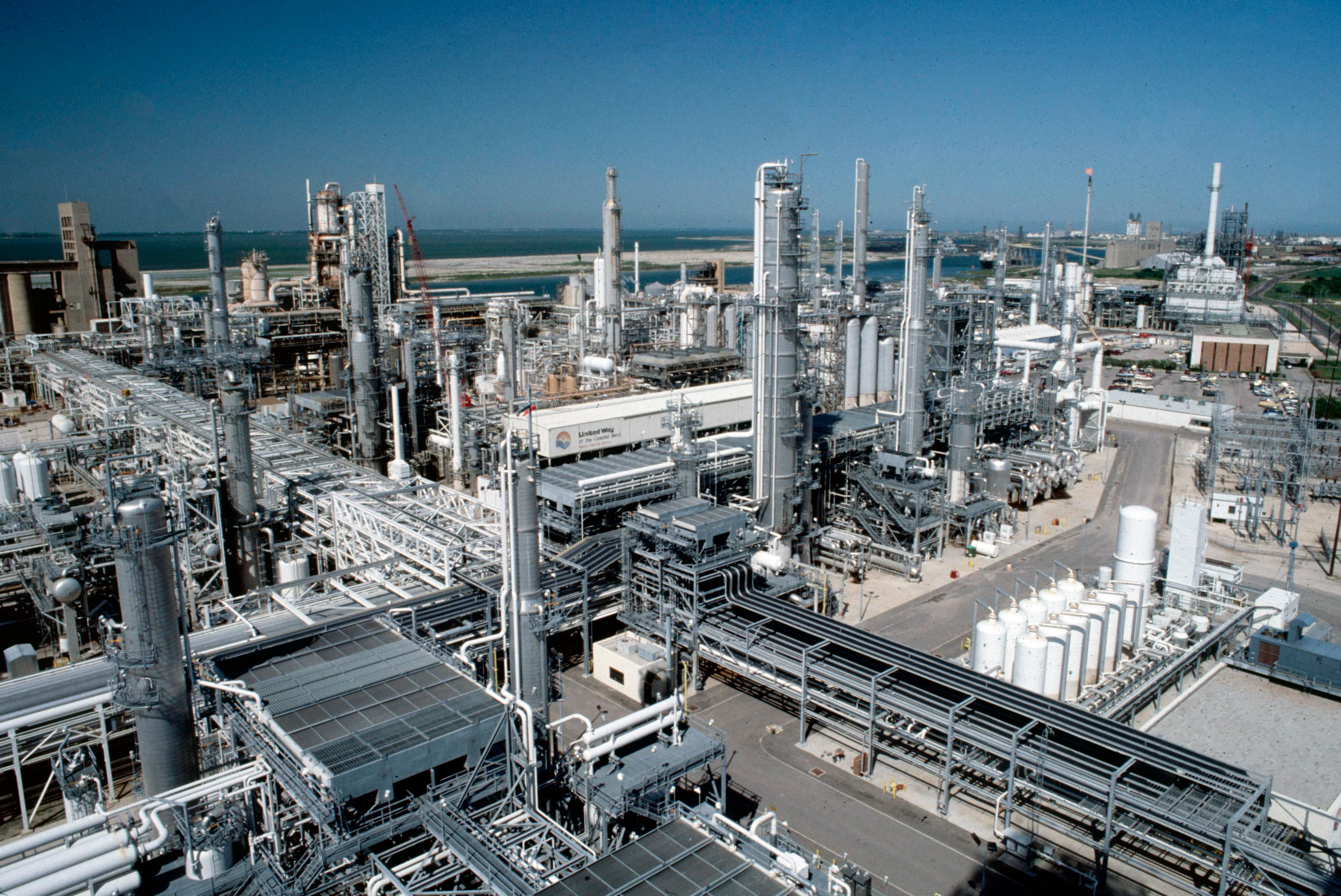
1993: Modular, skid mounted units installed at Valero Butane Upgrading Project in Corpus Christi, Texas
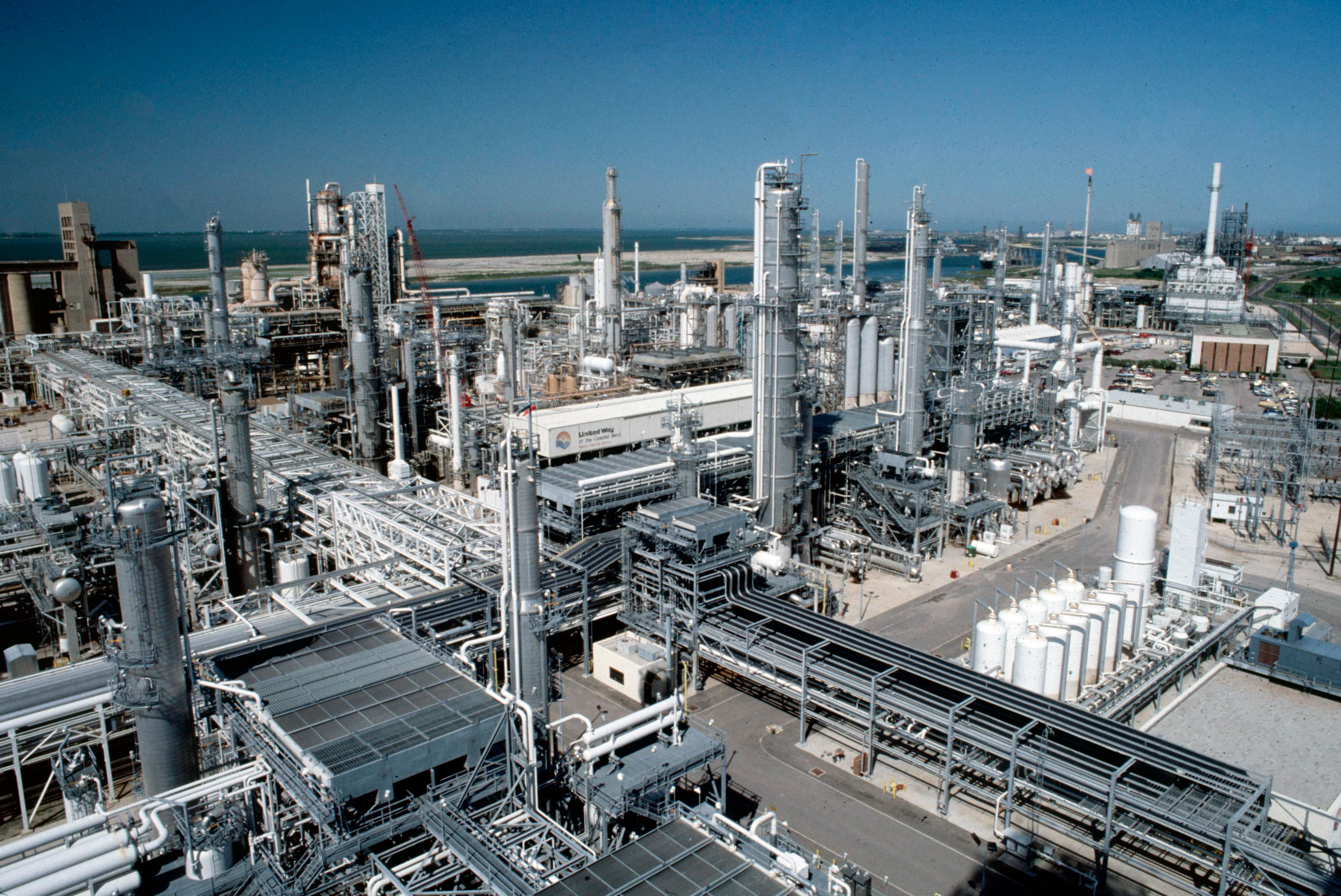
Fluor engineered, procured, and self performed-construction services on Valero's Butane Upgrading Project. The project included the installation of modular units for some of the plants major areas. The BU-PSA unit was a modular, skid-mounted unit designed by UOP to purify 17.8 MMCSFD of net gas from the Oleflex™. The Butamer™ merox unit and the Oleflex units also utilized a modular design.
1994
ARCO's management names GHX-2 modularization project "The Project of the Century"
&w=3840&q=75)
1994: ARCO's management names GHX-2 modularization project "The Project of the Century"
&w=3840&q=75)
Fluor was contracted by ARCO Alaska, Inc. to undertake a gas handling expansion operation. The operation, given the name GHX-2, was a multi-part endeavor in which specially built modules were first assembled, then shipped and brought on site. The modules were designed to facilitate the separation of gas from crude oil. Fluor built and shipped 26 modules, totaling 36,712 tons, in two sealifts from New Iberia, Louisiana to Prudhoe Bay on the northern coast of Alaska. The modules' journey then continued on land to flow stations and gathering centers on the North Slope of Alaska.
1995
DuPont Zytel® Manufacturing Facility successfully completed 9 months ahead of schedule using a modular approach
&w=3840&q=75)
1995: DuPont Zytel® Manufacturing Facility successfully completed 9 months ahead of schedule using a modular approach
&w=3840&q=75)
Fluor served as a full-service contractor providing engineering, procurement, and construction management services for this $90-million DuPont Nylon/Zytel chemical manufacturing facility. The project utilized a modular construction approach. The majority of module fabrication completed in the Philippines. Seventeen modules were used involving 65 percent of the construction, the largest being the continuous polymerization module that weighed 2,000 metric tons. Once completed, the modules were shipped to Pulau Sakra Island for final installation. The modularized approach saved the client approximately 10 percent of total installed cost.
1996
Modular construction used to complete Shell Gabon Oil & Gas Processing Facilities Expansion
&w=3840&q=75)
1996: Modular construction used to complete Shell Gabon Oil & Gas Processing Facilities Expansion
&w=3840&q=75)
Fluor and Shell Gabon S.A. worked together as an integrated team throughout engineering and design to minimize the impact on existing production and to ensure that all activities were achieved. As a result of the collaboration, Fluor implemented a modular construction approach with most of the modules fabricated and tested in Europe prior to shipment to the site in Gabon. The approach reduced the number of people required on the site and reduced the amount of time spent at the facility.
1996
NAM F3 Topsides offshore production platform installed
&w=3840&q=75)
1996: NAM F3 Topsides offshore production platform installed
&w=3840&q=75)
The F3 field, located in the Dutch Sector of the North Sea, was constructed using a combination concrete gravity structure and a single-lift production deck. Fluor was contracted to perform detailed design, engineering, procurement, and fabrication management assistance on the F3 Topsides project.
1997
Statoil Gas Terminal and Methanol Project maximizes practical modularization approach
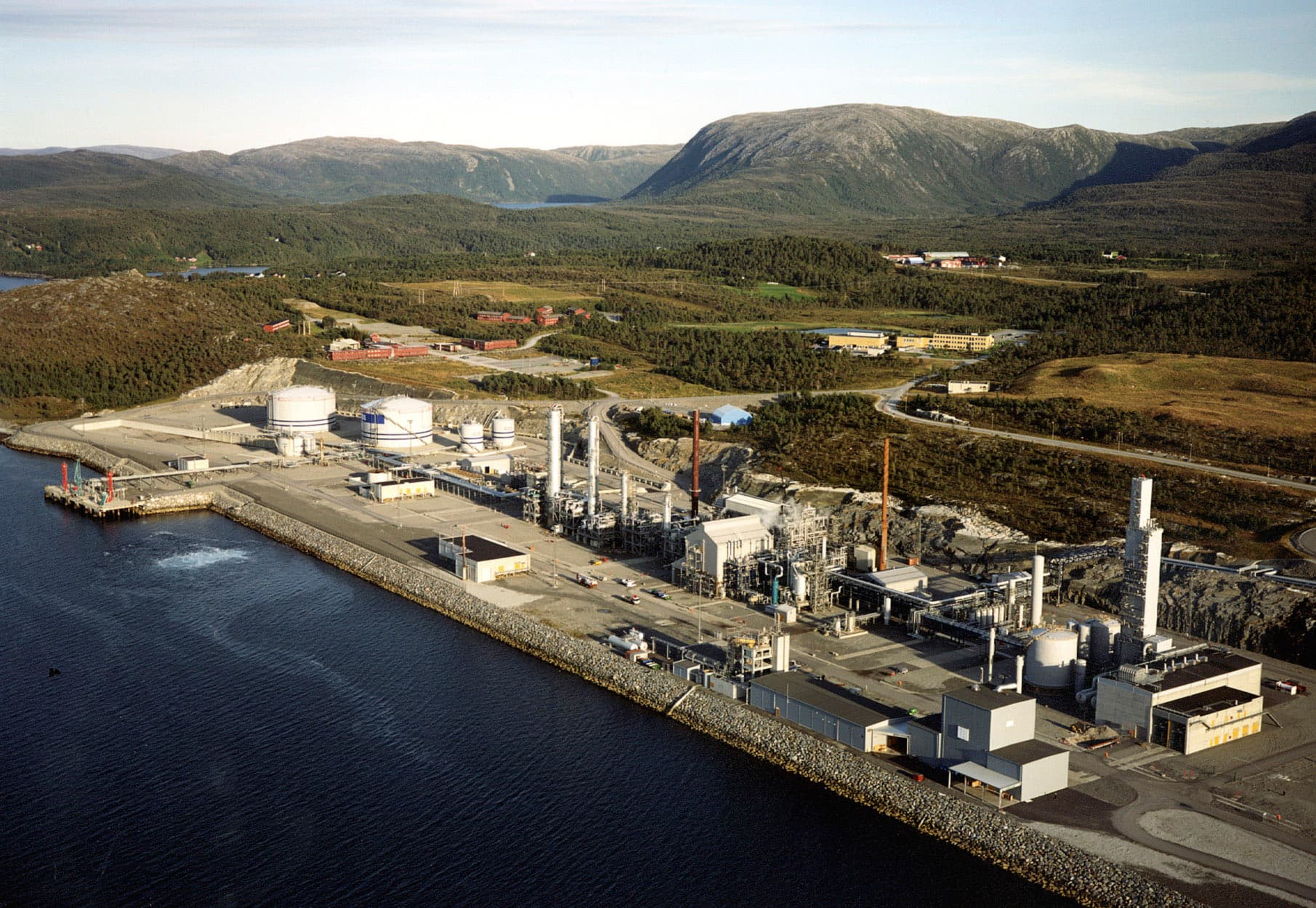
1997: Statoil Gas Terminal and Methanol Project maximizes practical modularization approach
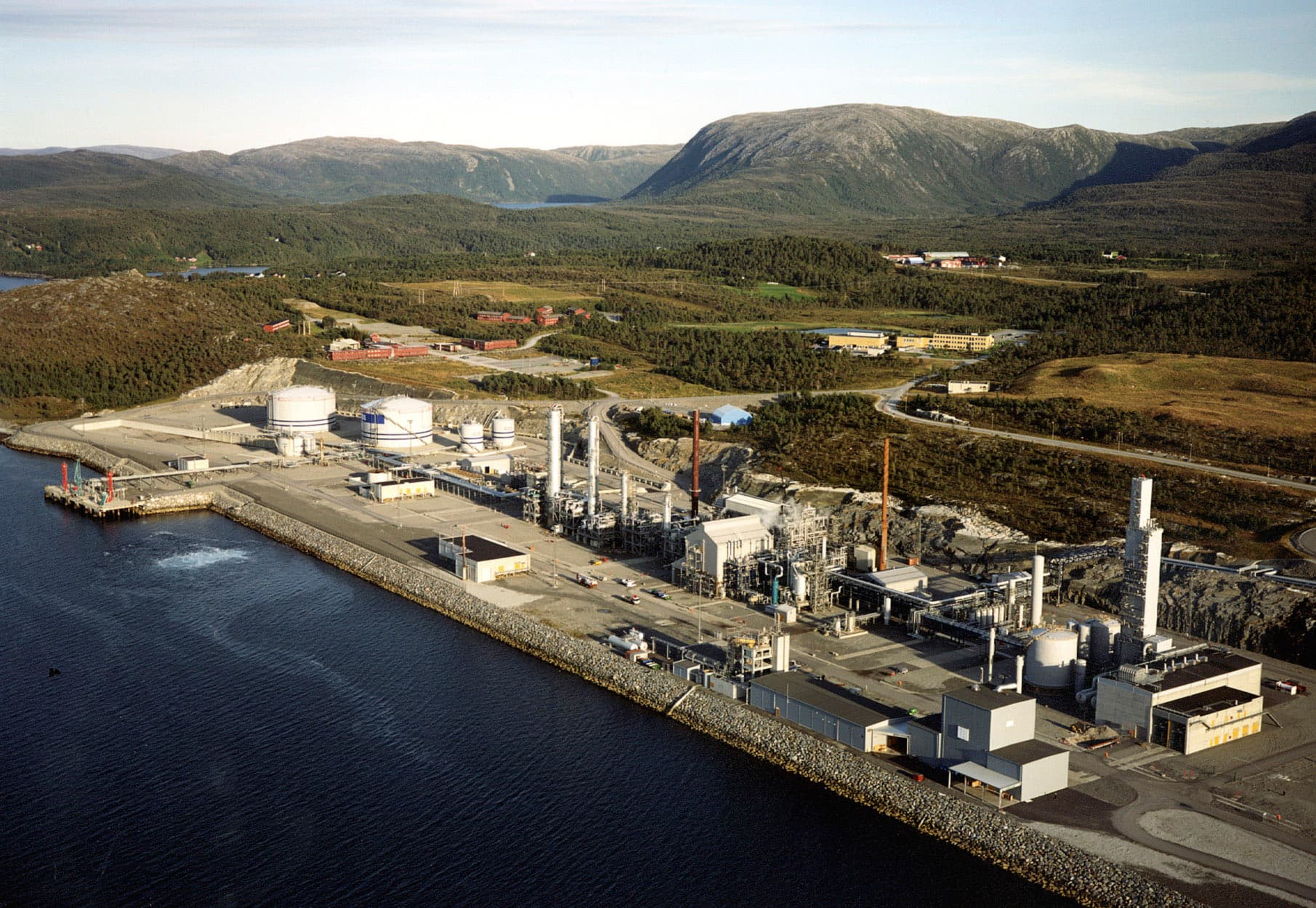
Completed in 1997, the Statoil Gas Terminal and Methanol project consisted of 8 pre-assembled units and 13 pre-assembled racks. Modularization was maximized on this project to improve the project schedule, reduce costs, and reduce peak labor at site. The fabrication yards were located in Haugesund and Averoy, Norway; and the modules were transported to Tjeldbergodden, Norway for installation.
2000s
Fluor continues to use modular construction on large projects.
2000
Bleo Holm FPSO process facility commissioned
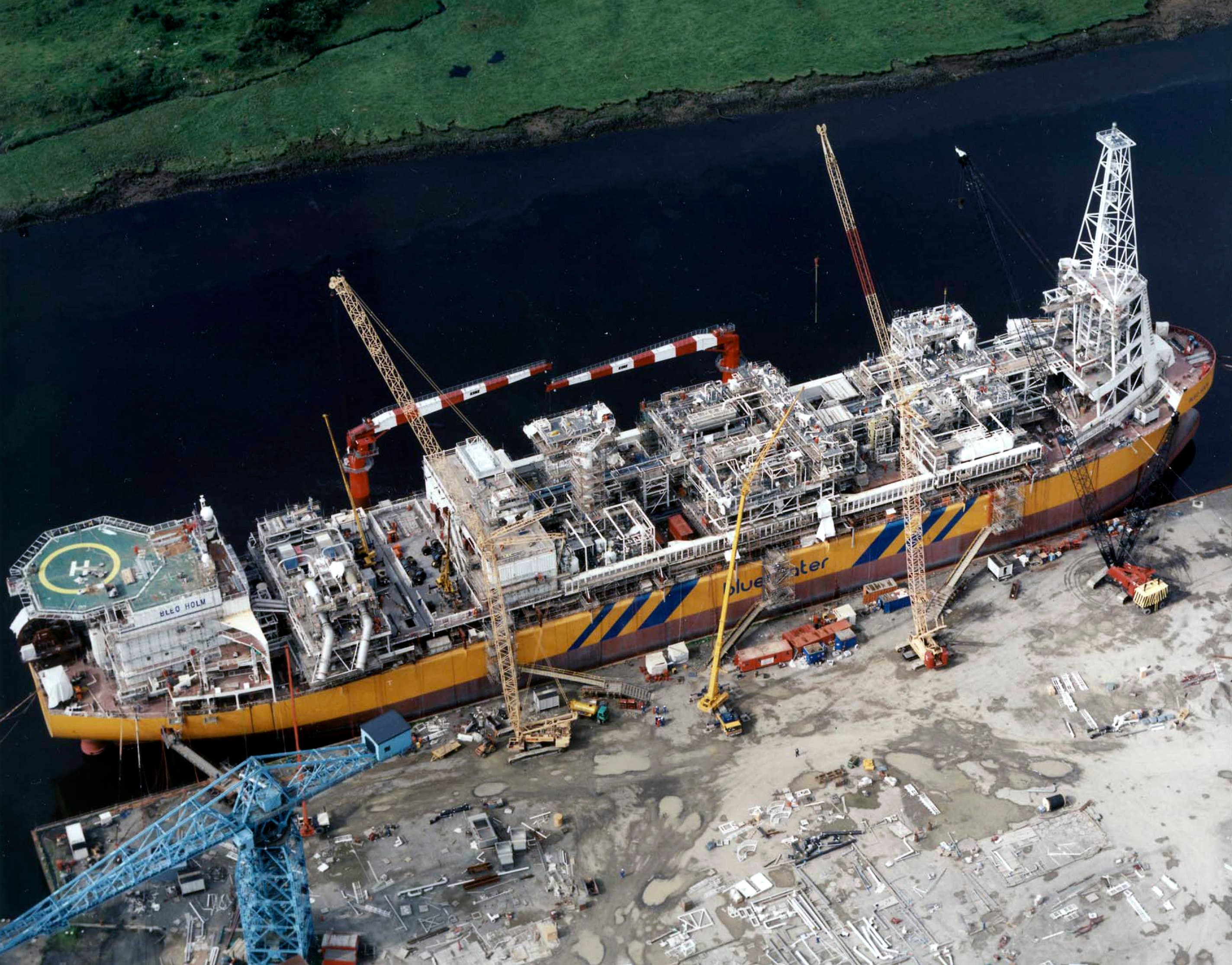
2000: Bleo Holm FPSO process facility commissioned
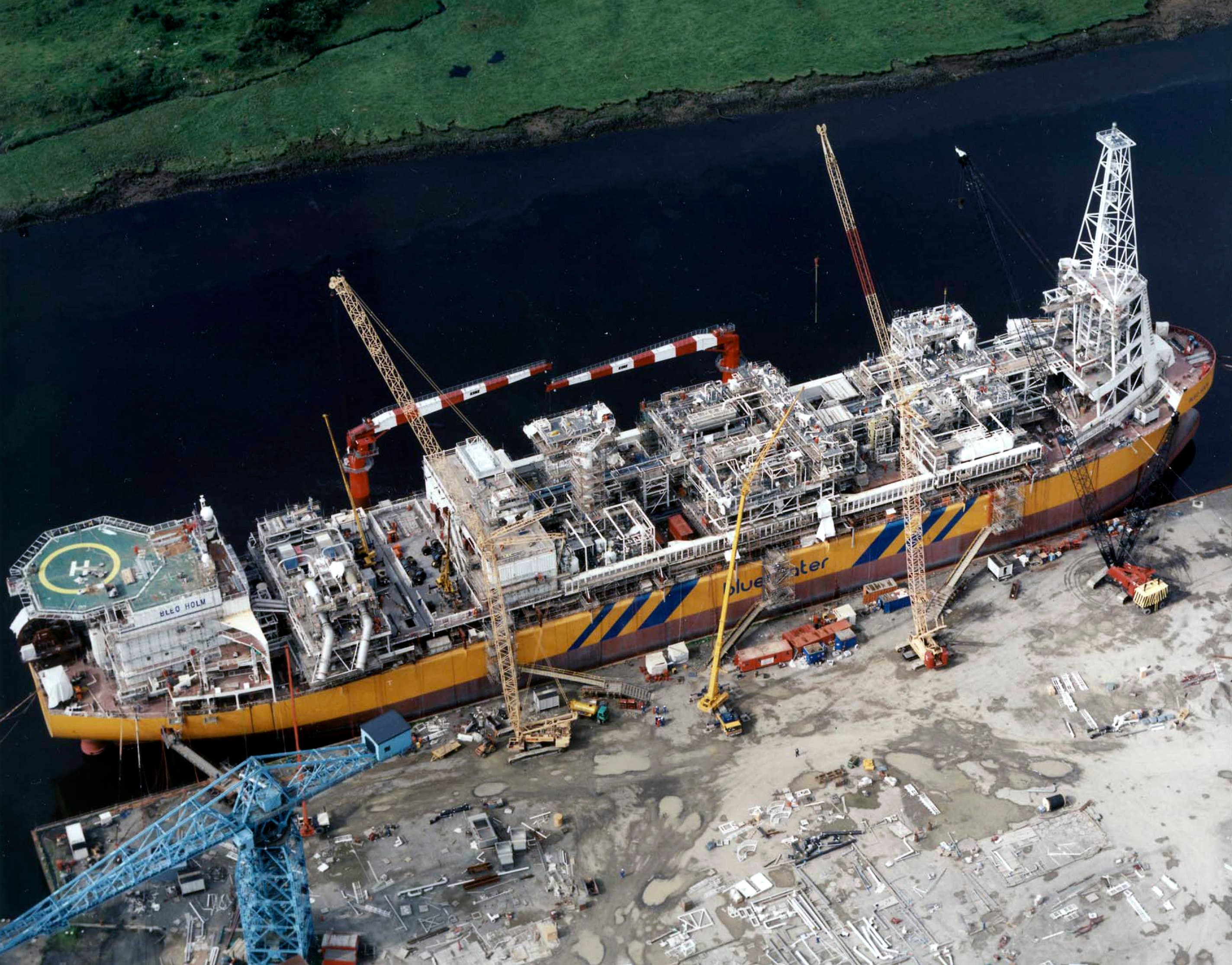
Fluor, in a joint venture with United Industrial Enterprise, performed engineering, procurement, and construction of the floating production storage and offloading (FPSO) process facility storage and offloading unit for Bluewater Engineering, B.V. The project required a modular construction approach in order to meet the demanding, fast-track schedule. The processing facility was completed in just 22 months.
