Life Sciences Timeline
Building a Better World With Life Sciences
For over 50 years, Fluor has designed, built and validated more than 1,000 life sciences projects, ranging from pilot plants and labs to critical commercial manufacturing facilities. Clients include developers and producers of drugs, biotherapeutics, vaccines and supplements for humans and animals, ranging from the major international manufacturers to mid-sized and emerging firms.
Project scopes include both conceptual studies and complete engineering, procurement, construction, and validation projects. Fluor's extensive experience in CGMP facility design has resulted in a success rate of 100% in compliant design and construction.
1970s
Fluor enters the Pharmaceutical industry.
1971
Schering Corporation engages Fluor for a series of construction projects in Manati, Puerto Rico
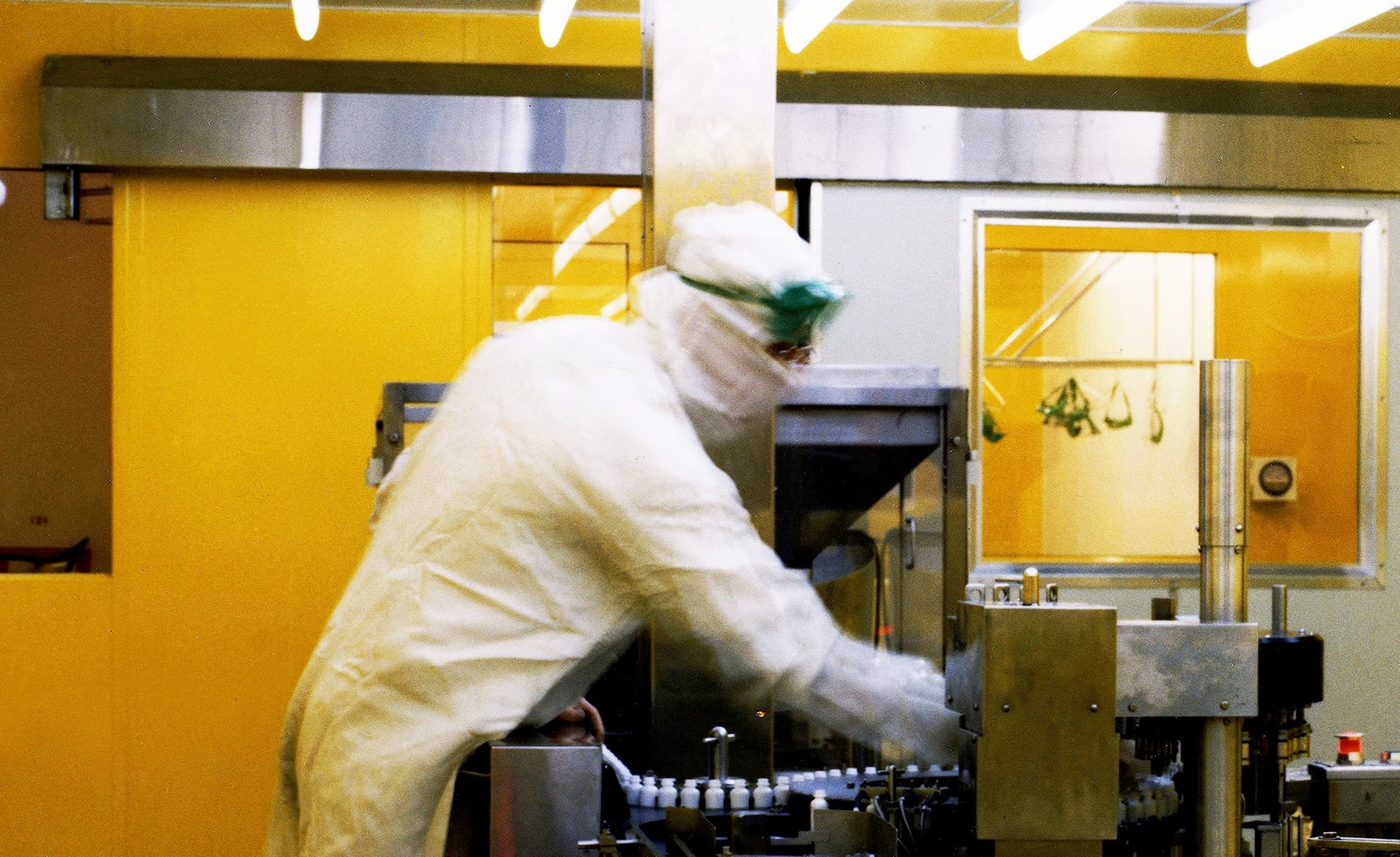
1971: Schering Corporation engages Fluor for a series of construction projects in Manati, Puerto Rico
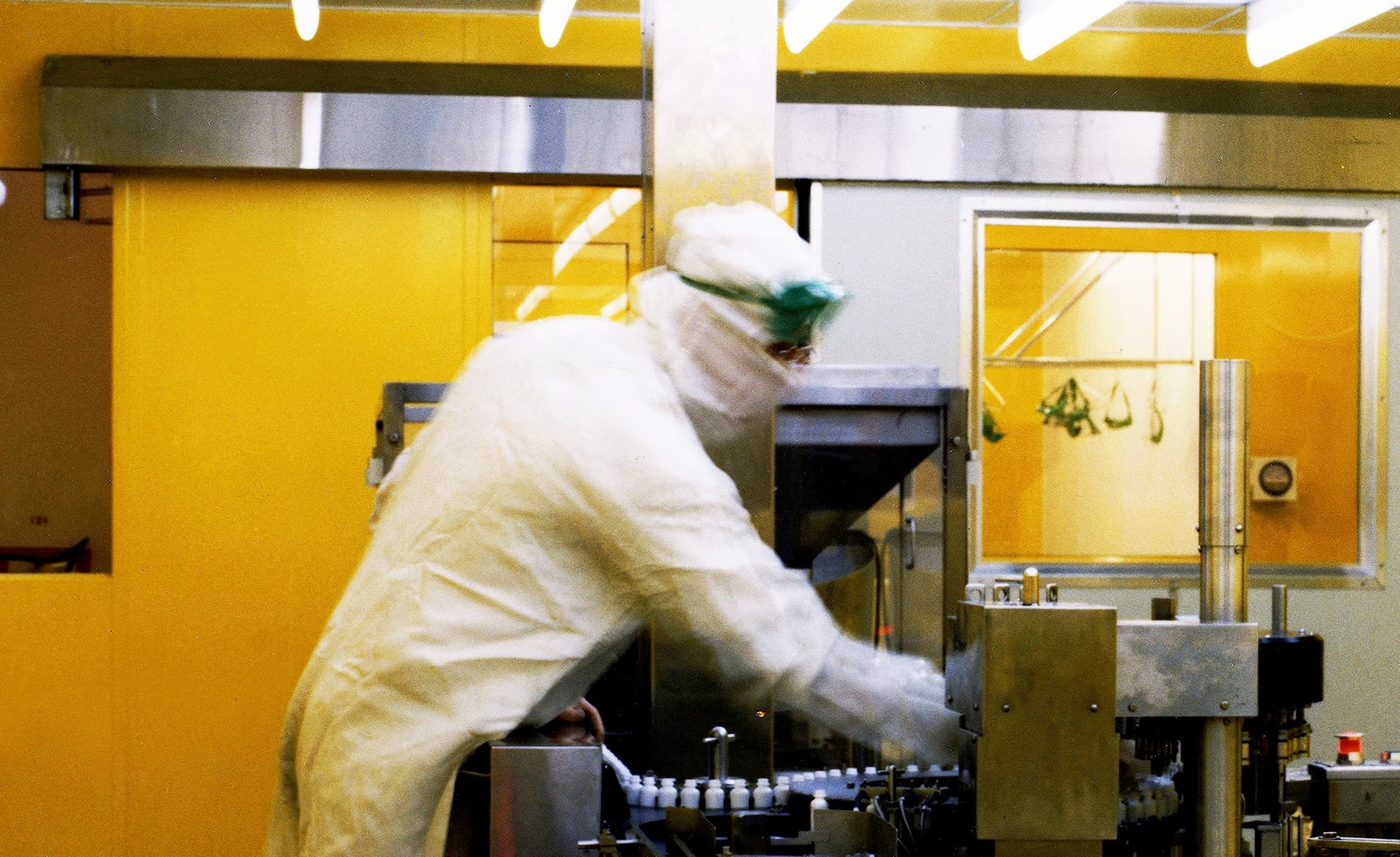
Fluor carried out a series of capital projects totaling approximately $100 million at Schering Corporation's pharmaceutical facilities in Manati, Puerto Rico. The facility manufactured antibiotics and steroid compounds in a variety of forms through fermentation and sterile manufacturing and packaging operations. The original installation consisted of a 215,000-square-foot manufacturing and packaging area, as well as laboratories, warehousing and service facilities.
1980s
Fluor completes first Biotech project.
1980
Fluor designs and builds first commercial biotech facility
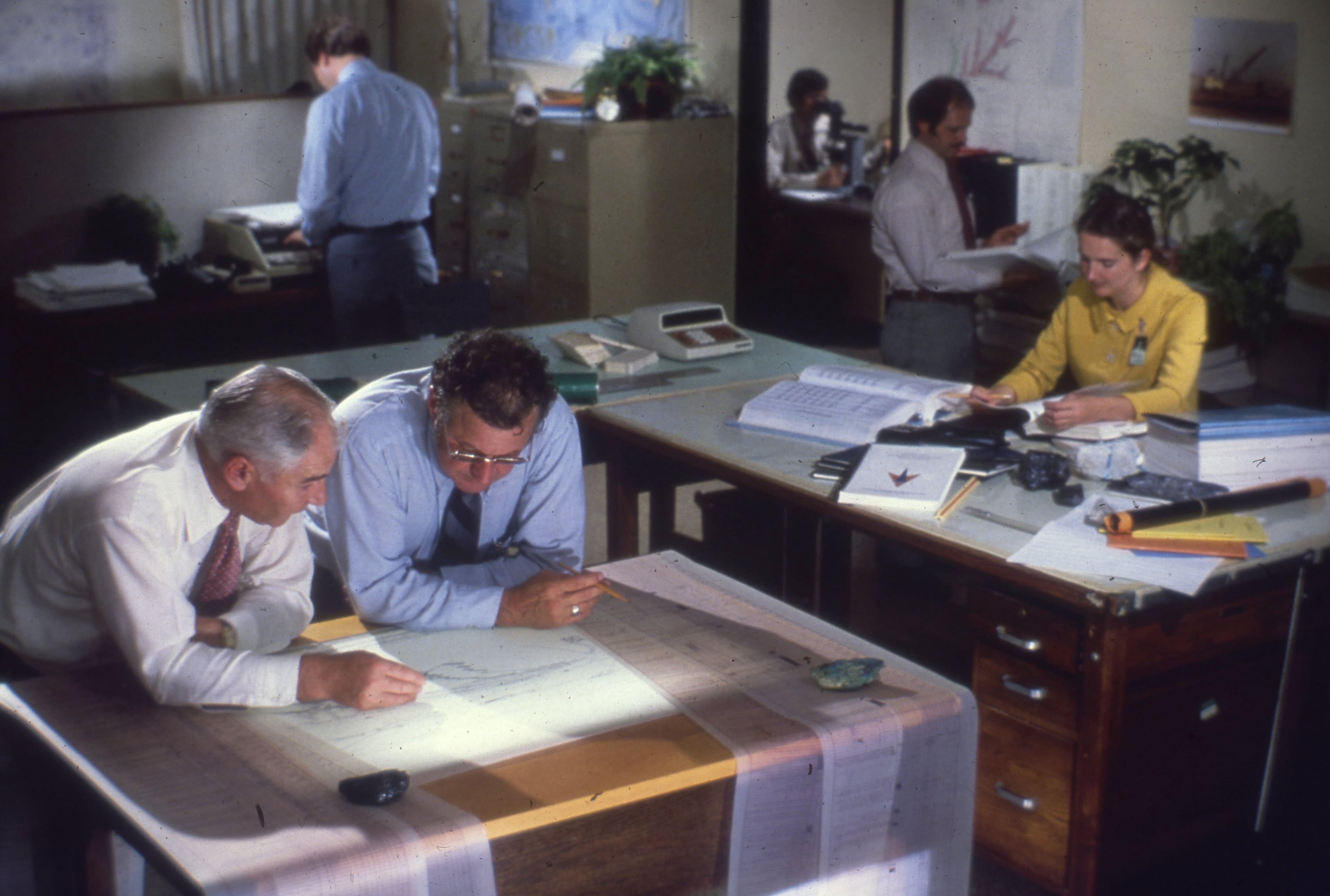
1980: Fluor designs and builds first commercial biotech facility
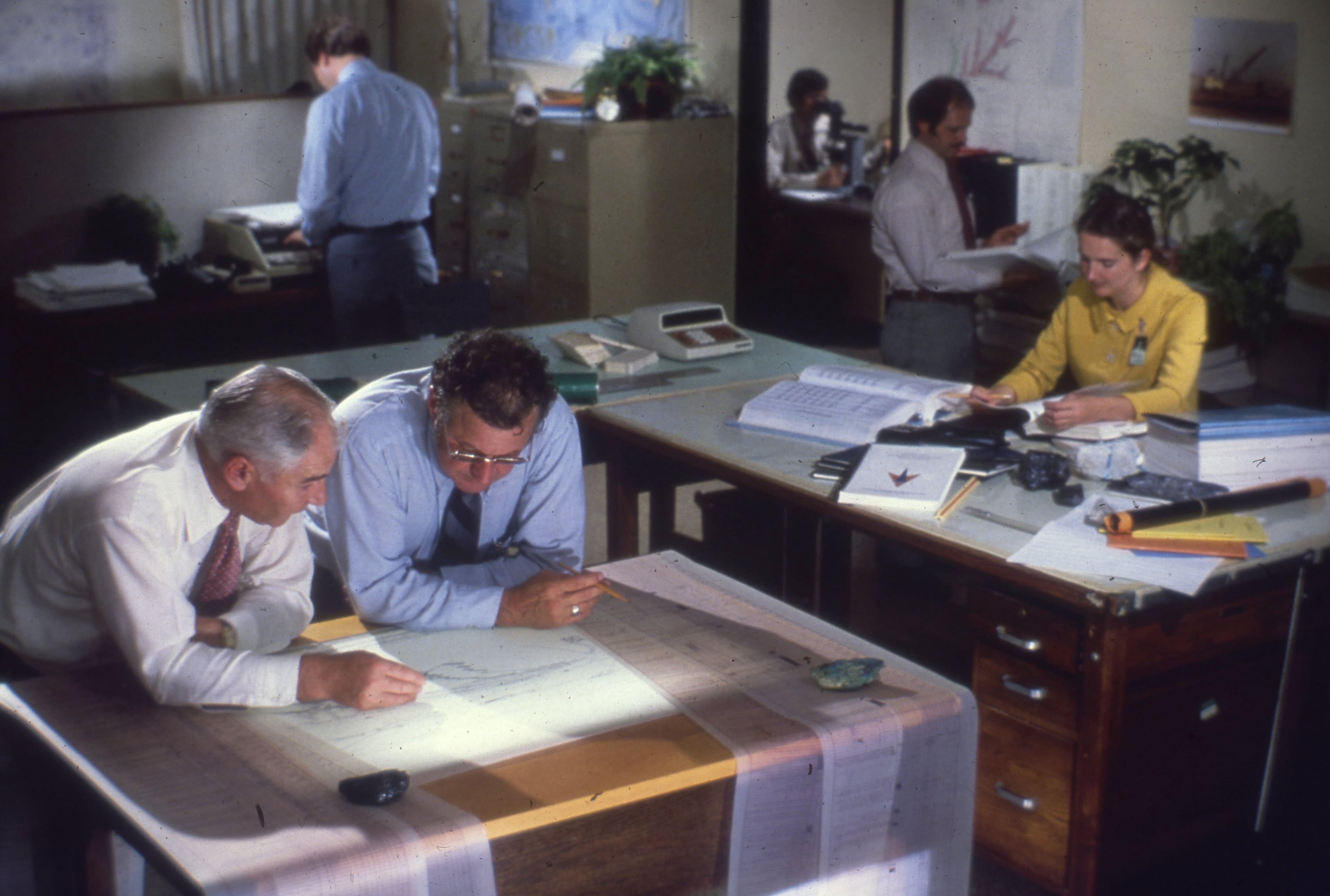
In 1980, Genentech chose Fluor to design and build the first biotechnology scale-up pilot plant, clinical manufacturing and commercial production facility in South San Francisco, California. Fluor began the design of this large-scale, multiproduct, recombinant microbial fermentation facility just as the public was beginning to recognize the potential of the emerging biotechnology industry. Construction was completed in 1983.
