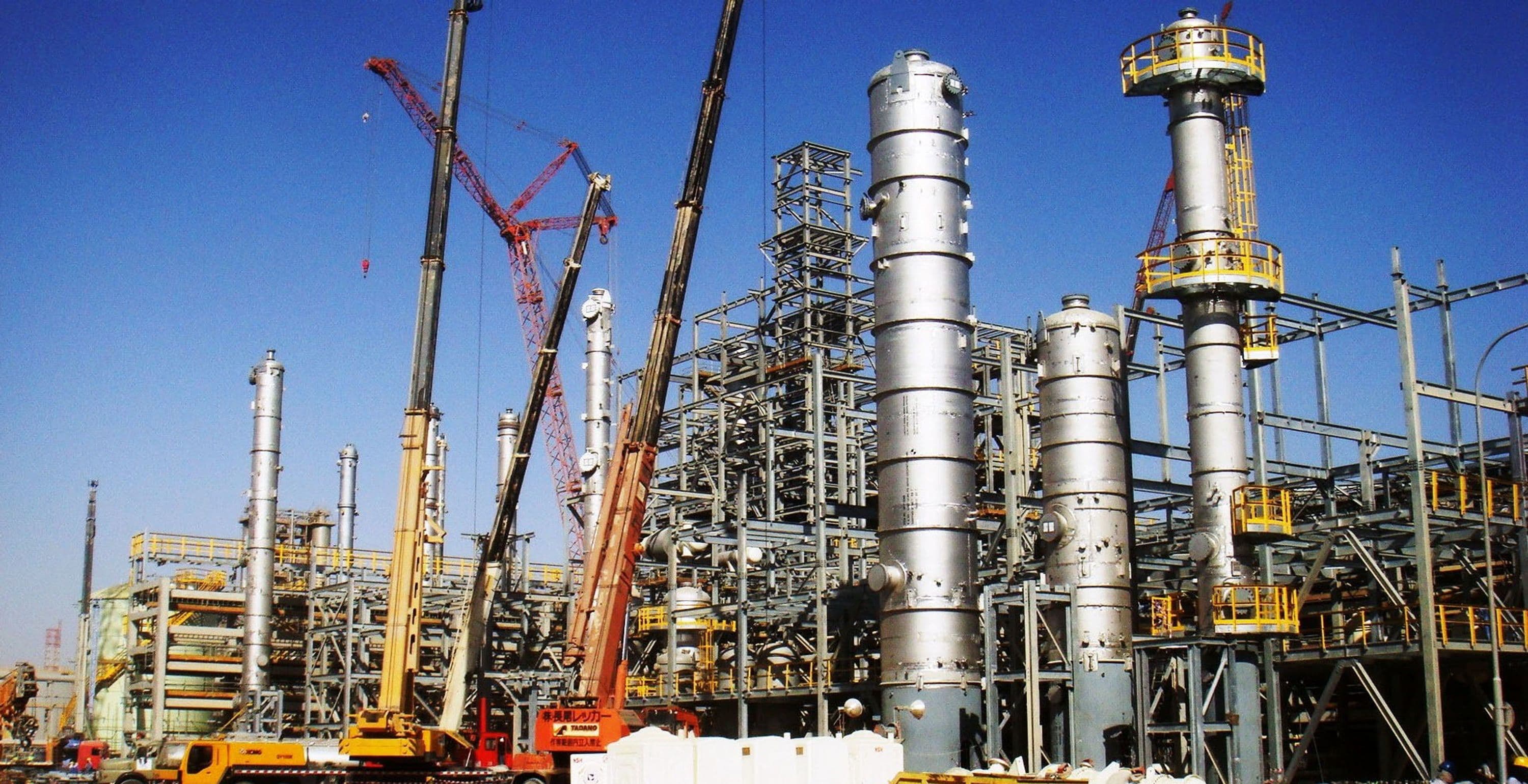
Jubail Acetyls Complex

Executive Summary
Fluor performed engineering, procurement, construction management and precommissioning for the acetic acid (AA), vinyl acetate monomer (VAM) and associated utilities plants for this $1.8 billion project. We also managed the general construction contractor, onsite tankage contractor and other owner's contractors onsite.
In 2009, despite the extremely hot weather conditions on site during construction this Sipchem project achieved 10 million safe work hours. This was a world-class achievement, particularly considering the different contractors that were involved, the complexity and organization of the work and the extreme environmental conditions during which construction and precommissioning activities were conducted.
This safety milestone was achieved with the development and continual improvement of safety habits by Sipchem, Fluor and the JAC Project contractors. The JAC Project was made up of contractors representing six continents speaking 12 languages who collectively and successfully met the challenge to foster a health, safety, security and environment (HSSE) culture to achieve an incident-free workplace.
