Chemicals & Petrochemicals Timeline
Building a Better World With Chemicals & Petrochemicals
For nearly 80 years, Fluor has designed and built major chemicals and petrochemicals facilities around the world. Fluor projects have included consulting and design-build of new facilities as well as plant revamp services.
Clients look to Fluor for expertise in commodity and specialty chemicals, polymers and petrochemicals. This experience also extends to renewables, where Fluor has earned a leading position in solar energy.
1940s
Fluor diversifies into the chemicals and petrochemicals industry.
1946
Fluor diversifies into the Chemicals and Petrochemicals industry
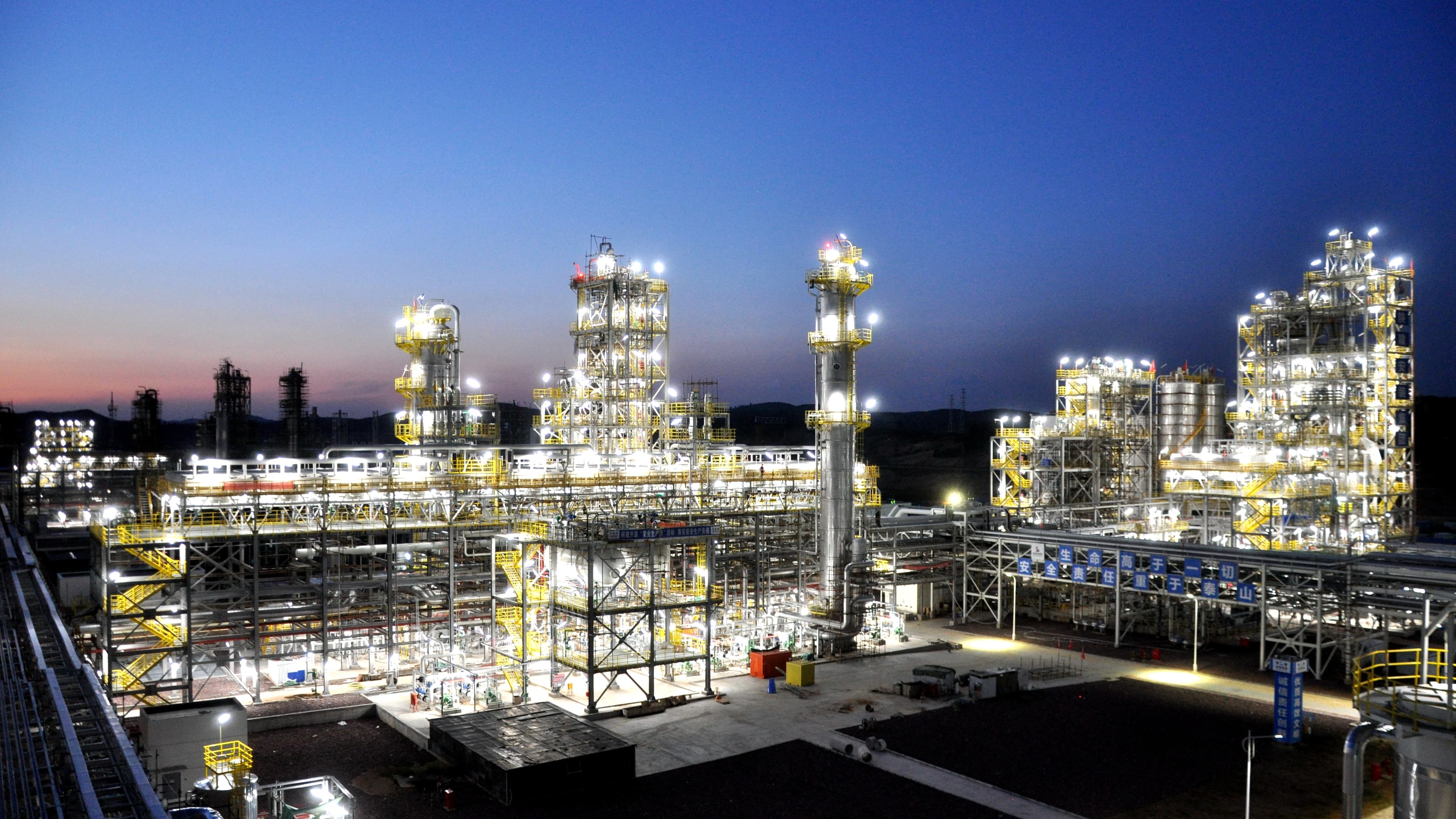
1946: Fluor diversifies into the Chemicals and Petrochemicals industry
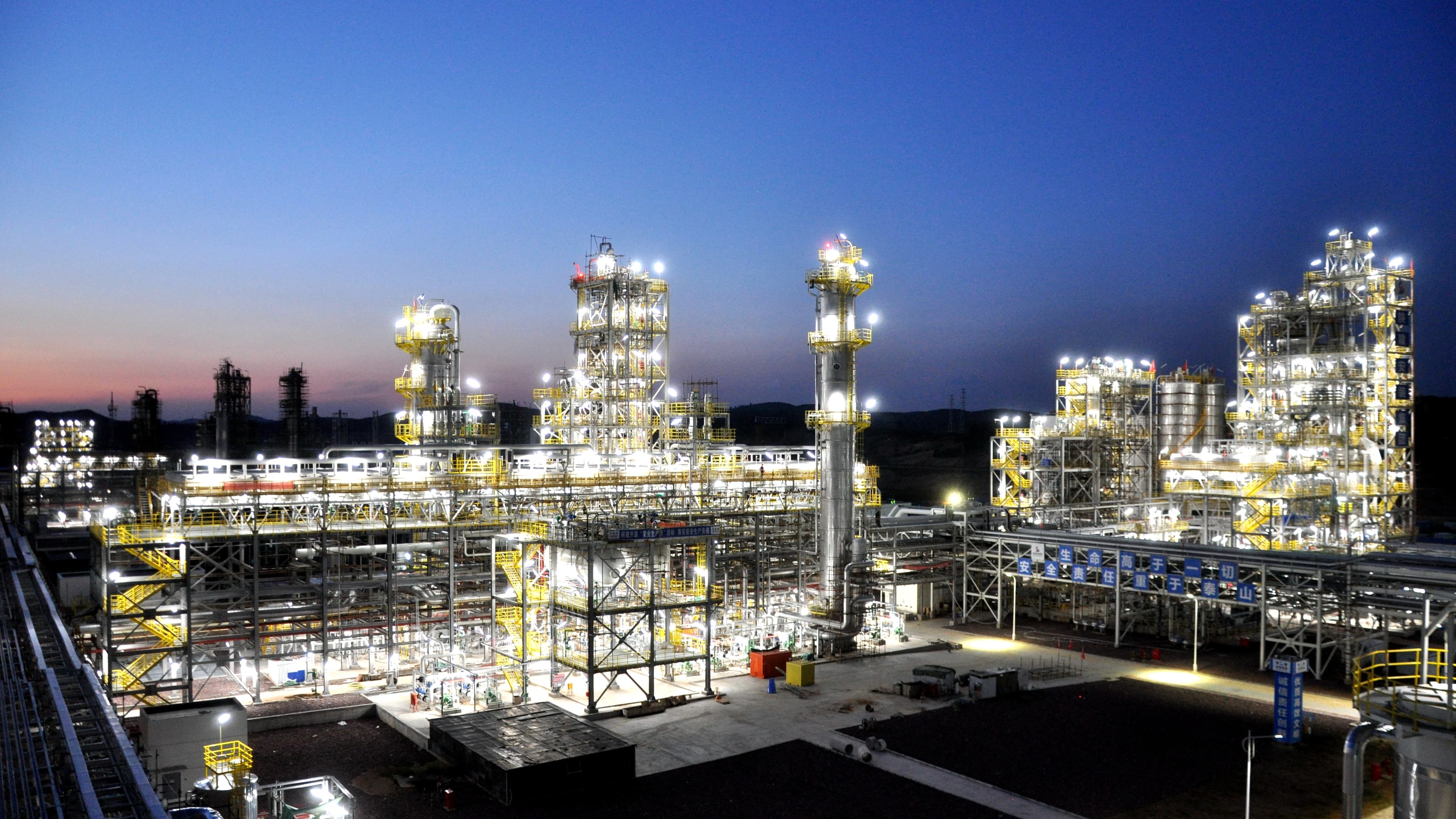
When the war ended, oil demand dropped, and Fluor diversified to focus on work in the petrochemical, chemical and power industries.
1947
American Potash and Chemical Co.'s Trona plant processes raw materials from Lake Searles to produce soda ash and borax
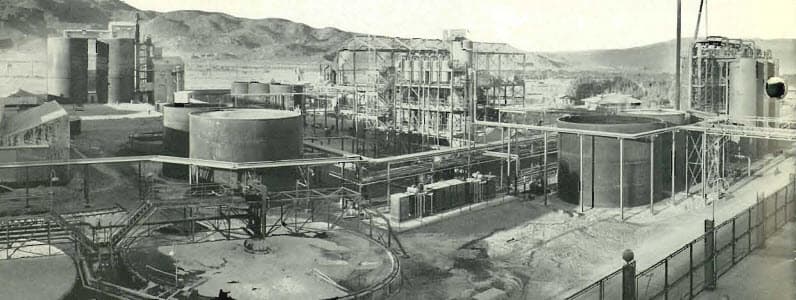
1947: American Potash and Chemical Co.'s Trona plant processes raw materials from Lake Searles to produce soda ash and borax
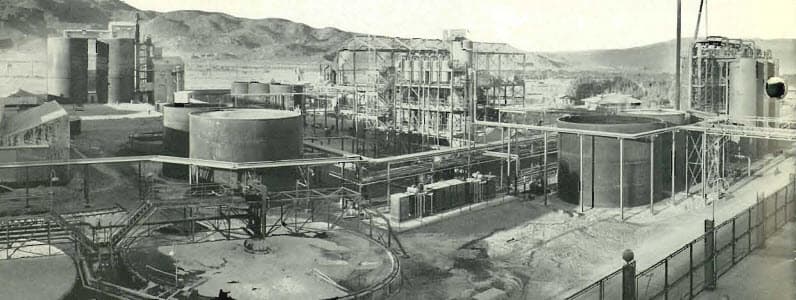
The lowest and hottest place in the United States is California's Death Valley. Fluor constructed the soda ash plant in this desolate, but mineral-rich, spot. The soda ash plant processed the raw materials from Lake Searles, producing up to 60,000 tpy of soda ash and 30,000 tpy of borax. One notable project accomplishment was the employment of advanced rigging methods, which contributed to the successful erection of some unusually large vessels.
1948
Effluent plant treats refinery waste
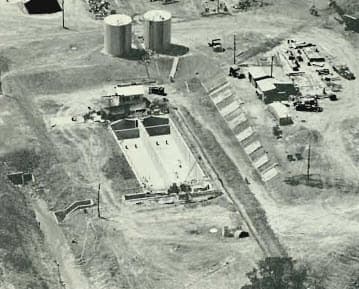
1948: Effluent plant treats refinery waste
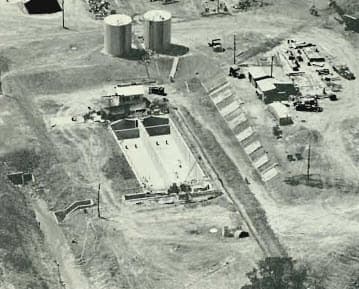
Fluor designed and built an effluent plant to treat the waste from the drains of a large refinery. The plant also recovered certain oils and acids. Dual design permitted cleaning without shutdown, and special acid-resistant cement was employed to withstand the effects of the chemically active effluent.
1949
Fluor establishes research and development department focused on chemical engineering
&w=3840&q=75)
1949: Fluor establishes research and development department focused on chemical engineering
&w=3840&q=75)
Fluor's research and development department established a chemical engineering research and service section in 1949. Chemical engineering research included CO2 recovery, H2S removal and advanced mathematical methods for rating cooling towers. Chemical engineering services focused on improving the start-up and testing of amine plants, H2S reabsorption plants, catalytic cracker dust problems and methods for rating extended surface heat exchangers.
1950s
Fluor enters the international chemicals and petrochemicals market.
1954
Mississippi River Fuel Corporation contracts Fluor to build 140,000 tpy ammonia plant
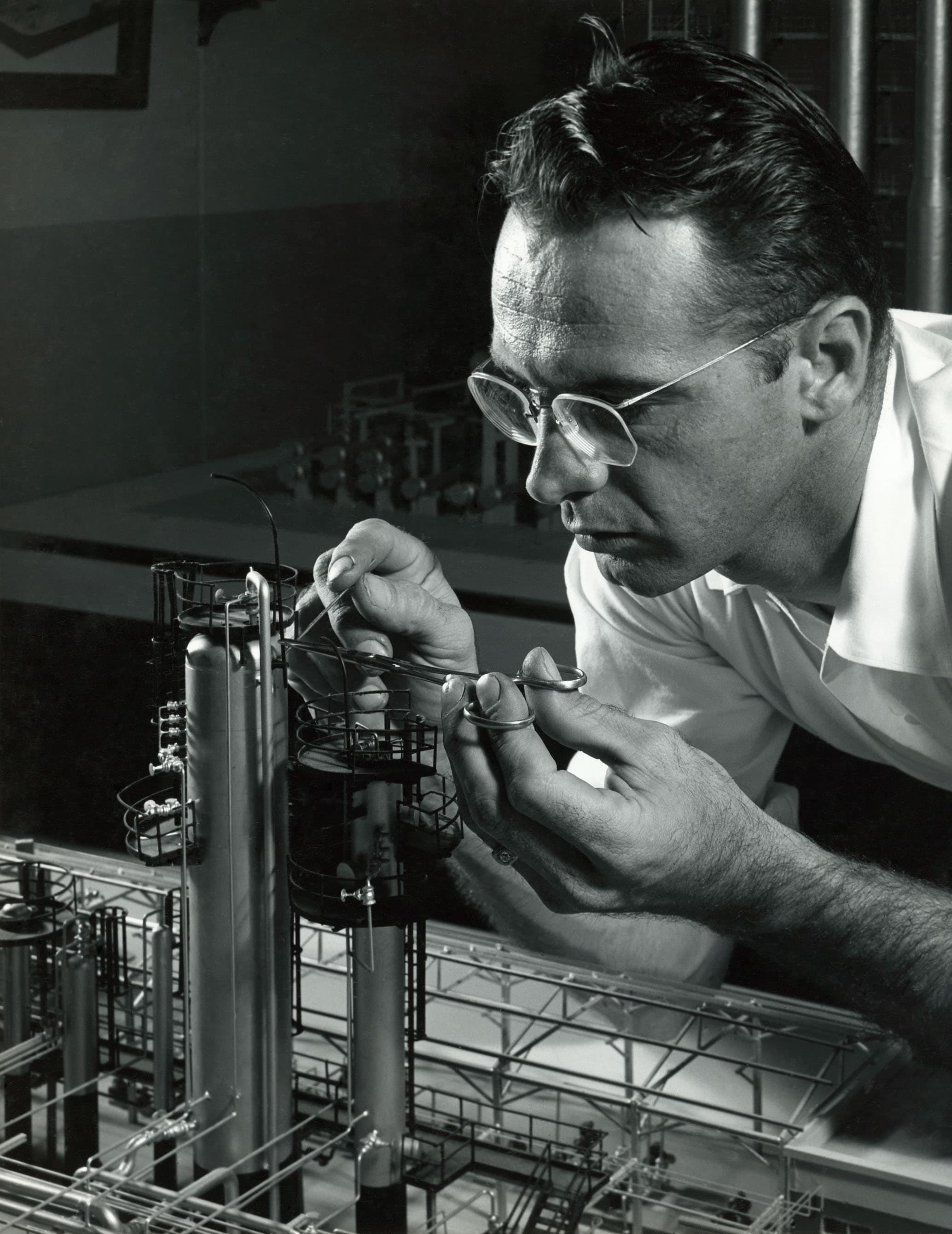
1954: Mississippi River Fuel Corporation contracts Fluor to build 140,000 tpy ammonia plant
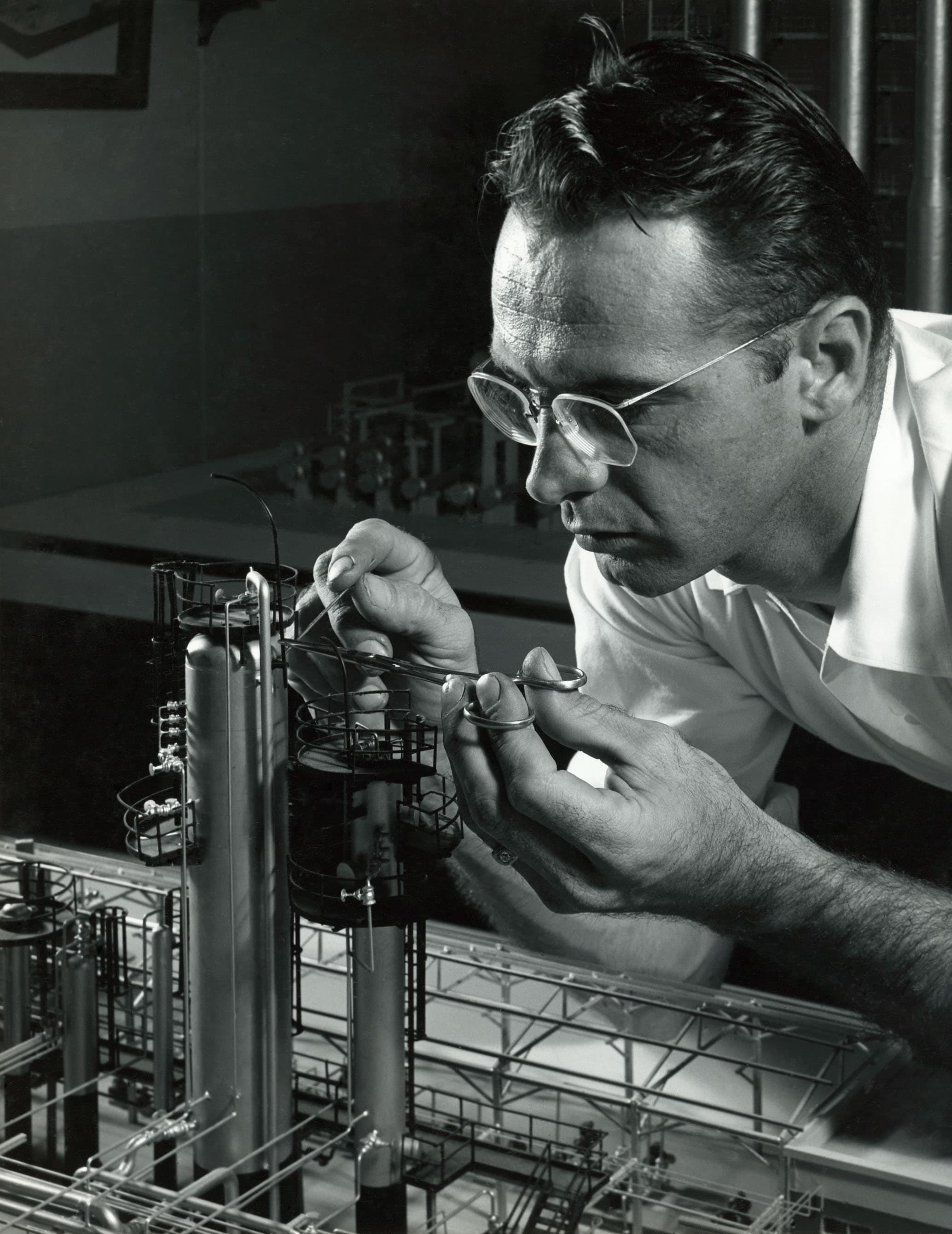
Fluor constructed the Mississippi River Fuel Corporation's 15-million dollar ammonia plant near Crystal City, Missouri. Initial capacity of the plant was 140,000 tpy of three basic nitrogen products - anhydrous ammonia, ammonium nitrate and ammonium solutions.
1955
Columbia River Chemicals manufactures chemicals and fertilizers in the Pacific Northwest
&w=3840&q=75)
1955: Columbia River Chemicals manufactures chemicals and fertilizers in the Pacific Northwest
&w=3840&q=75)
Fluor was awarded a sizeable contract for the design and construction of Columbia River Chemical's 12-million dollar chemicals and fertilizer plant near Pasco, Washington. Field work began in the fall of 1954, and construction was completed in 1955. It was the first major chemicals project of its kind in the Pacific Northwest.
1956
Methanol unit designed for Tarnów Chemical Works
1956: Methanol unit designed for Tarnów Chemical Works
Fluor designed a 25 tpd methanol unit for Tarnów Chemical Works. The methanol design became a specialty of the Prosynchem office. Prosynchem was later acquired by Fluor.
1956
Butadiene plant capacity increased to 79,000 tpy for Petroleum Chemicals, Inc.
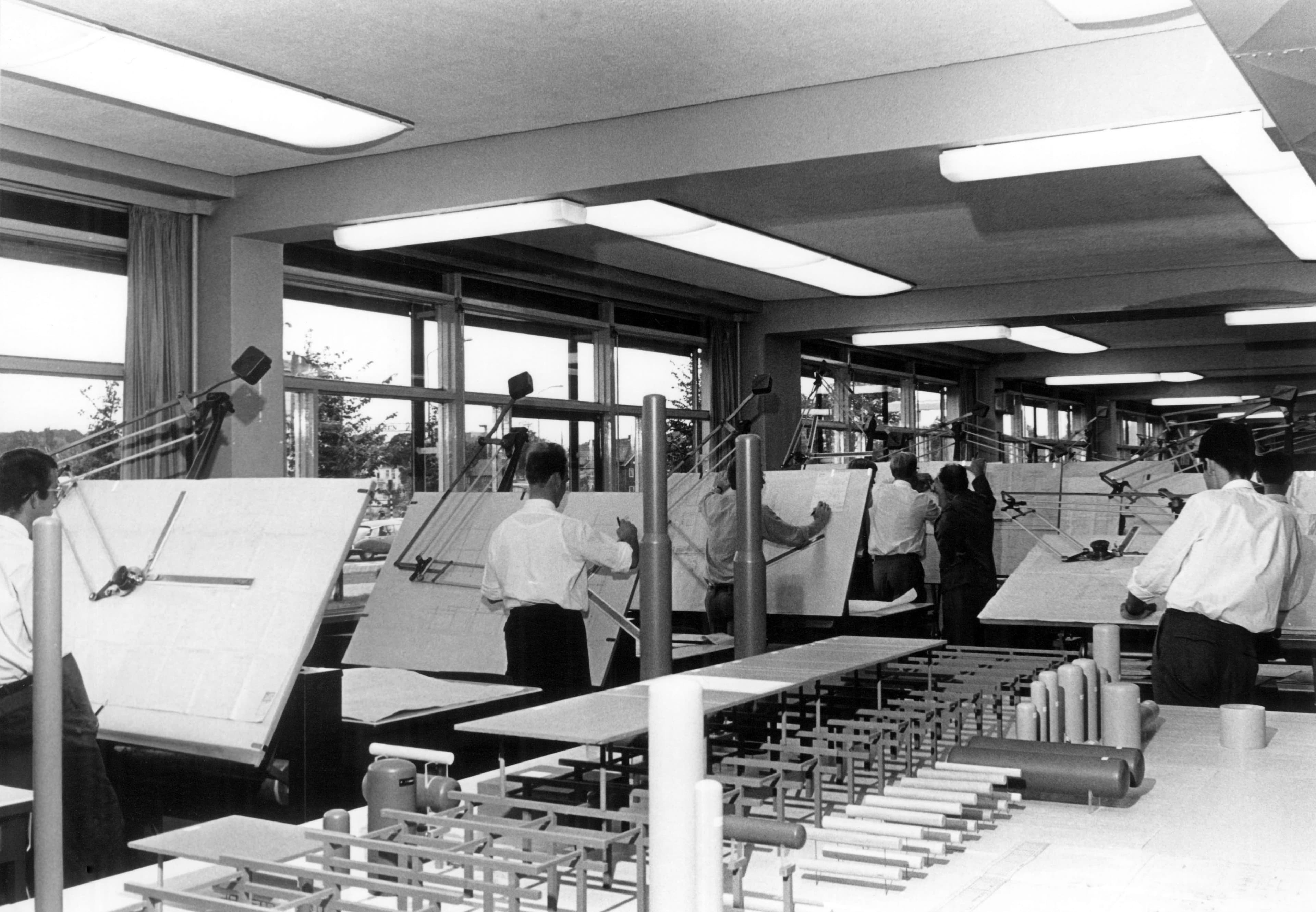
1956: Butadiene plant capacity increased to 79,000 tpy for Petroleum Chemicals, Inc.
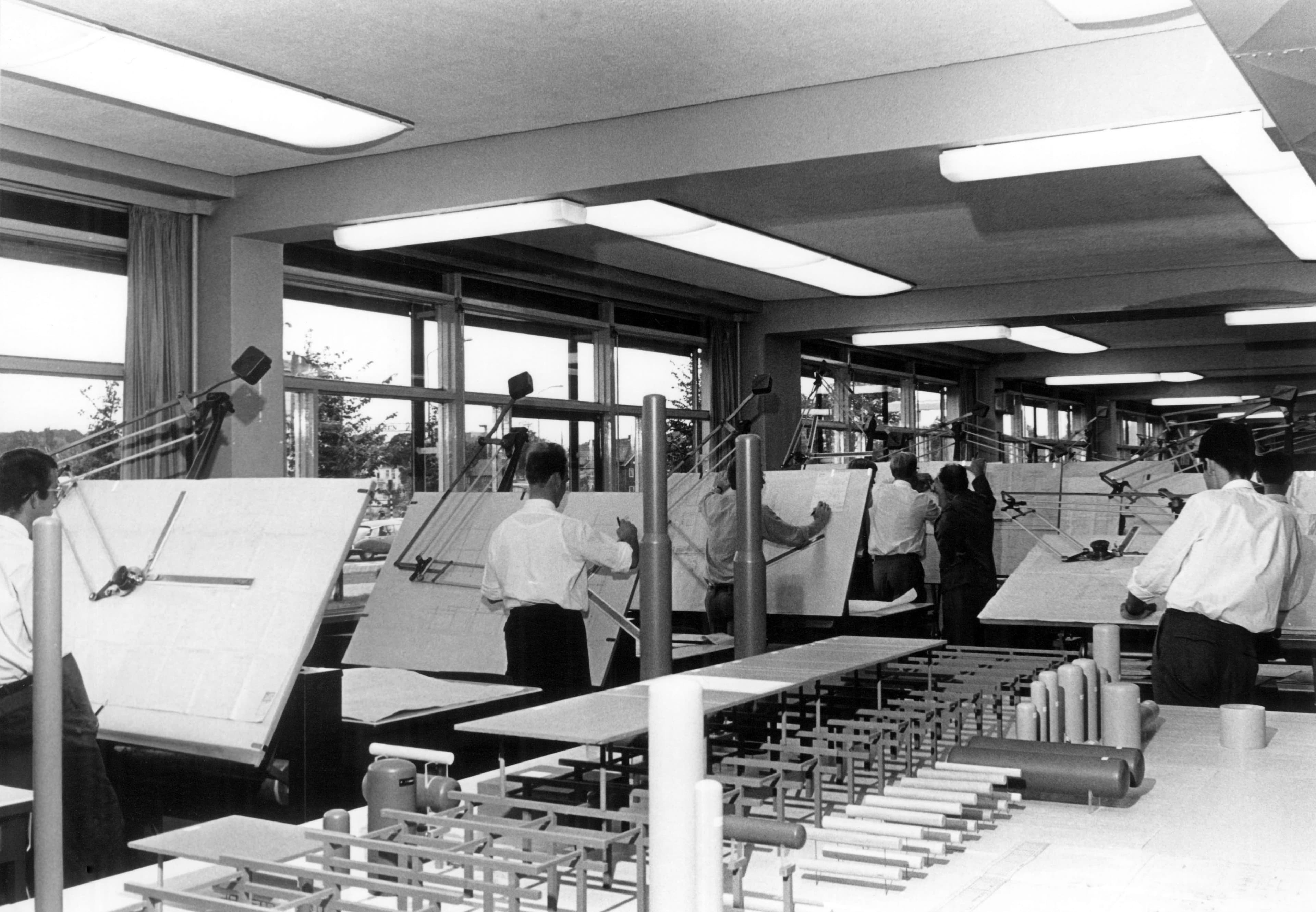
Fluor was awarded an expansion program for Petroleum Chemicals, Inc. The project increased the Lake Charles plant's capacity from 63,000 tpy to 79,000 tpy of butadiene.
1957
Texas Butadiene and Chemical Corp 43,000 tpy butadiene plant increases production on site to 60,000 tpy
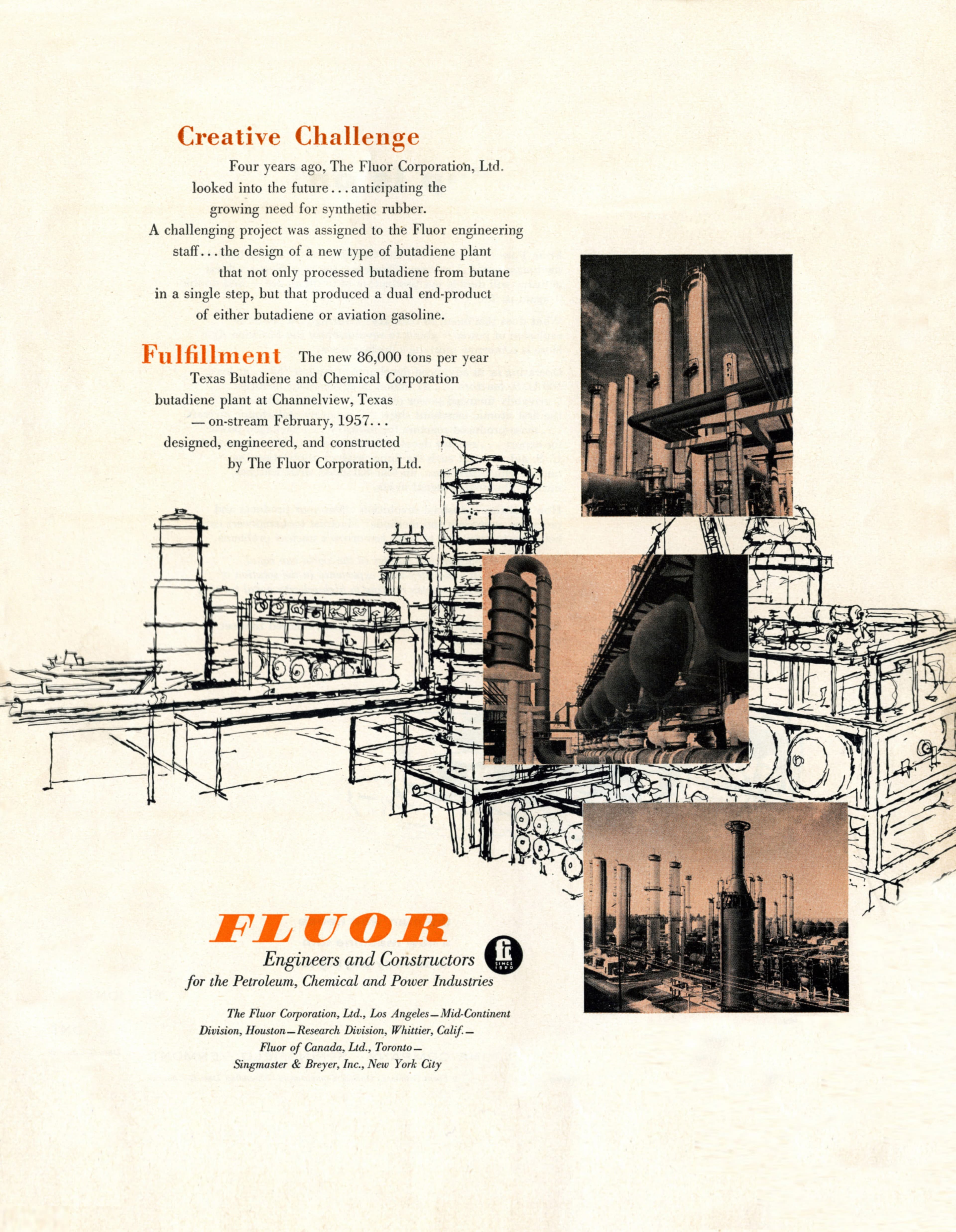
1957: Texas Butadiene and Chemical Corp 43,000 tpy butadiene plant increases production on site to 60,000 tpy
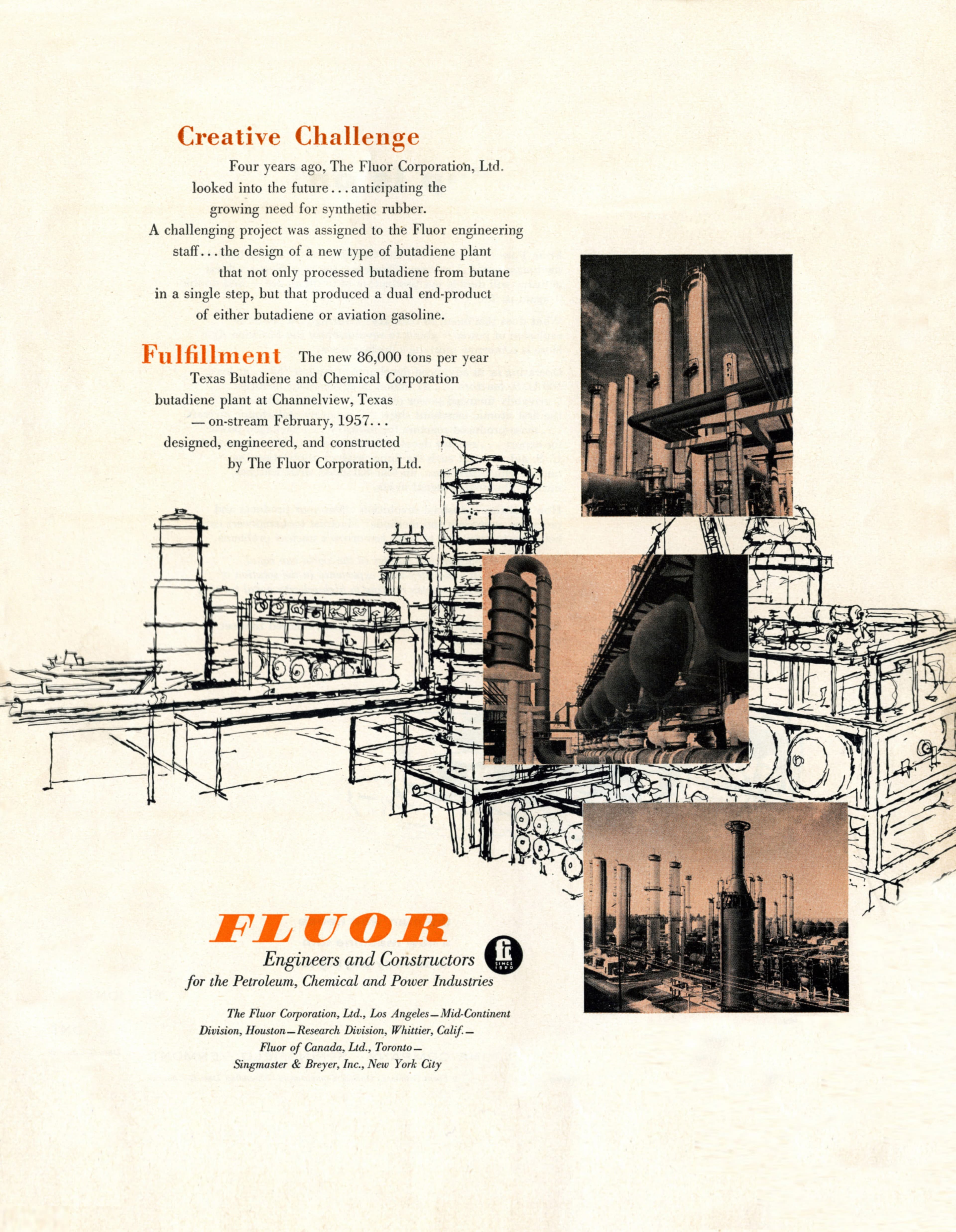
The Texas Butadiene and Chemical Corp. awarded Fluor the contract to design, engineer and construct a 43,000 tpy butadiene plant. The new plant brought total site capacity to 60,000 tpy.
1957
Grace chemical project includes construction of semi-works plant for polymers
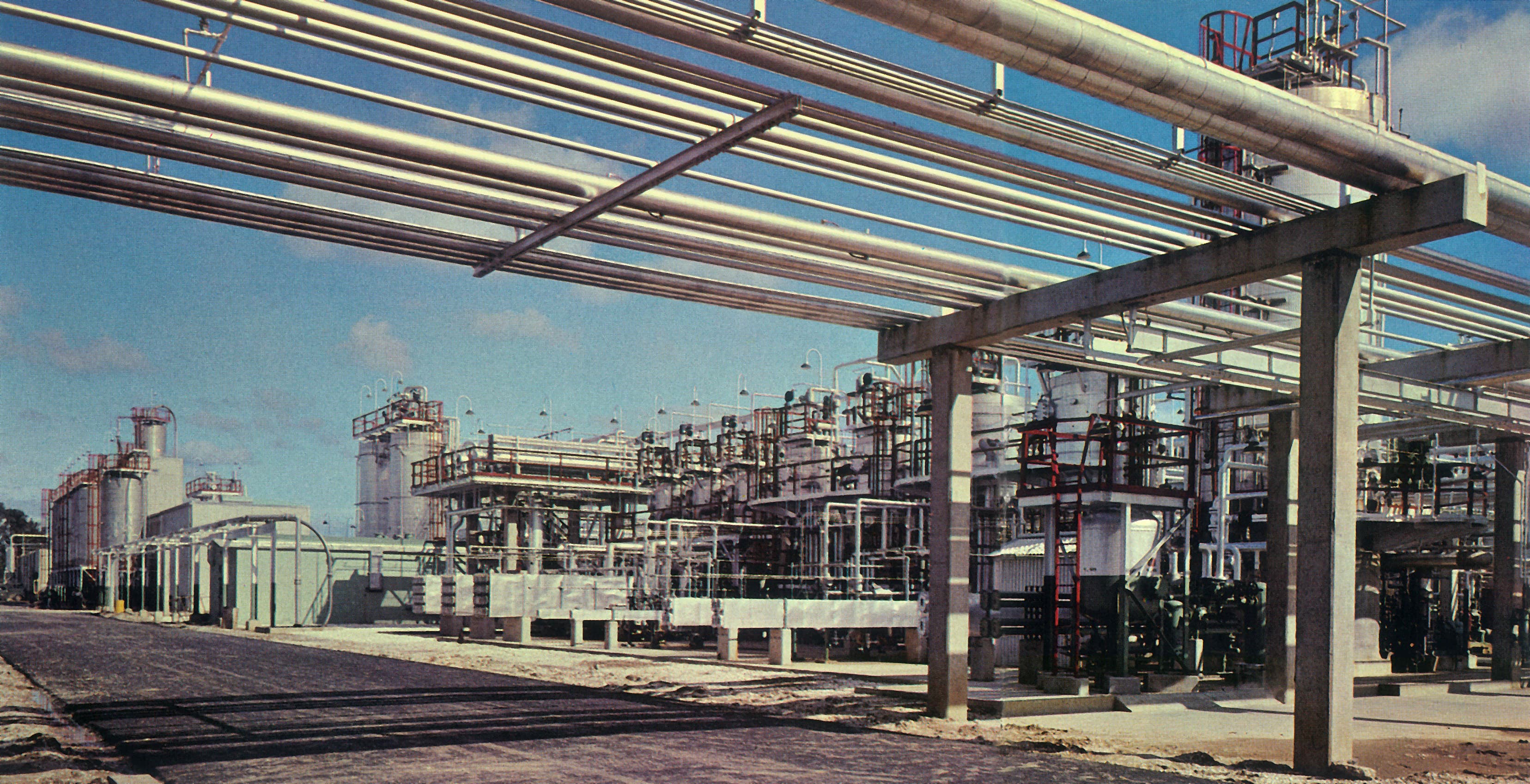
1957: Grace chemical project includes construction of semi-works plant for polymers
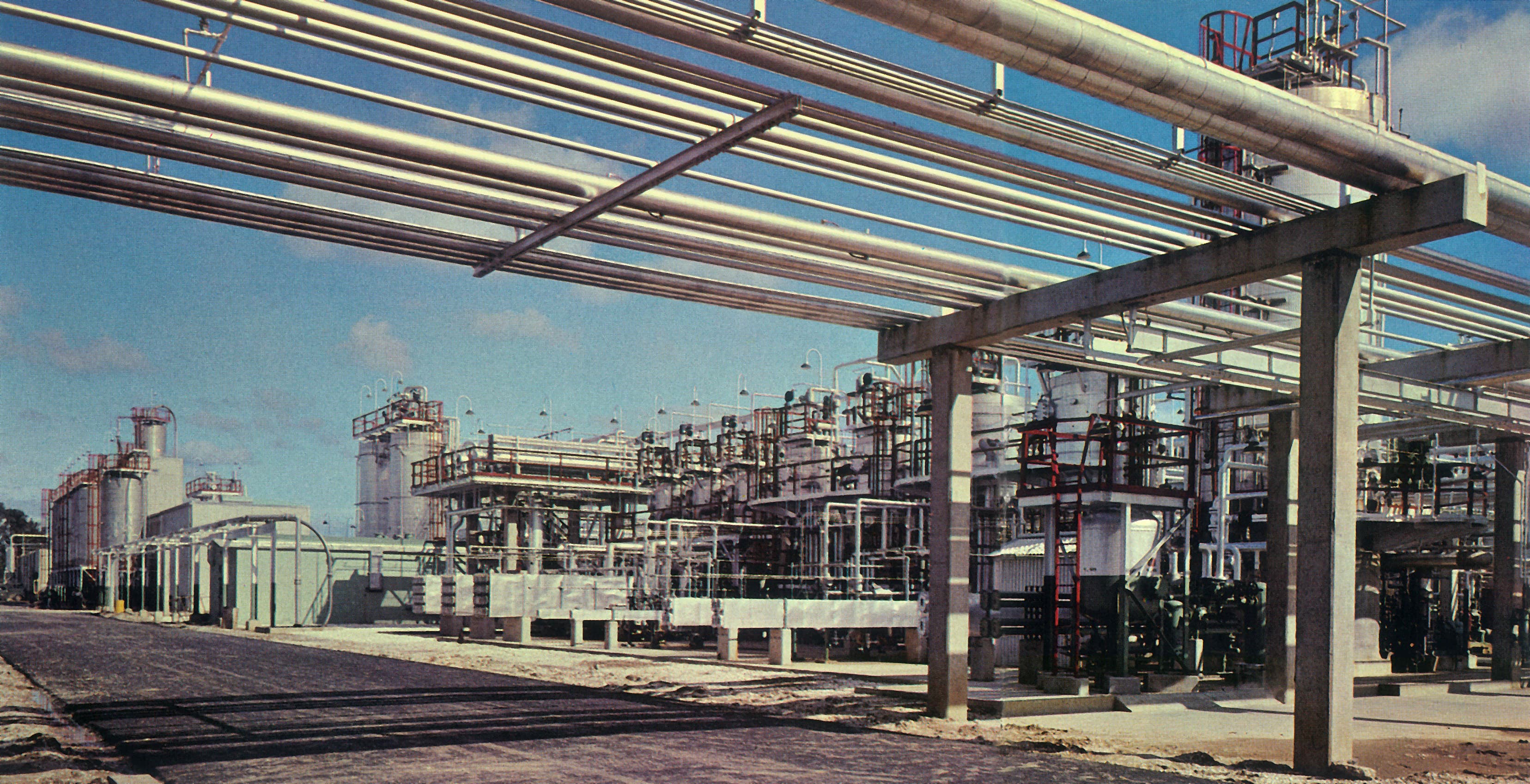
The Grace chemical project in Baton Rouge, Louisiana included the construction of a semi-works plant for polyethylene and other polymers. The plant began commercial operation in 1957.
1960s
Fluor continues work on international chemicals and petrochemicals projects, including Fluor's first project in South Africa.
1960
Fluor's first project in South Africa is to design and build Sasol's Styrene Butadiene production plant
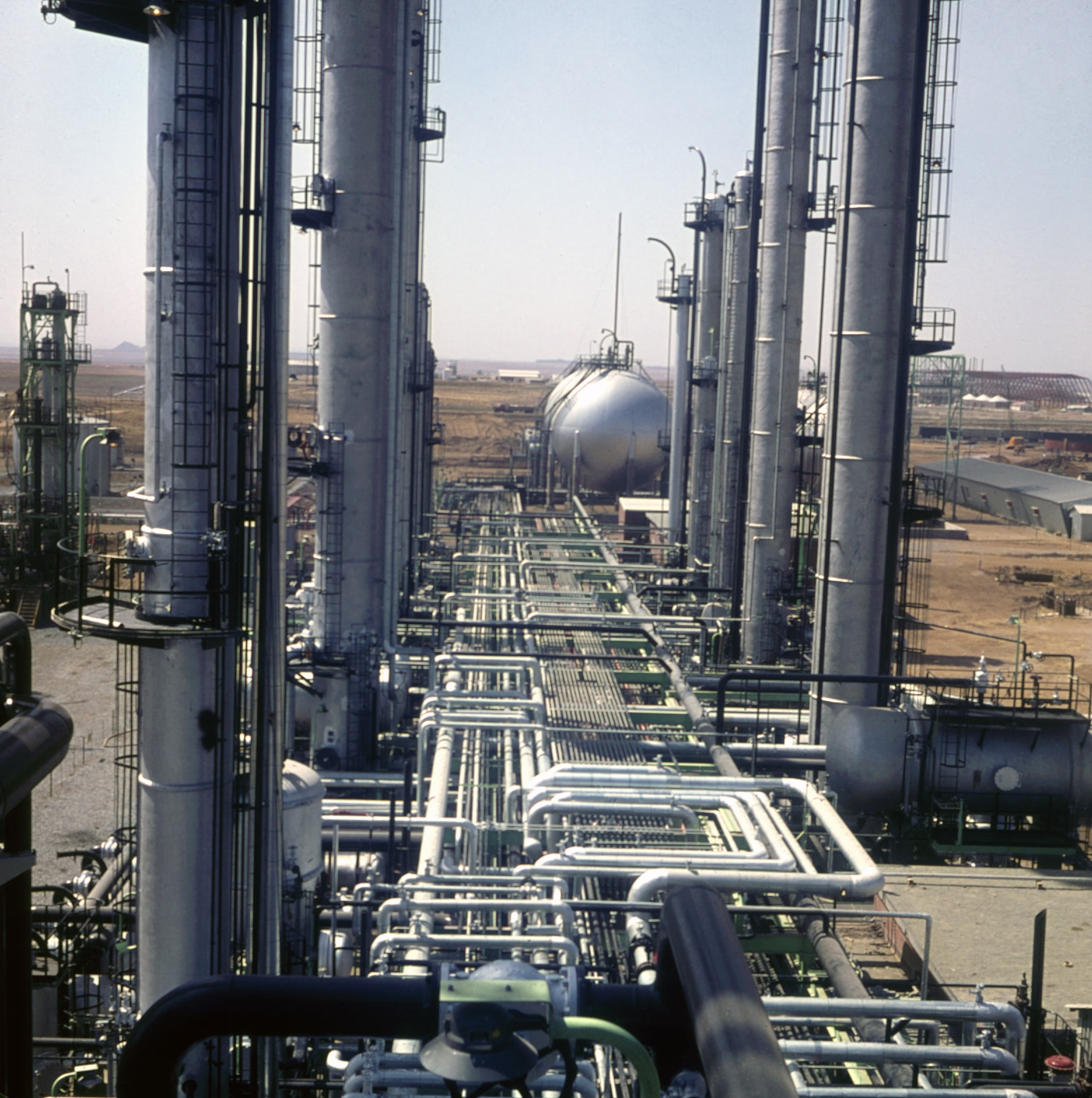
1960: Fluor's first project in South Africa is to design and build Sasol's Styrene Butadiene production plant
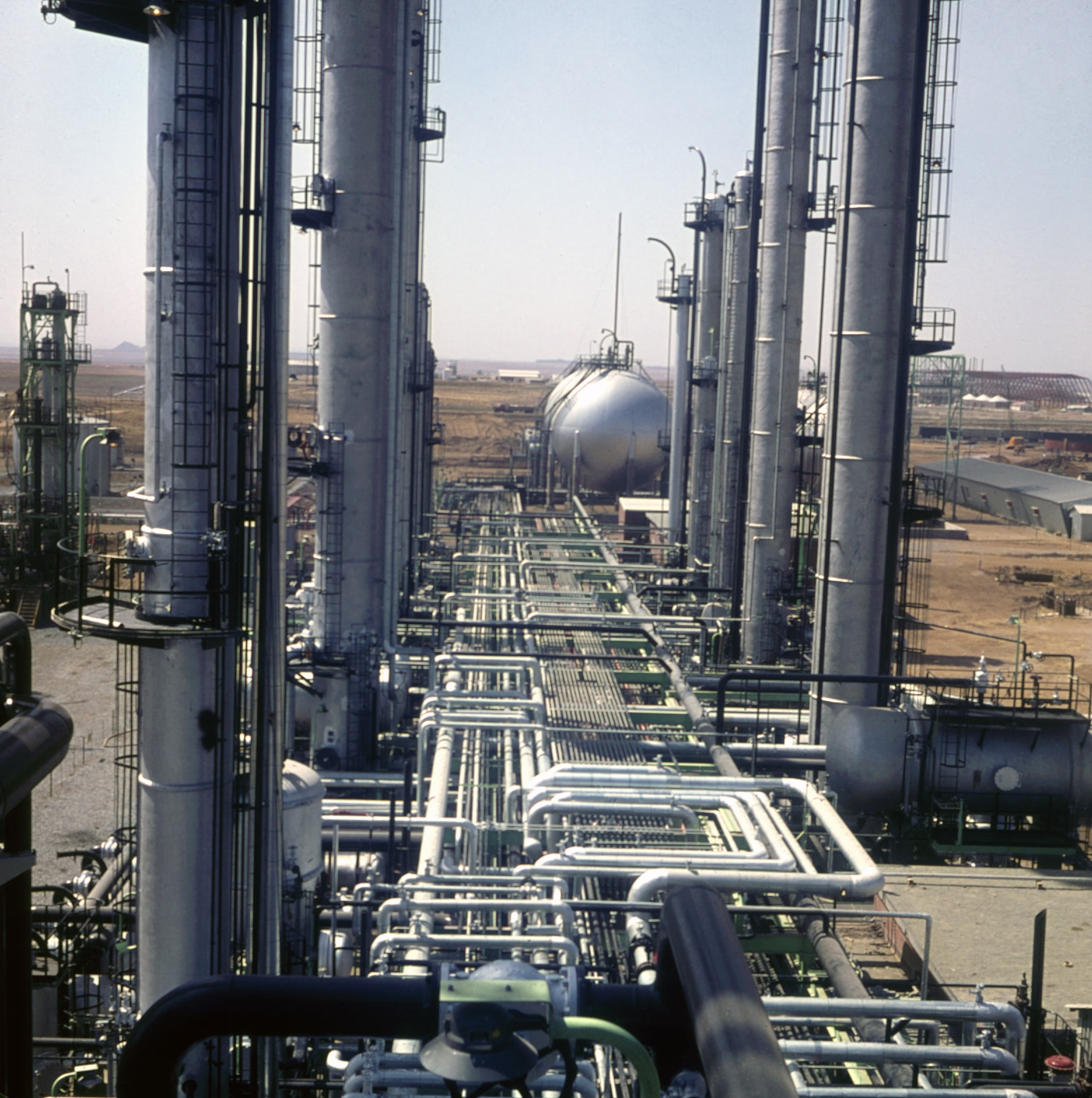
Fluor's presence in South Africa began with the award of the Sasol Styrene Butadiene project. The project was divided into two $7 million contracts. One was a total-responsibility contract awarded to Fluor by South African Coal, Oil, and Gas Corporation, Limited (Sasol), for a plant to produce 10,000 long tons per year of styrene and 20,000 long tons per year of butadiene. Under the other contract, Fluor and Polysar International S.A. built the SBR installation for the Synthetic Rubber Corporation of South Africa.
