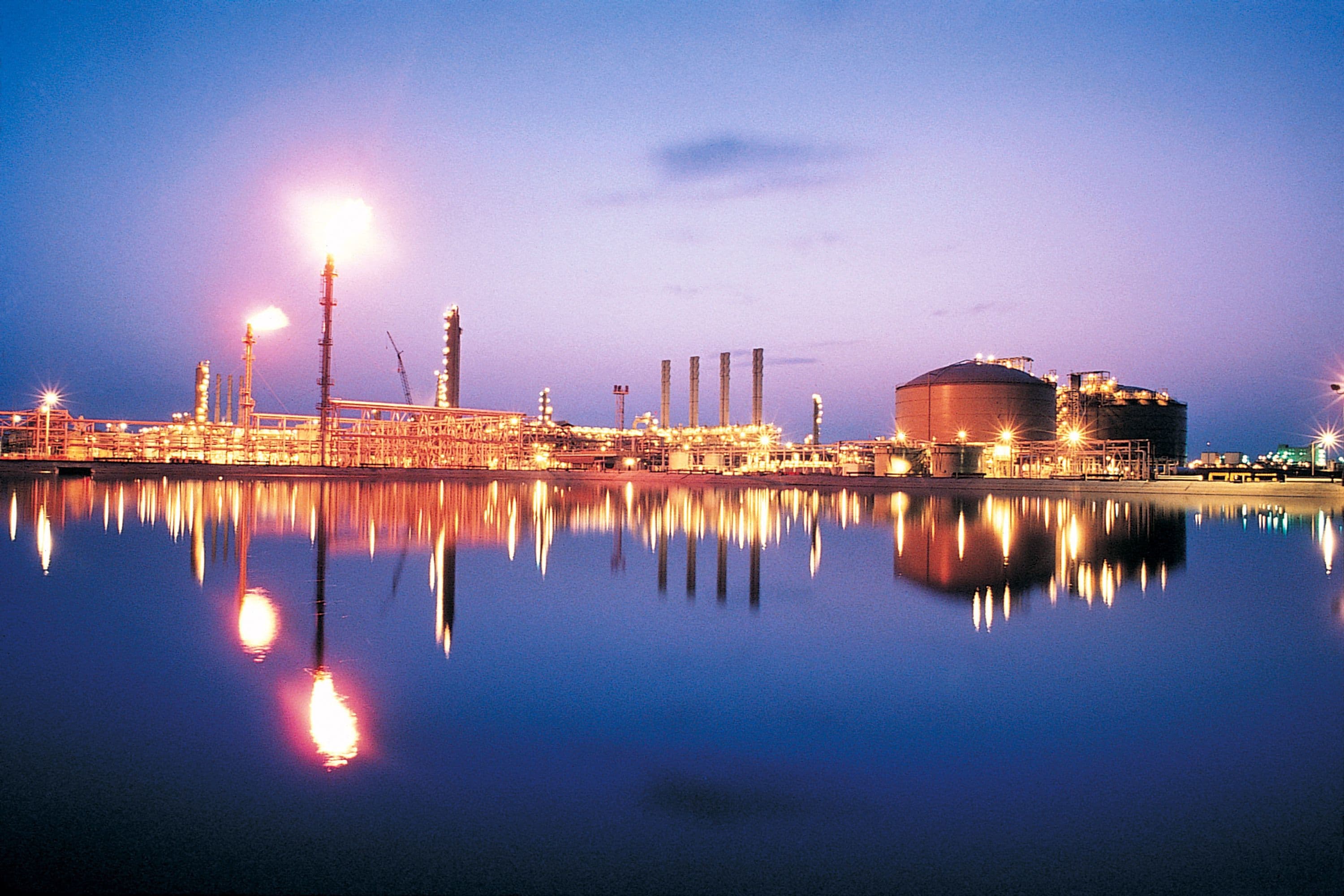
SADAF Petrochemical Complex Modular Construction
Client: Saudi Arabia Petrochemical Company (SADAF)
Location: Al Jubail, Saudi Arabia
Business Segment: Energy Solutions
Industry: Chemicals

Executive Summary
Fluor served as the managing contractor on a 500-acre grassroots ethylene-based petrochemical complex for Saudi Arabia Petrochemical Company (SADAF) at Al Jubail, Saudi Arabia.
Approximately 40% of the complex was completed using modular construction, the largest modular project at the time.
Client's Challenge
SADAF is a joint venture between Saudi Basic Industries Corp. (SABIC) and Pecten Arabian Ltd., an affiliate of Shell Oil Company USA.
SADAF wanted to build a grassroots ethylene-based petrochemical complex. The 500-acre complex was to comprise six process units, utility systems, offsites and general auxiliary facilities.
The SADAF project is located in Madinat Al Jubail Al Sinaiyah, or Jubail Industrial City, which is on the Arabian Gulf about seven miles north of the town of Jubail. Jubail Industrial City is a planned, integrated conglomerate of primary industries, secondary and support industries, infrastructure systems and a housing community. Other locations on the site were designated for primary industries and for a full range of secondary and support industries.
The complex was a major part of the downstream investment planned for Saudi Arabia's east coast. It produces ethylene, ethyl-benzene, styrene, ethylene dichloride, chlorine, caustic soda and crude industrial ethanol. It depends, in large part, on feed streams from the gas-gathering project done by Fluor for the Aramco gas program. The complex, in turn, would provide some of the output to feed Al Jubail Petrochemical Company's nearly linear low density polyethylene plant, also a Fluor project.
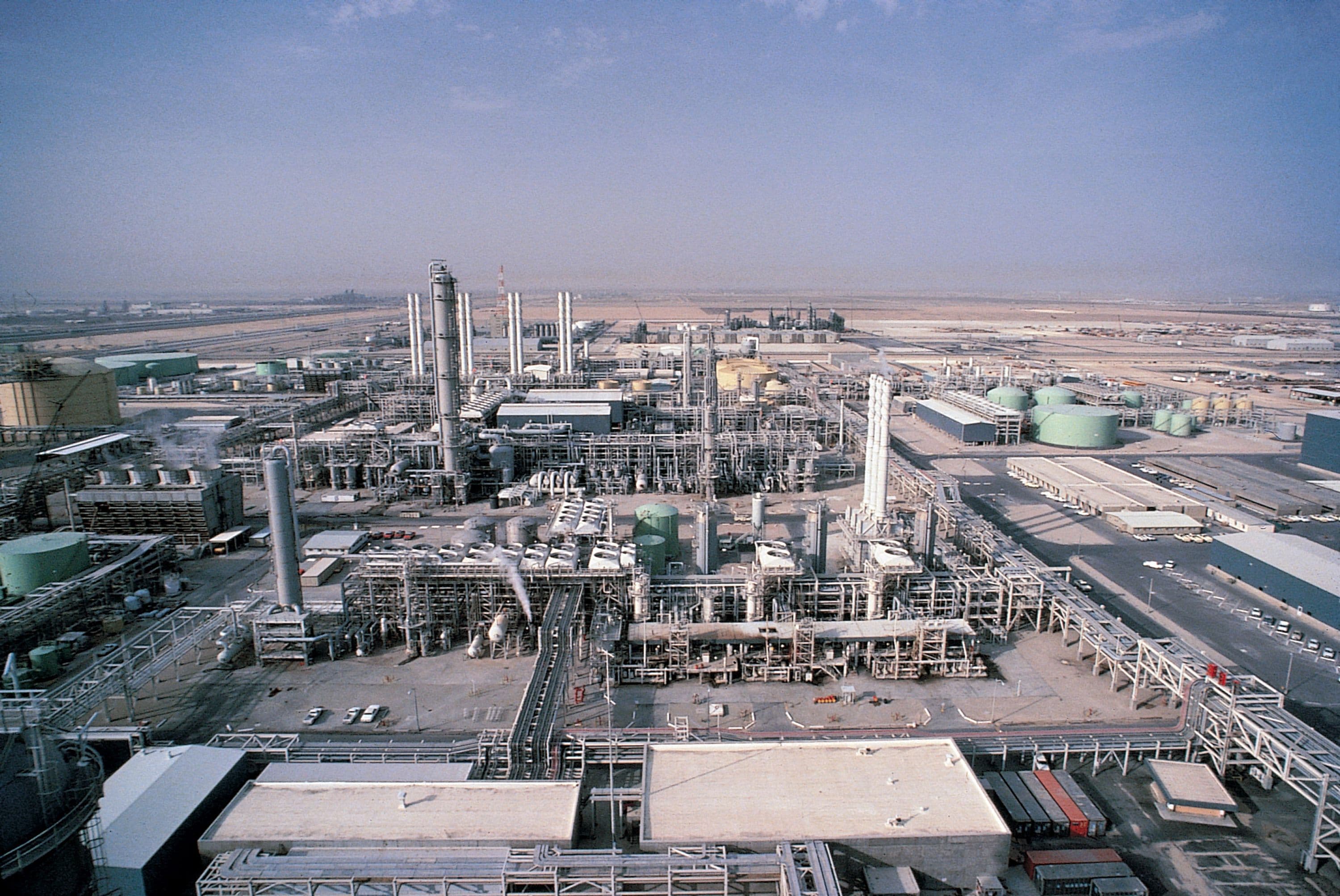
Fluor's Solution
As the managing contractor for SADAF's petrochemical complex, we executed the design of all utility plants, utilities and distribution networks, offsites and general auxiliaries. The process design and detailed engineering on the seven process units were subcontracted. Our scope also included placing orders for equipment and bulk material, maintaining schedule and cost control activities.