Client's Challenge
Saudi International Petrochemical Company (Sipchem) is a Saudi joint stock company founded in 1999 with current paid-in capital of $978 million. Its shareholders are leading corporate organizations and investors in the Gulf Cooperation Council region and the Saudi public. The estimated overall value of the acetyls complex was $1.8 billion, which included a carbon monoxide plant, port and other infrastructure facilities.
The project was the second phase of the Sipchem Complex development at Jubail Industrial City, adding CO, AA and VAM plants and additional support Utilities.
The plant for VAM, a high-end specialty plastic using DuPont technology, has a capacity of 330,000 metric tonnes per annum (MTPA), and the AA plant, using Eastman technology, has a capacity of 400,000 MTPA acetic acid and 50 MTPA acetic anhydride. The utilities plant provides new utilities to supply the complex, including cooling water, steam generation, interconnecting pipe racks, wastewater treatment and other utility systems.
The Acetyls Complex project also included a new carbon monoxide production plant, with the world's largest capacity, to provide feedstock to the Acetic Acid Plant and port facilities at King Fahd Industrial Port. This work was performed by others under separate contracts.
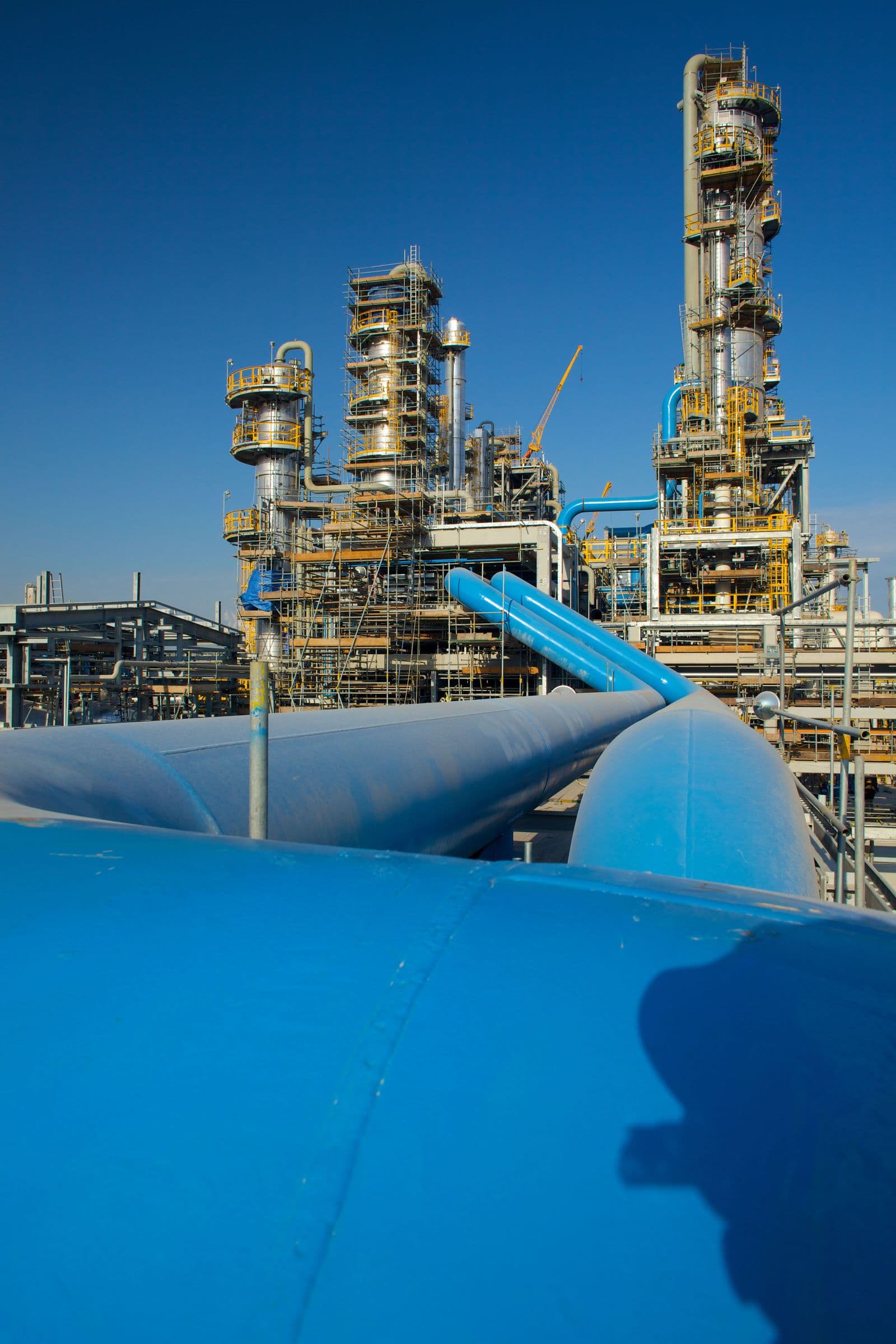
Fluor's Solution
Foster Wheeler was responsible for the front0end engineering and design (FEED) package of the JAC project. Fluor was originally responsible to develop the FEED package into an open book, lump sum conversion proposal. However, Sipchem subsequently decided to continue with the project on a cost reimbursable basis using the engineering, procurement and construction management services approach.
