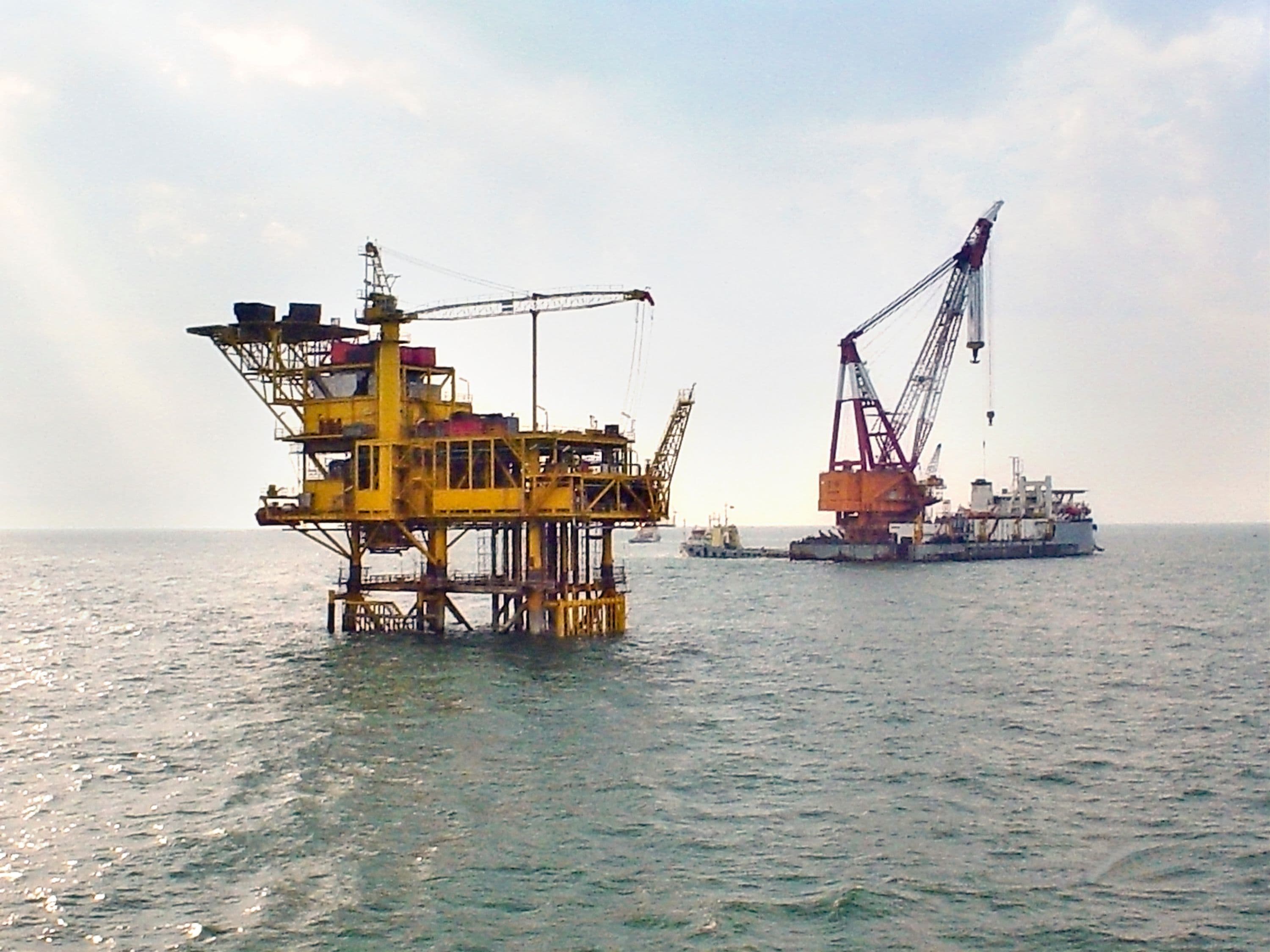
ConocoPhillips China Bohai Bay Phases I & II Offshore Development - Construction
Client: ConocoPhillips China, Inc.
Location: Bohai Bay, China
Business Segment: Energy Solutions
Industry: Fuels

Executive Summary
Fluor was selected by ConocoPhillips China, Inc. to develop the largest offshore oil production facility in Bohai Bay, China. The Bohai Development project, jointly owned by ConocoPhillips China (COPC) and China National Offshore Oil Corporation (CNOOC), involved the development of an oil field with a production capacity of 190,000 barrels per day. The field is located 140 miles offshore in Bohai Bay, the innermost gulf on China’s northeast coast and one of the busiest seaways in the world.
The full field development project included six remote wellhead platforms, central riser/utilities platform, a soft yoke mooring tower and a double-hull floating production storage and offloading (FPSO) system with crude oil storage capability of 2,000,000 barrels.
