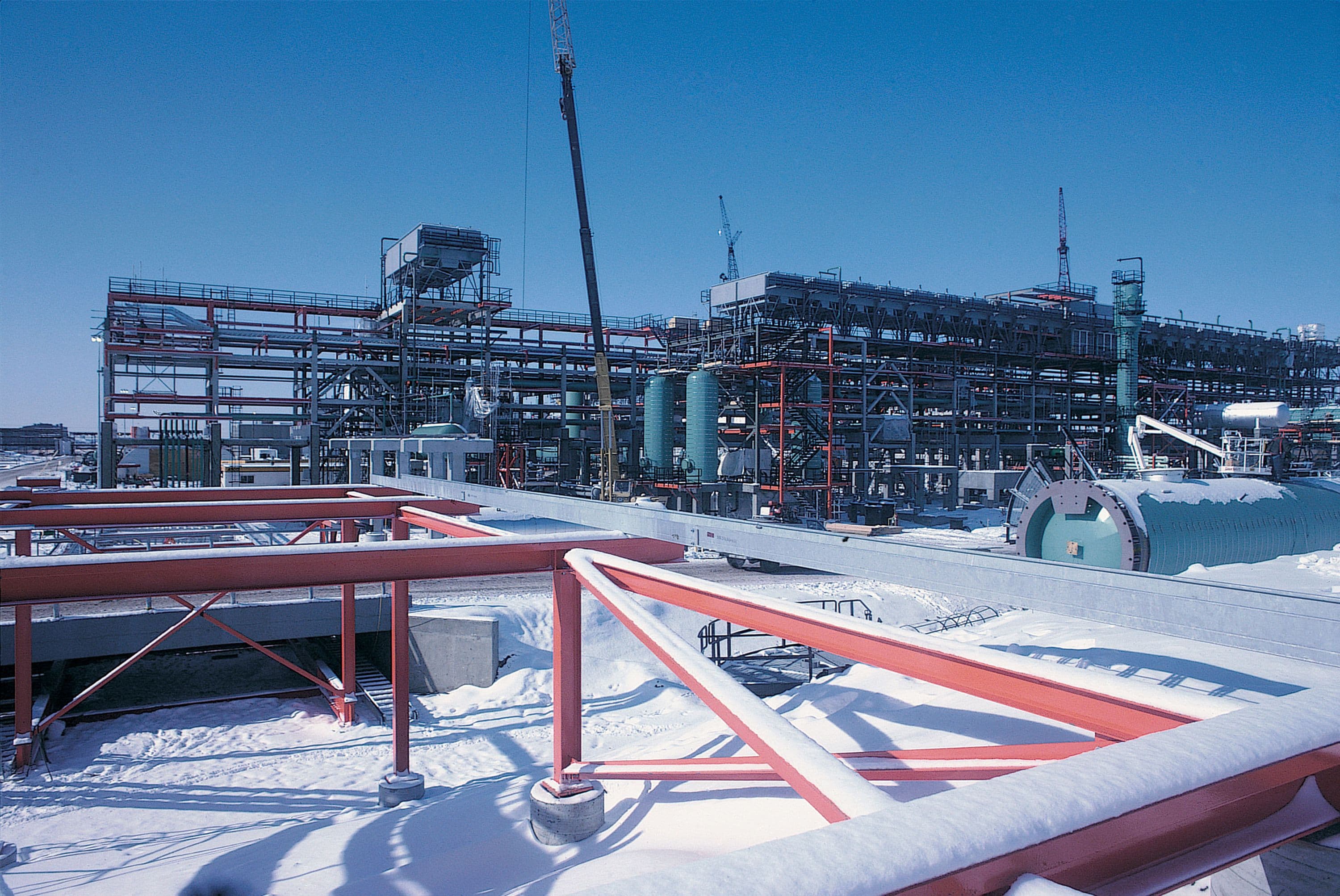
Alberta EnviroFuels MTBE Manufacturing Plant
Client: Alberta EnviroFuels
Location: Strathcona County, East of Edmonton, Alberta,Canada
Business Segment: Energy Solutions
Industry: Chemicals

Executive Summary
Capitalizing on technology never before used anywhere in the world, Fluor performed engineering, procurement and construction on Alberta EnviroFuels' $360 million methyl tertiary butyl ether (MTBE) manufacturing plant. The Canadian-based plant was the first of its kind in North America. Located in Strathcona County, which is east of Edmonton, EnviroFuels' new factory commenced operation in early 1992, achieving an annual production capacity of 530,000 tons of MTBE.