2000
Modularization helps the BP Clean Fuels Project achieve an aggressive schedule
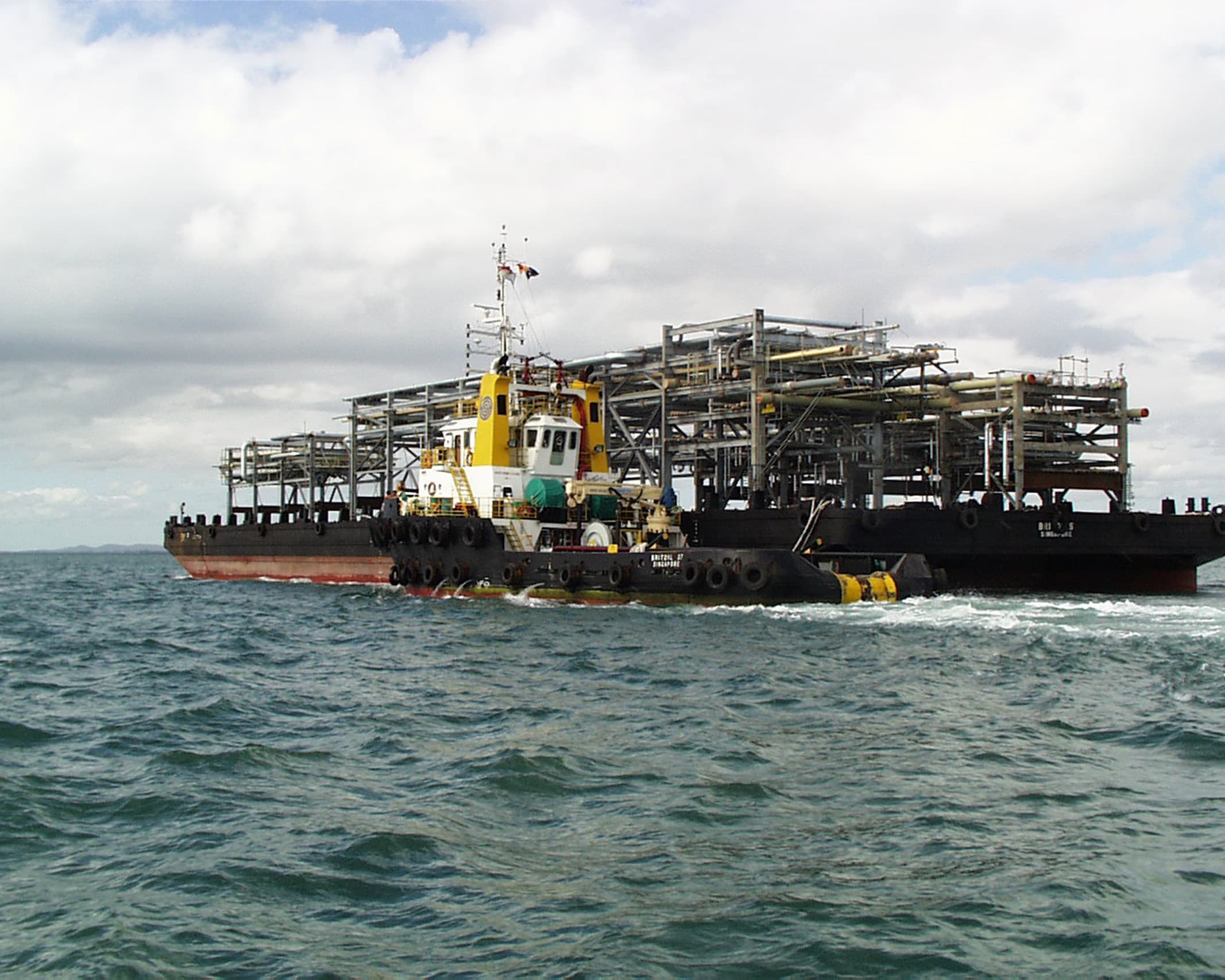
2000: Modularization helps the BP Clean Fuels Project achieve an aggressive schedule
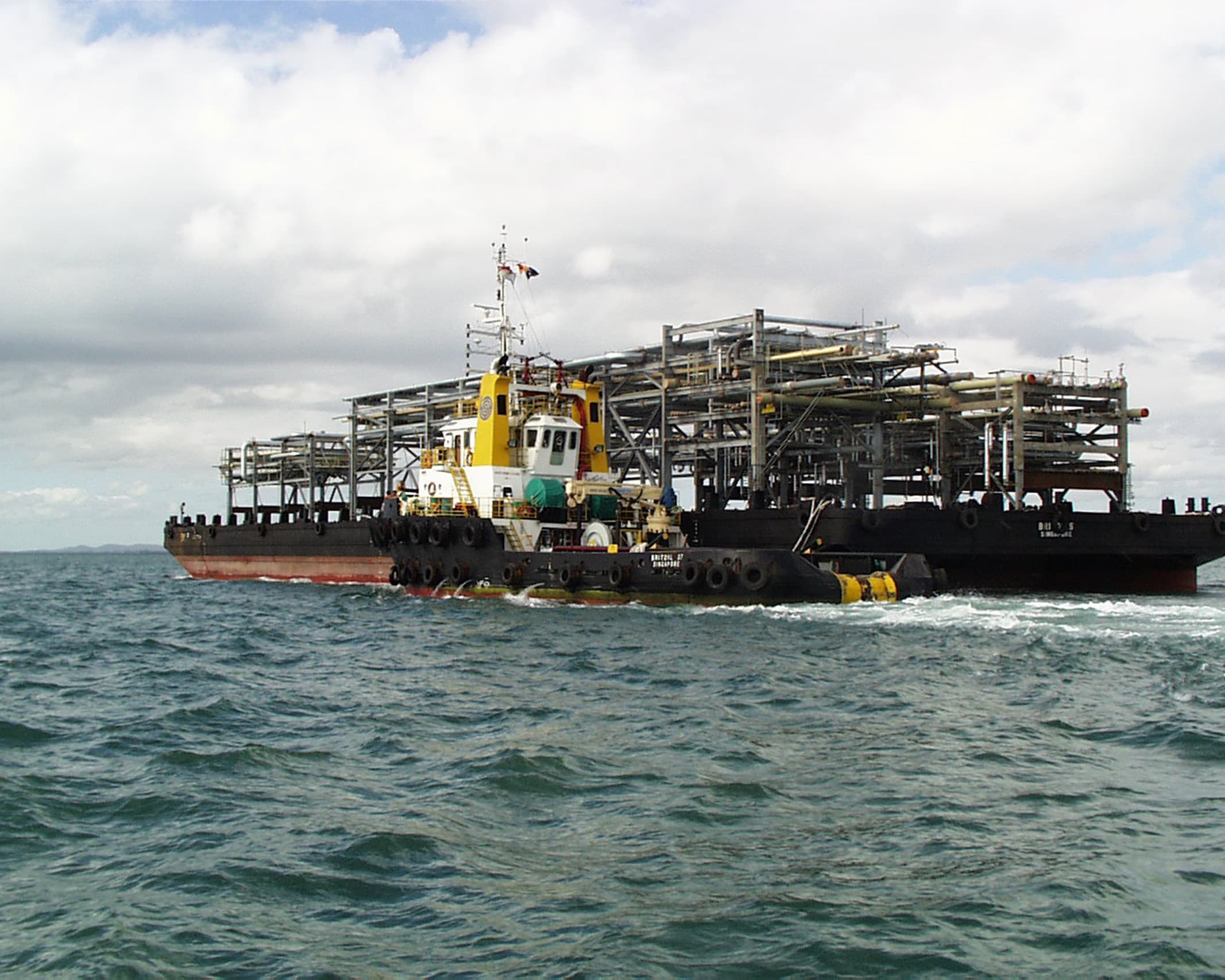
Fluor was one of several companies forming a unique alliance with BP, enabling it to play its part in the Southeast Queensland Regional Air Quality Strategy. As part of the project alliance, Fluor called on the experience of its experts in Calgary, Canada, who had completed many similar hydrocrackers. The alliance proved to be a great success: the parties worked together to modularize the construction and made plans early in the project for shipping and heavy lifting of the modules, installation, and commissioning.
2002
One hundred and twenty modules installed at Muskeg River Oil Sands Project
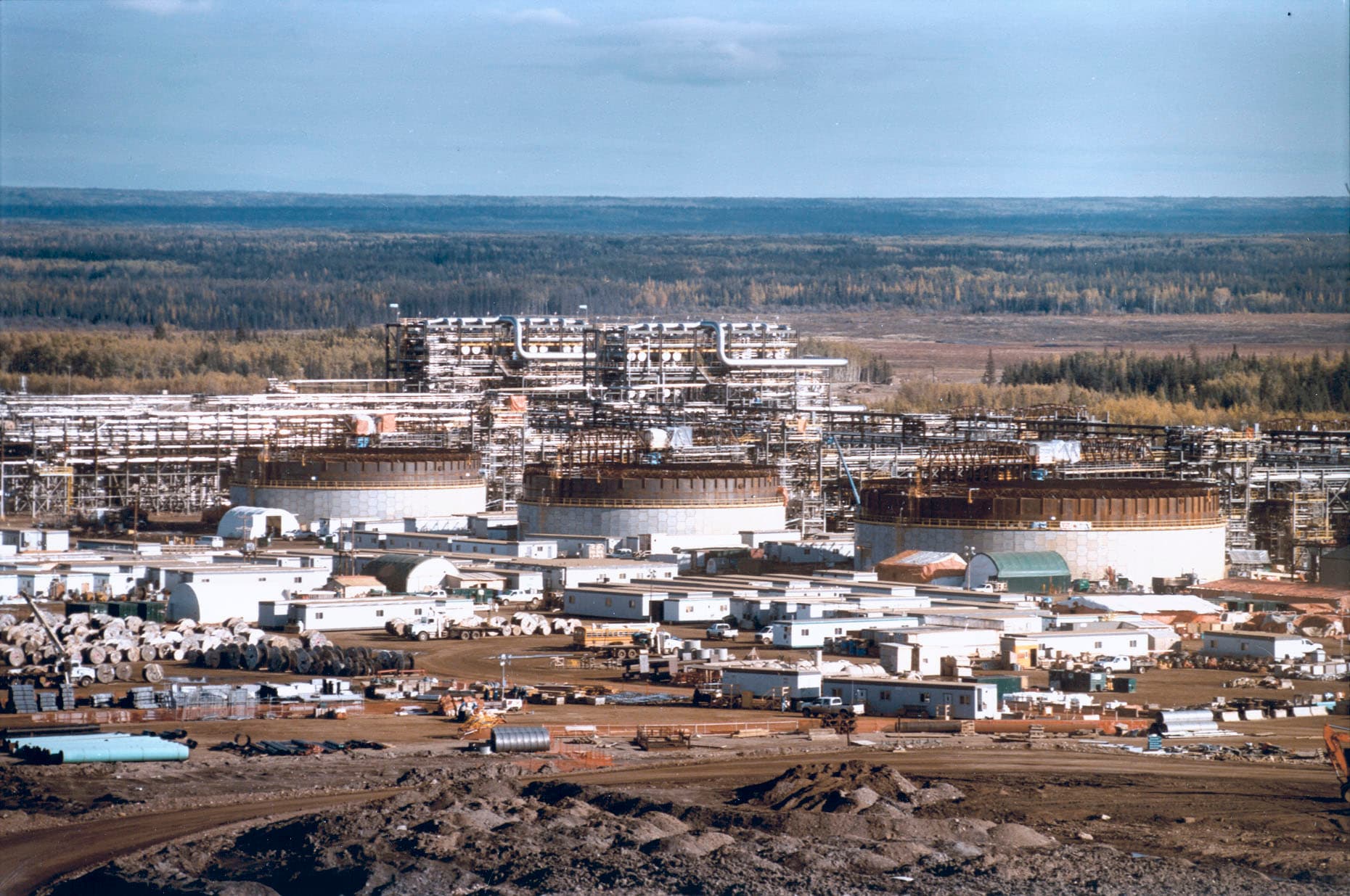
2002: One hundred and twenty modules installed at Muskeg River Oil Sands Project
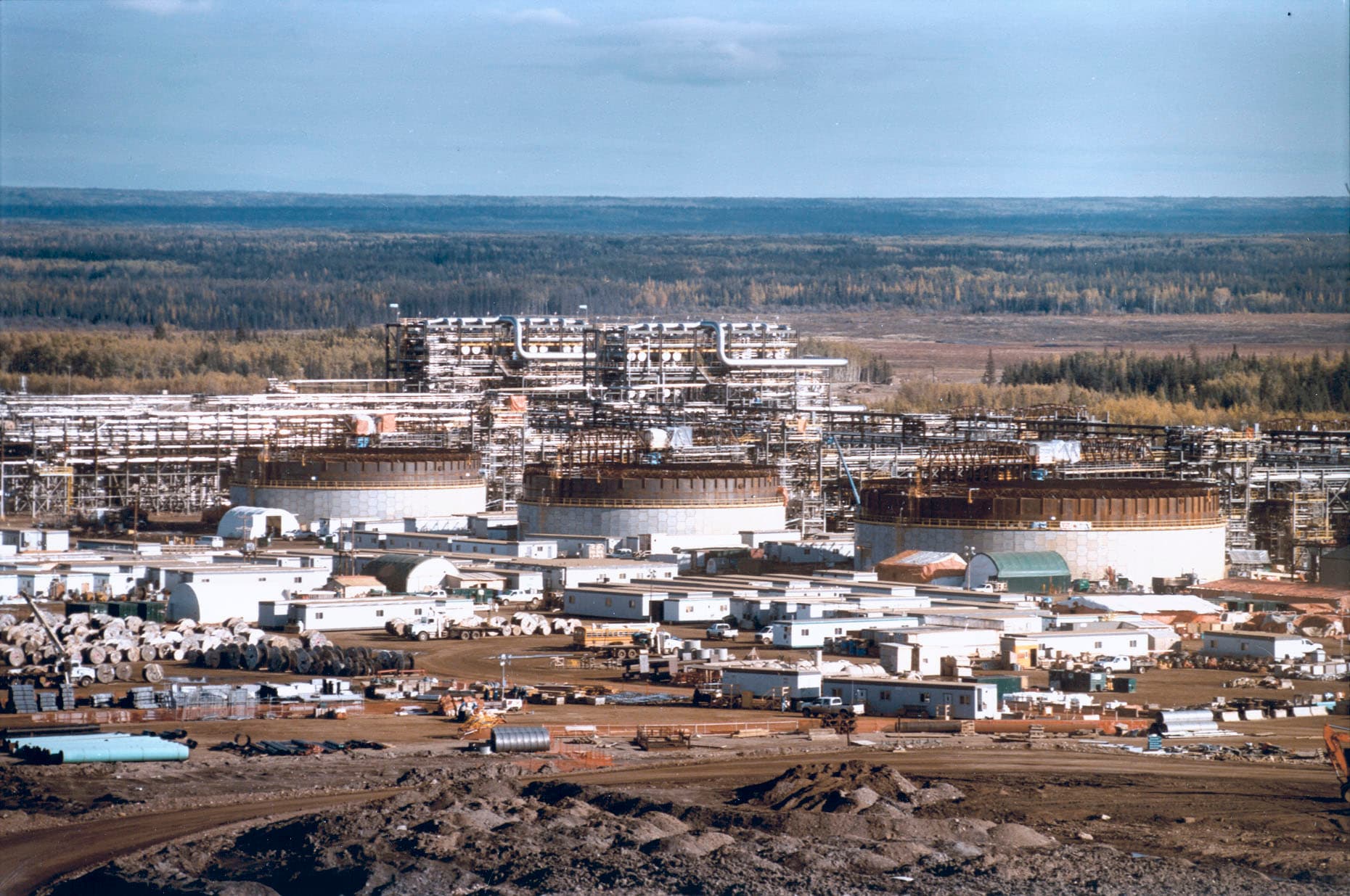
Fluor performed engineering, procurement, construction, and maintenance services for the Muskeg River Oil Sands Mine constructed as part of the Athabasca Oil Sands project. The project was designed to produce 155,000 barrels per day of bitumen. Production began in late 2002 and will continue for approximately 30 years.