1960
First Fluor JV with Utah in Australia constructs the Altona Petrochemical Plant
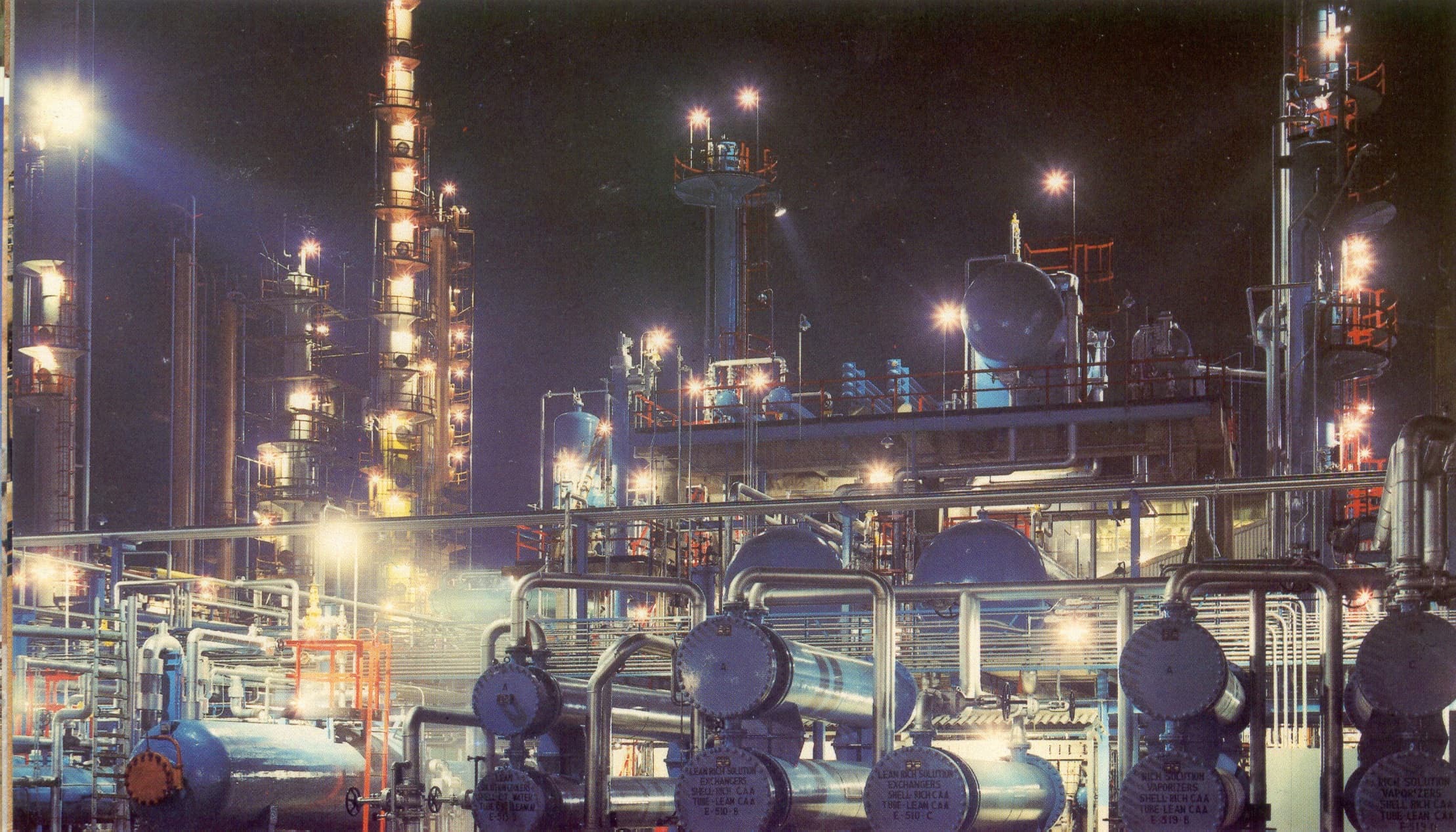
1960: First Fluor JV with Utah in Australia constructs the Altona Petrochemical Plant
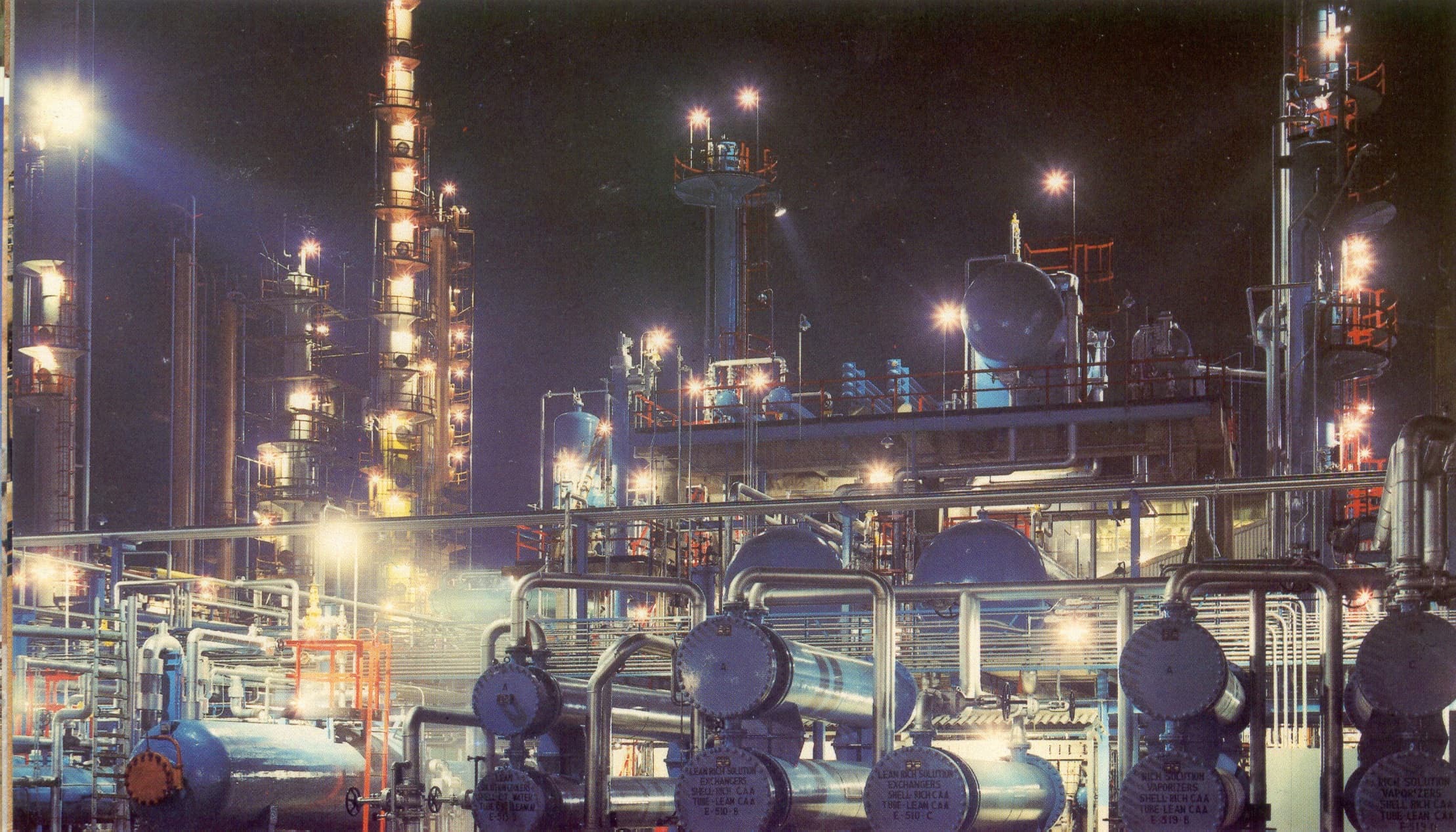
Fluor joint venture with Utah engineers and constructs the Altona Petrochemical Plant, launching Melbourne's Altona strip of chemical plants. This was the first of a series of engineering and construction projects for oil, gas and chemical plants that eventually included every oil refinery in Australia.
1960
W.R. Grace Polyethylene facility study complete and site construction begins
&w=3840&q=75)
1960: W.R. Grace Polyethylene facility study complete and site construction begins
&w=3840&q=75)
In 1960, Fluor completed the preliminary engineering, engineering, procurement and construction for the W.R. Grace XPF Polyethylene Facility in Baton Rouge, Louisiana. The project was completed in 1961.
1961
Design of Poland's first refinery and petrochemical complex completed
1961: Design of Poland's first refinery and petrochemical complex completed
Prosynchem completed the general initial design of Poland's first refinery and petrochemical complex for Mazovian Refinery & Petrochemical Works. Prosynchem designed the petrochemical complex, storage facilities, power needs and connections, demand for land, connections with the refinery and financial and economic conditions for the project. Prosynchem was later acquired by Fluor.
1962
Oświęcim Chemical Works' new 140 tpd methanol unit design significantly increases site production
1962: Oświęcim Chemical Works' new 140 tpd methanol unit design significantly increases site production
Oświęcim Chemical Works contracted Prosynchem to design a 140 tpd unit to replace a 30 tpd unit that had been designed by Prosynchem's predecessor GBIO. Prosynchem was later acquired by Fluor.
1963
Fluor engineers and procures chemical plant in Campos Eliseos
1963: Fluor engineers and procures chemical plant in Campos Eliseos
Fluor performed engineering and procurement for a 73 MMLB / year butadiene recovery plant in Campos Eliseos, Brazil.
1963
Svenska Esso petrochemical plant processes crude into ethylene and butadiene

1963: Svenska Esso petrochemical plant processes crude into ethylene and butadiene

Fluor constructed Svenska Esso's petrochemical plant. The construction included the lift of several large columns, including the lift of an 80-ton, 140-foot vessel. The plant processed crude oil into hydrocarbon feedstocks for further processing into ethylene and butadiene.
1964
Design for chemical plant in Zabrze complete
1964: Design for chemical plant in Zabrze complete
Prosynchem developed the design and models for the Concordia Chemical Plant in Zabrze, Poland. Prosynchem was later acquired by Fluor.
1967
Polyester polymer plant in the Netherlands producing 30 MM lb/year
1967: Polyester polymer plant in the Netherlands producing 30 MM lb/year
Fluor completed the EPCM services for ICI Holland NV's polyester polymer plant with a capacity of 30 MM lbs/year in Rozenburg, Netherlands.
1969
Płock petrochemical complex operable
1969: Płock petrochemical complex operable
Prosynchem completed the engineering for the Płock petrochemical complex. The complex included a liquid gas separation and propylene concentration unit, dry gas desulfurization unit, liquid gas desulfurization unit, storage and shipment facilities for the petrochemical complex and raw material and power connections with the refinery. Prosynchem was later acquired by Fluor.
1970s
Fluor executes several chemicals and petrochemicals projects in Western Europe.
1971
Contract to provide small capital projects and plant support services for DuPont at Cape Fear begins
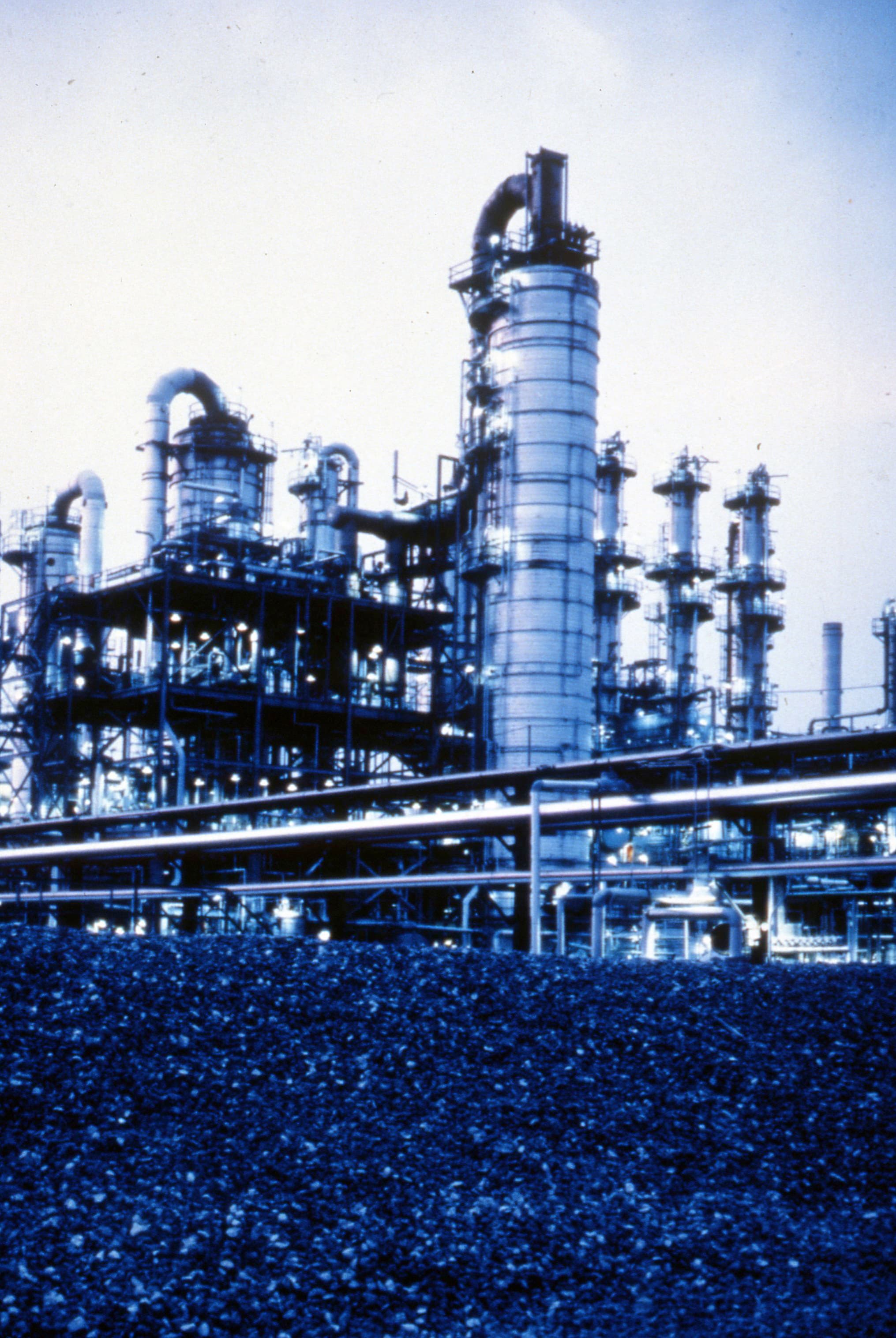
1971: Contract to provide small capital projects and plant support services for DuPont at Cape Fear begins
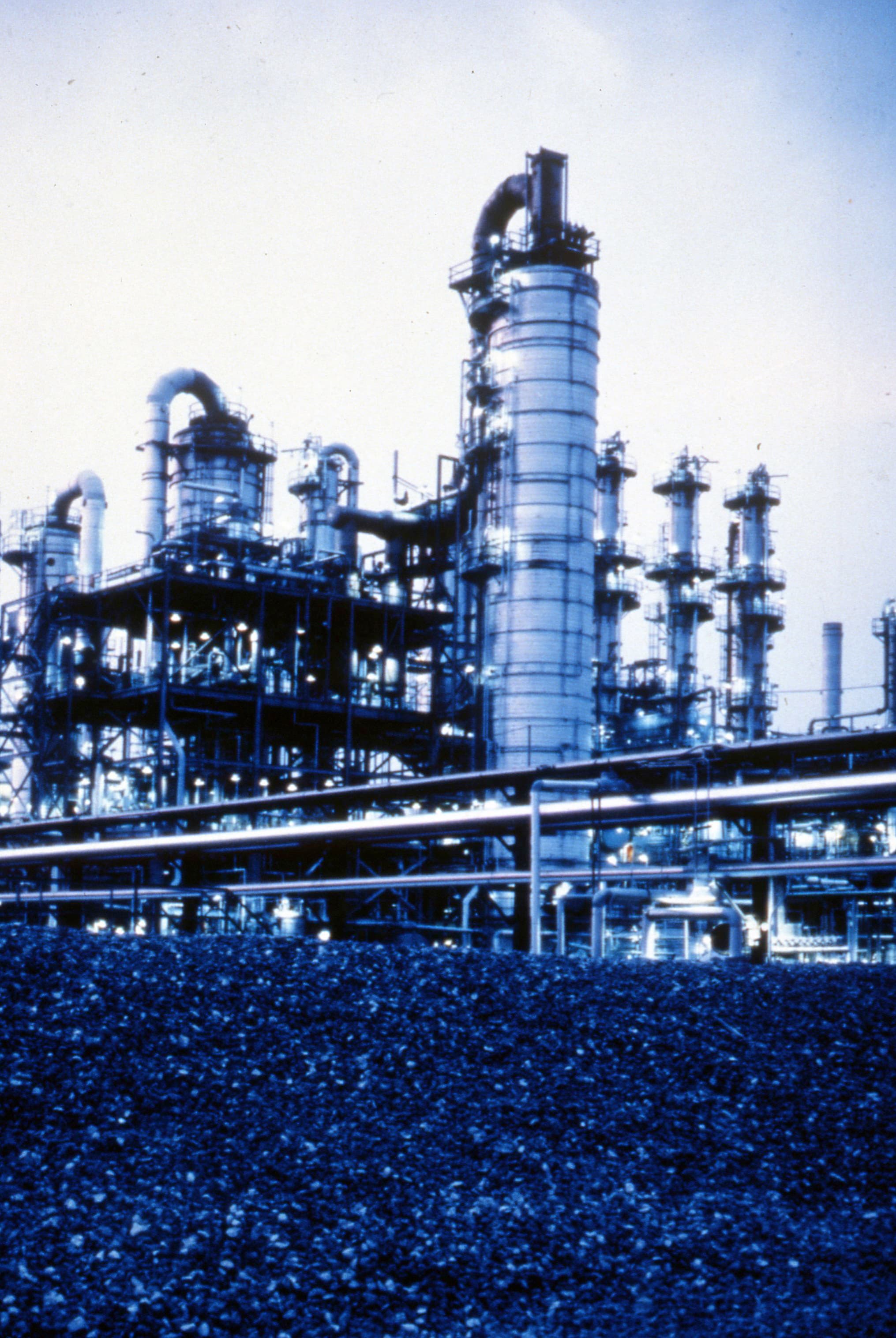
Fluor provided small capital projects and plant support services. The manpower peaks exceeded 3,000 craft employees. This site held a national record in the industry for safety, having over 20 million man-hours without a lost-time accident.
1972
Fluor constructs Dow Chemical Plant and Warehouse in Stade, Germany
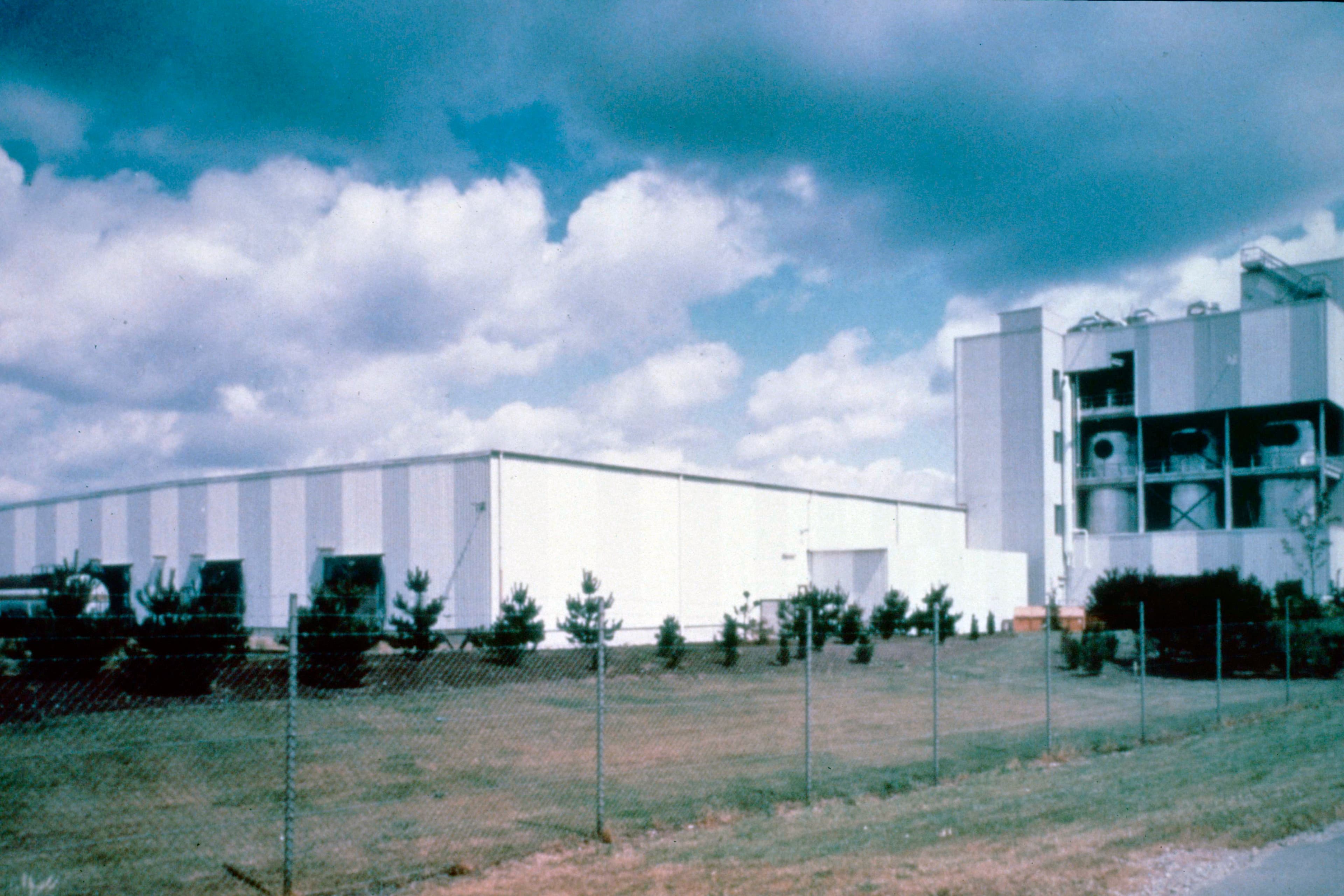
1972: Fluor constructs Dow Chemical Plant and Warehouse in Stade, Germany
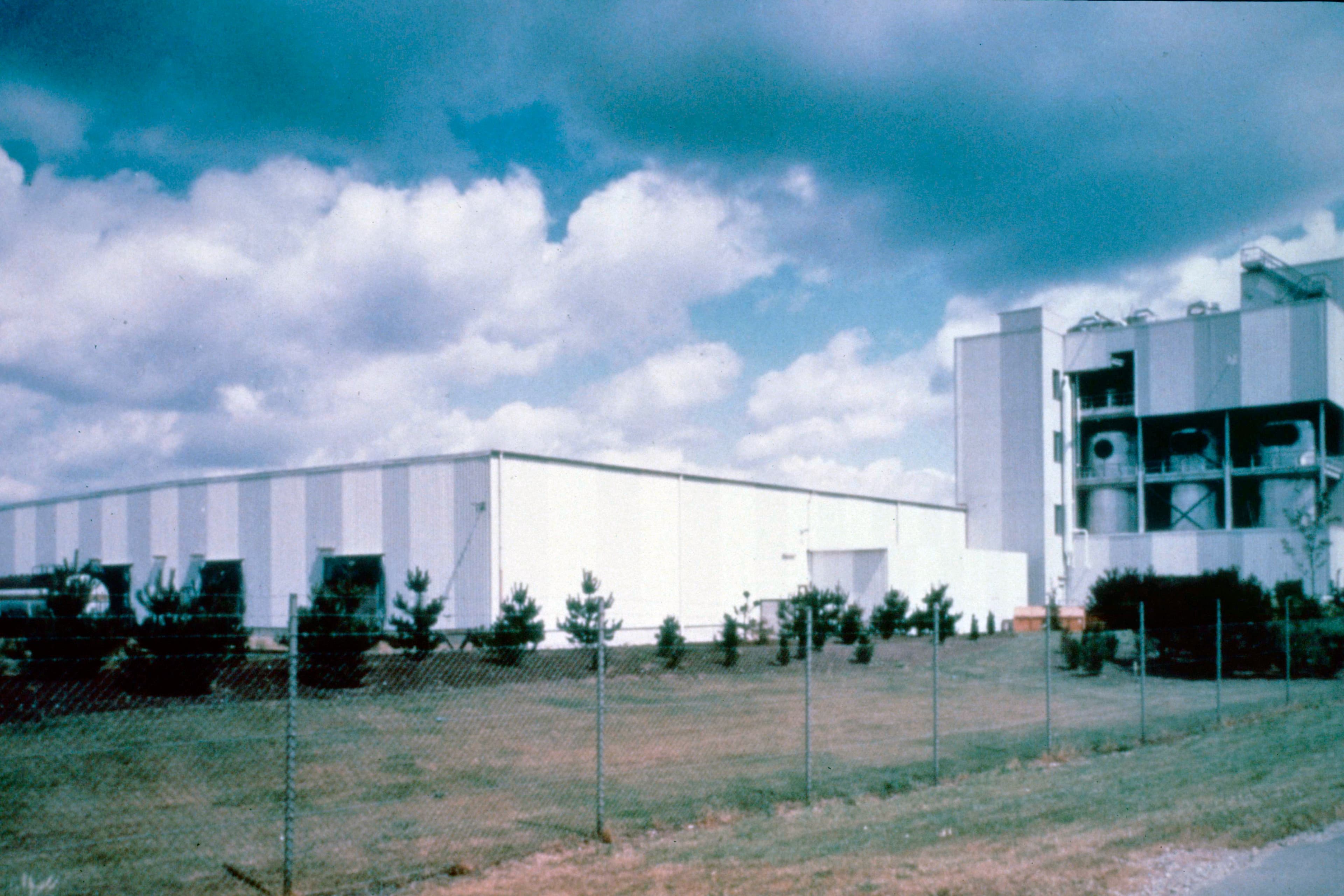
In 1972, Fluor was contracted by Dow Chemical Co. to construct a chemical plant and warehouse in Stade, Germany. The project was completed in early 1973.
1974
Fluor's chemical group designs plastics plant for Dow Corning
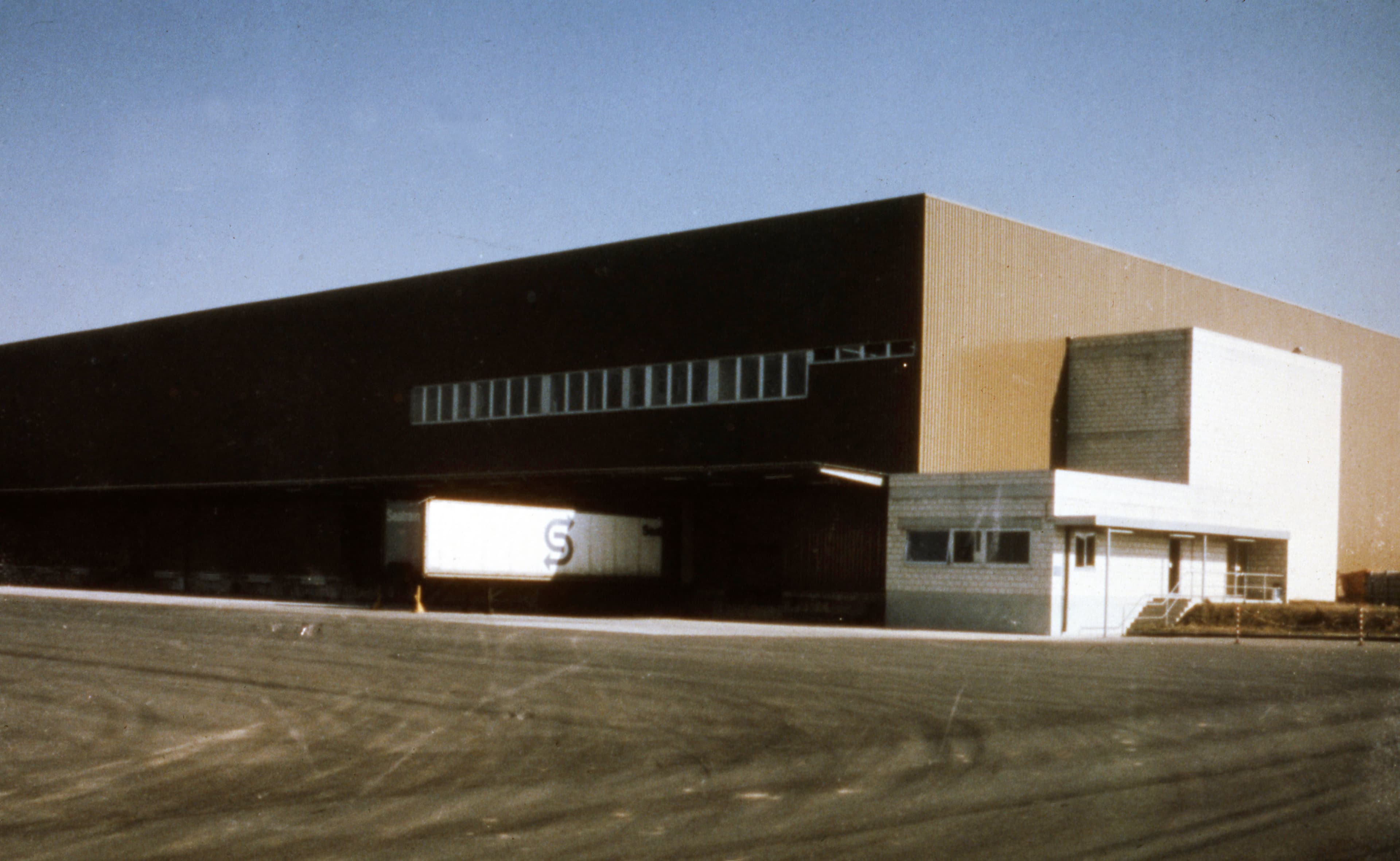
1974: Fluor's chemical group designs plastics plant for Dow Corning
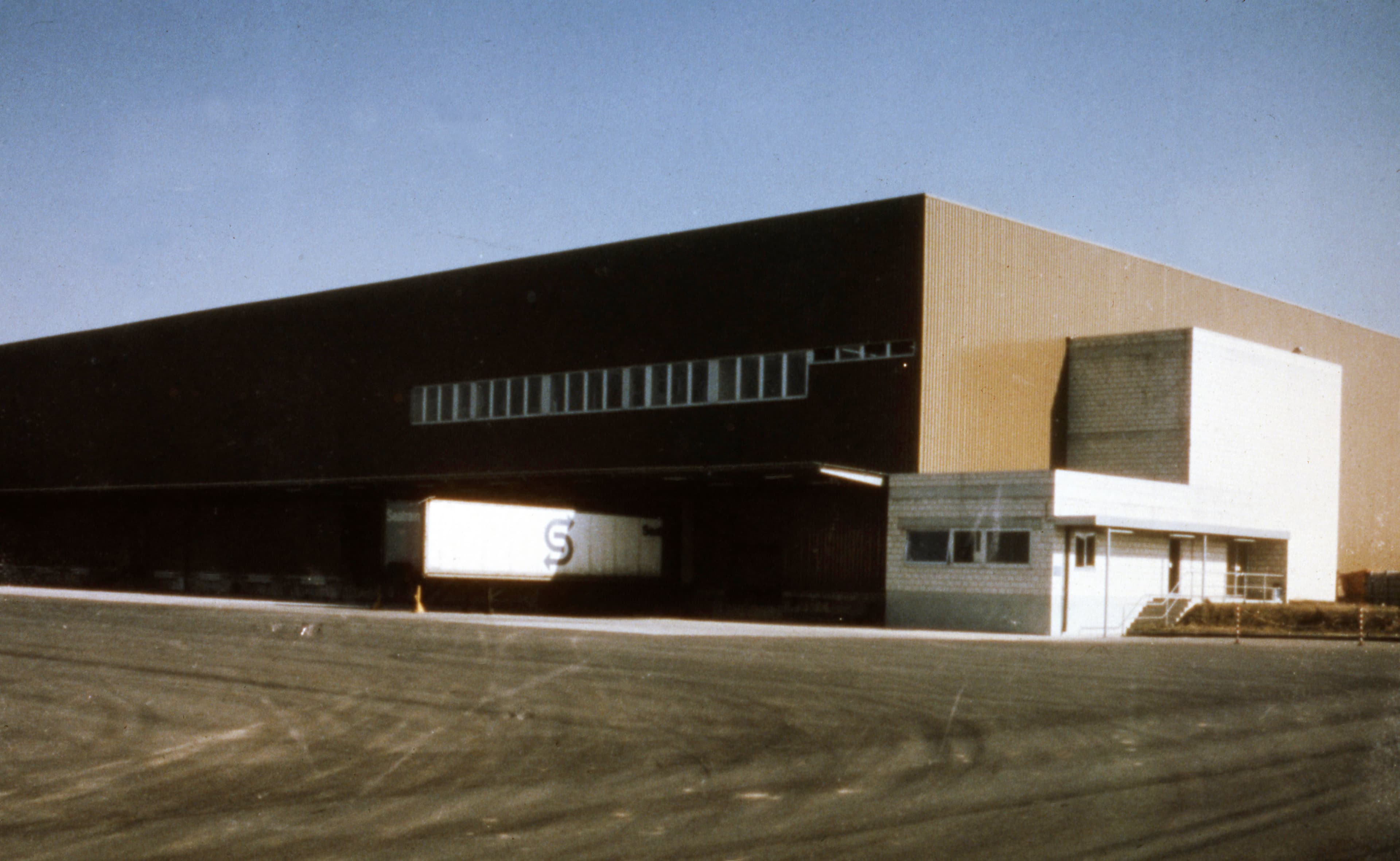
Fluor's Chemicals group designed and constructed a plastics facility for Dow Corning in Seneffe, Belgium.
1974
Chemical Fibers Plant start-up completed
1974: Chemical Fibers Plant start-up completed
Prosynchem in cooperation with the Heavy Chemical Synthesis Institute completed the process design for the dimethyl terephthalate unit in Torun, Poland. The unit had a production capacity of 74,000 tons per year. Prosynchem was later acquired by Fluor.
1975
Stauffer Chemical uses Fluor as a contractor in Belgium
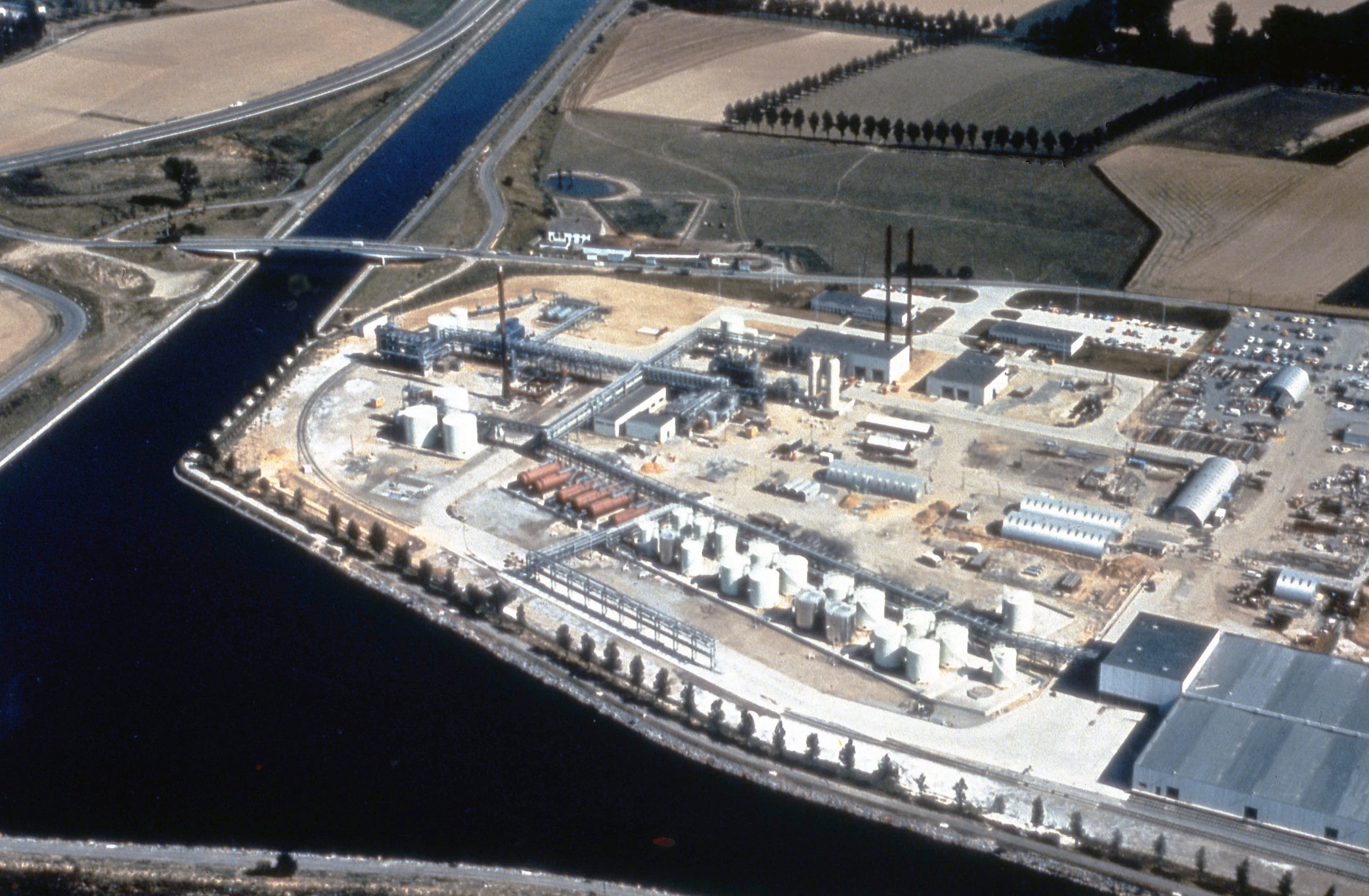
1975: Stauffer Chemical uses Fluor as a contractor in Belgium
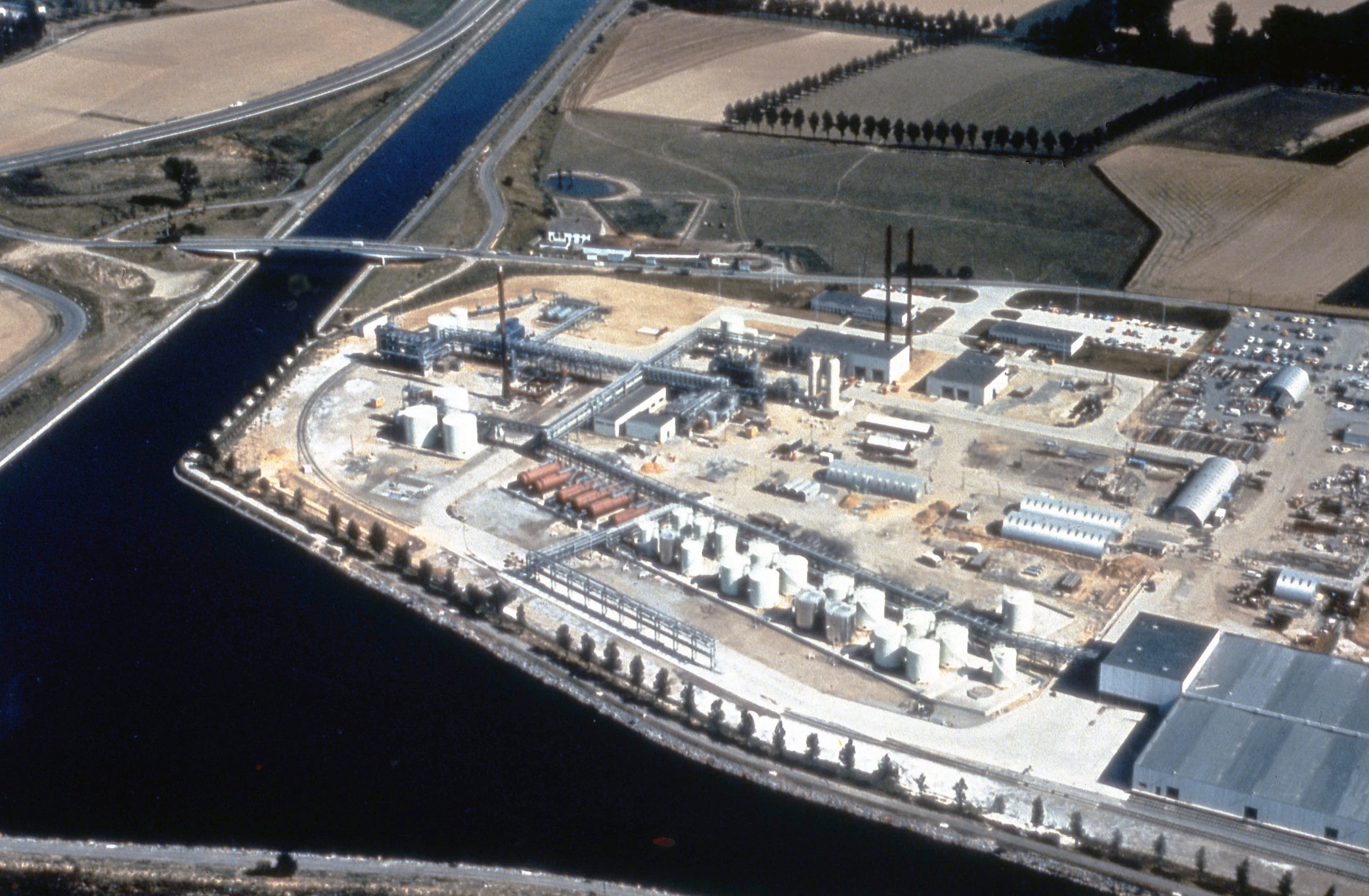
Fluor began the design and construction scope for Stauffer Chemical's $50 million herbicide plant in Seneffe, Belgium. The project was completed in 15 months.
1975
LDPE Plant with Ethylene Recovery constructed in Antwerp
&w=3840&q=75)
1975: LDPE Plant with Ethylene Recovery constructed in Antwerp
&w=3840&q=75)
Fluor performed engineering, procurement and construction management to successfully erect USI's LDPE Plant with ethylene recovery in Antwerp, Belgium.
1976
Esso Chemie N.V.'s 768 tpd LDPE plant begins production
&w=3840&q=75)
1976: Esso Chemie N.V.'s 768 tpd LDPE plant begins production
&w=3840&q=75)
Fluor served as the engineering, procurement and construction management contractor on Esso's 768 tpd low density polyethylene plant construction in Meerhout, Belgium.
1977
SADAF's grassroots ethylene-based petrochemical complex EPC scope launches
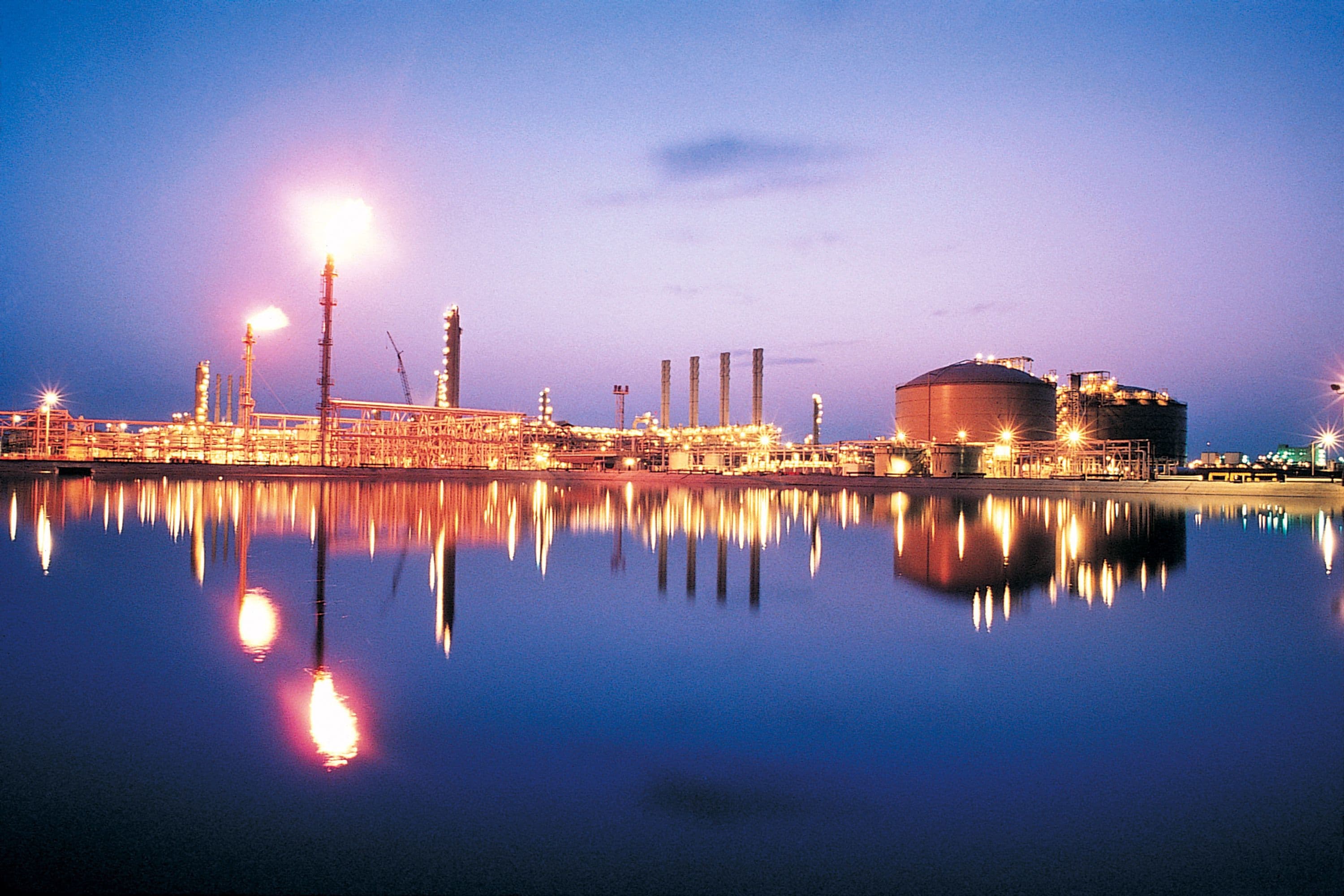
1977: SADAF's grassroots ethylene-based petrochemical complex EPC scope launches
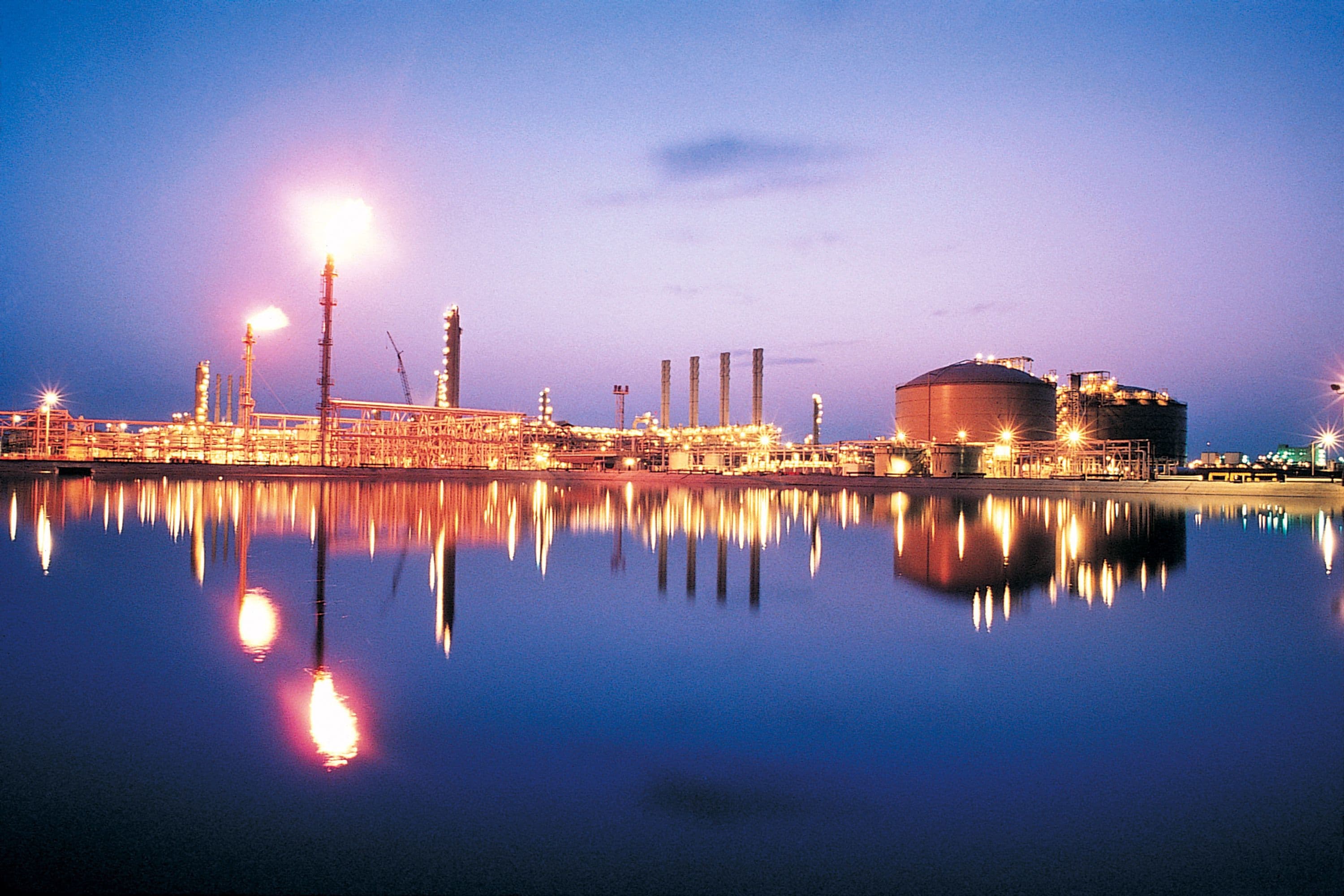
Fluor engineered and constructed Saudi Petrochemical Company's ethylene based grassroots petrochemical complex. The complex included crude industrial ethanol, ethylbenzene, styrene, chlorine and ethylene dichloride units on plot.