Approximately 40% of the project involved modular construction, the largest modular project at the time. About 220 modules, some ranging up to 1,800 tons, were constructed for the process plants, utilities, and offsite complexes. We conducted extensive surveys and evaluations before the module contracts were let. The modules were shipped on 30 voyages from fabricators in Japan over a two-year period.
When the modules first arrived at the jobsite, it took three days to transport them from the Port of Jubail and install them on their foundations. As more modules arrived, productivity improved to the point that modules could be transported and installed in less than a day. Module jacking systems were designed and used to accurately place the modules on their foundations.
The benefits included a reduction in construction work hours by 50%, fewer onsite facilities for construction workers and schedule control enhancement.
The various plants on the petrochemical complex were completed months ahead of schedule.
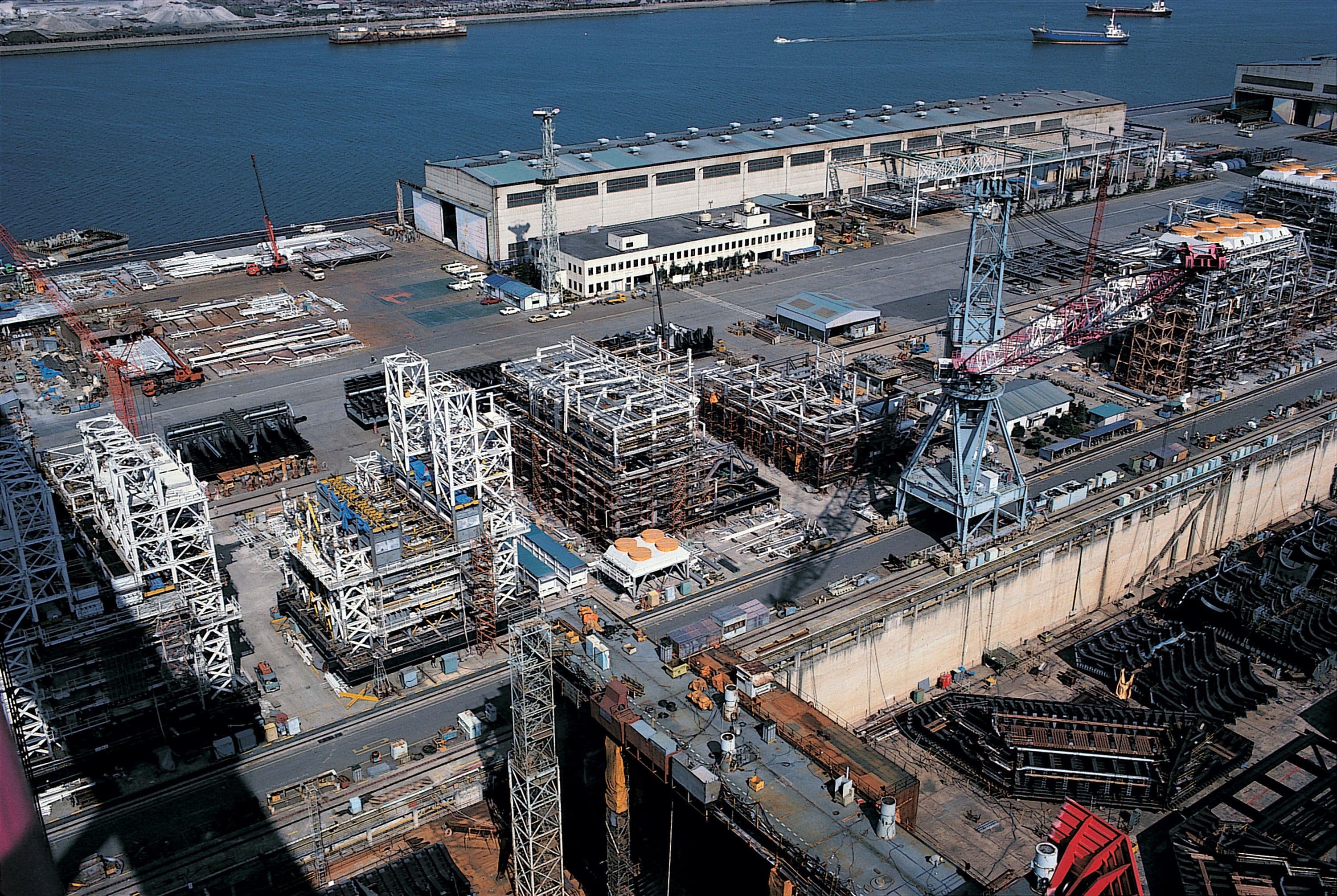
Conclusion
Fluor delivered the mega petrochemical complex to SADAF months ahead of schedule by implementing a 40% modular construction effort, the world's largest modular project at the time.
The cost in modular construction was more than offset by the reduction in construction personnel, onsite facilities and fewer expats into Saudi Arabia.
We used our global experience and procurement network to evaluate and select the fabrication vendors for this massive modular project.
As program manager, we oversaw four major process equipment contracts and the fabrication of nearly 220 modules in Japan for transport to Saudi Arabia.