We provided a team of construction management professionals that grew to over 200 strong in order to manage the local construction contractor building three process units under a work unit rate contract, The project was supported by our home office personnel who provided the detailed design and procurement from three different offices in Calgary, Greenville and New Delhi.
Construction was executed by a local contractor and managed by a combined Sipchem/Fluor team. The construction workforce peaked between 3,500 to 4,000 personnel.
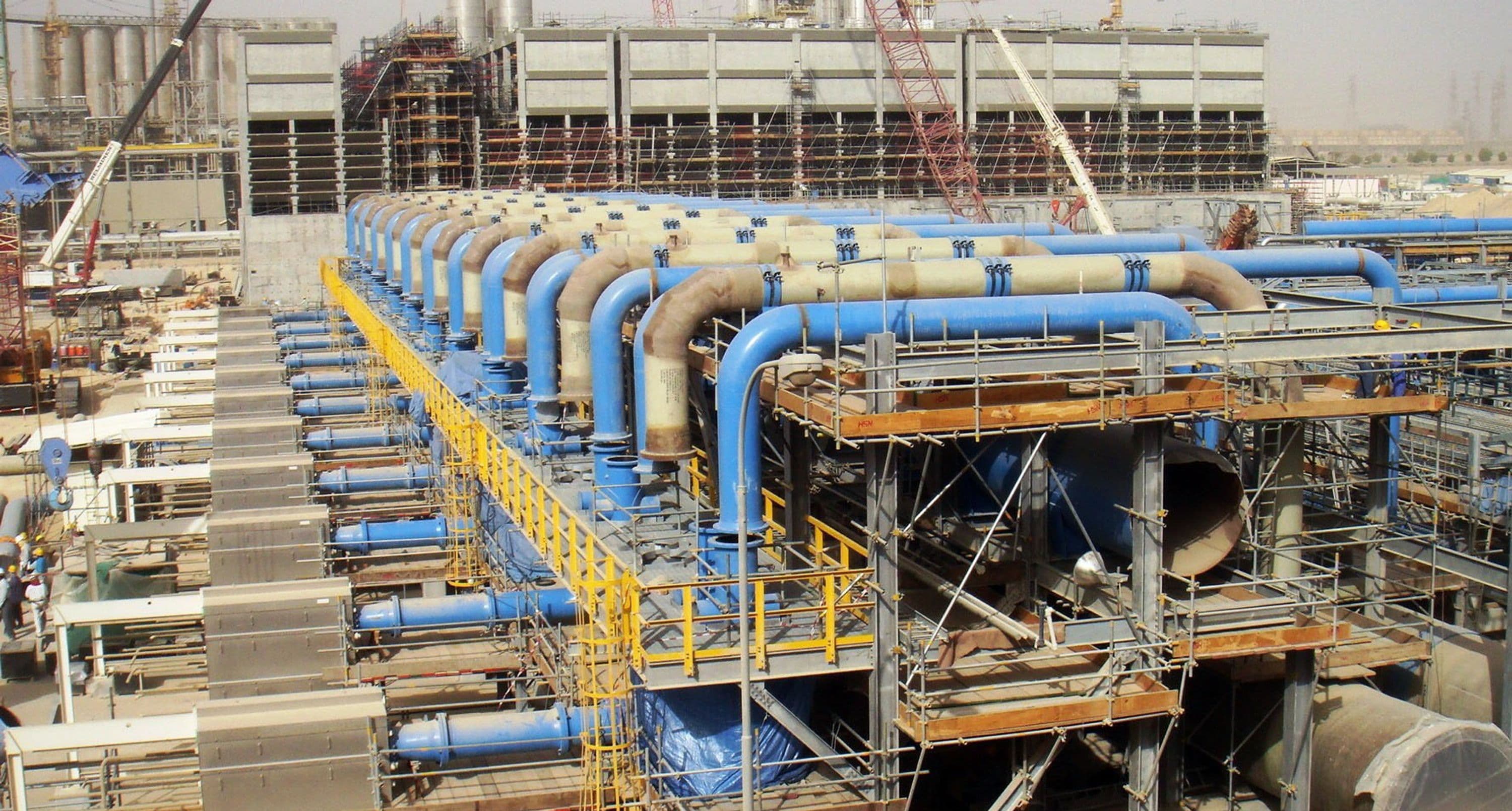
Conclusion
In late 2009, Sipchem sent its first acetic acid commercial shipment to Asia through the King Fahd Industrial Port.