1977
Fluor finishes Hercules' chemical plant
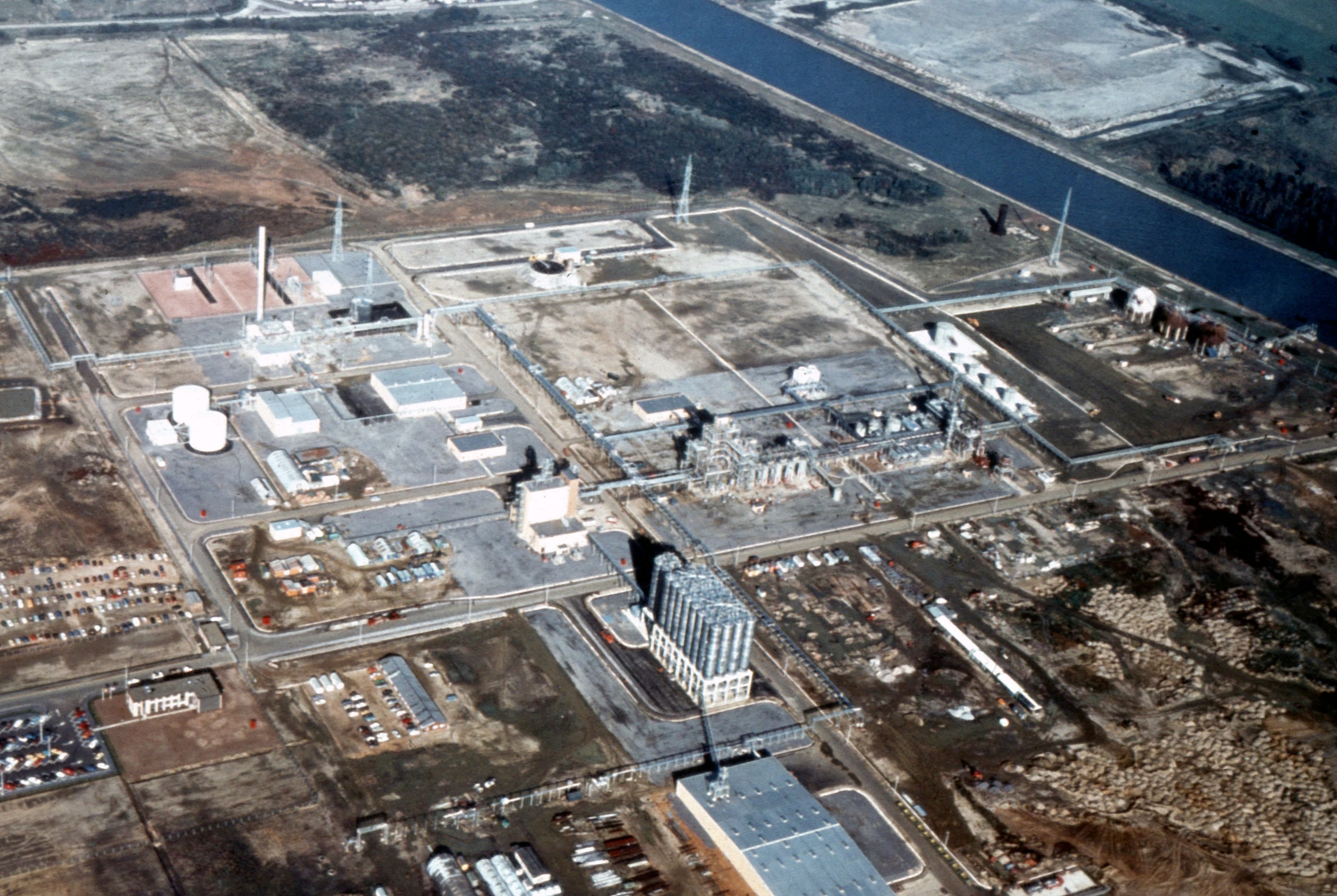
1977: Fluor finishes Hercules' chemical plant
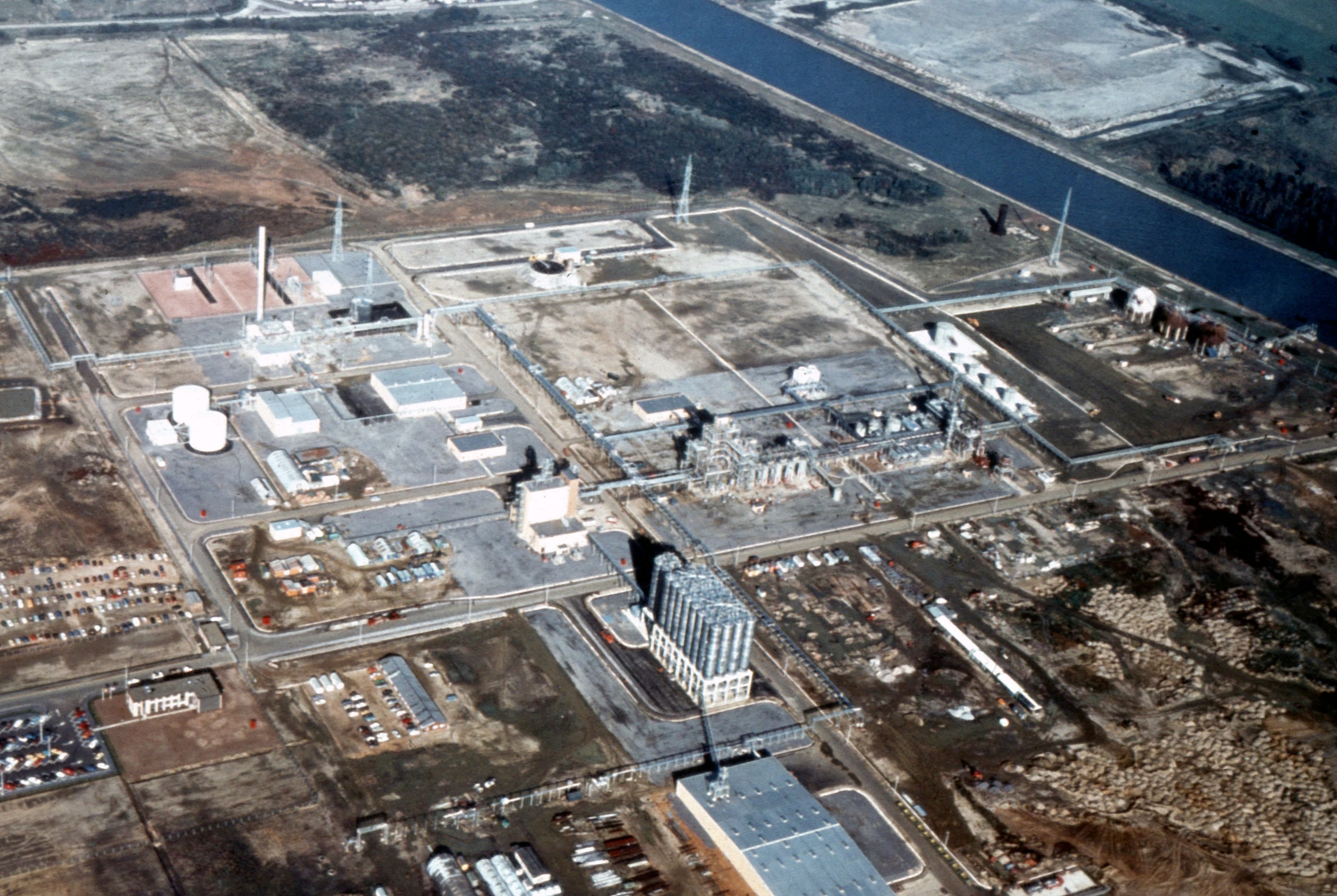
Fluor successfully constructed the Hercules' chemicals manufacturing facility and office building in Paal, Belgium.
1977
Woodward, Oklahoma 1,200 tpd Ammonia Plant in operation
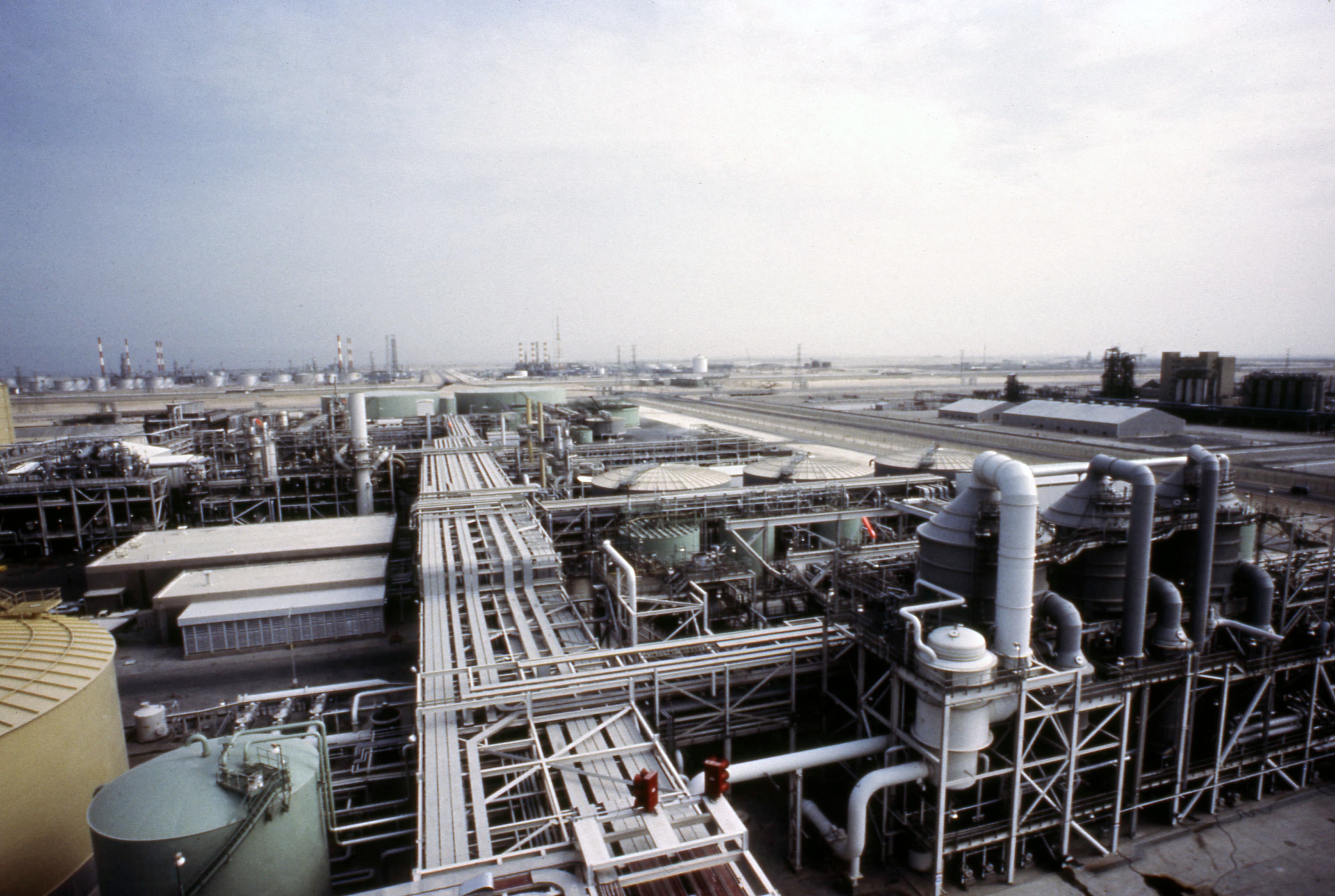
1977: Woodward, Oklahoma 1,200 tpd Ammonia Plant in operation
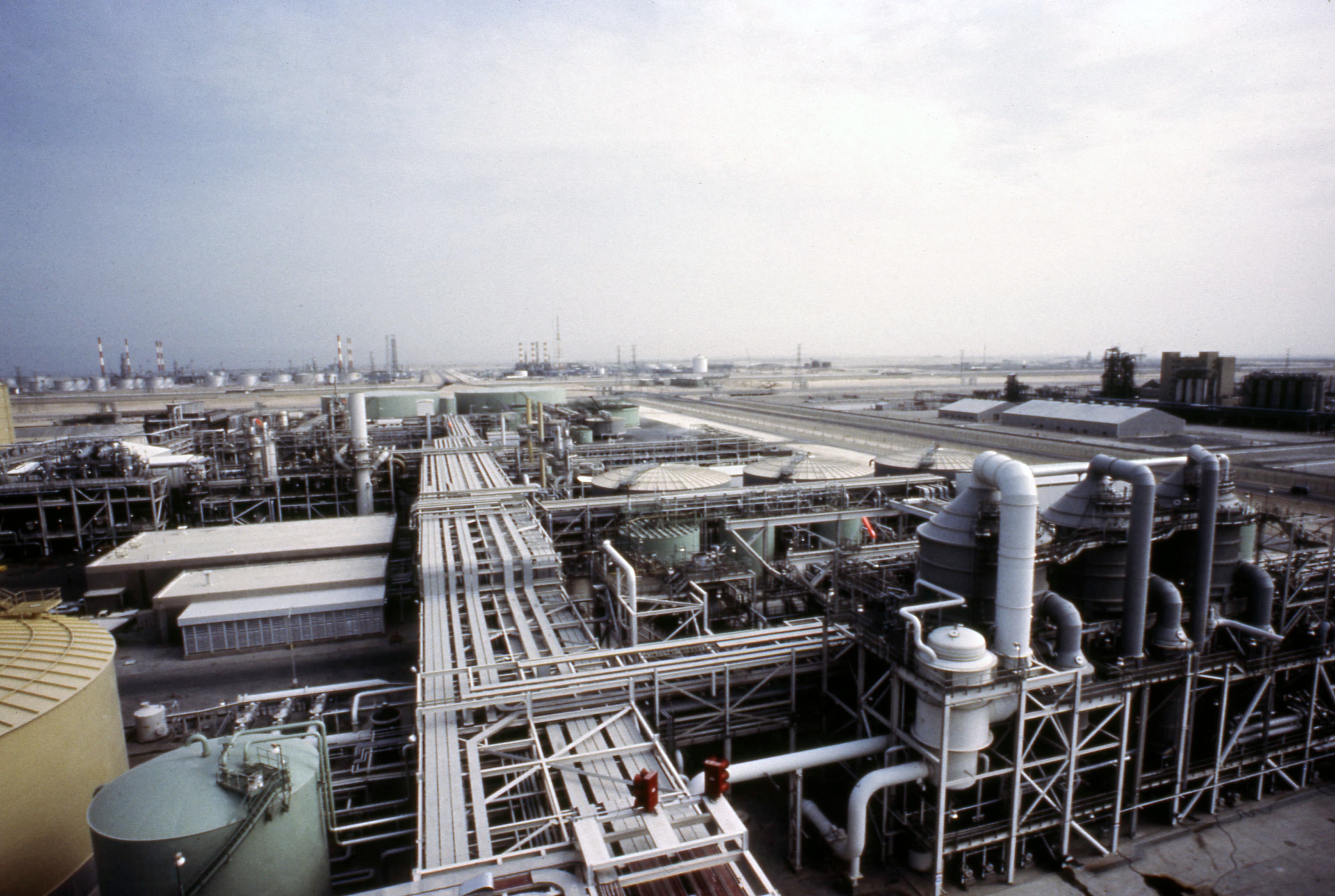
Fluor engineered, procured and constructed a 1,200 tpd Ammonia Plant using centrifugal compressors and Fluor patented ammonia processes. In addition, Fluor completed the scope for the utilities and offsites, which included a storage and loading system.
1978
Design and build of Degussa Carbon Black Corp Herbicides plant complete
&w=3840&q=75)
1978: Design and build of Degussa Carbon Black Corp Herbicides plant complete
&w=3840&q=75)
Between 1975 - 1978, Fluor provided design, construction and maintenance services to Degussa Carbon Black Corp for the construction and operations of their Theodore, Alabama herbicides plant.
1978
Rubicon Chemicals Plant operational in Geismar, Louisiana
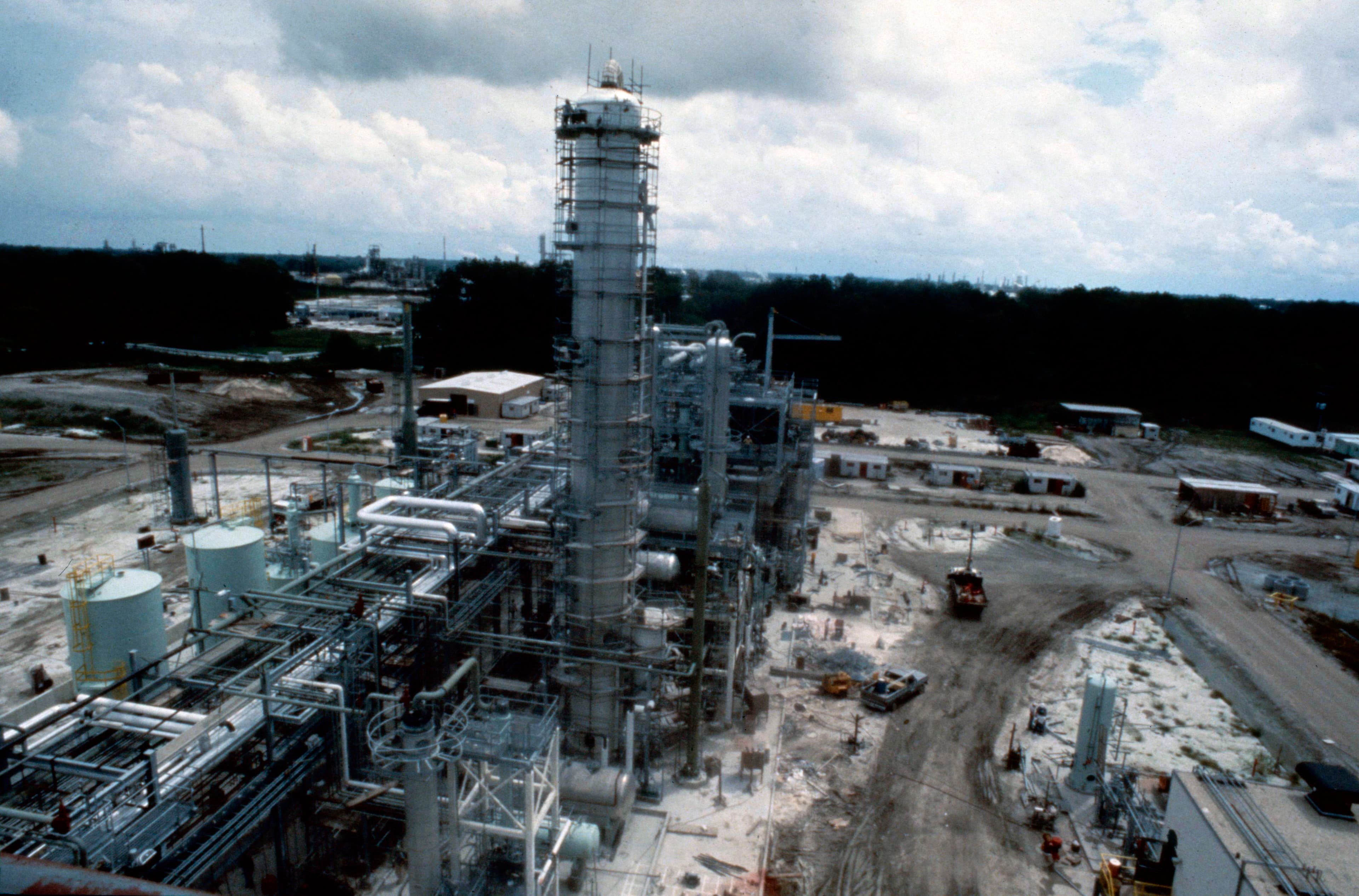
1978: Rubicon Chemicals Plant operational in Geismar, Louisiana
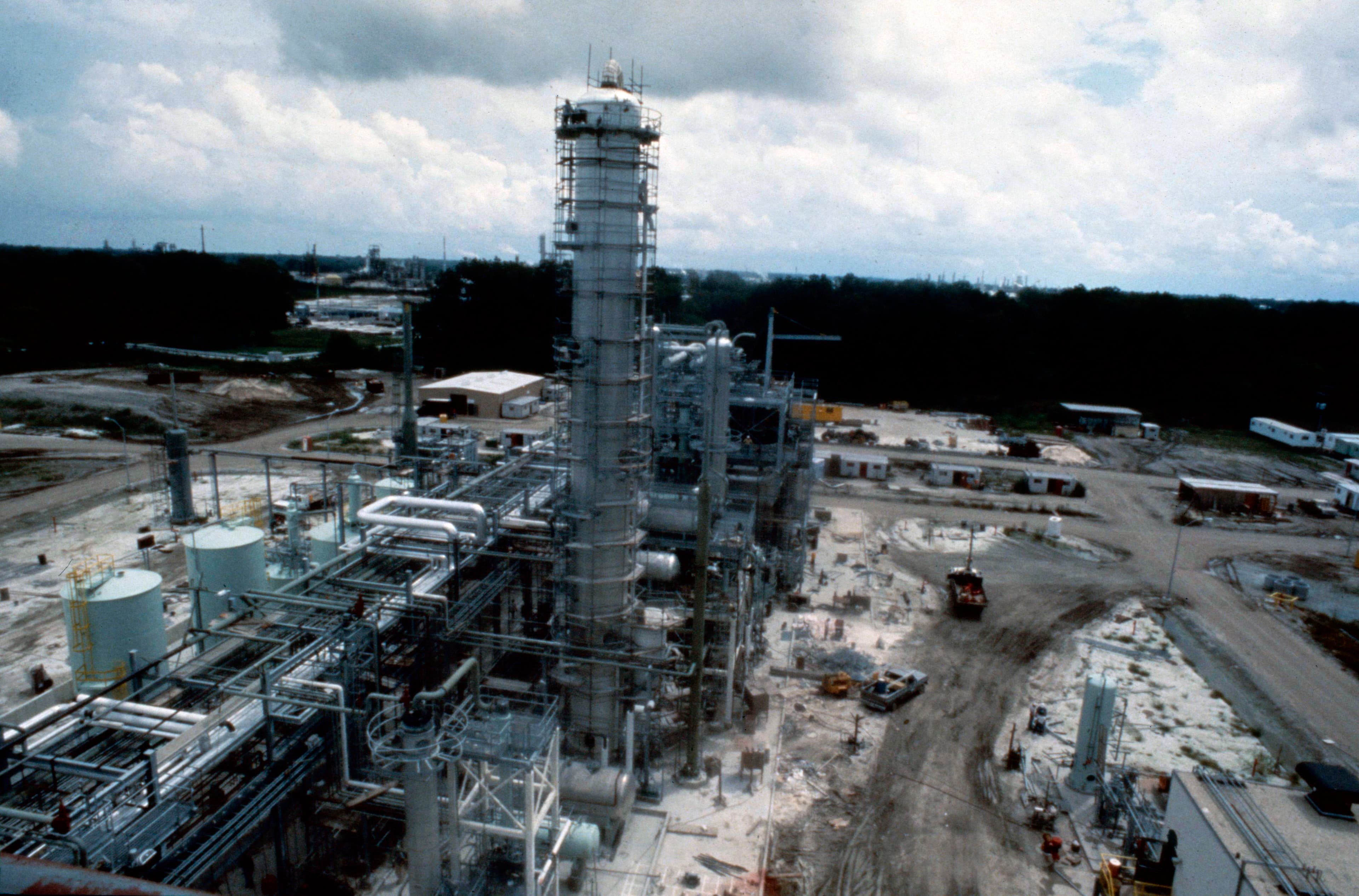
Rubicon Chemicals' Geismar plant developed the following end use products: aniline, nitrobenzene and DPA. Fluor constructed the facility in 1978.
1979
PEMEX grassroots aromatics complex processes catalytic reformate into benzene, toluene, orthoxylene, paraxylene, hexane, heptane and mixed xylenes
&w=3840&q=75)
1979: PEMEX grassroots aromatics complex processes catalytic reformate into benzene, toluene, orthoxylene, paraxylene, hexane, heptane and mixed xylenes
&w=3840&q=75)
Fluor performed engineering and procurement for the Petróleos Mexicanos (PEMEX) Aromatics Complex in Vera Cruz, Mexico. The petrochemical complex included a 240,000 tpy CRC paraxylene crystallization unit, 120,000 tpy toluene charge hydrodealkylation unit (HRI) and xylene isomerization (Octafiner).
1979
Geismar, Louisiana grassroots herbicide plant ties into existing chemical process facility
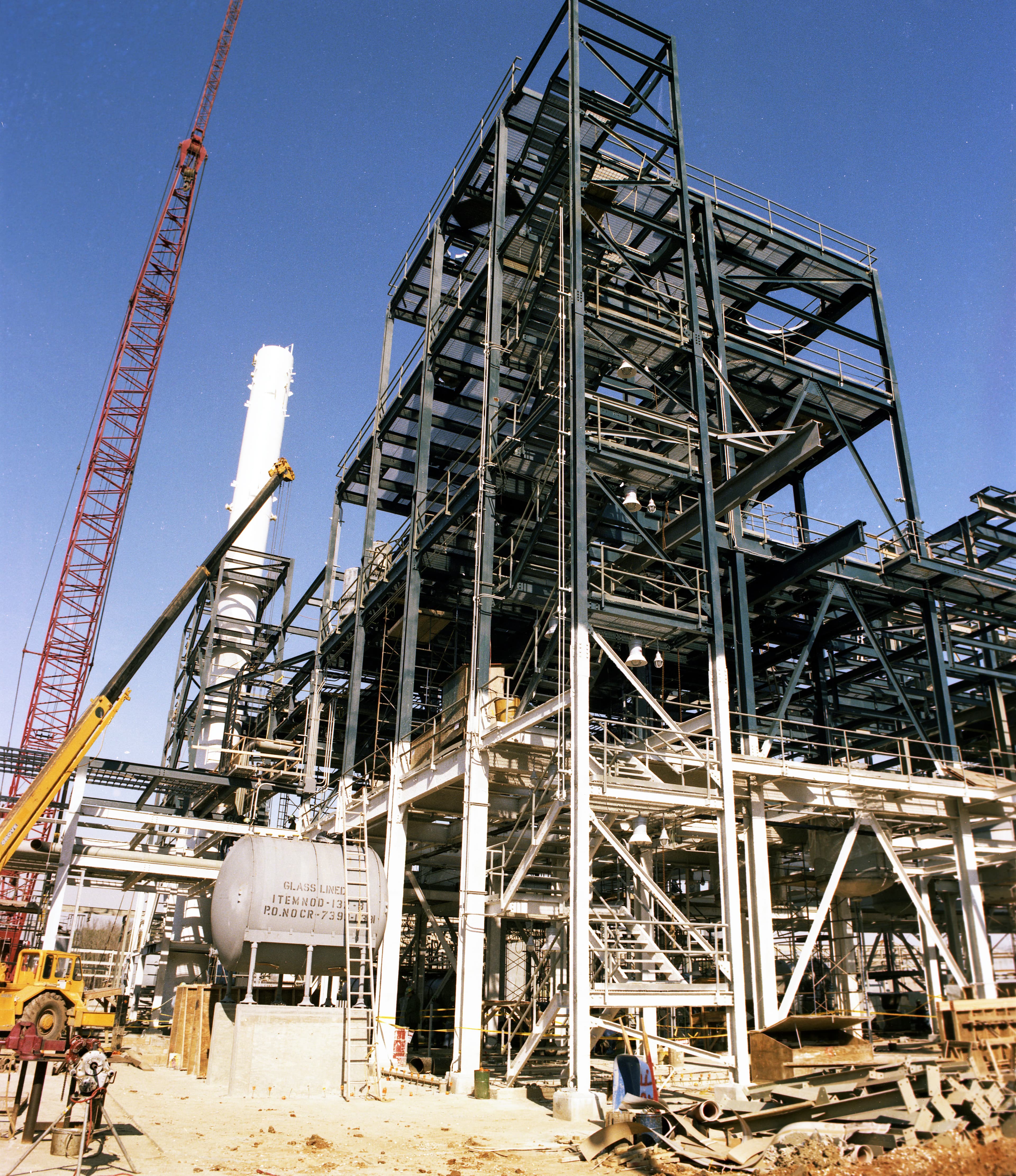
1979: Geismar, Louisiana grassroots herbicide plant ties into existing chemical process facility
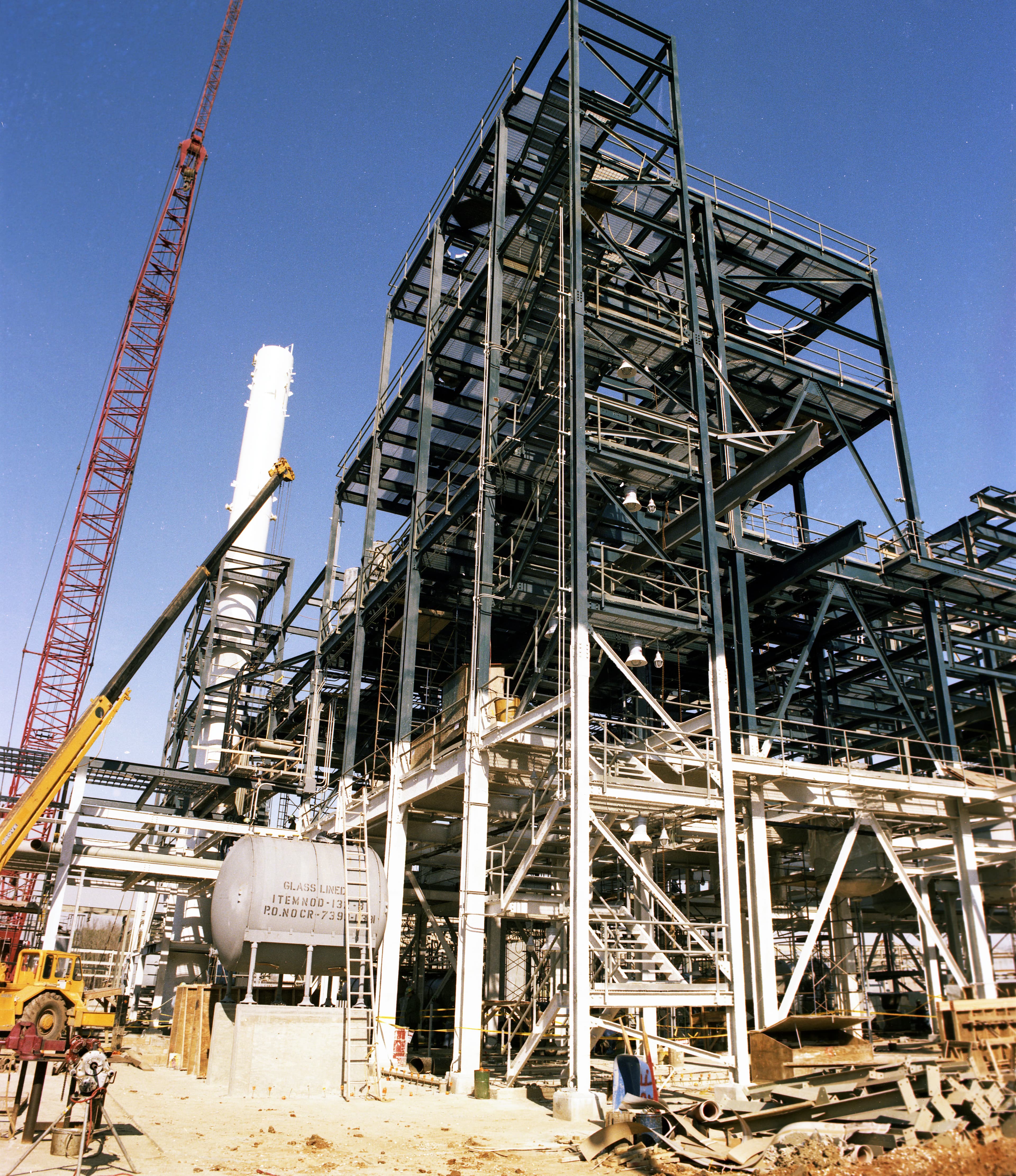
Fluor procured construction materials and completed construction responsibility for this grassroots herbicide plant. The site's location adjacent to an existing facility necessitated tie-ins to that facility. Total construction capital cost was in excess of $60 million. Manpower peaked at 850. Subcontracts for metal buildings, roofing, piling, site drainage and grading were issued.
1980s
Fluor employs a modular construction approach on a major downstream petrochemical complex.
1980
Vinyl Chloride Monomer Plant operational in Wilhelmshaven, Germany
&w=3840&q=75)
1980: Vinyl Chloride Monomer Plant operational in Wilhelmshaven, Germany
&w=3840&q=75)
Fluor provided the engineering, procurement and construction management for a vinyl chloride monomer plant in Wilhelmshaven, Germany. The project was completed in 1980.
1982
Methanol plant expansion increases Alberta Gas Chemical's production capacity to 1,200 tpd
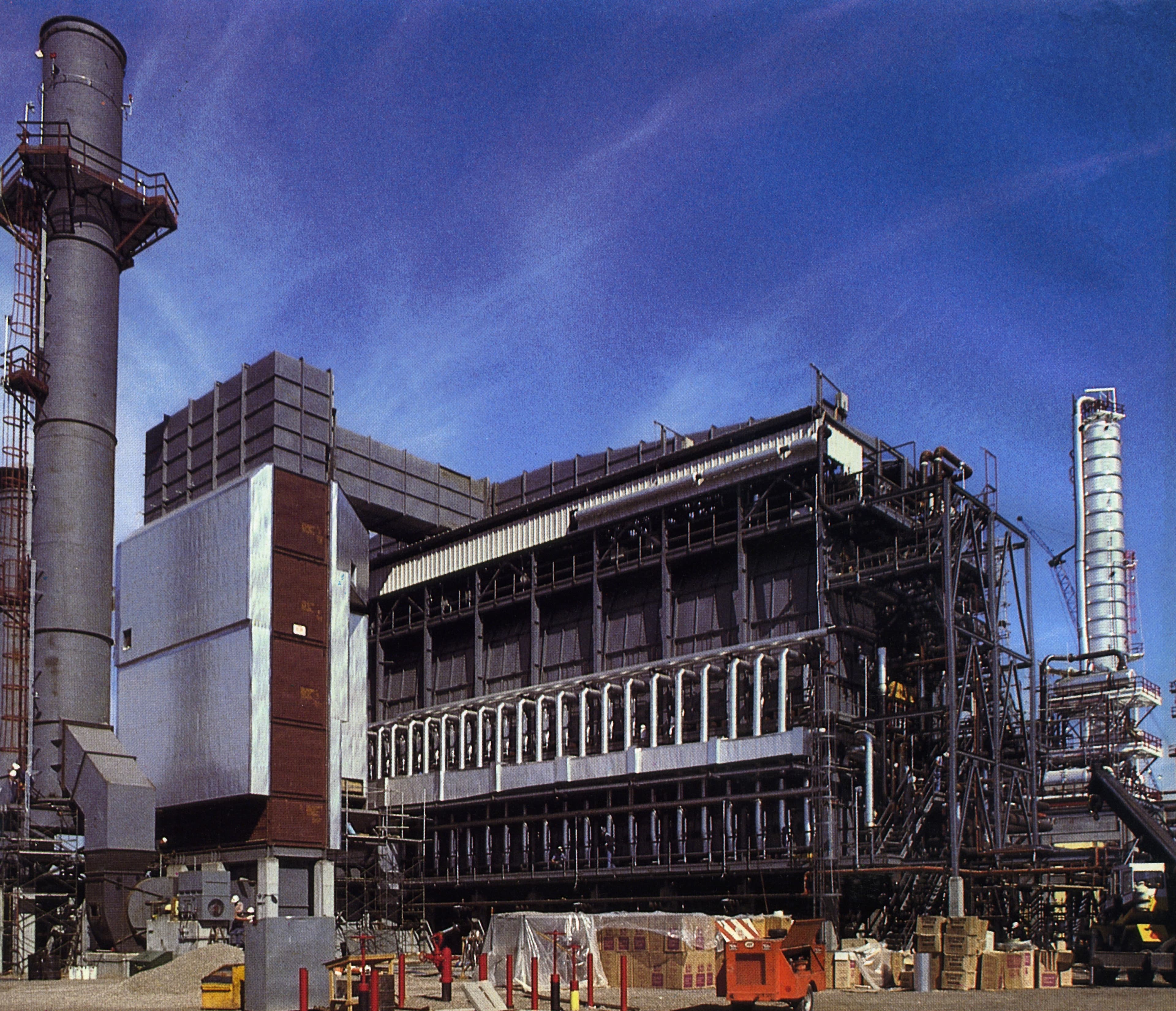
1982: Methanol plant expansion increases Alberta Gas Chemical's production capacity to 1,200 tpd
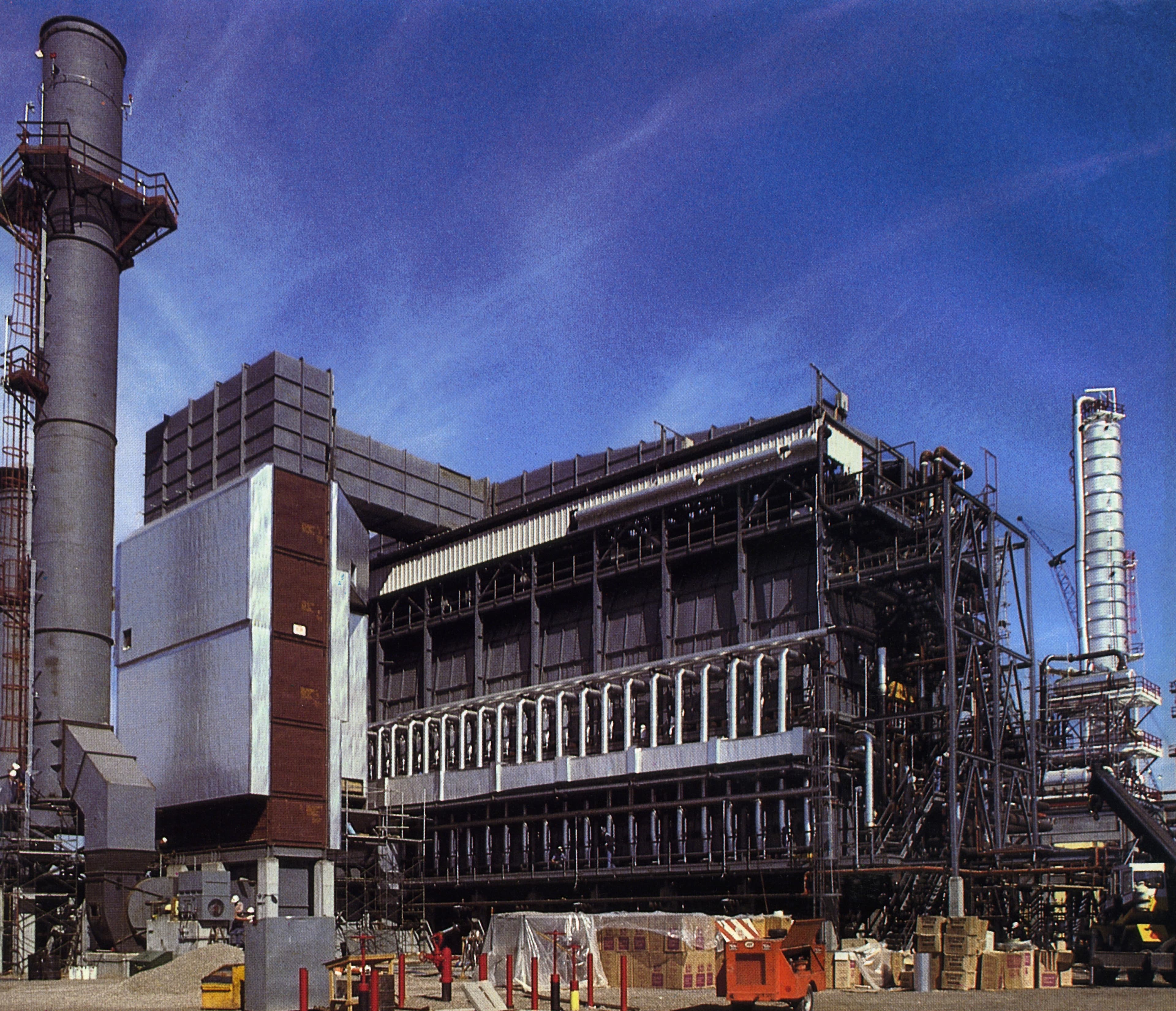
Fluor built the largest single-unit reformer to date in Canada. It was a key element Alberta Gas Chemical's Methanol Plant Expansion in Medicine Hat, Alberta. Fluor's project scope encompassed the engineering, procurement and construction of this world-scale, 1,200 tpd methanol plant including reforming, compression and synthesis, distillation, offsites, utilities and integration with the existing facility.
1982
Herbicides plant starts production in Laudenbach, Germany
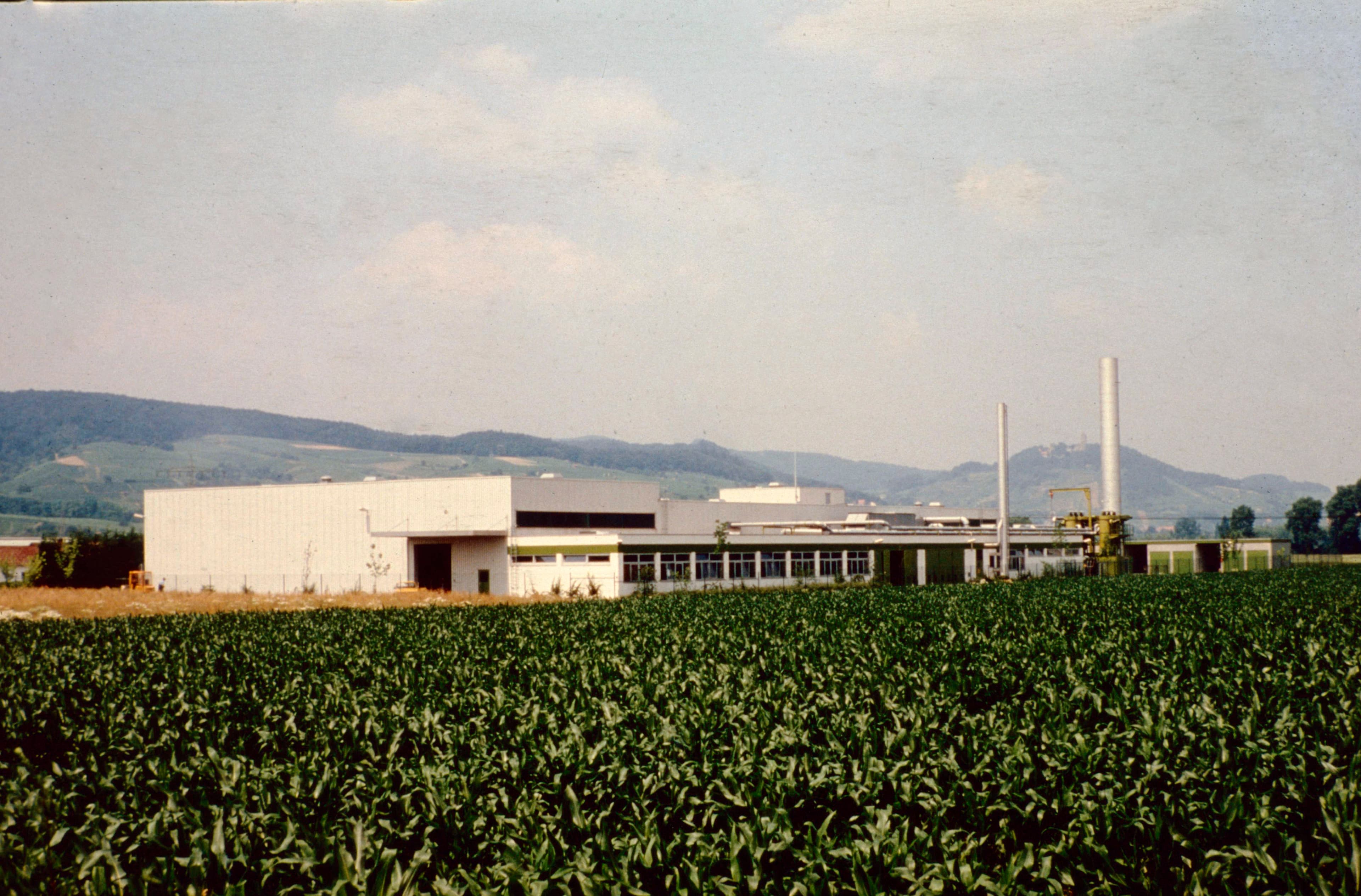
1982: Herbicides plant starts production in Laudenbach, Germany
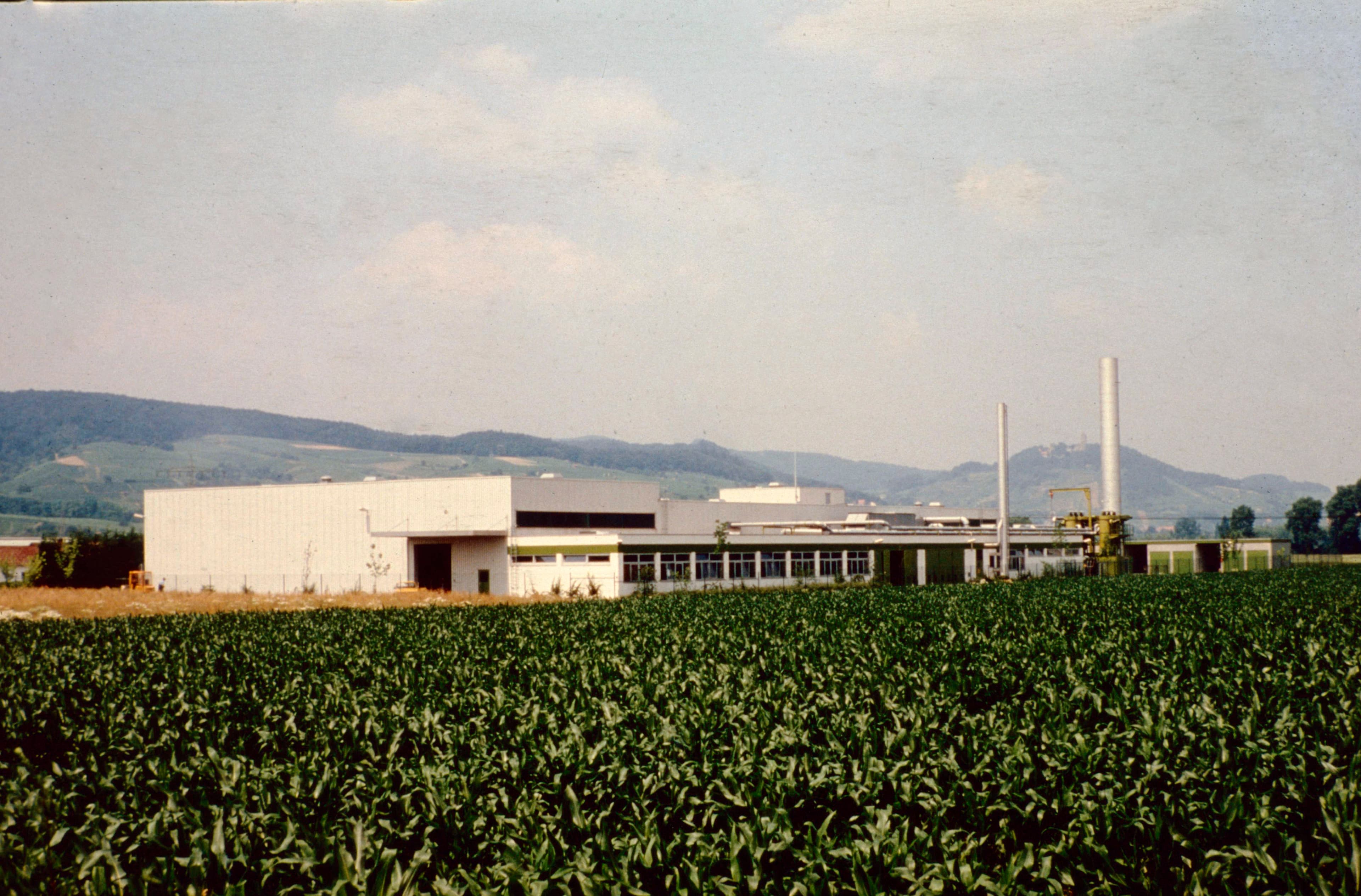
Fluor procured and constructed a herbicides plant and warehouse in Laudenbach, Germany. Fluor was contracted by Detia Freyberg GMBH in 1980, and the project was completed in 1982.