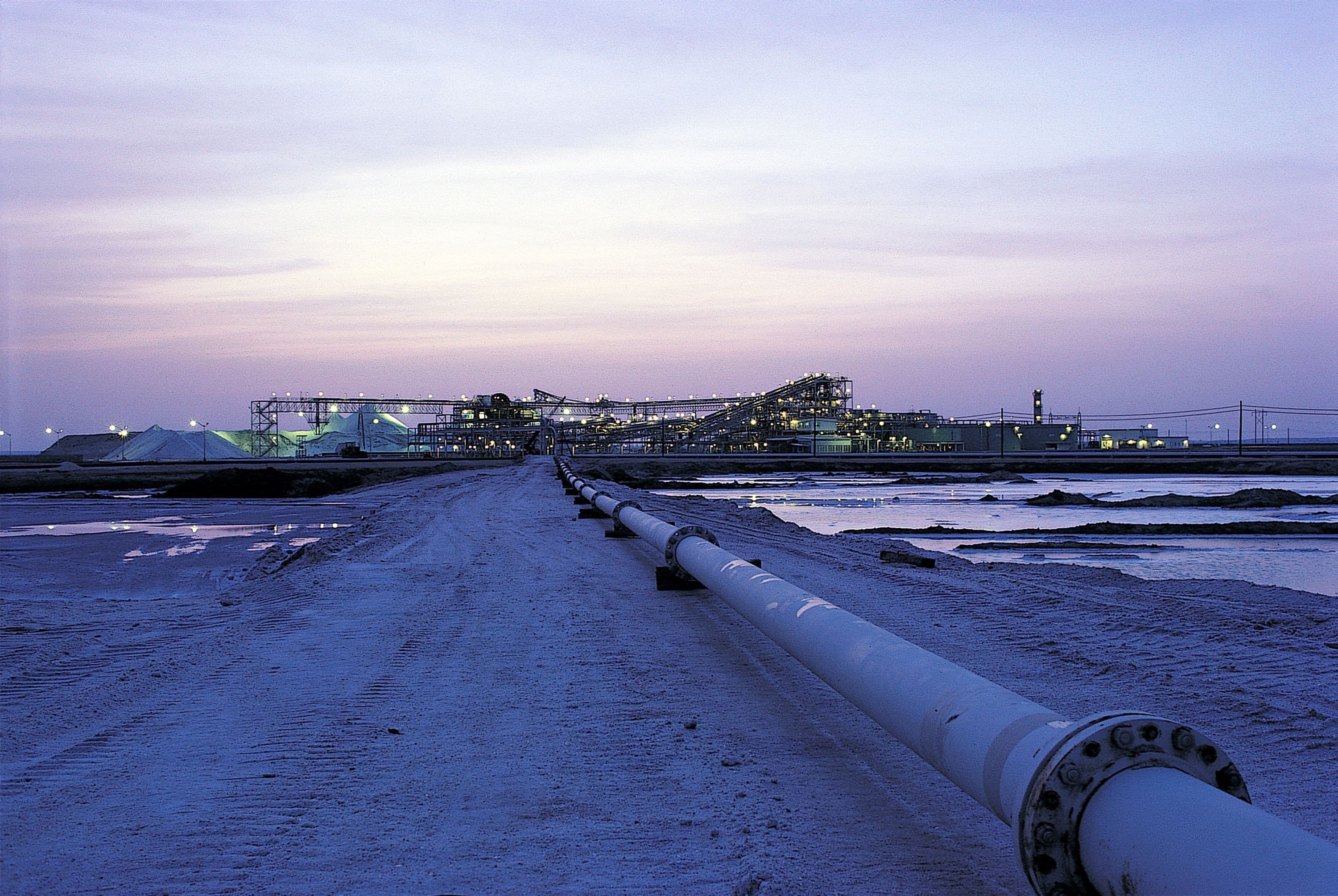
Project Gallery
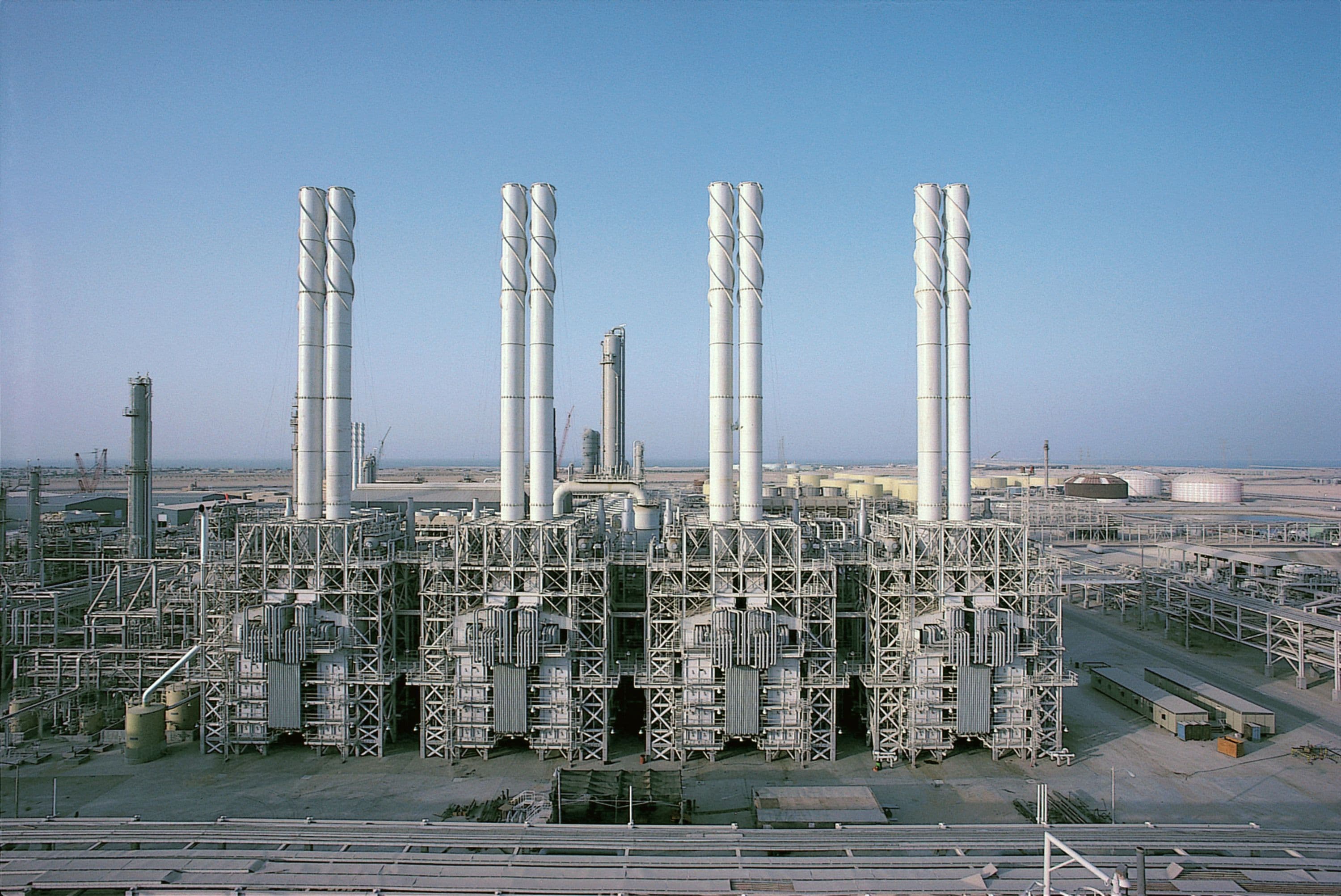