In January 2010, Sipchem sent its first shipment of vinyl acetate monomer (VAM) to the European markets through King Fahd Industrial Port.
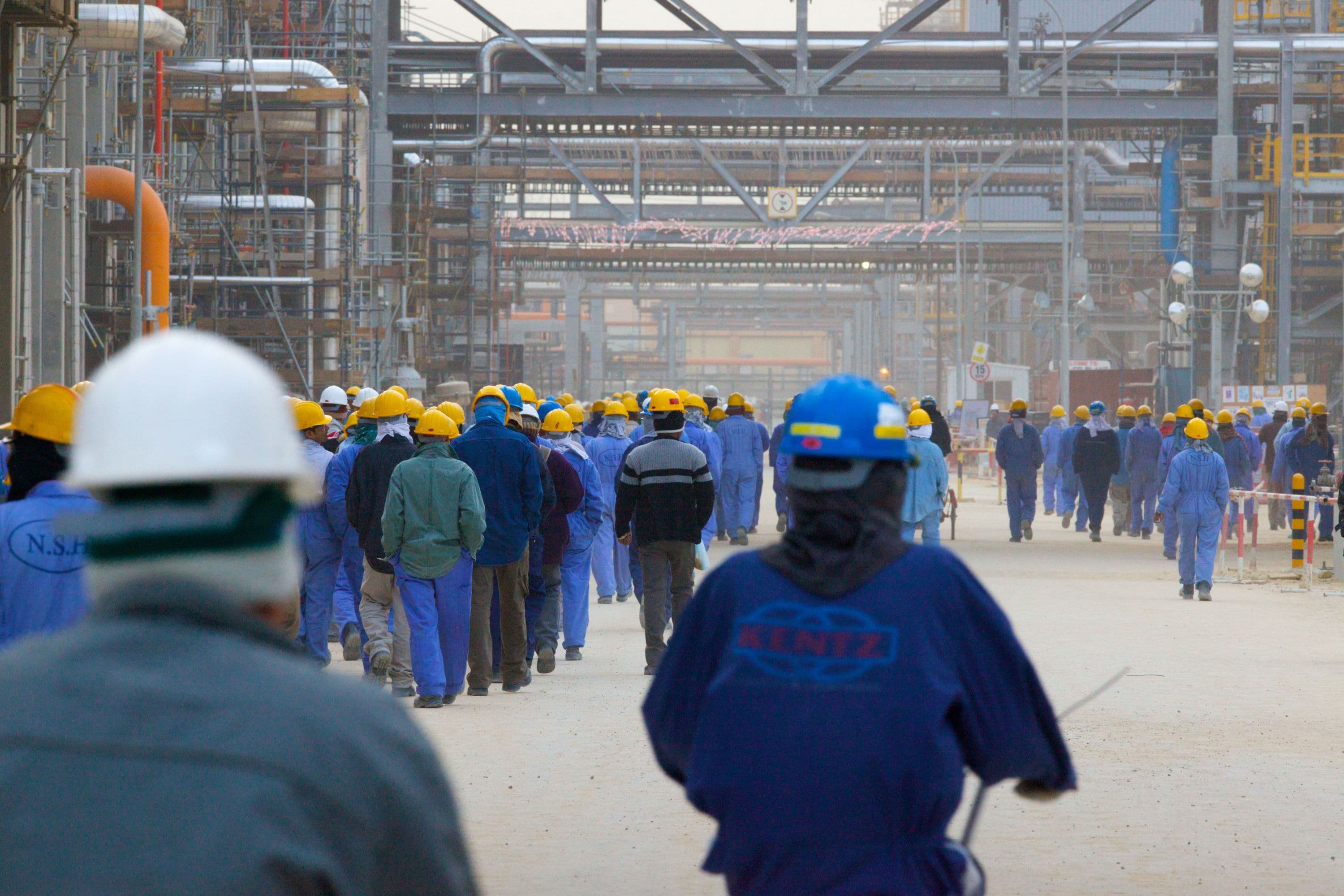