1983
Fluor constructs Canada's largest polyethylene facility
&w=3840&q=75)
1983: Fluor constructs Canada's largest polyethylene facility
&w=3840&q=75)
In spite of a tight construction schedule, Canada's largest polyethylene facility was constructed on time, under budget and exceeded expectations of initial operations. The plant was designed to produce 270,000 metric tons per year of linear low-density polyethylene (LLDPE).
1984
Al Jubail Petrochemical company produces 260,000 tpy LLDPE at new grassroots plant
1984: Al Jubail Petrochemical company produces 260,000 tpy LLDPE at new grassroots plant
Fluor was responsible for the design, detailed engineering, procurement and construction management of this grassroots state of the art linear low density polyethylene plant, which produces 260,000 tpy. Ethylene feedstock for the polymer plant was supplied by the Saudi Petrochemical Company (SADAF) complex, also constructed by Fluor.
A total of 28 modules were used on the project. Modules were constructed in Korea, and arrived to the site with all structures, equipment, piping and electrical work already installed on a permanent steel base frame.
The project was completed in August 1984, approximately three months ahead of schedule.
1984
Fluor Canada completes grassroots 1,200-metric tpd methanol plant in New Zealand
&w=3840&q=75)
1984: Fluor Canada completes grassroots 1,200-metric tpd methanol plant in New Zealand
&w=3840&q=75)
Fluor performed engineering, procurement and construction management support for Petralgas’s grassroots, 1,200-metric tpd methanol plant in Waitara, New Zealand. Fluor also participated in front-end optimization studies, developed computer simulations and was responsible for all equipment data sheets for all onsite systems, as well as many offsite systems. This was one of Fluor Canada's first international projects.
1985
Modules successfully installed at SADAF's 500‑acre, major downstream petrochemical complex
&w=3840&q=75)
1985: Modules successfully installed at SADAF's 500‑acre, major downstream petrochemical complex
&w=3840&q=75)
Fluor served as the managing contractor on a grassroots ethylene-based petrochemical complex for Saudi Arabia Petrochemical Company (SADAF) in Al Jubail, Saudi Arabia. The complex produced ethylene, ethyl-benzene, styrene, ethylene dichloride, chlorine, caustic soda and crude industrial ethanol. It depended in large part on feed streams from the gas-gathering project done by Fluor for the Aramco gas program. The complex, in turn, would provide some of the output to feed Al Jubail Petrochemical Company’s nearly linear low density polyethylene plant, also a Fluor project. Approximately 40% of the complex was completed using modular construction, the largest modular project at the time.
1988
Fluor takes over engineering of Petrolite's Polyethylene Wax Facility in Barnsdall, Oklahoma
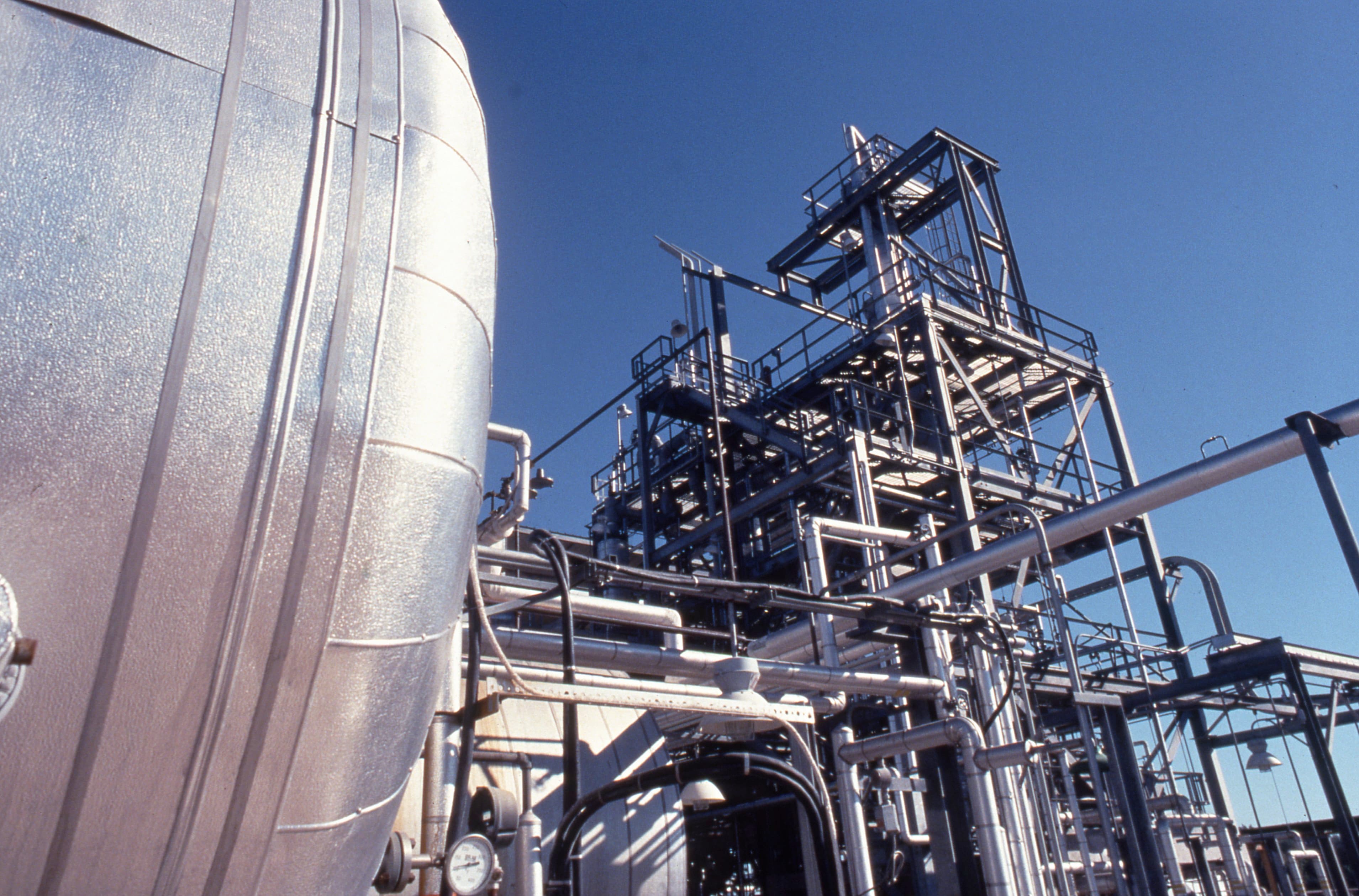
1988: Fluor takes over engineering of Petrolite's Polyethylene Wax Facility in Barnsdall, Oklahoma
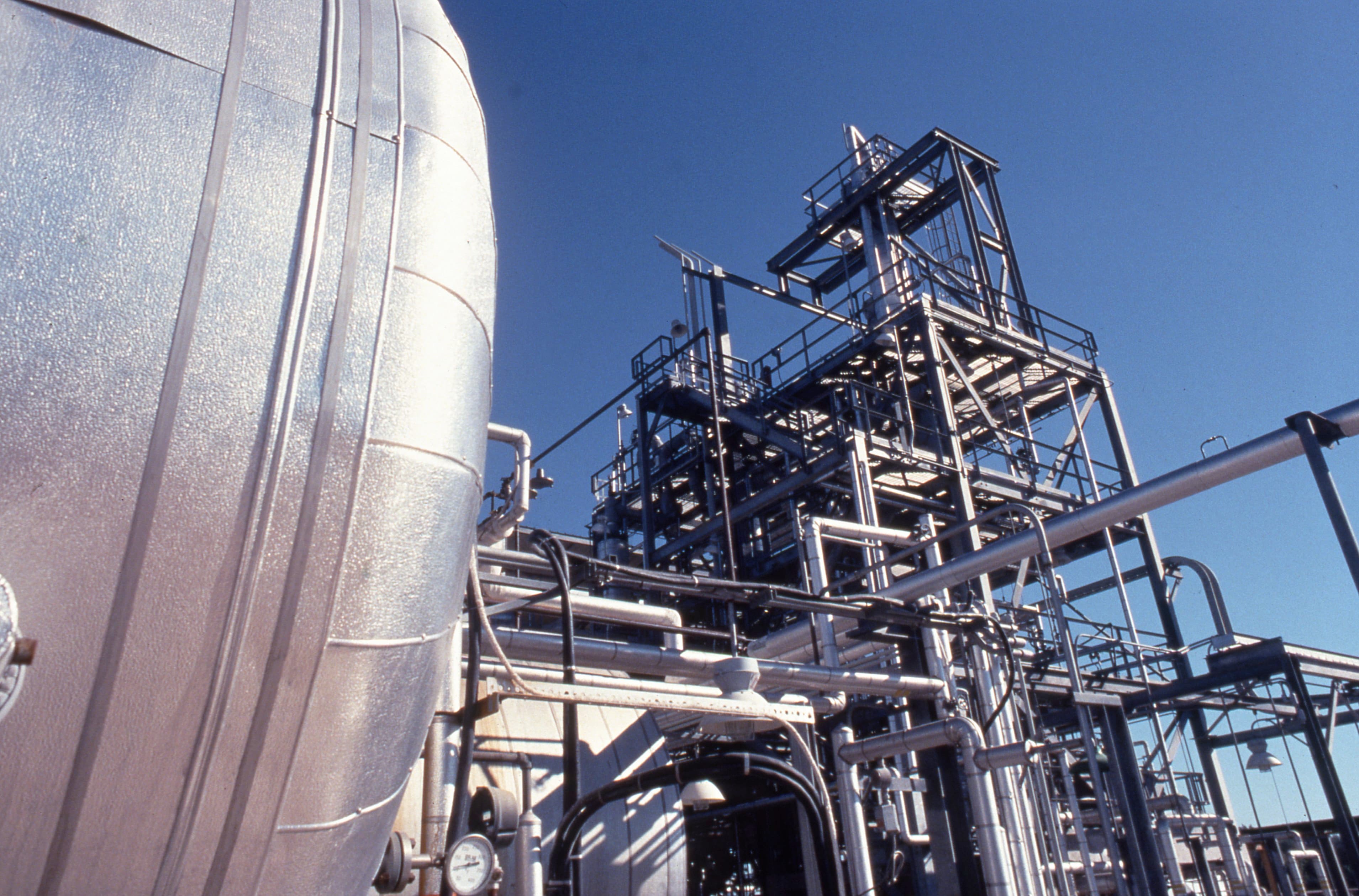
Fluor performed engineering, procurement and construction services for Petrolite's Polyethylene Wax Facility. The facility was located in Barnsdall, Oklahoma. Fluor was awarded the project in March and completed it in September of that year.
1989
Shantou Ocean Services 50,000-tpy grassroots polystyrene plant awarded
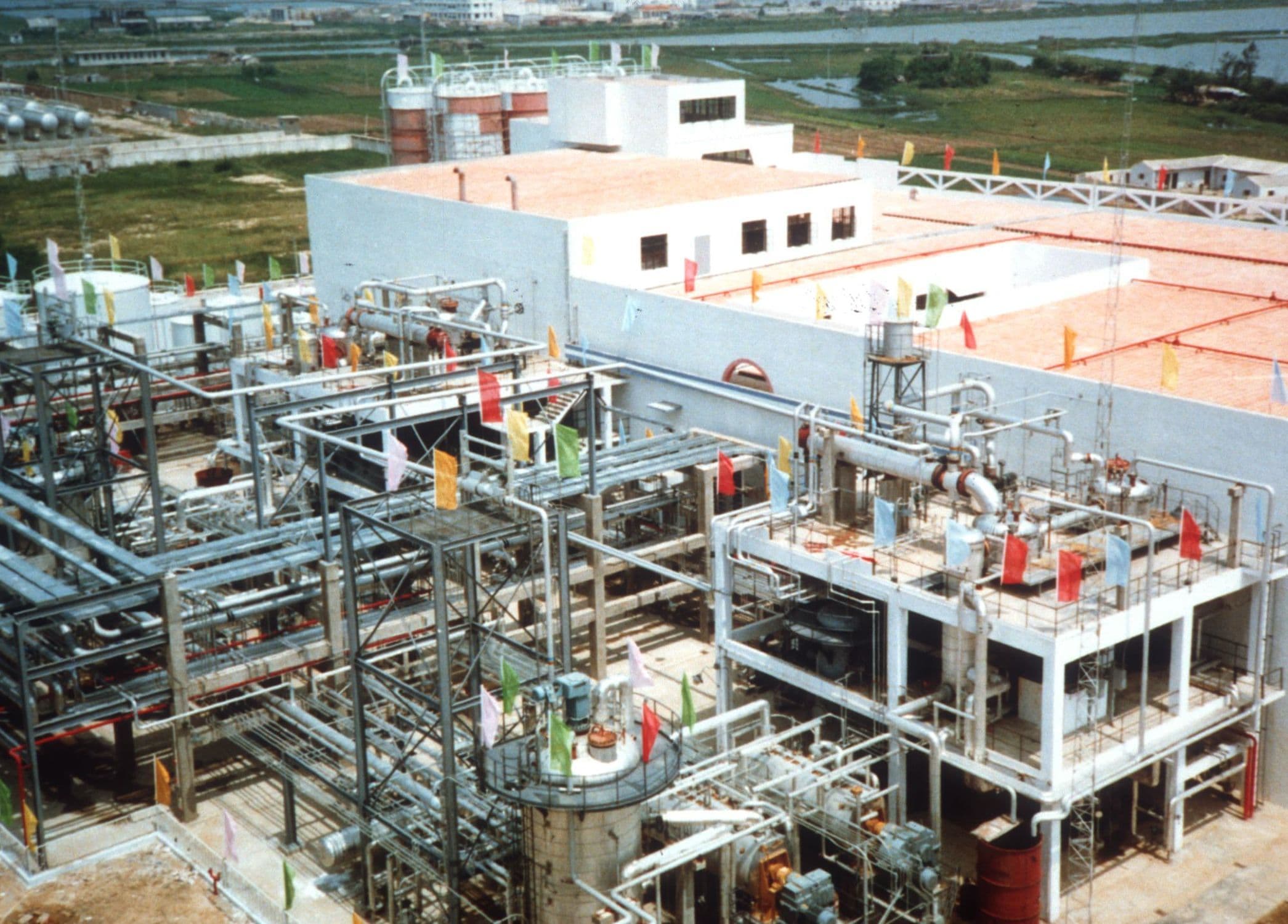
1989: Shantou Ocean Services 50,000-tpy grassroots polystyrene plant awarded
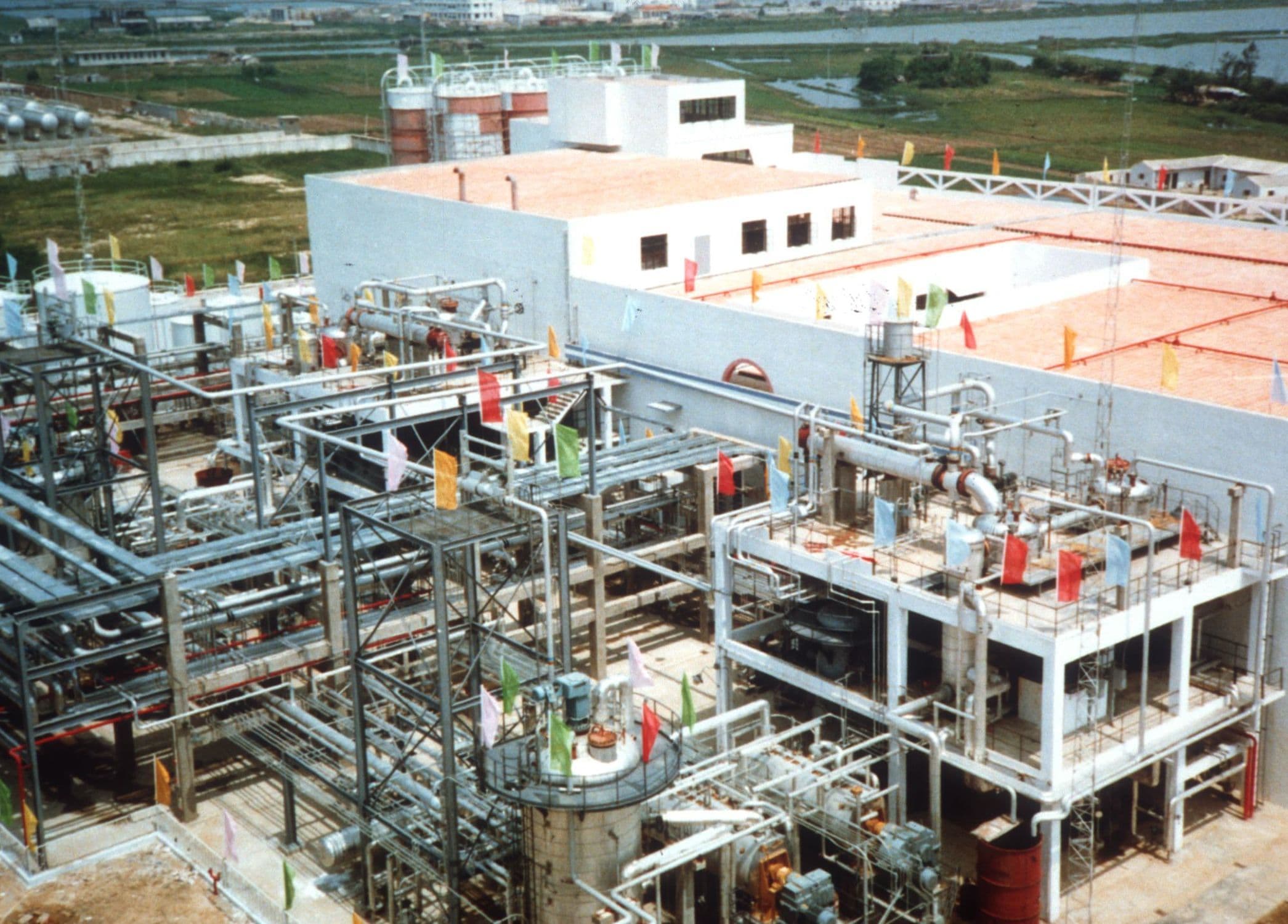
The lump-sum 50,000-tpy grassroots plant included a two-train continuous solvent polymerization plant that produced high-impact and general purpose polystyrene with its design based on Fina licensed technology. Fluor executed engineering, procurement of major offshore equipment and bulk materials and construction management.
1990s
Fluor capitalizes on world-first technology to build Canadian MTBE plant.
1990
Henkel KGaA TAED plant commissioning begins 15 months after the start of construction
1990: Henkel KGaA TAED plant commissioning begins 15 months after the start of construction
Fluor provided detailed engineering, procurement and construction management services for Henkel's TAED plant in Cork, Ireland. The plant produces the bleach activator tetraacetylethylenediamine (TAED) as a granulated crystal by the two-stage reaction of ethylene diamine with acetic acid and acetic anhydride. The plant consists of a five-story building of two parts: an open-steel structure which houses the liquids processing function, and a closed reinforced concrete section containing the solids processing area. All process facilities are fully automated. Fluor completed the design and construction of the plant and handed over to the client in 19 months.
1990
DuPont European Lycra® Facilities Expansion Program underway
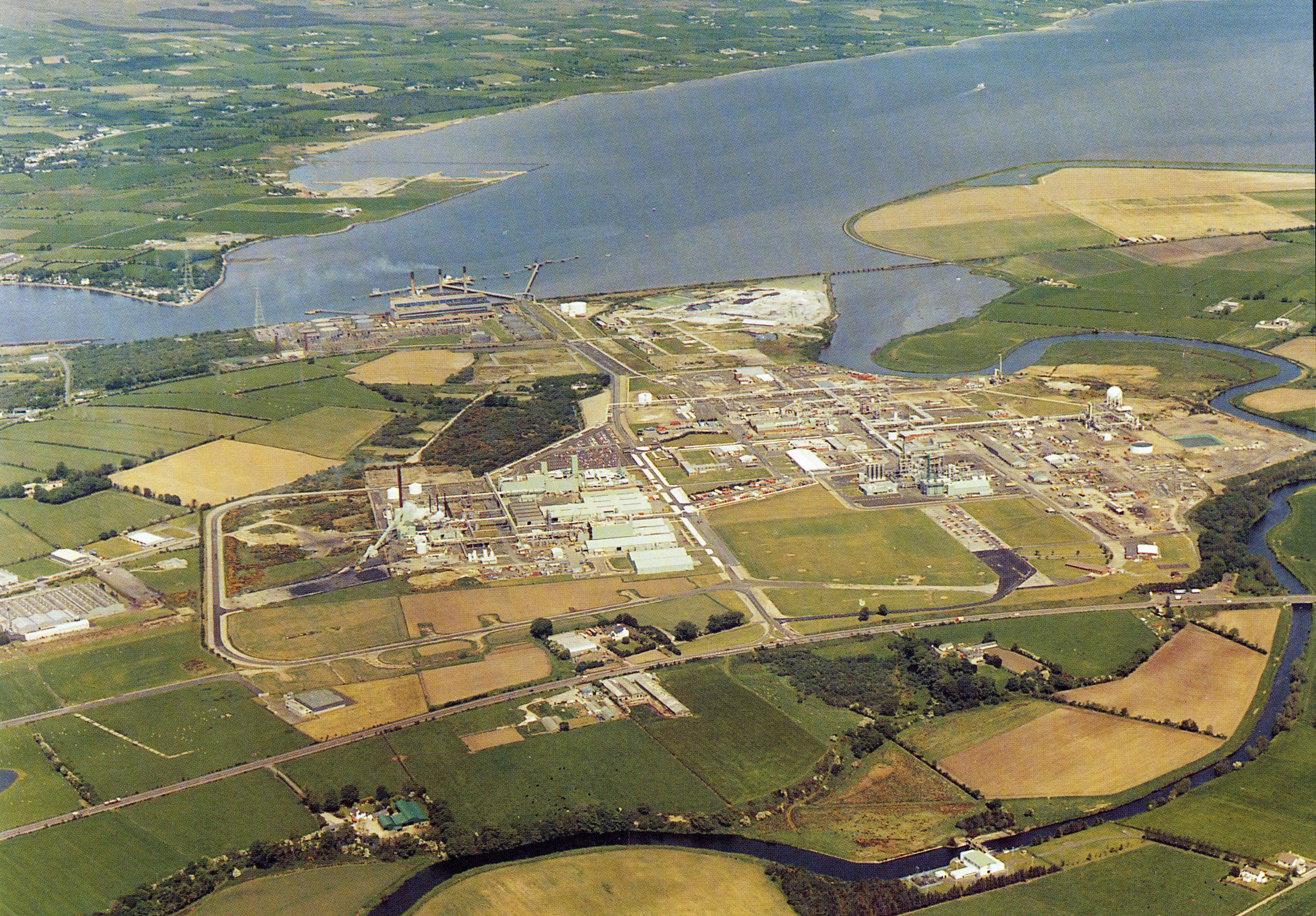
1990: DuPont European Lycra® Facilities Expansion Program underway
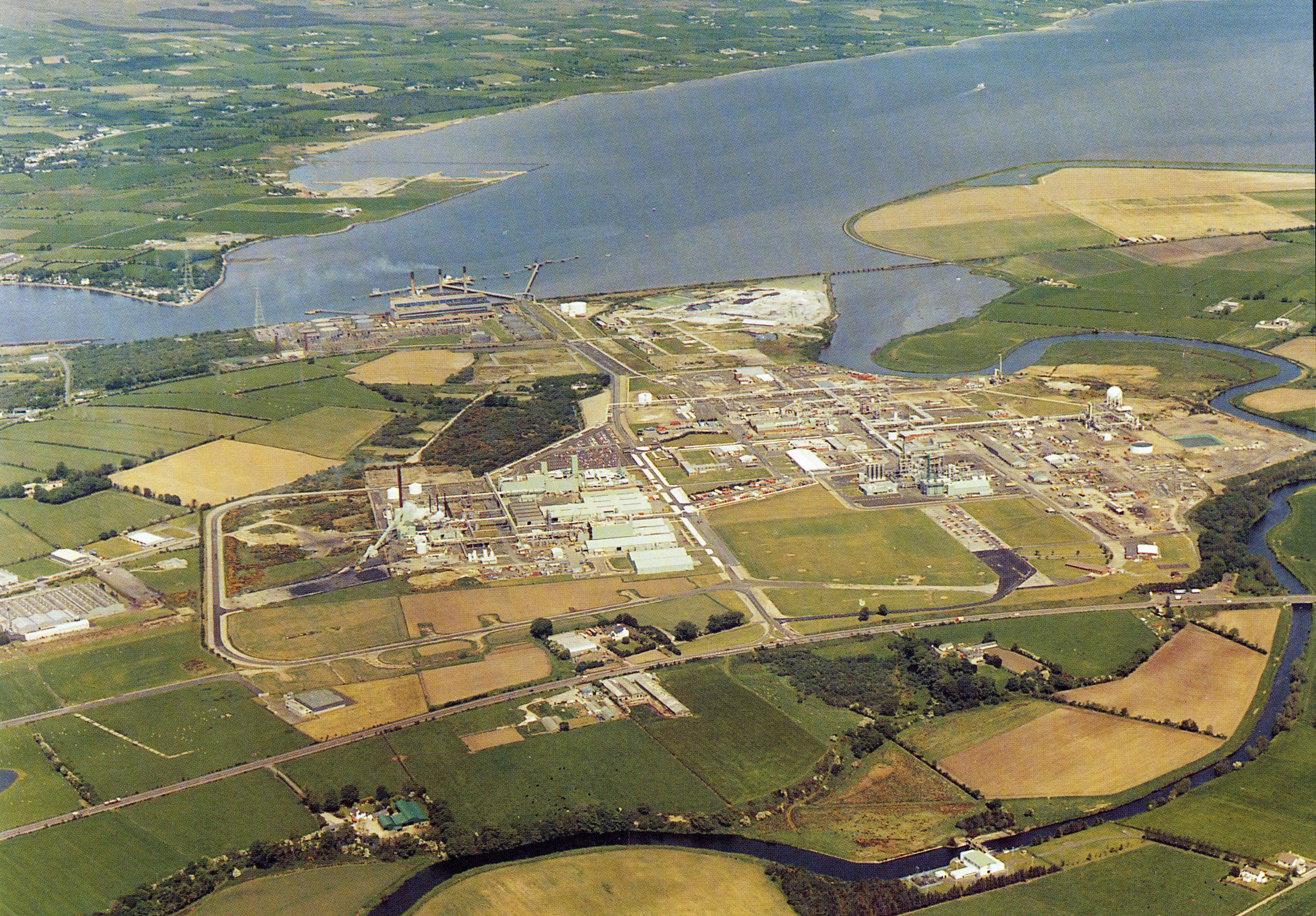
Fluor performed engineering services for DuPont for their continuous expansion program of Lycra plants in The Netherlands and Northern Ireland. To increase the production capacity and to allow flexibility in product lines, the existing facilities were extended to include raw material handling, additional polymerization units, polymer storage, extra spinning machines, enlarged yarn inspection and packing and storage facilities. Supporting utilities, including solvent recovery, nitrogen gas system, HVAC and feeders for purchased power, were added to serve the increased plant demand. The additional facilities incorporated distributed control equipment, partly as an extension to the existing system and partly as a new and separate system.
1991
Hydrogen Peroxide Facility reaches mechanical completion
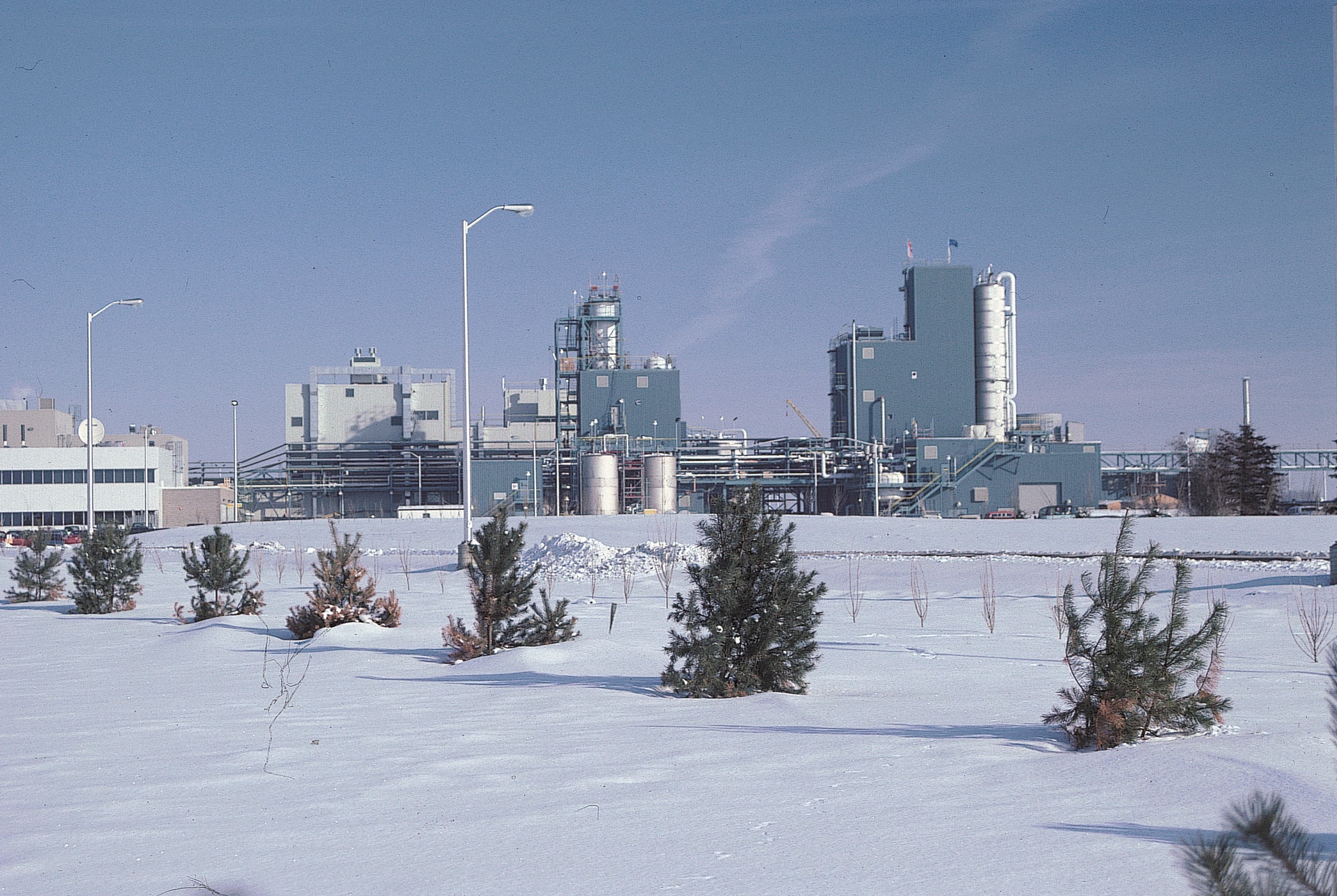
1991: Hydrogen Peroxide Facility reaches mechanical completion
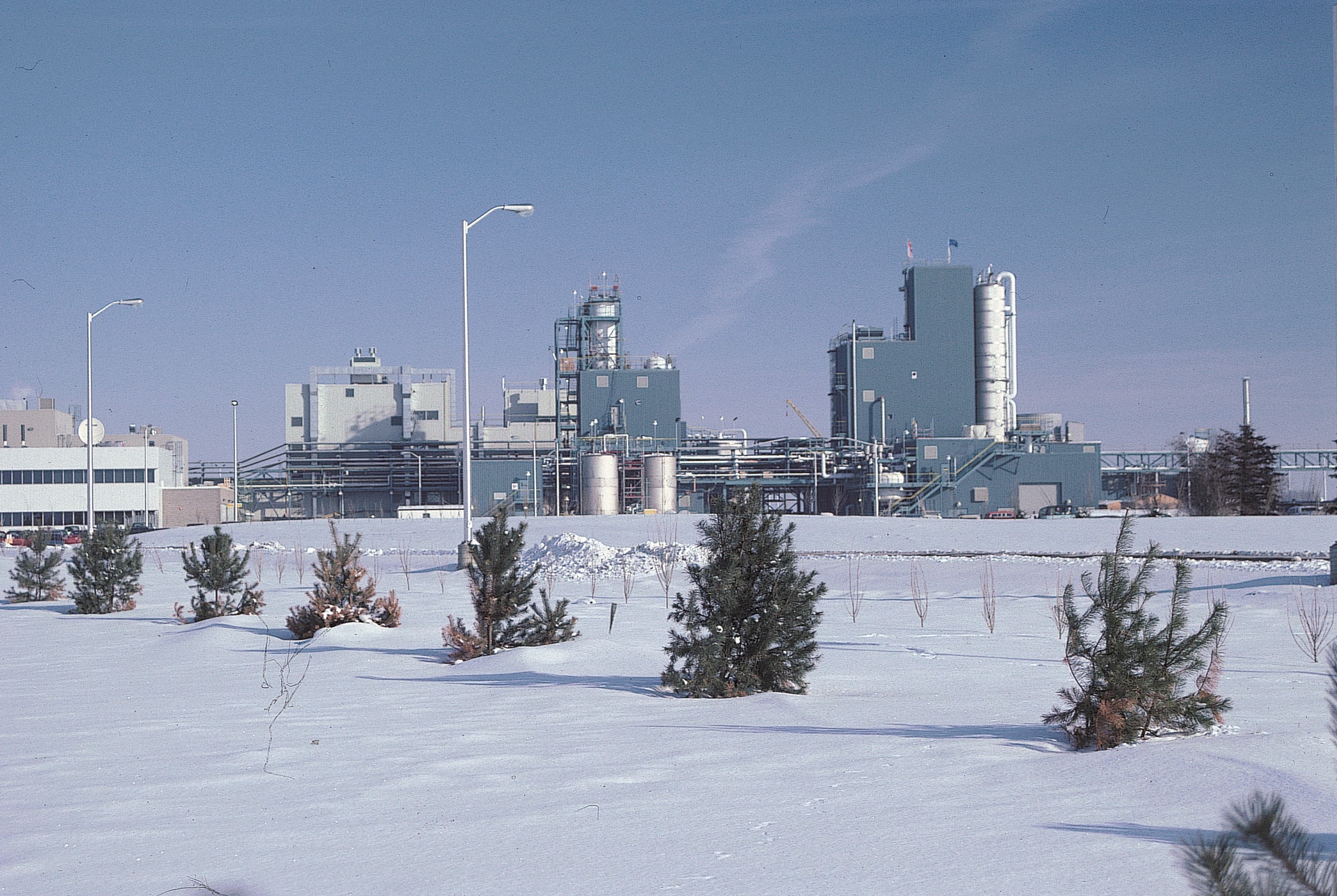
DuPont's hydrogen peroxide plant was signed over to the client in 1991. Fluor provided detailed engineering, procurement assistance and construction services for the grassroots 36,000-ton/year facility.
1991
Fluor completes Alberta EnviroFuels grassroots 530,000 tpy MTBE plant
&w=3840&q=75)
1991: Fluor completes Alberta EnviroFuels grassroots 530,000 tpy MTBE plant
&w=3840&q=75)
Capitalizing on technology never before used anywhere in the world, Fluor performed engineering, procurement, and construction on Alberta EnviroFuels’ $360 million methyl tertiary butyl ether (MTBE) manufacturing plant. The Canadian-based plant was the first of its kind in North America. Located in Strathcona County – which is east of Edmonton – EnviroFuels’ new factory commenced operation in early 1992 achieving an annual production capacity of 530,000 tons of MTBE. In completing the project, Fluor developed a fast-track execution plan using many innovations. Some of those approaches included the use of piperack modularization and erection/transport of field super modules; extensive use of precast concrete for structures; pre-dressing of major columns; shop fabrication of mall-bore piping as well as the use of 3D CAD.
1991
Start-up at Hoechst Celanese Pampa Plant complete 18 months after major chemical explosion
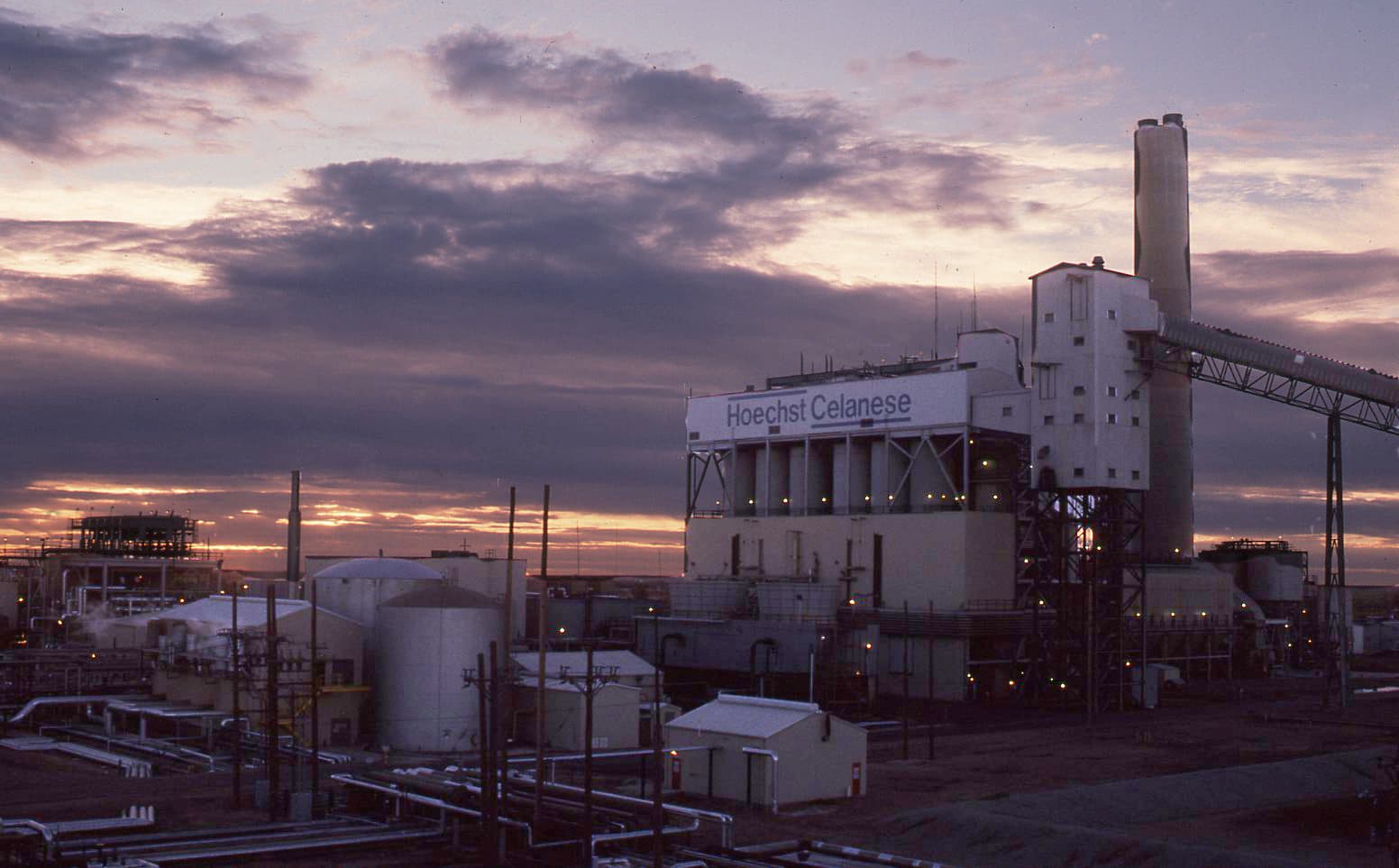
1991: Start-up at Hoechst Celanese Pampa Plant complete 18 months after major chemical explosion
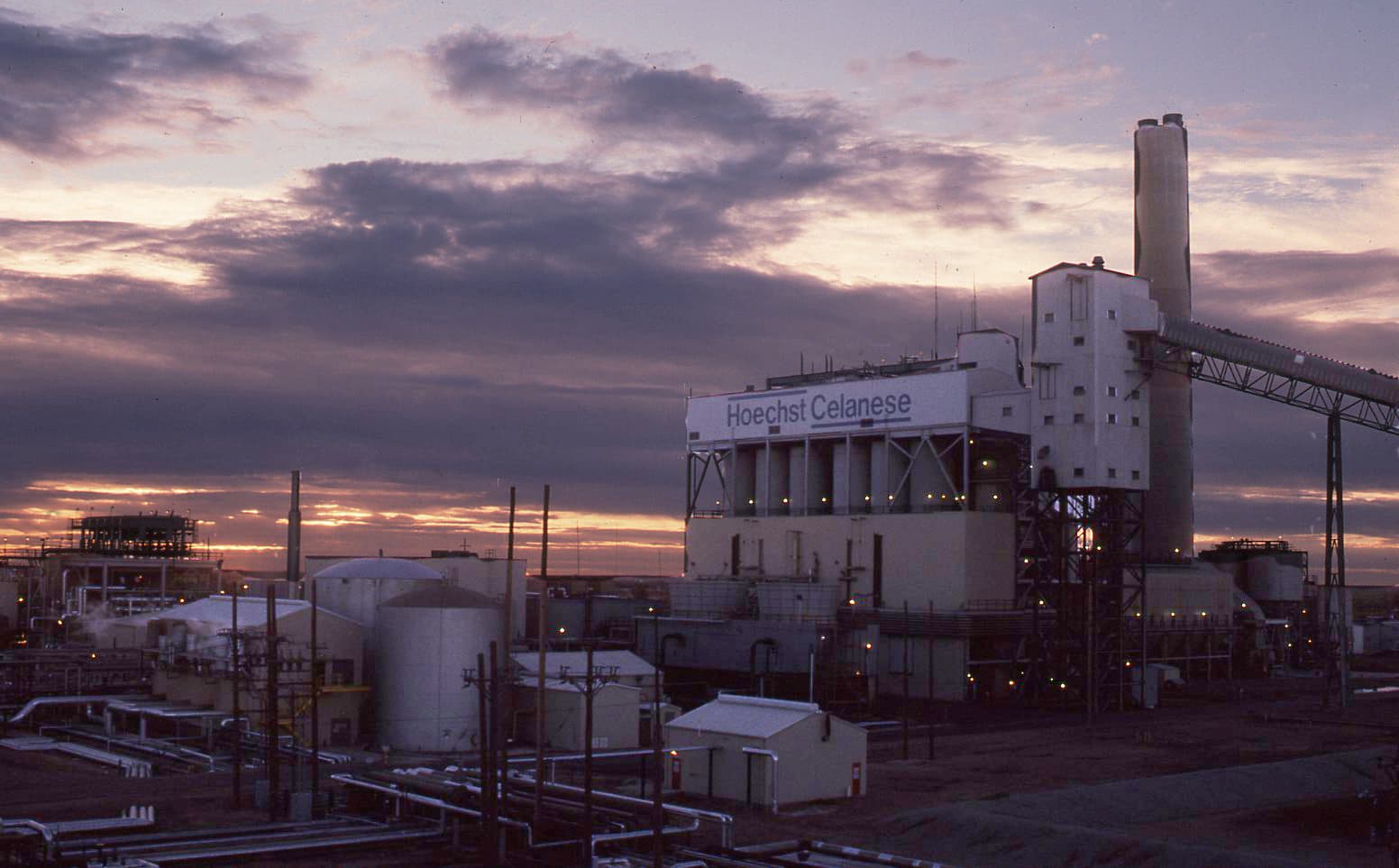
Fluor was contracted by Hoechst Celanese to provide engineering, procurement and construction support for the rebuild of the Pampa plant immediately following a major explosion that resulted in extensive damage and shutdown of the facility. The plant produces a variety of organic chemicals.Hoechst Celanese decided to rebuild the facility in a short time period due to market conditions and to the extensive business interruption costs being incurred. Fluor accomplished the demolition, decommissioning, rebuilding and start-up in an 18-month period. An original 30-month schedule was anticipated by Hoechst Celanese. Remediation of the facility involved extensive joint planning with Hoechst Celanese and Fluor, requiring simultaneous planning, engineering, demolition, procurement and construction activities.