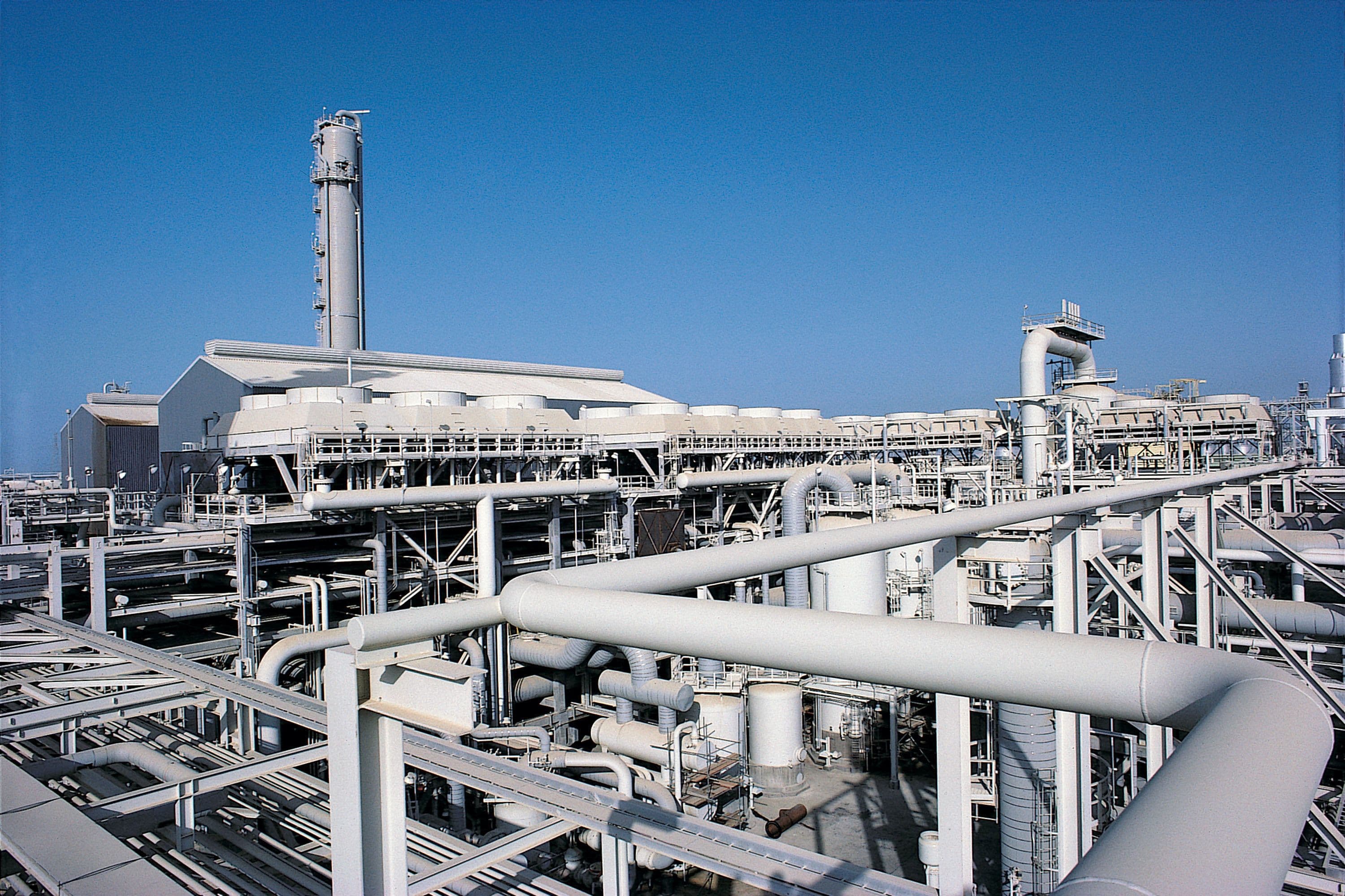
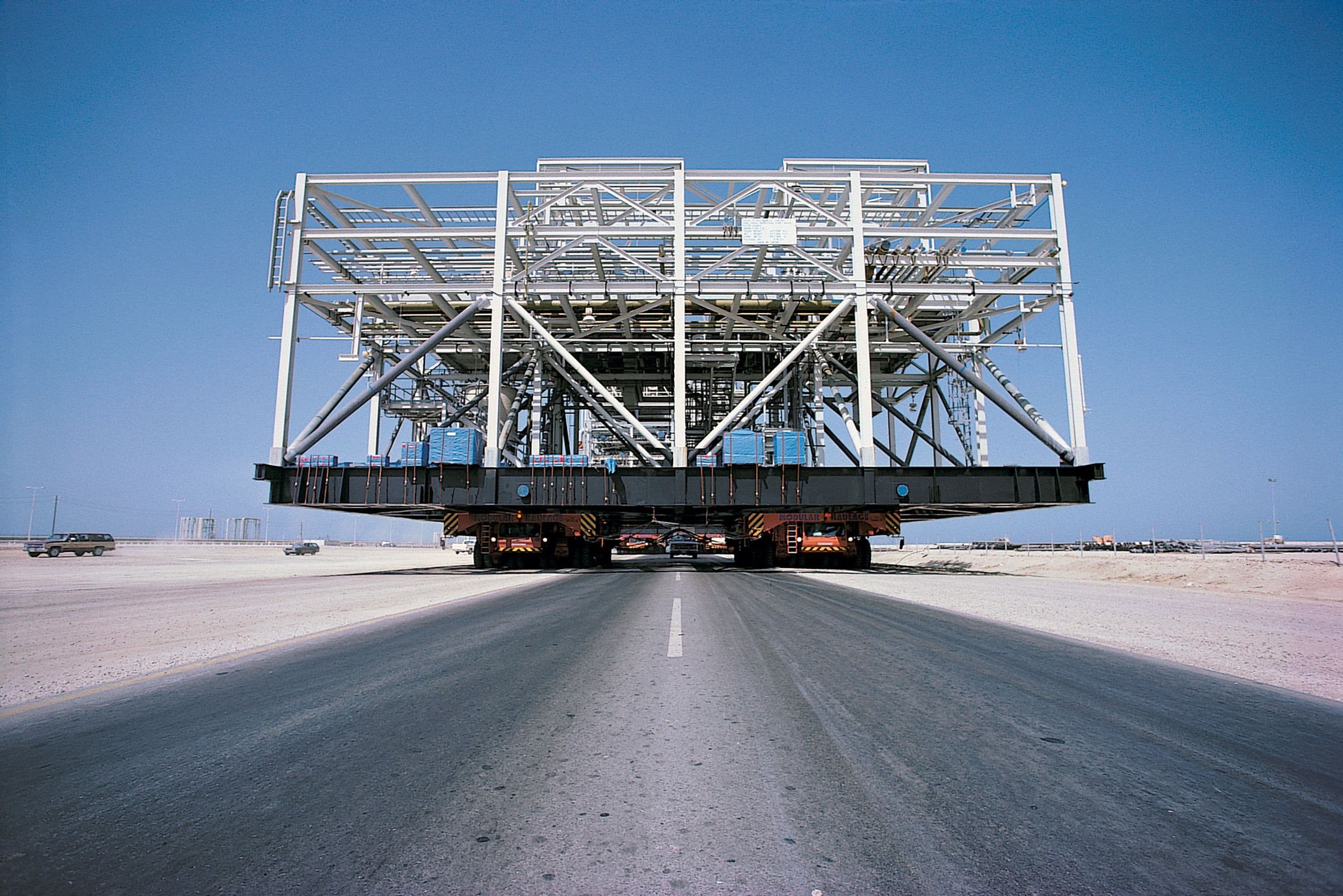