1981
A.H. Robins Pharmaceutical Plant in Puerto Rico complete
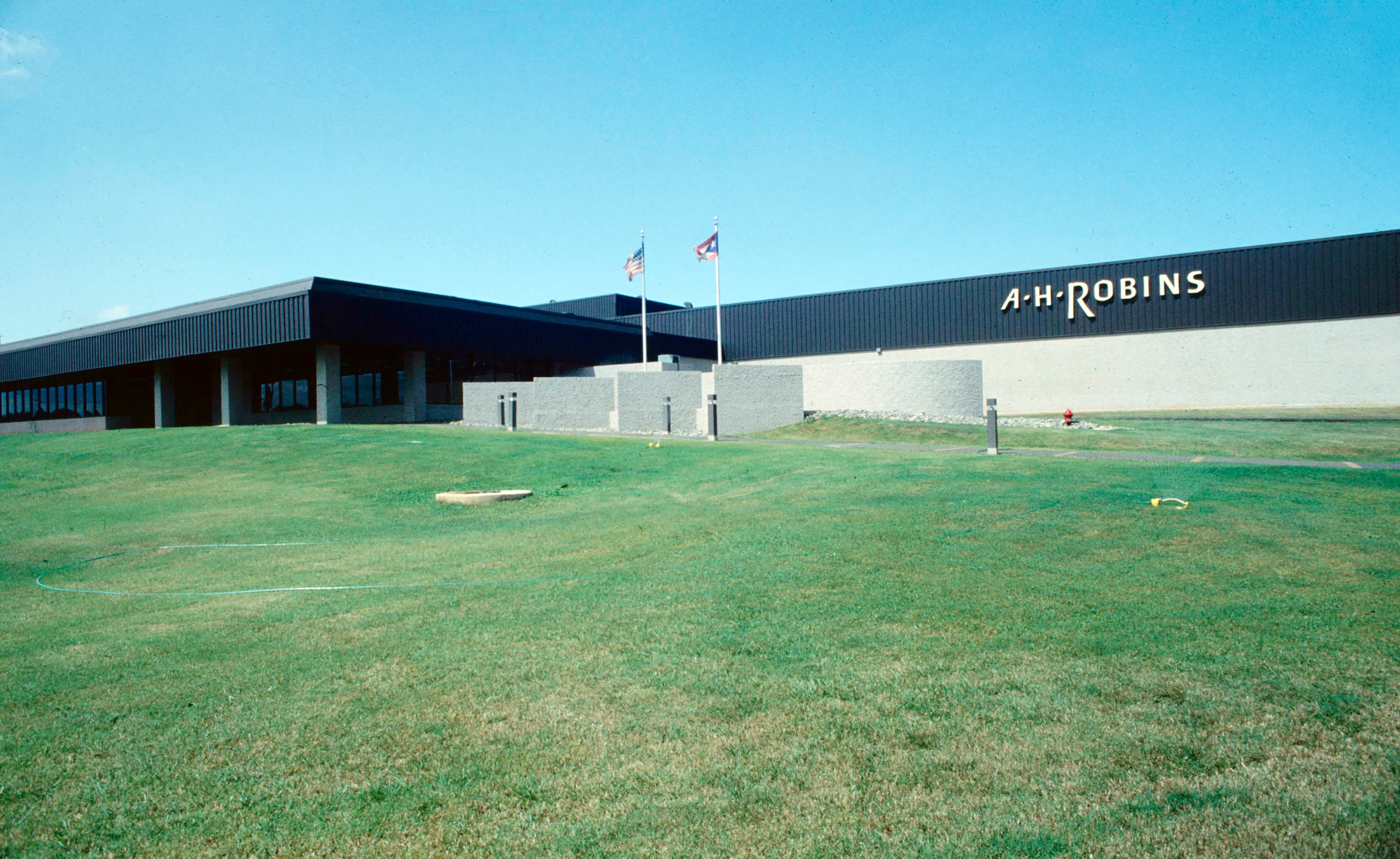
1981: A.H. Robins Pharmaceutical Plant in Puerto Rico complete
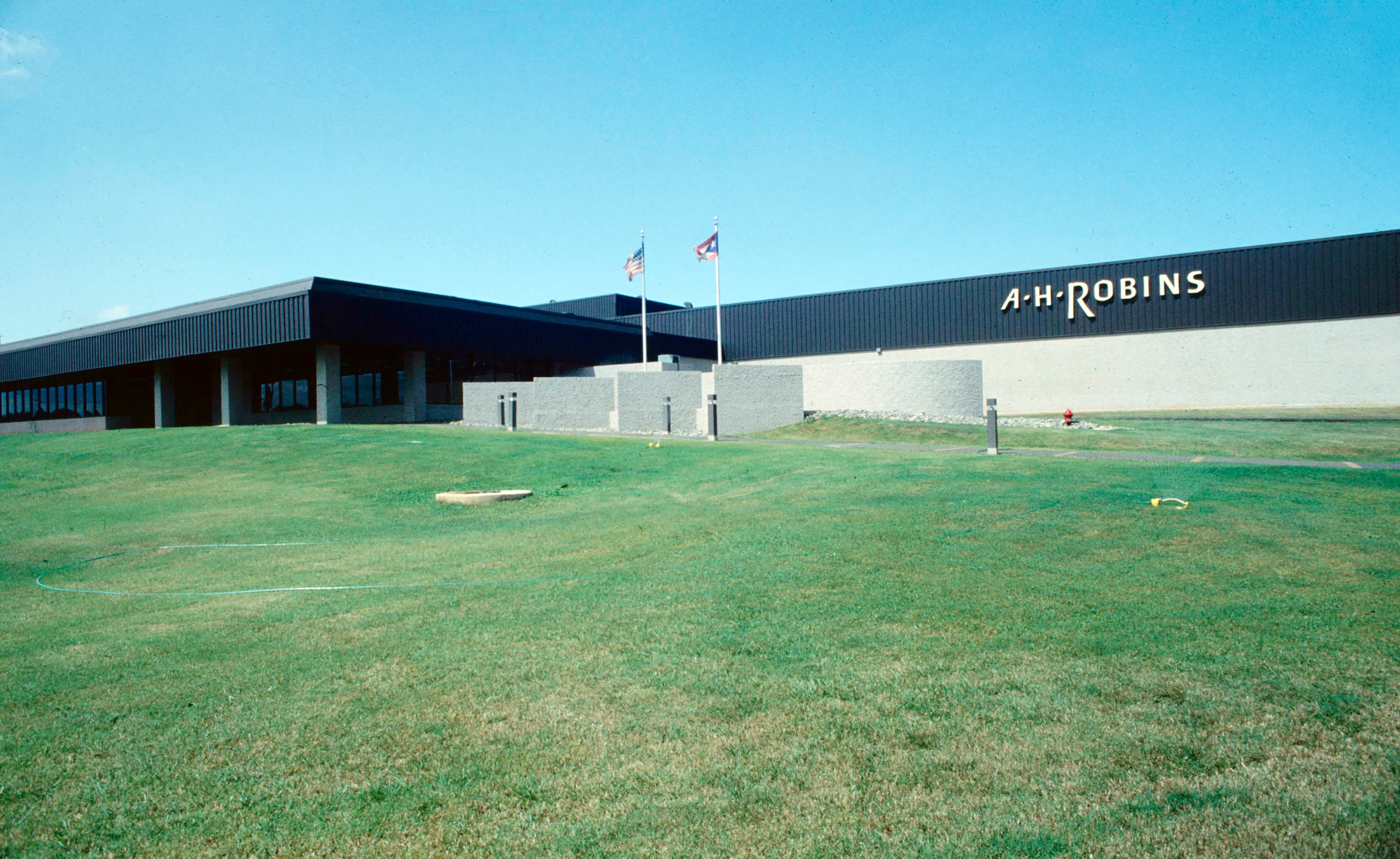
Fluor performed the design, procurement and construction of the A.H. Robins' pharmaceutical plant in Arecibo, Puerto Rico.
1983
Fluor supports the construction of a monoclonal antibodies pilot plant for BioResponse in California
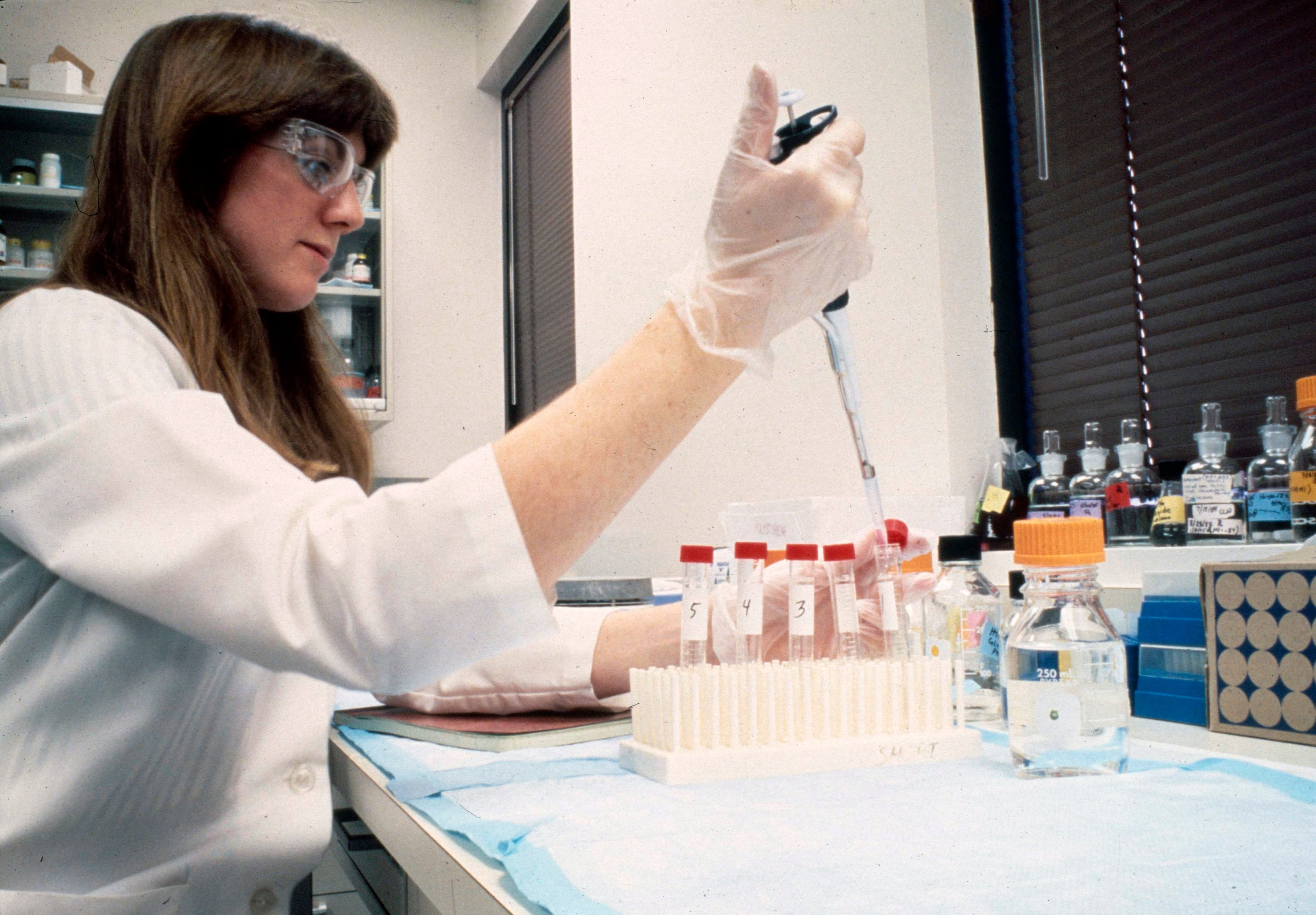
1983: Fluor supports the construction of a monoclonal antibodies pilot plant for BioResponse in California
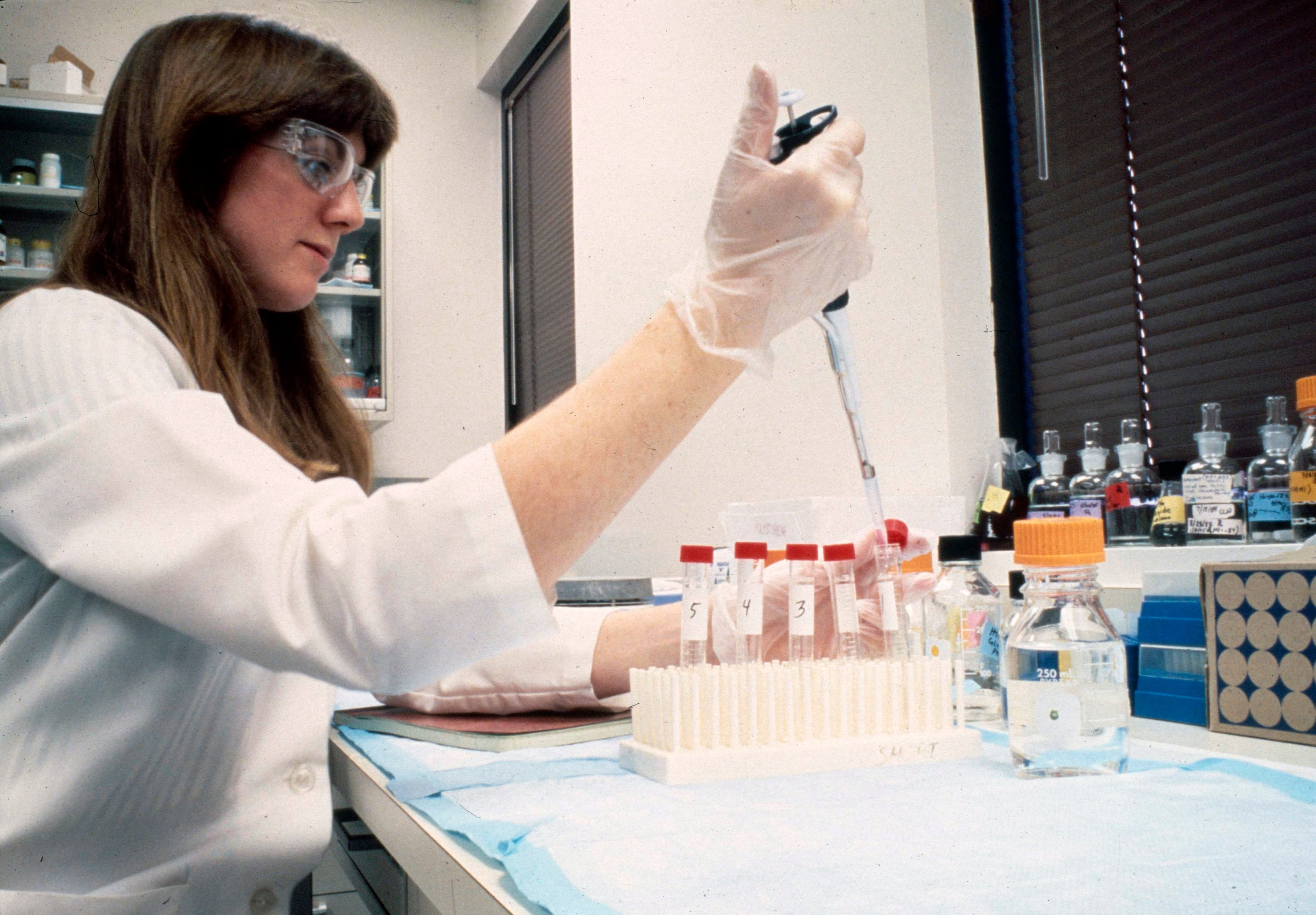
Fluor provided architectural consultation and mechanical/electrical and HVAC support, with limited process and process consulting support for BioResponse's facility. Fluor developed lab arrangements, furnished schedules and specifications and critiqued the overall facility arrangements. Fluor developed the water for injection process, clean steam and other critical utility systems. The facility consisted of offices, labs, animal rooms, cold rooms, special process and controlled product filing rooms, a warehouse and required utilities. The building was designed to meet FDA and NIH requirements while functioning as the client's operations office.