1993
Grassroots Fiber Grade Acetate Plant built adjacent to existing Tennessee Eastman site achieves mechanical completion
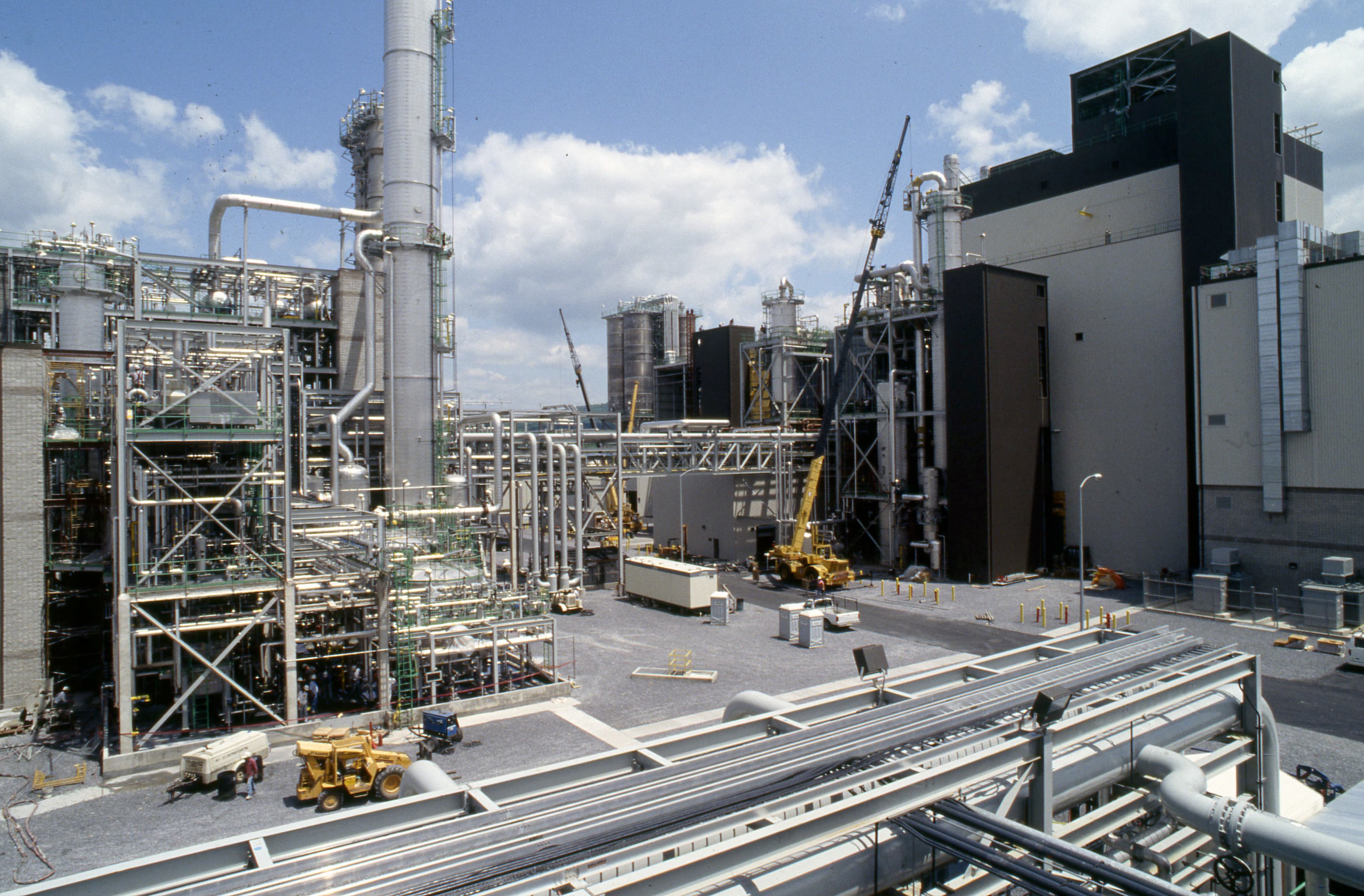
1993: Grassroots Fiber Grade Acetate Plant built adjacent to existing Tennessee Eastman site achieves mechanical completion
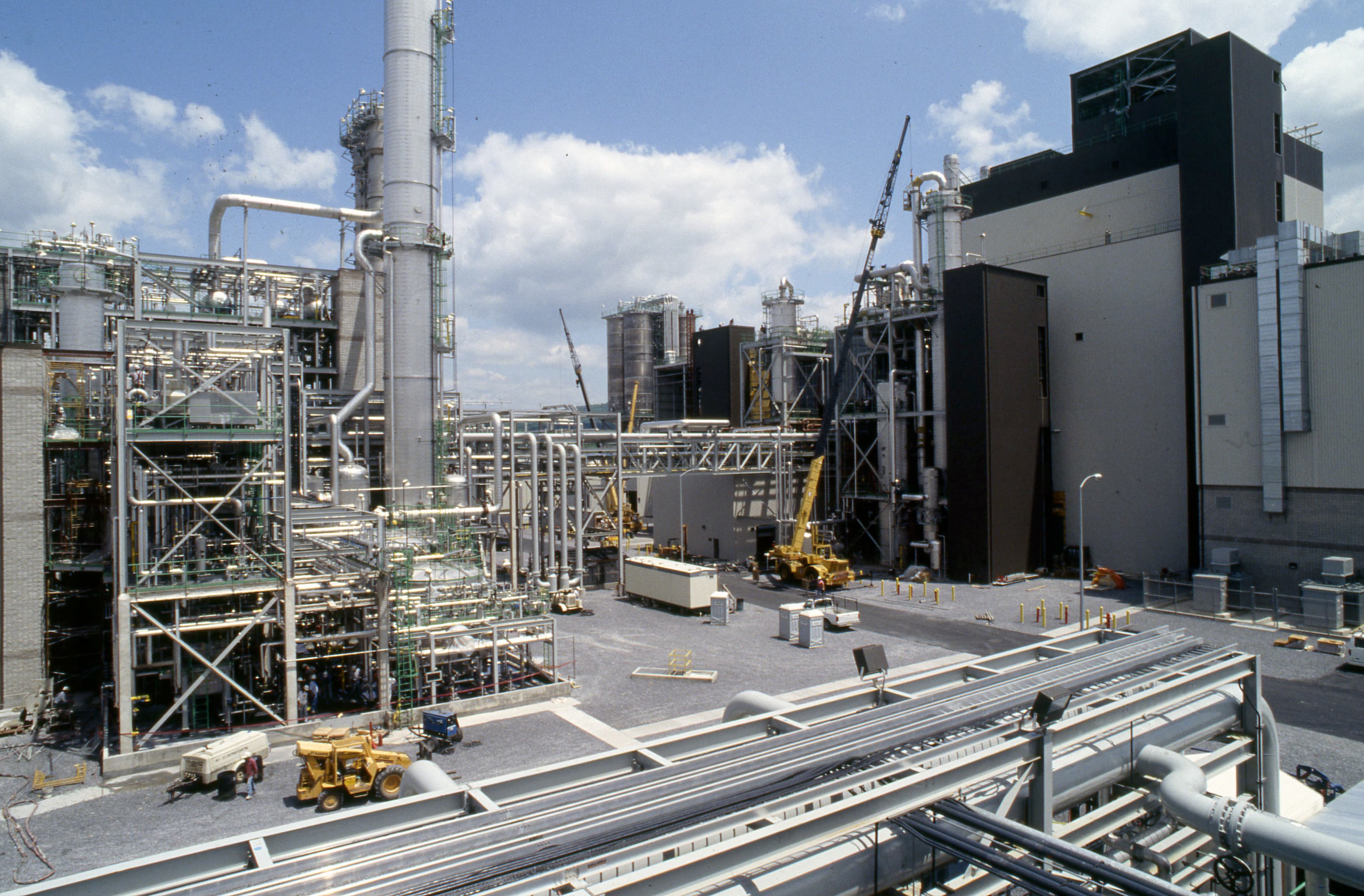
PRIMESTER, a joint venture between Eastman Chemical Company and Rhone Poulenc S.A., contracted Fluor in 1991 to provide engineering, procurement and construction services for a fiber grade acetate plant. Eastman had primary responsibility for project execution. The most important factors that contributed to project success were quality management and PRIMESTER and Fluor alignment. The project was completed ahead of schedule with significant savings.
1993
GE Plastics Polycarbonate Resin Manufacturing Complex produces LEXAN©
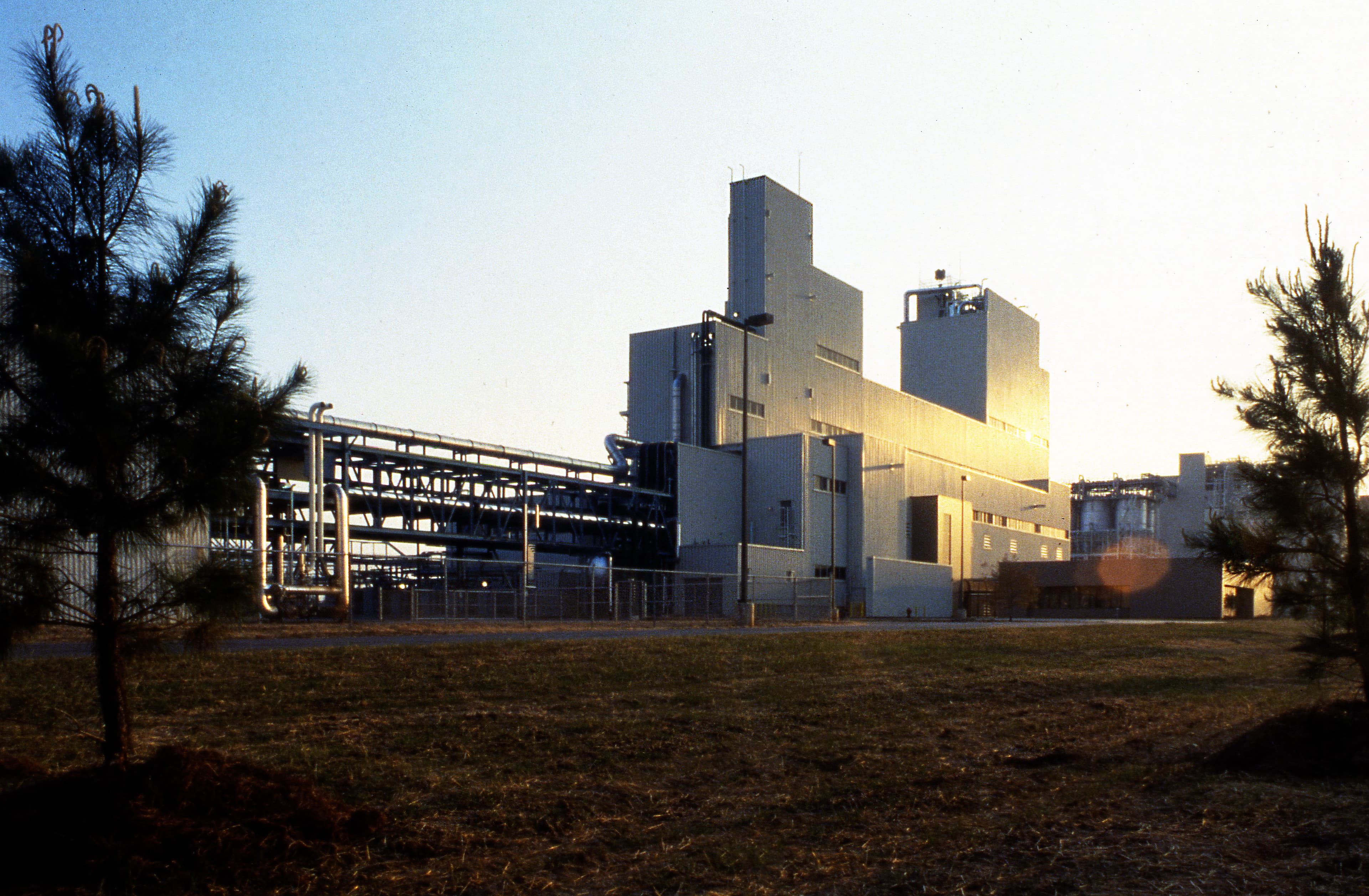
1993: GE Plastics Polycarbonate Resin Manufacturing Complex produces LEXAN©
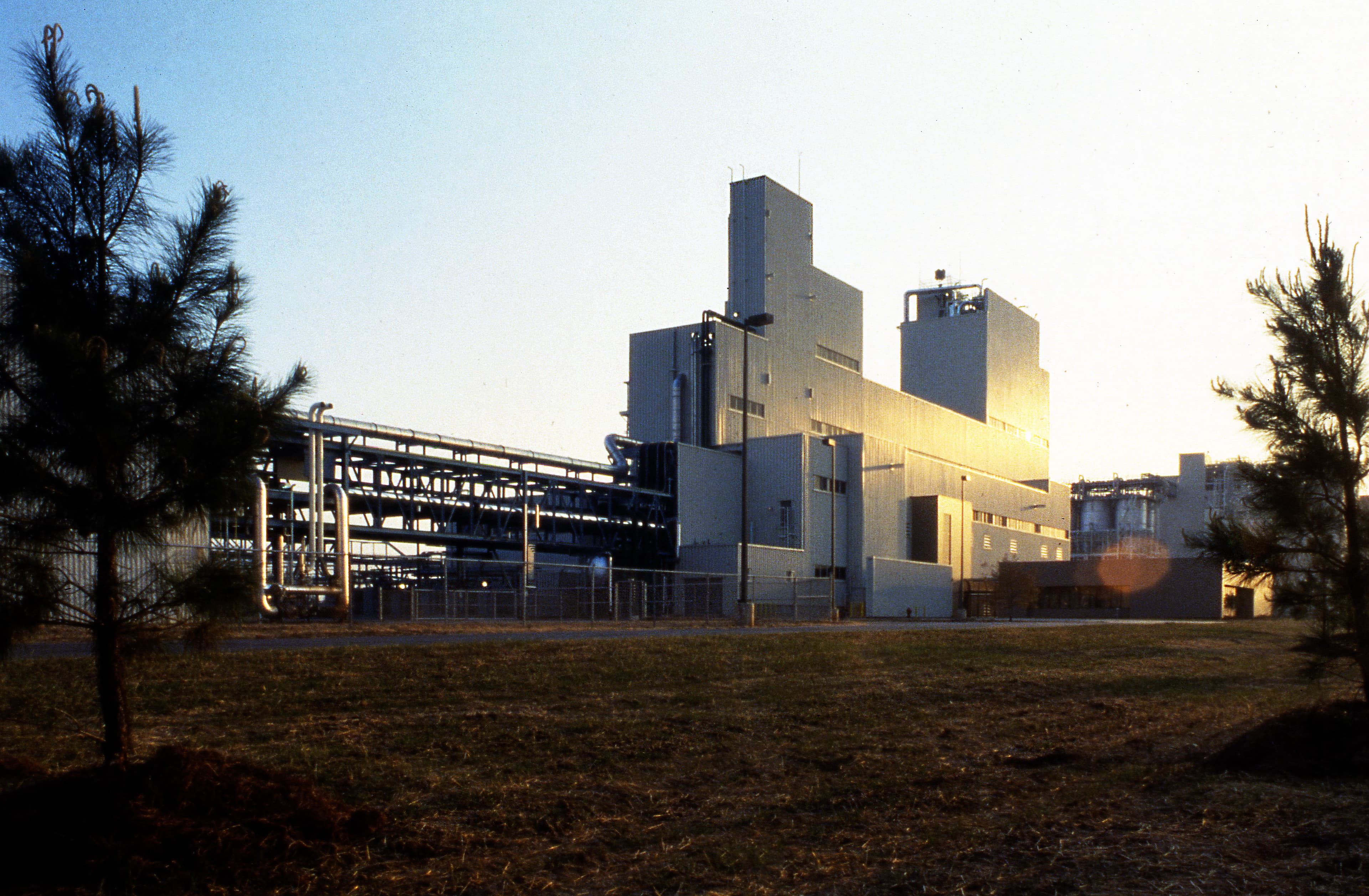
Fluor provided design and construction services for the infrastructure, compounding operations and chemical operations of this major grassroots manufacturing complex for GE Plastics. The facility produces LEXAN, a polycarbonate resin plastic. At construction, the plant was one of the most fully automated plastic manufacturing plants in the world. The complex consisted of four production stages and was designed to allow for aggressive expansion. Work in the polymerization facility included design and construction of additional raw material synthesis facilities for a primary reactant. The site-wide automation system was designed and constructed by Fluor.
1994
Operations begin at National Methanol Company's 700,000 tpy MTBE complex
1994: Operations begin at National Methanol Company's 700,000 tpy MTBE complex
Fluor provided detailed engineering / design and procurement services for the 700,000 tpy MTBE Complex located within the existing National Methanol Company property in Saudi Arabia. The complex consisted of three process units (isomerization, CATOFIN® and MTBE) with associate offsites (flare, storage, port, seawater cooling, boilers and buildings).
1996
Fluor engineers Aromax® Benzene & Cyclohexane Complex
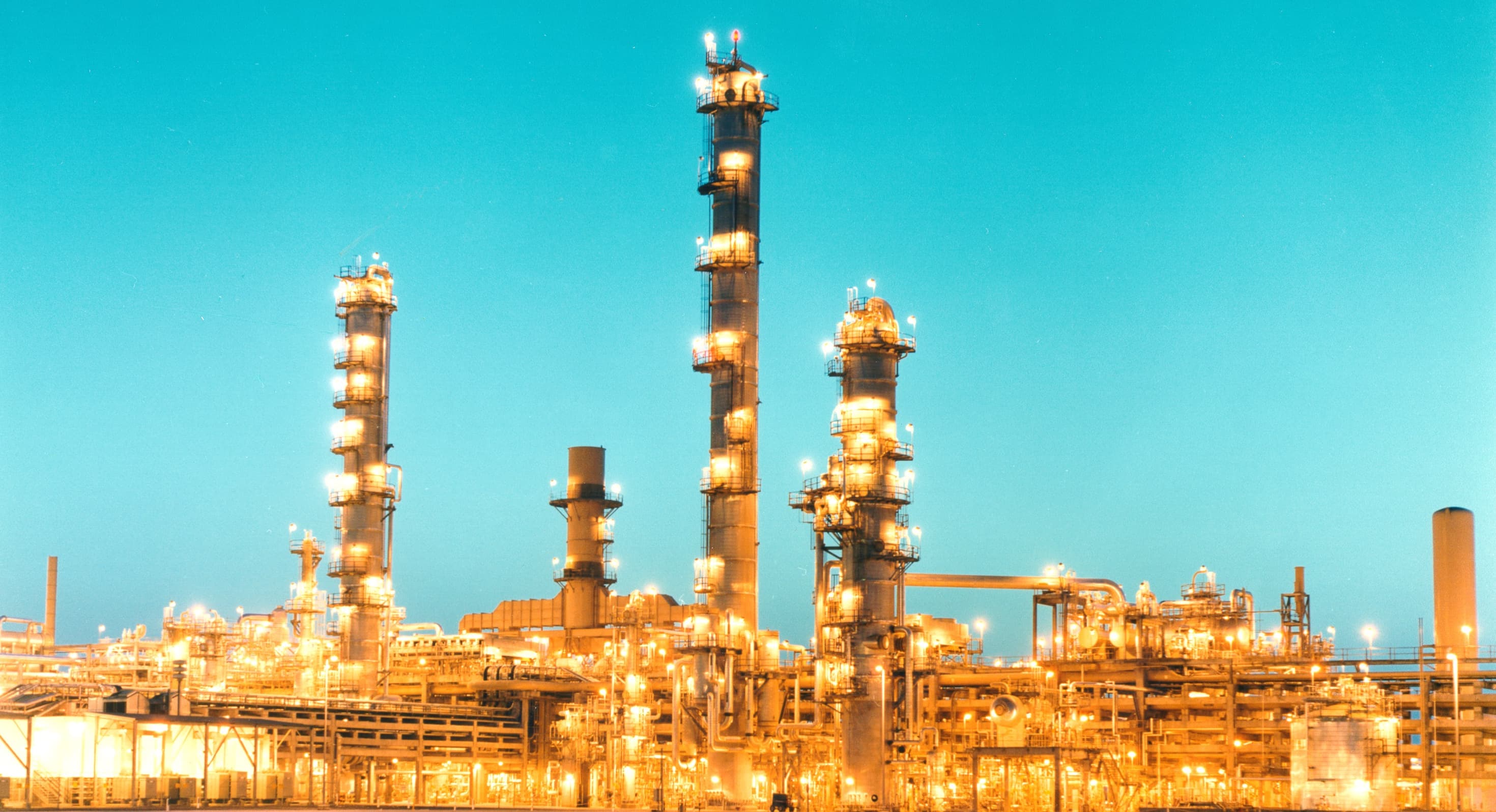
1996: Fluor engineers Aromax® Benzene & Cyclohexane Complex
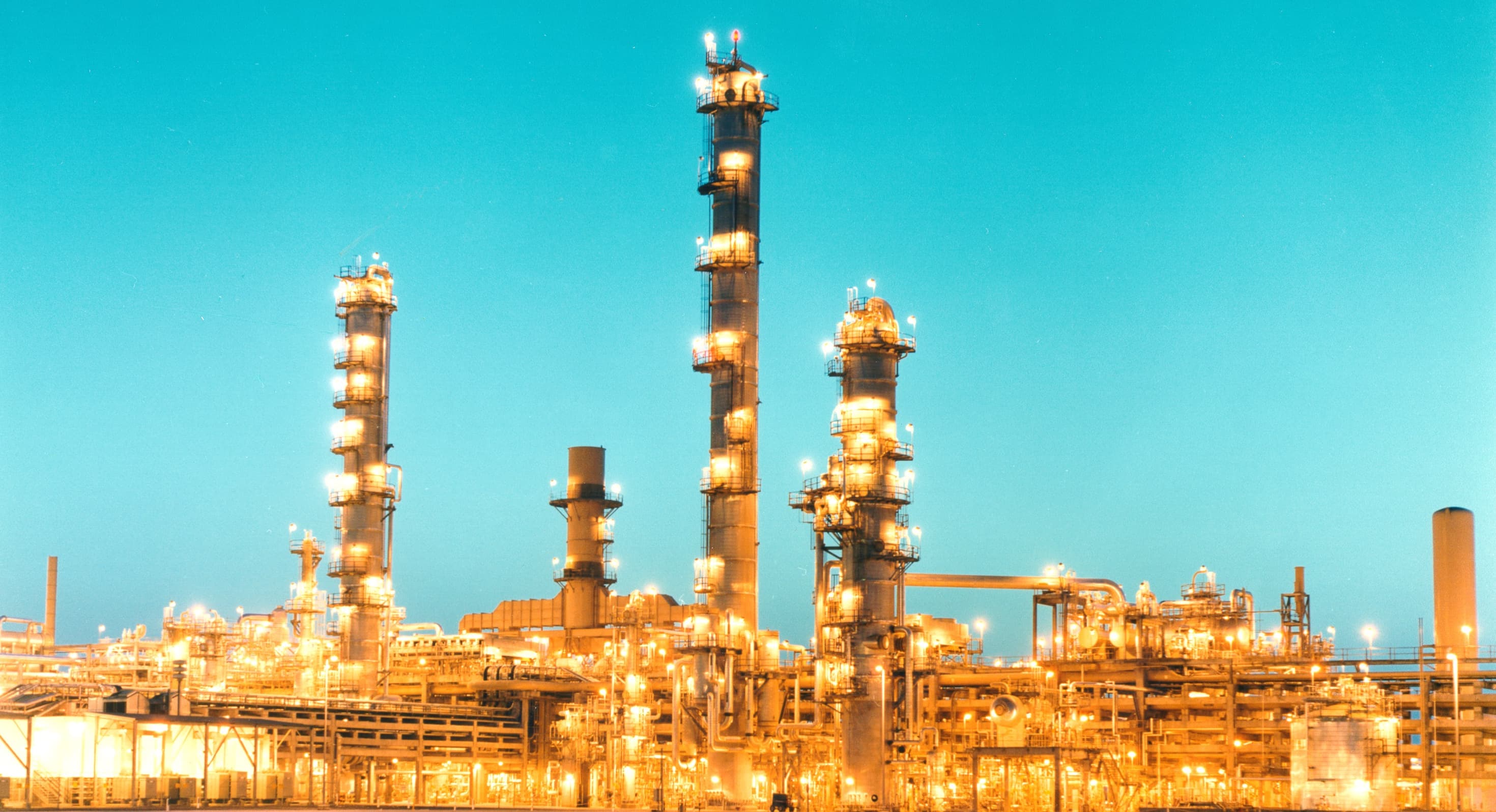
Fluor was awarded the front-end engineering and program management portion of the entire Aromax project. In addition, Fluor executed the detailed engineering, procurement and construction management for off-plot facilities.
1996
Fluor engineers Monsanto facility
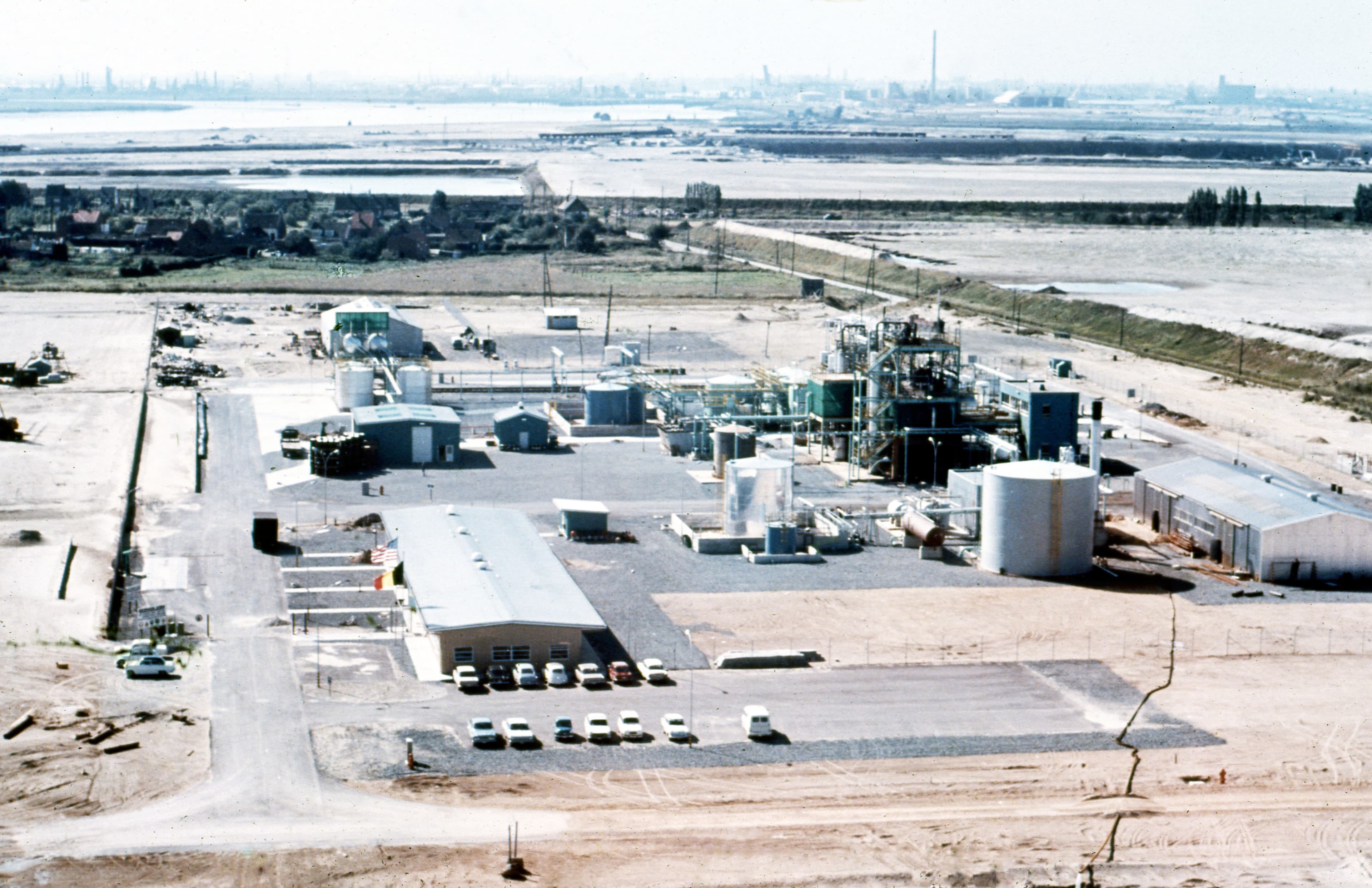
1996: Fluor engineers Monsanto facility
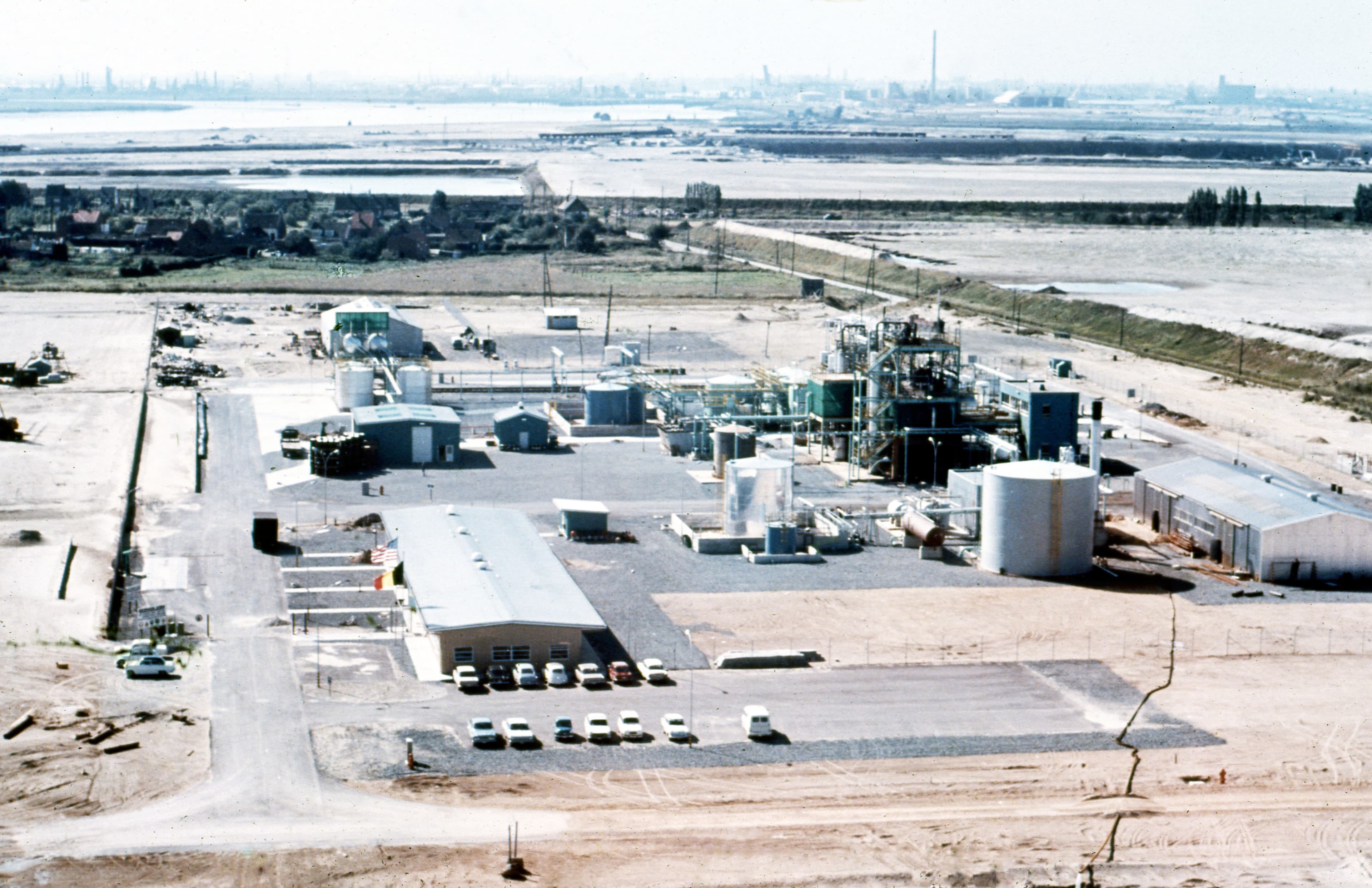
Fluor provided engineering support for Monsanto's Antwerp agricultural chemicals expansion project. Fluor's engineering scope was completed in 7 months.
1996
BP Chemicals Acrylonitrile Reactor Train completed three months ahead of schedule
&w=3840&q=75)
1996: BP Chemicals Acrylonitrile Reactor Train completed three months ahead of schedule
&w=3840&q=75)
Fluor was awarded the engineering, procurement and construction for the Green Lake project, which added an acrylonitrile reactor train and associated plant modifications at the BP Chemicals Green Lake plant. The project was fast-tracked to meet an aggressive 18-month total schedule. Upon completion of the expansion, Green Lake was the world's largest acrylonitrile production plant.
1997
Fluor awarded front-end engineering for José Petrochemical Complex
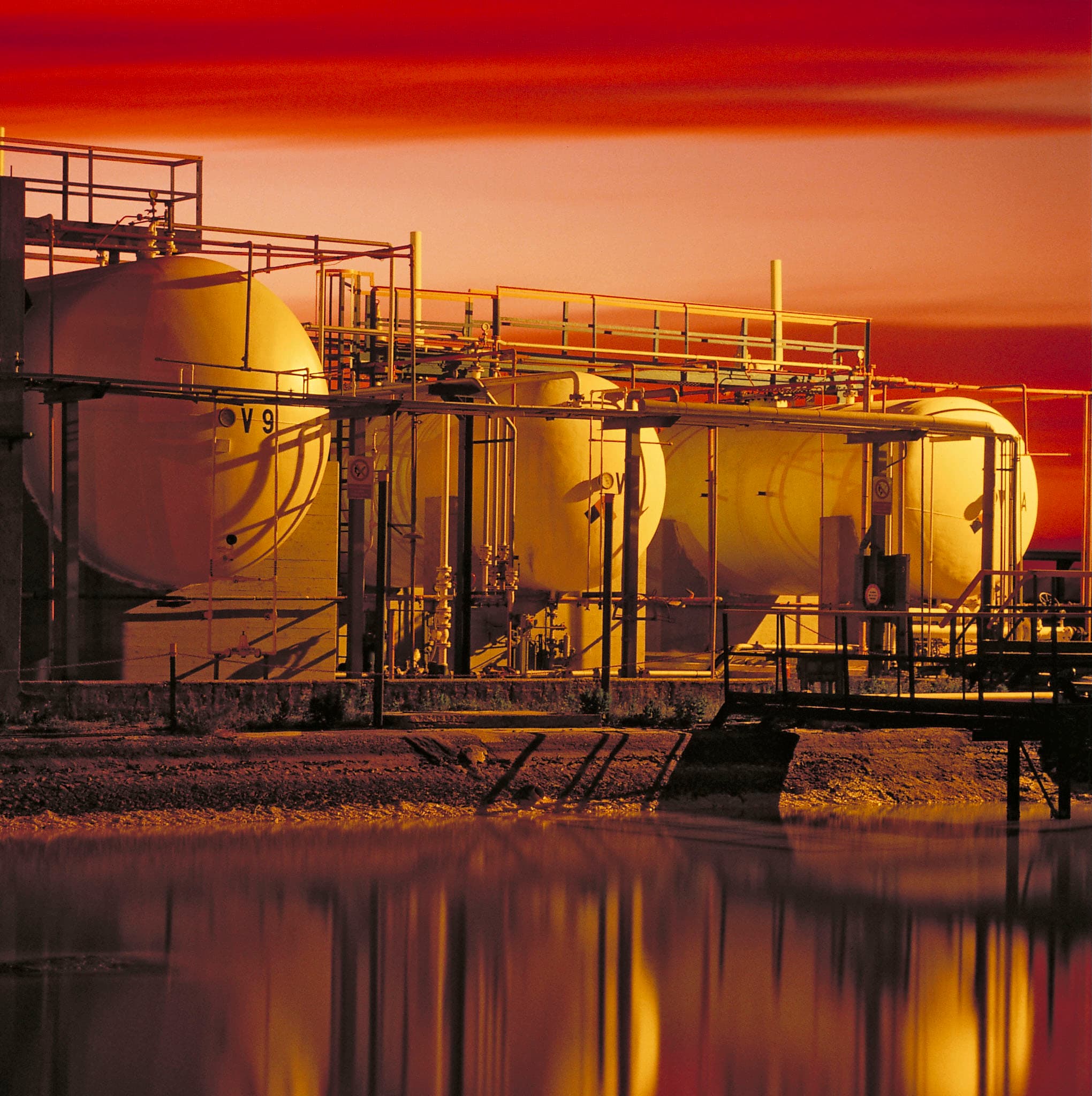
1997: Fluor awarded front-end engineering for José Petrochemical Complex
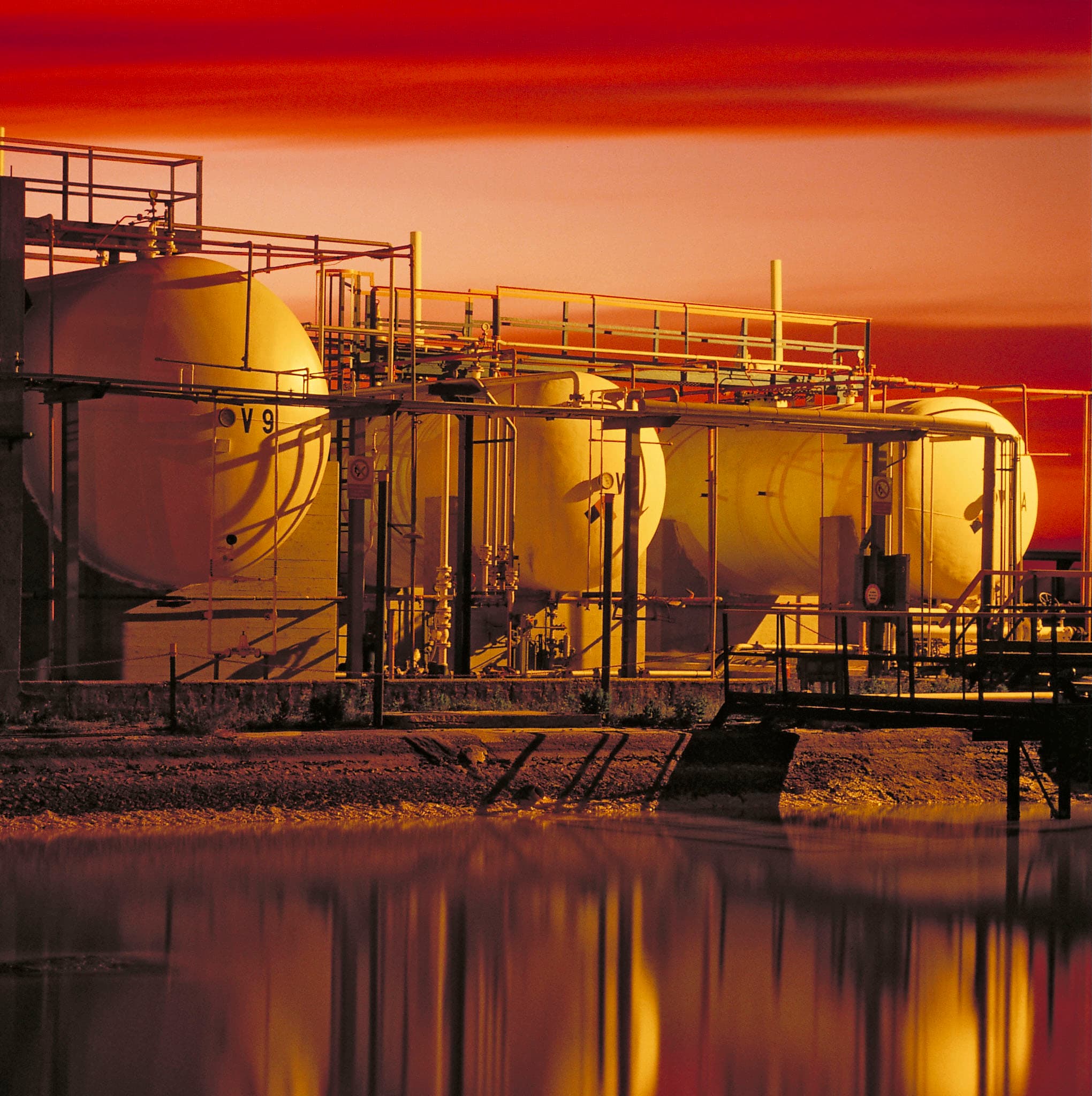
Fluor, Snamprogetti and Tecnofluor contracted with Mobil / Pequiven to complete front-end engineering and capital cost estimating services for the José Petrochemical Complex.
Major petrochemical process units included ethylene 750,000 metric tons per annum (MTA), linear low-density polyethylene (LLDPE) 300,000 MTA, low-density polyethylene (LDPE) 200,000 MTA and ethylene glycol 400,000 MTA.
1997
Fluor completes petrochemical grassroots complex located in Shuaiba, Kuwait
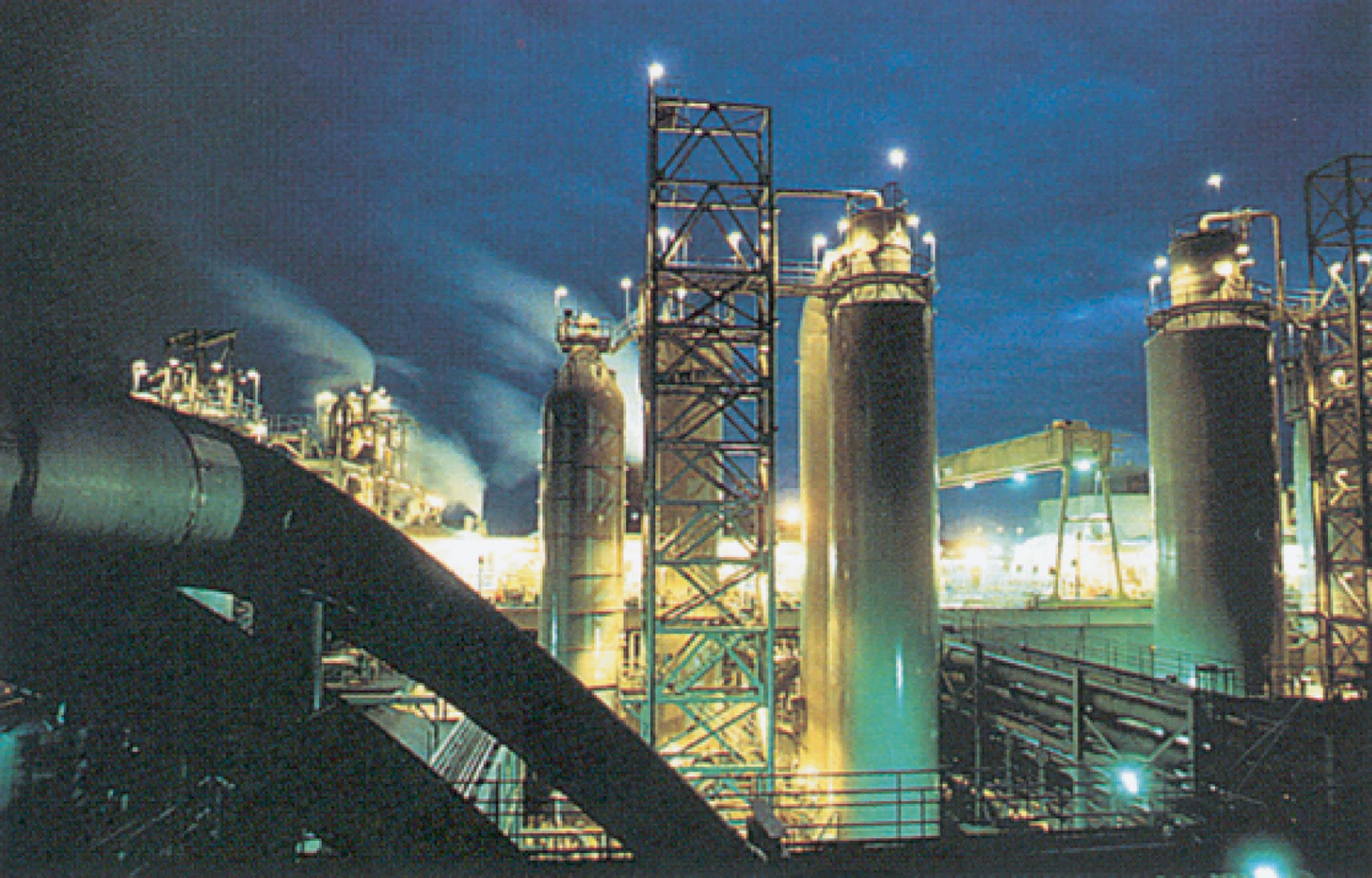
1997: Fluor completes petrochemical grassroots complex located in Shuaiba, Kuwait
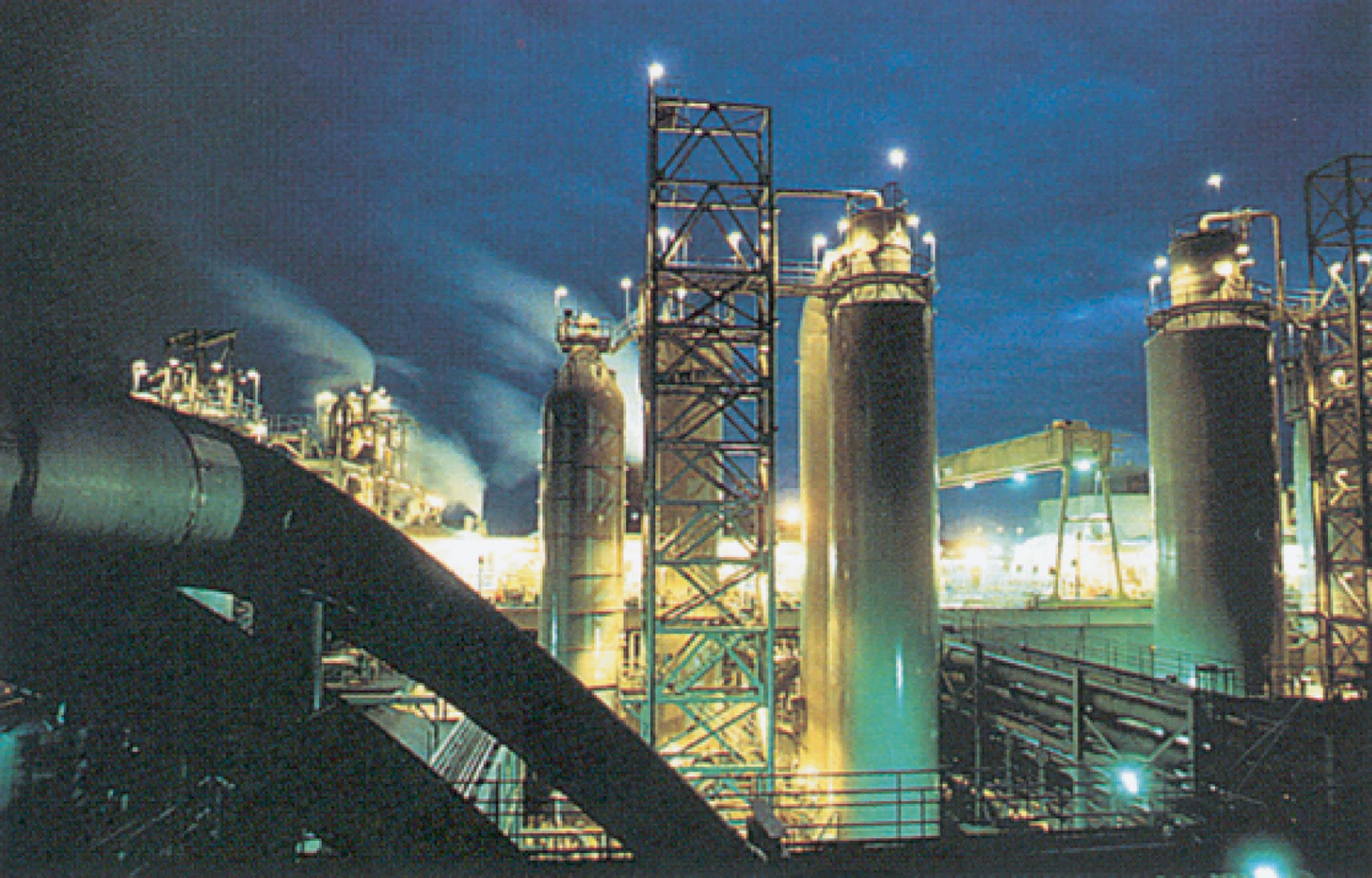
EQUATE, formerly Kuwait Petrochemical Joint Venture (KPJV), selected Fluor to perform program management. Fluor supervised the overall execution of a grassroots petrochemical complex and prepared the coordination procedures, specifications and plans.
1997
Design begins for derivatives facility consisting of butyl acetate, butyl glycol ethers, ethanol amines and alkoxylation units
&w=3840&q=75)
1997: Design begins for derivatives facility consisting of butyl acetate, butyl glycol ethers, ethanol amines and alkoxylation units
&w=3840&q=75)
Fluor was contracted to provide the conceptual and front-end process packages for the four derivative units of the Petronas / Union Carbide Integrated Petrochemical Complex. The design effort established detailed facility scope packages.
1997
Antwerp Aromatics project produces chemical grade benzene and mixed xylenes from reformate
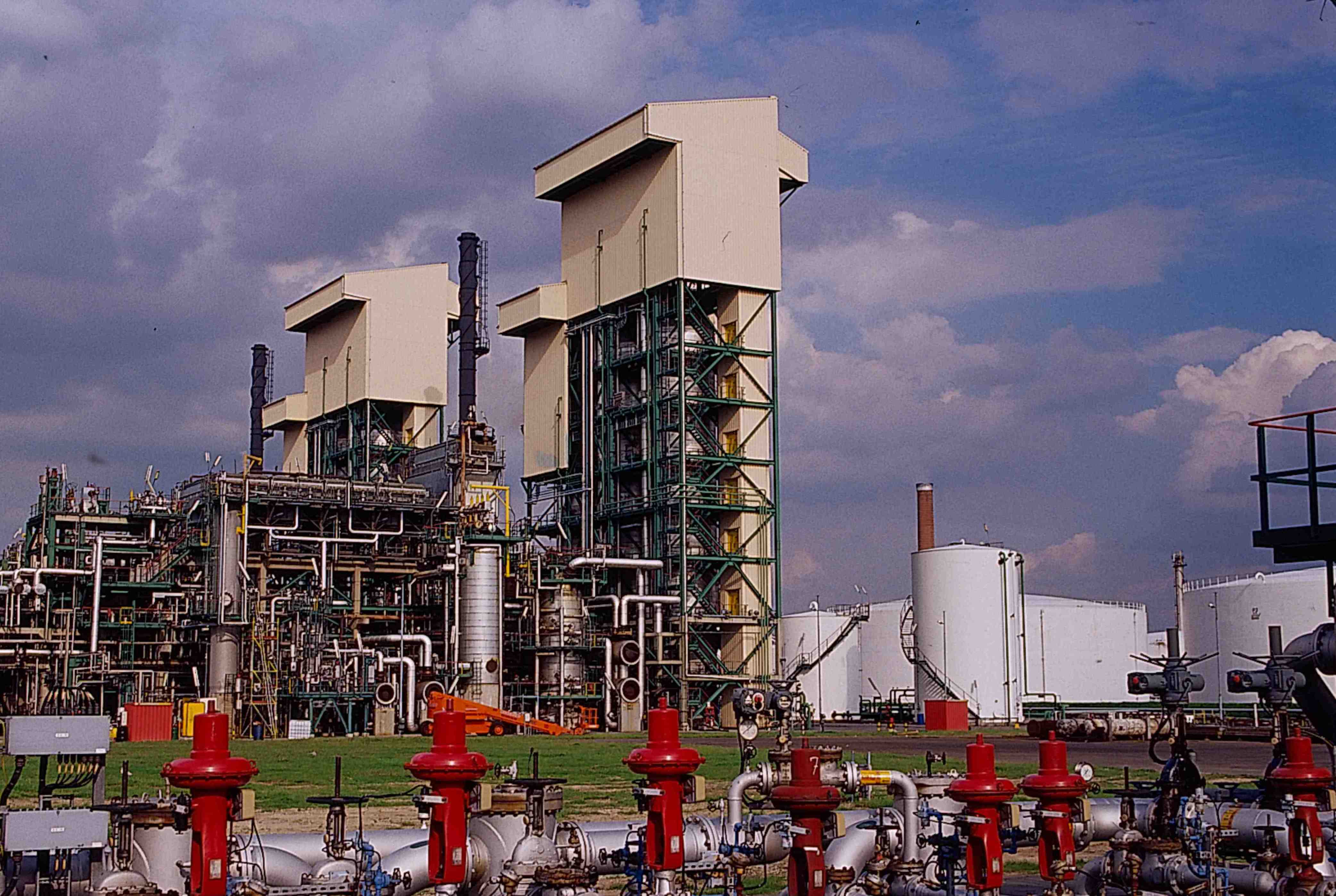
1997: Antwerp Aromatics project produces chemical grade benzene and mixed xylenes from reformate
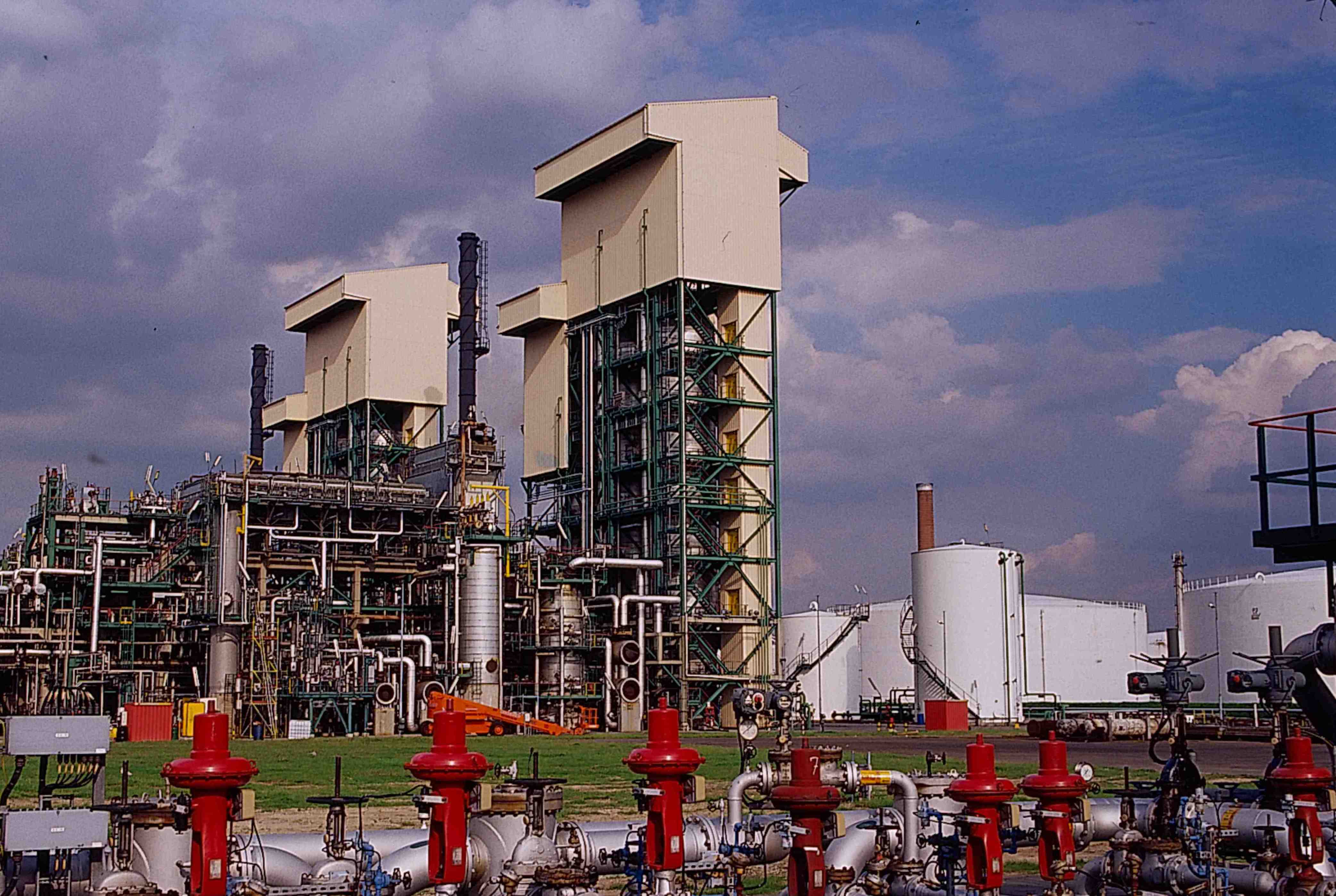
The Fina Raffinaderij Antwerp Aromatics project included the processing facilities required for producing chemical grade benzene and mixed xylenes from reformate. The main on-site facilities included a new 240 tonne/hr reformate fractionation section (RFS), the revamping of an existing unit for the benzene hydrotreater (C6HT), and a new 60 tonne/hr extractive distillation unit (EDU). Fluor provided detailed engineering and design, procurement, construction management and precommissioning assistance.