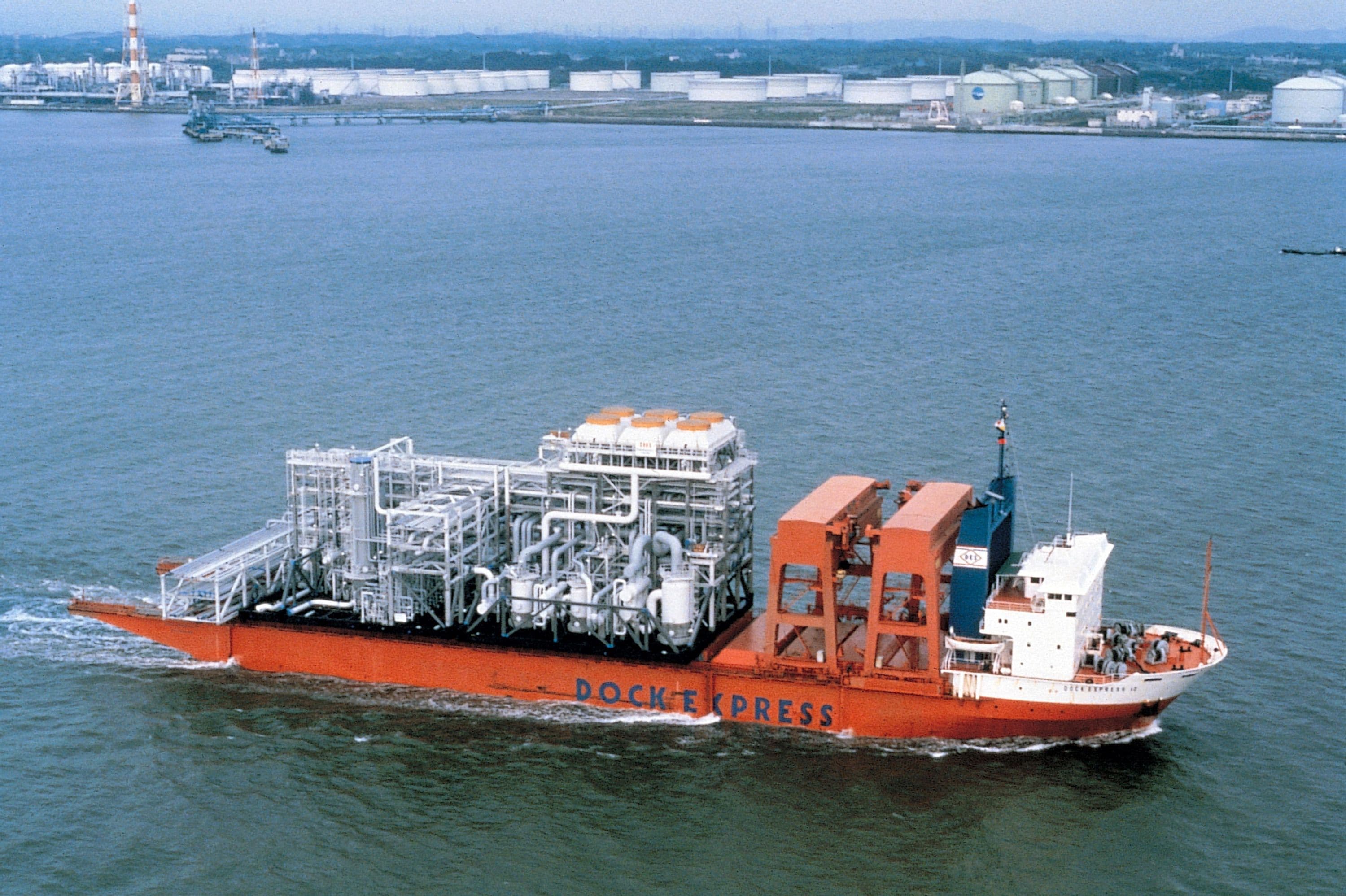
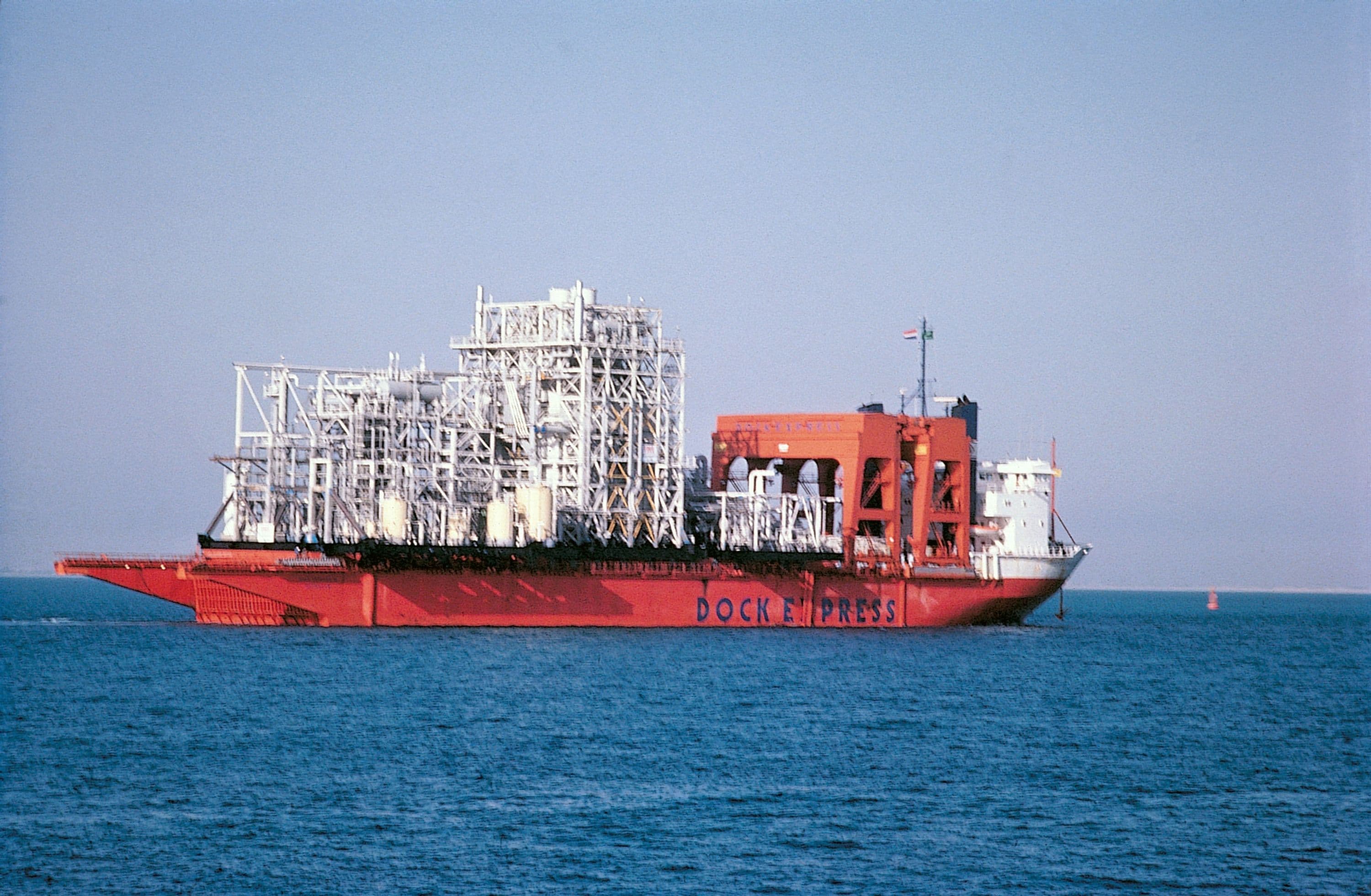