2003
ICA Fluor acquires Industria del Hierro Fabrication and Module Yards in Tampico, Mexico
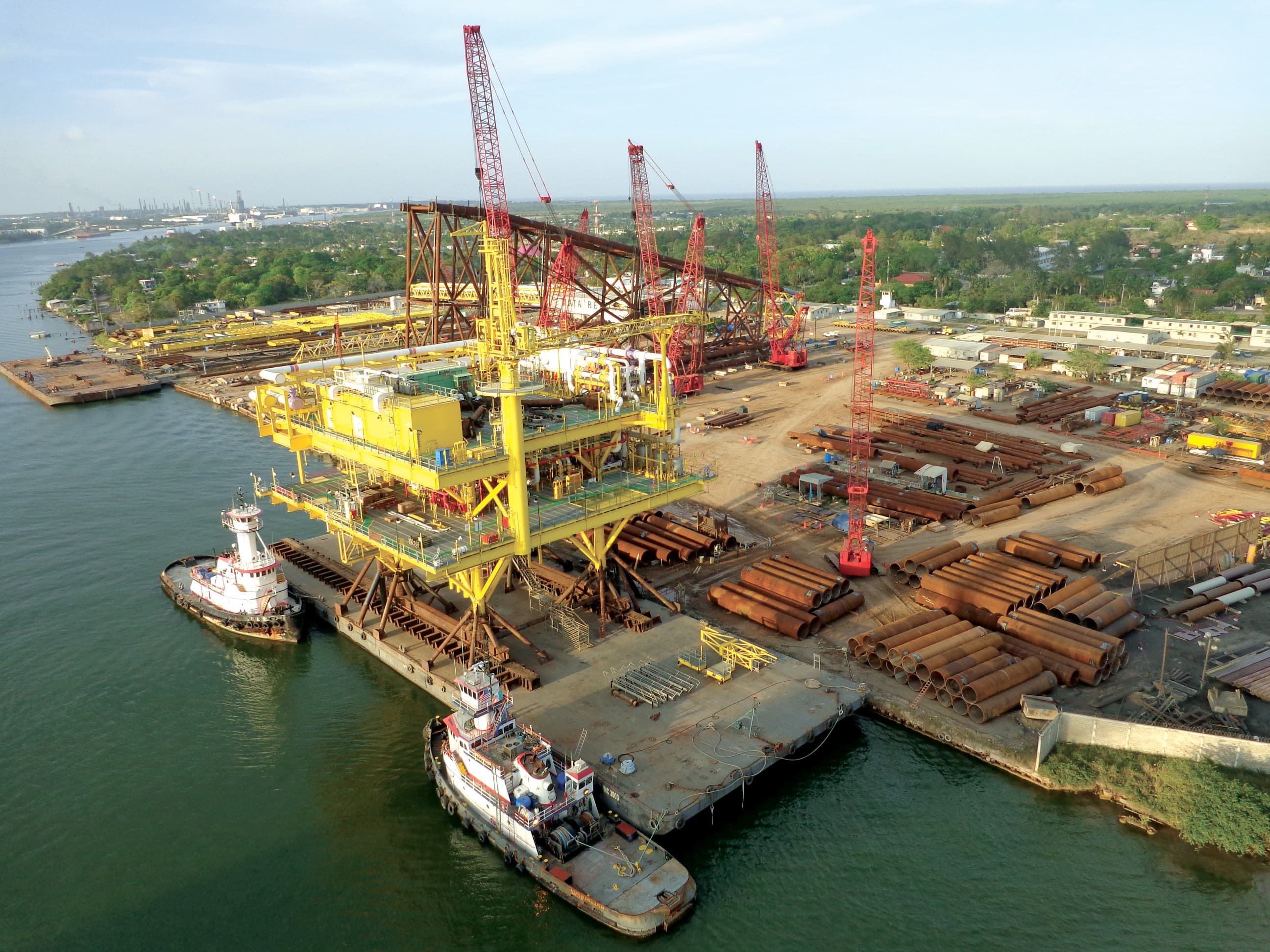
2003: ICA Fluor acquires Industria del Hierro Fabrication and Module Yards in Tampico, Mexico
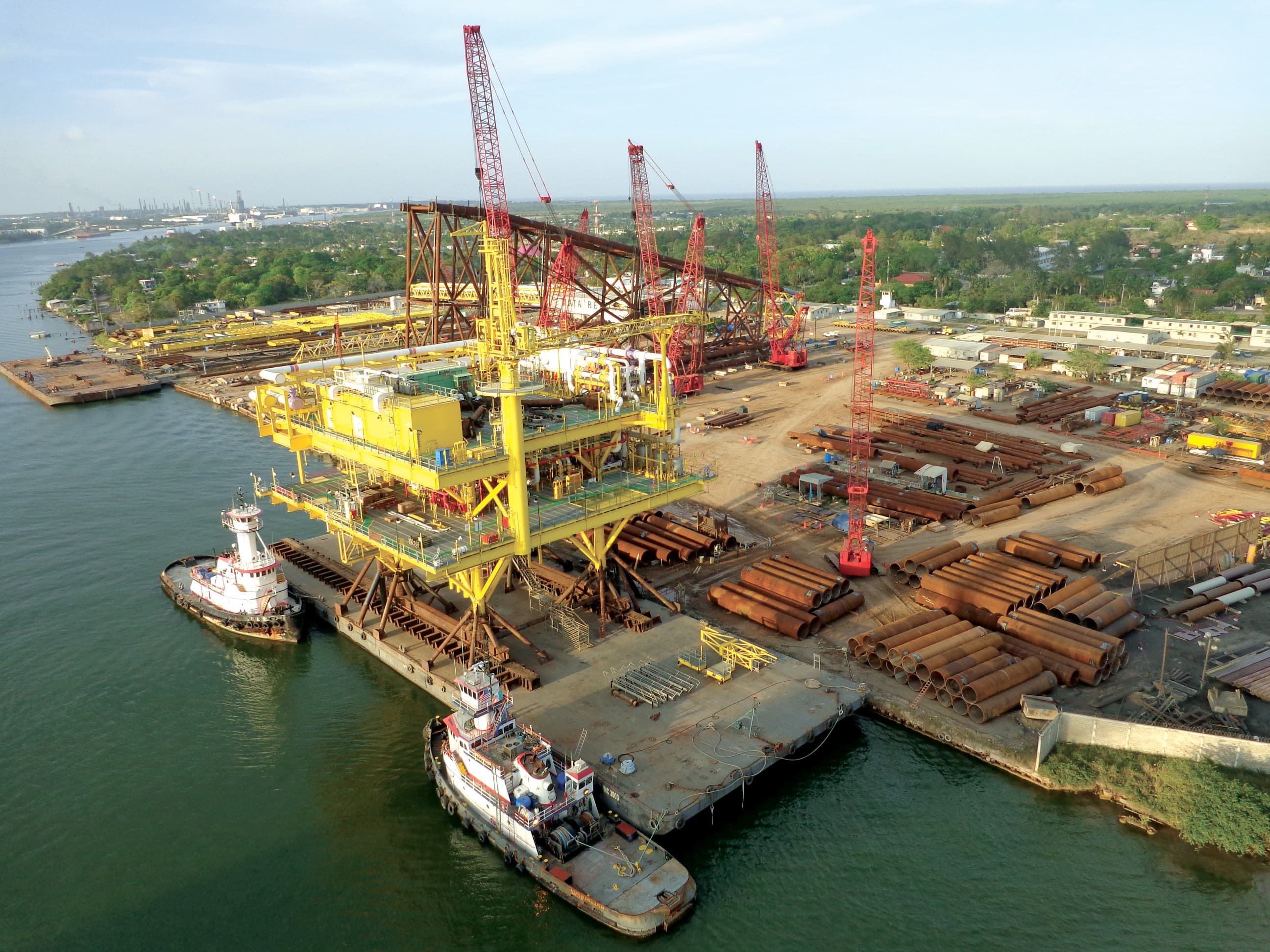
In 2003, Fluor acquired Industria del Hierro's two fabrication yards, Mata Redonda and El Empalme, in Tampico, Mexico. With a combined capacity of 45,000 MTs per year, the fabrication facilities can support pipe racks, offshore platforms, and process module fabrication. The joint venture has a large, qualified workforce and has one of the largest crane fleets in the Gulf Coast region.
2005
Modular barracks constructed for U.S. Army Corps of Engineers in the Middle East
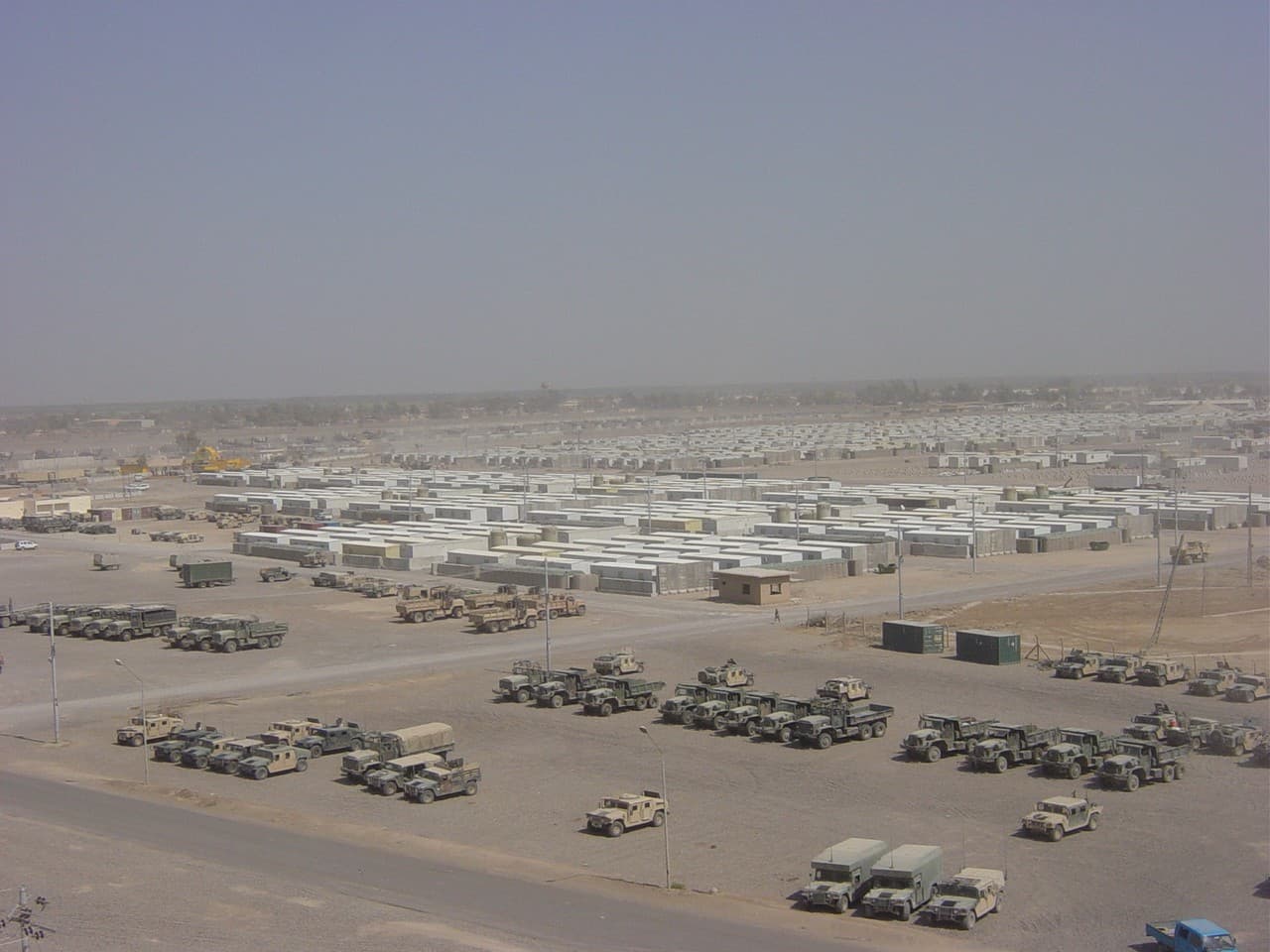
2005: Modular barracks constructed for U.S. Army Corps of Engineers in the Middle East
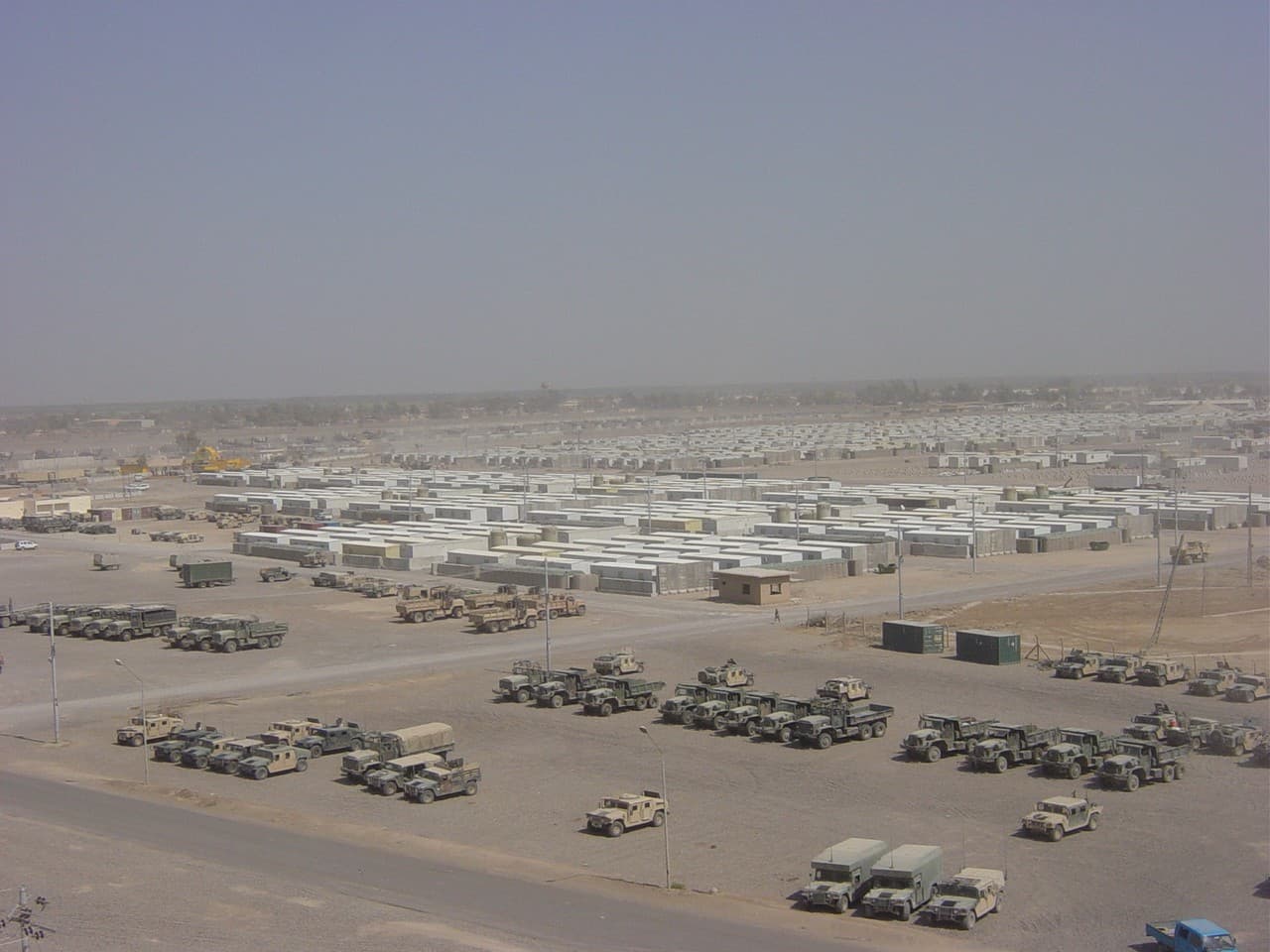
After successfully completing CETAC I, Fluor was awarded CETAC II by the U.S. Army Corps of Engineers to provide planning, design-build, general construction, renovation and repairs, life support services, and operations and maintenance to the military in a 25-country Area of Responsibility.
2008
Biogen Idec Large Scale Manufacturing Facility is the first life sciences project in the U.S. to use a modular construction approach
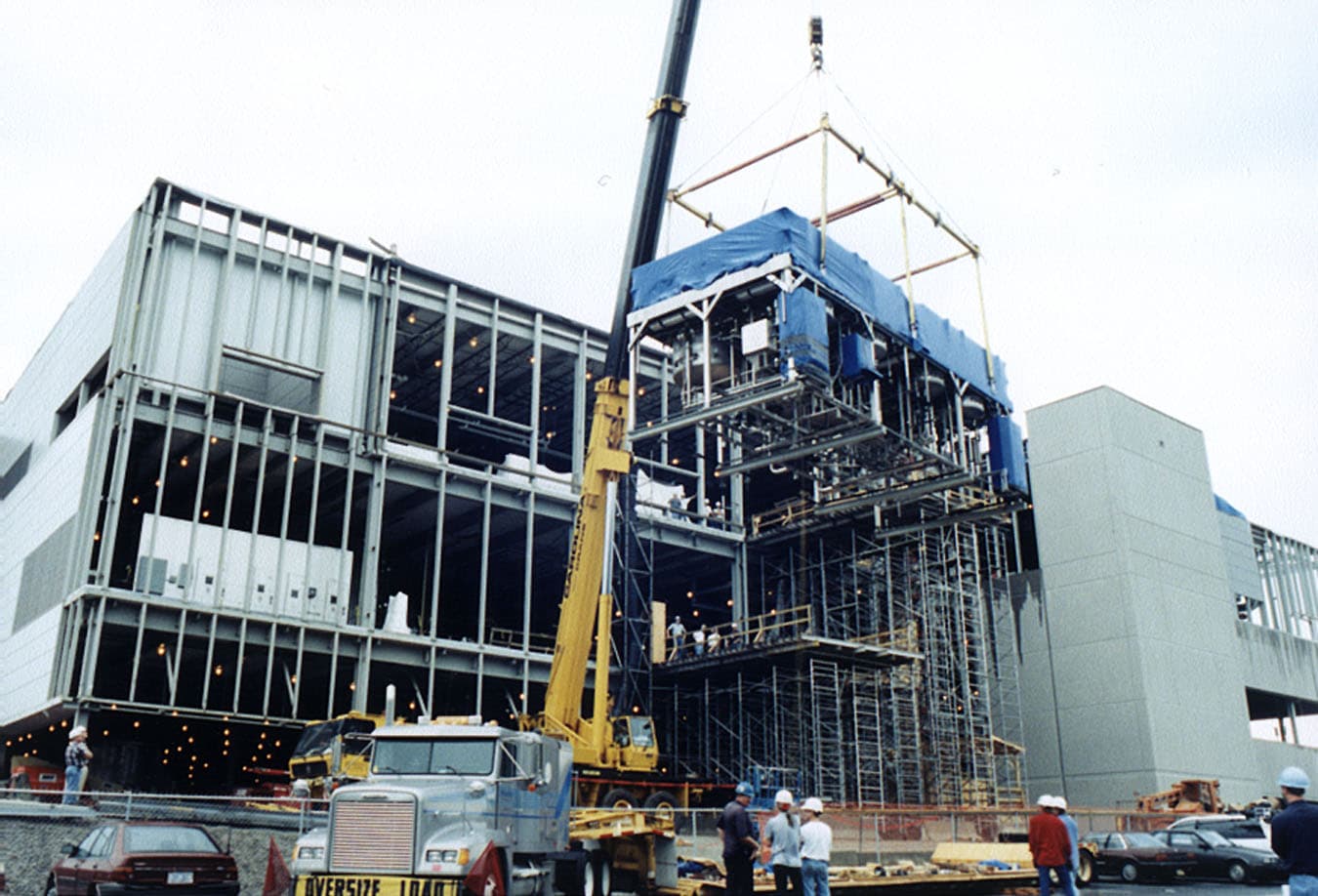
2008: Biogen Idec Large Scale Manufacturing Facility is the first life sciences project in the U.S. to use a modular construction approach
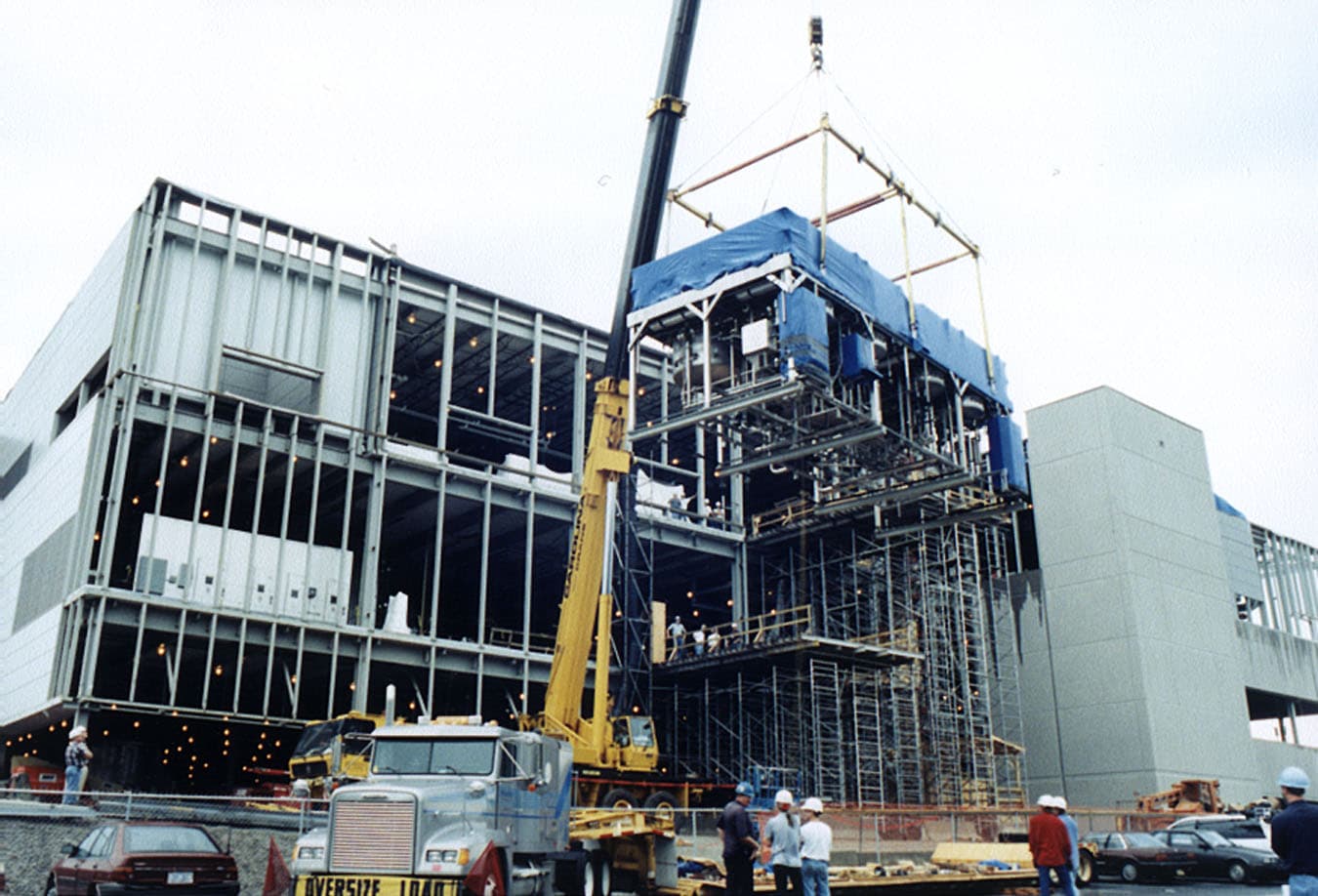
Fluor provided conceptual design, engineering, procurement, construction management, and validation services to Biogen Idec for the company’s Large Scale Manufacturing (LSM). The use of modular construction for the LSM facility was a first in the biotech industry. The modules had to meet the FDA’s Current Good Manufacturing Practices, and Fluor implemented stringent methodologies for coordination and management during module design, fabrication, and delivery.