1997
Fluor completed THF and butane pipelines
1997: Fluor completed THF and butane pipelines
Fluor was contracted by E.I. Dupont de Nemours & Co. to engineer, procure and construct tetrahydrofuran (THF) and butane pipelines in Spain. The project was designed and built to supply THF, a row material of Lycra®.
1998
Titanium Pigment Manufacturing Facility successfully adapts German technology to meet U.S. manufacturing requirements
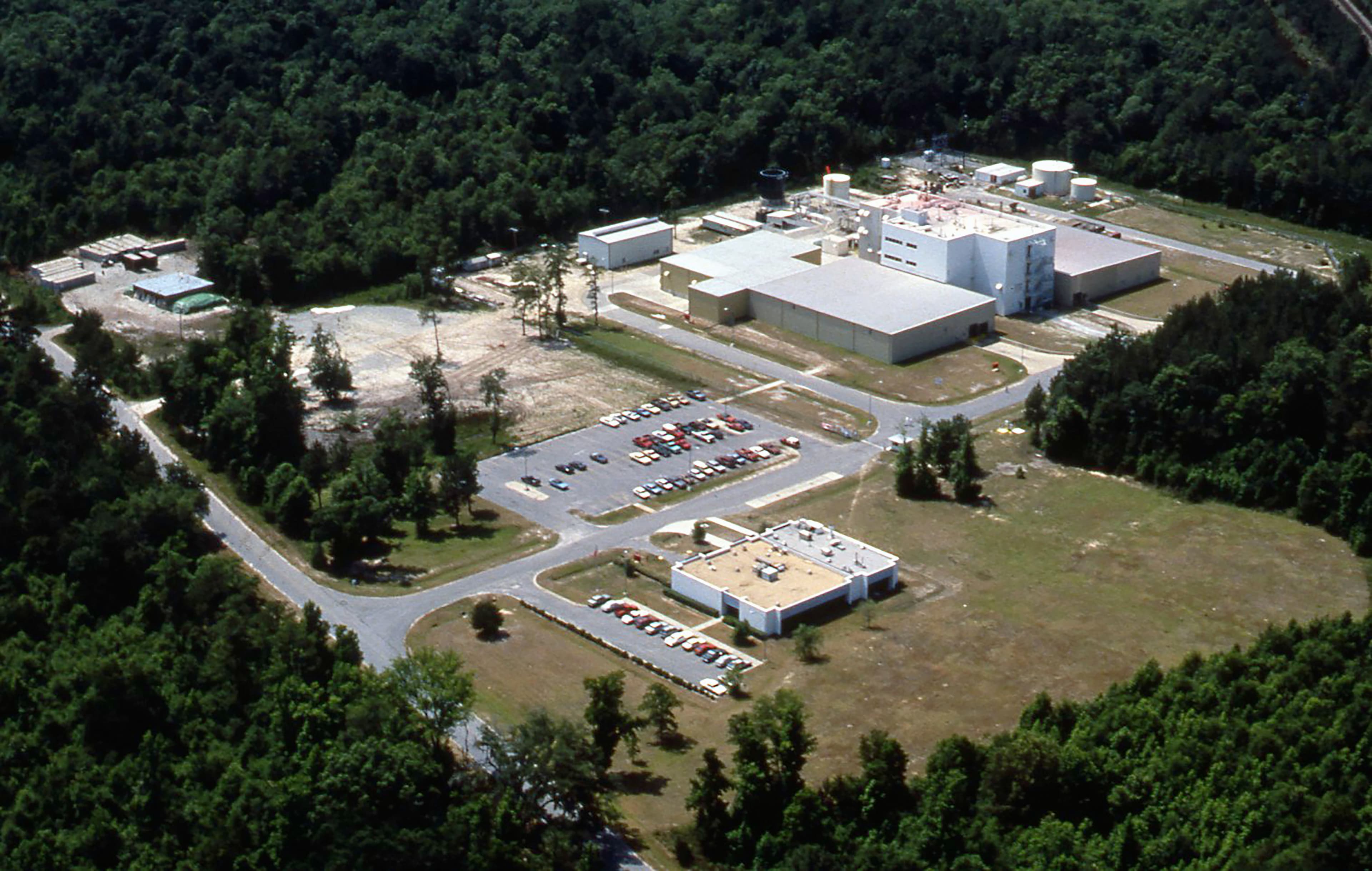
1998: Titanium Pigment Manufacturing Facility successfully adapts German technology to meet U.S. manufacturing requirements
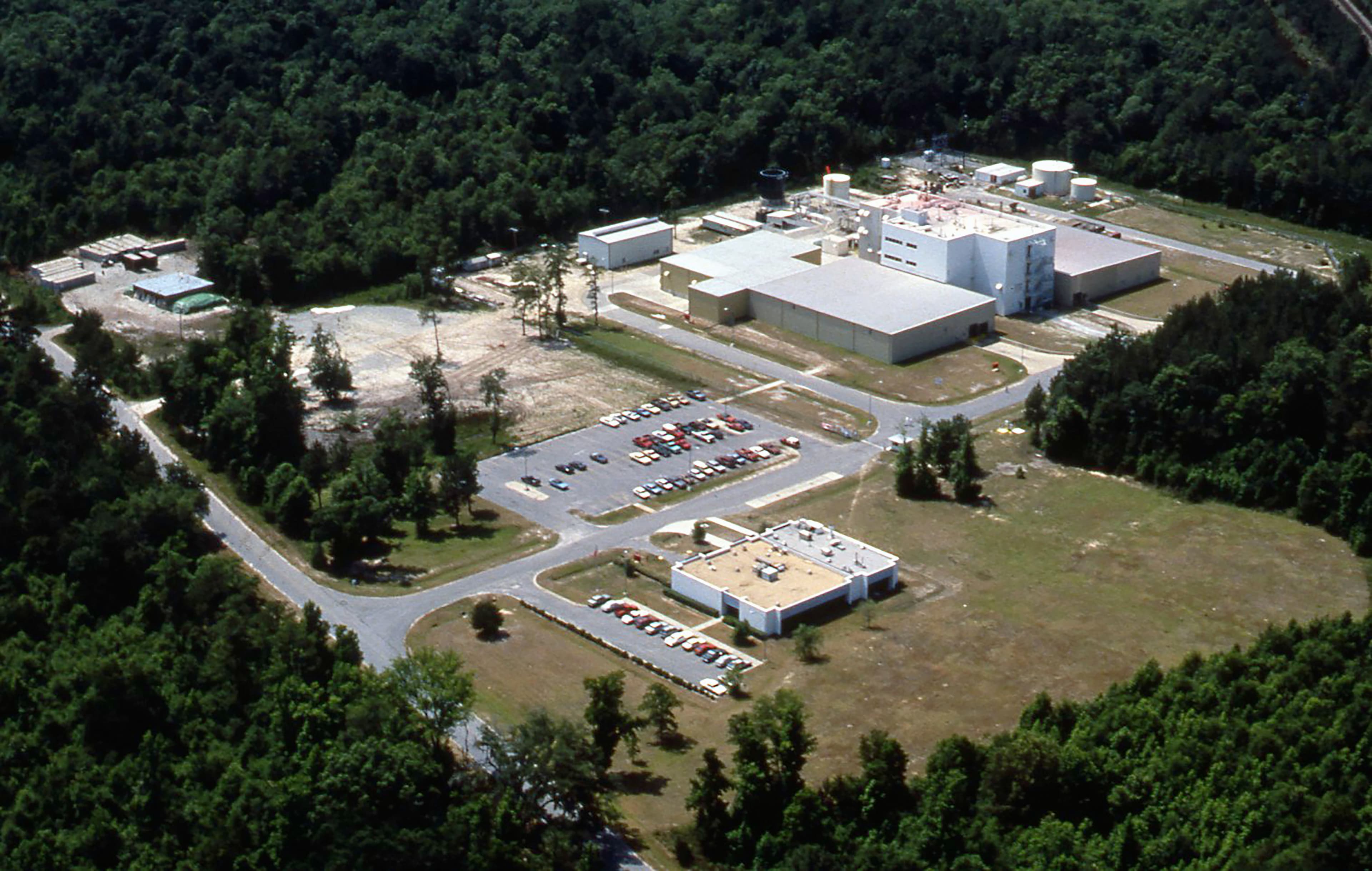
Fluor provided complete design, engineering, procurement and construction services for the grassroots facility which produces high-quality, titanium-coated mica pigments for use in cosmetics and plastics. The facility was German-based E. Merck's first major grassroots chemical manufacturing plant constructed in the United States. The project involved adapting German process technology to a full-scale production facility using U.S. manufacturing requirements and technology. The process involved pulverizing raw mica, grading by size and weight, solution coating, filtering, drying and blending. The pigments are produced by highly corrosive processes and required technologically sophisticated environmental emissions control and wastewater treatment facilities.
1999
Maleic Anhydride plant combined capacity reaches 56,000 tpa
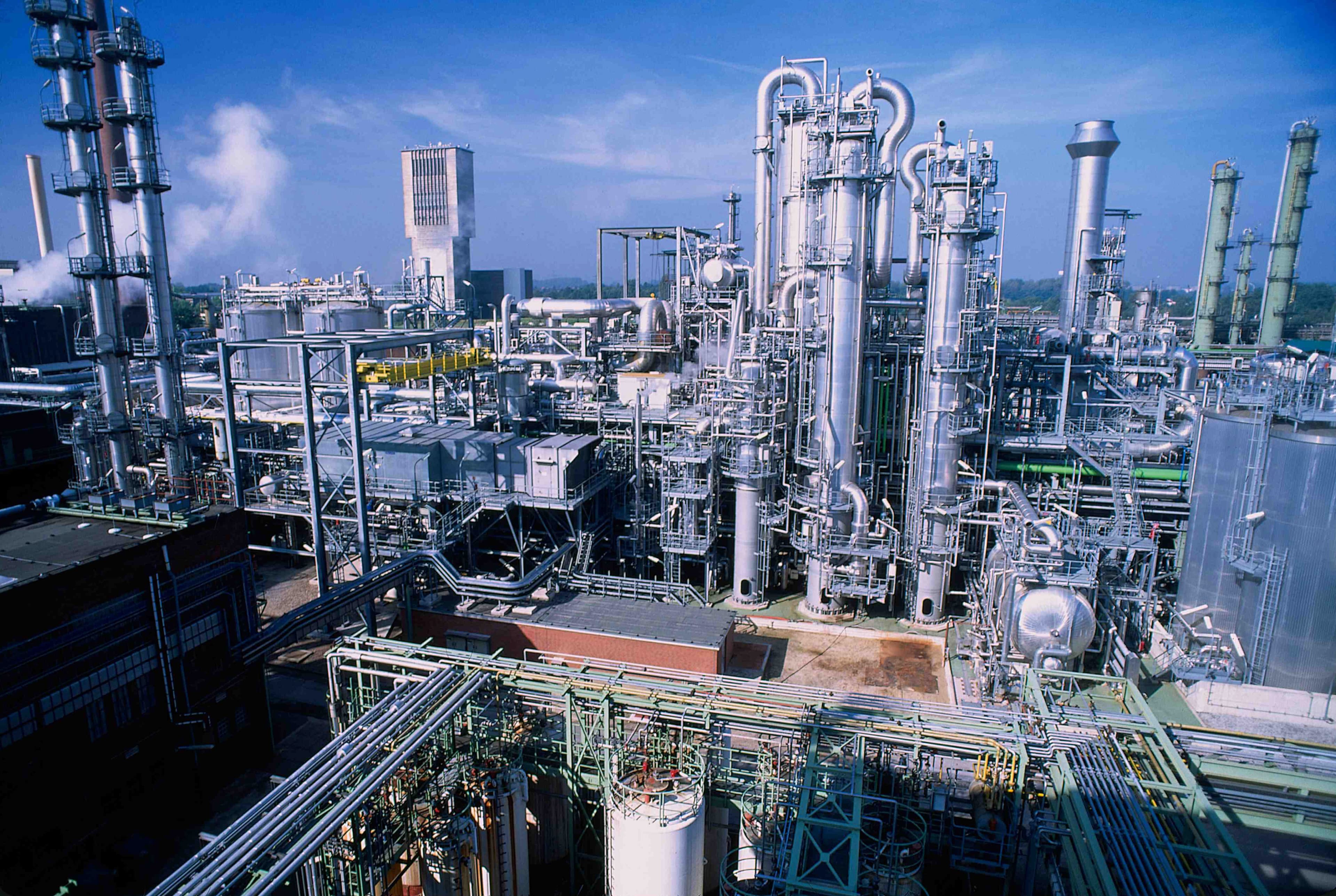
1999: Maleic Anhydride plant combined capacity reaches 56,000 tpa
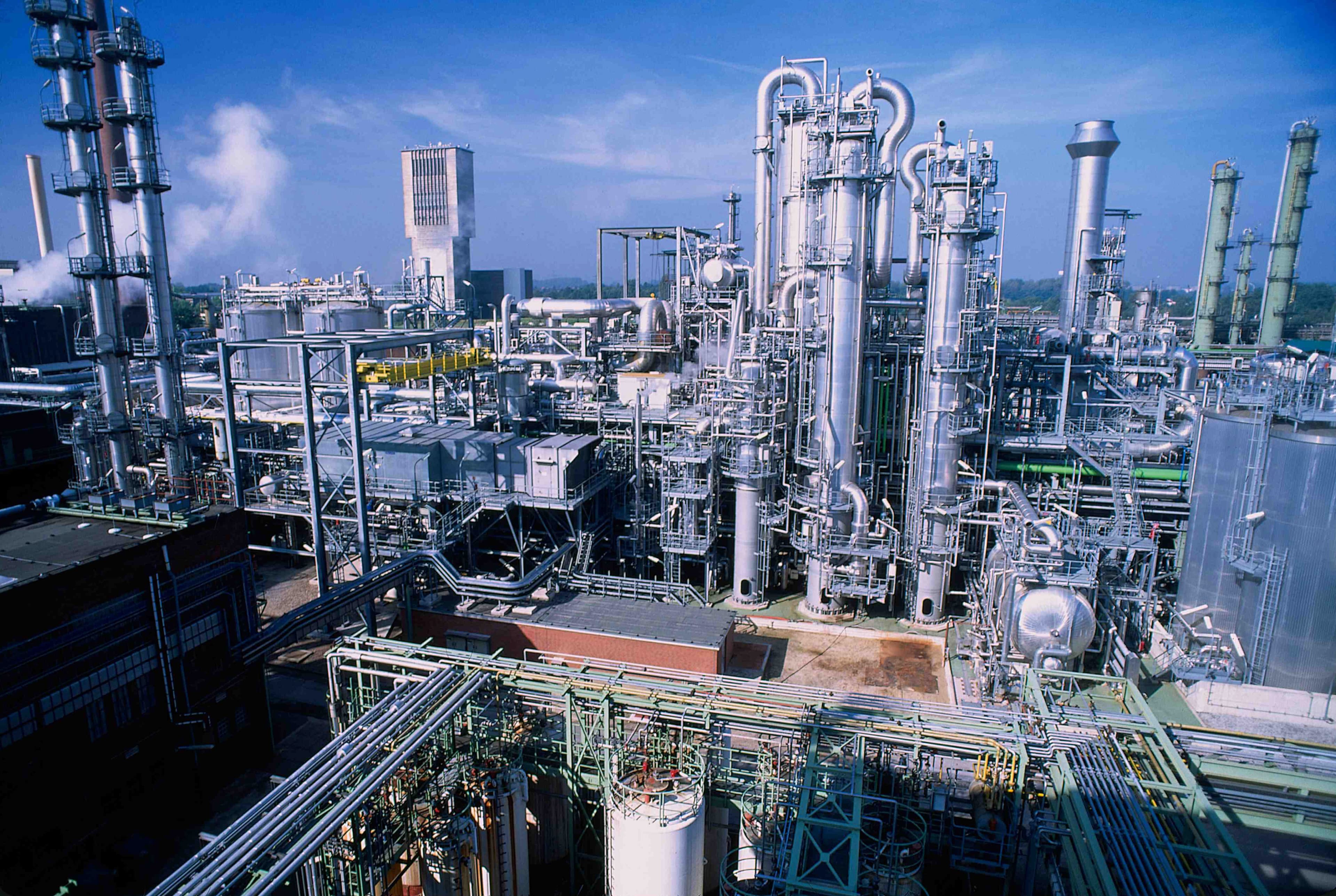
Fluor was contracted by Condea-Huntsman to provide detailed engineering, procurement and construction management services for the addition of a new and the upgrade of an existing Maleic Anhydride plant. Maleic Anhydride (MA) is manufactured with a Huntsman owned process by partial oxidation of butane and subsequent separation with a selective solvent. The extracted MA is then distilled and stored. Once completed, the total combined capacity reached 56,000 tpa. The new MA plant has a capacity of 40,000 tpa whilst the existing plant with an original capacity of 12,000 tpa was debottlenecked and integrated.
1999
Amoco No. 4 Polypropylene Facility project completed
&w=3840&q=75)
1999: Amoco No. 4 Polypropylene Facility project completed
&w=3840&q=75)
A Fluor and Technip joint venture completed the Amoco No. 4 Polypropylene Facility project in 1999. The joint venture team performed the engineering, procurement and precommissioning scope, with construction solely self-performed by Fluor.
2000s
Fluor is selected to develop mega chemicals and petrochemicals projects in the Middle East.
2000
Awarded BASF-YPC Integrated Petrochemical Site Project in Nanjing
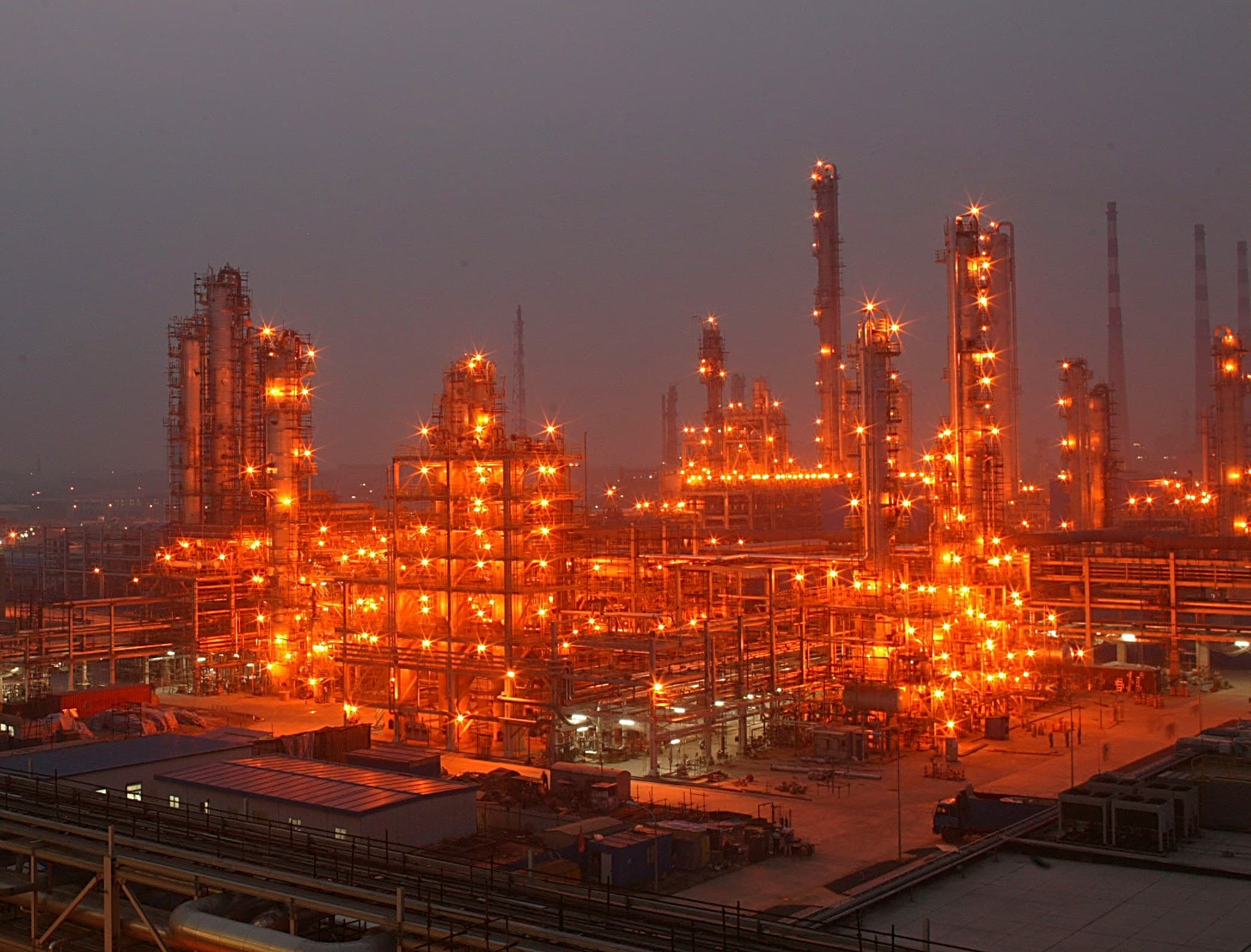
2000: Awarded BASF-YPC Integrated Petrochemical Site Project in Nanjing
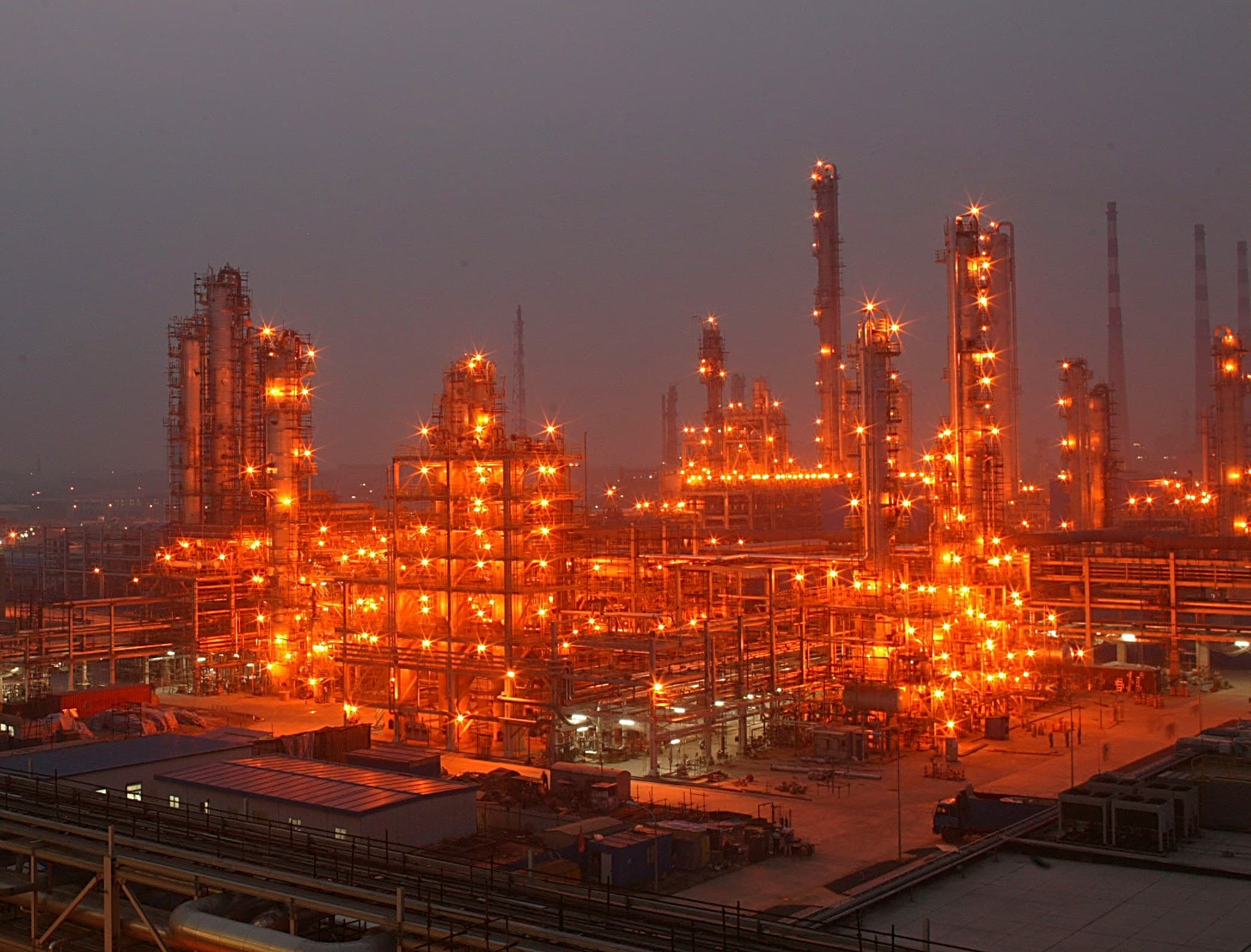
Fluor provided program management services to BASF-YPC as part of an integrated management team of personnel from Fluor, BASF and Yangzi Petroleum Corp (a subsidiary of Sinopec). This major petrochemicals complex in Nanjing, China, was the largest single project to be undertaken by BASF and was our first large project management contract in China. We also performed front-end engineering and design and engineering, procurement and construction management services for the offsites, utilities and infrastructure. The whole program was completed in 2005.
2000
Kodak China Program completed, the first $1B investment by a U.S. company in China
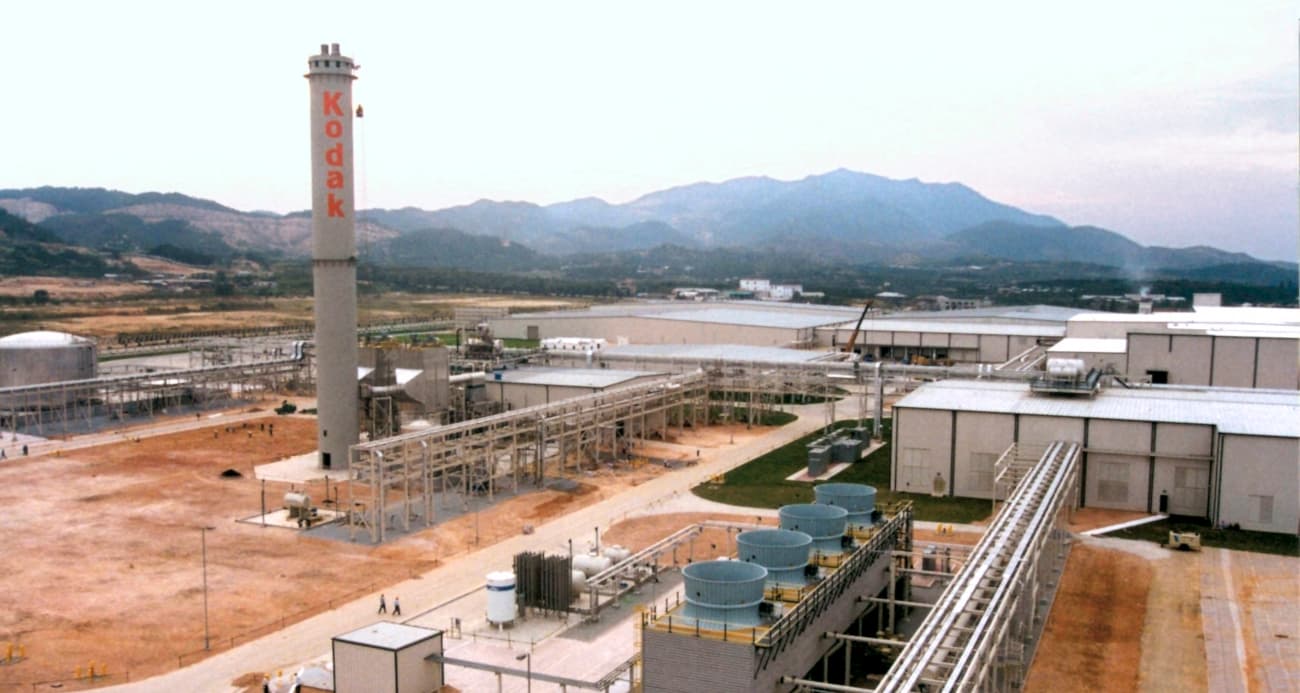
2000: Kodak China Program completed, the first $1B investment by a U.S. company in China
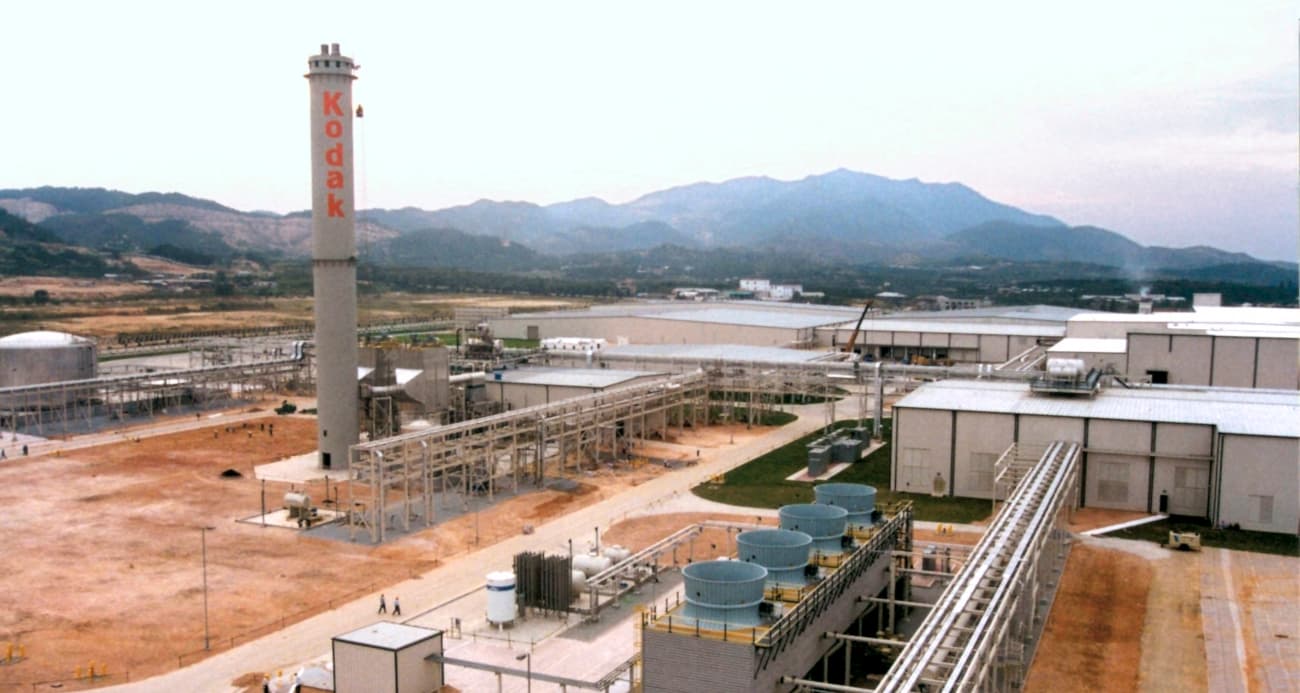
Fluor provided overall program management, engineering, procurement, construction management and partial commissioning services for the program, which combined emulsion manufacturing, film and paper sensitizing and finishing, packaging and shipping, utilities and associated infrastructure. The project was completed ahead of a critical schedule and within a tight budget, to world-class quality standards and with zero lost-time accidents.
The project received Fluor's Hugh Coble Project Excellence Award in 2000. The award is based on outstanding performance in several areas, including safety, value creation and client and community relations.
2001
Yanpet Expansion increases production of ethylene and polypropylene
&w=3840&q=75)
2001: Yanpet Expansion increases production of ethylene and polypropylene
&w=3840&q=75)
Fluor was the program management contractor for the total project responsible for performing the front-end engineering design (FEED) and the procurement of critical equipment and materials. Fluor provided engineering, procurement and construction (EPC) services for the utilities and offsites, as well as polymer engineering and procurement services. The expansion facilities provide 800,000 tpy ethylene capacity and convert ethylene into 535,000 tpy polyethylene and 410,000 tpy ethylene glycol. In addition, it provides 260,000 tpy of polypropylene.
2001
Conoco's eight million pounds per year petroleum-based carbon fiber manufacturing plant operational
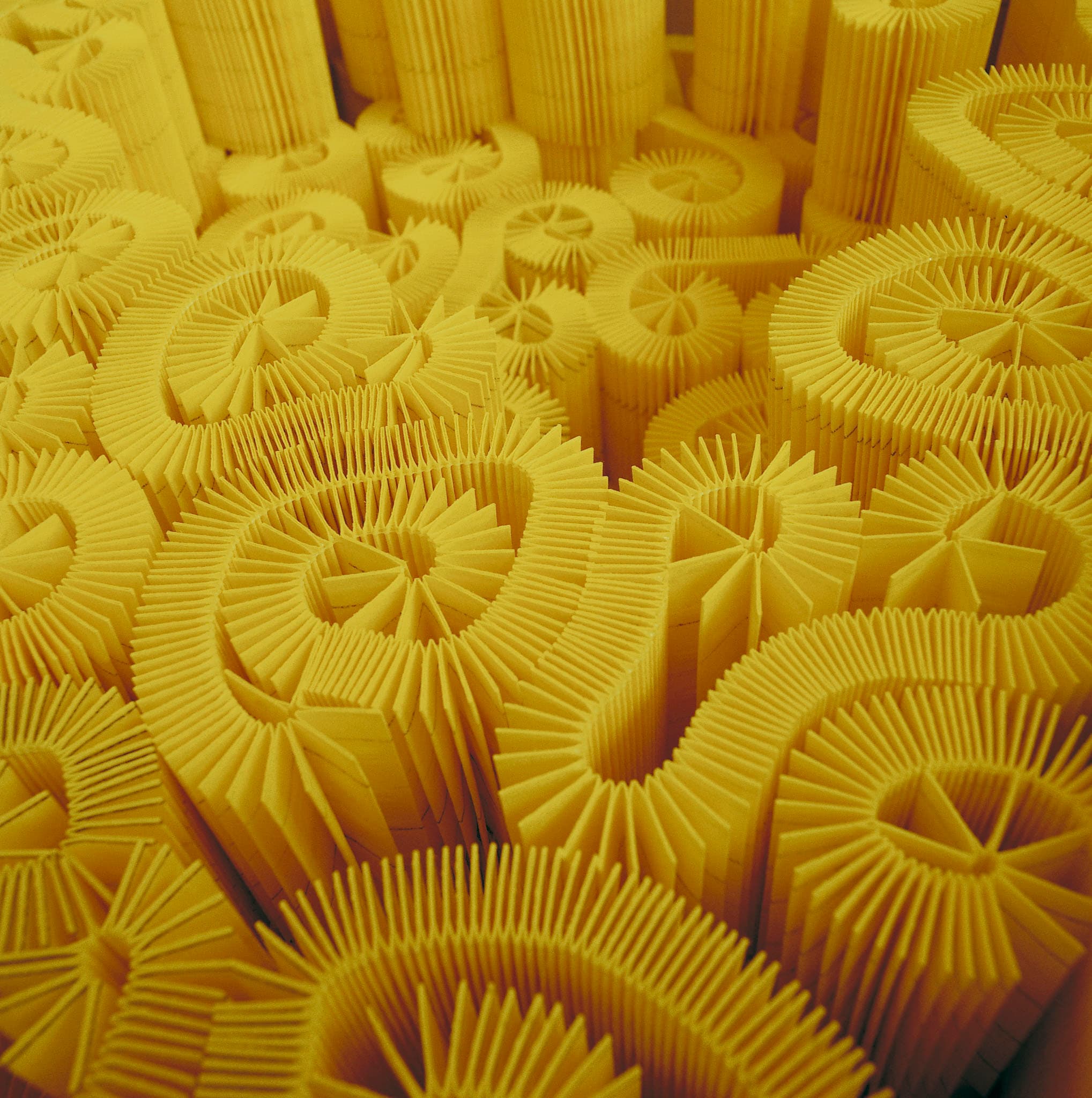
2001: Conoco's eight million pounds per year petroleum-based carbon fiber manufacturing plant operational
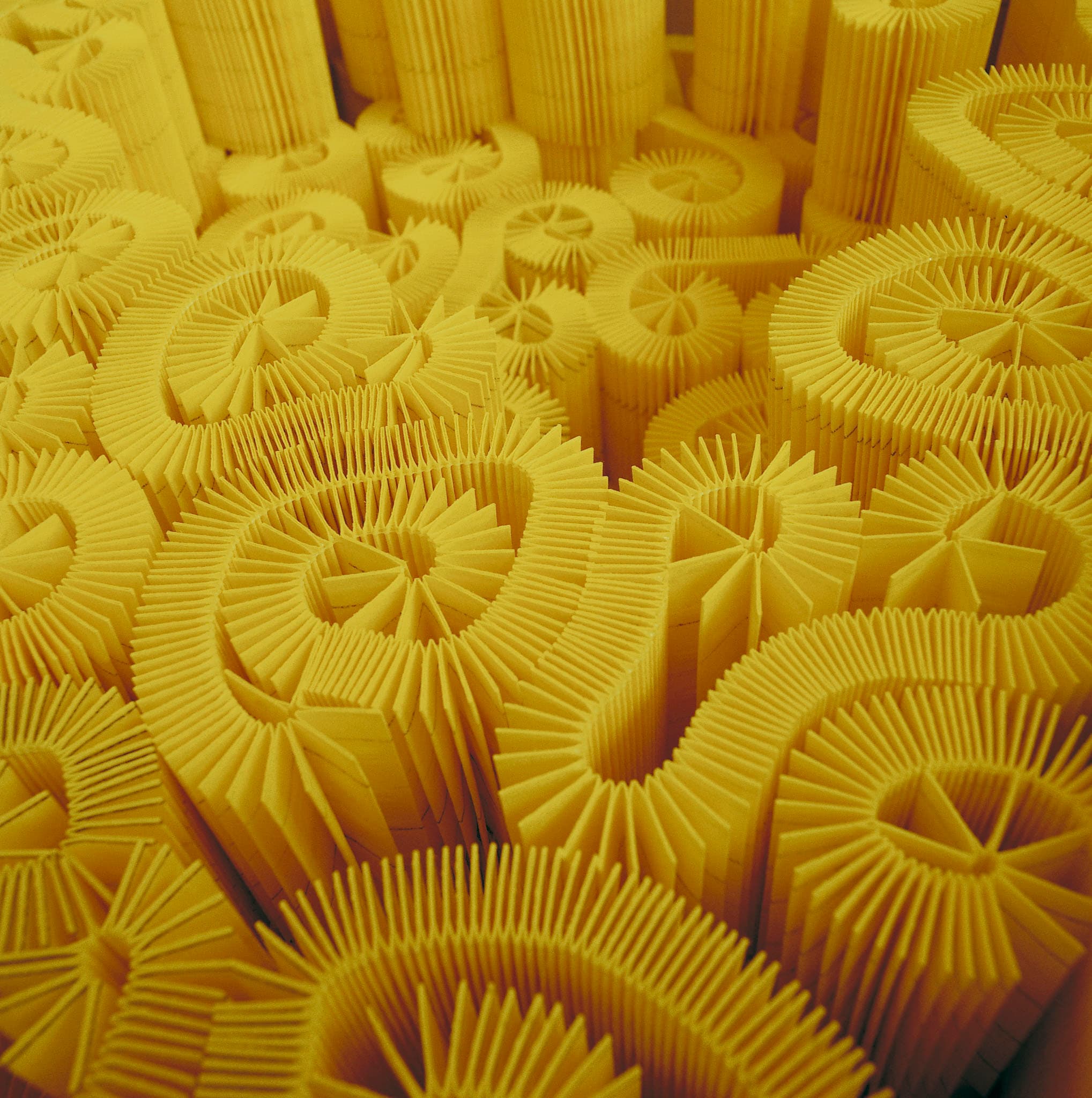
Conoco selected Fluor to develop its revolutionary petroleum-based carbon fiber. The product has unique applications in the electronics, composite materials, plastics, automotive, construction, transportation and other niche markets. Fluor provided support on an as-needed basis during front-end loading (FEL)-1 and 2 of the design. In 1997, Fluor was awarded FEL-3. Upon the timely completion of front-end design, Fluor continued with the project and completed detail engineering and procurement. Process challenges included the processing of chemicals at high pressure and temperature, and design as well as development of unique material handling systems. Operation of an 8-million-pounds-per-year manufacturing plant began in the second half of 2001 in Ponca City, Oklahoma.
2002
DuPont UK revamps ICI nylon intermediates plants located in Teesside
&w=3840&q=75)
2002: DuPont UK revamps ICI nylon intermediates plants located in Teesside
&w=3840&q=75)
Beginning in 1996, Fluor helped DuPont ICI UK upgrade and modernize several of its nylon intermediates plants located at the Wilton Complex in Teesside, England. This program won DuPont's Excellence award.
2004
Integrated project management team with TASNEE formed
&w=3840&q=75)
2004: Integrated project management team with TASNEE formed
&w=3840&q=75)
Fluor, together with TASNEE, formed an integrated project management team that oversaw the entire Ethylene Cracker / PE complex, resulting in contract awards to a consortium of Linde / Samsung in July of 2005 for the cracker project and Tecnimont in January 2006 for the PE projects. These projects were performed onsite at TASNEE's combined Ethylene and Polyethylene project.
2009
BASF-YPC awards second phase of Integrated Petrochemical Site Expansion Project in Nanjing
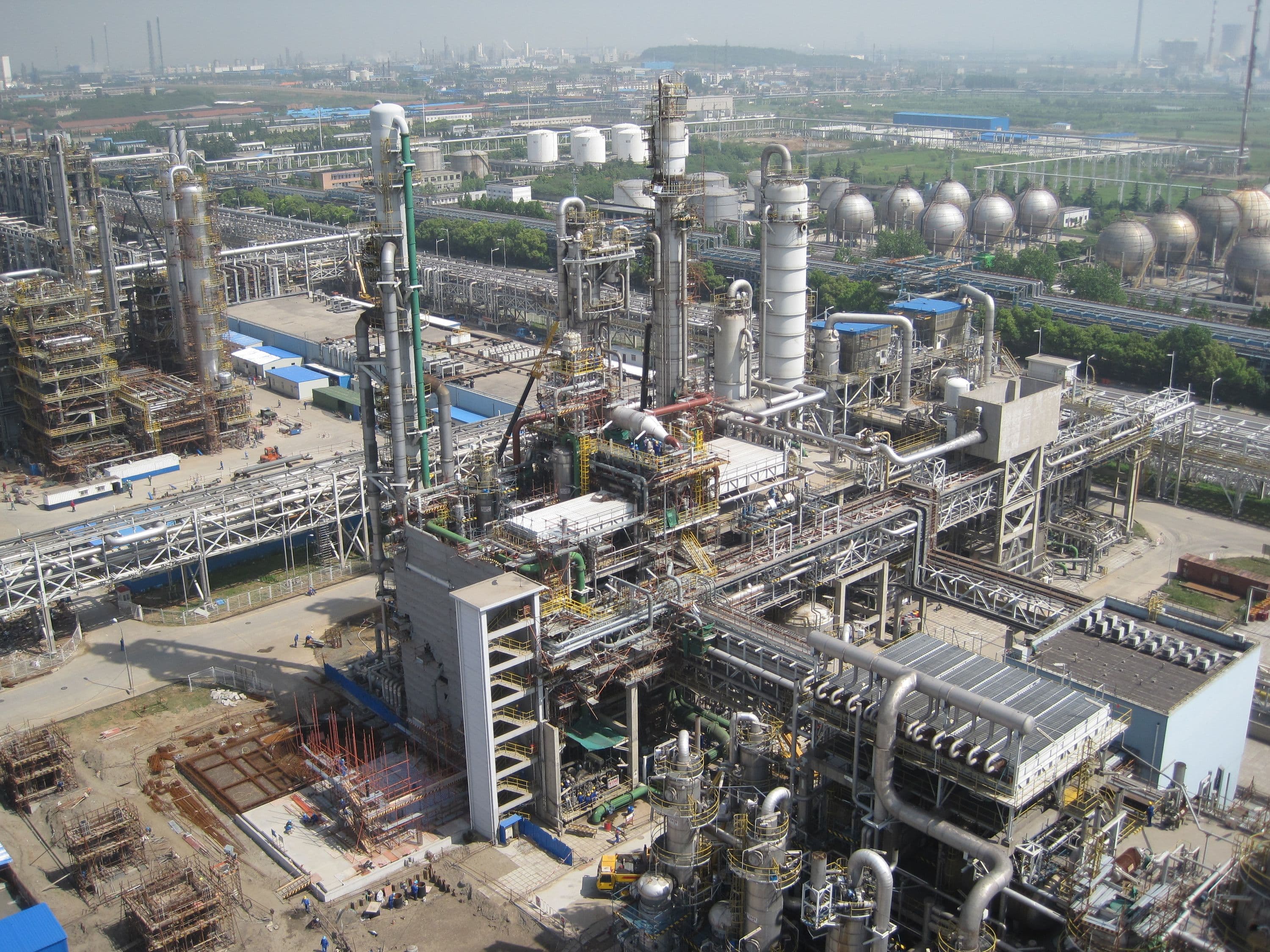
2009: BASF-YPC awards second phase of Integrated Petrochemical Site Expansion Project in Nanjing
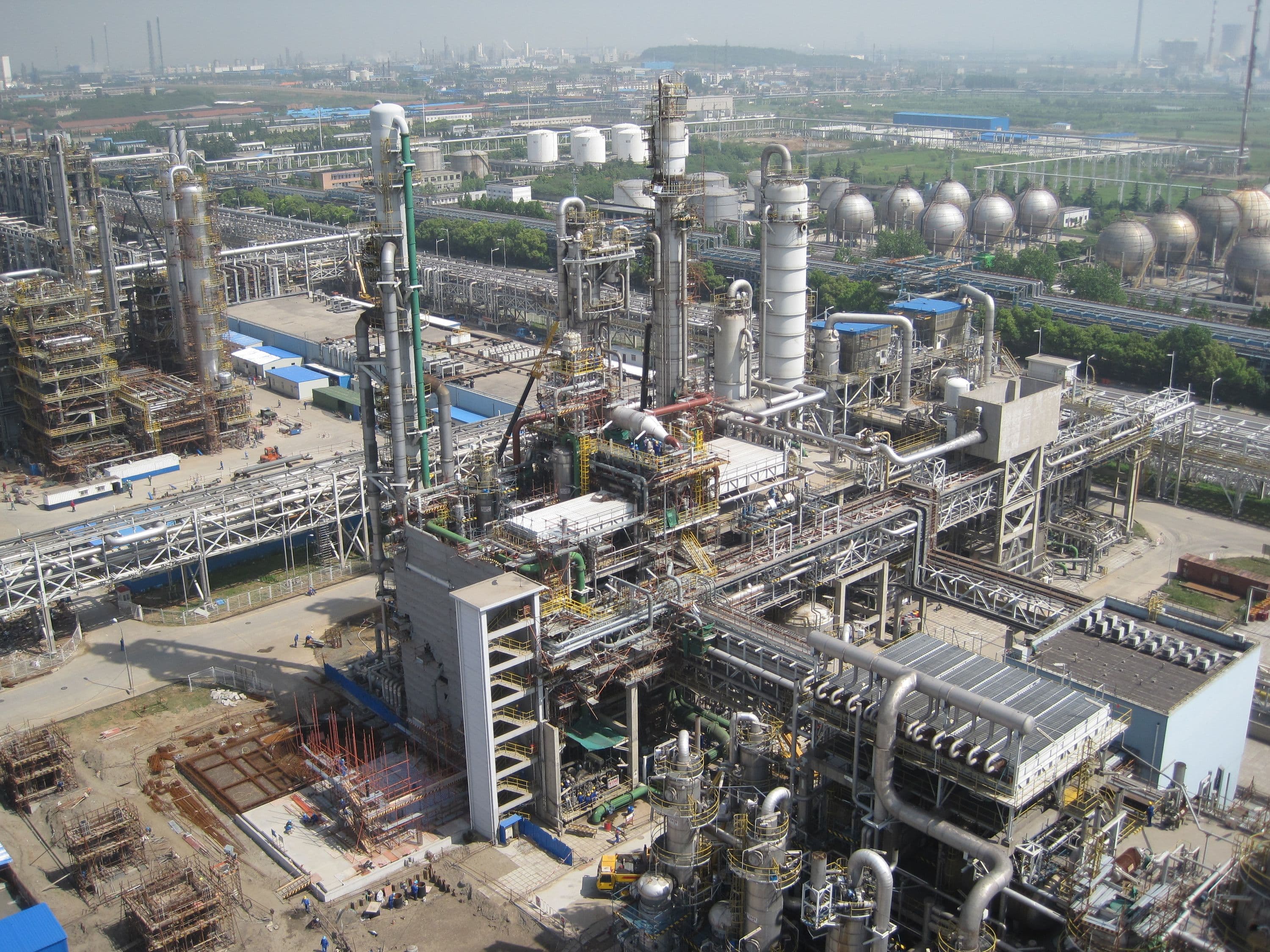
Integrated Petrochemical Site Expansion Phase II (IPS II) was the second phase investment project after the expansion of the facility was completed in 2005. This new phase increased production capacity for ethylene products, added fine-chemical plants and expanded site utilities and infrastructure. Joining Toyo and Daelim in an international consortium, we were responsible for the engineering, procurement and construction management (EPCm) of our own portion of the project. We also performed EPCm services for the offsites, utilities, infrastructure, non-ionic surfactants and ethylene oxide/ethylene glycol unit.