In completing the project, we developed a fast-track execution plan using many innovations. Some of those approaches included the use of pipe rack modularization and erection/transport of field super modules; extensive use of precast concrete for structures; pre-dressing of major columns; shop fabrication of mall-bore piping; and the use of 3D CAD.
Client's Challenge
The plant was designed to minimize all emissions, including fugitive hydrocarbon, MTBE and methanol. Primarily an octane enhancer for gasoline, MTBE became an increasingly important product worldwide as governments legislated the restriction and elimination of lead from gasolines. As such, all safety valves within the plant's process area were vented to the flare systems, and mechanical seals were used in centrifugal pumps and compressors to minimize fugitive emissions.
In an effort to meet all requirements of the Alberta Environment's Clean Air Act, Clean Water Act and Solid Waste Disposal Guidelines, Alberta EnviroFuels' factory was constructed as an environmentally clean facility complete with a manufacturing process producing no hazardous waste.
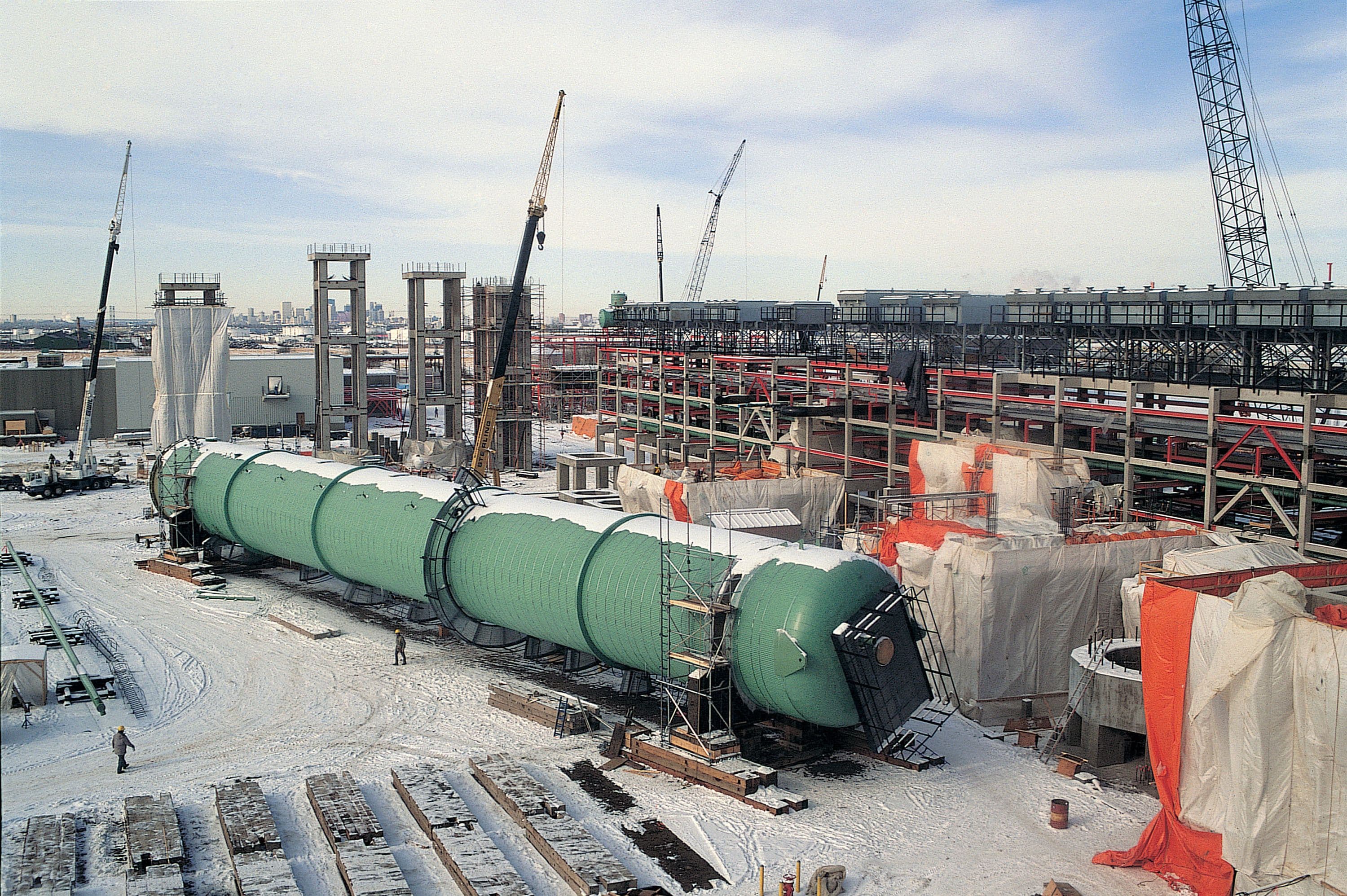
Fluor's Solution
We used innovative approaches to meet the fast-track schedule for the MTBE manufacturing facility:
Pipe Rack Modularization - The pipe rack consisted of precast concrete support bents, structural steel supported pipeways, accessways and overhead air coolers mounted on top of the entire assembly. The lifting of the pre-dressed column structural steel pipeway portion was fabricated in two sections in a modularized manner consisting of accessways, cable trays and fireproofed structural steel. The piping was also complete with insulation and tracing.
Successful Use of Precast Concrete for Pipe Rack - Precast concrete structures were used to minimize site erection time and interference of crafts associated with fireproofing steel structures. Also, precast ladder structures, with connecting beams and table tops, were used to support plant reactors. Additionally, precast structures were used in place of conventional fireproofed heavy steel structures. The ease of assembly over approximately 3½ weeks and the ability to proceed without the need of fireproofing and without inefficiencies due to craft interference were instrumental in completing construction in this area, which was the last to complete due to licensor design changes. This same approach was used successfully for several minor pipe racks with similar benefits.