2008
Topside module design exemplifies innovative engineering for offshore industry
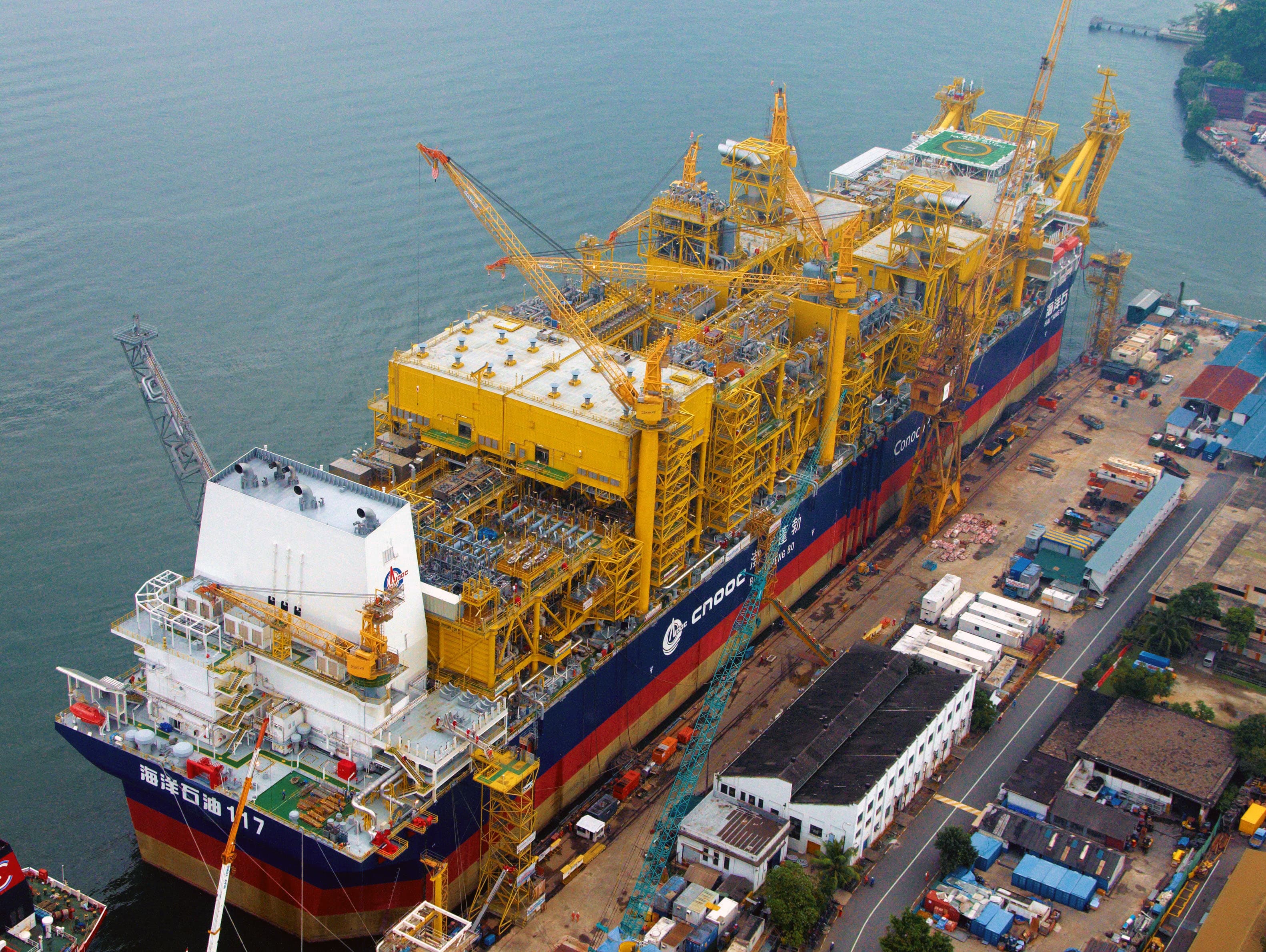
2008: Topside module design exemplifies innovative engineering for offshore industry
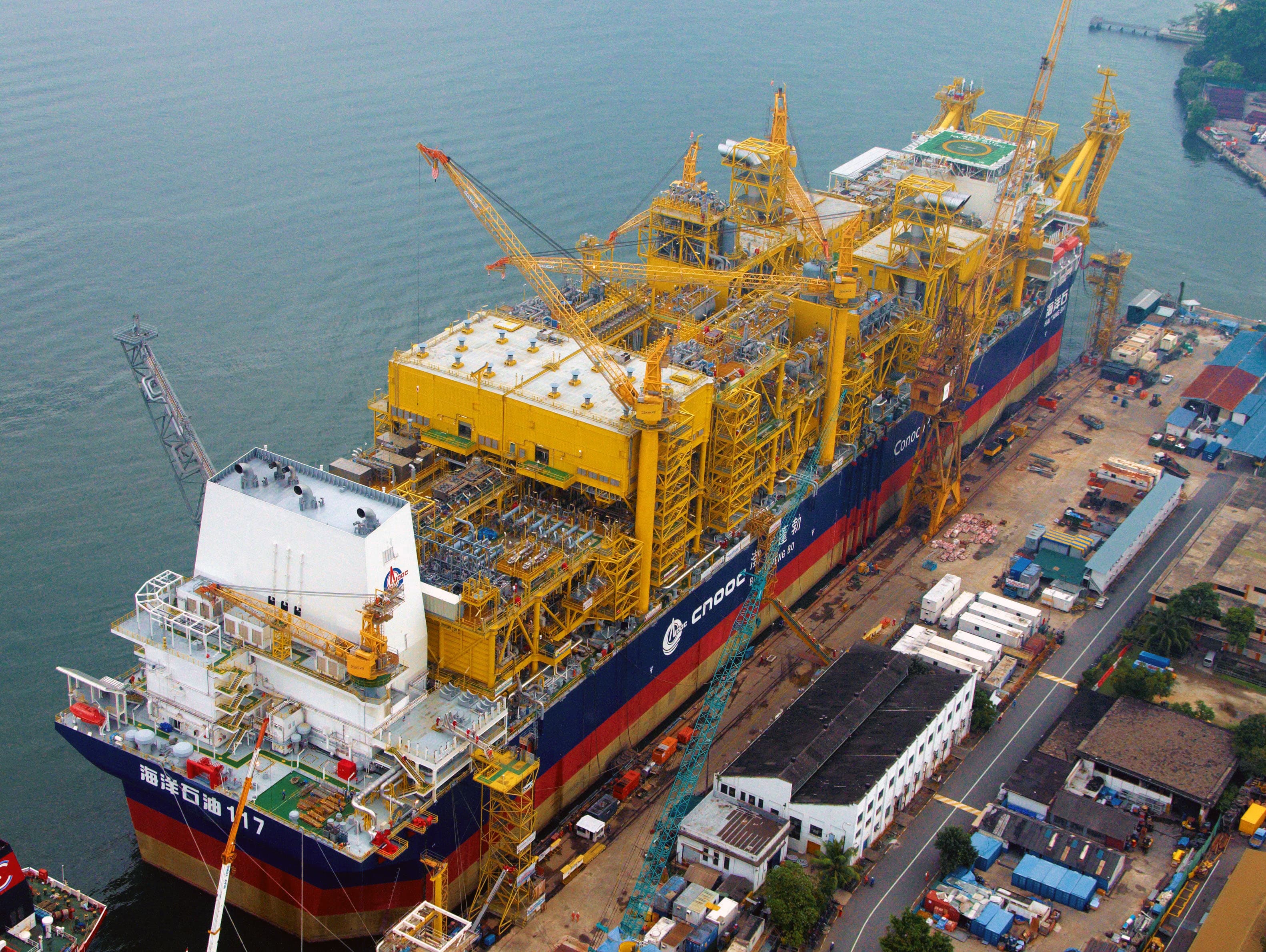
Fluor assisted ConocoPhillips China, Inc. develop the largest offshore oil production facility in Bohai Bay, China. The full field development project included six remote wellhead platforms, central riser/utilities platform, and double-hull floating production storage and offloading (FPSO) system. For the FPSO topside modules, Fluor used state-of-the-art spectral fatigue analysis to calculate the stress concentration factors on critical structural connections. Fluor also designed flexible elastomeric bearings to rest the modules on the hull supports, a simpler design pioneered by Fluor for FPSOs that avoids the precision machining and exotic materials of traditional friction pendulums or bearing pots.
2010s
Fluor's investment in modular construction increases.
2010
Cost-saving modularization strategies at Total's Port Arthur refinery succeed
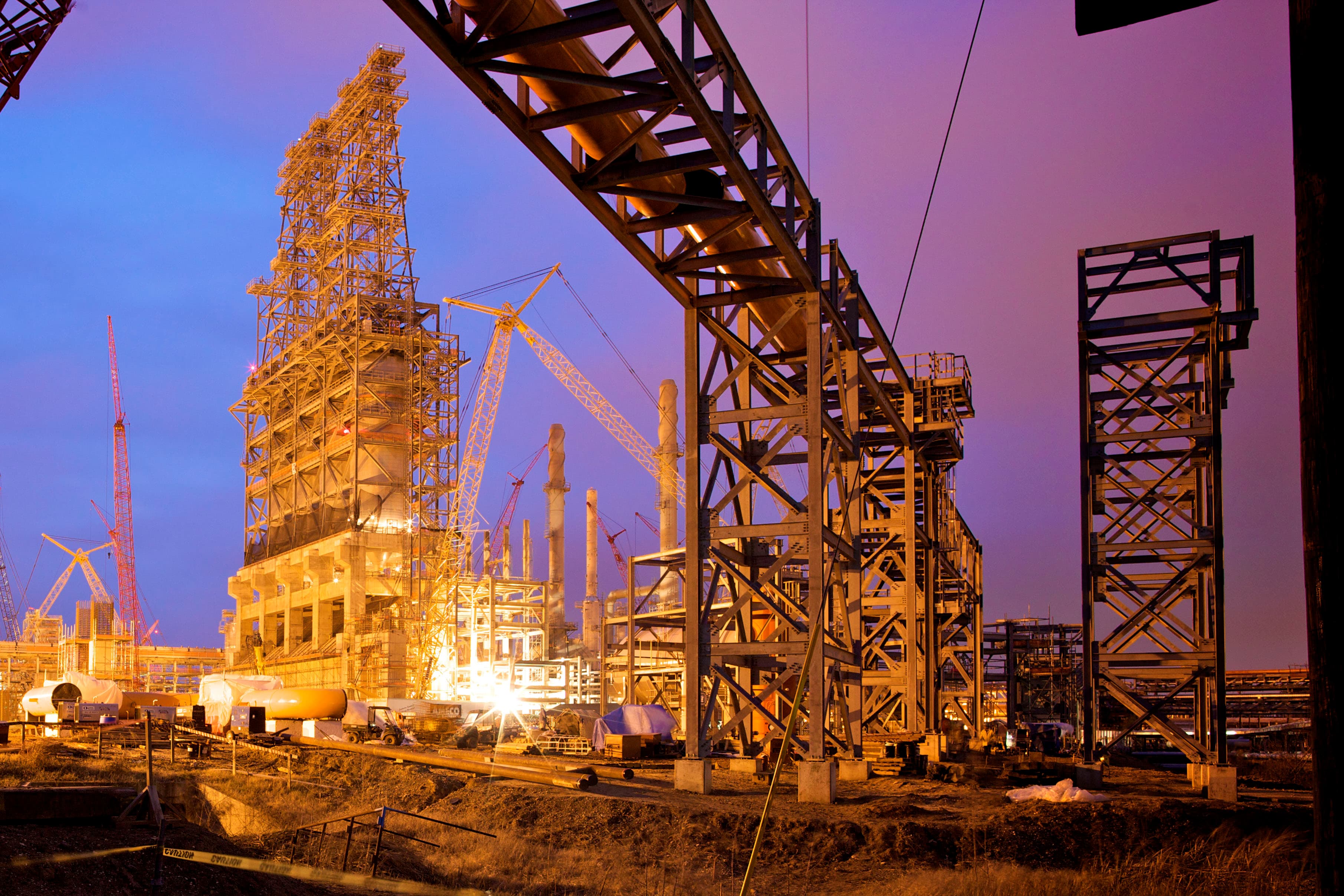
2010: Cost-saving modularization strategies at Total's Port Arthur refinery succeed
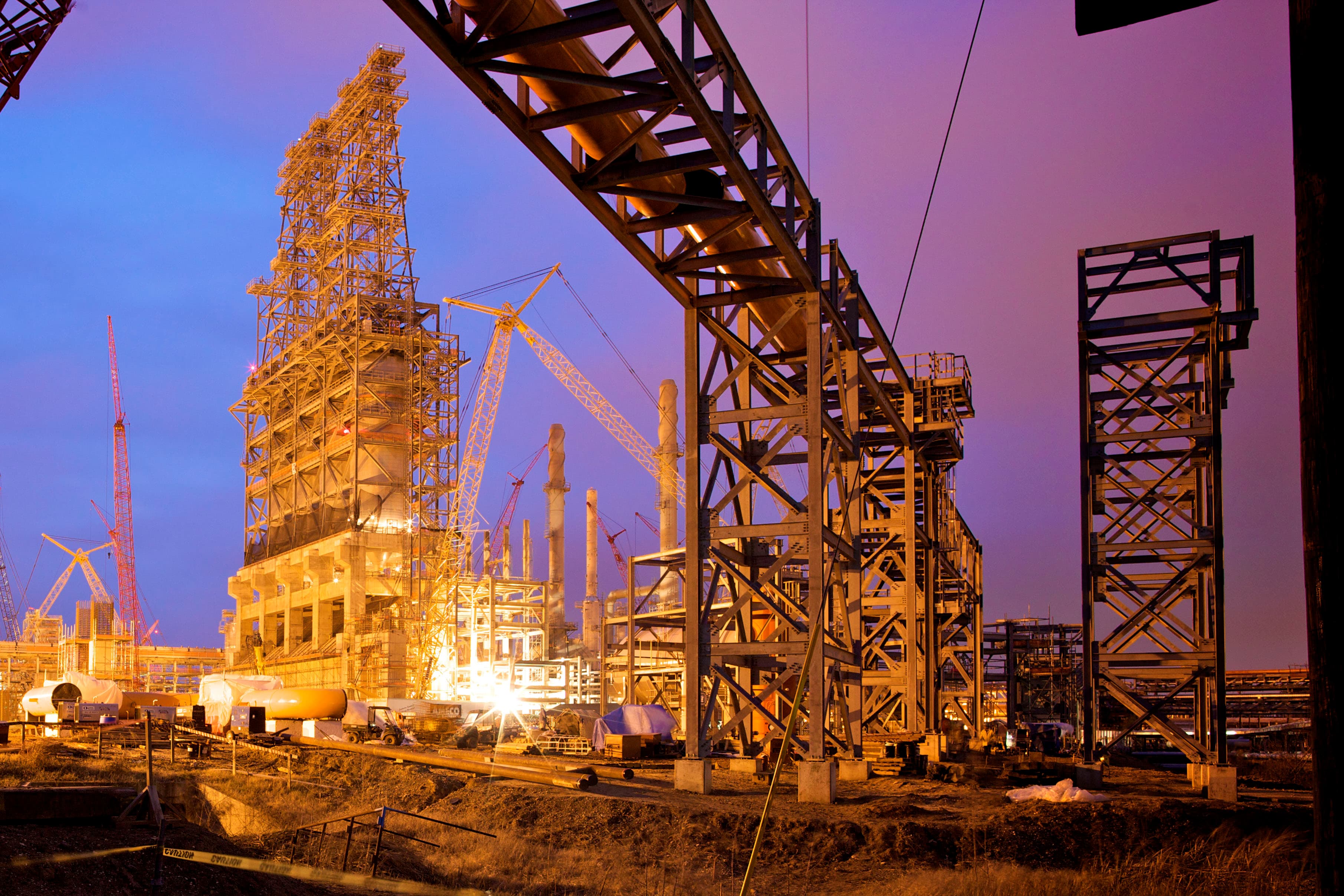
Fluor provided comprehensive services to Total for its refinery upgrade and modification in Port Arthur. Services included the initial feasibility study through commissioning support. The project was carried out to add flexibility to process heavy sour crudes into cleaner burning fuels for the U.S. market.
Fluor drove many cost-saving measures and strategies to achieve success. These included modularization of interconnecting pipe racks, worksharing, and strategic partnerships with contractors and suppliers.
2011
Integrated solar modules installed at Iberdrola Copper Crossing Solar Power Plant
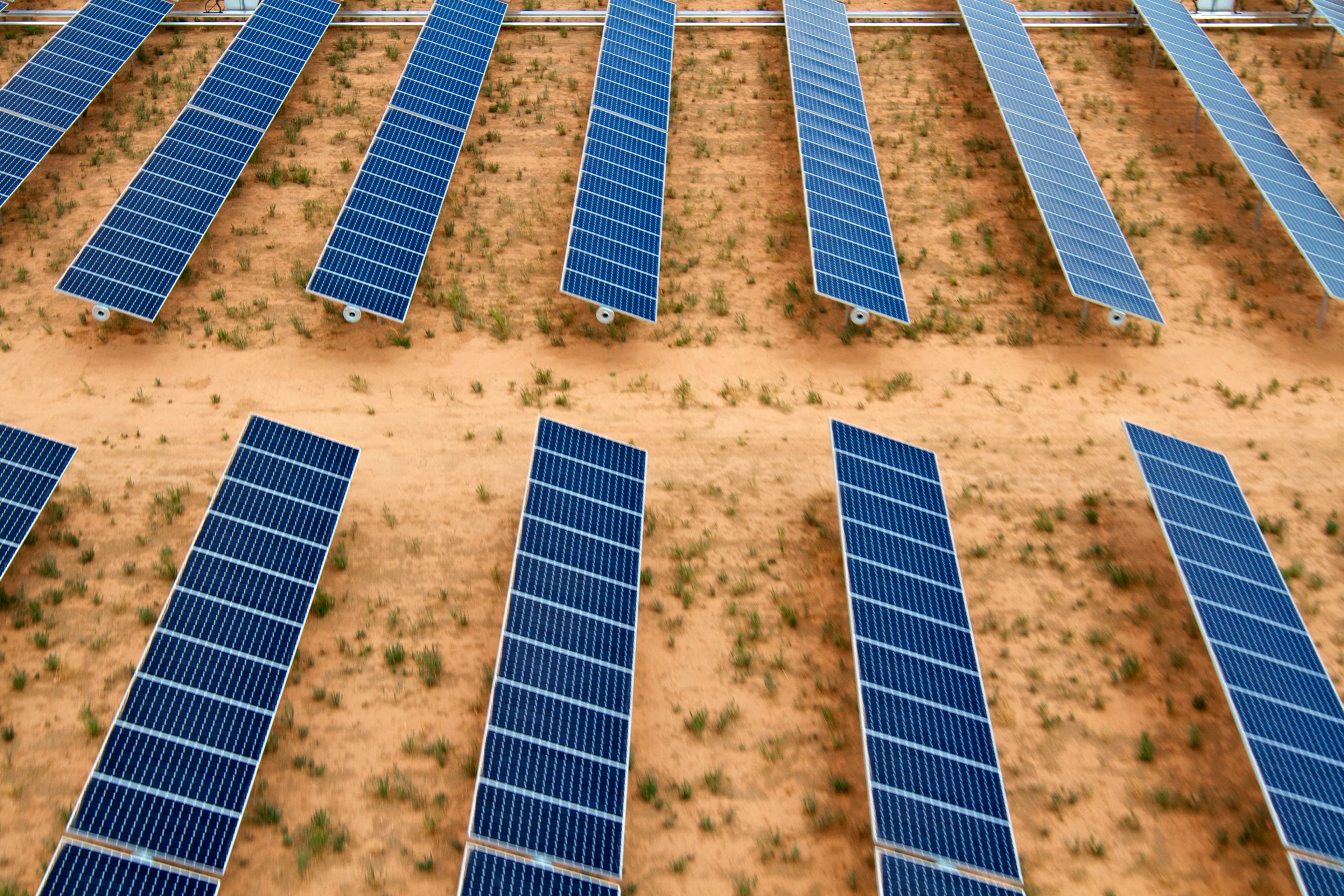
2011: Integrated solar modules installed at Iberdrola Copper Crossing Solar Power Plant
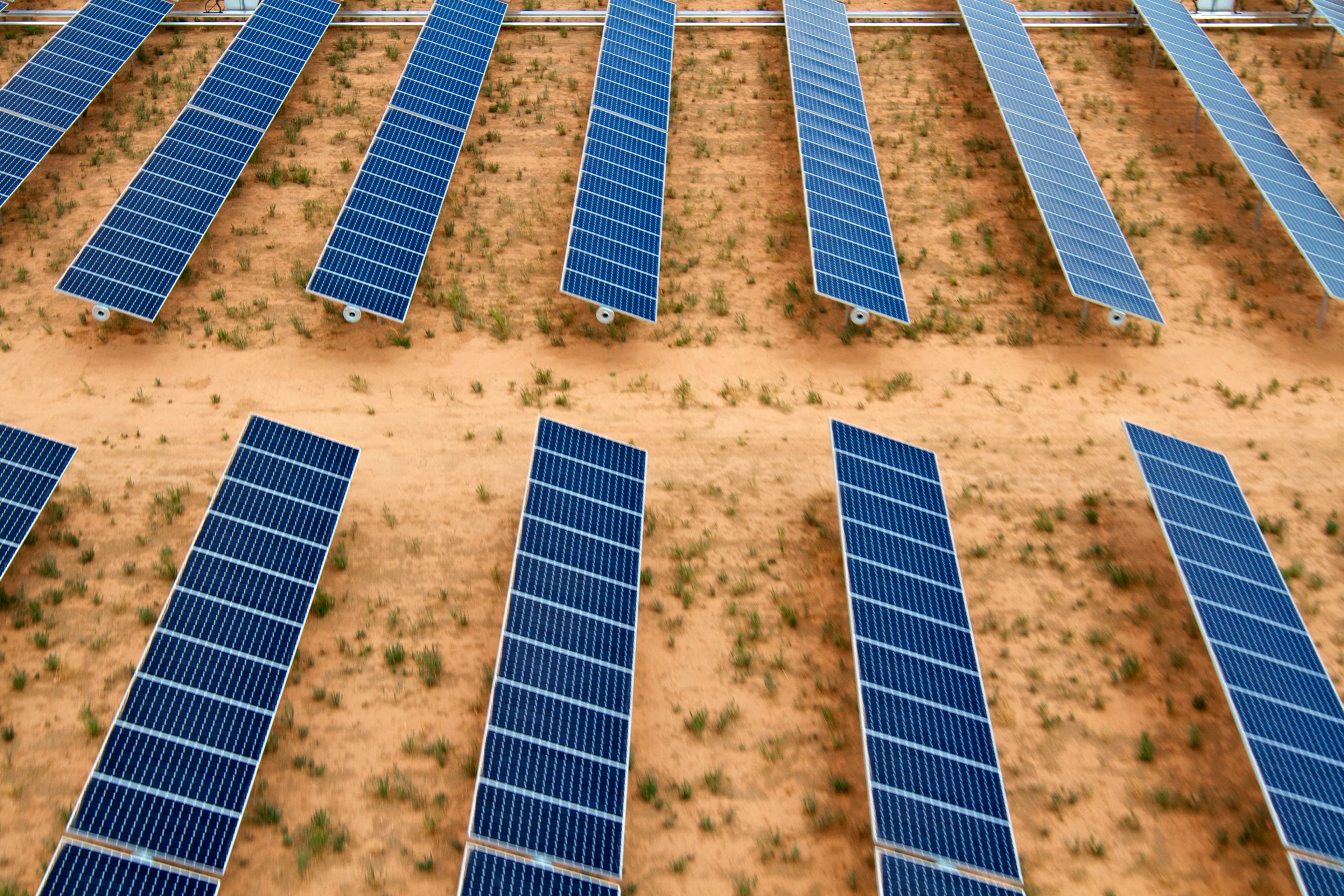
Fluor constructed the Copper Crossing plant on 144 acres of formerly private agricultural land. The developer was Iberdrola Renewables, a leader in developing solar power projects. Iberdrola also owns and operates the plant. The Copper Crossing 20-megawatt solar power project was constructed using two distinct tracker systems with two different size panels. The first 12MW were constructed using the SunPower® T0 Tracker system combined with 320-watt panels. The second 8MW were constructed using the SunPower Oasis® power plant combined with 425-watt panels. This was the first installation of the plant, which contains a solar power block that contains fully integrated modules, trackers, and inverters.