1984
Fluor completes Guayama, Puerto Rico facility modification in 14 months from design to startup
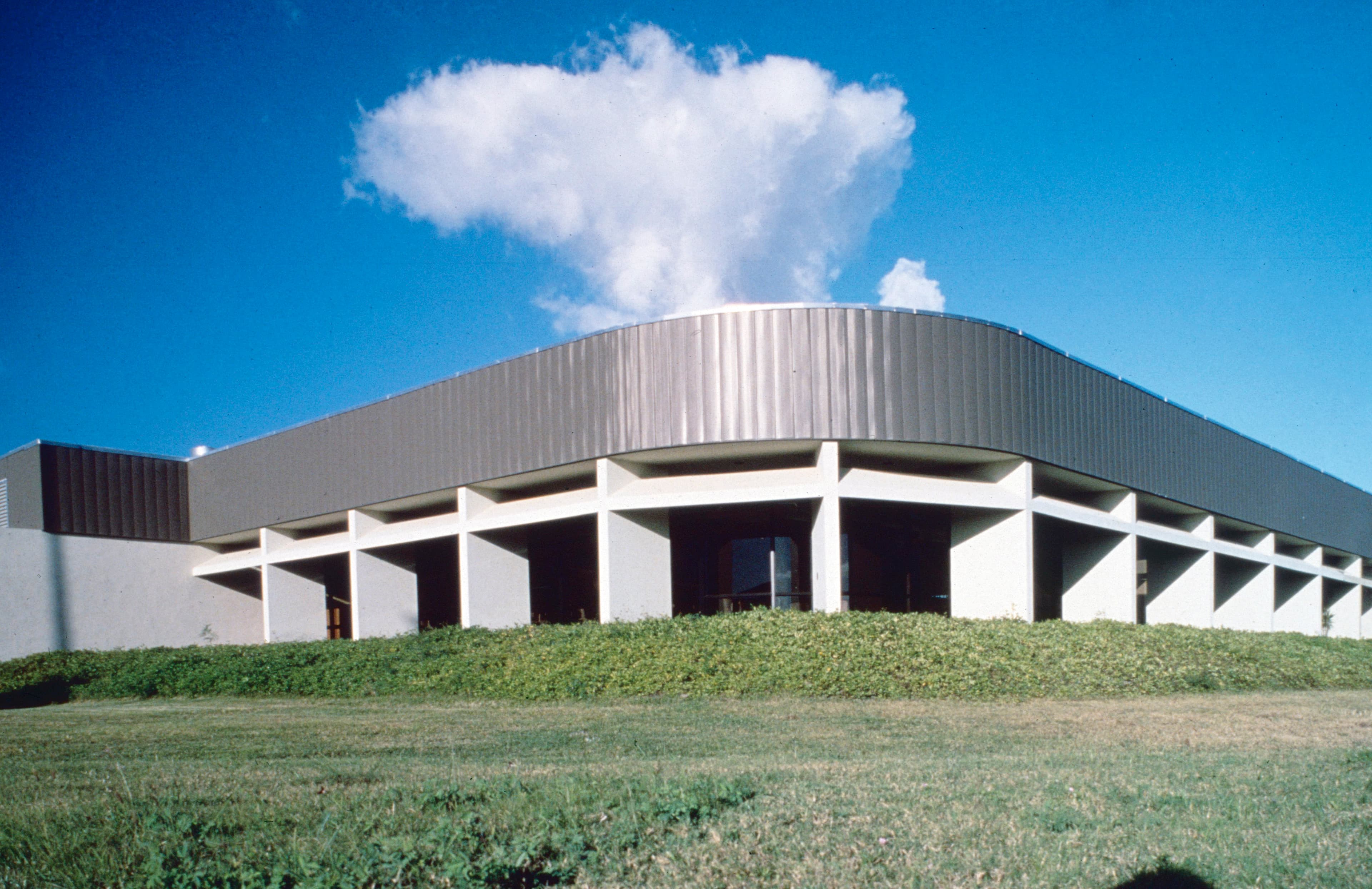
1984: Fluor completes Guayama, Puerto Rico facility modification in 14 months from design to startup
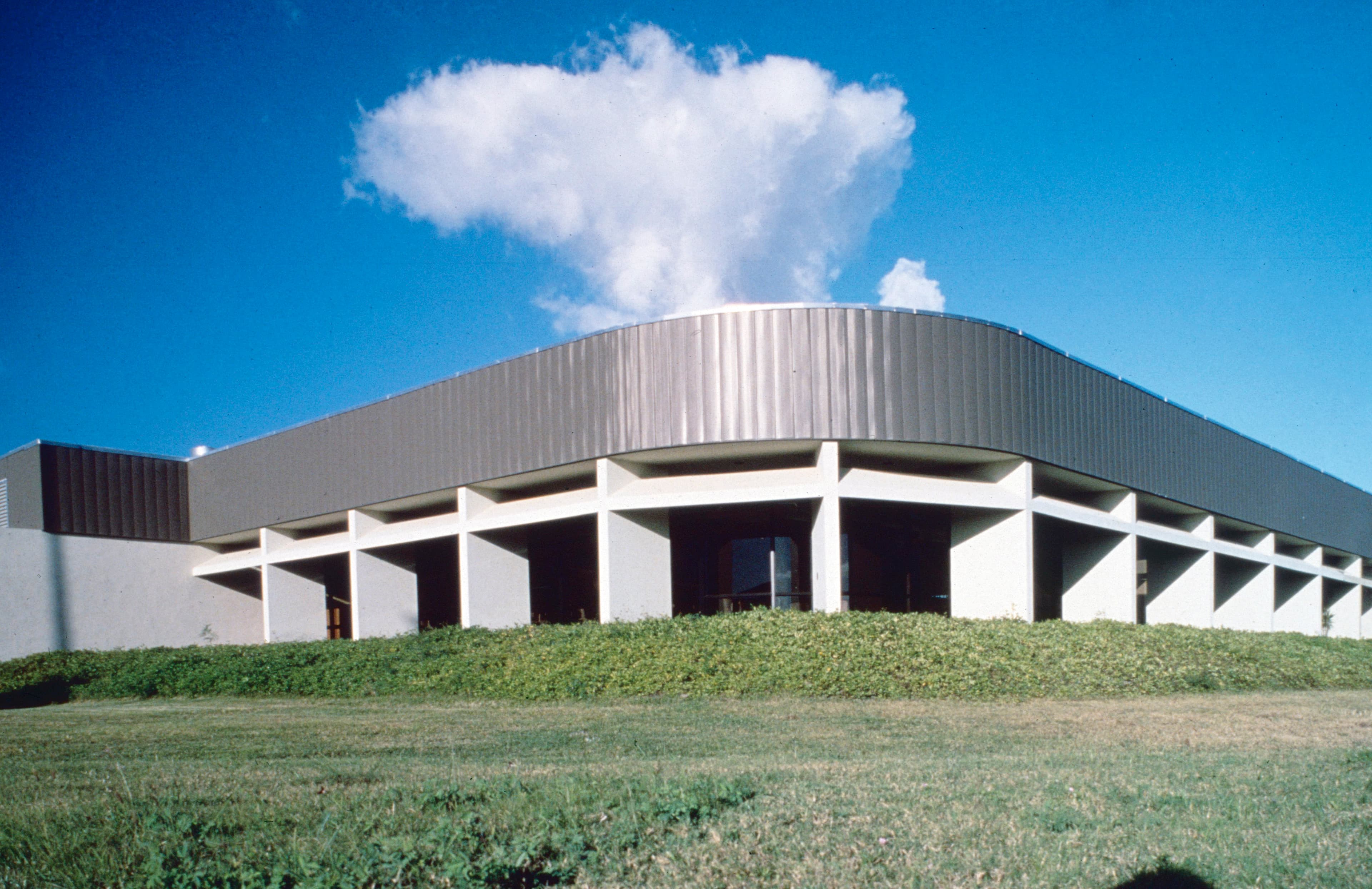
Fluor provided design and construction services to convert one of Puerto Rico's largest existing manufacturing facilities into a pharmaceutical plant for American Home Products Corporation. The former 600,000-square-foot textile plant was modified to produce 17 different pharmaceutical product lines, including tranquilizers, oral contraceptives and anti-hypertensive drugs. The $60 million renovation includes new manufacturing, warehousing, packaging, labeling and process areas. All manufacturing areas are considered clean areas requiring sophisticated airflow and pressurization control.
1984
Upjohn GmbH opens new pharmaceutical complex eight months after groundbreaking
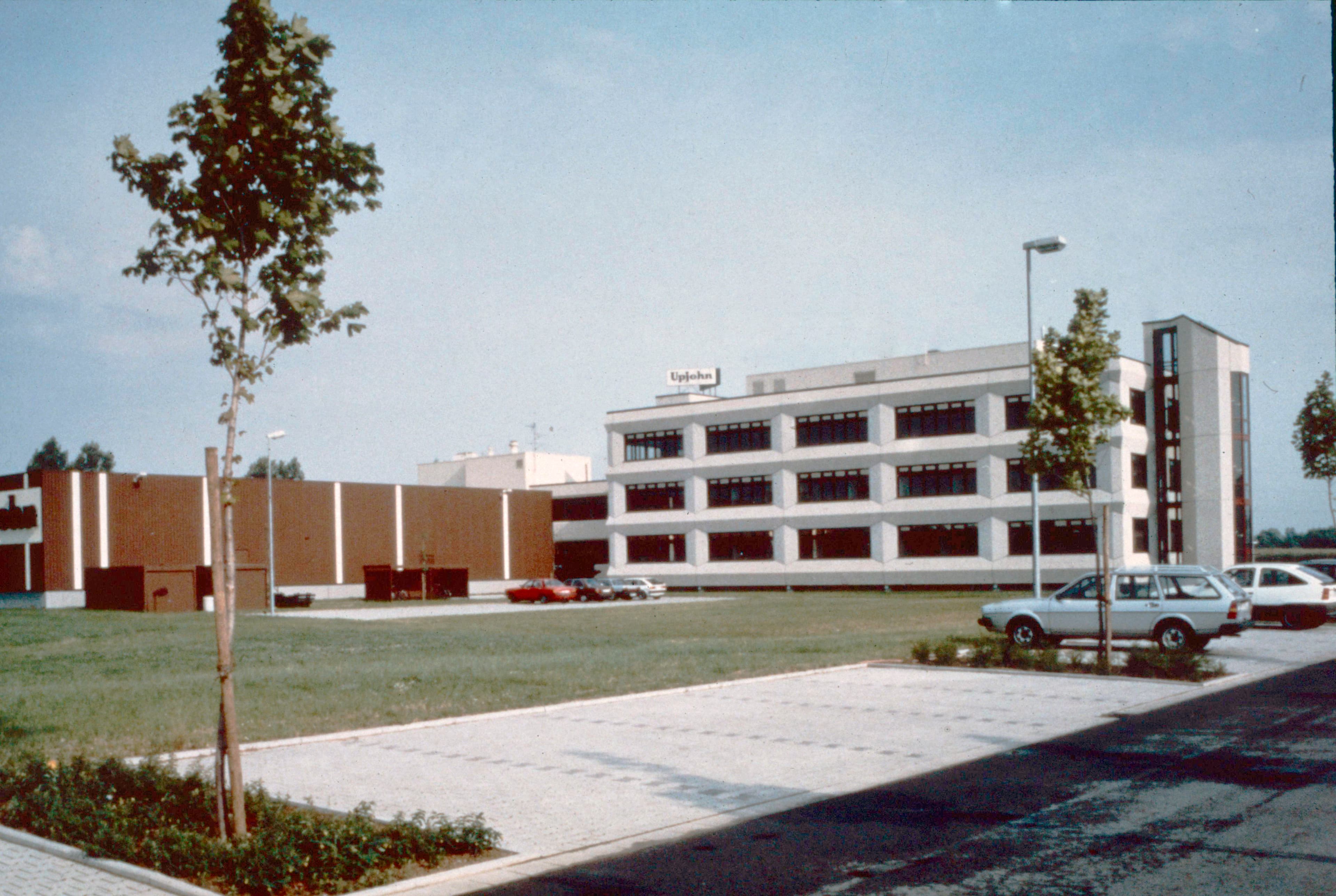
1984: Upjohn GmbH opens new pharmaceutical complex eight months after groundbreaking
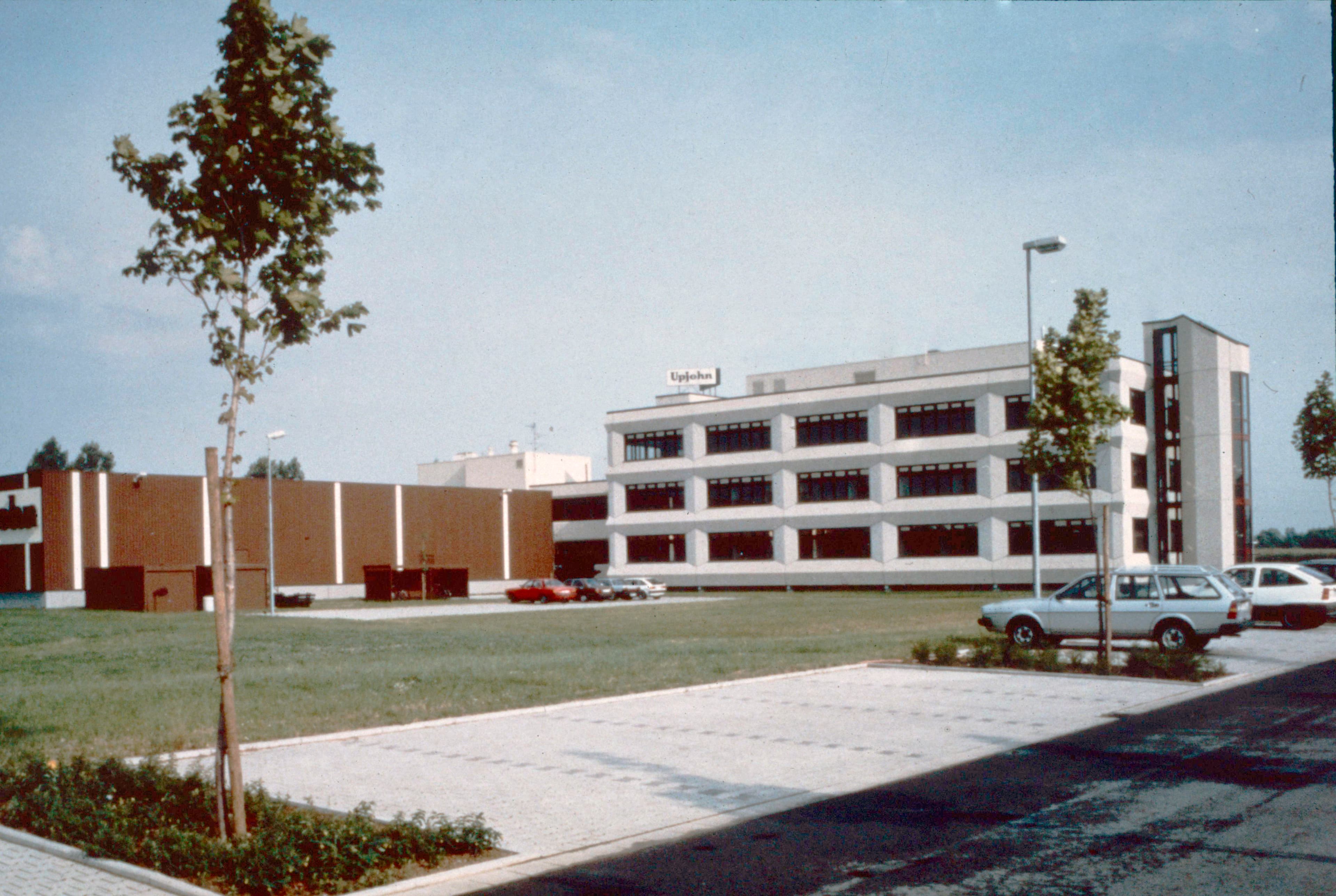
Fluor was awarded a lump-sum contract for the erection of a new office building and the remodeling of an existing warehouse by Upjohn GmbH at Heppenheim in West Germany. The project scope included 1,950 square meters of offices on the third floor and a penthouse to accommodate all mechanical equipment. As general contractor, Fluor was also responsible for procurement and expediting in conjunction with the client's local and American management. The project was completed and occupied by the client within eight months of breaking ground.