&w=3840&q=75)
Dressing of Major Columns at Grade - Pre-dressing of columns prior to erection included installation of piping, cabling, ladders and platforms and lighting. This was completed for all six of the project's columns and included trays and reboilers for all except the largest tower, which was limited by crane capacity.
This concept was used for cost savings and safety considerations based on the following:
Maximum height for workers pre-dressing a column was 1.5 column diameters
Virtually eliminated scaffold requirements
Executed more rapidly based on ability of full length of tower available for work and craft workers getting to their jobs more quickly than having to make climbs of increasing height as labor progressed
This approach required a great deal of planning and coordination, particularly as this work had to be executed in parallel with design development to be effective.
Shop Fabrication of Small-bore Piping – Virtually all small-bore piping, down to ½ inch, was pre-fabricated as the accuracy of the 3D CAD system allowed. Significant savings in field installation time and costs were achieved as a result.
3D CAD Design and Construction Planning – We used 3D CAD in the design of the process area, resulting in low levels of rework and allowing approaches such as the shop fabrication of small-bore piping. Use of 3D CAD provided Alberta EnviroFuels the benefits of having the latest design technology without delays in plant completion. The 3D CAD also provided the ability to handle the significant licensor changes expeditiously without having to redesign from scratch.

Conclusion
The execution of this first-class facility, completed on an extremely fast-track schedule while overcoming many significant obstacles, was achieved based on the utilization of innovative construction approaches and project execution strategies.