2011
Process plant modularization optimized for Satah Al Razboot gas gathering facilities
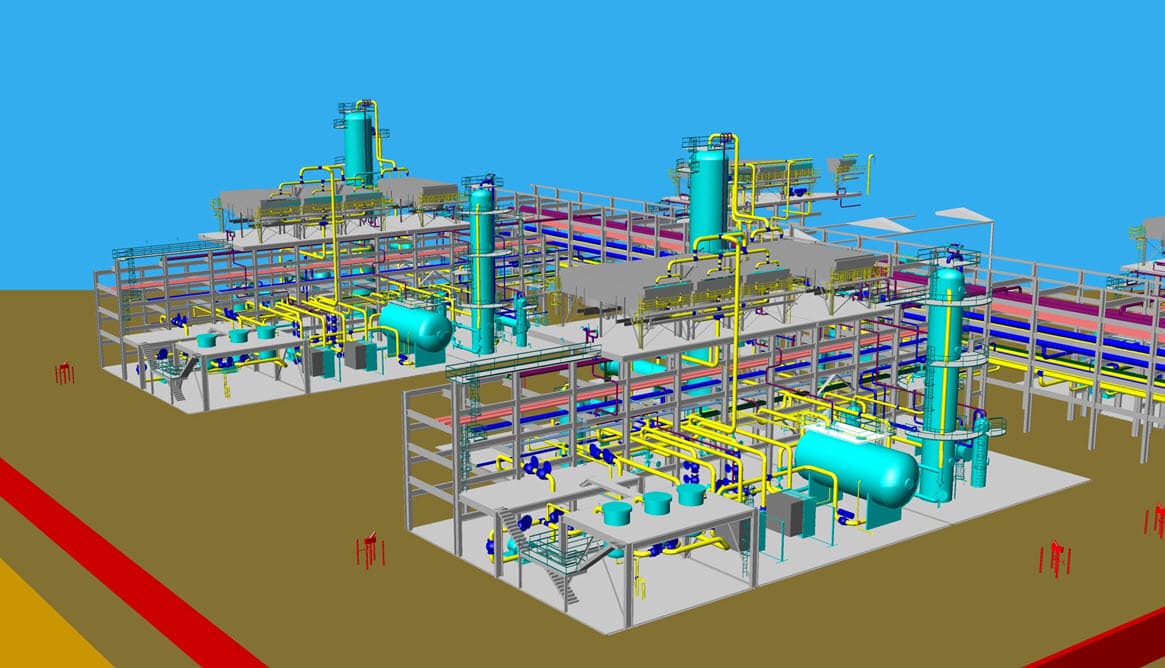
2011: Process plant modularization optimized for Satah Al Razboot gas gathering facilities
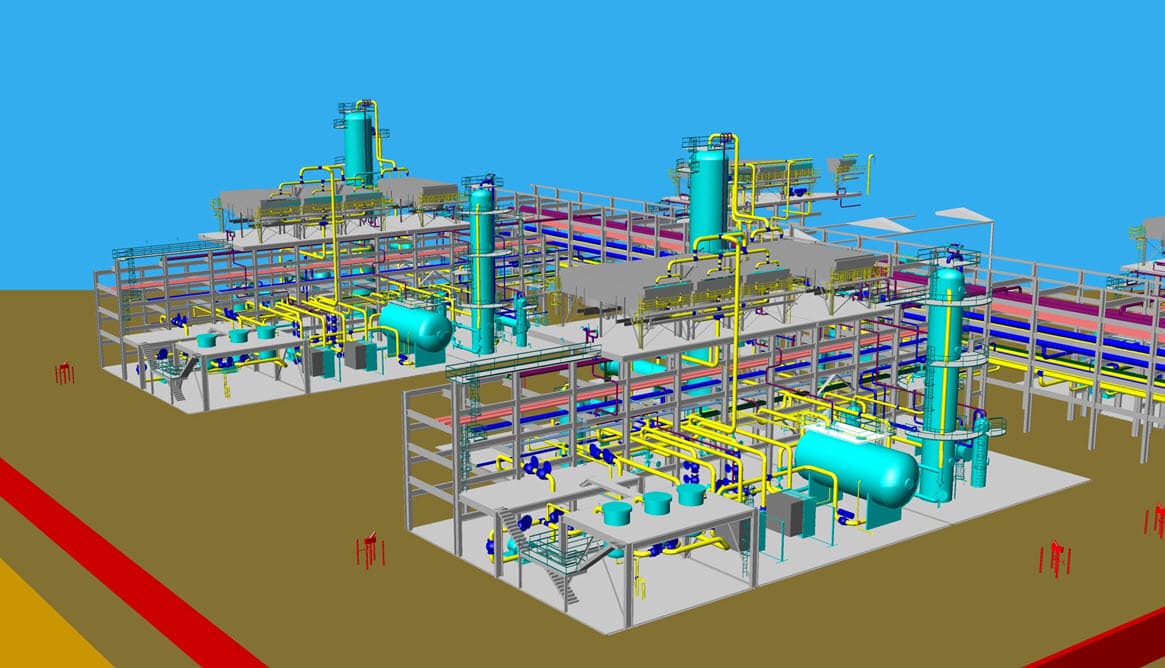
Fluor’s scope of work included the design of two artificial island drilling and wellhead production gathering facilities; subsea pipelines to transport well fluids, high pressure injection gas, and injection seawater; onshore (Zirku Island) facilities including crude oil and gas receiving, processing, handling, storage, and export facilities; along with supporting utilities and infrastructure. Due to the remote locations and limited access and laydown on Zirku Island for construction labor, Fluor recommended an execution plan that maximized preassembly and modularization of process plant and gas gathering facilities. Infrastructure designs (jetty and heavy hall roads), necessary to accommodate large modules, were included in the FEED phase engineering to accommodate early site development and define the execution approach for EPC contractors.
2012
Remote project drives extensive use of modular construction for Nexen Long Lake Upgrader
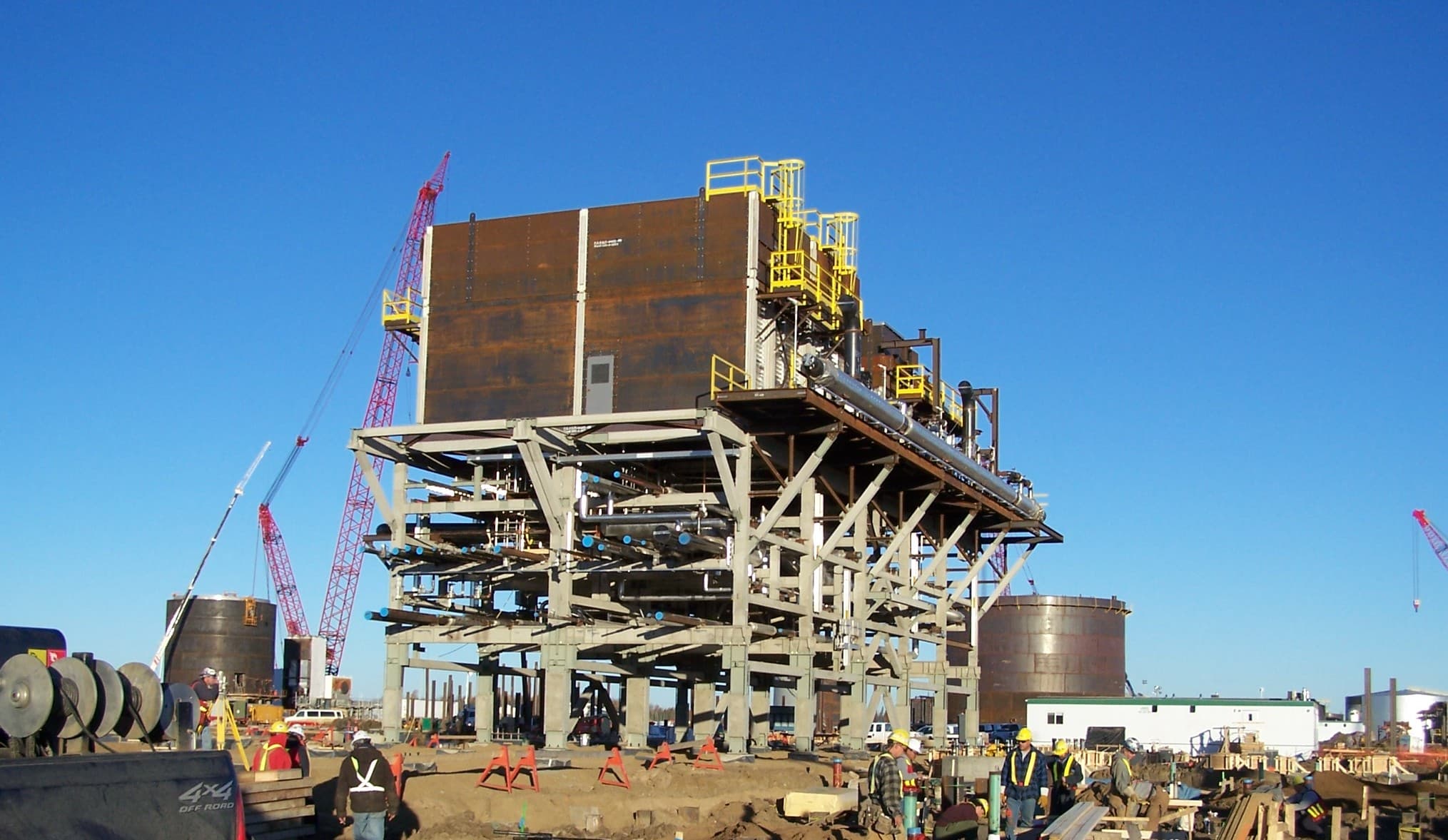
2012: Remote project drives extensive use of modular construction for Nexen Long Lake Upgrader
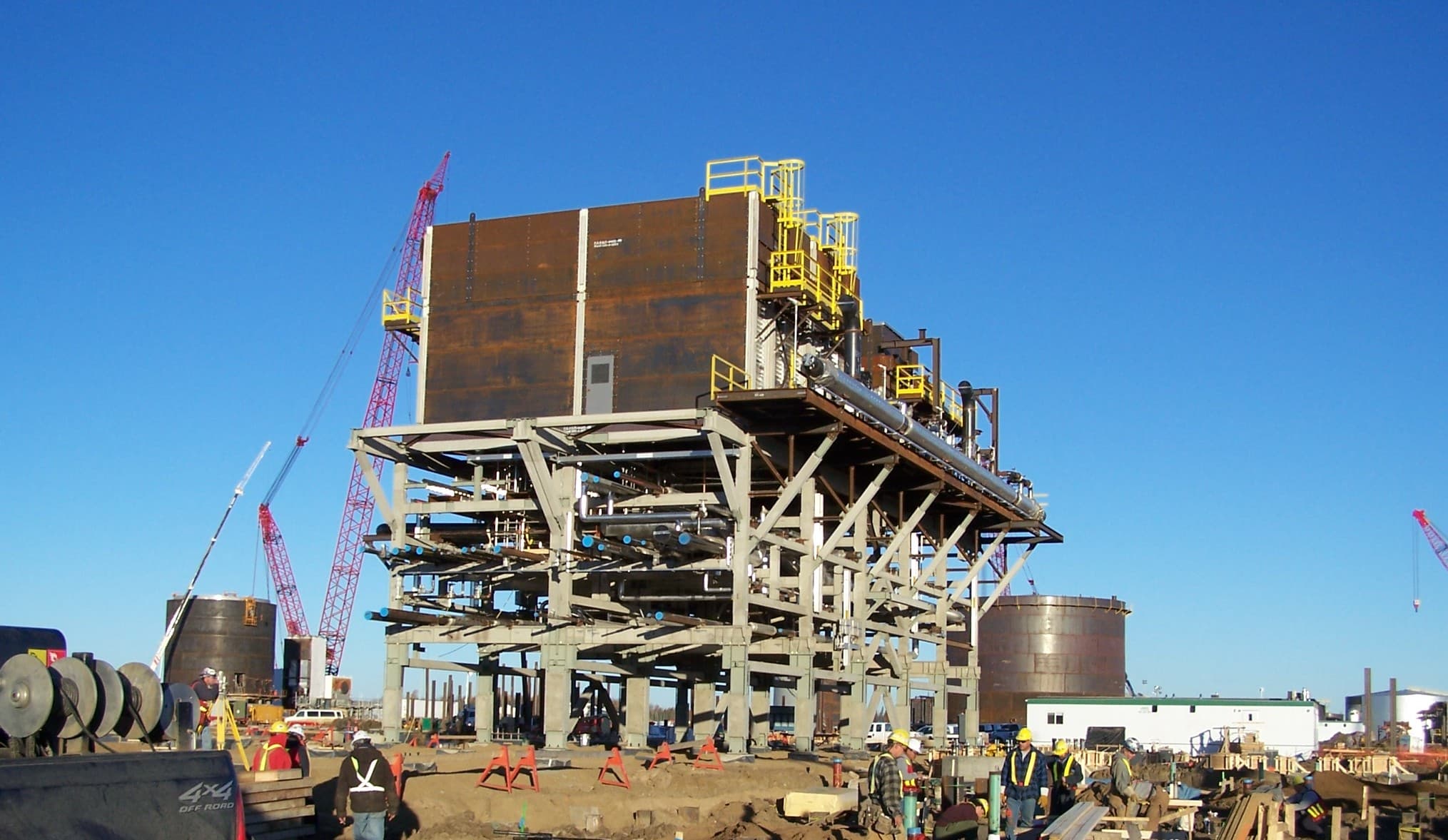
The Long Lake integrated oil sands facility represents a new approach to upgrading bitumen from Alberta oil sands: steam-assisted gravity drainage extraction integrated with onsite upgrading. Fluor provided engineering and procurement for major portions of the 72,000 barrel per day upgrader as well as licensed technology and construction for the Sulfur Recovery Unit.
The remote project location, with limited site access, and a strained labor market drove the extensive use of modular construction.
2012
Critical modular approach facilitates aggressive schedule for Grifols' North Fractionation Facility
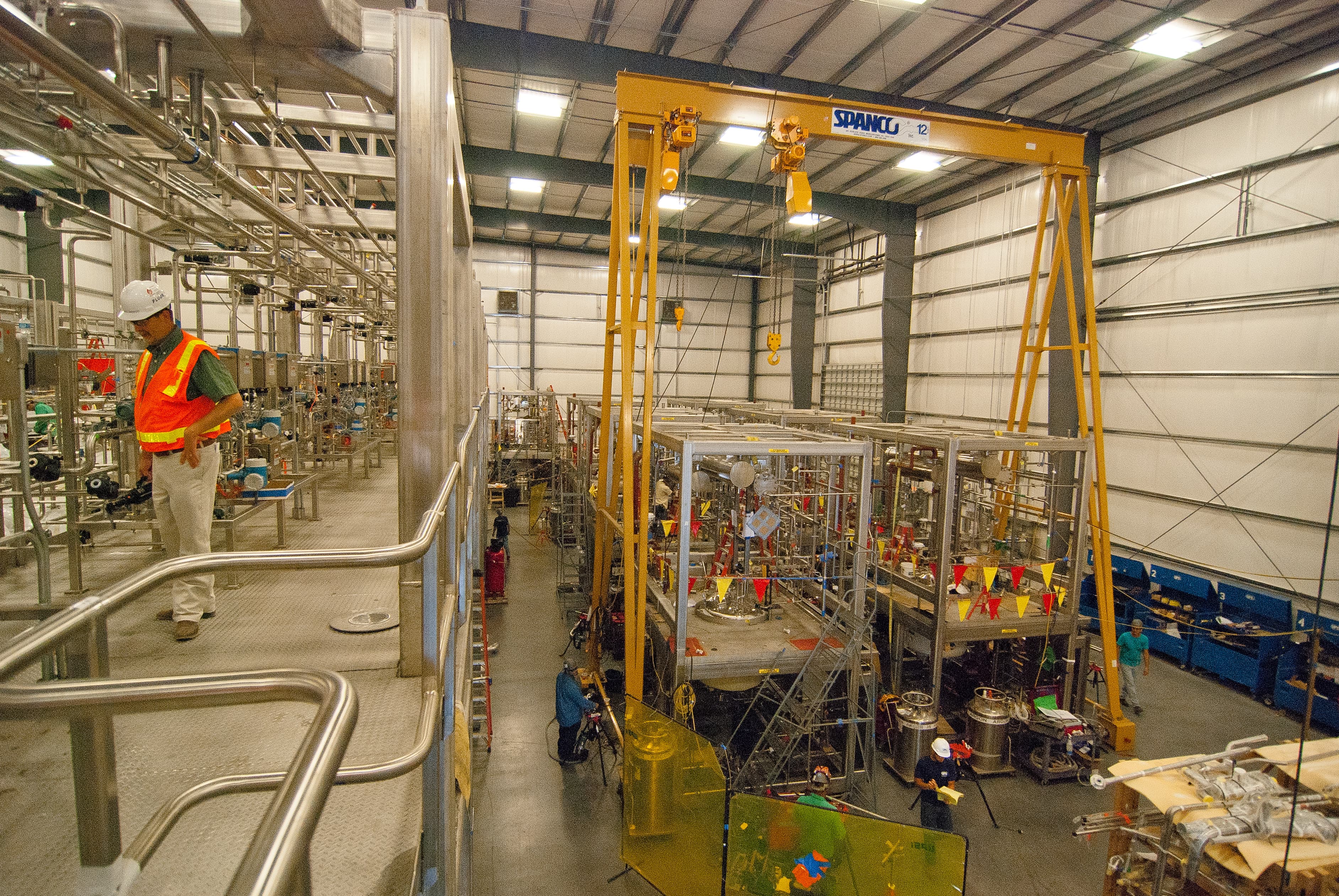
2012: Critical modular approach facilitates aggressive schedule for Grifols' North Fractionation Facility
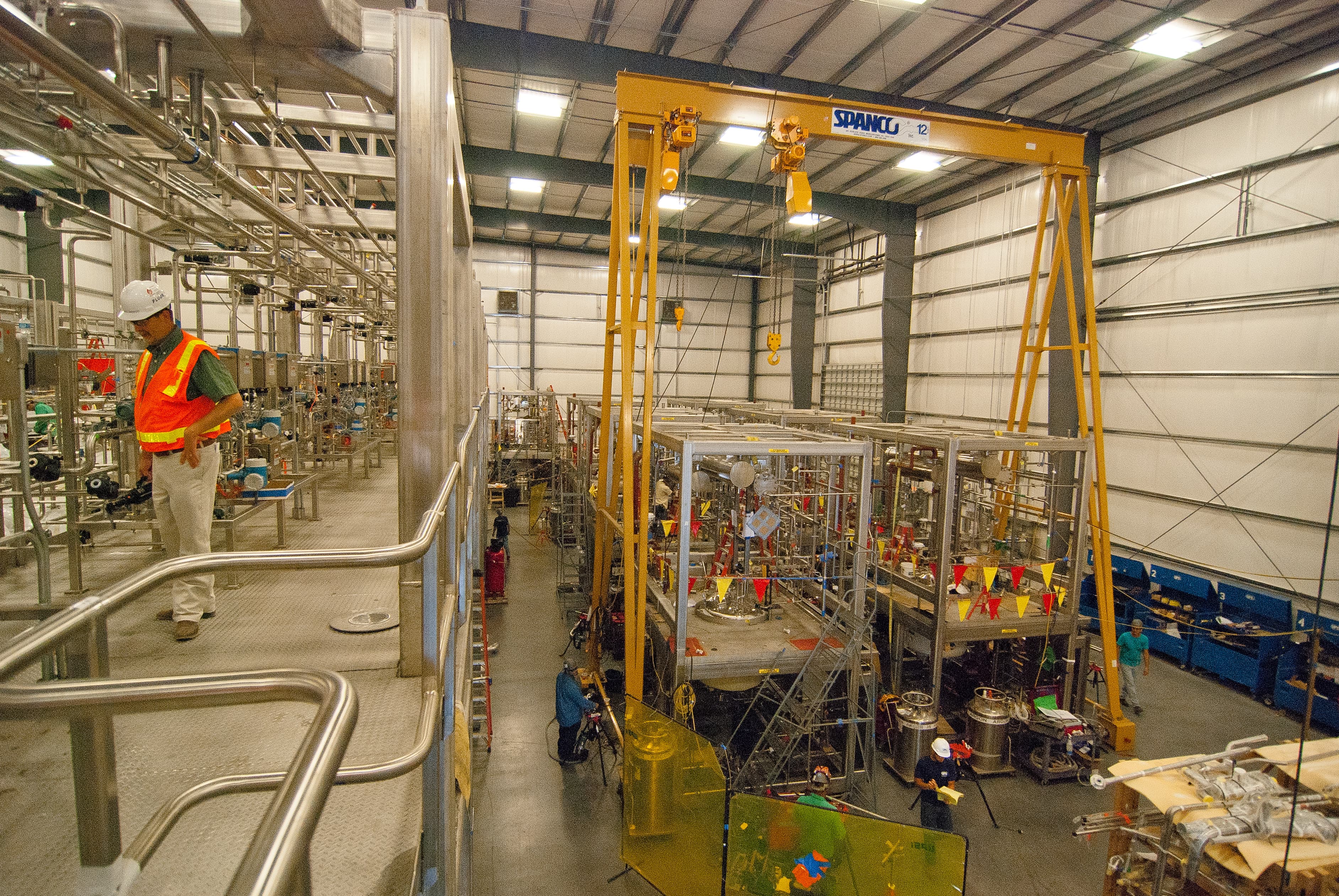
Fluor was selected by Grifols, a global biotherapeutic and biotechnology company, to significantly expand their manufacturing capacity. The Grifols project employed advanced modular design and construction techniques to build both the structure and processing units simultaneously in order to shorten the overall schedule. Rather than a sequential construction approach, where the building is first constructed, then process units are installed, piped, and finally started up, the NFF construction strategy was based upon a concurrent build model.