1985
Fluor contracts to provide maintenance services to Pfizer
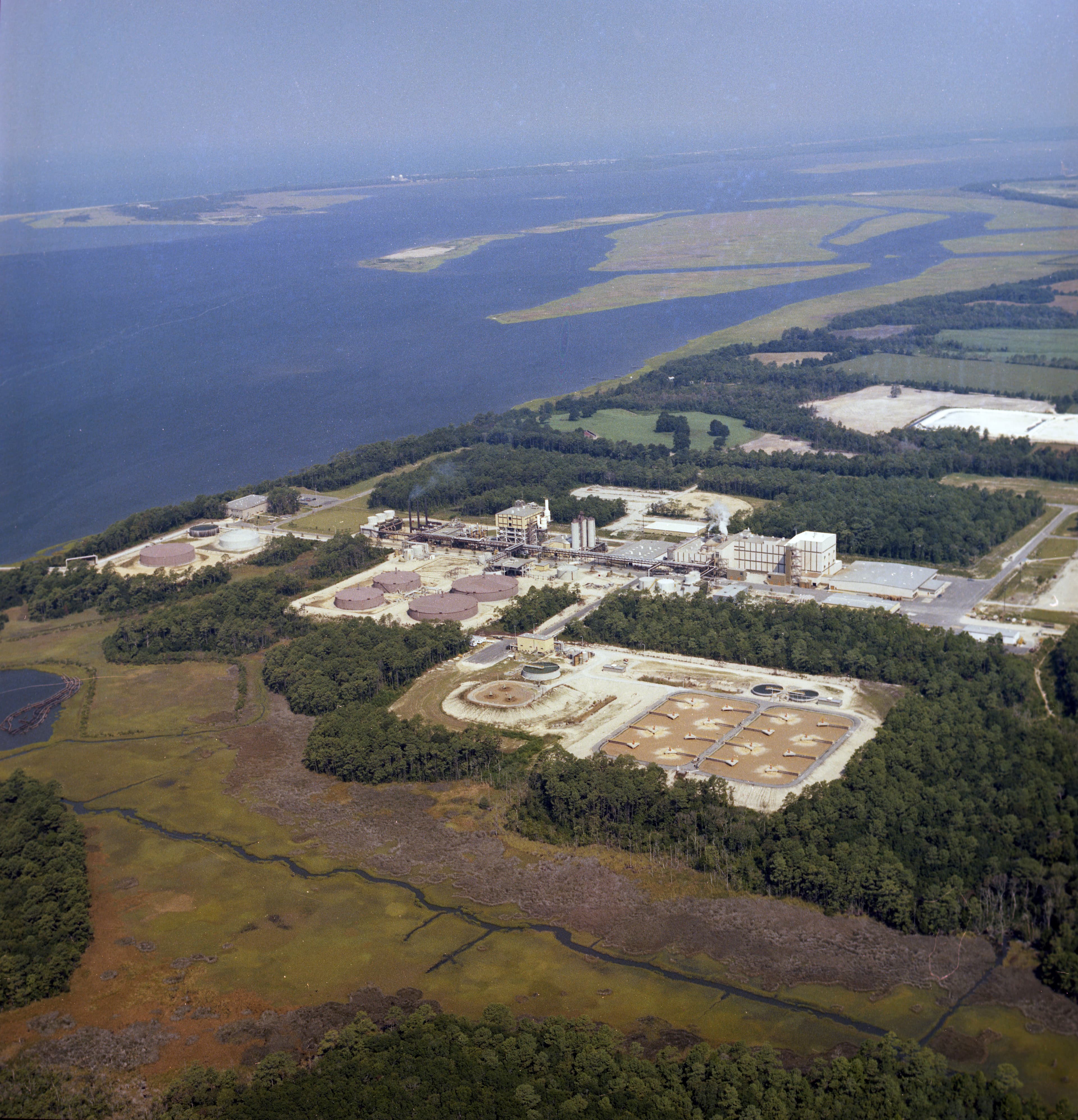
1985: Fluor contracts to provide maintenance services to Pfizer
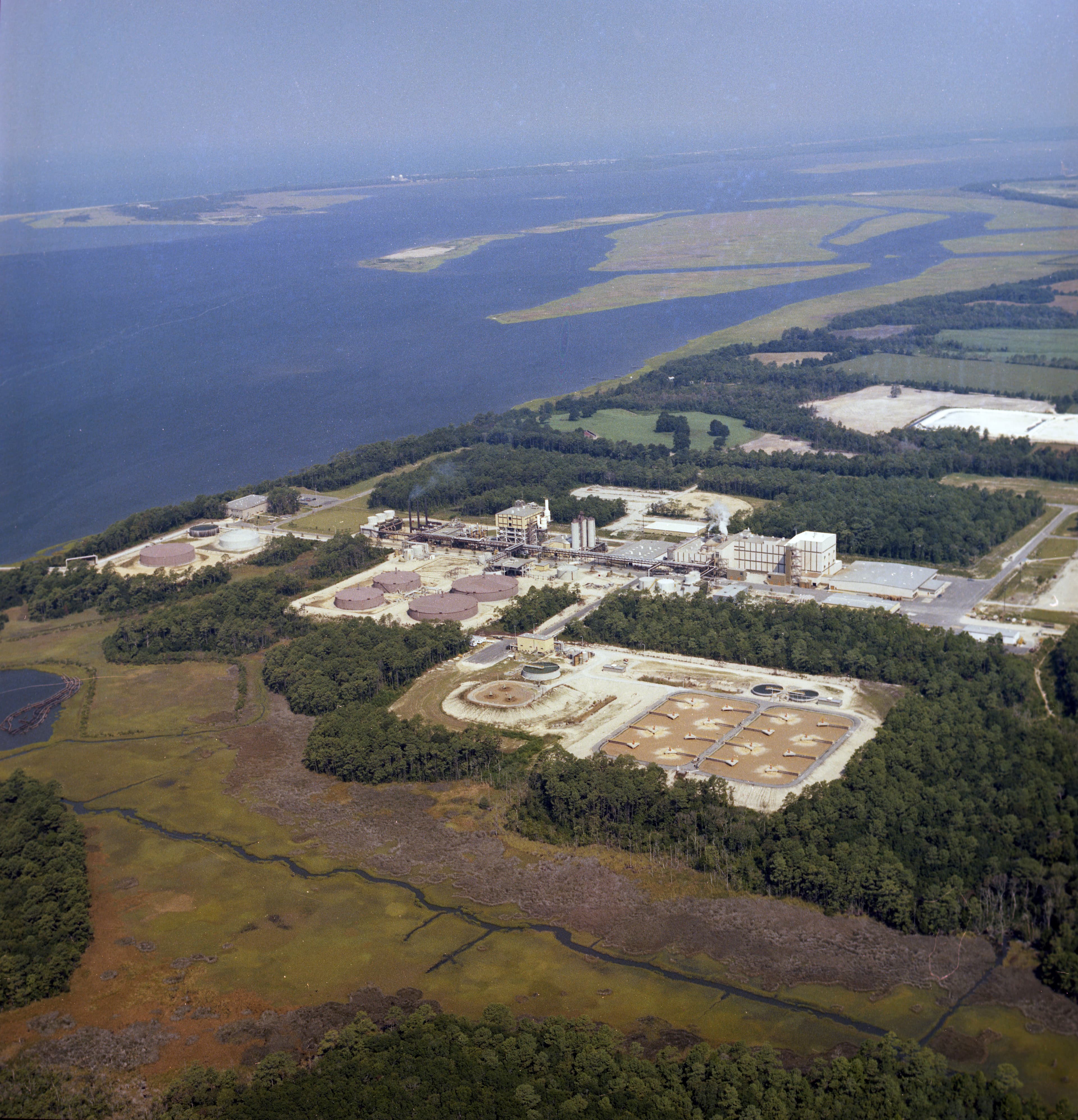
Pfizer selected Fluor as their maintenance provider at the Southport, North Carolina Citric Acid Facility from 1985 - 1990.
1986
Ajinomoto produces amino acids through large scale fermentation
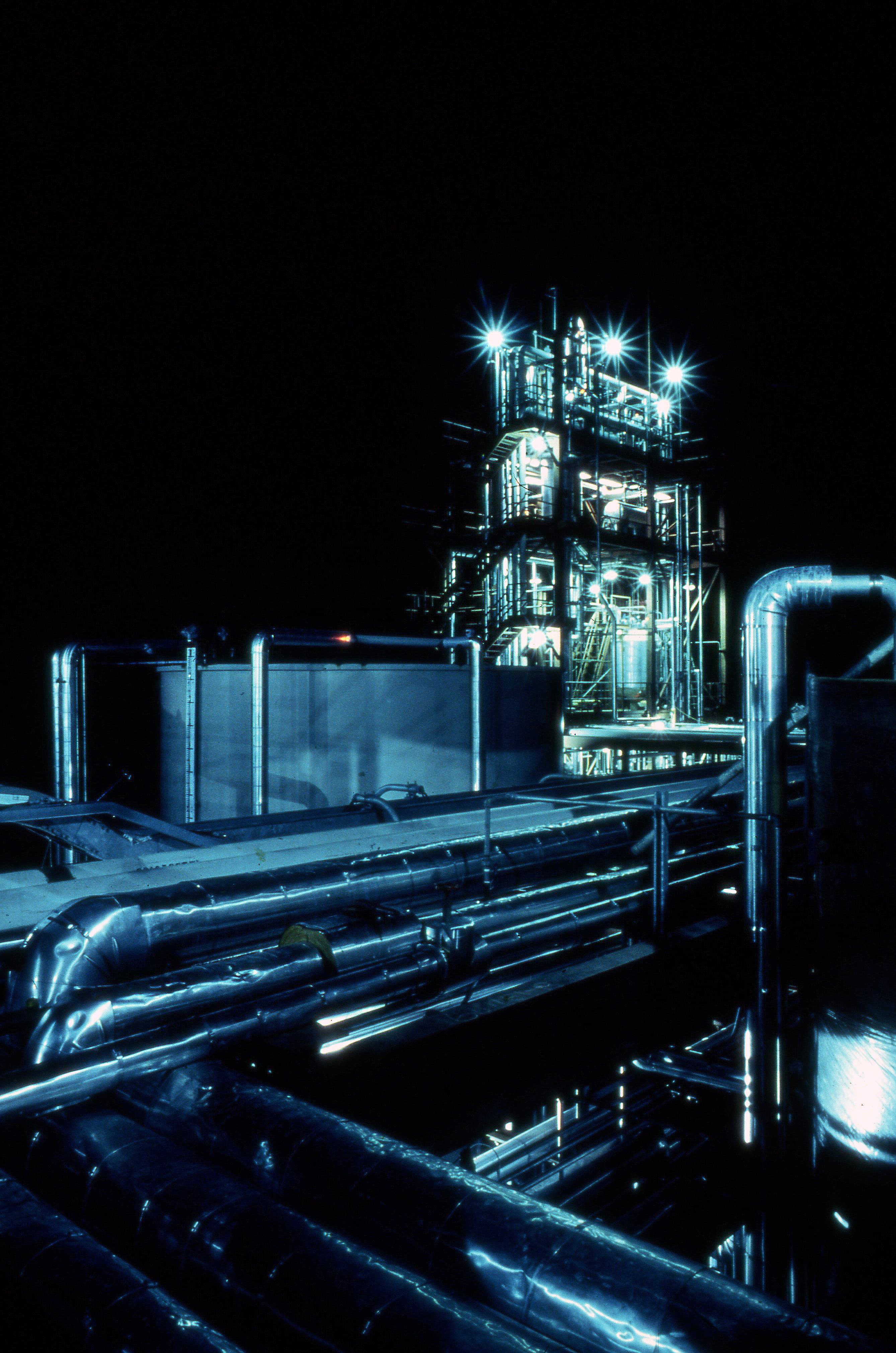
1986: Ajinomoto produces amino acids through large scale fermentation
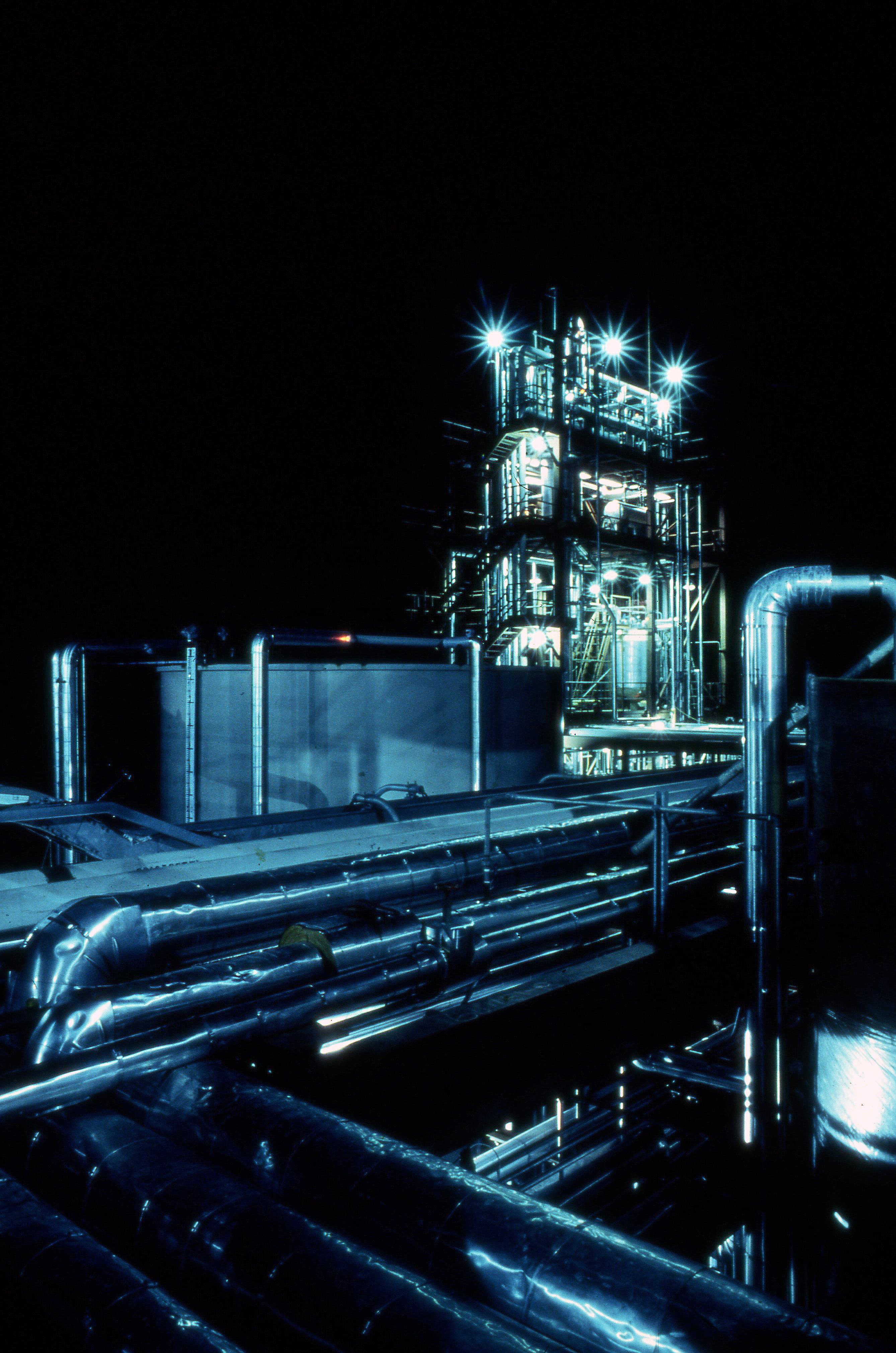
Fluor performed conceptual and detailed design, procurement and construction services for Ajinomoto Company, Inc. at its first amino acids manufacturing facility in the U.S. Fluor and Ajinomoto formed a team that successfully delivered the project ahead of schedule and under budget.
1986
First European commercial biotech facility EPC contract awarded to Fluor
&w=3840&q=75)
1986: First European commercial biotech facility EPC contract awarded to Fluor
&w=3840&q=75)
Fluor was awarded the engineering, procurement, construction management and project management of the greenfield Thomae biotech plant in Biberach, Germany. The large-scale production plant used fermentation technology to produce active pharmaceutical ingredients, e.g., t-PA, a protein capable of dissolving blood clots in the human body.
1986
Fluor begins EPCM contract for Baxter Travenol Laboratories Inc. in Utrecht
1986: Fluor begins EPCM contract for Baxter Travenol Laboratories Inc. in Utrecht
Fluor engineered, procured and managed the construction efforts for Baxter Travenol's warehouse, office and laboratory in Utrecht.