Fluor's Solution
This was the first large-scale offshore project in the world to use disk stack centrifuges to separate water and sand from the crude oil. This system was selected, over the more traditional electrostatic treating, for its higher efficiency and greater flexibility with changing crude/water ratios.
In spite of using wellhead completion techniques to minimize solids production, about 72 metric tons of sand per day could potentially be produced mixed with crude emulsion. On the FPSO vessel, sand is separated, collected and slurried using a one-of-a-kind solids handling system for reinjection into subsea disposal wells. As a secondary alternative, the sand can be dewatered in decanter centrifuges prior to being taken to shore in tote bins.
For the FPSO topside modules, which are subject to dynamic loading as the hull moves and flexes, we used state-of-the-art spectral fatigue analysis to calculate the stress concentration factors on critical structural connections. We also designed flexible elastomeric bearings to rest the modules on the hull supports, a simpler design pioneered by Fluor for FPSOs that avoids the precision machining and exotic materials of traditional friction pendulums or bearing pots.
The FPSO is one of the largest in the world measuring 320 meters long by 63 meters wide, with the ability to process 190,000 barrels per day and store two million barrels.
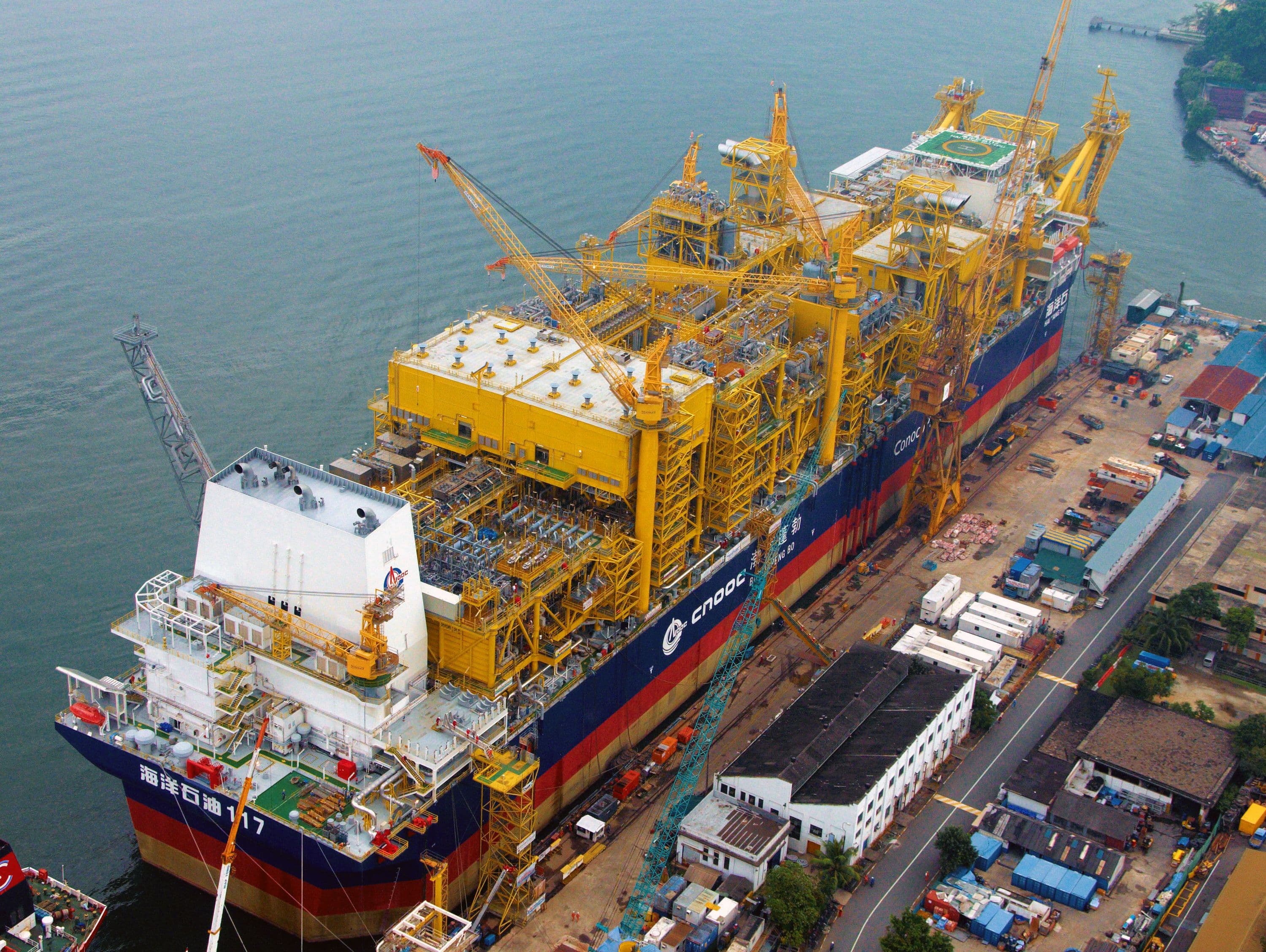
Conclusion
The task force, distributed among Fluor's Houston, Manila and Shanghai offices, achieved significant engineering cost savings through work sharing, a disciplined value awareness program and efficiencies obtained in the repetitive design of the fixed platforms.