2012
Offsite modularization key strategy for construction execution at Marathon's Detroit refinery
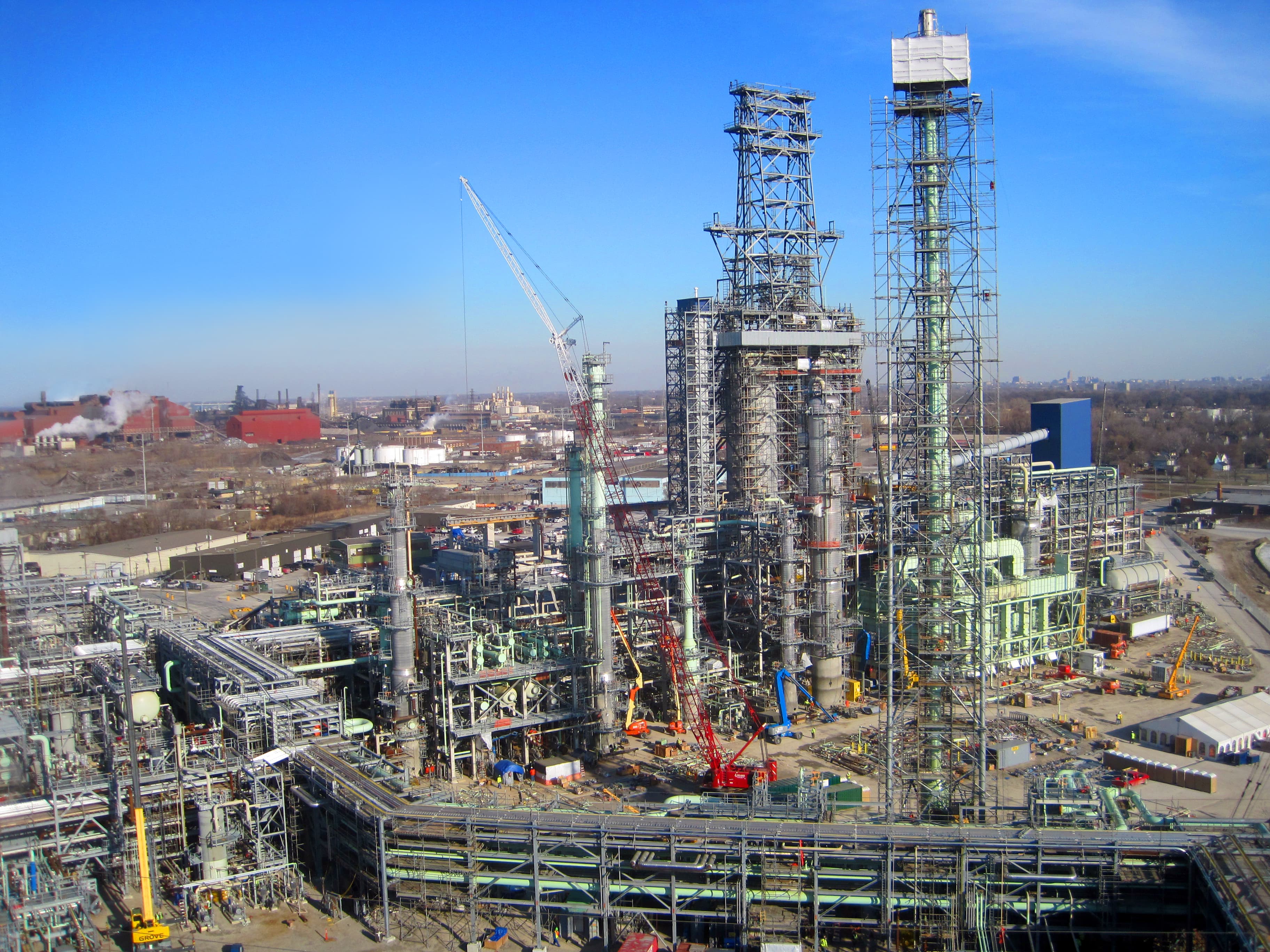
2012: Offsite modularization key strategy for construction execution at Marathon's Detroit refinery
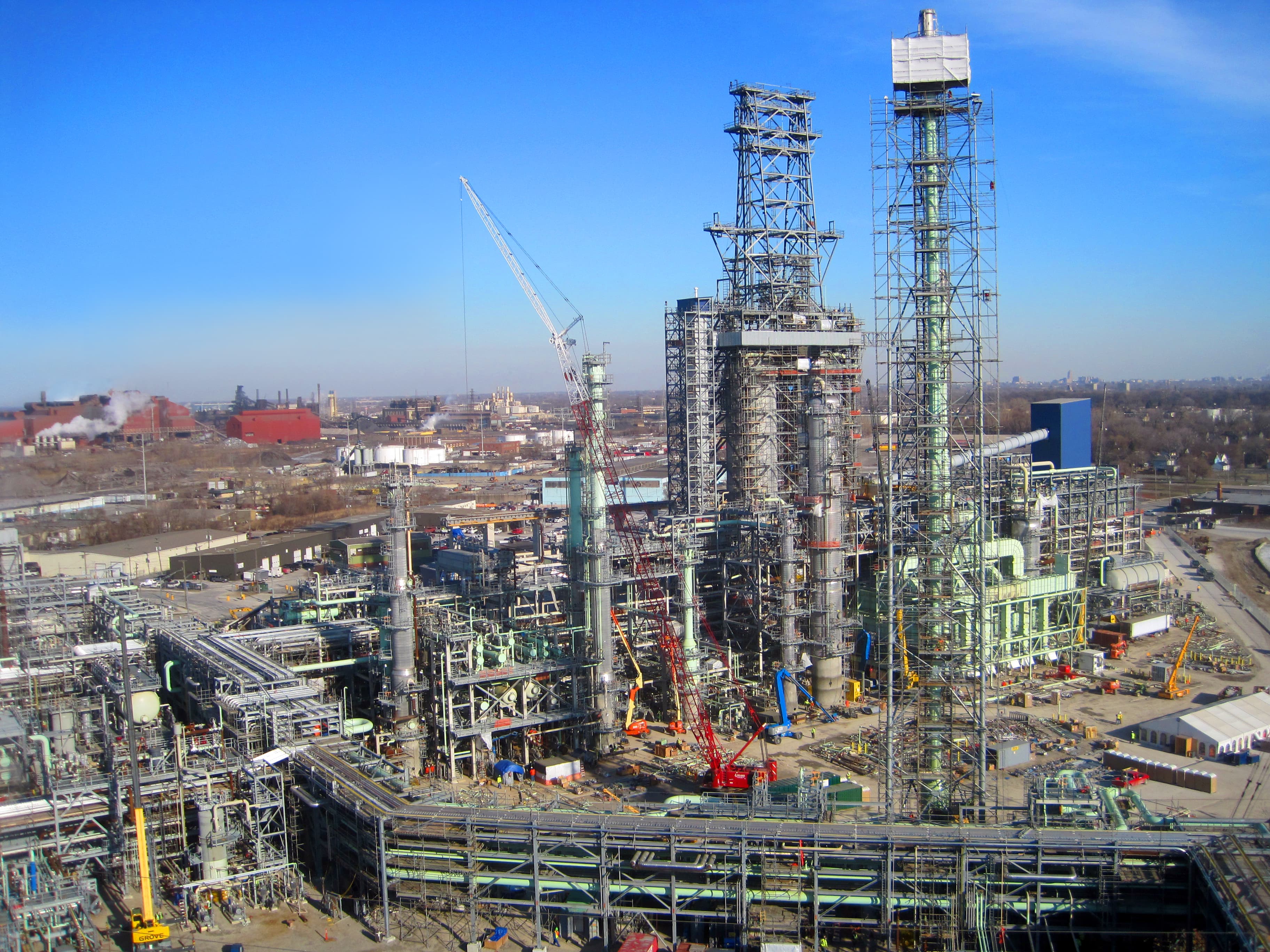
Marathon's Detroit Heavy Upgrade Project required over 1,000 pieces of equipment and large quantities of bulk materials, all procured from 7 primary global fabrication and supply areas. Offsite modularization of process facilities was a key execution strategy implemented as 51 large process modules were fabricated and barged from ICA Fluor’s mod yard located in Tampico, Mexico.
2012
Self-propelled modular transporters move bridges into place during full freeway closure for Utah's I-15 CORE Project
&w=3840&q=75)
2012: Self-propelled modular transporters move bridges into place during full freeway closure for Utah's I-15 CORE Project
&w=3840&q=75)
Provo River Constructors [PRC], a Fluor-led joint venture, designed and reconstructed a 24-mile-long stretch of Interstate-15 (I-15) in northern Utah. PRC used Accelerated Bridge Construction [ABC] to expedite the schedule. Under this ABC method, four bridges were constructed on the side of I-15. These bridges are as heavy as 3.8 million tons, and as long as a football field, including end zones. With the use of a remote-controlled, self-propelled modular transporter, the bridges were be moved into place overnight, allowing for full freeway closure without impacting the safety or travel times of motorists using the interstate.
2013
Over 600,000 photovoltaic modules installed on a single axis tracking system for LS Power
&w=3840&q=75)
2013: Over 600,000 photovoltaic modules installed on a single axis tracking system for LS Power
&w=3840&q=75)
In 2011, LS Power awarded Fluor an engineering, procurement, and construction contract to design and build a new, 125-megawatt solar photovoltaic (PV) facility in Arizona. The Arlington Valley Solar Energy II (AVSE II) project uses more than 600,000 PV panels to harness the power of the sun in order to provide clean energy for the region.
2014
Innovative modular execution approach used to construct Shell's Carbon Capture and Storage Facility
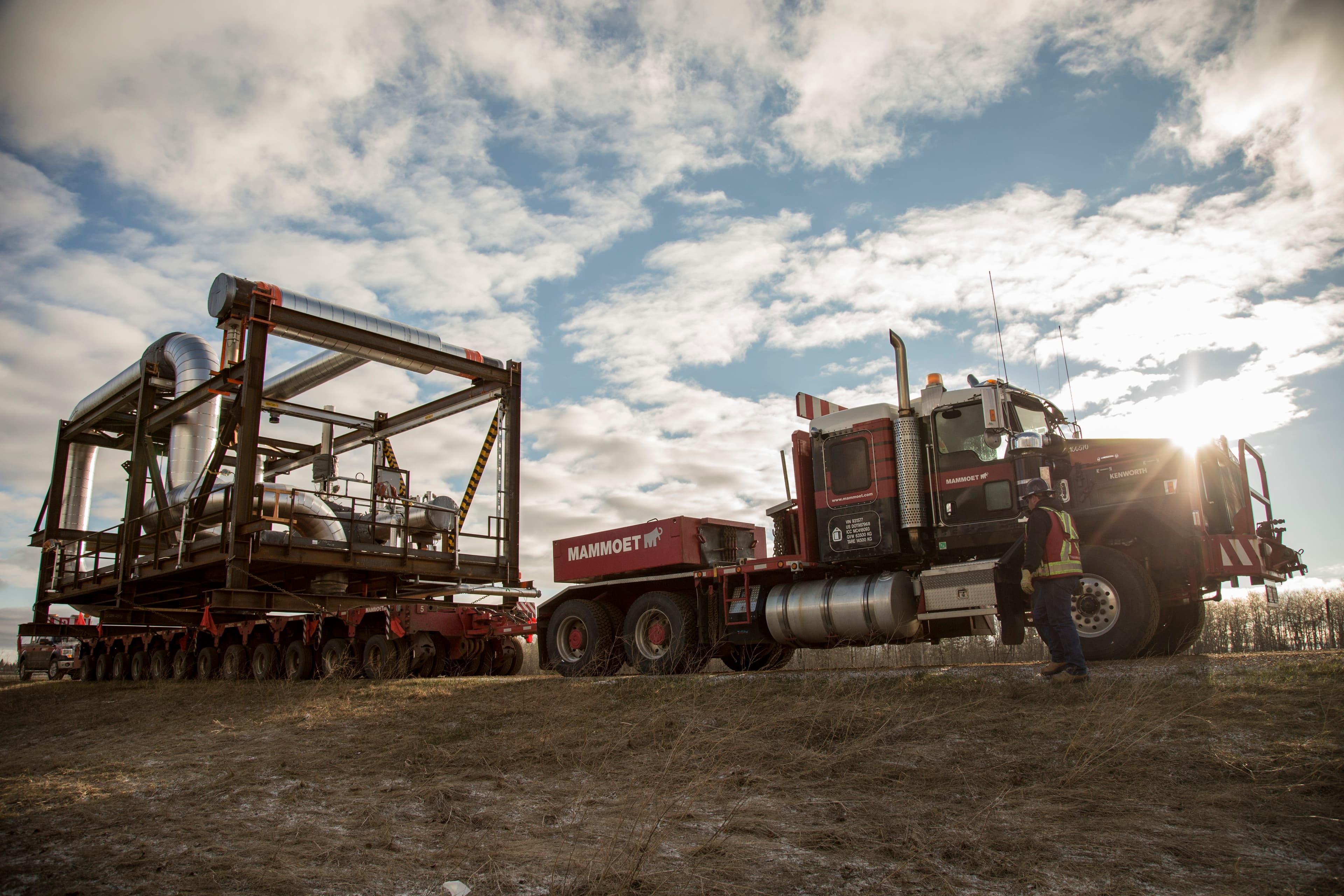
2014: Innovative modular execution approach used to construct Shell's Carbon Capture and Storage Facility
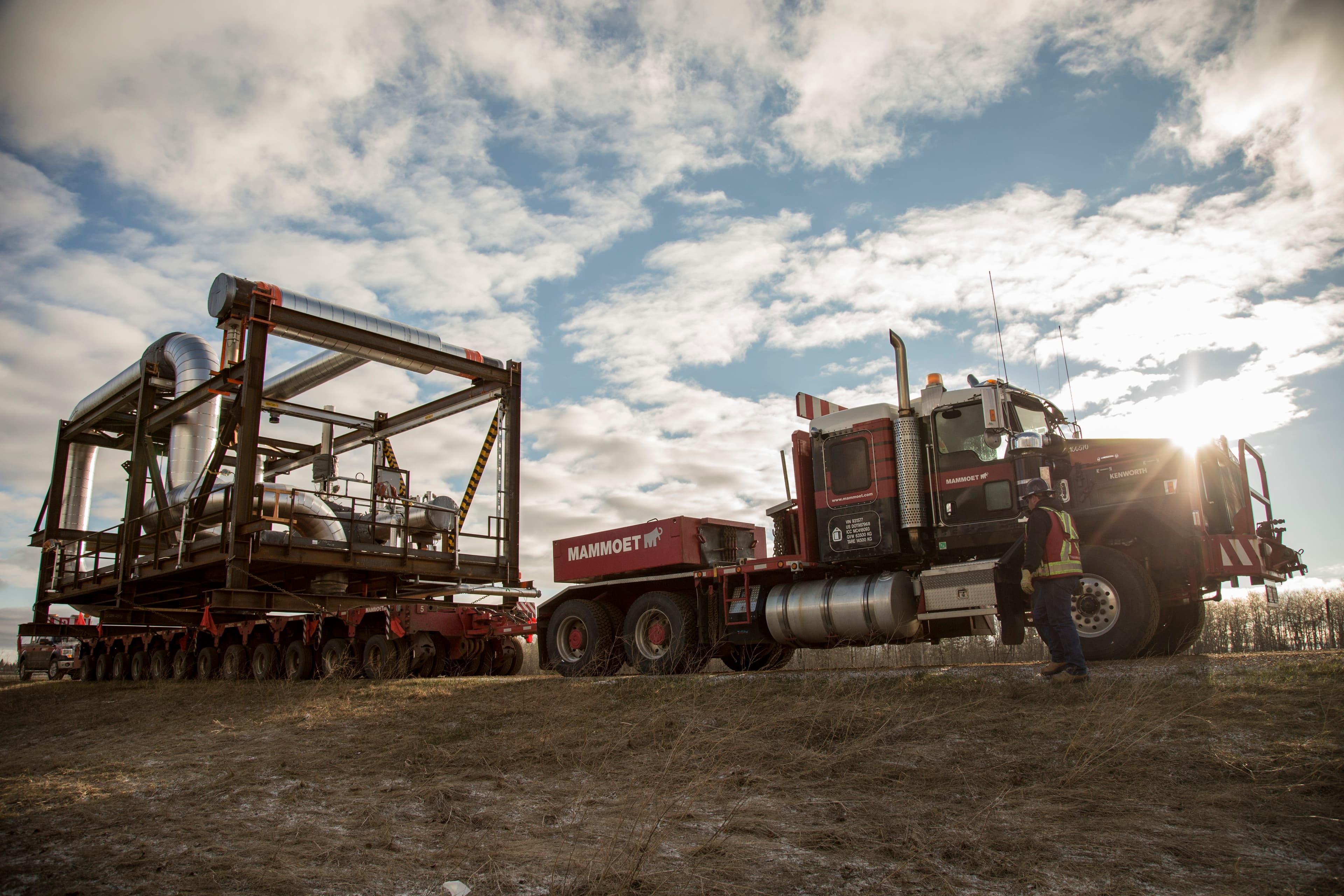
Fluor provided preliminary services, front-end engineering and design, engineering, procurement, and construction for Shell's Carbon Capture and Storage Quest project. Fluor used an innovative modular execution approach for the 1.1 million tonne-per-year carbon capture facility at the Scotford Upgrader. Captured carbon dioxide is sent about 80 kilometers from the facility via underground pipeline to an underground storage site.
2014
Extensive module program used to construct Vale's Long Harbour Nickel Processing Plant
2014: Extensive module program used to construct Vale's Long Harbour Nickel Processing Plant
Fluor performed engineering, procurement, and construction management services for the Long Harbour Nickel Processing Plant built by Vale. The plant produces 50,000 tonnes per year of finished nickel product, together with associated cobalt and copper products. The project had an extensive module program. Approximately 200 modules were constructed at 4 different yards.
2014
Shell Quest project recognized by Engineering News-Record
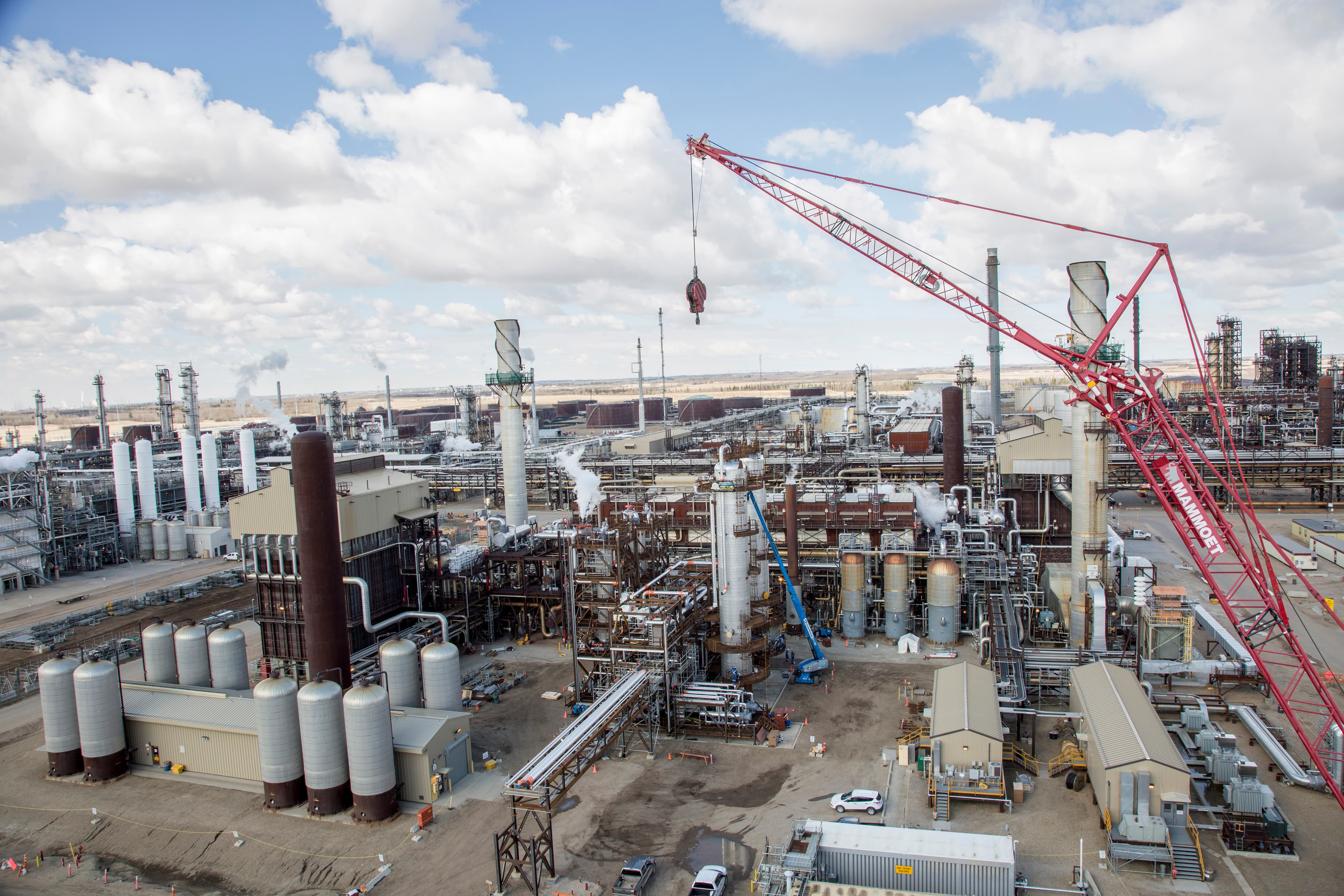
2014: Shell Quest project recognized by Engineering News-Record
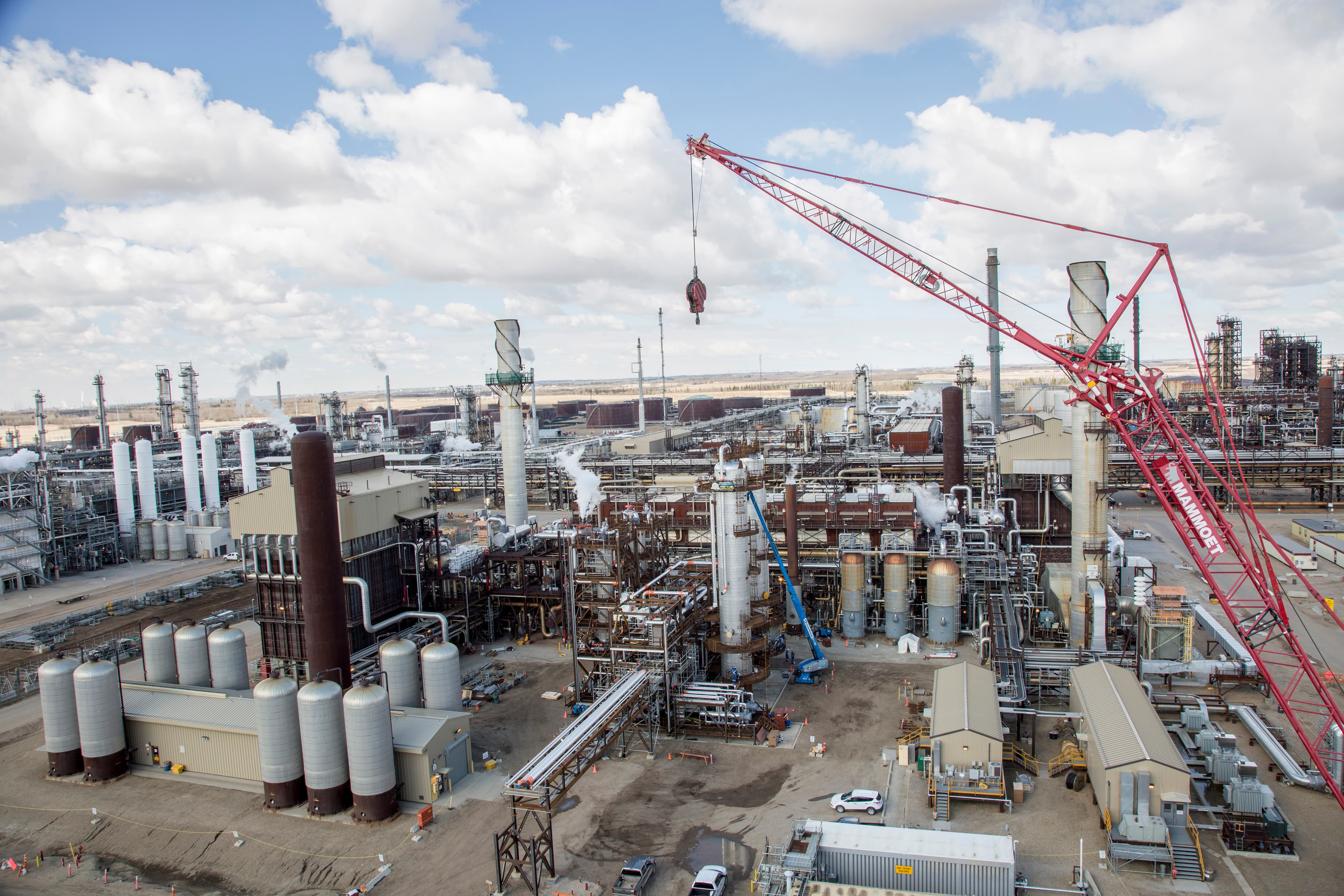
Fluor's work on the Shell's Carbon Capture and Storage (CSS) Quest project tied for first place in Engineering News-Record's category of Best Project, Power/Industrial.