1986
Schering Bulk Pharmaceuticals and Finishing greenfield facility validated
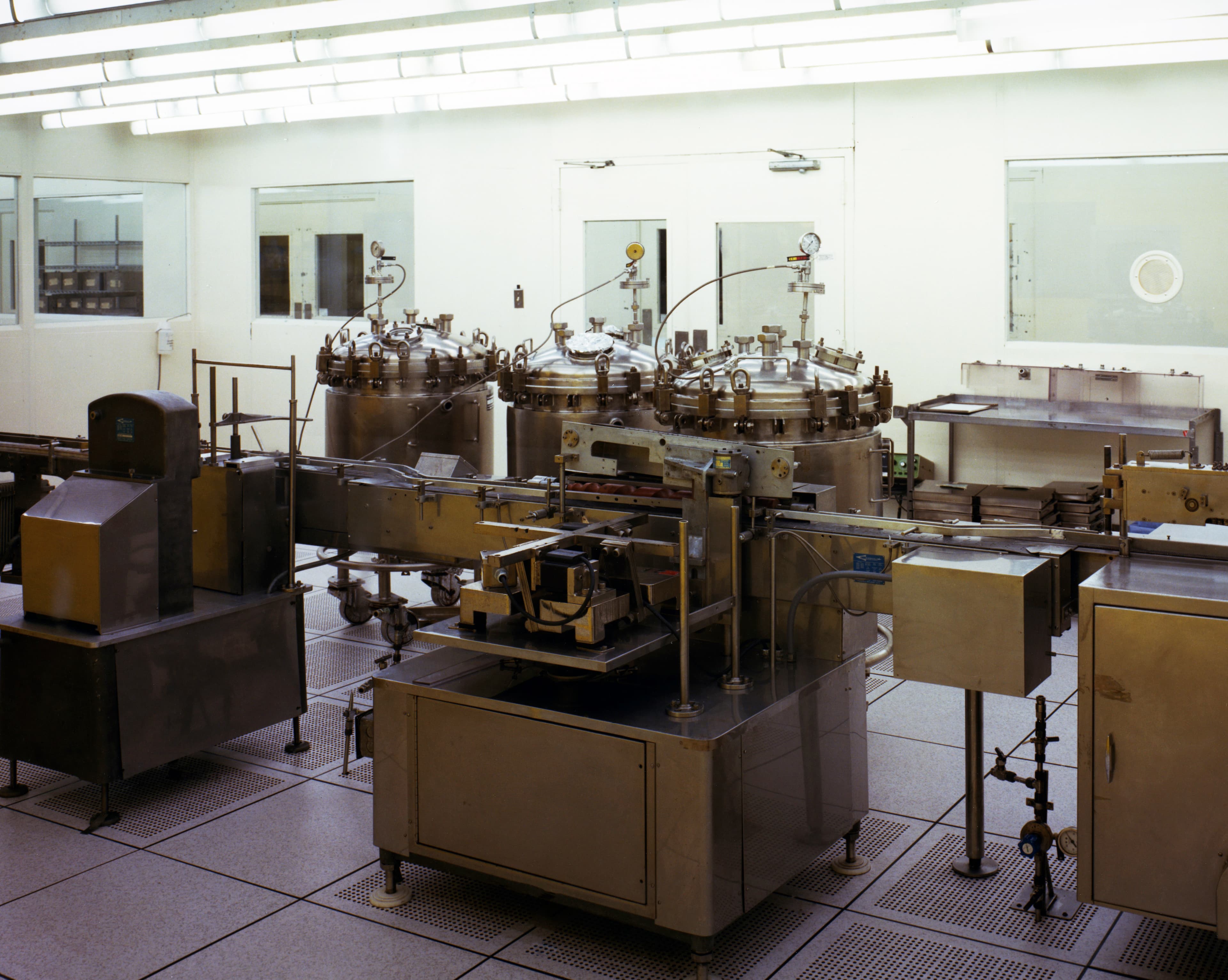
1986: Schering Bulk Pharmaceuticals and Finishing greenfield facility validated
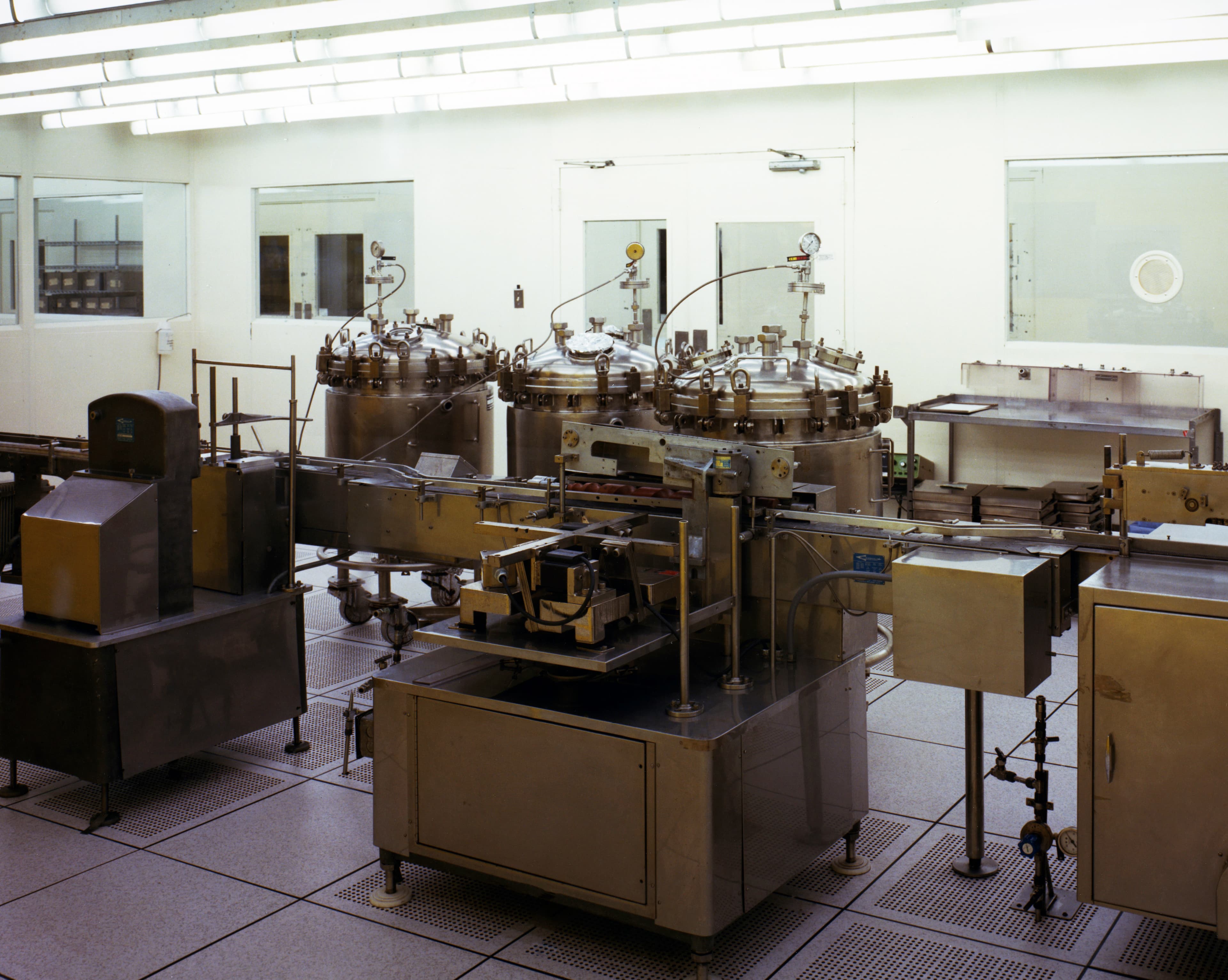
Schering contracted Fluor to provide detailed engineering, procurement, construction, start-up and validation support services for this $55 million greenfield facility. The plant produced antibiotics and dry bulk chemical intermediates in injectable and intravenous, tablet and capsule forms. Full-scale production, packaging, utilities, warehousing, a Class 100 cleanroom and administrative facilities were constructed and governed by special process design considerations for biochemical fermentation, chemical synthesis, chemical solvent recovery, water for injection, clean-in-place, steam-in-place, clean steam, purified water and deionized water.
1987
Suppository packaging area online for Wyeth
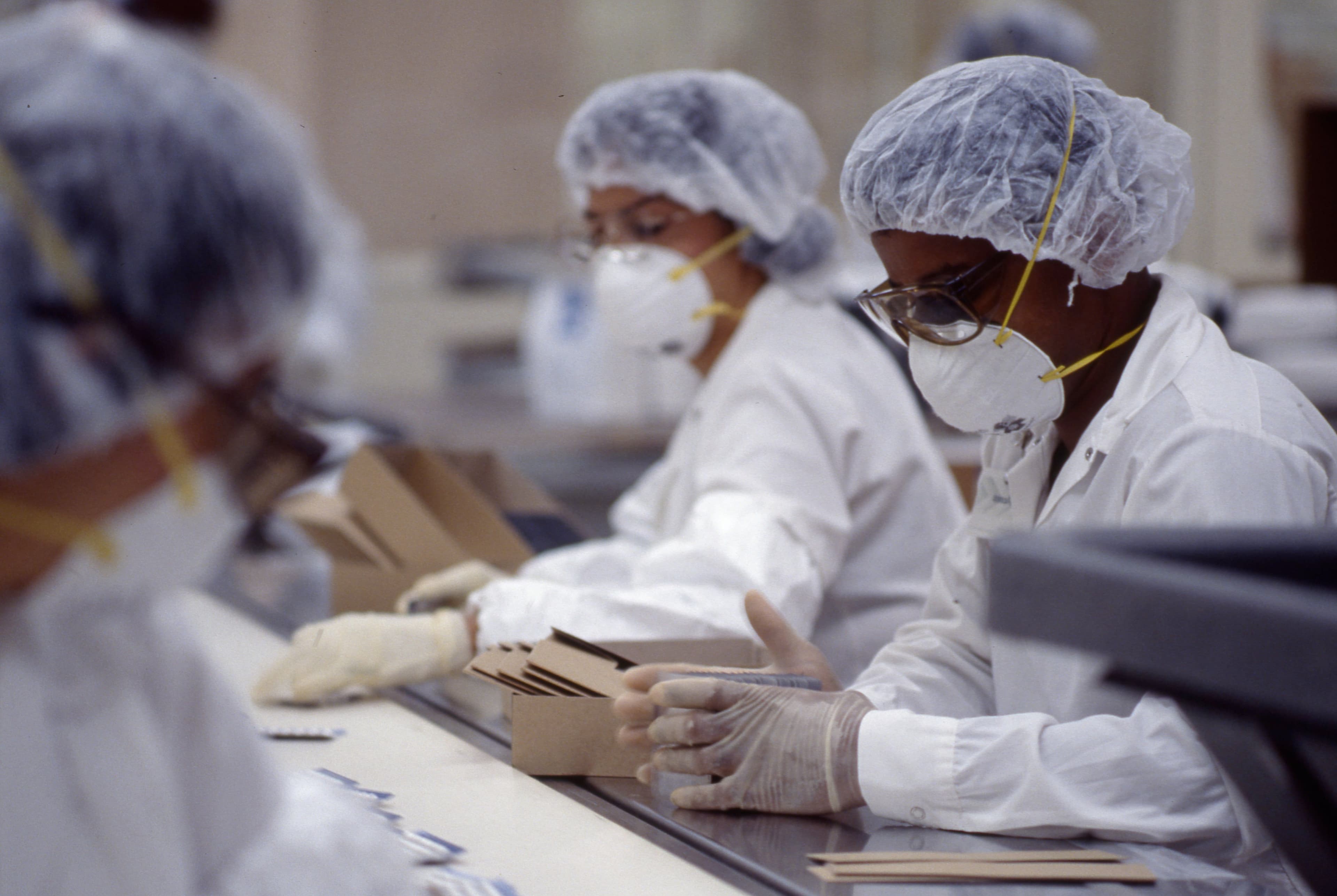
1987: Suppository packaging area online for Wyeth
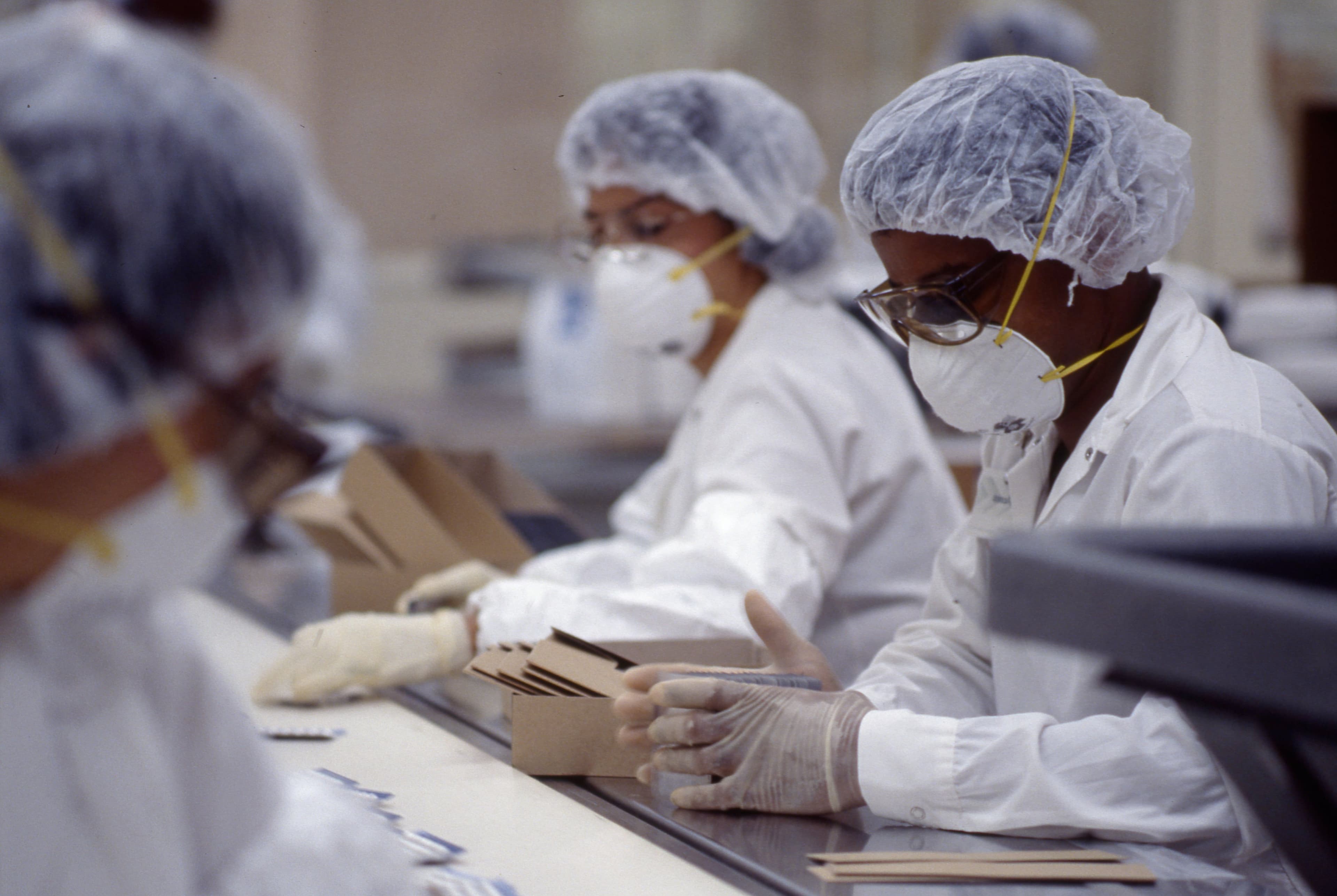
Fluor performed the engineering, procurement and construction of Wyeth's Solid Dosage Packaging Area in Guayama Puerto Rico. The scope included the renovation and installation of Wyeth's new suppository packaging area.
1987
Barceloneta, Puerto Rico facility produces veterinary drugs and timolol maleate
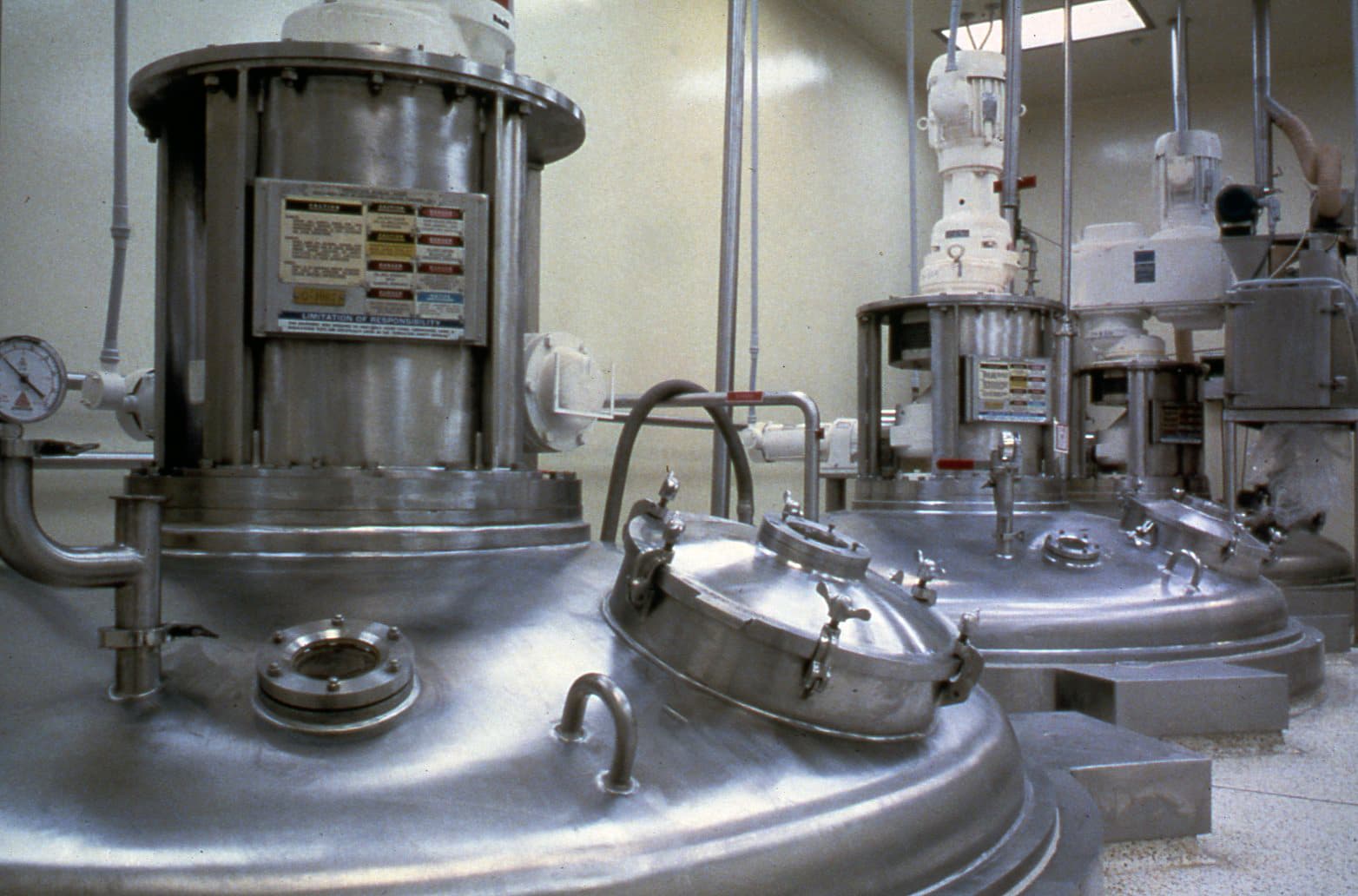
1987: Barceloneta, Puerto Rico facility produces veterinary drugs and timolol maleate
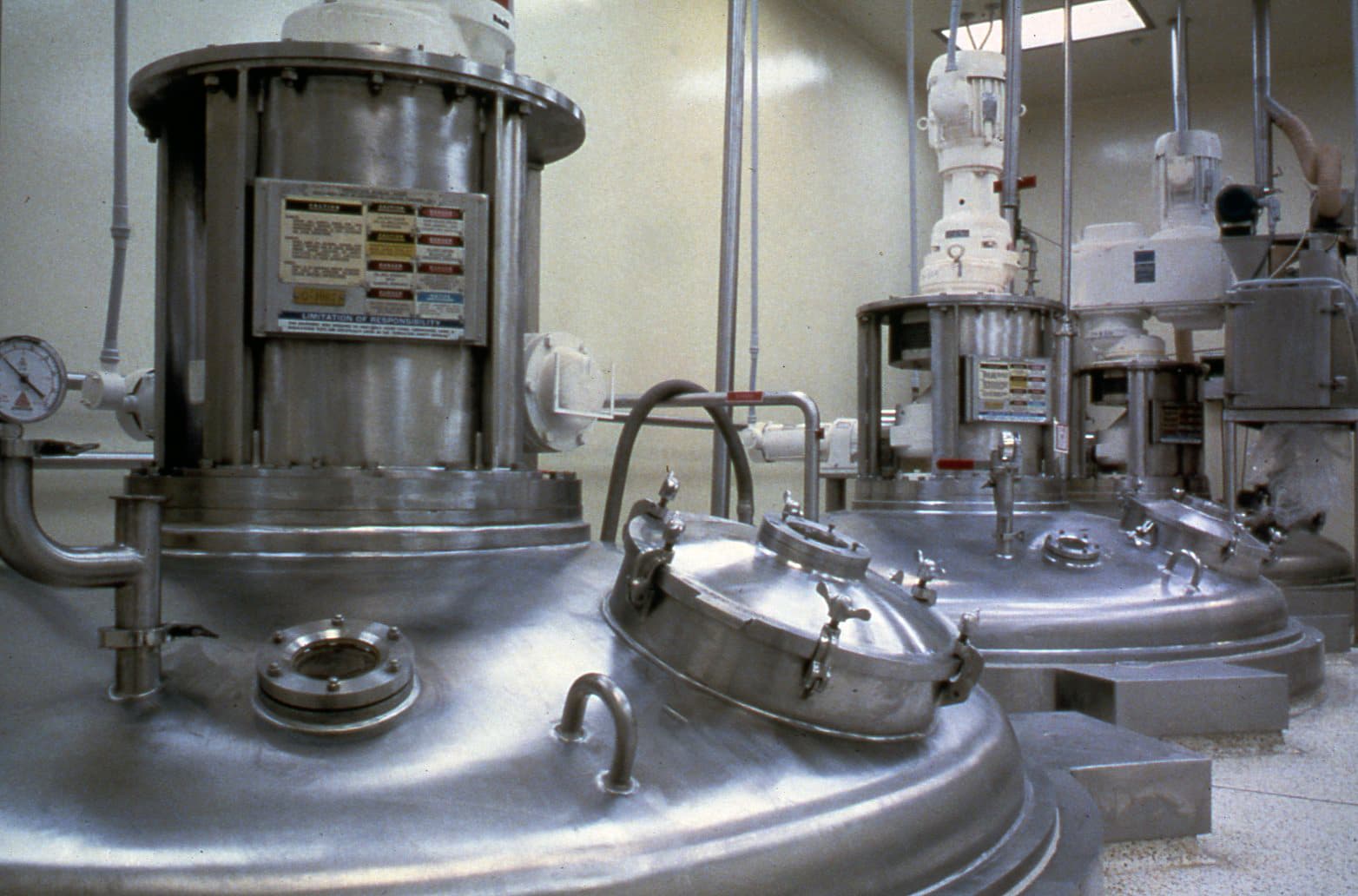
Fluor provided design, procurement and construction services for two separate projects and other ongoing small capital projects at Merck, Sharp and Dohme's Puerto Rican operations. The primary projects were additions to an existing plant complex originally built by Fluor. These two high-end technology projects were completed and in production within 23 months. The larger of the two projects provides for bulk production of Ivermectin, a veterinary drug used to treat heartworm in dogs and large animals. Fluor also provided services for an addition to existing facilities which manufacture timolol maleate in bulk, used for ophthalmic treatments and in coronary disease prevention.