The safety record for this project was remarkable, with zero lost time incidents on more than 3.4 million Fluor work hours.
The result is a world-class offshore development project that was named Platts' 2010 Engineering Project of the Year in the “Premier Projects” category and received the ConocoPhillips SPIRIT award.
The Bohai Bay project also received Fluor's Hugh Coble Project Excellence Award in 2009. The award is based on outstanding performance in several areas, including safety, value creation and client and community relations.
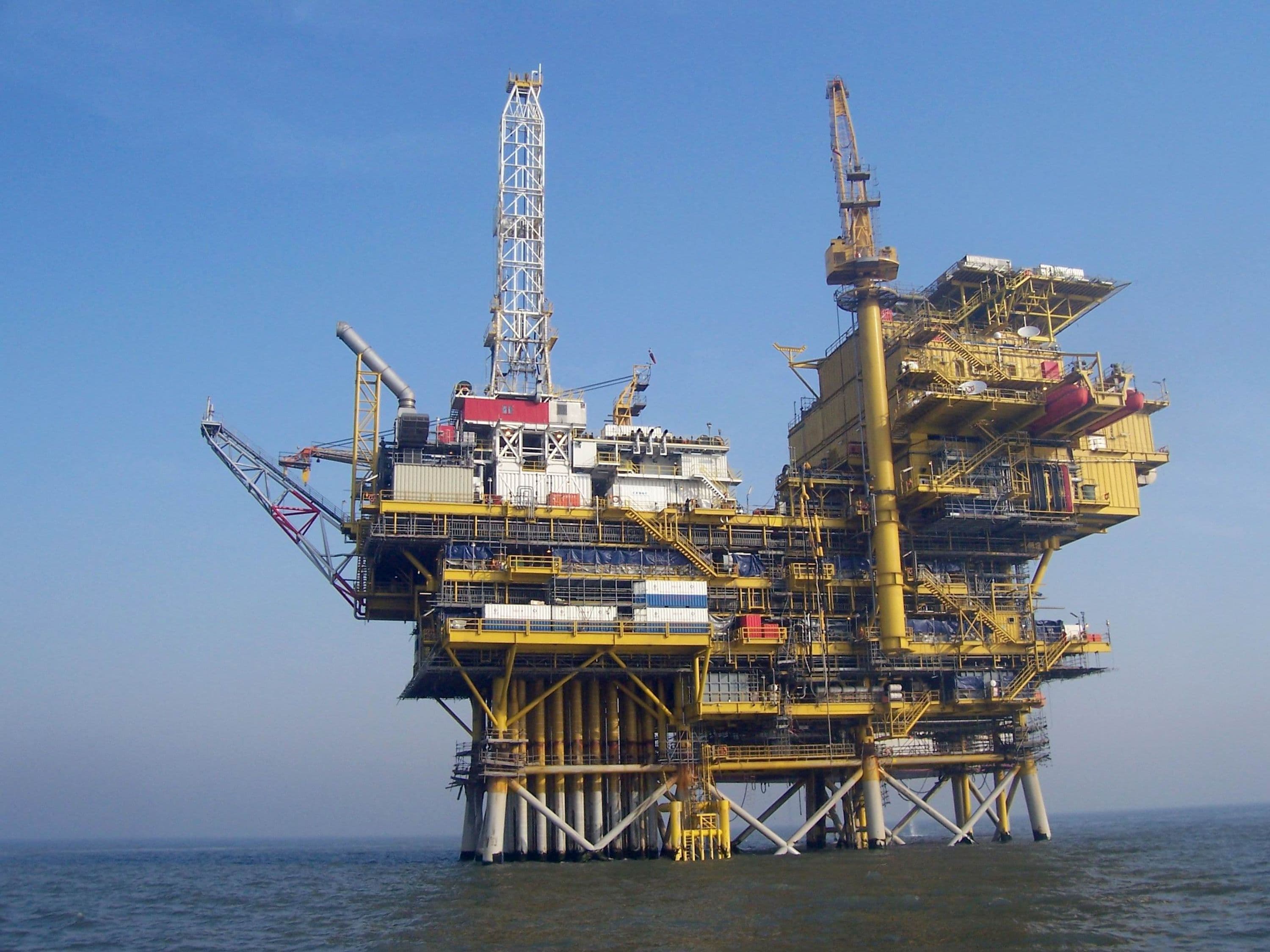