2009
New ethylene and derivatives complex, OL2K, complete in Shuaiba, Kuwait
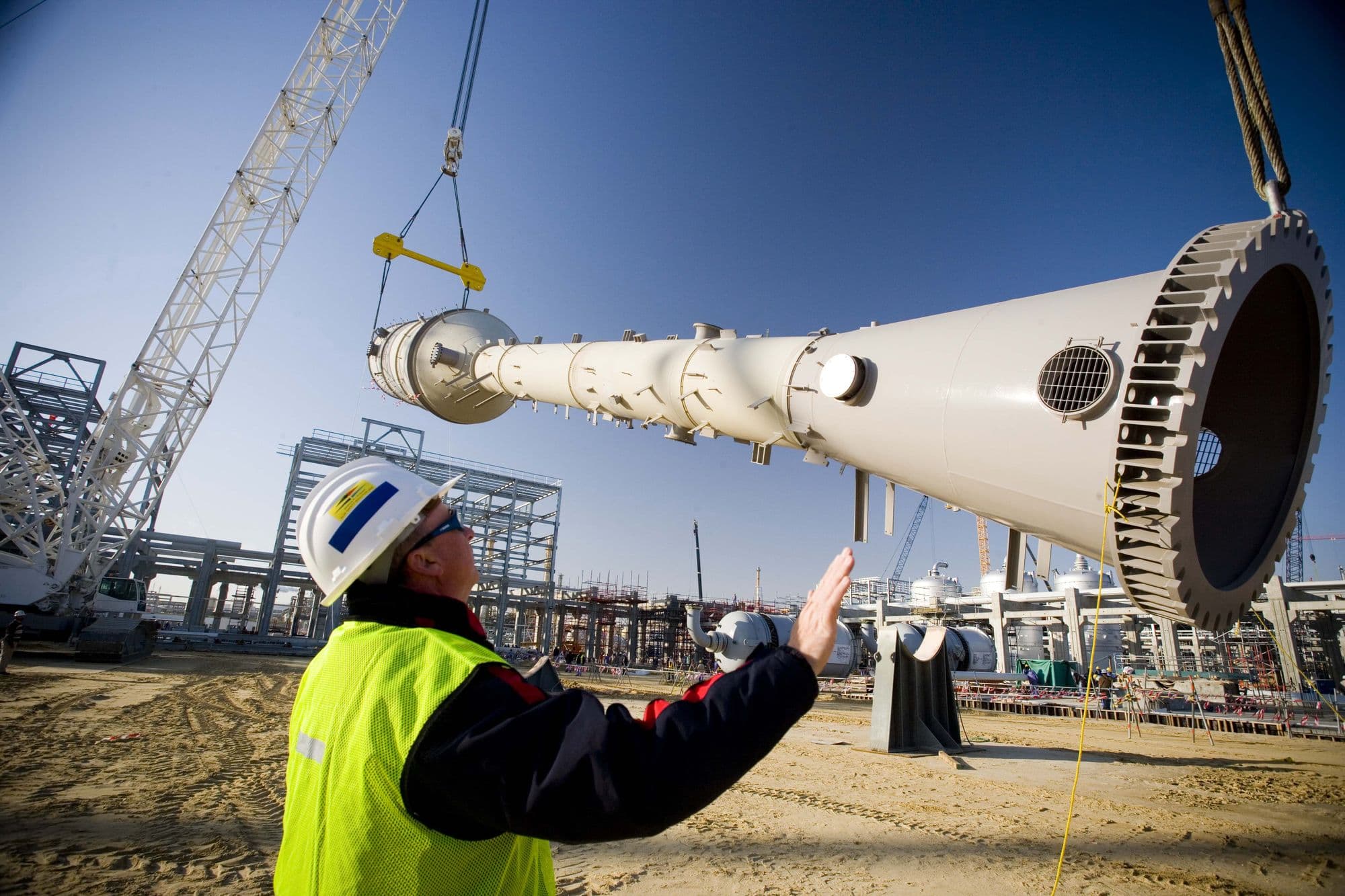
2009: New ethylene and derivatives complex, OL2K, complete in Shuaiba, Kuwait
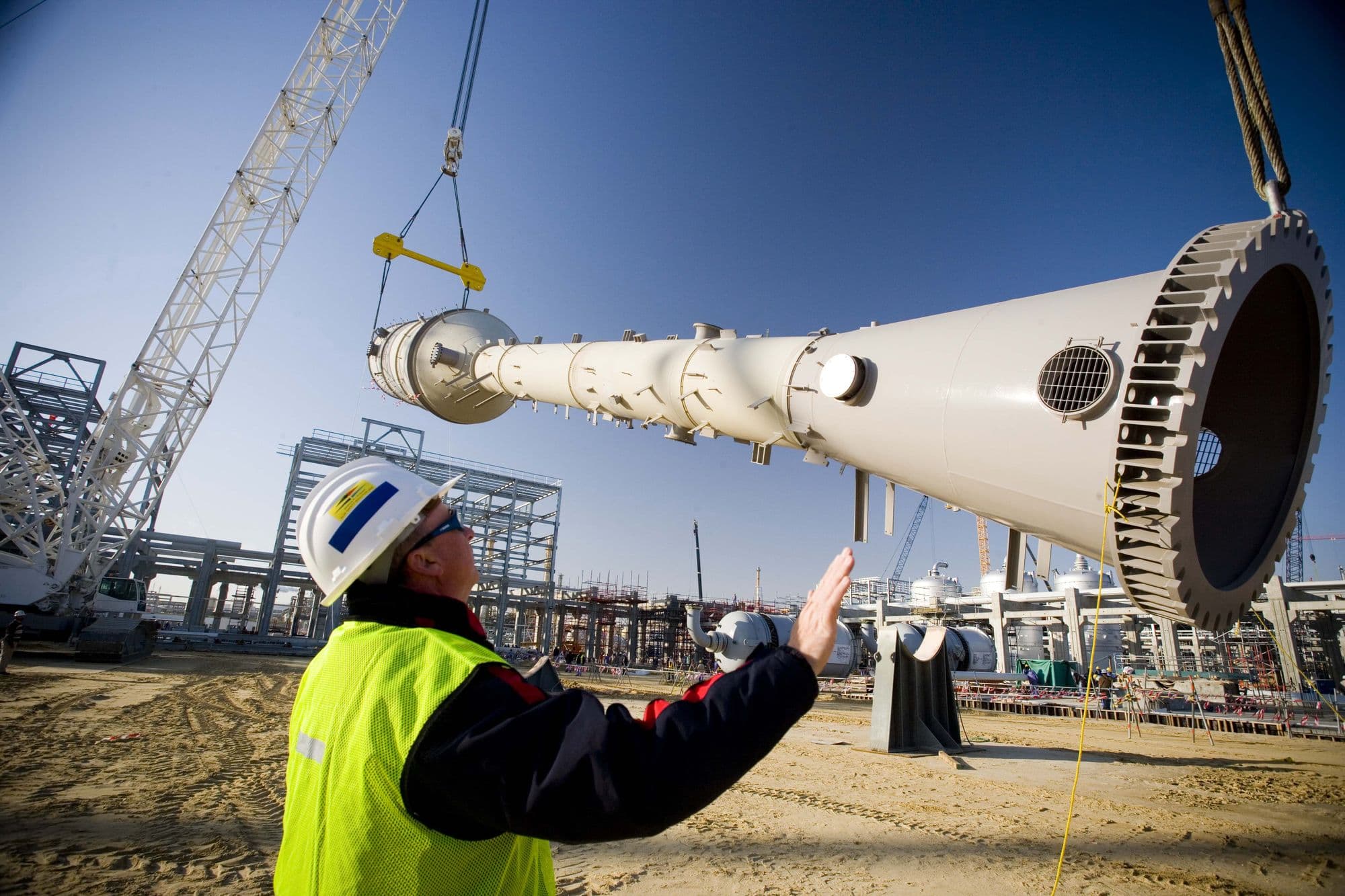
Fluor began work on the OL2K project in July 2004 by providing overall management consultancy and front-end engineering and design (FEED) work for utilities and infrastructure. The OL2K project was completed in June 2009 with an impeccable safety record. In addition to the overall management consultancy and FEED work, Fluor was awarded the FEED and engineering, procurement and construction management for the seawater cooling towers, polyethylene expansion, expansion of existing utilities and infrastructure and new utilities and infrastructure shared with aromatics. During the five-year project, Fluor introduced innovative solutions to meet many of the unique challenges including assisting our client in the development of a closed circuit seawater cooling system including onsite hyperbolic cooling towers.
2009
Jubail Acetyls Complex sends first commercial shipment of acetic acid to Asia
&w=3840&q=75)
2009: Jubail Acetyls Complex sends first commercial shipment of acetic acid to Asia
&w=3840&q=75)
Fluor performed engineering, procurement, construction management and precommissioning of the acetic acid (AA), vinyl acetate monomer (VAM) and associated utilities plants for this $1.8 billion project. Fluor also managed the general construction contractor, onsite tankage contractor and other owner’s contractors onsite. The first shipment to Asia was sent in 2009. Subsequently, the first shipment to Europe was sent in 2010.
2010s
Fluor expands EPC agreements with clients to execute projects around the world.
2010
Saudi Kayan Petrochemical Company constructs one of the largest petrochemical projects in the world to date
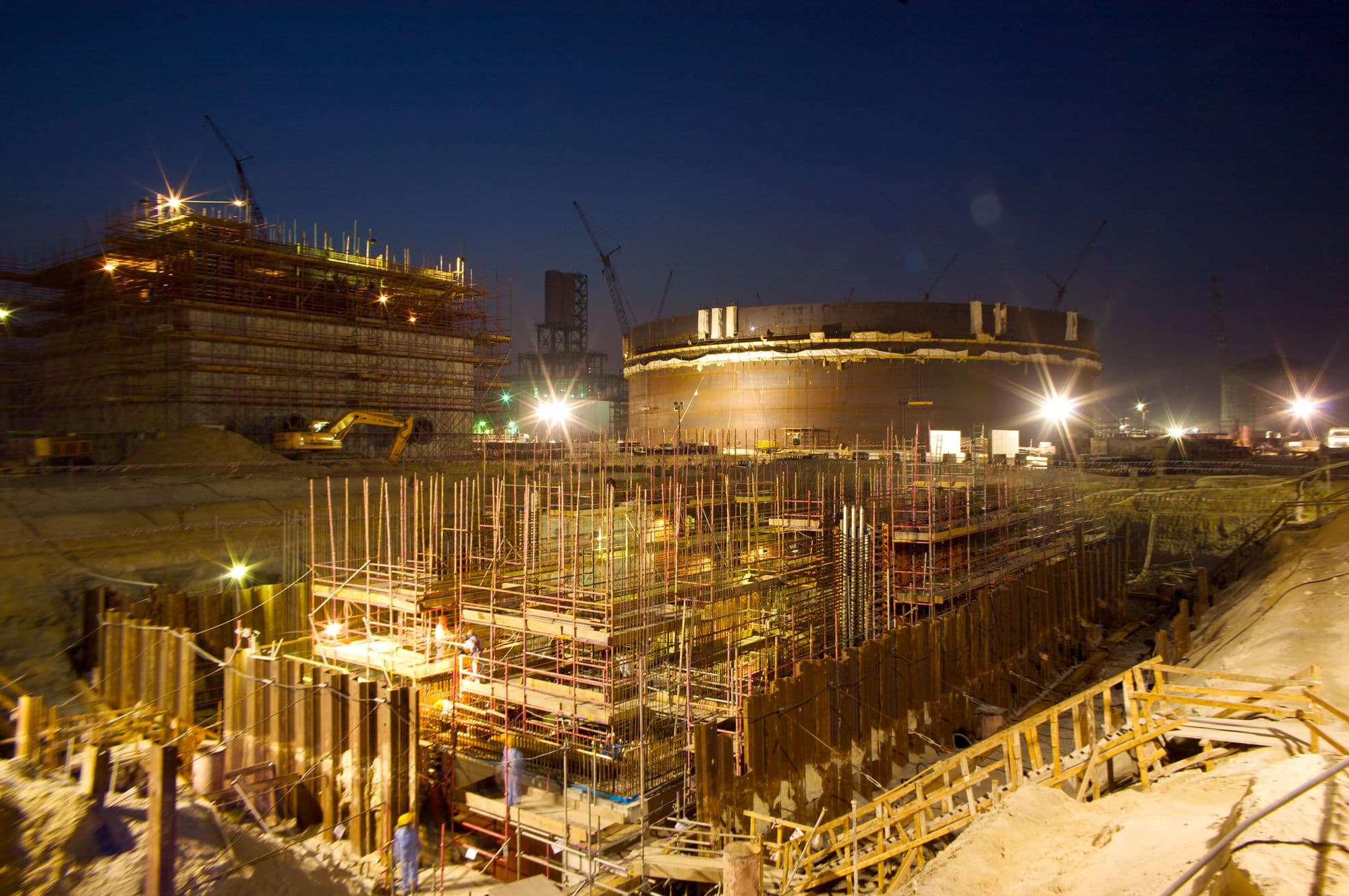
2010: Saudi Kayan Petrochemical Company constructs one of the largest petrochemical projects in the world to date
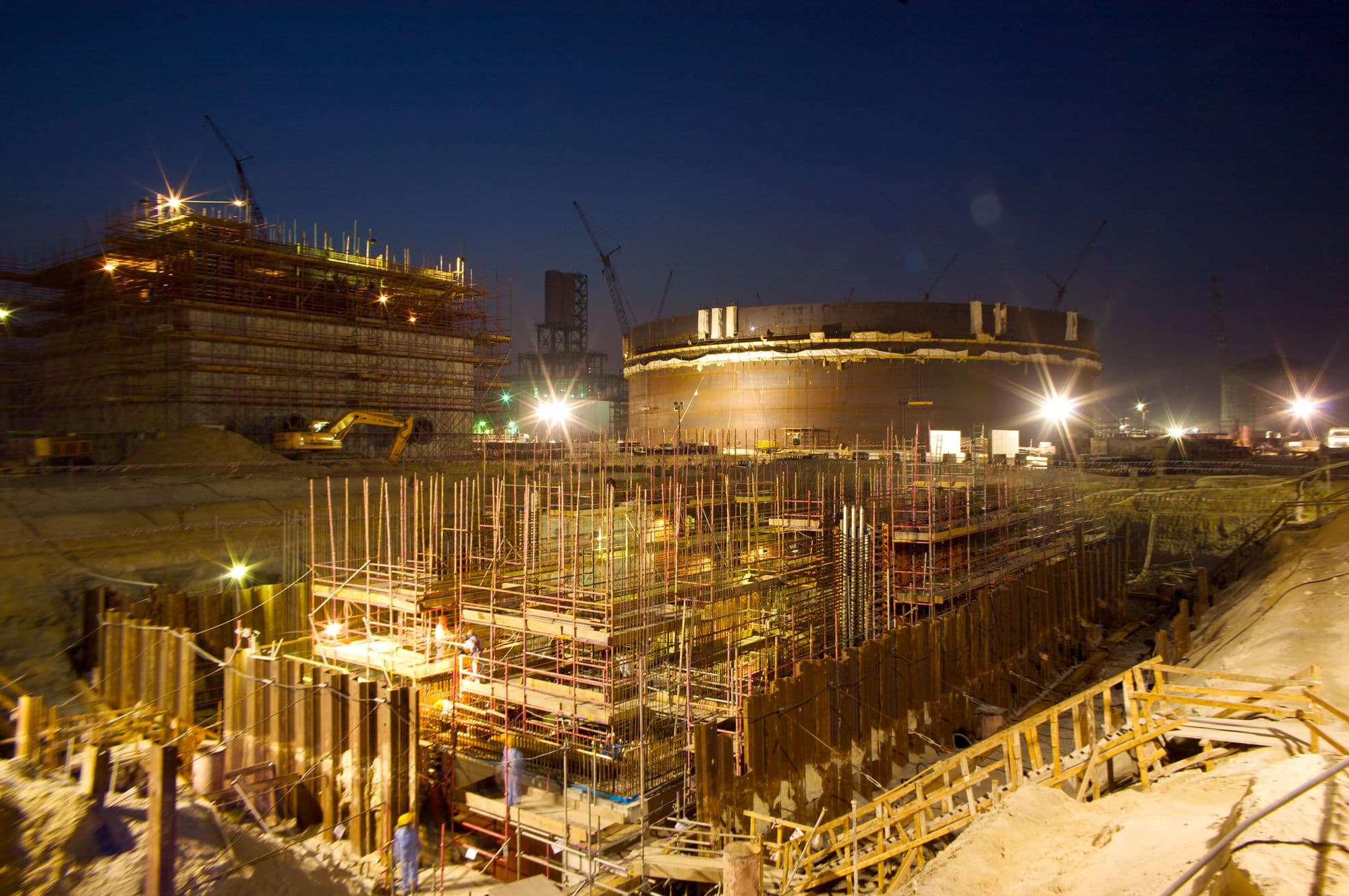
The Saudi Kayan Petrochemical Complex includes a 2 million-tons-per-year ethane / butane cracker, including benzene extraction facilities; a 700,000-tpy polyethylene plant; a polypropylene plant with capacity of at least 350,000 tpy; and a 530,000-tpy ethylene glycol unit. An integrated phenolics plant, including cumene, phenol and Bisphenol-A units, produce feedstock for a 260,000-tpy, high-value polycarbonates plant. Additional amine derivative facilities were installed for the production of methylamines, ethanolamines, ethoxylates and choline chloride. Fluor was responsible for engineering, procurement and construction management of the Utilities and Offsites scope, which comprised approximately 30 percent of the total project.
2011
BASF selects Fluor as Asia-Pacific engineering partner
&w=3840&q=75)
2011: BASF selects Fluor as Asia-Pacific engineering partner
&w=3840&q=75)
In 2011, Fluor was selected by BASF as their engineering partner in Asia-Pacific. The €150 million BASF Dahej project is the first to be executed under this umbrella contract for BASF projects in Asia-Pacific and is BASF's largest investment in India.
2010
Dow Corning Siloxane Project in Zhangjiagang completed
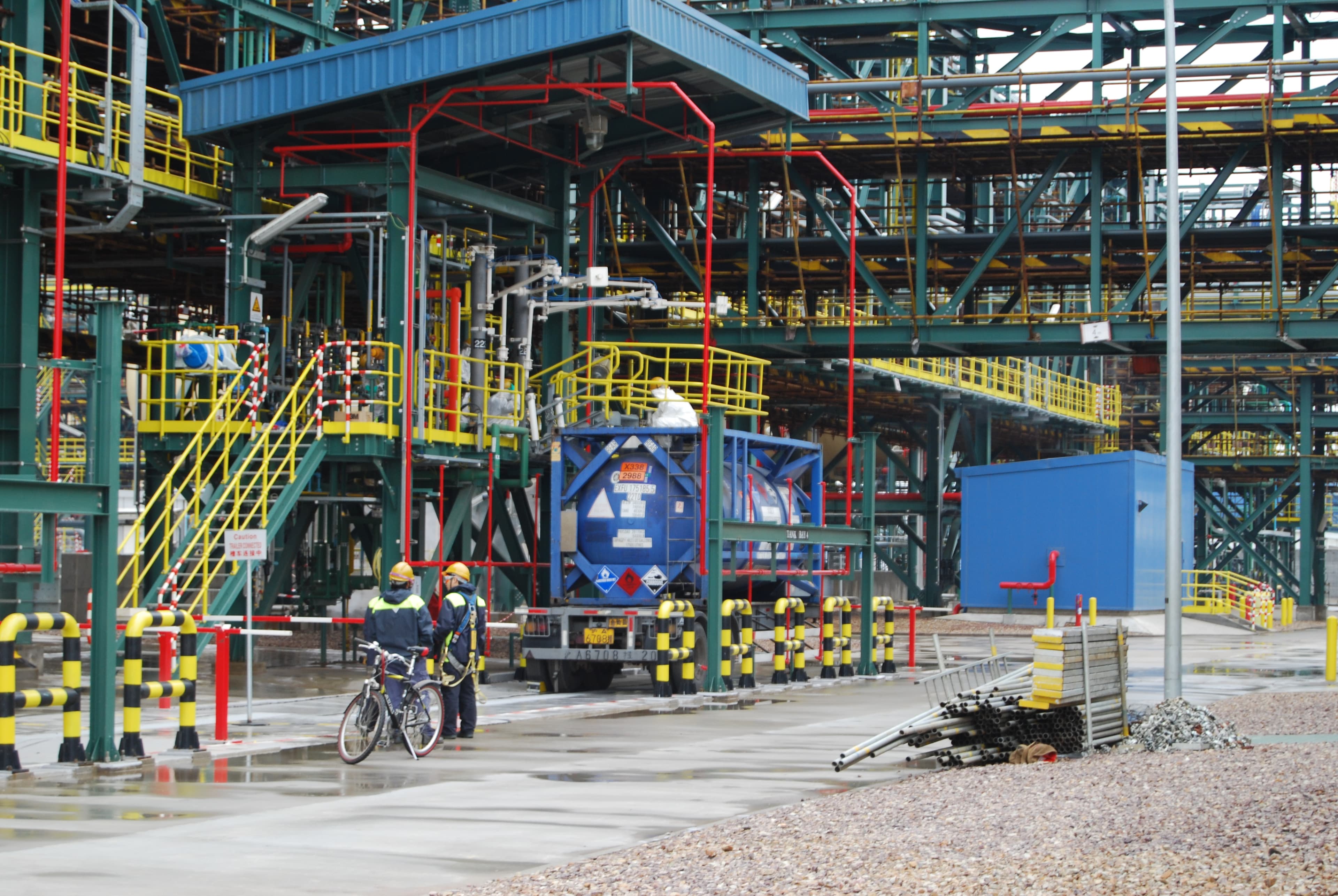
2010: Dow Corning Siloxane Project in Zhangjiagang completed
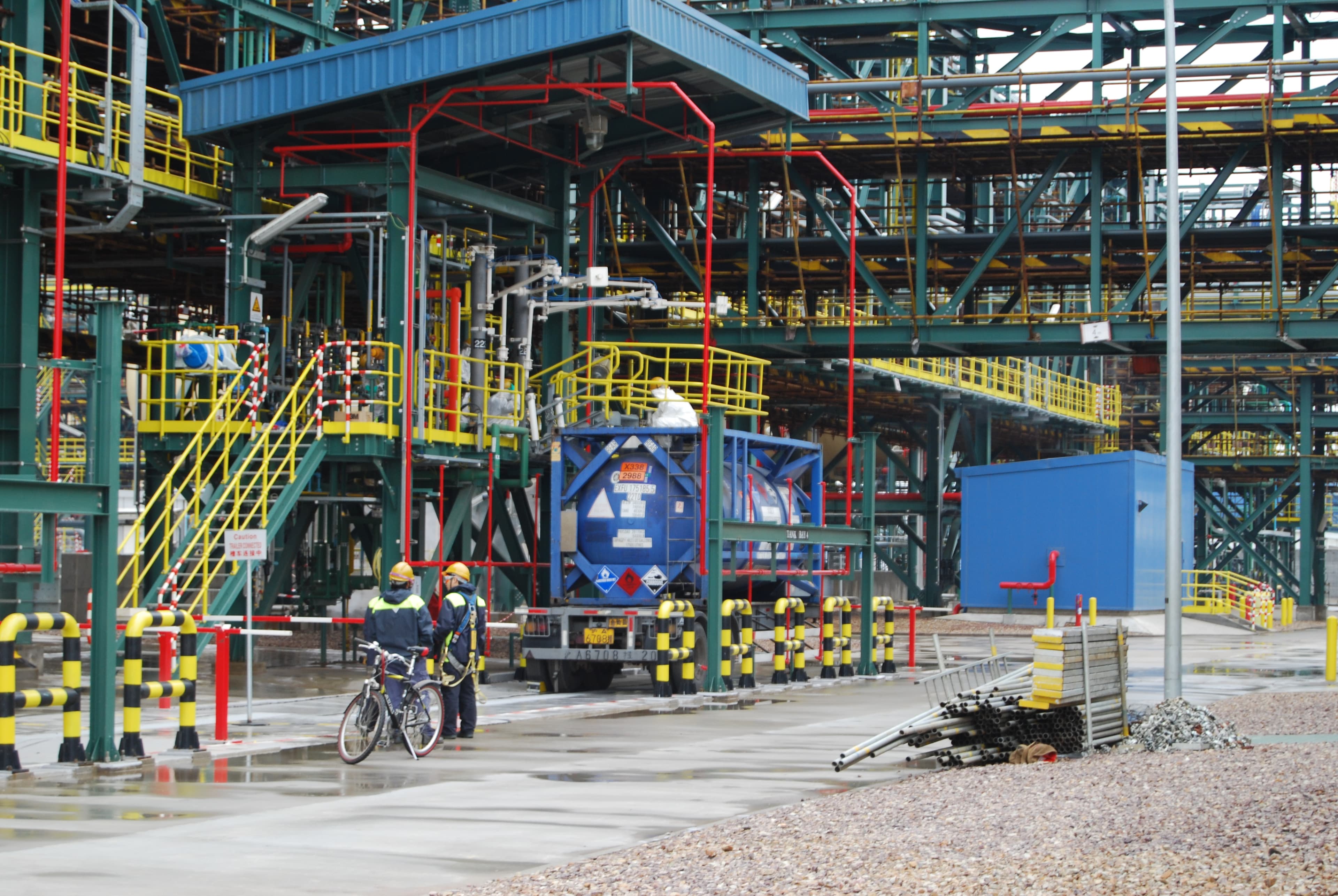
Fluor performed engineering, procurement, construction management and project management for a major siloxane intermediate facility constructed in the Jiangsu Yangtze River Chemical Industrial Park. The scope included chlorosilane storage, methyl chloride storage, overheads/pipe rack, undergrounds, wastewater treatment and water scrubber, product storage, demineralized water and steam boiler systems, tank farm and material and energy recover unit, acid neutralization and solids treatment.
2012
Dow and Fluor sign Strategic Global EPC Agreement
&w=3840&q=75)
2012: Dow and Fluor sign Strategic Global EPC Agreement
&w=3840&q=75)
The Dow Chemical Company and Fluor sign a Strategic Global Engineering, Procurement, Construction (EPC) and Construction Management Agreement in support of Dow’s global capital projects program ranging across all Dow products.
2014
Super Absorbent Polymer Plant selected as Global Best Project in Manufacturing by ENR
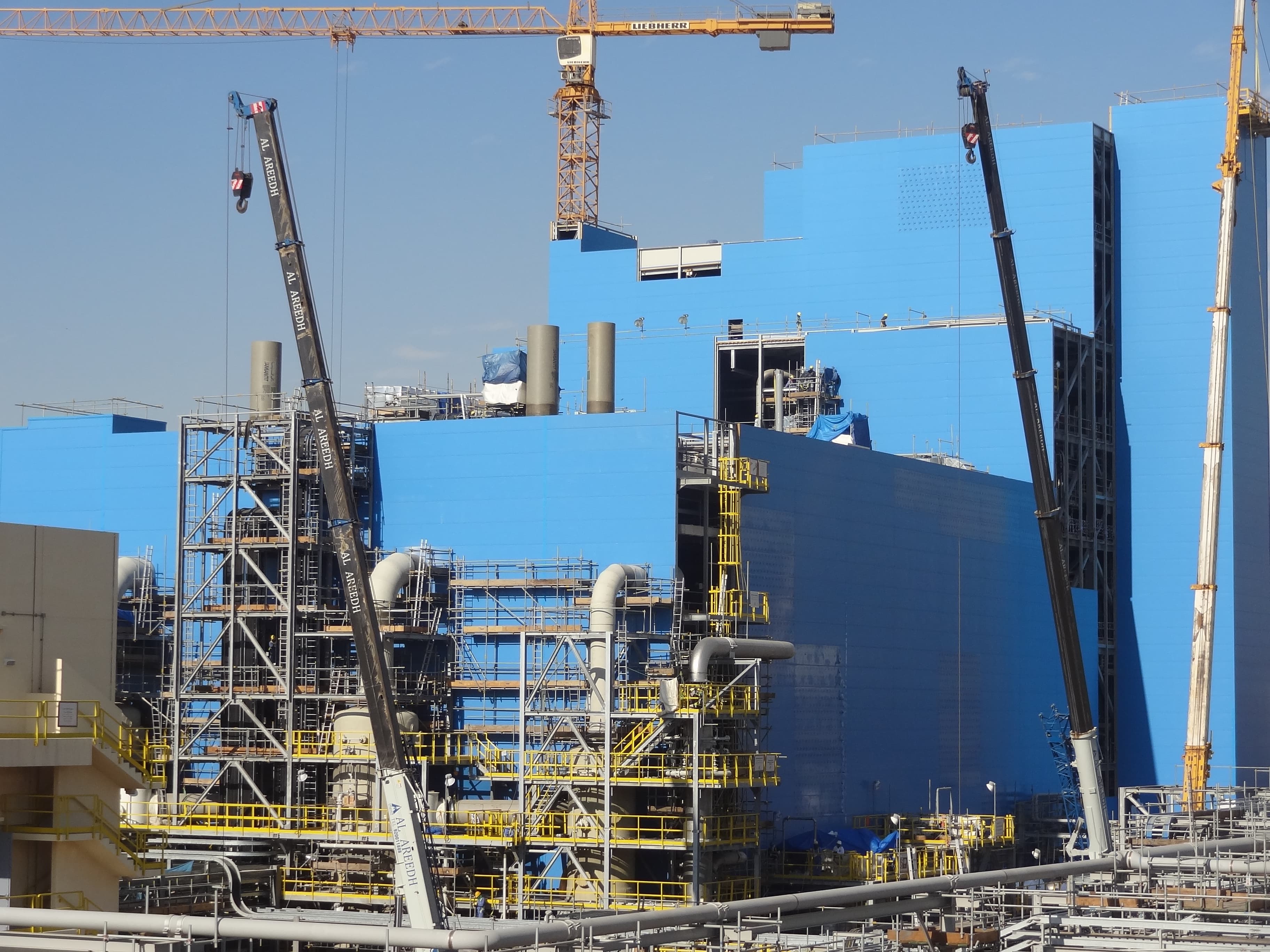
2014: Super Absorbent Polymer Plant selected as Global Best Project in Manufacturing by ENR
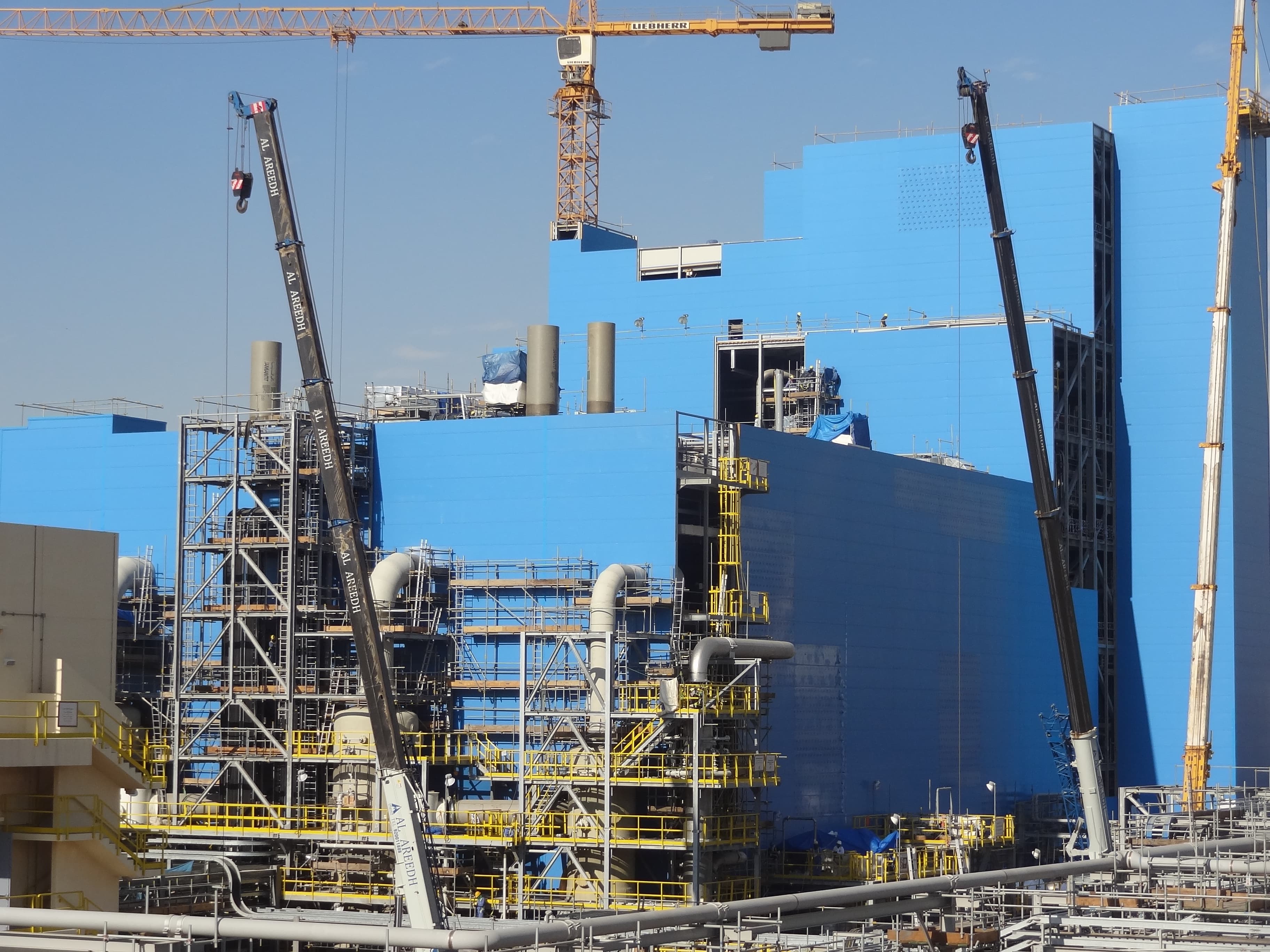
SAPCO has a proprietary process to produce super absorbent polymer. They contracted Fluor to build their new production facilities. Fluor was responsible for basic engineering of the plant as well as engineering, procurement and construction of the facilities. In 2014, Fluor's Super Absorbent Polymer project was selected by Engineering News-Record as the Global Best Project in the Manufacturing category.
2014
Production at BASF's large-scale GIR chemical complex commences
&w=3840&q=75)
2014: Production at BASF's large-scale GIR chemical complex commences
&w=3840&q=75)
This was Fluor's first project in India for BASF with a focus on utilizing local engineering and locally sourced equipment.
The new site is an integrated hub for polyurethane manufacturing and houses production facilities for care chemicals and polymer dispersions for coatings and paper. The chemical complex also comprises associated infrastructure, storage, utilities and offsites.
2014
Aromatics Ingredients Facility manufactures chemicals used in home and personal care products, fragrances, food and pharmaceuticals
&w=3840&q=75)
2014: Aromatics Ingredients Facility manufactures chemicals used in home and personal care products, fragrances, food and pharmaceuticals
&w=3840&q=75)
BASF PETRONAS Chemicals awards engineering, procurement and construction management (EPCM) contract to Fluor for an integrated aroma ingredients facility in Kuantan, Malaysia. Among other chemicals, the new facility will produce citral, which is identical to a main component found in lemongrass and other essential oils.
2015
BASF Ultramid® Polymerization Plant operational in Shanghai
&w=3840&q=75)
2015: BASF Ultramid® Polymerization Plant operational in Shanghai
&w=3840&q=75)
The BASF Ultramid® Polymerization Plant was the first contract awarded in China under the BASF-Fluor Asia Umbrella Partnership agreement announced in July 2011. The Fluor China team achieved mechanical completion of the BASF Ultramid® Polymerization Plant in Shanghai on October 10, 2014, ahead of schedule with no LTI and under budget.
2015
Fluor completes world-scale isononanol plant for BASF and Sinopec
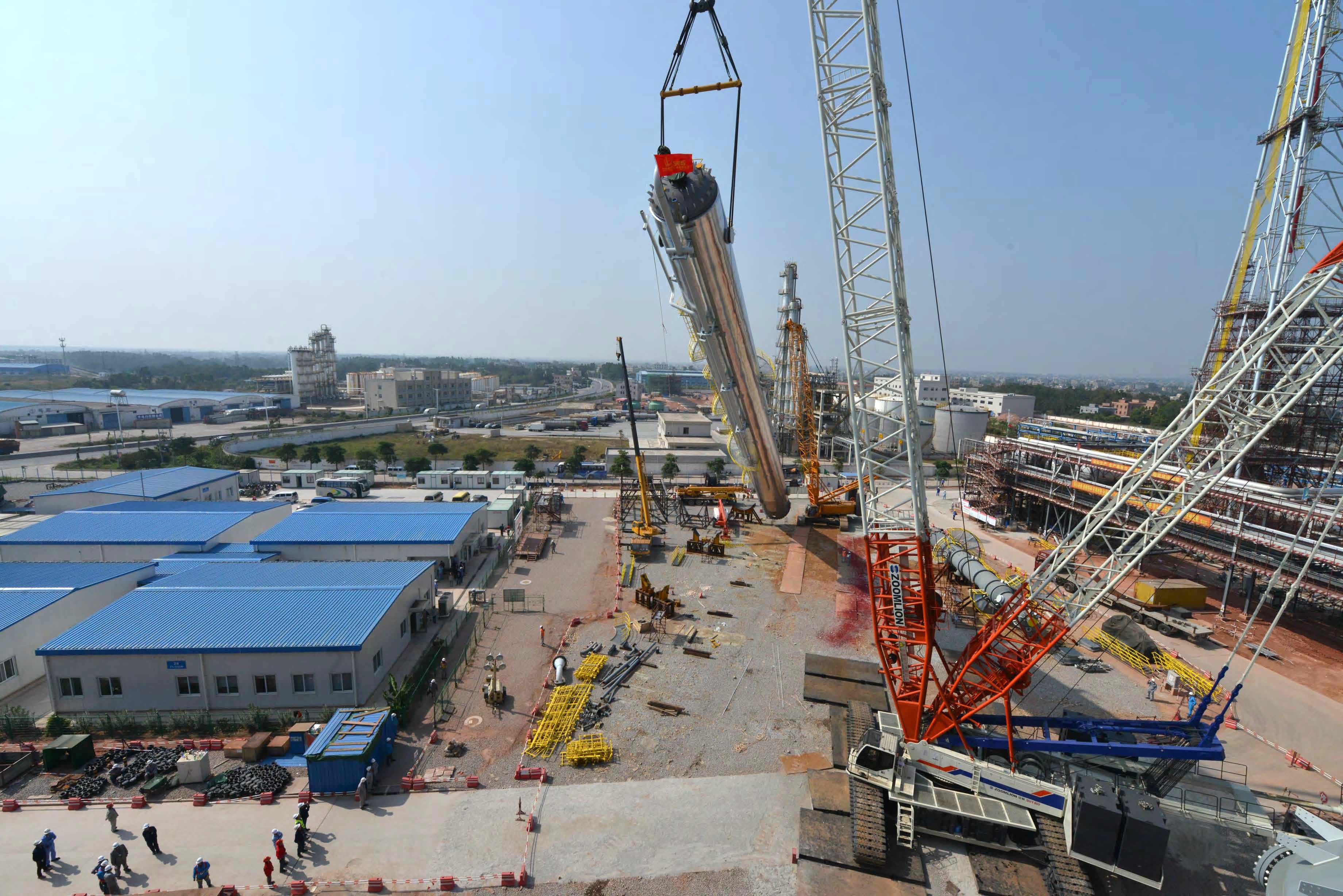
2015: Fluor completes world-scale isononanol plant for BASF and Sinopec
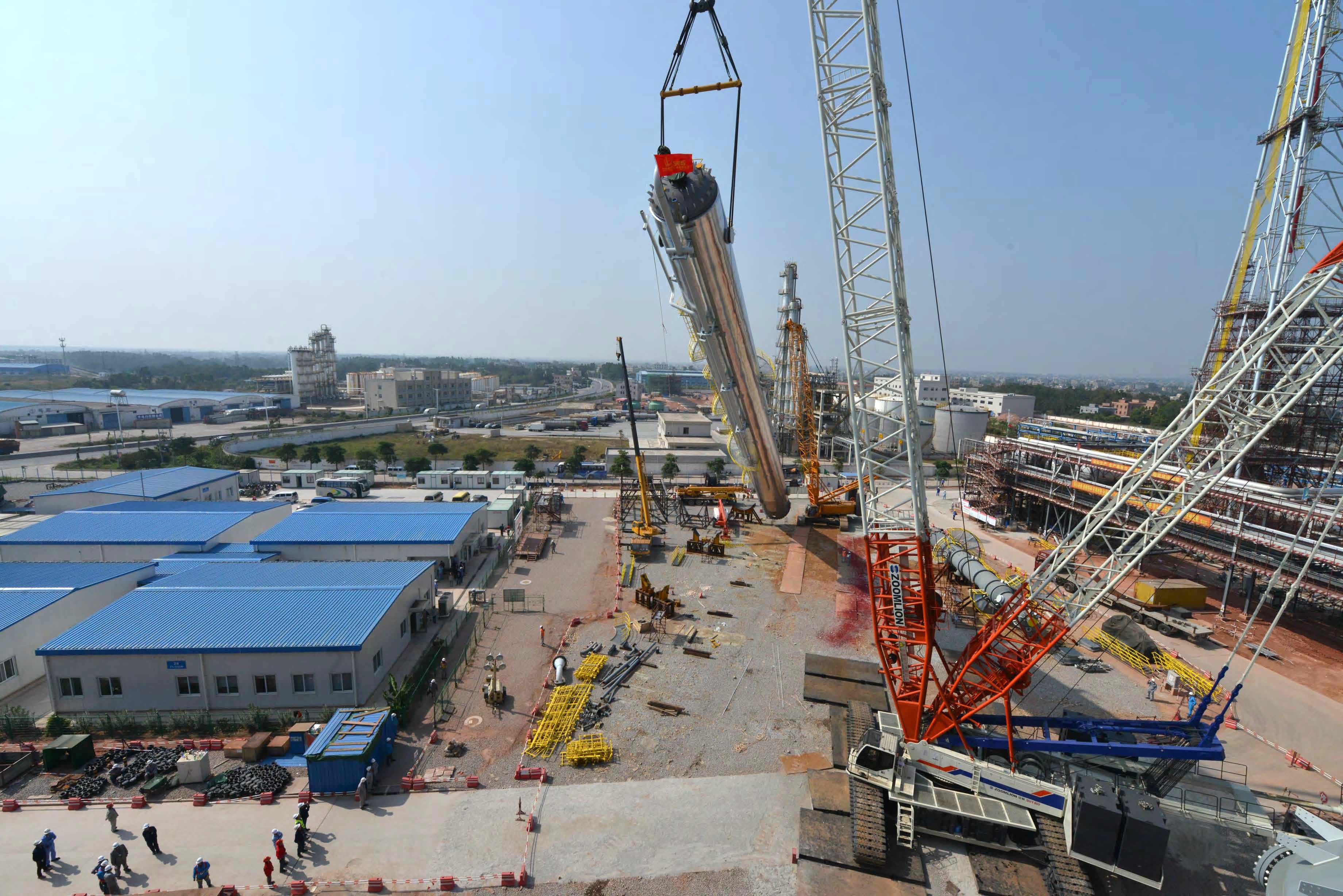
Fluor’s Shanghai office executed the pre-front-end engineering and design (pre-FEED) support, FEED and detailed engineering, procurement and construction management for BASF and Sinopec’s isononanol (INA) plant in Maoming, China. The INA plant is one of the first self-performed comprehensive FEED projects to be done in China and one of the first FEED projects executed entirely by a local Chinese team. The INA plant, a first-of-its-kind in Asia, has an annual capacity of 180,000 metric tons of INA.