1987
Burroughs Wellcome pharmaceutical facility constructed in Raleigh
&w=3840&q=75)
1987: Burroughs Wellcome pharmaceutical facility constructed in Raleigh
&w=3840&q=75)
Fluor constructed the Burroughs Wellcome pharmaceutical facility in North Carolina's Research Triangle Park.
1988
First-of-its-kind EPOGEN® manufacturing facility validated in Thousand Oaks, California
&w=3840&q=75)
1988: First-of-its-kind EPOGEN® manufacturing facility validated in Thousand Oaks, California
&w=3840&q=75)
Fluor performed the design and construction of the Amgen EPOGEN (Erythropoietin) facility in Thousand Oaks, California. The project was a first-of-its-kind facility for manufacturing, using an anchorage dependent, genetically engineered mammalian cell line.
1988
Fluor renovates Pharmaceutical Tableting Facility
&w=3840&q=75)
1988: Fluor renovates Pharmaceutical Tableting Facility
&w=3840&q=75)
Nutrilite contracted Fluor to provide the engineering and procurement support for their Pharmaceutical Tableting Facility Renovation in Buena Park, California.
1988
Tableting pilot lab facility designed for confidential client in Palo Alto and Vacaville, California
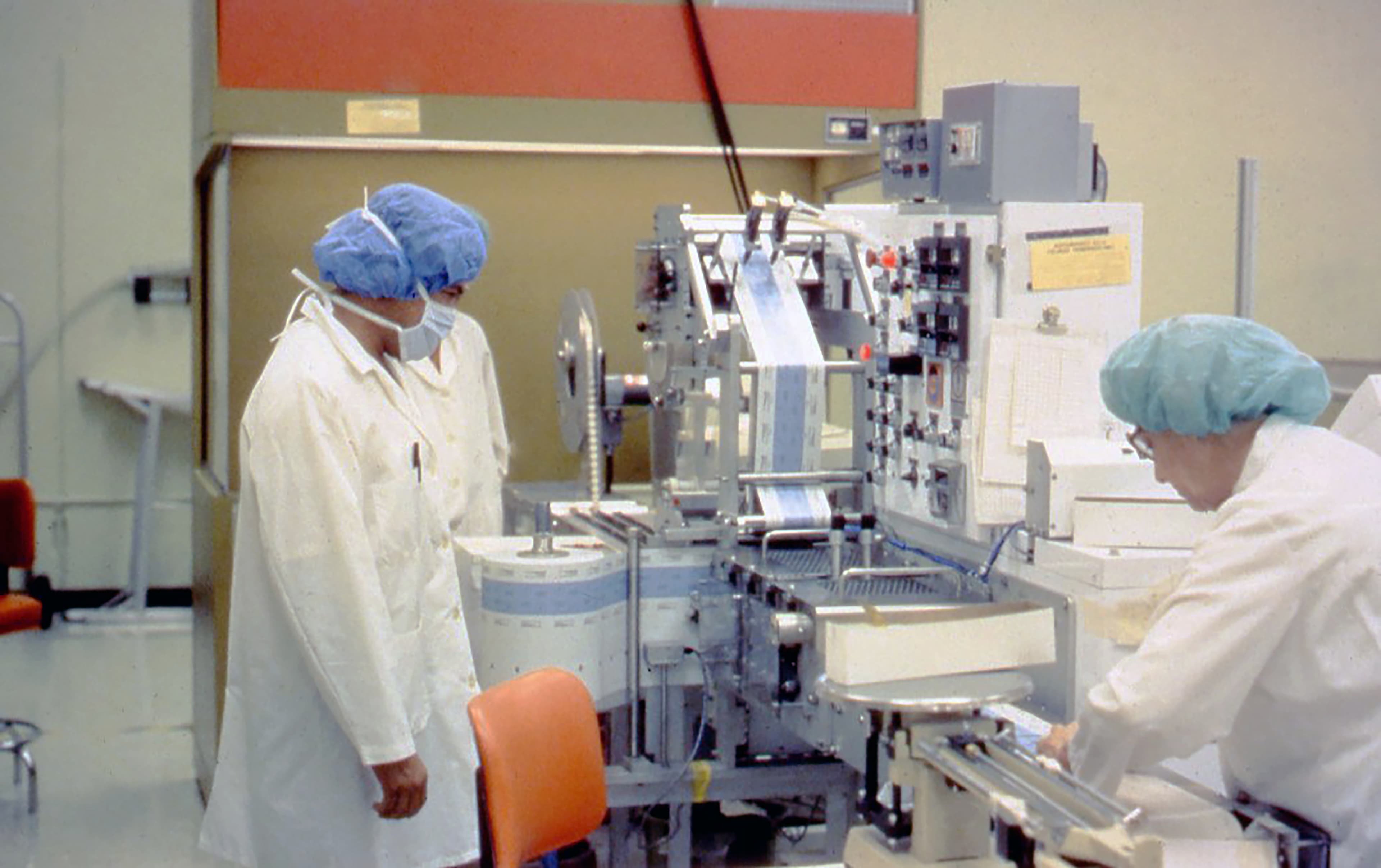
1988: Tableting pilot lab facility designed for confidential client in Palo Alto and Vacaville, California
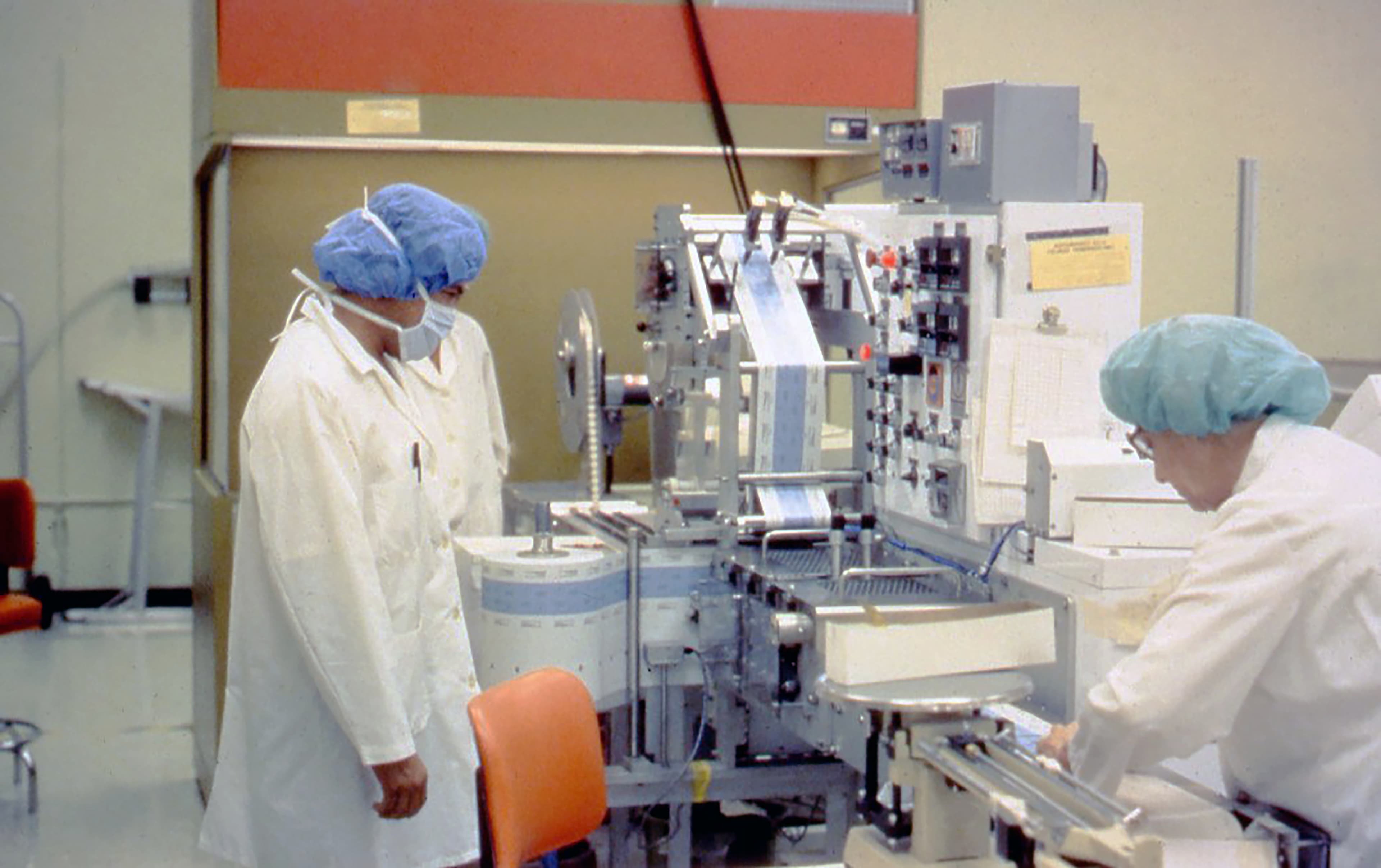
Fluor designed a 15,000 square foot pilot lab facility as an addition to an existing pharmaceuticals plant in Palo Alto, California. In addition, Fluor engineered a 116,000 square foot grassroots facility in Vacaville, California.
The primary processes included the manufacture of coated time-release tablets and transdermal. The tableting process included wet granulation, fluid bed dryers, sieving, mulling, tableting, pan coating, laser drilling and printing. The packaging of the tablets includes bottling, cottoning, capping, labeling and cartoning. Tablets were also packaged in blister packs and cartoned. The transdermal process entailed process film casting, lamination, drying, printing, dye-cutting, pouching and cartoning. The trail manufacturing was made up of five packaging lines for the two processes. The processes are equipped with a USP water system, which utilizes two-stage osmosis and a three stage clean-in-place system.
1988
World’s largest, multi-product genetic engineering and manufacturing plant constructed
1988: World’s largest, multi-product genetic engineering and manufacturing plant constructed
A large biotech client selected Fluor to design, engineer, procure and manage construction for a 72,000 square-foot, multi-product genetic engineering and manufacturing plant. The facility produced a variety of products, such as human growth hormone, tissue plasminogen activator (TPA) and Interferon, made by fermentation processes involving genetically modified microorganisms. Using bench-scale data, Fluor process engineers worked closely with the client’s research personnel to establish process definition and flow diagrams, piping and instrumentation diagrams and equipment data sheets for the pilot plants and for production scale-up. The project included laboratories, semiworks and production-scale fermentation processing controlled by advanced computer systems. Separation and purification processes designed for growth hormone and other proteins involved the first commercial scale-up of protein separation technology.