Meticulous planning, teamwork and unselfish cooperation between design and construction teams also played a large role in the completion of this challenging project.
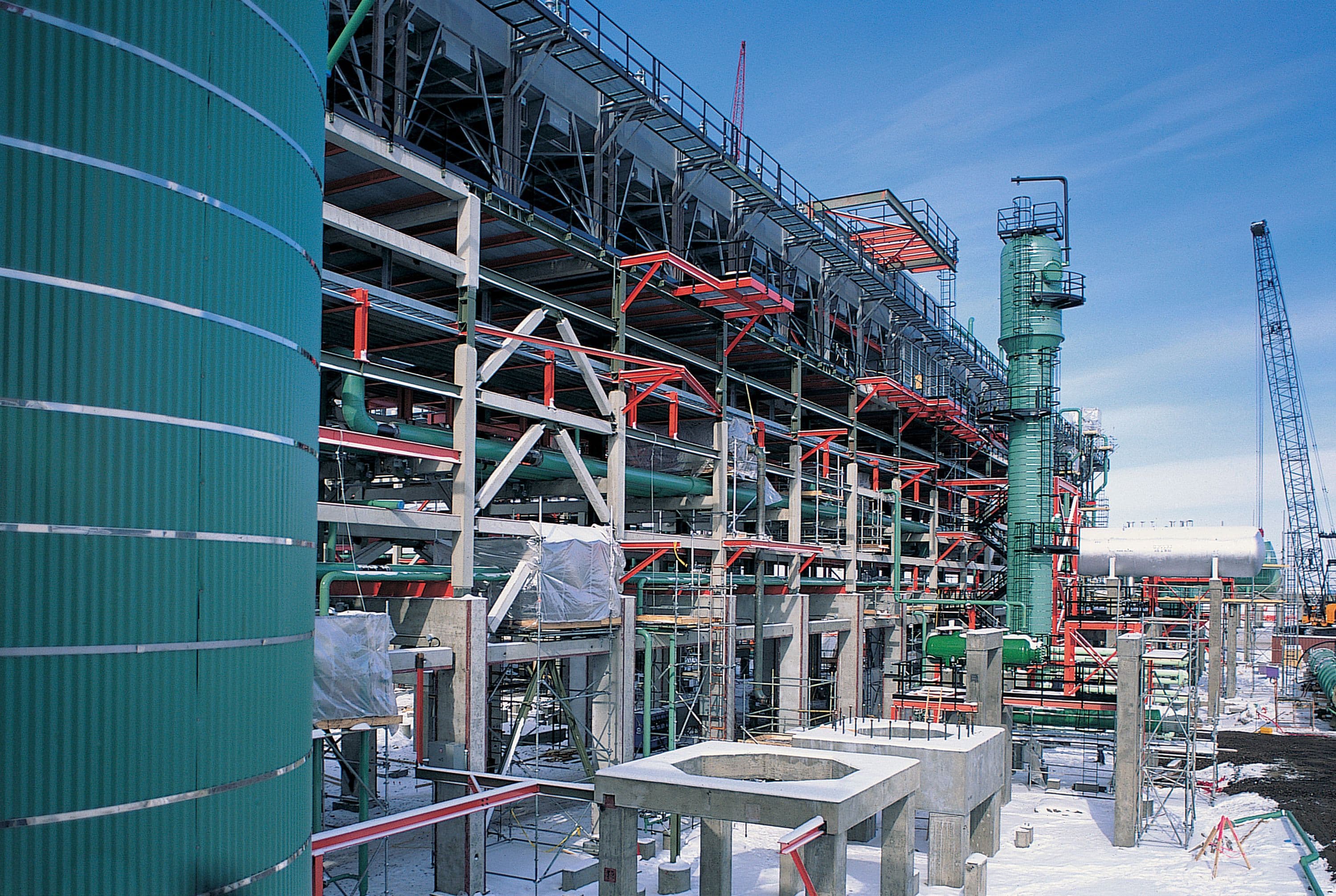