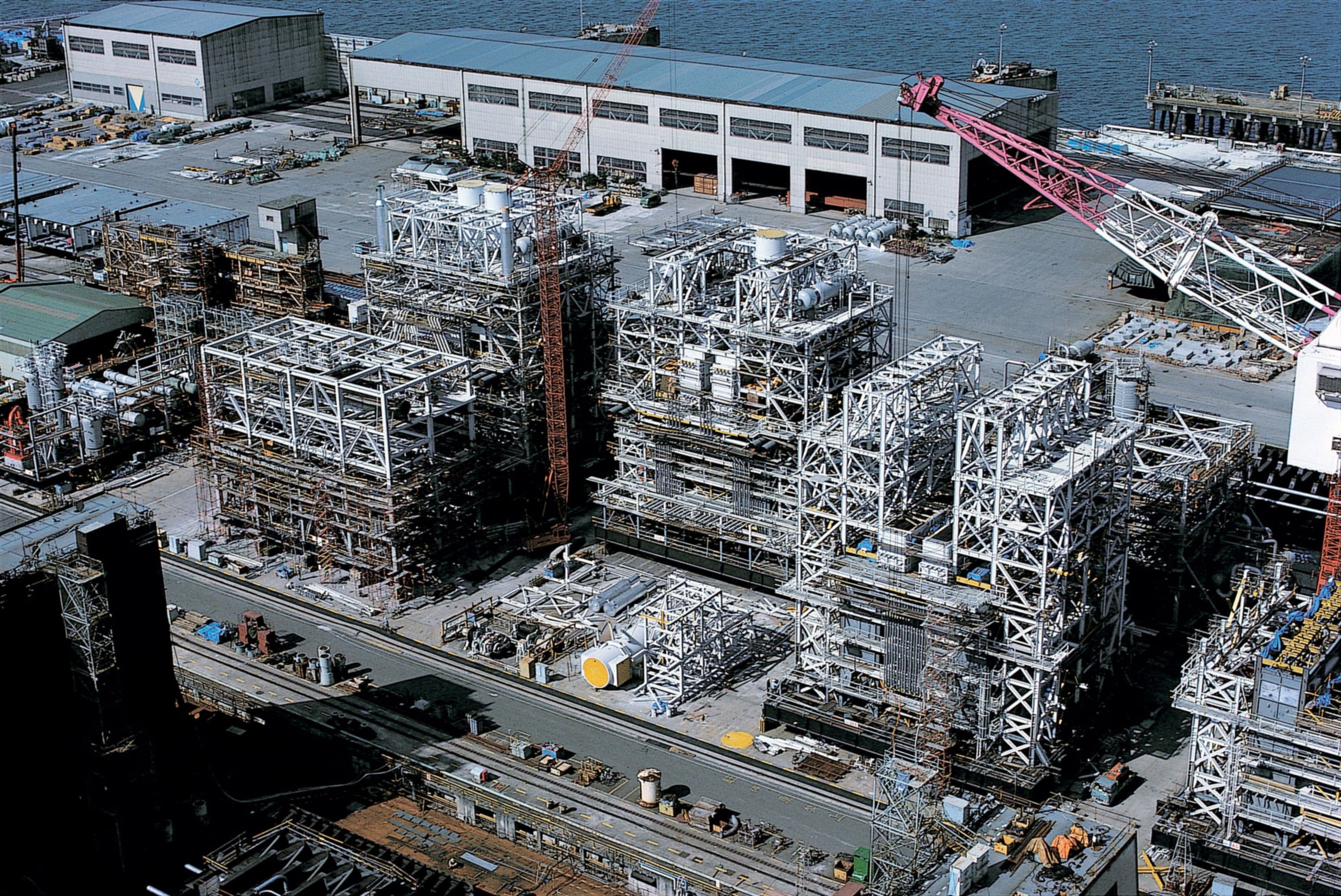
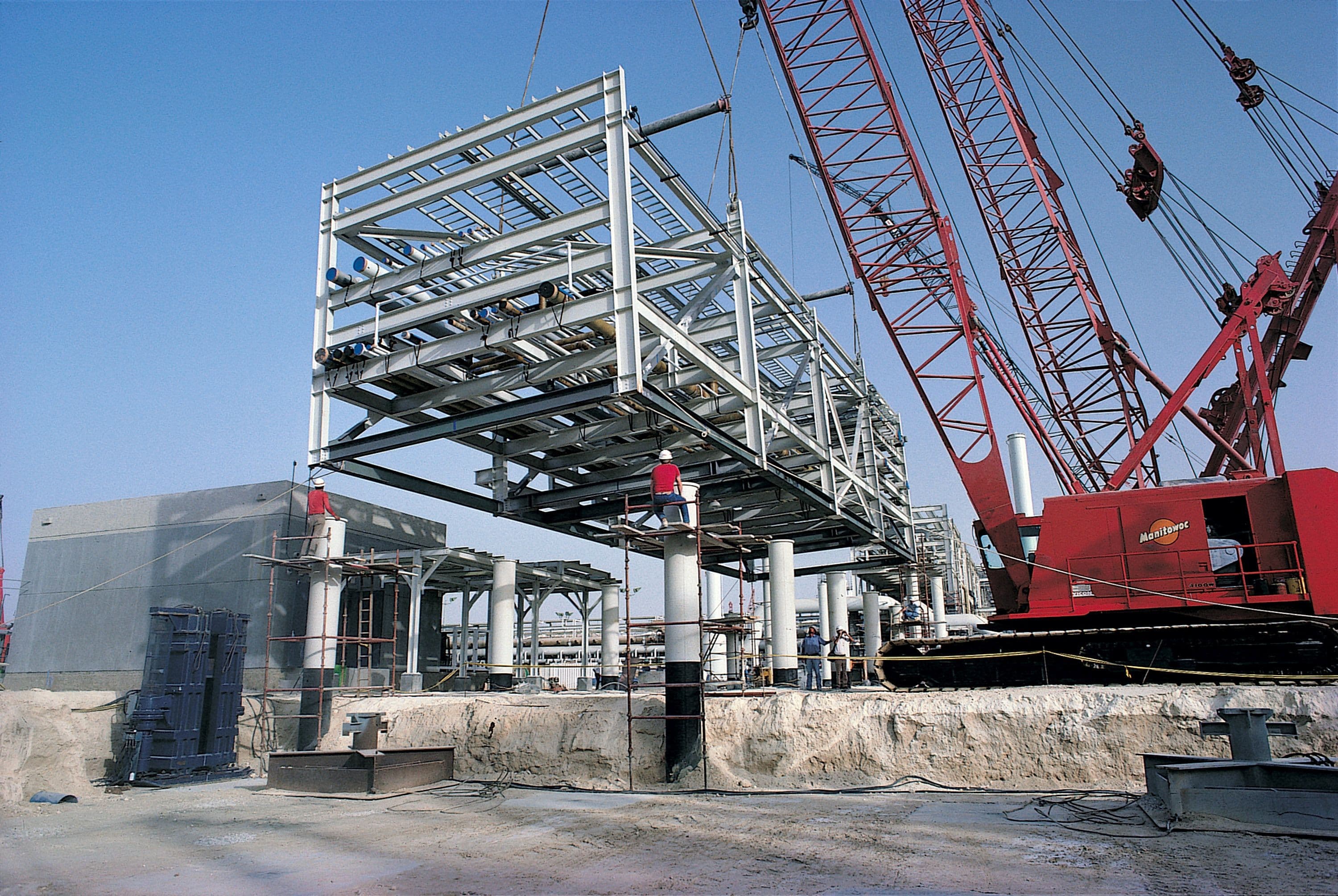