2016
World-scale ethane cracker and derivatives complex will triple Sasol's chemical production capacity in the United States
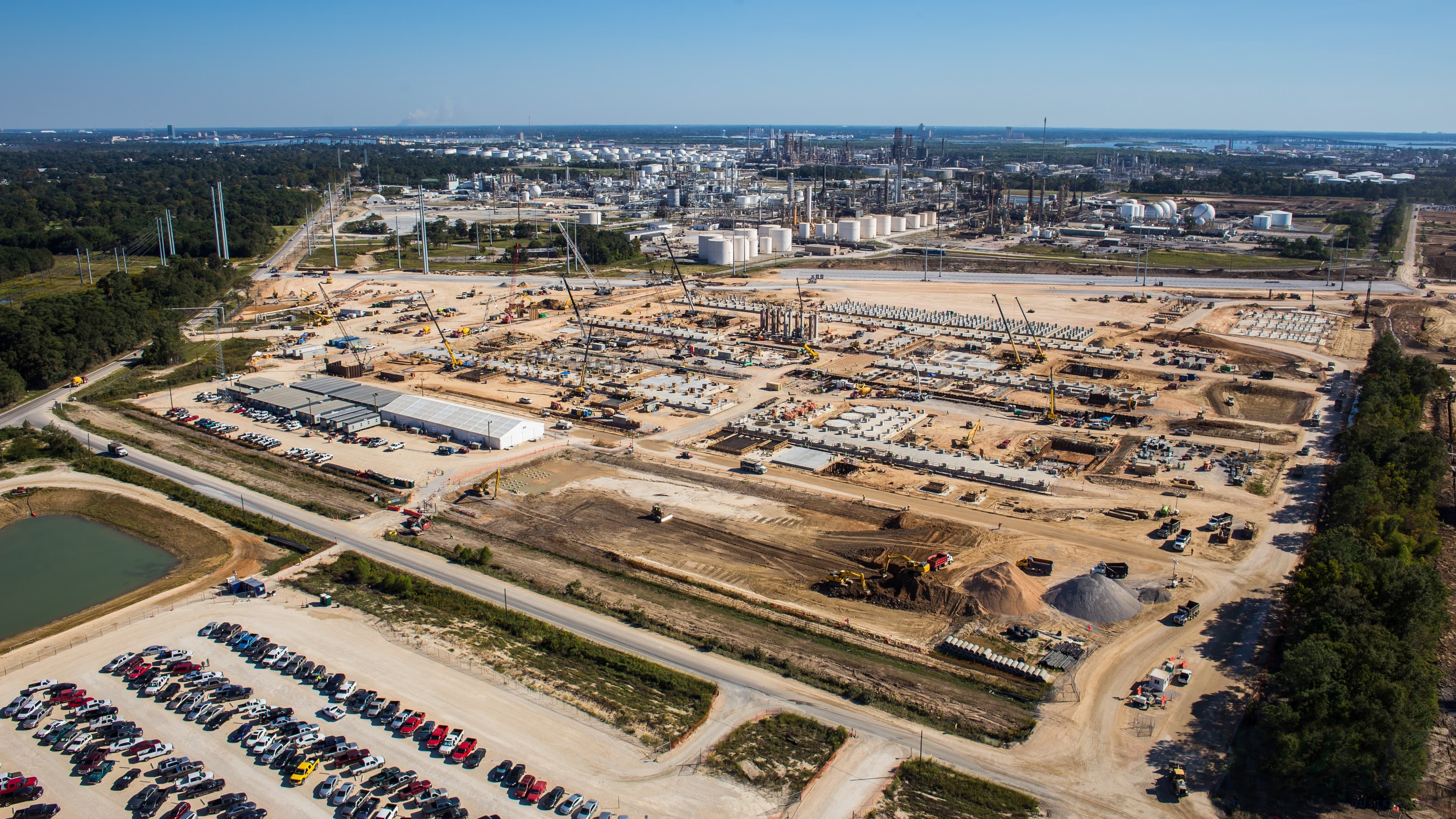
2016: World-scale ethane cracker and derivatives complex will triple Sasol's chemical production capacity in the United States
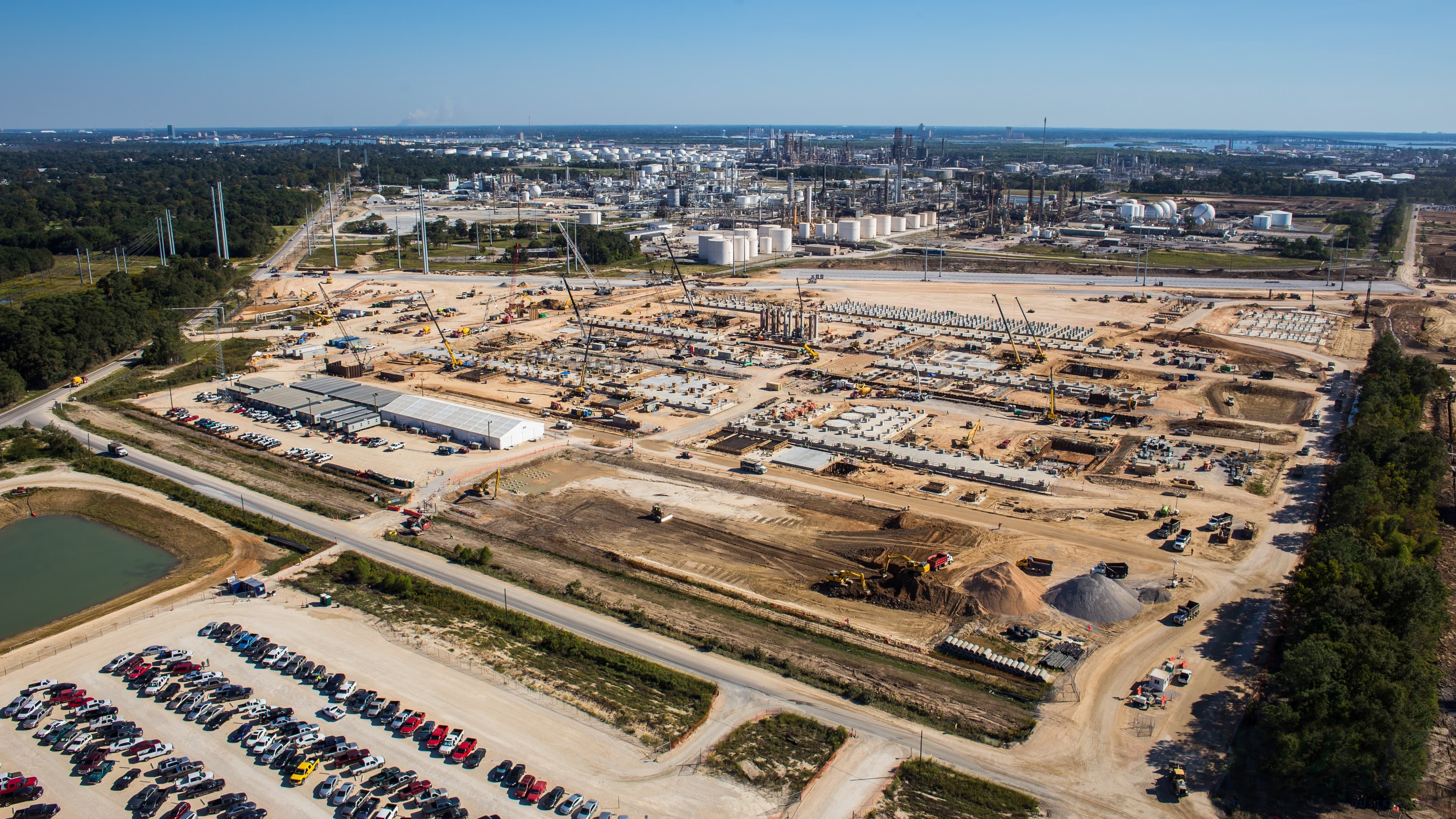
The new complex, located adjacent to Sasol’s existing facility in Southwest Louisiana, encompasses a 1.5 million tons-per-year ethane cracker, six downstream derivatives units, and associated utilities, offsites and infrastructure work. Leveraging our supply chain expertise, Fluor is focusing on the use of Louisiana vendors and suppliers to support local investment and job creation. Construction activities are underway and expected to be complete in 2018.
2016
Dow expands production facilities on the Gulf Coast in Freeport, Texas and Plaquemine, Louisiana
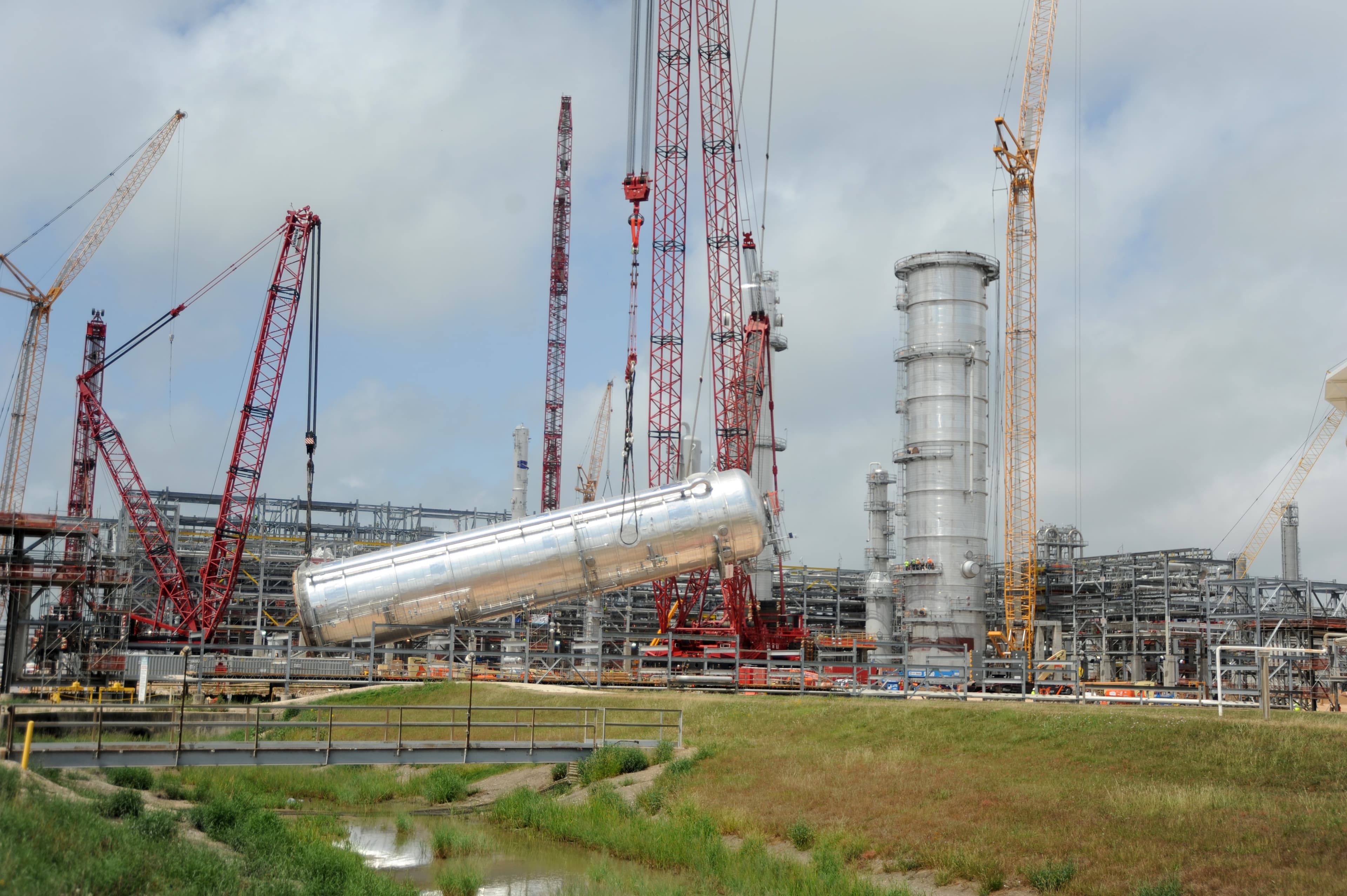
2016: Dow expands production facilities on the Gulf Coast in Freeport, Texas and Plaquemine, Louisiana
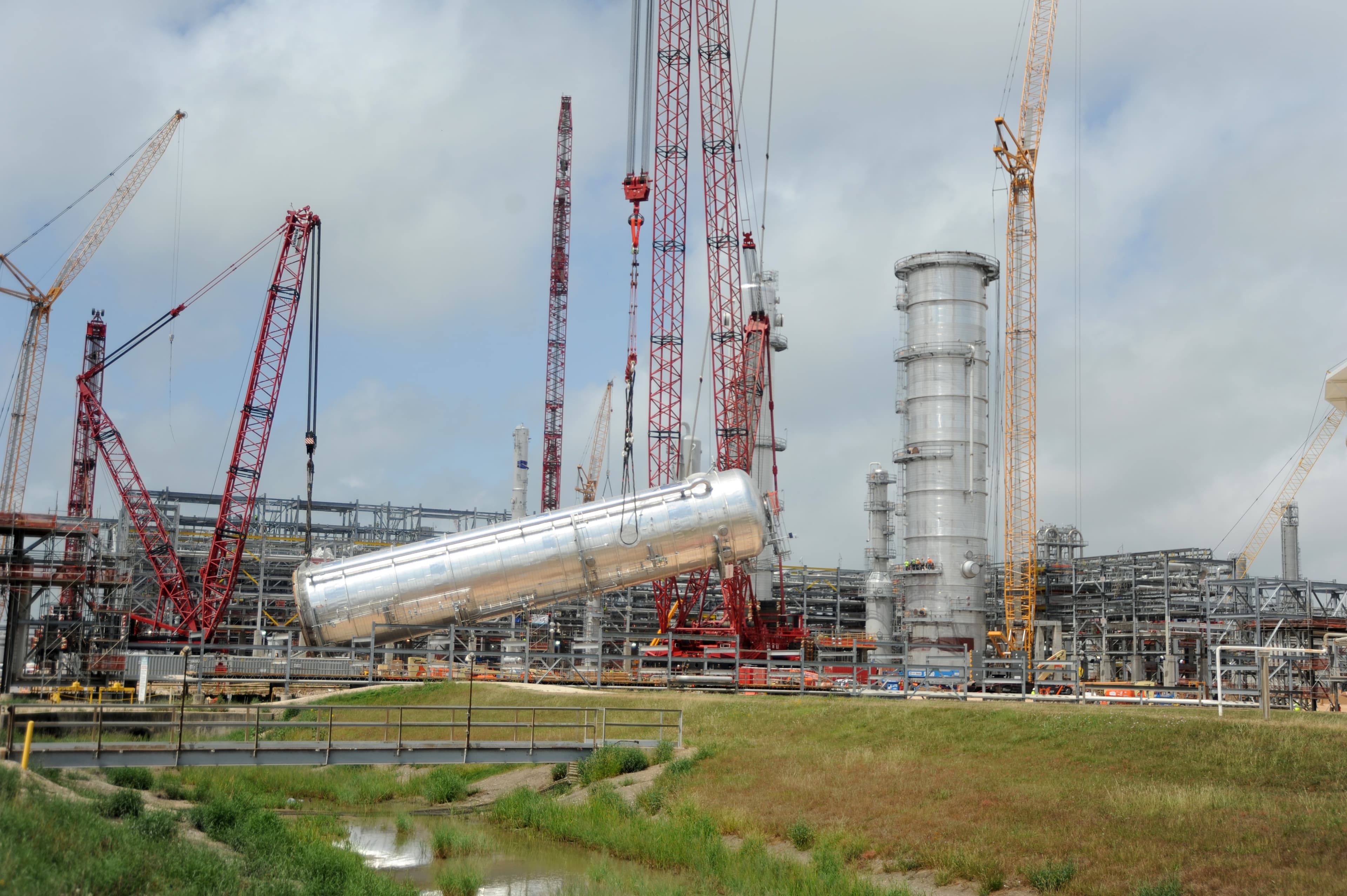
Fluor performed a significant portion of the program on the Oyster Creek site. Fluor’s scope consisted of a Propylene Dehydrogenization (PDH) unit and a state of the art Light-Hydrocarbon (LHC-9) unit. Fluor leveraged our proven processes to recruit a large number of direct-hire craft and construction management staff to build the facility. Construction completed in March 2017.
2017
Dow Ethylene Production Facility honored as a Global Best Project
&w=3840&q=75)
2017: Dow Ethylene Production Facility honored as a Global Best Project
&w=3840&q=75)
The Dow Ethylene Production Facility was honored in Engineering News-Record's (ENR) 5th annual Global Best Projects competition with an Award of Merit in the Power/Industrial category. The Dow/Fluor project teams were recognized for leading the outstanding design and construction efforts of 2017.
2017
BASF Automotive Coatings Plant reaches mechanical completion
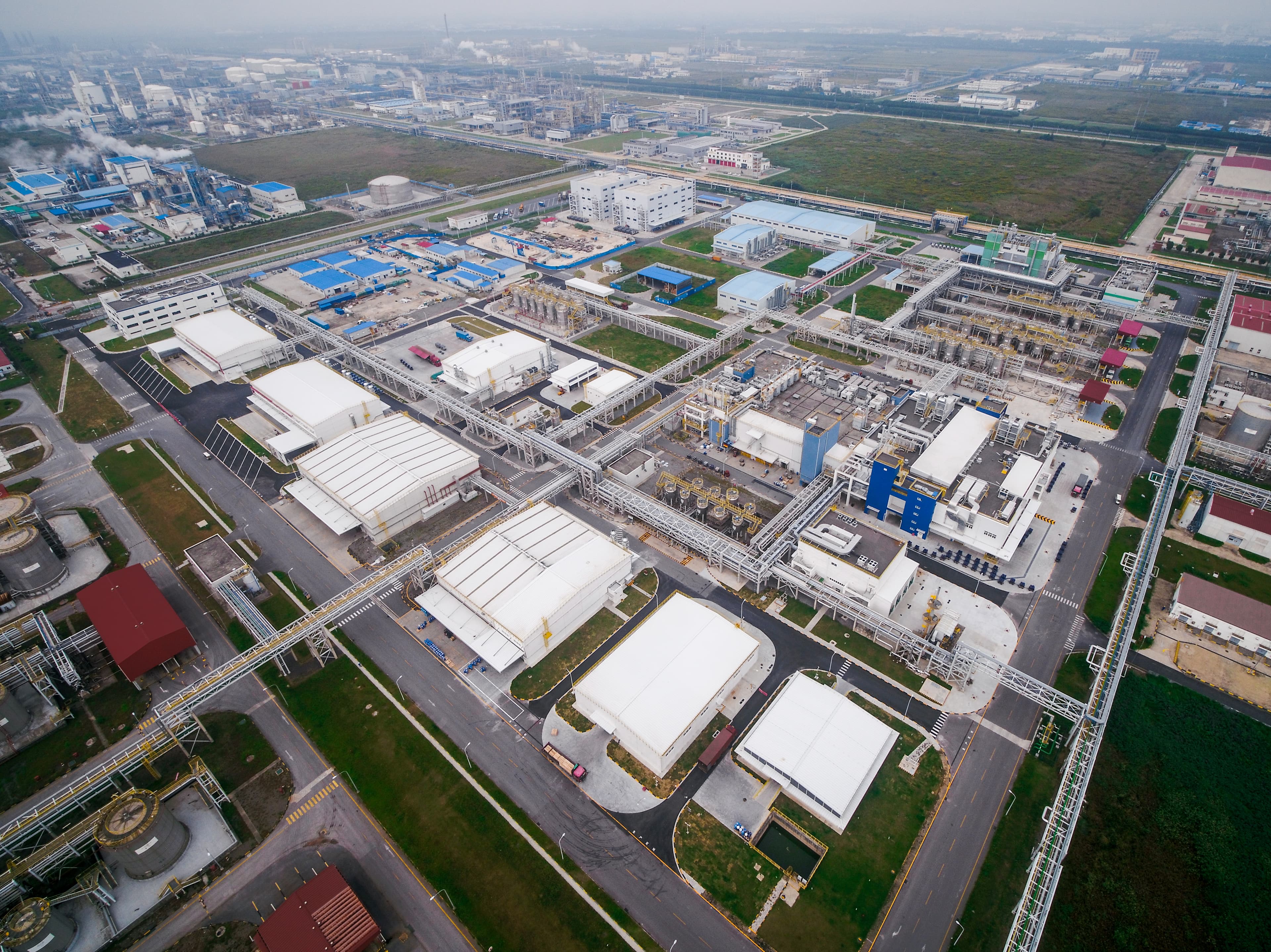
2017: BASF Automotive Coatings Plant reaches mechanical completion
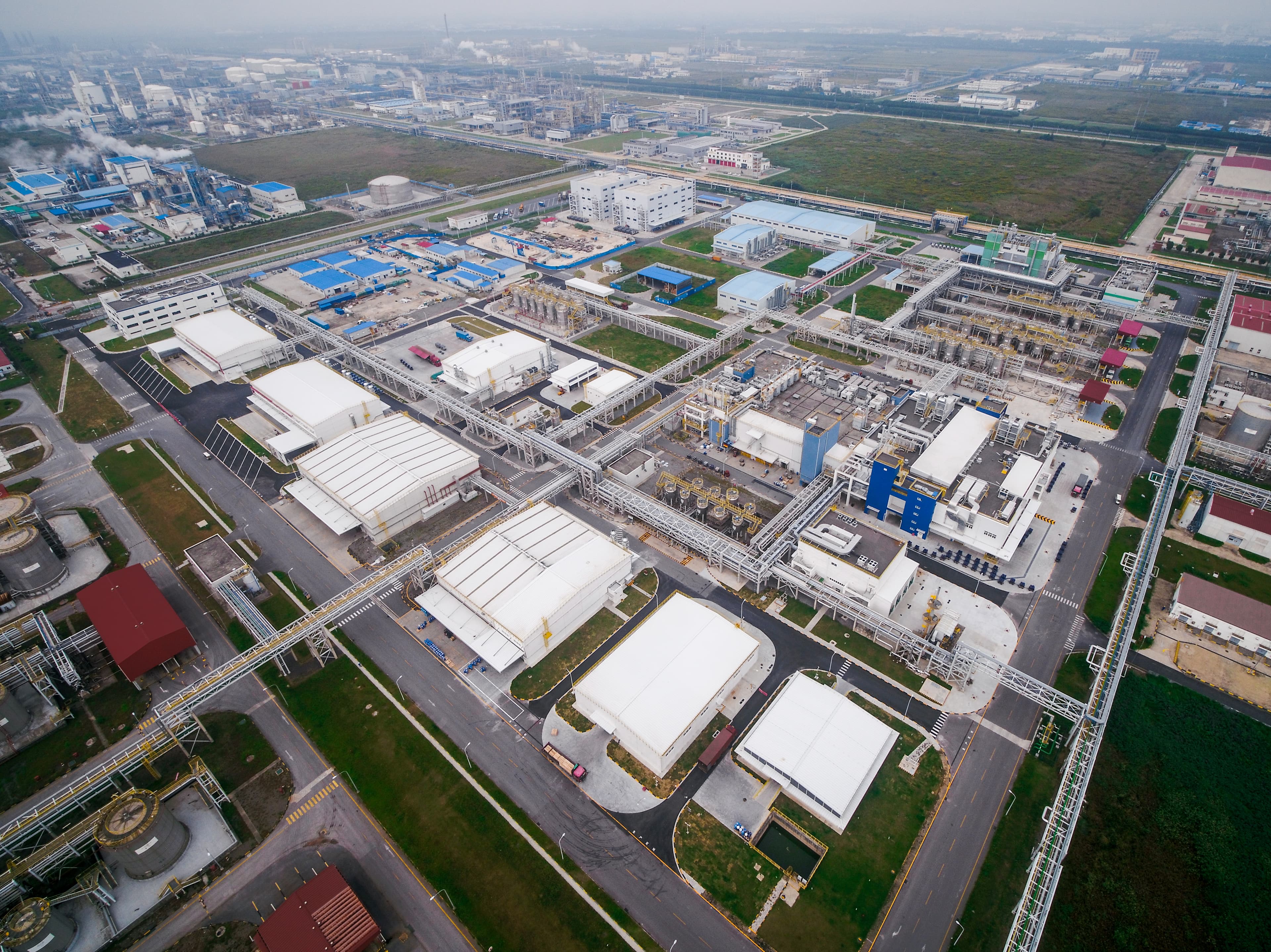
Fluor was selected by BASF to provide front-end engineering and design and engineering, procurement and construction management for a new automotive coatings plant in Shanghai. The expanded facility produces innovative and eco-efficient automotive coatings that support the growing automotive industry in China and better serve local car manufacturers.
2017
LyondellBasell selects Fluor for world's largest propylene oxide and tertiary butyl alcohol plant
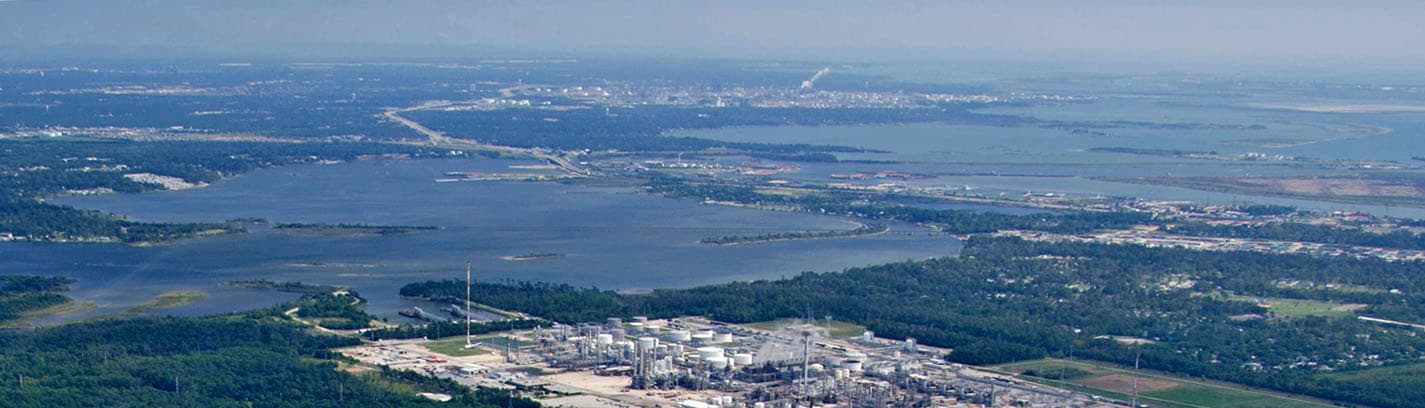
2017: LyondellBasell selects Fluor for world's largest propylene oxide and tertiary butyl alcohol plant
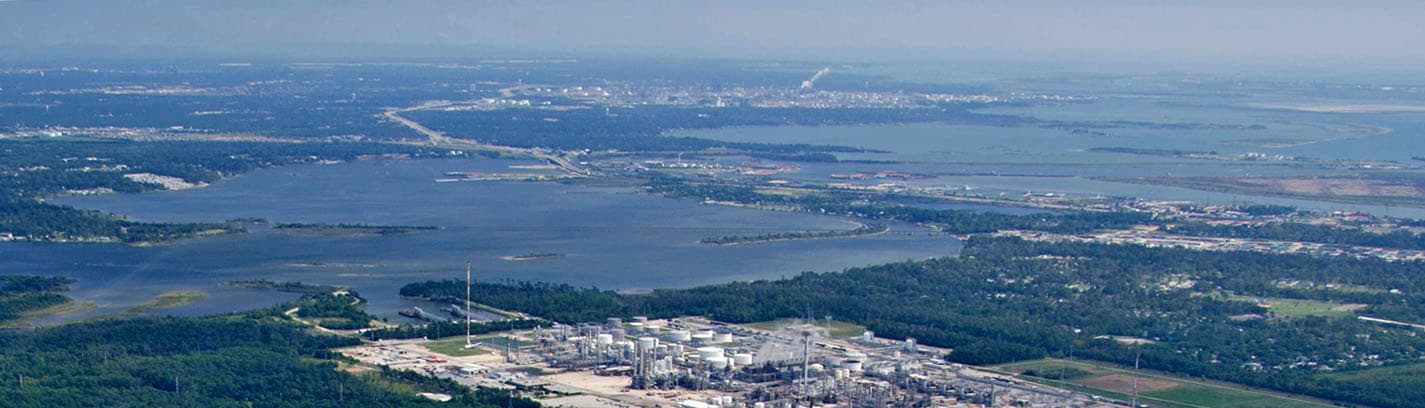
Fluor performed front-end engineering and design (FEED) work for LyondellBasell's new propylene oxide and tertiary butyl alcohol plant. After FEED completion, Fluor was awarded the engineering and procurement contract in 2017. The new plant will be the world’s largest of its type and represents the single-largest capital investment in LyondellBasell’s history.
2018
Fluor provides EPCm services for Ingevity’s China LD Project in Changshu
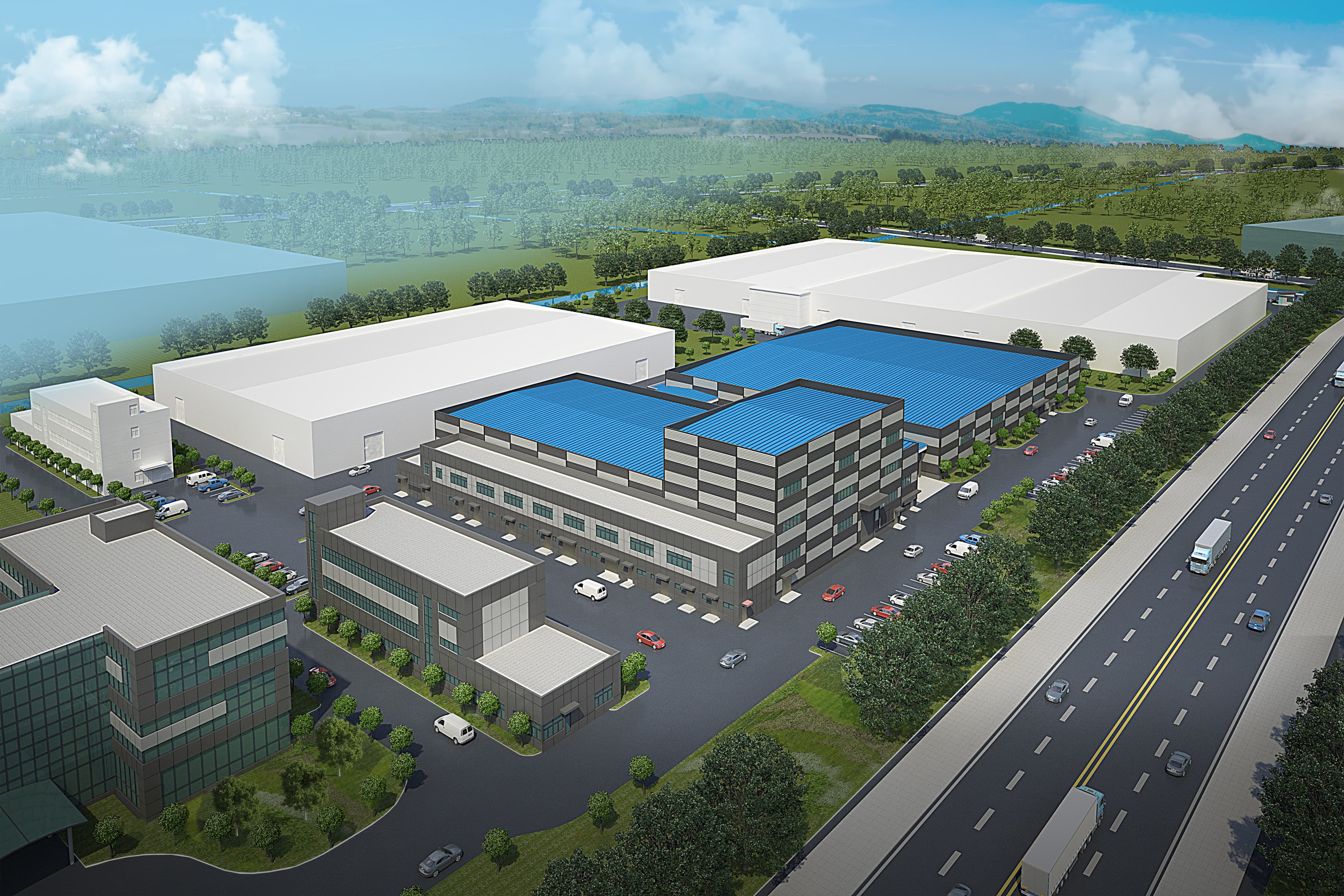
2018: Fluor provides EPCm services for Ingevity’s China LD Project in Changshu
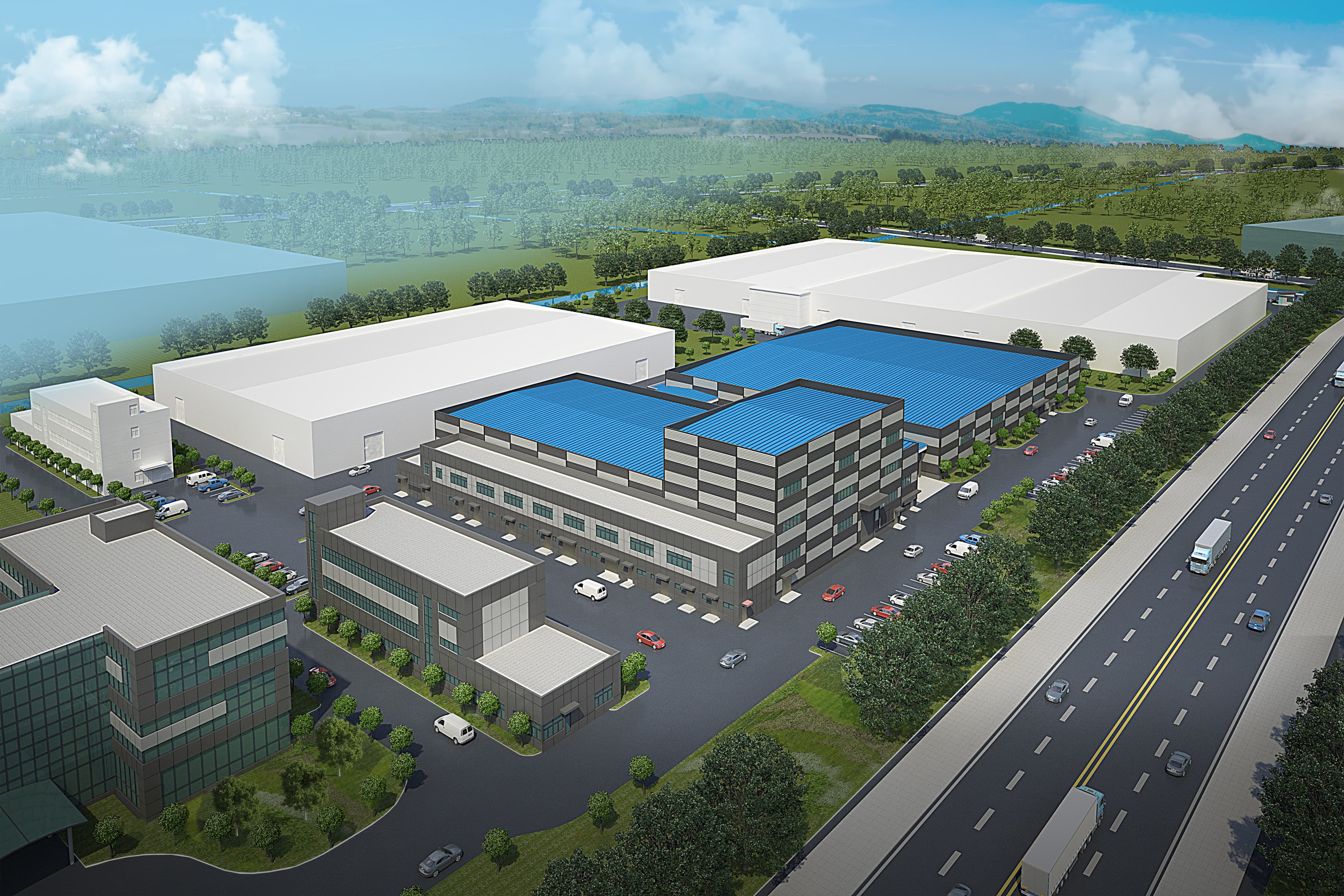
Fluor will provide engineering management, procurement and construction management (EPCm) services to build a greenfield installation for Ingevity’s new activated carbon facility in Changshu, China. The new, larger facility will consist of two identical production lines of activated carbon for use in automotive products.
2018
Fluor expands Ingevity’s activated carbon facilities in Zhuhai, China
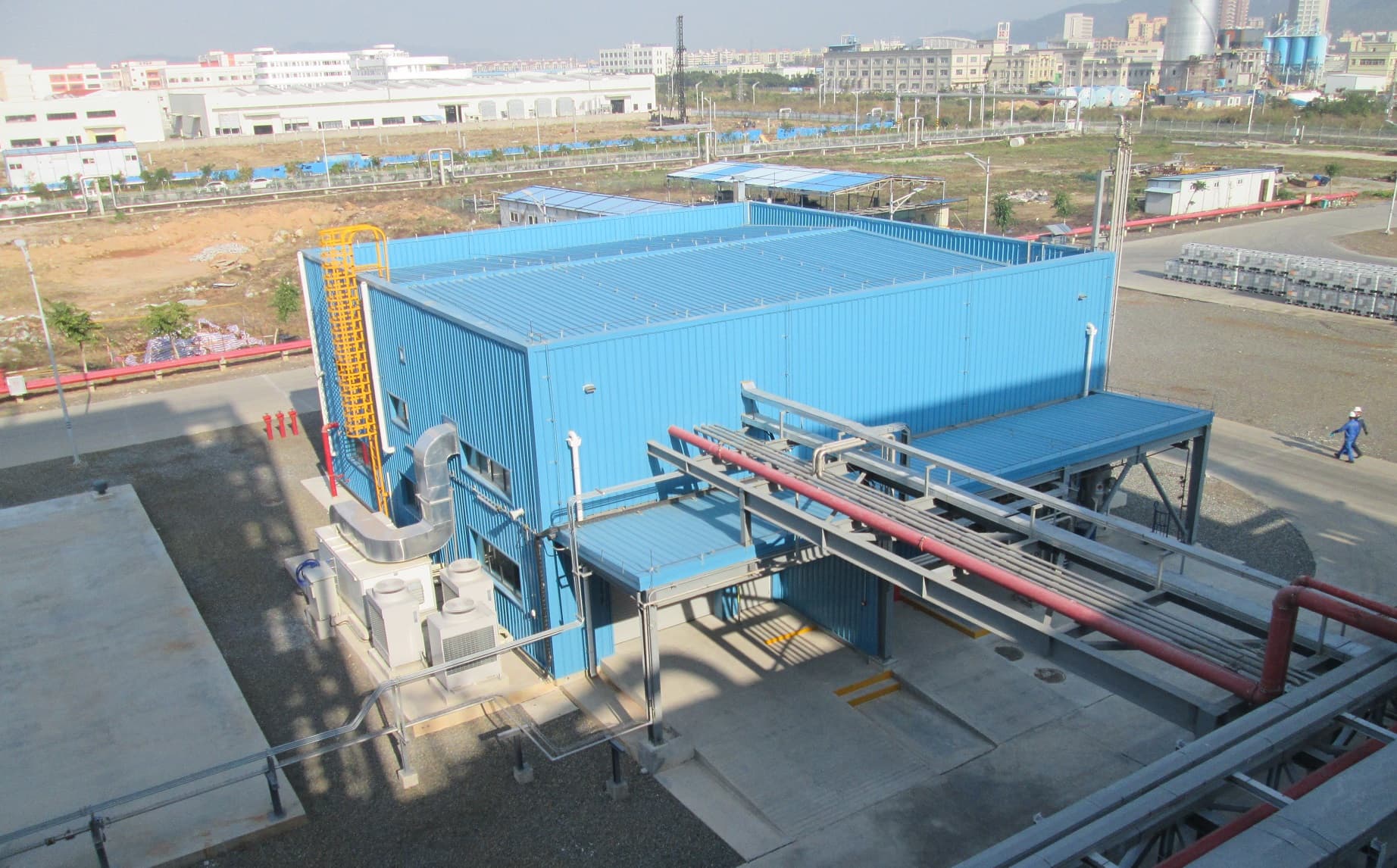
2018: Fluor expands Ingevity’s activated carbon facilities in Zhuhai, China
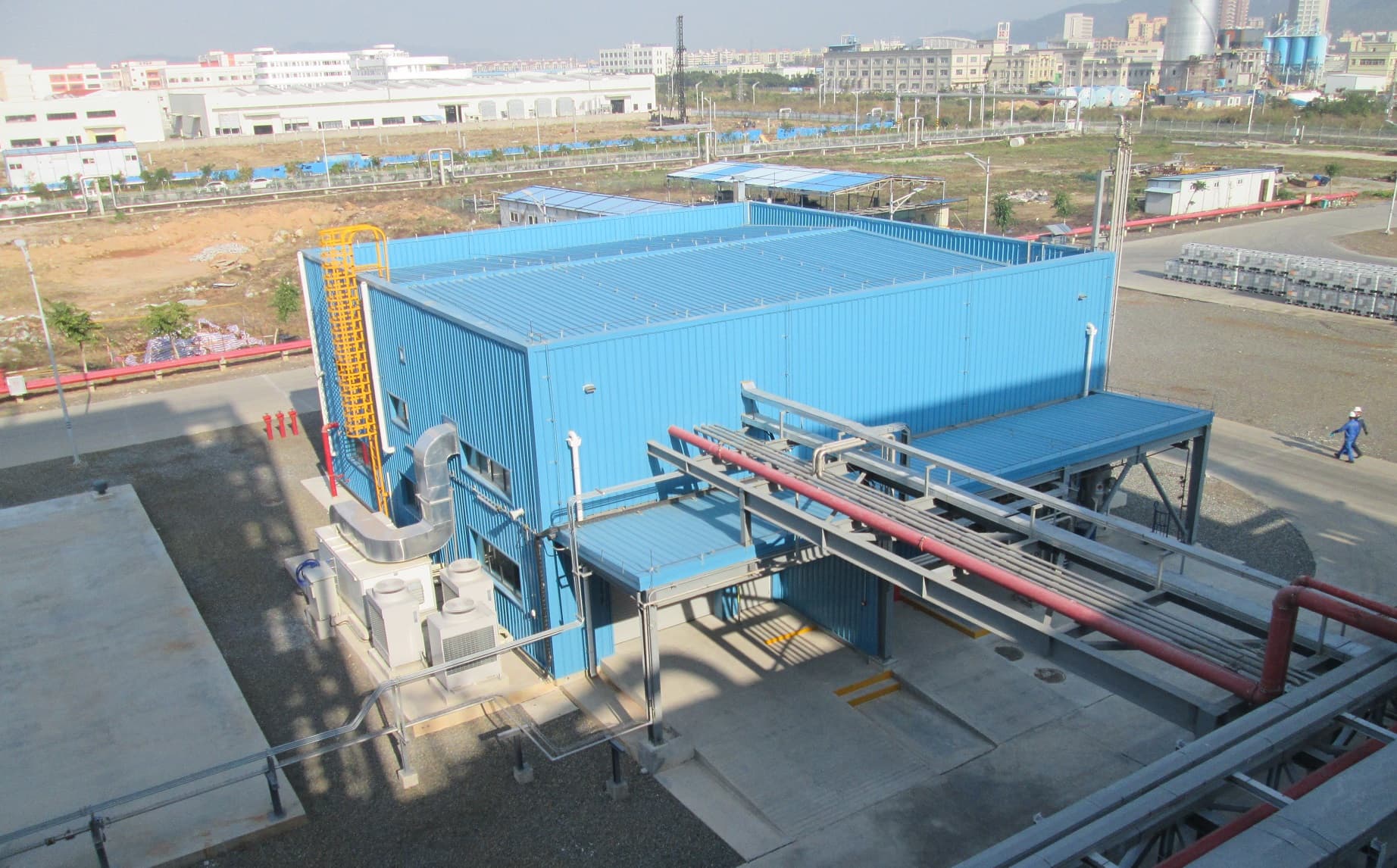
Fluor is executing engineering, procurement and construction management (EPCm) for an expansion of Ingevity’s facilities in Gaolan Port Economic Zone in Zhuhai, China. The Ingevity facilities will be expanded to meet the demand for activated carbon products. The activated carbon is used in automotive emission controls and water, food and beverage purification products.
2018
Fluor provides mechanical construction for monoethylene glycol manufacturing facility
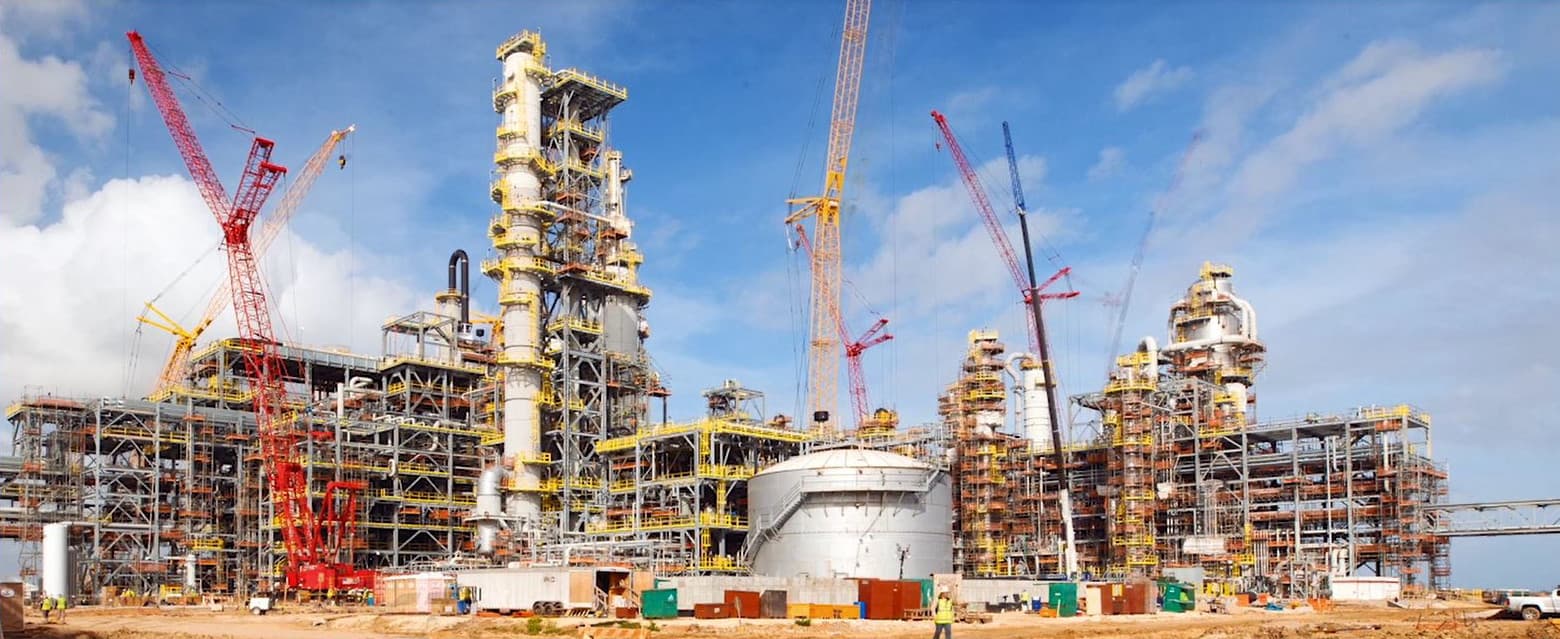
2018: Fluor provides mechanical construction for monoethylene glycol manufacturing facility
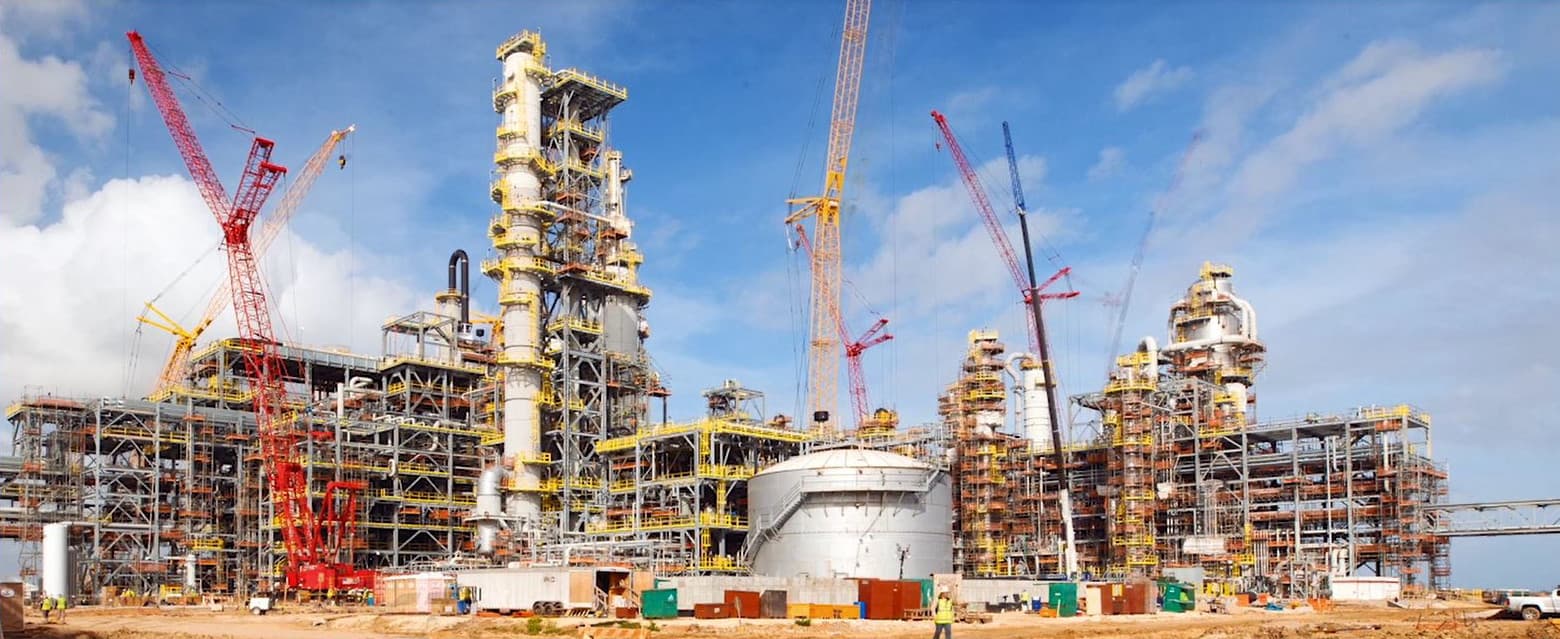
Fluor is providing mechanical construction of a new world-scale monoethylene glycol (MEG) manufacturing facility at its Oyster Creek site near Freeport, Texas. The new Oyster Creek MEG facility is owned by MEGlobal and represents MEGlobal’s first unit in the United States. Mechanical construction is expected to be complete mid-2019.
2020s
2020 and beyond.
2020
Fluor joint venture achieves final provisional turnover for KNPC Clean Fuels Project facilities
&w=3840&q=75)
2020: Fluor joint venture achieves final provisional turnover for KNPC Clean Fuels Project facilities
&w=3840&q=75)
In August 2020, Fluor announced that its joint venture with Daewoo Engineering & Construction and Hyundai Heavy Industries successfully achieved final provisional turnover of the facilities for Kuwait National Petroleum Company’s (KNPC) Mina Abdullah Package 2 (MAB2) Clean Fuels Project in southern Kuwait. This significant milestone marks the completion and successful handover of MAB2 facilities to KNPC.
2020
MEGlobal project named Project of the Year by Engineering News-Record
&w=3840&q=75)
2020: MEGlobal project named Project of the Year by Engineering News-Record
&w=3840&q=75)
In 2020, MEGlobal’s 750,000 metric-ton-per-annum monoethylene glycol and di-ethylene glycol facility was named Energy/Industrial Project of the Year for the Texas and Louisiana region by Engineering News-Record. Fluor served as construction contractor on the project. The project was completed safely, ahead of schedule and under budget and began operations in October 2019.