We designed and built the facility using 69 separate interlocking modules that were assembled at the jobsite. This Athabasca oil sands project was delivered under budget and on schedule with an exemplary construction safety record.
We were responsible for the engineering, procurement and construction services for the capture portion of the Quest CCS project, which was built adjacent to an existing operating facility. In order to minimize the capital costs of the new facility and reduce disruptions to the existing operating facility, we implemented our modular execution strategy to fabricate the interlocking modules offsite and then deliver them for installation.
2015
Iron Ore Modularization Project nearly triples BHP Billiton's Iron Ore production capacity
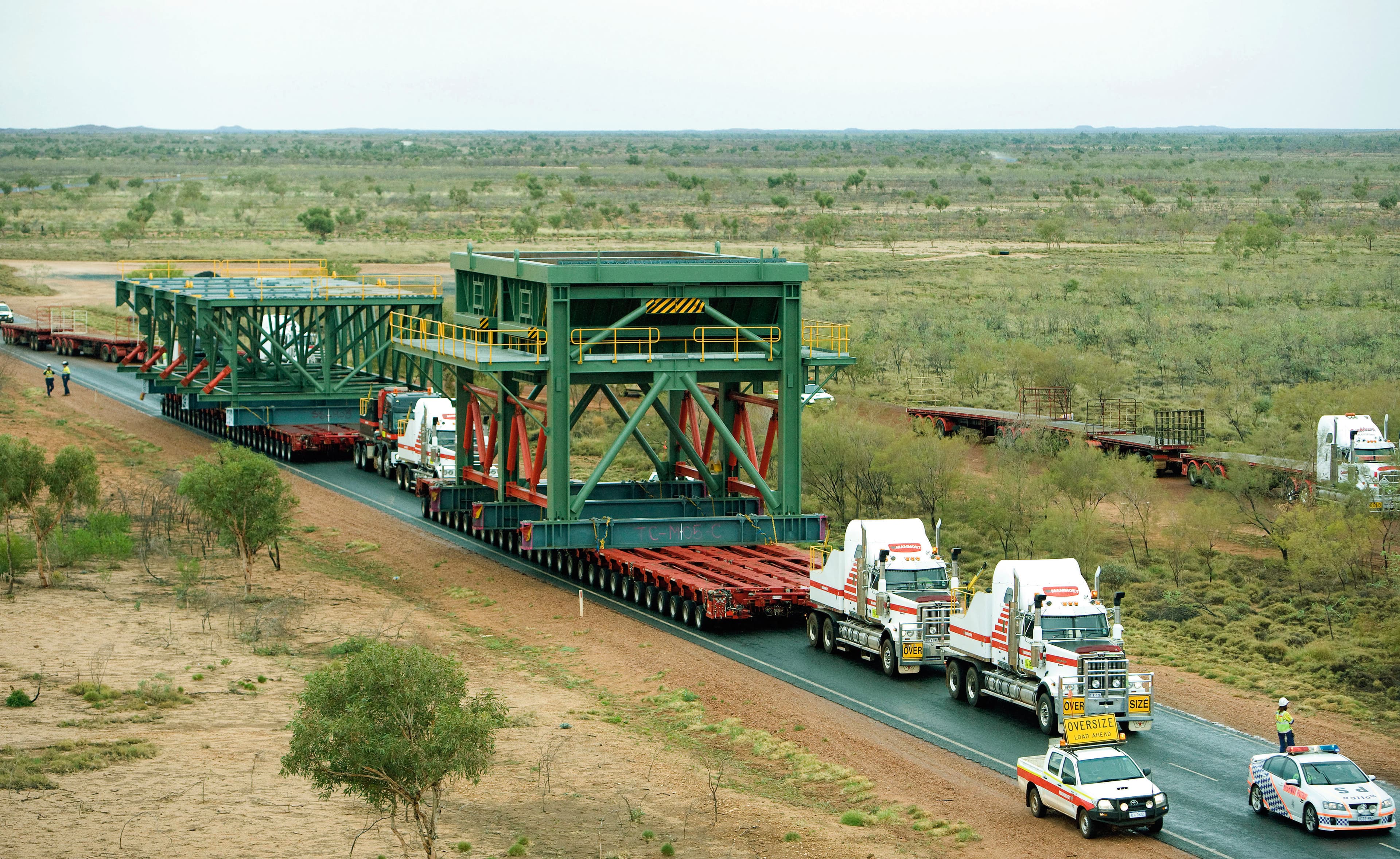
2015: Iron Ore Modularization Project nearly triples BHP Billiton's Iron Ore production capacity
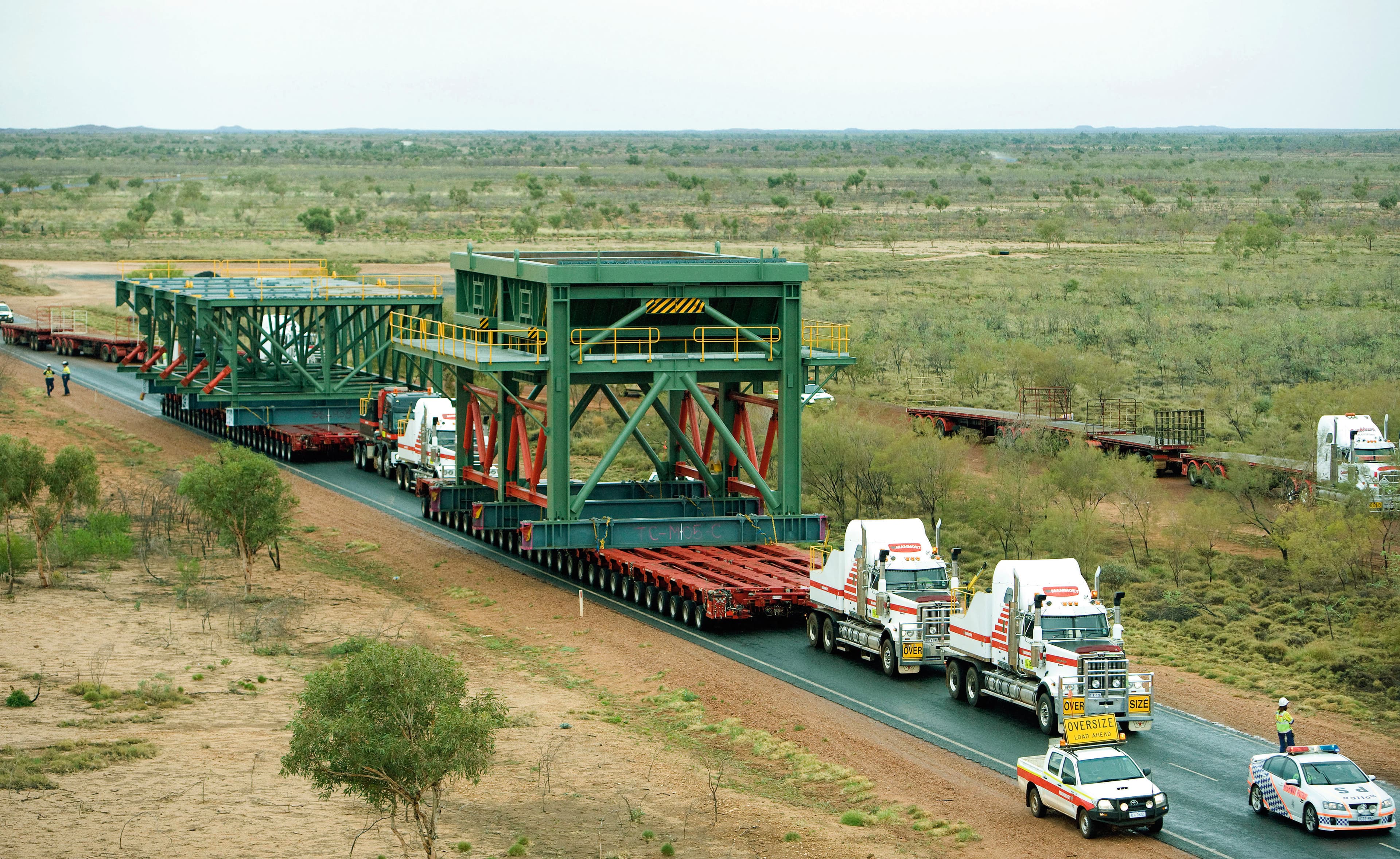
Fluor, as part of a joint venture with SKM, provided engineering, procurement, and construction management services and programme managed a series of multi-billion dollar projects for BHP Billiton Iron Ore (BHPBIO) in Western Australia. The Fluor-led joint venture was engaged by BHPBIO to assist in the execution of its iron ore expansion projects to increase mining, processing, rail transportation, stockpiling, and shiploading capabilities across BHP Billiton’s Pilbara iron ore assets. The project included large-scale modularization to reduce on-site construction workforce requirements.
2015
Delivery and installation of key modular components for the Dow Gulfstream Project drives project progress
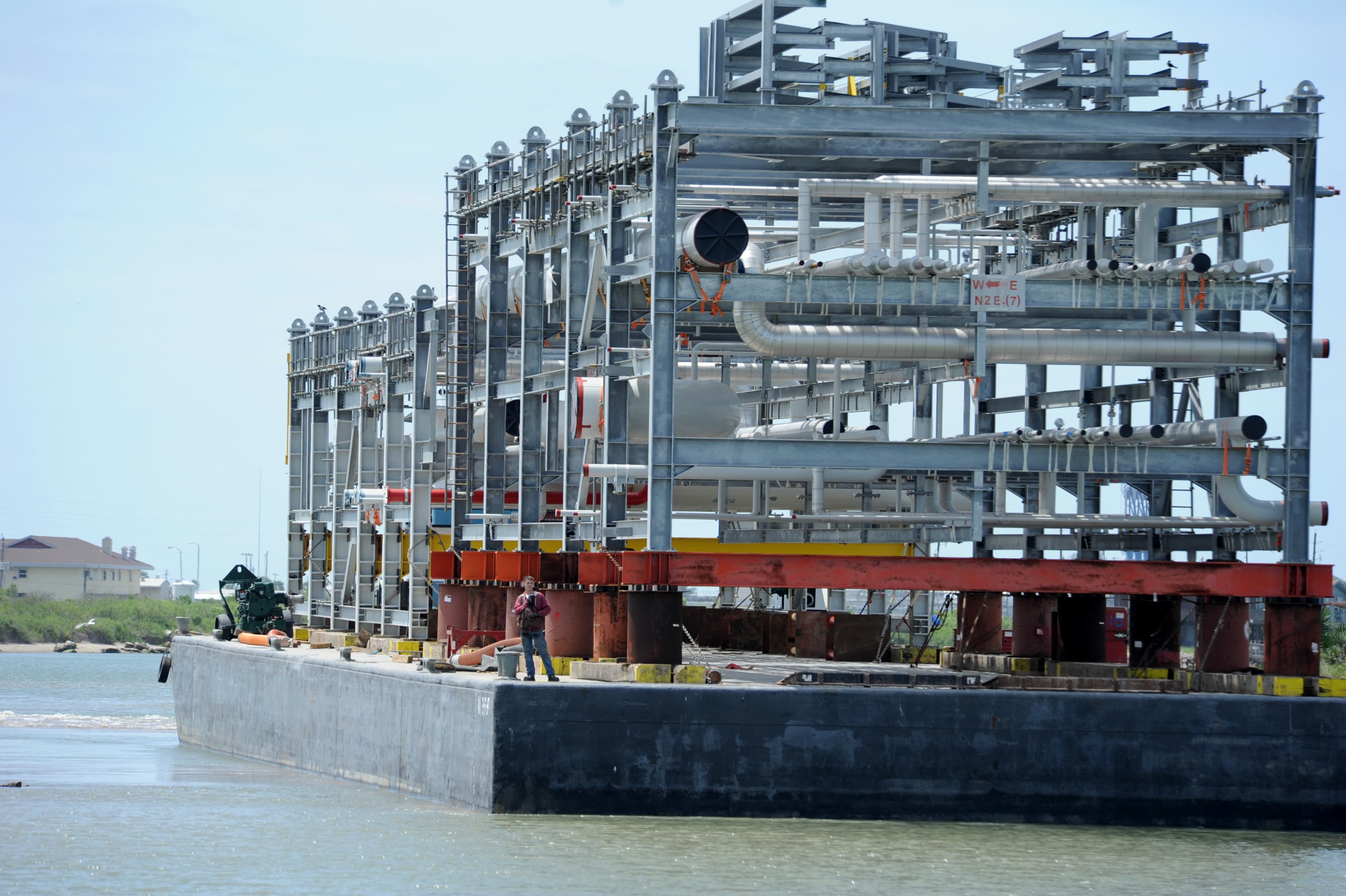
2015: Delivery and installation of key modular components for the Dow Gulfstream Project drives project progress
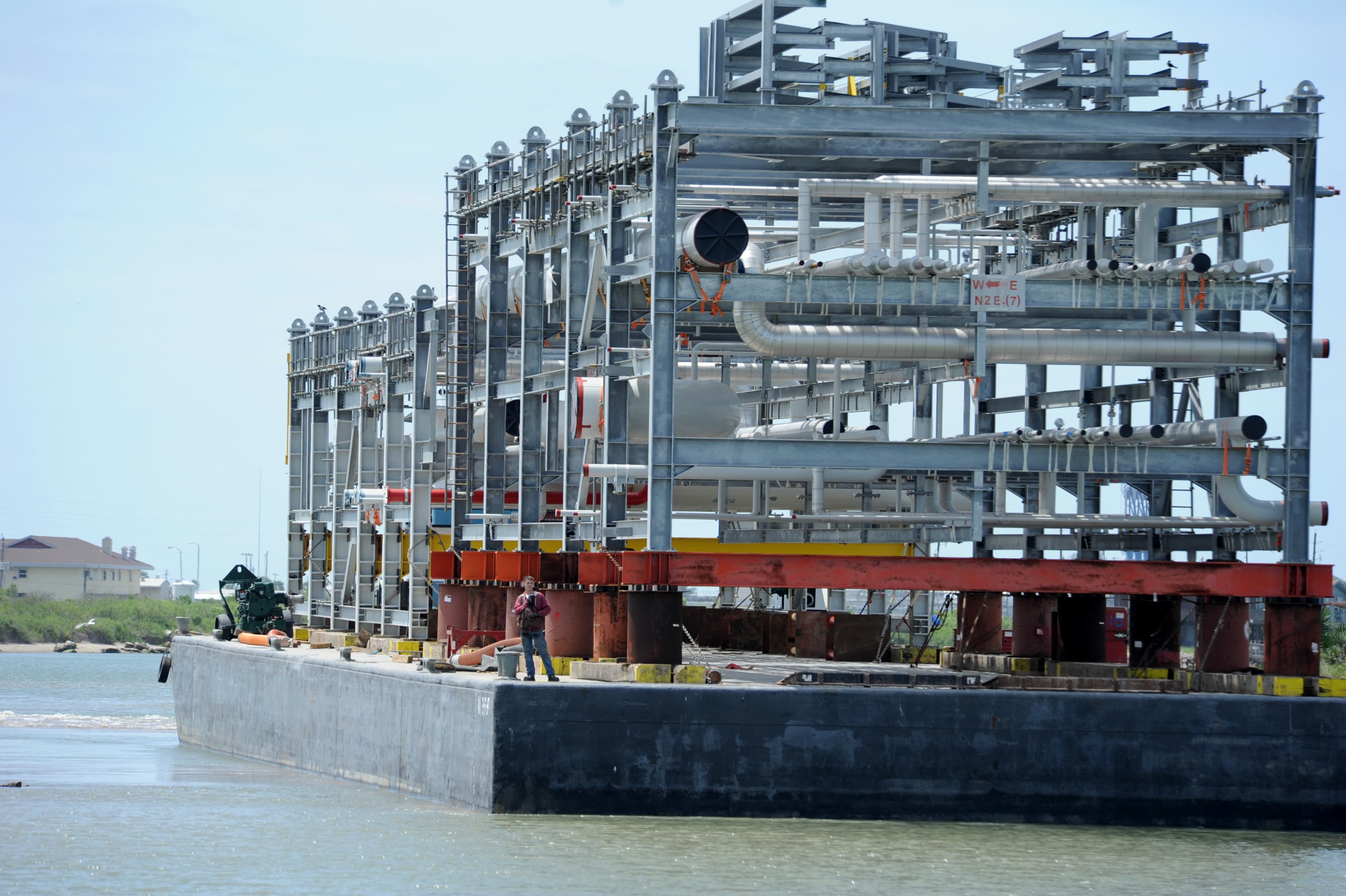
Dow is currently expanding its production facilities on the Gulf Coast in Freeport, Texas and Plaquemine, Louisiana with its Gulfstream Program. Fluor is performing the very significant portion of the program on the Oyster Creek site. Fluor’s scope consists of a Propylene Dehydrogenization (PDH) unit, the Power, Utilities, & Infrastructure (PUI) scope, and a state of the art Light-Hydrocarbon (LHC-9) unit. Fluor will leverage its proven processes to recruit a large number of direct-hire craft and construction management staff to build the facility.