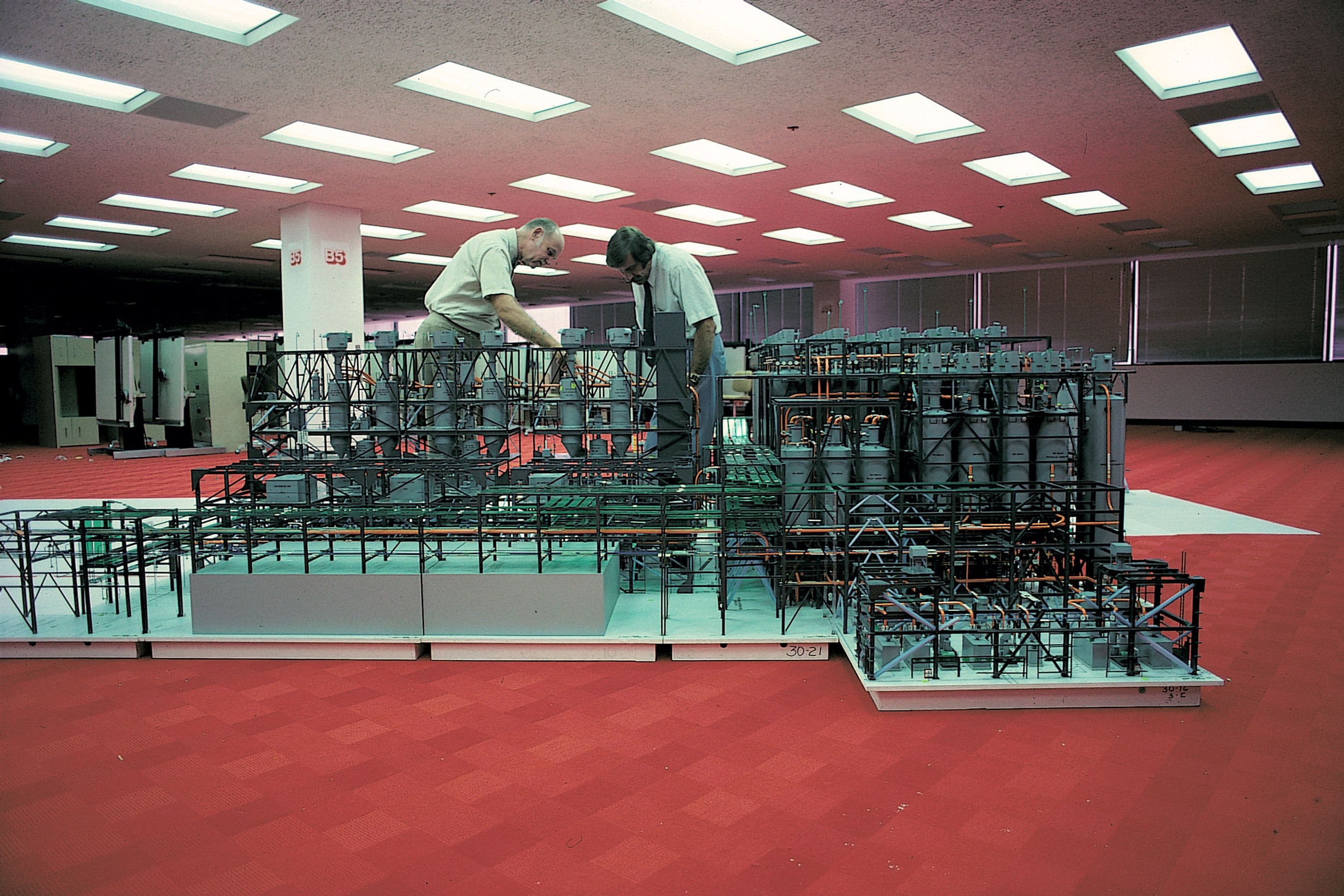
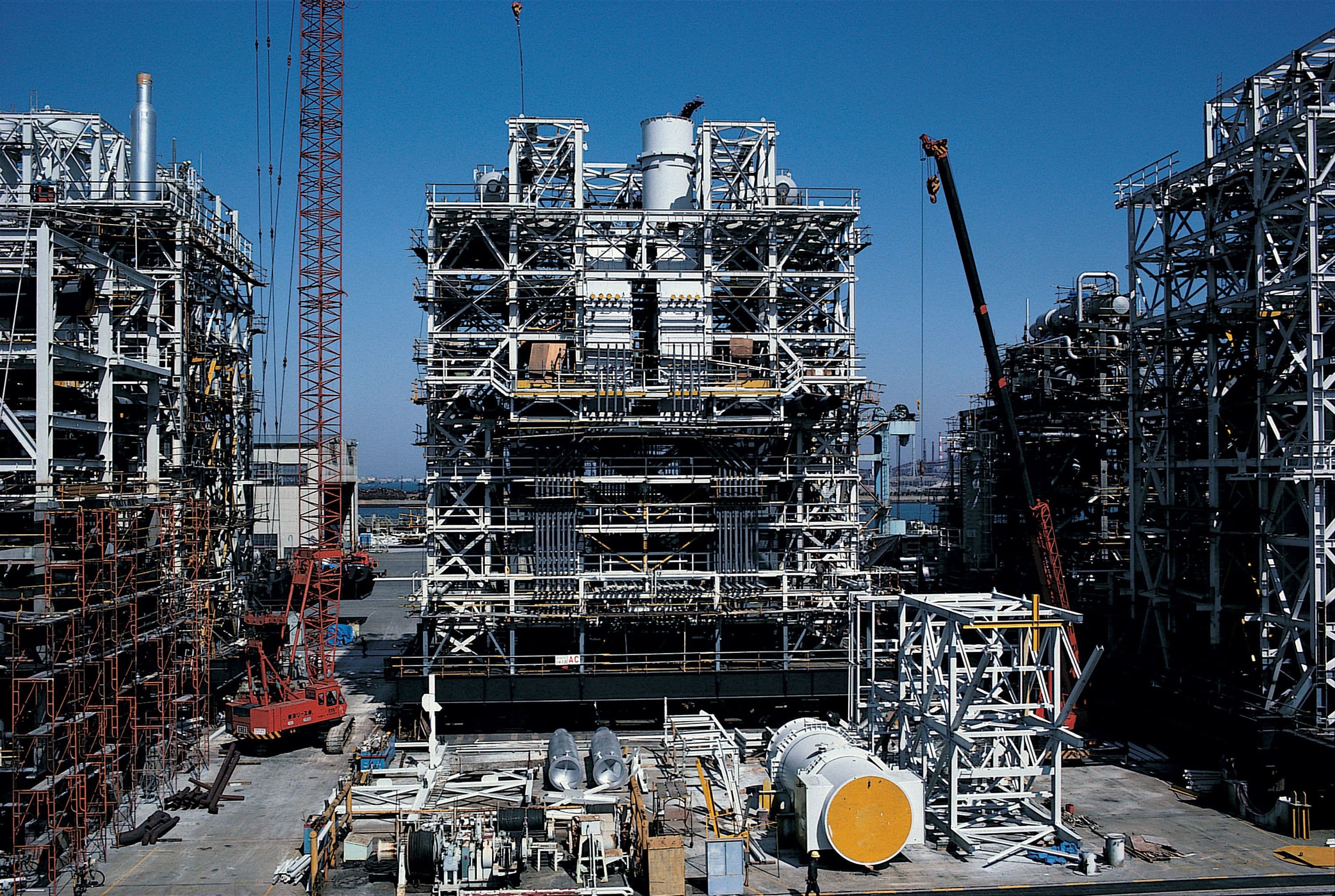