1989
Construction completed for Merck building repair
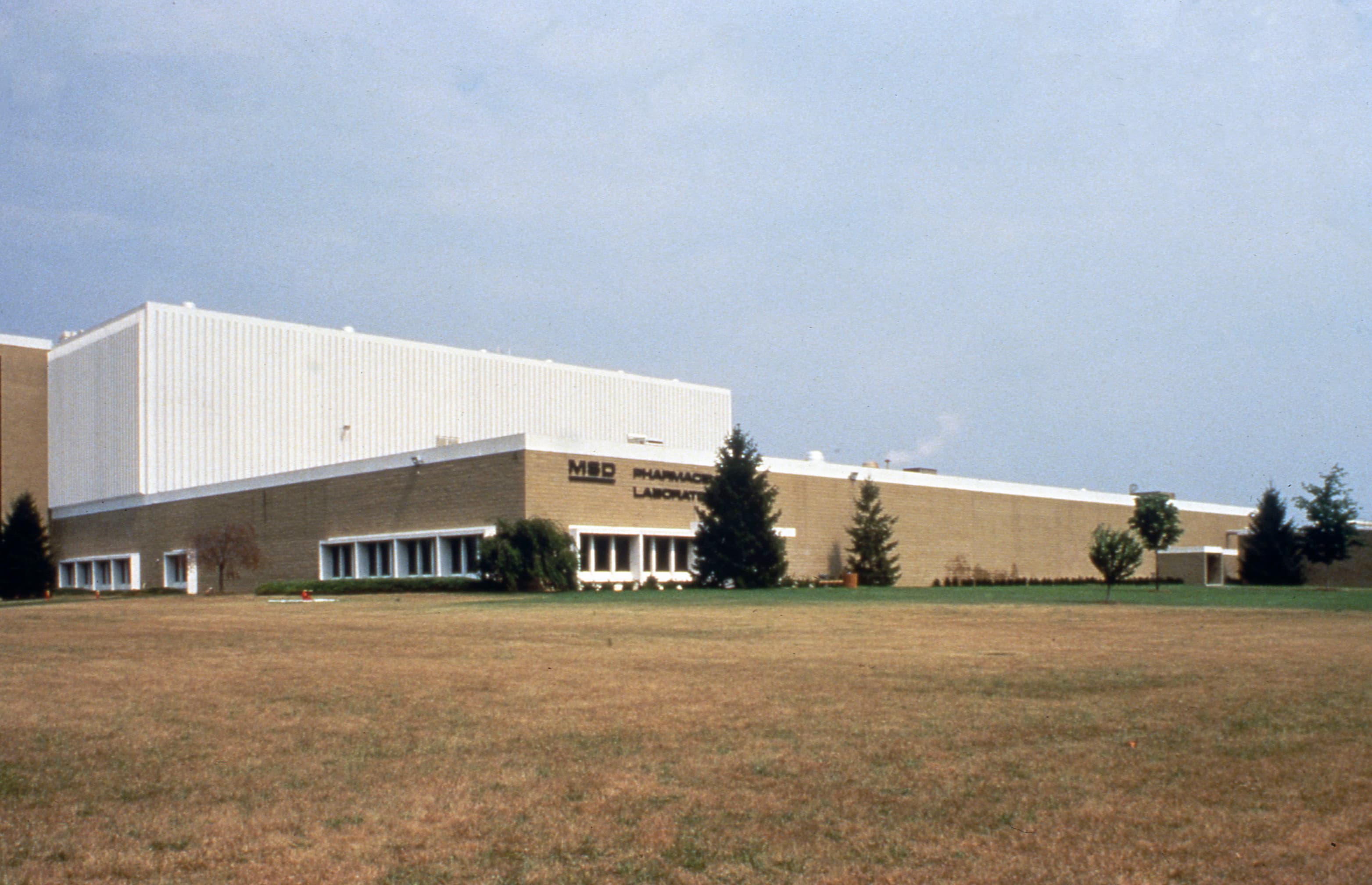
1989: Construction completed for Merck building repair
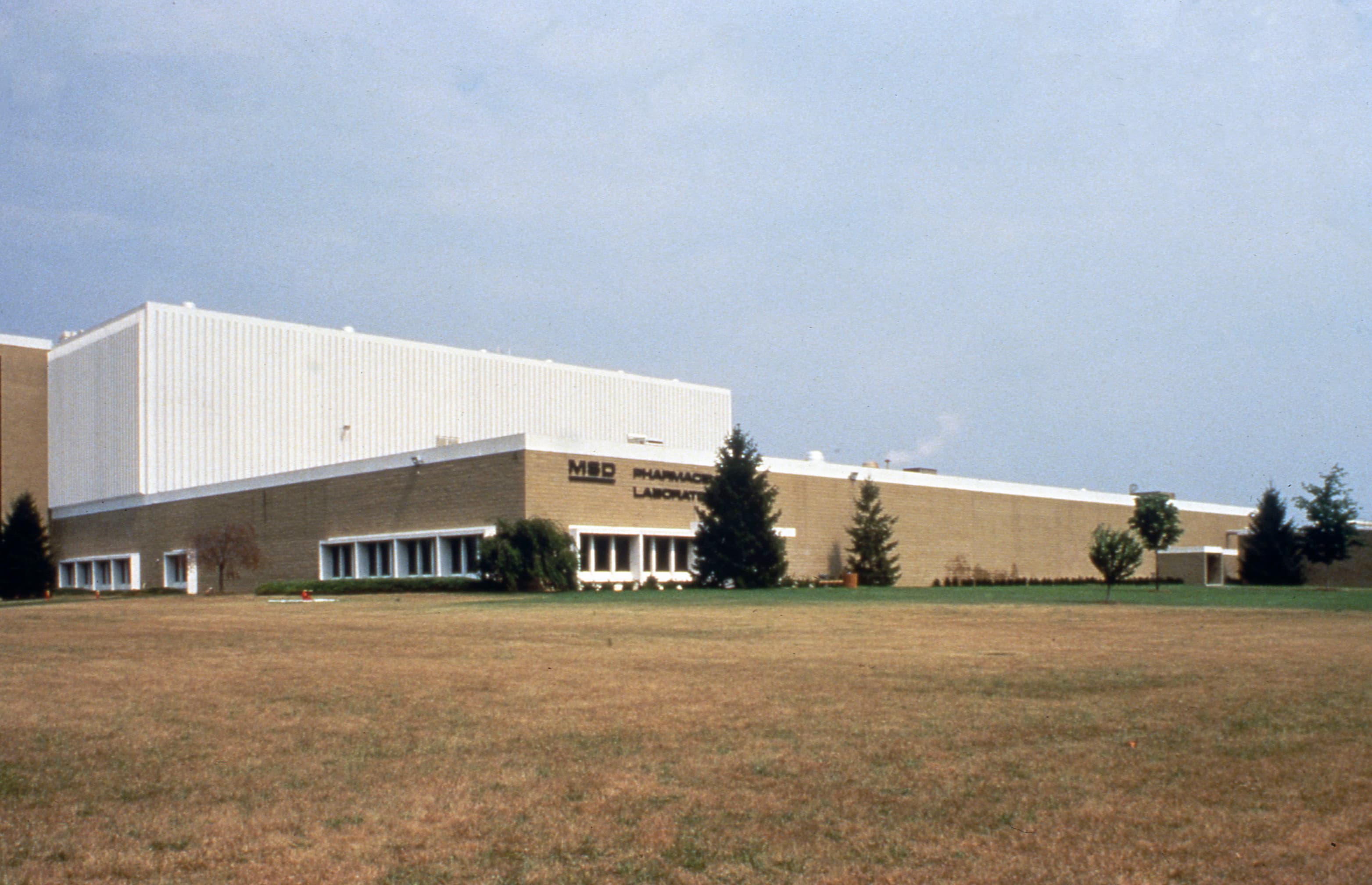
Fluor contracted in 1984 to construct and modify Merck's facility in Elkton, Virginia. The project was later completed in 1989.
1989
Alcon Laboratories ophthalmic line relocates to Humacao, Puerto Rico
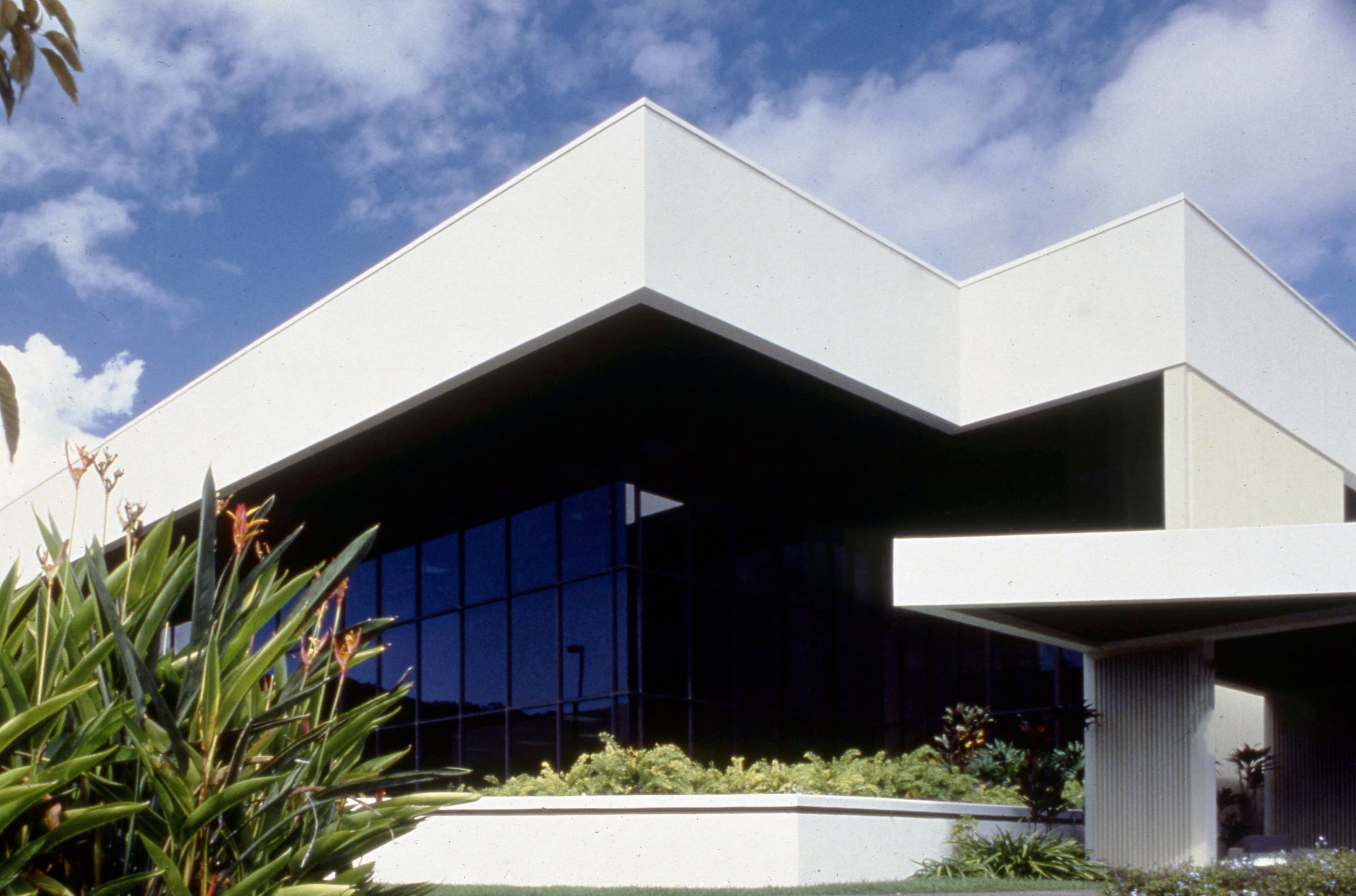
1989: Alcon Laboratories ophthalmic line relocates to Humacao, Puerto Rico
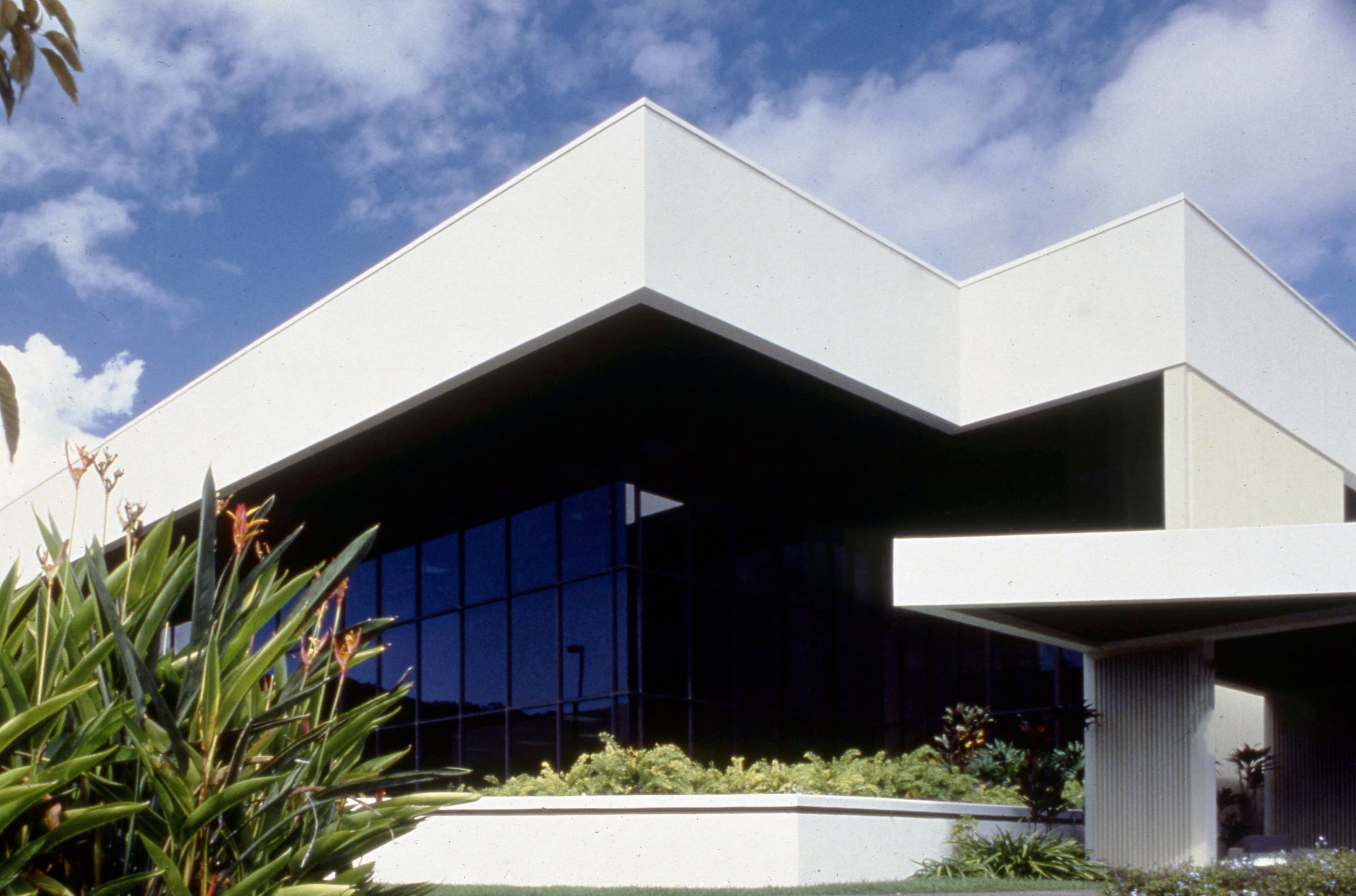
The sterility and control requirements for ophthalmic solutions are the most stringent after injectable products. Fluor's scope of work involved relocating an ophthalmic line from Dallas, Texas to Alcon Laboratories' Humacao, Puerto Rico facility. Special attention was paid to the HVAC system including room pressurization, supply and return air with HEPA-filtered laminar-flow ceilings and automated controls. The total project included two separate formulation and packaging plants of 28,000 and 45,000 square feet, as well as an administration complex, laboratory, cafeteria and energy center.