2015
Modular execution and construction innovation used for Antwerp Northwest Europe Resid Upgrade Project
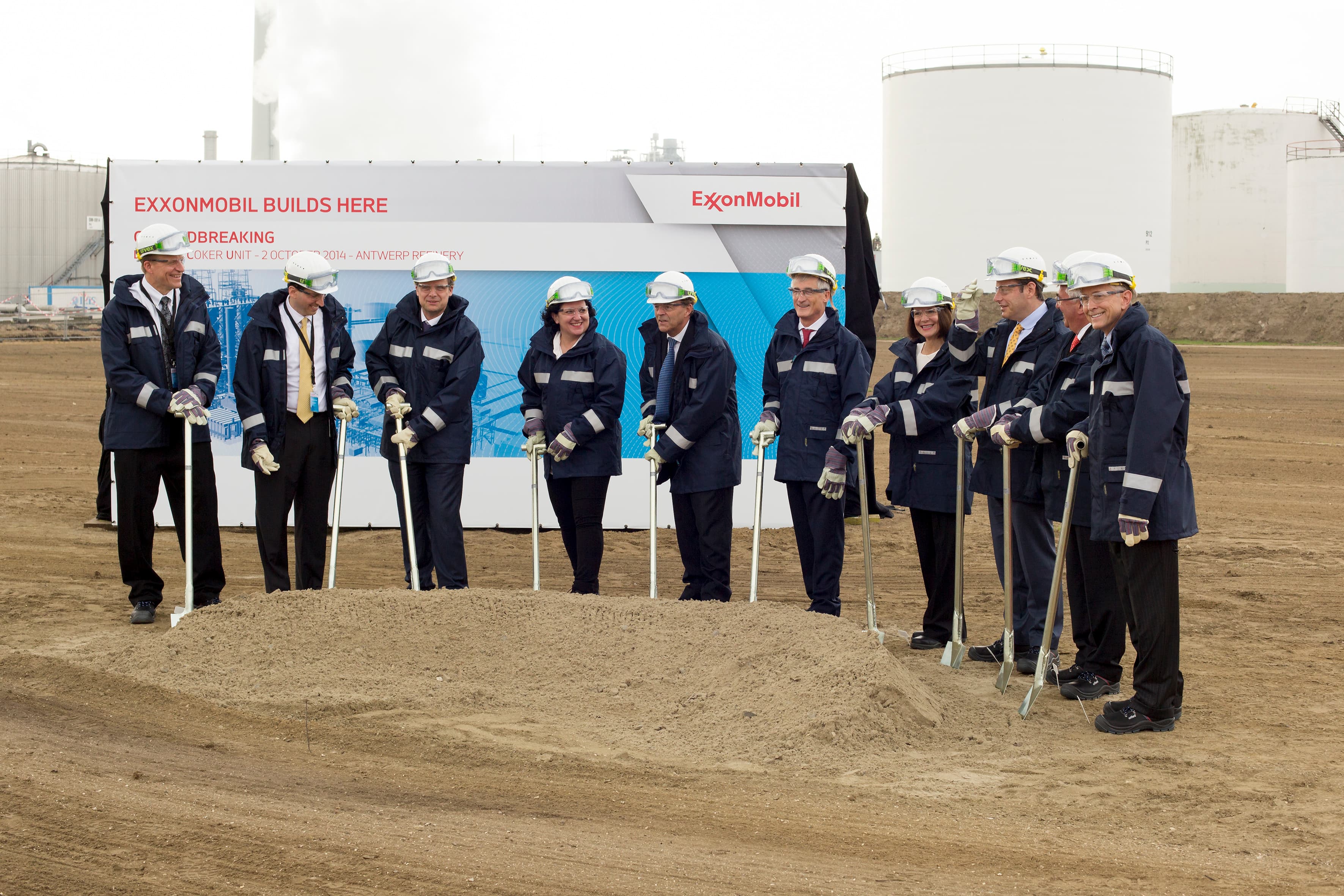
2015: Modular execution and construction innovation used for Antwerp Northwest Europe Resid Upgrade Project
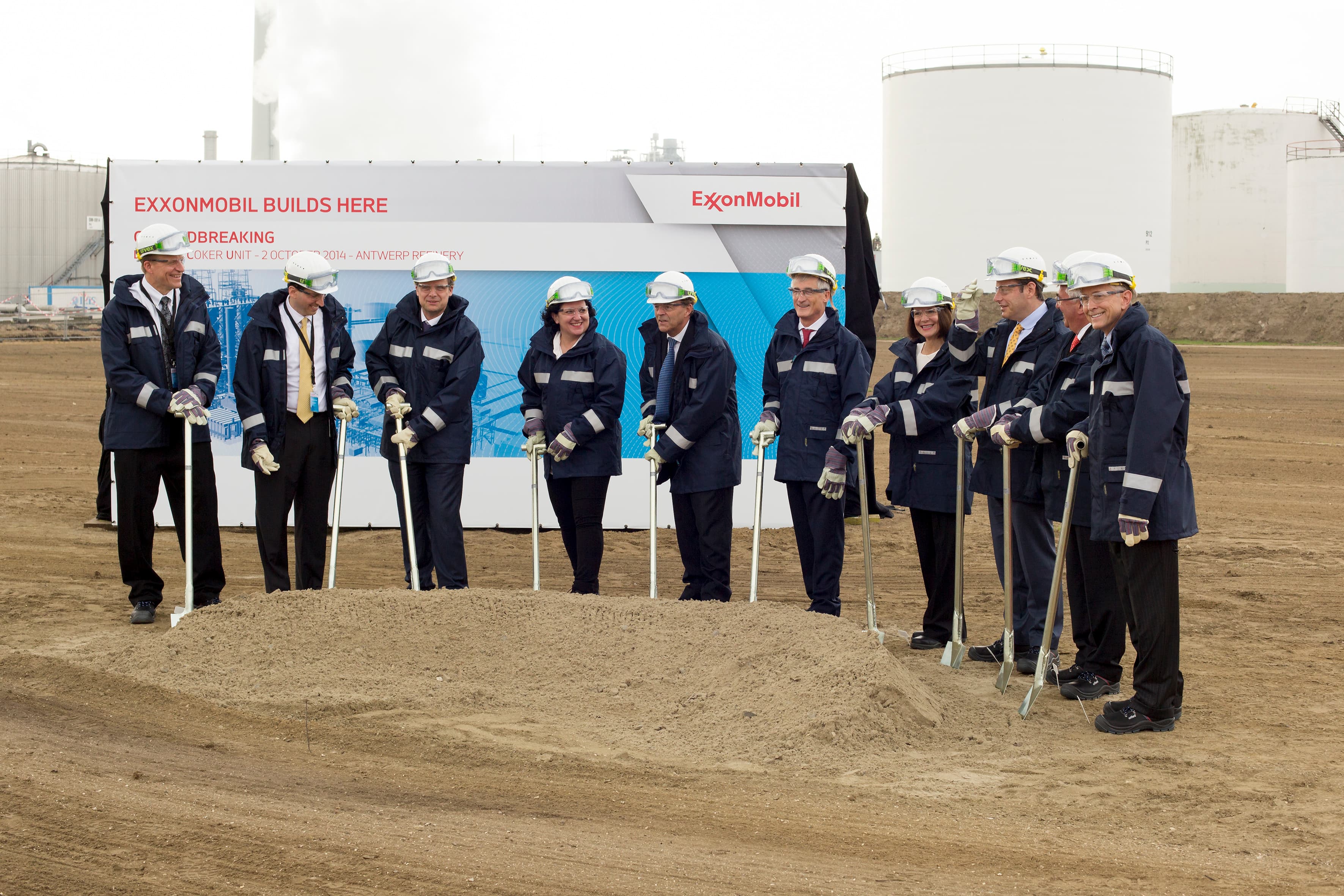
Fluor’s responsibilities span the project’s life cycle and include design, engineering, procurement, module fabrication, transportation, installation, and construction. Fluor is responsible for the new delayed coker unit that will convert heavy, higher sulfur residual oils into transportation fuel products such as marine gasoil and diesel fuel.
2015
Fluor and COOEC form fabrication joint venture
2015: Fluor and COOEC form fabrication joint venture
Fluor and Offshore Oil Engineering Co., Ltd. (COOEC) agreed to form a fabrication joint venture, COOEC Fluor Heavy Industries Co., Ltd, to provide very large modules for offshore clients in the Asia Pacific region and globally. The Zhuhai Fabrication Yard is a world-class, state-of-the-art facility and is located near Hong Kong in the Zhuhai Gaolan Port Economic Zone. The facility can accommodate fabrication modules weighing more than 50,000 tons.
2017
Fluor applies modular approach to Letlhakane Mine project
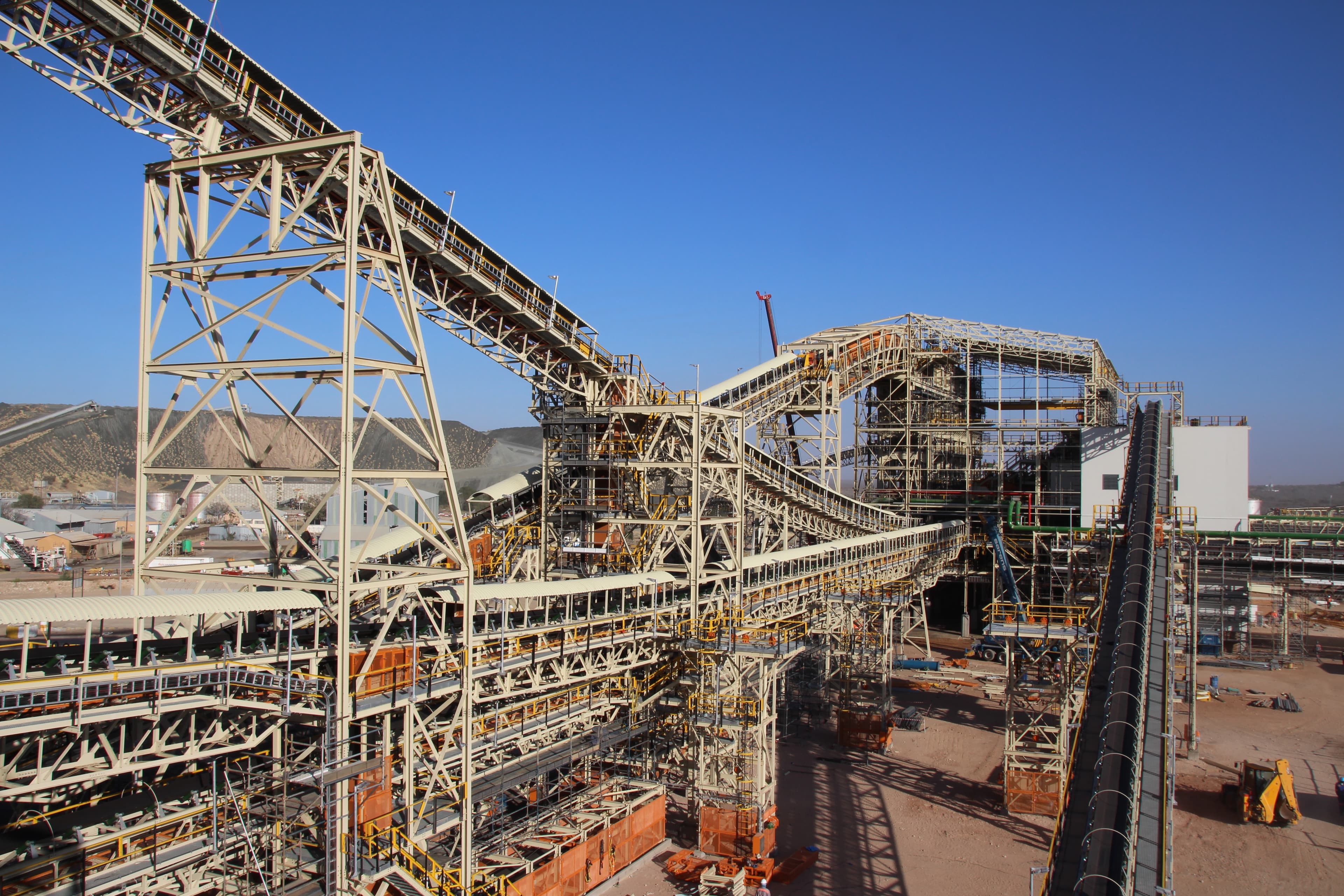
2017: Fluor applies modular approach to Letlhakane Mine project
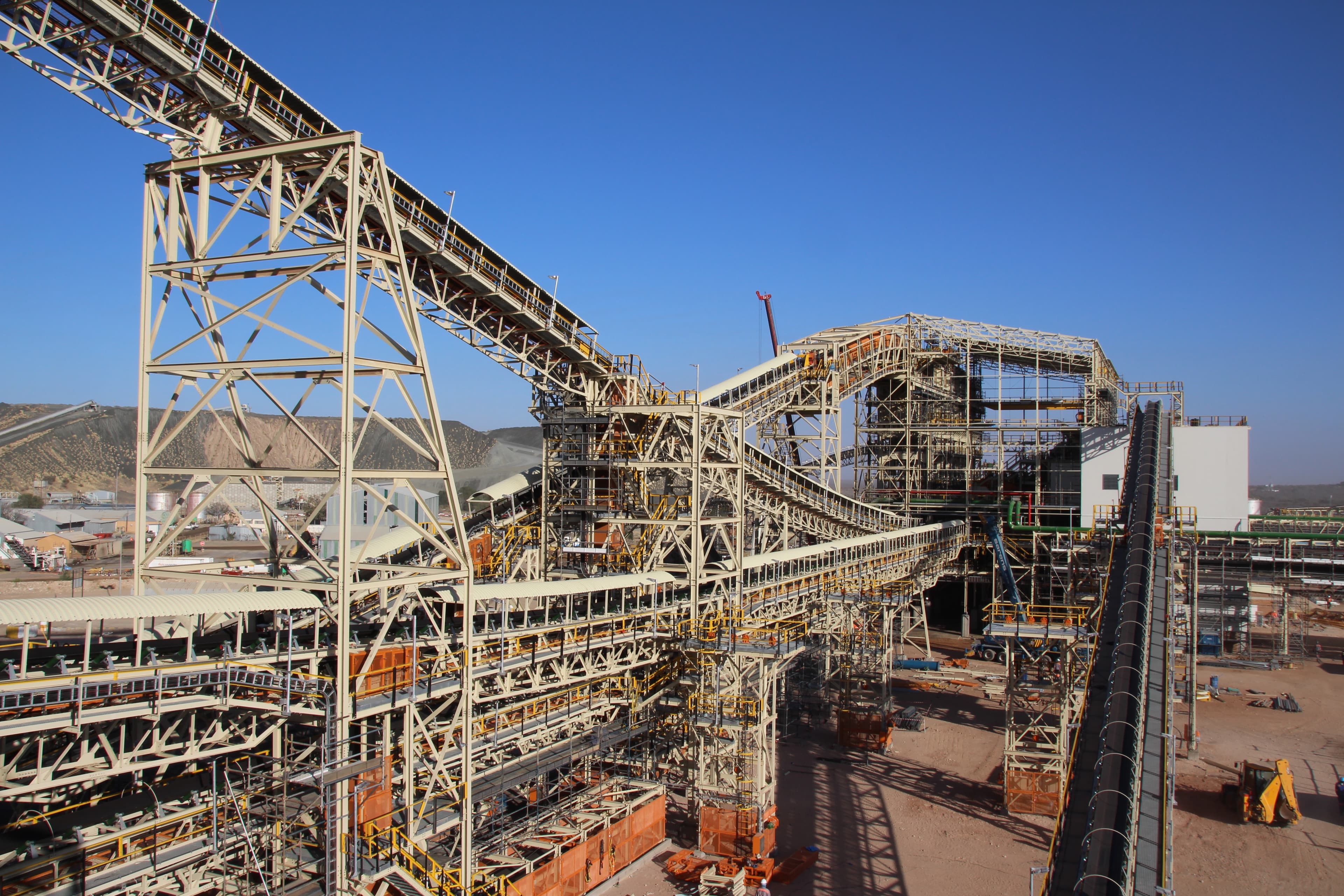
Fluor designed 60 process modules and 106 conveyor and services gantry modules for Debswana Diamond Company’s Letlhakane Mine Tailings Resource Treatment Project in Botswana. The project will extend the Letlhakane operation’s life-of-mine by 25 years.
2017
Fluor and Suncor groups closely aligned on fabrication priorities
&w=3840&q=75)
2017: Fluor and Suncor groups closely aligned on fabrication priorities
&w=3840&q=75)
Fluor performed engineering, procurement, fabrication and construction for the Fort Hills Utilities Project in Alberta, Canada. As part of this scope, we managed module fabrication and shipment of the modules, all of which were fabricated near Edmonton, Alberta. Engineering and construction personnel were integrated into the fabrication teams to support construction-driven execution through the phases. The 95 modules were fabricated and shipped in 10 months.
2020s
Fluor applies modular construction across industries and around the world.
2021
Largest iron ore processing facility ever built in Western Australia
&w=3840&q=75)
2021: Largest iron ore processing facility ever built in Western Australia
&w=3840&q=75)
Fluor completed our construction delivery scope on budget and on schedule for BHP’s $3.6 billion South Flank iron ore project, contributing to the delivery of first ore. The project was one of the largest iron ore processing facility ever built in Western Australia and one of the largest iron ore processing hubs in the world. We provided engineering, procurement and construction management support on the project, which includes an 80-million-ton-per-year crushing and screening plant, state-of-the-art overland conveyor systems and rail-loading facilities.
2023
Ground Breaking at Major Pharmaceutical Manufacturing Facility
&w=3840&q=75)
2023: Ground Breaking at Major Pharmaceutical Manufacturing Facility
&w=3840&q=75)
The Lebanon Project (LP1) was a $3.7 billion investment by Lilly expected to create up to 700 new jobs. We were responsible for engineering, procurement and construction management on LP1's eight buildings encompassing more than 1.4 million square feet including a peptides complex, small molecule and oligonucleotides manufacturing, central utility building, tank farm and support facilities. The project incorporated almost 200 truckable modules into the design that would be assembled at multiple assembly yards in the US and Puerto Rico.
2023
215 modules fabricated and transported to LNG Canada site
&w=3840&q=75)
2023: 215 modules fabricated and transported to LNG Canada site
&w=3840&q=75)
Working with our joint venture partner JGC Corporation, Fluor delivered EPFCC services for the LNG Canada project. This was the largest self-perform construction project for our Energy Solutions group. Upon completion, this facility would help meet the world’s rising energy demand and displace carbon-intensive forms of energy such as coal.
The construction process was unique due to the cost-effective modular approach. Large and complex modules were assembled by several existing local and international fabrication yards and transported to site, minimizing construction congestion and disruptions in the community. In total, 215 modules were built and transported to the site, with the final module from Zhuhai, China, received at the site in July 2023.
2025
Completion of the Future Growth Project (FGP)
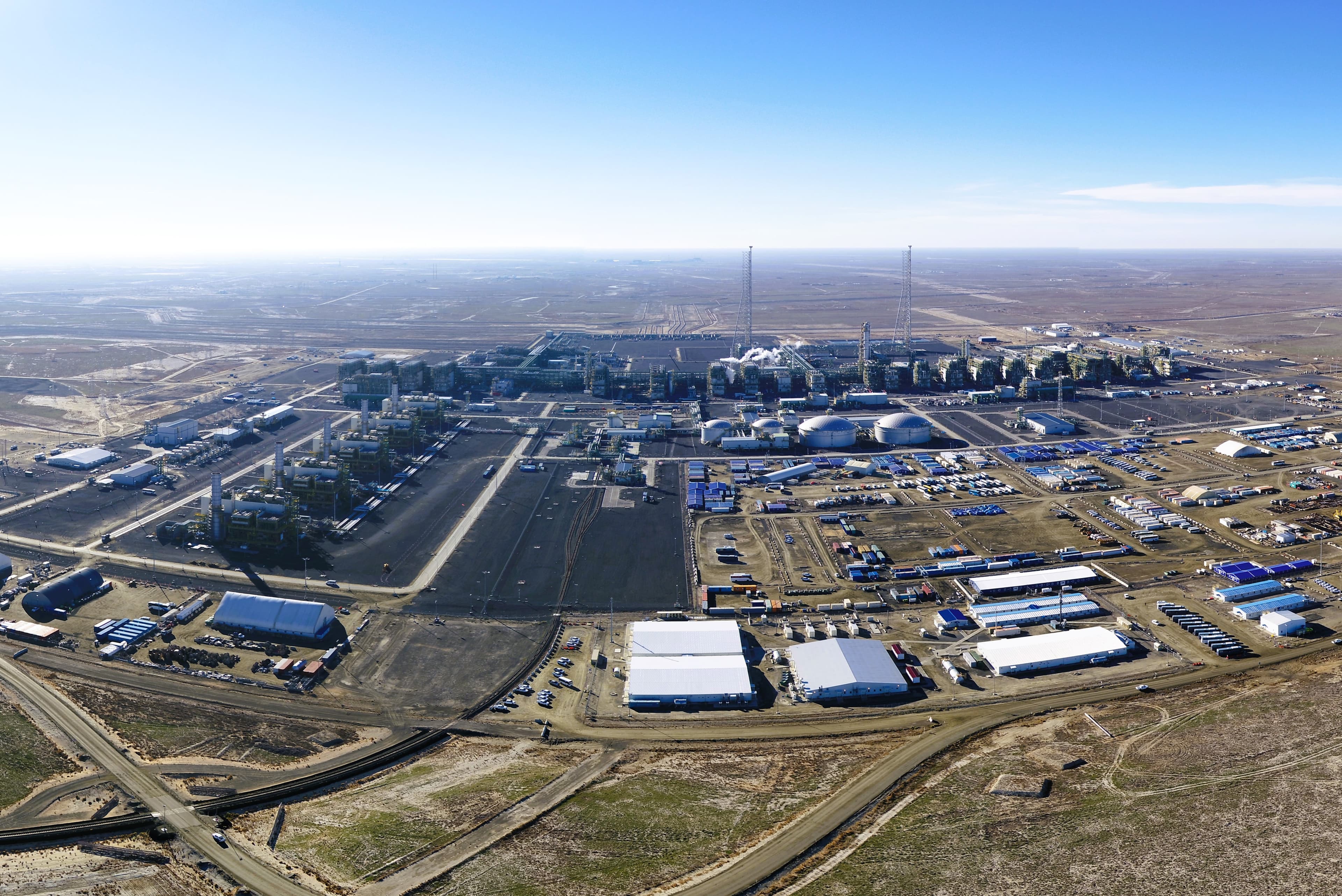
2025: Completion of the Future Growth Project (FGP)
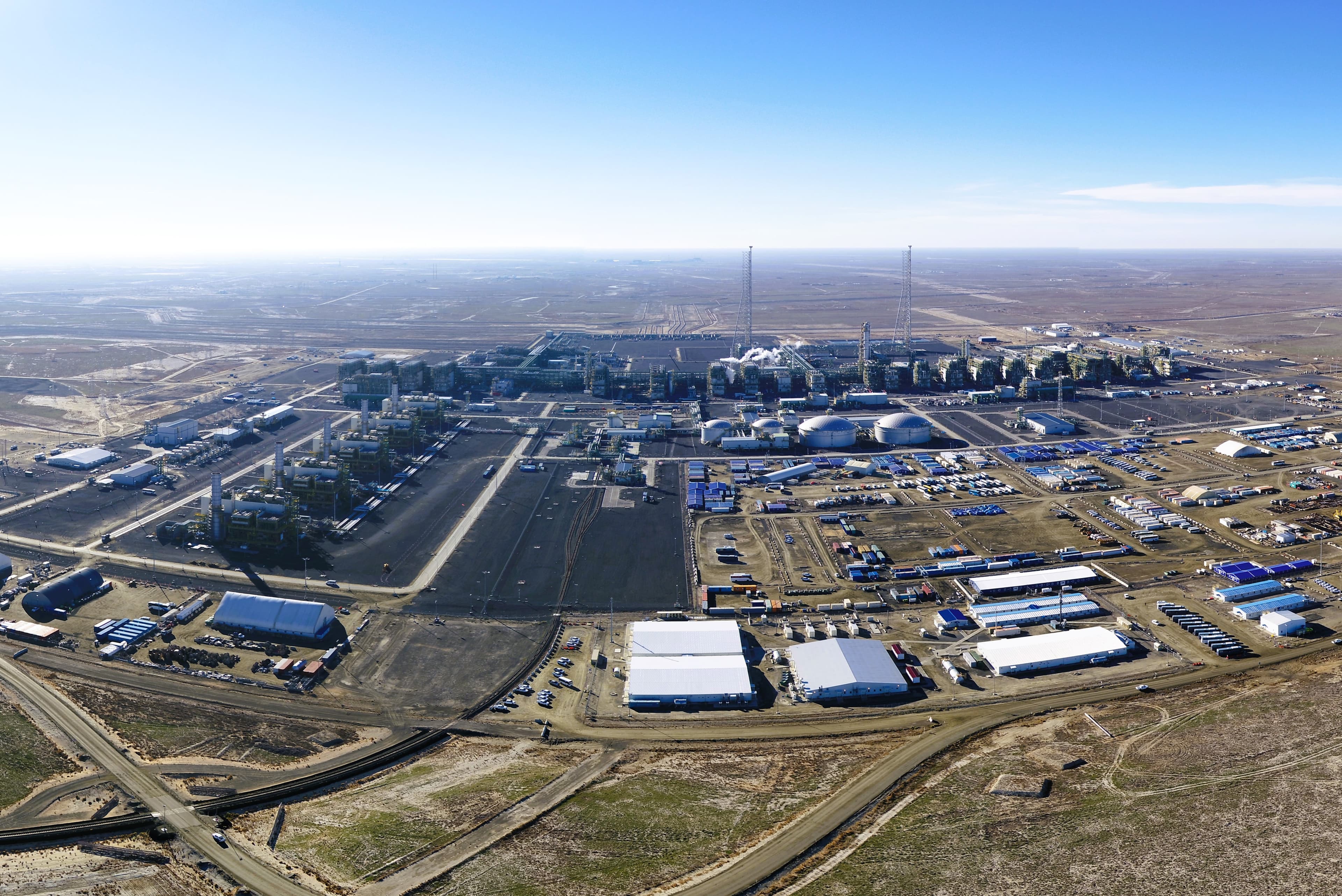
Fluor’s joint venture, KPJV, provided detailed engineering, procurement and construction management support services for the Future Growth/Wellhead Pressure Management Projects in Western Kazakhstan. The project entailed 230,000 tons of modules shipped from Korea to Tengiz over three sea lifts.