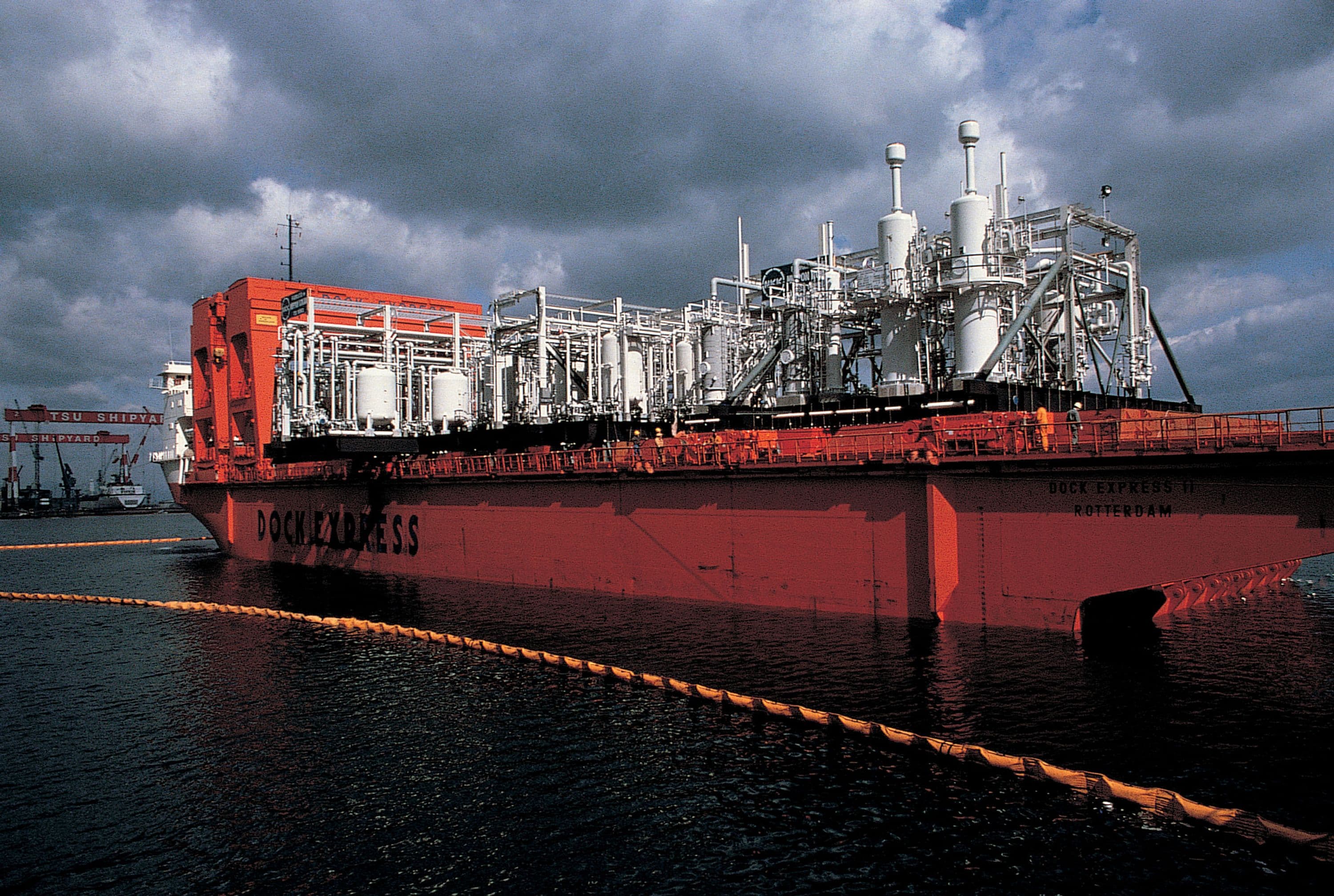
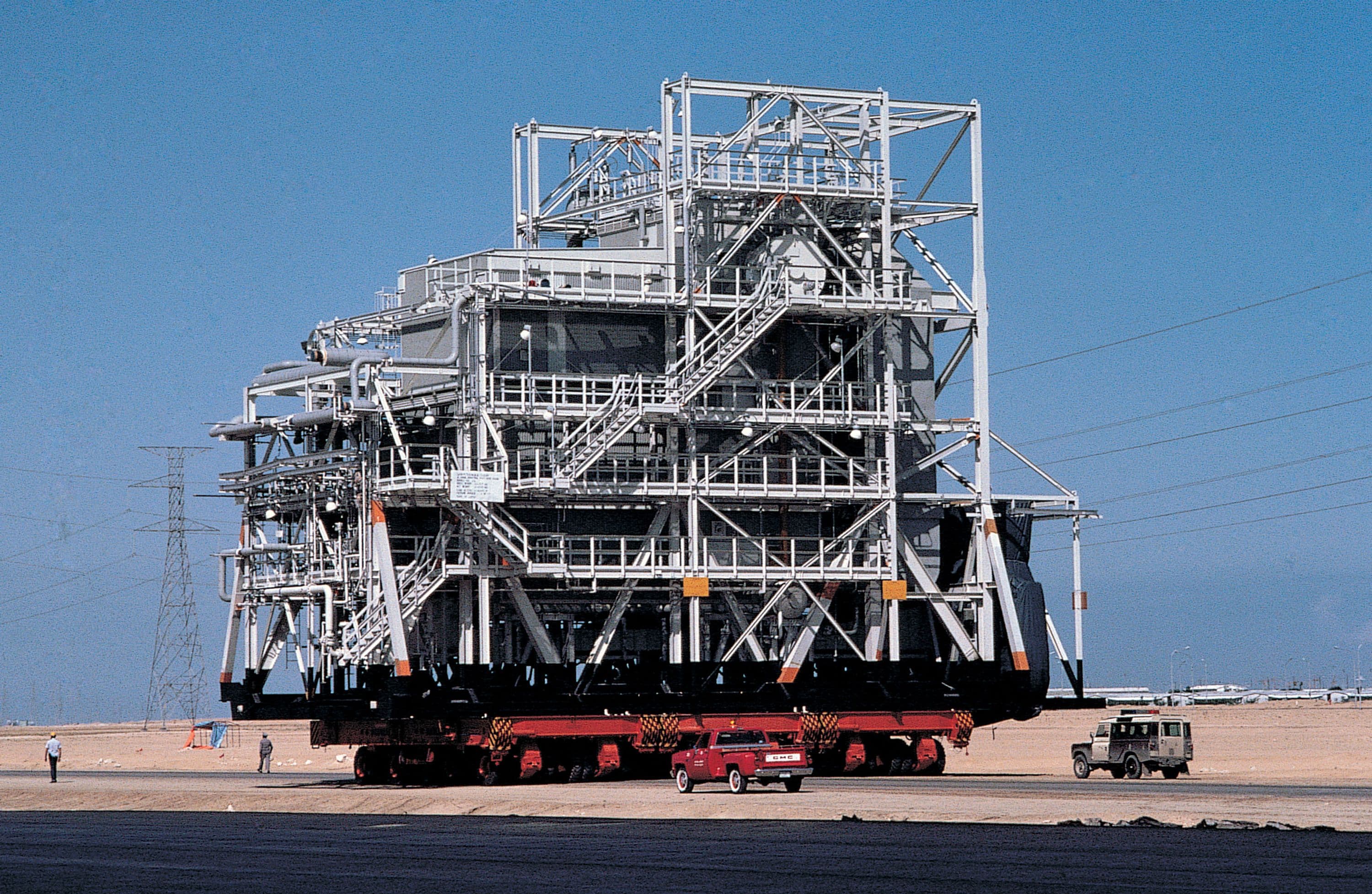