1989
Fluor completes grass-roots, 230,000-square-foot facility for Merck, Sharp & Dohme
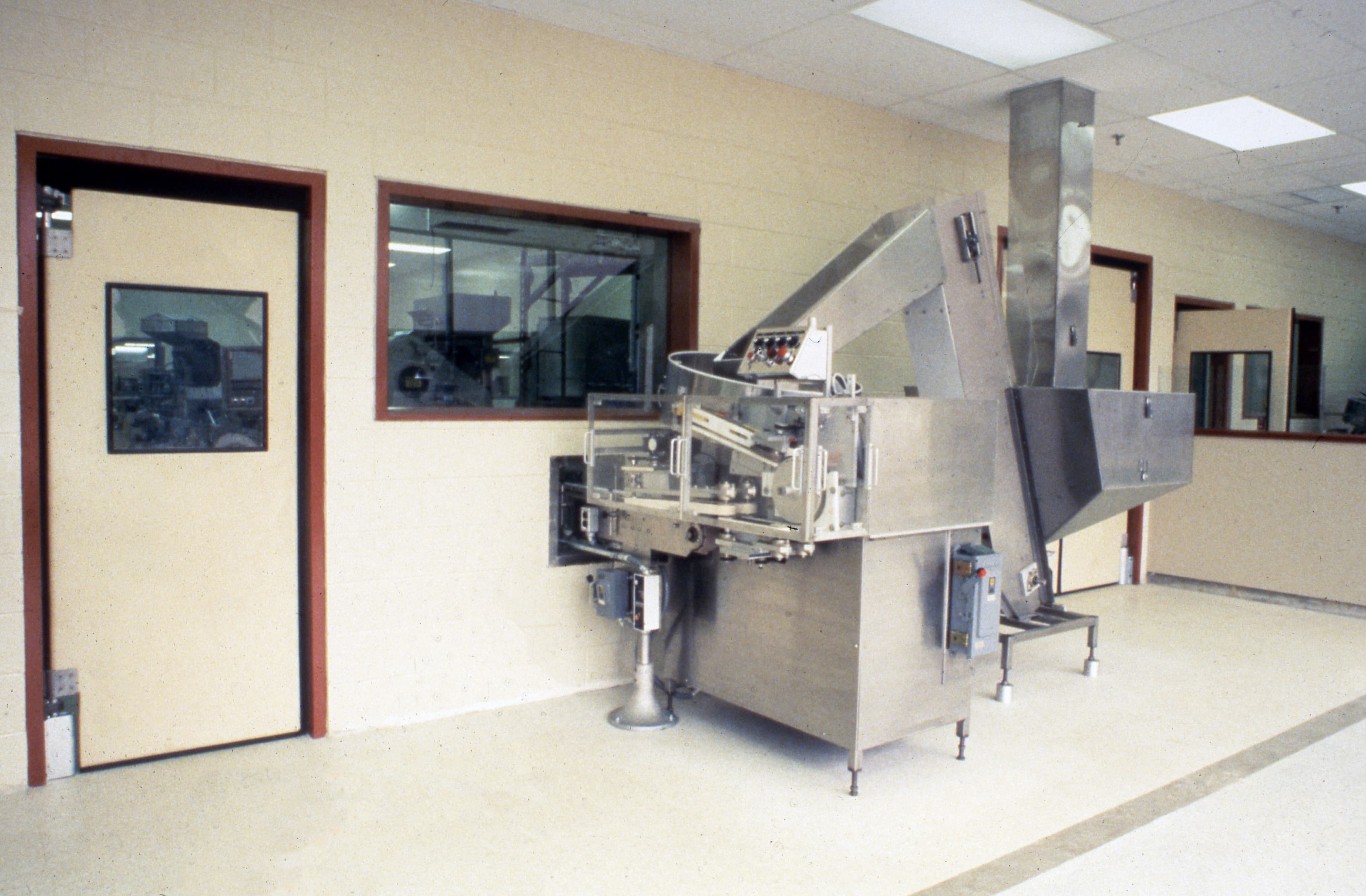
1989: Fluor completes grass-roots, 230,000-square-foot facility for Merck, Sharp & Dohme
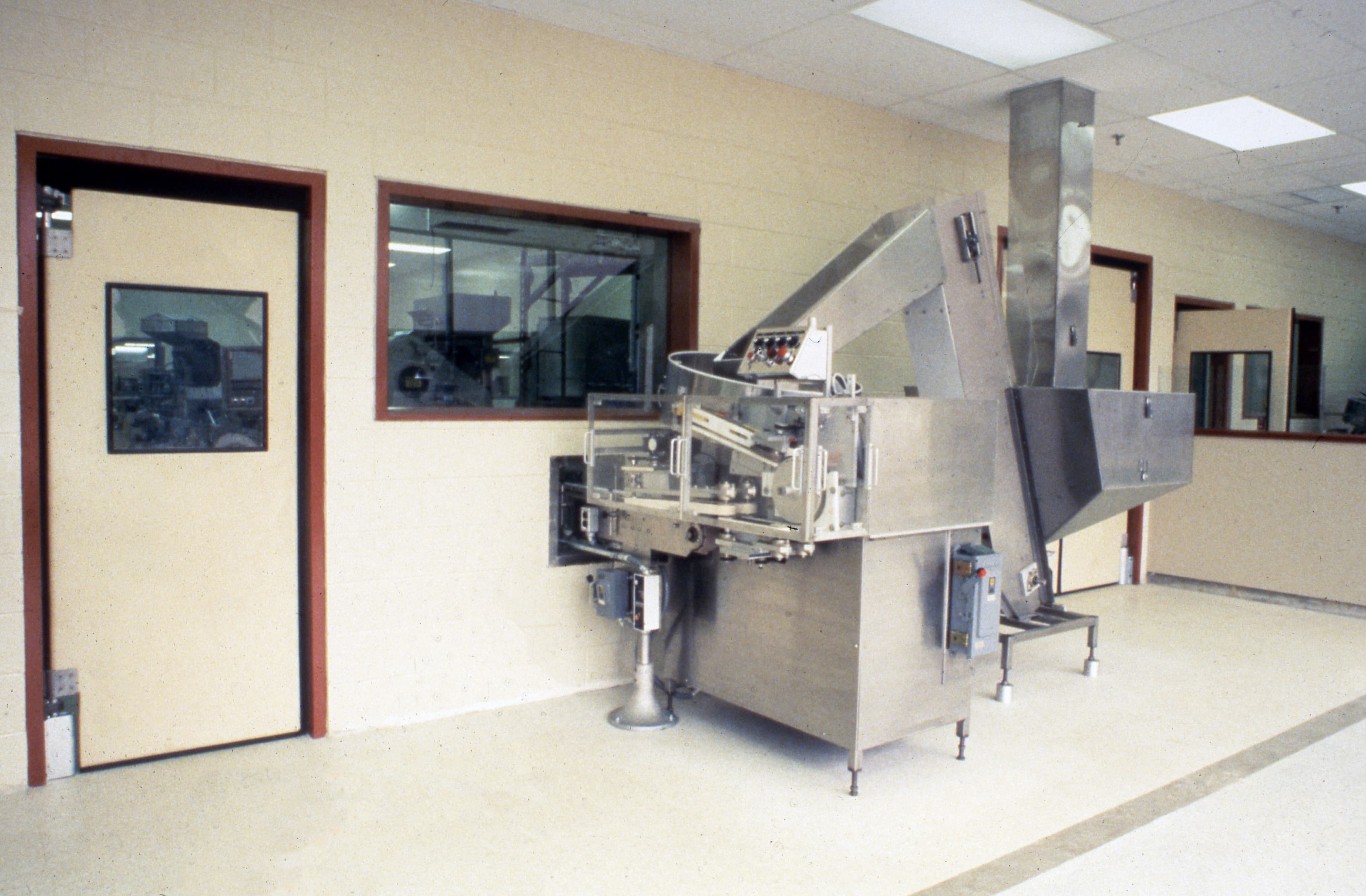
Merck, Sharp and Dohme's plant in Wilson, North Carolina was a fast track, design-build project for ingested coated tablets. Only 15 months were required from design commencement to completion of construction. Special clean room environments were integrated into the design, and dust-resistant, cleanable materials were used for the walls and ceilings in the manufacturing areas. Fluor also designed the packaging area. The ingredients and final pharmaceutical formulation were pneumatically conveyed by a dense phase vacuum conveying system selected to eliminate dusting problems and to avoid particle attrition and separation.
1989
Fluor builds and subsequently expands Parenteral Facility for Lederle Labs
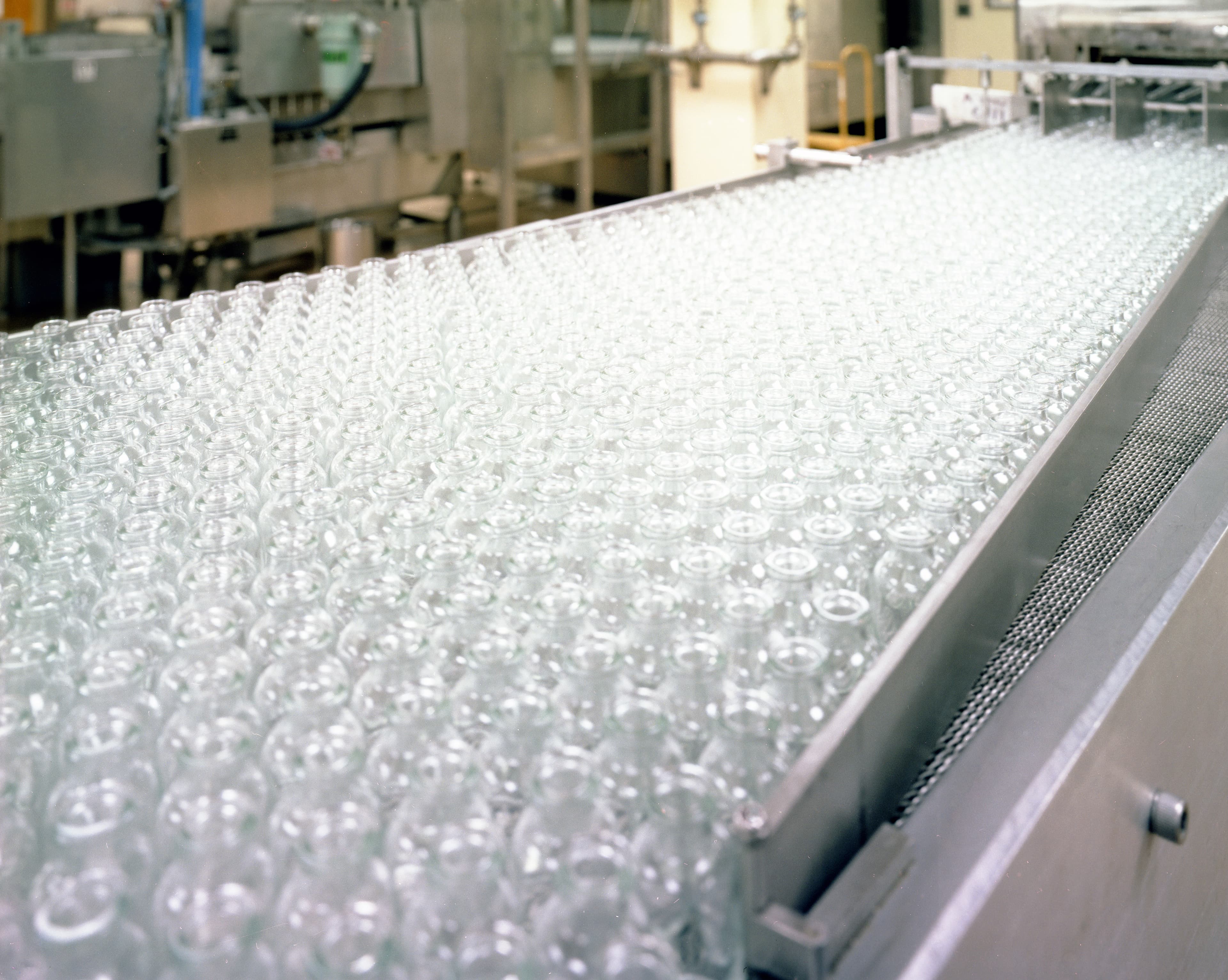
1989: Fluor builds and subsequently expands Parenteral Facility for Lederle Labs
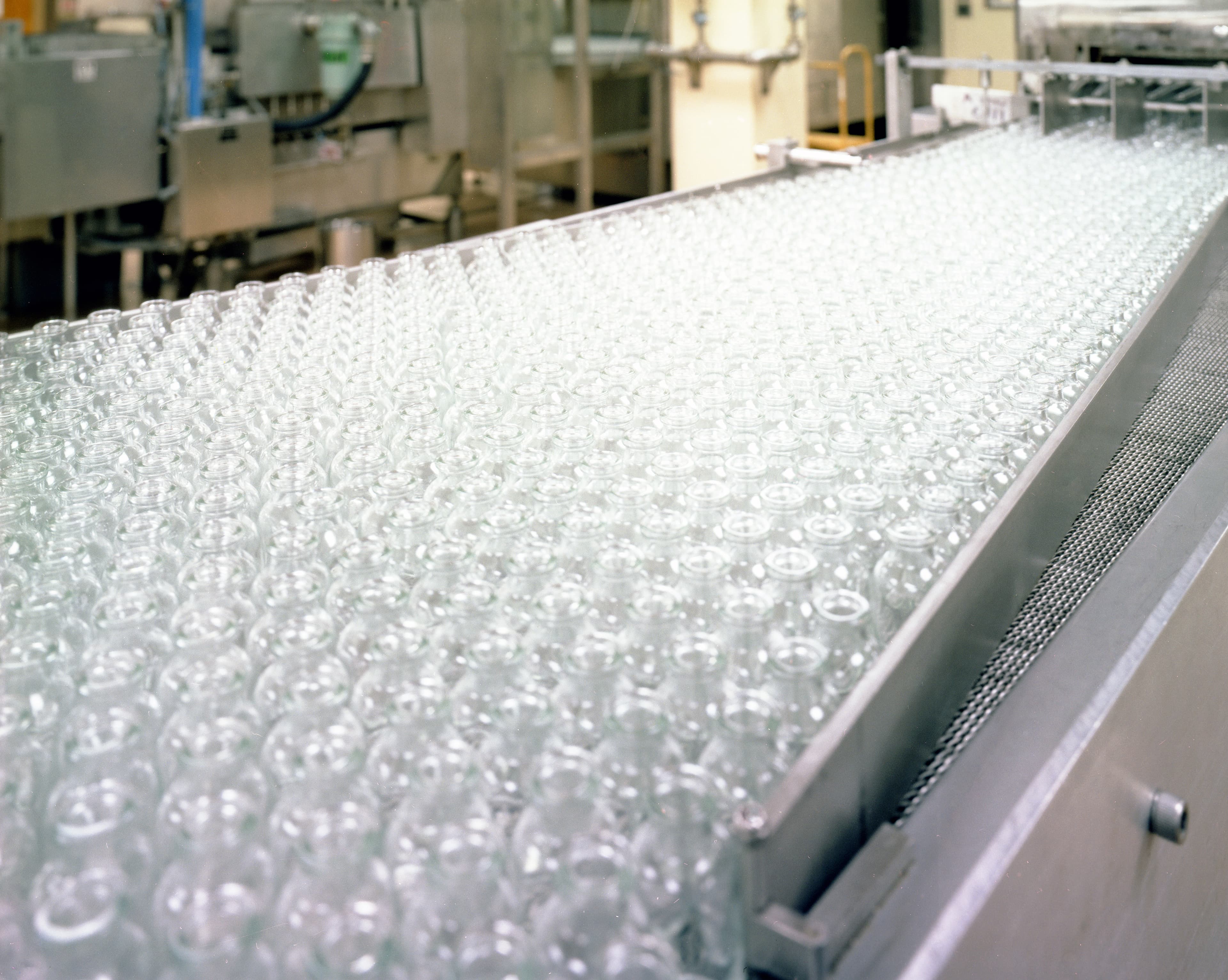
Fluor conducted a series of design-build projects in Carolina, Puerto Rico for Lederle Labs. The original work was for a 55,000-square-foot parenteral facility. The design included primary and secondary high efficiency particulate air- (HEPA) filtered air under laminar flow conditions. The system was field balanced by Fluor. Special consideration was given to control of the environment through a system of airlocks and interlocked doors to maintain cascading pressure differentials. The dynamic water for injection (WFI) system included demineralization, multiple-effect distillation, carbon filtration and ultraviolet sterilization of the circulating water.
Fluor expanded the facility as well. The project included installation of new reverse-osmosis (RO) units, ultrafiltration units, IPA distillation towers and an upgrade of some of the sterile areas.
1990s
Fluor designs and builds first-of-a-kind biopharmaceutical facilities.
1990
Eastman Kodak Bioprocess Manufacturing Facility Expansion operational
&w=3840&q=75)
1990: Eastman Kodak Bioprocess Manufacturing Facility Expansion operational
&w=3840&q=75)
Fluor provided design and construction management services for the Bio-Products Development Center of Eastman Kodak's Life Sciences Division. The building was the headquarters and process development facility for the division and produces a variety of products used in the pharmaceutical, diagnostic chemical and nutrition markets. Subsequently, Fluor was awarded additional engineering and construction contracts for the facility, including a maintenance contract for the Center.
1990
Eli Lilly & Co. bulk pharmaceutical facility produces antibiotics
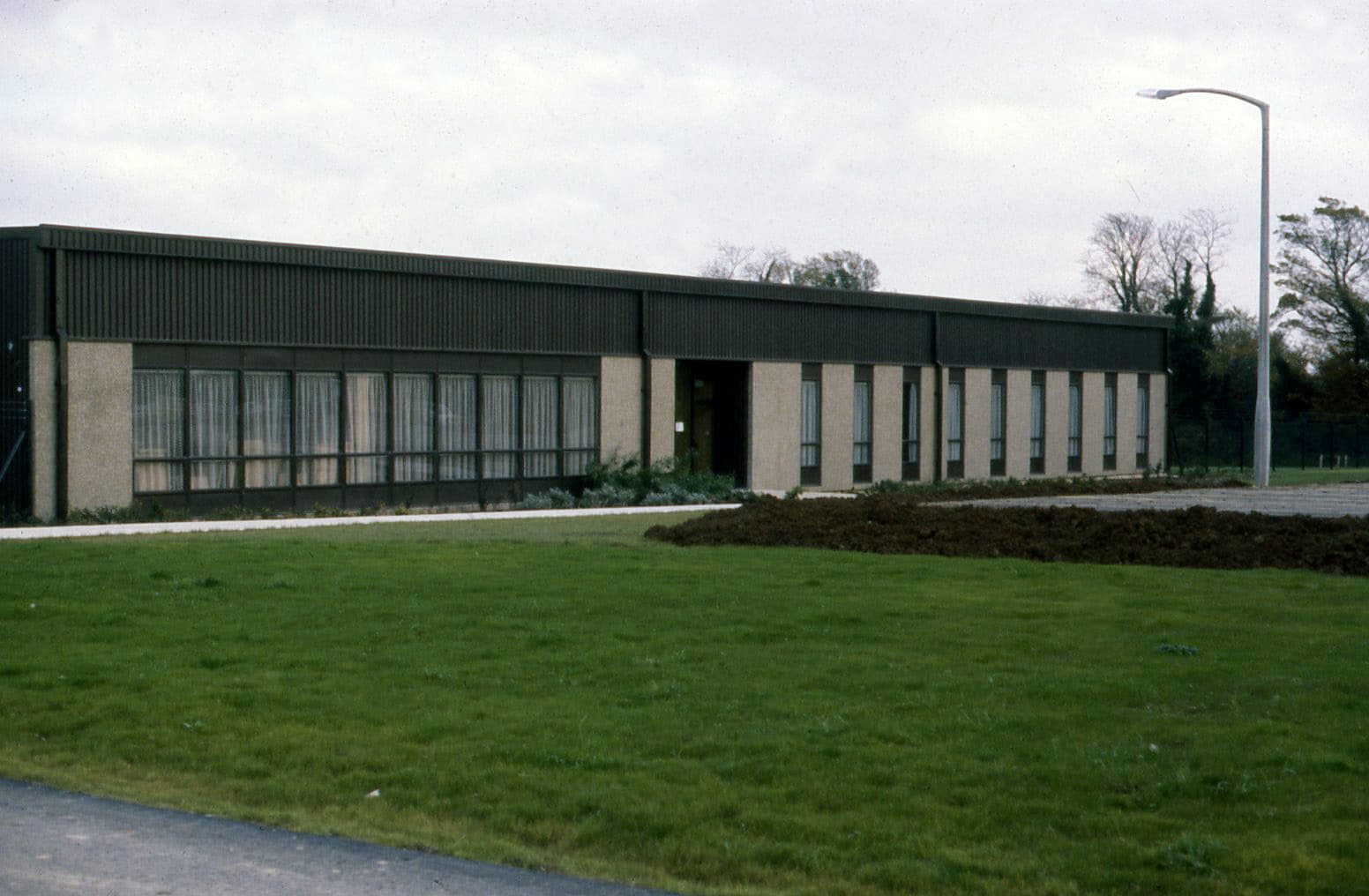
1990: Eli Lilly & Co. bulk pharmaceutical facility produces antibiotics
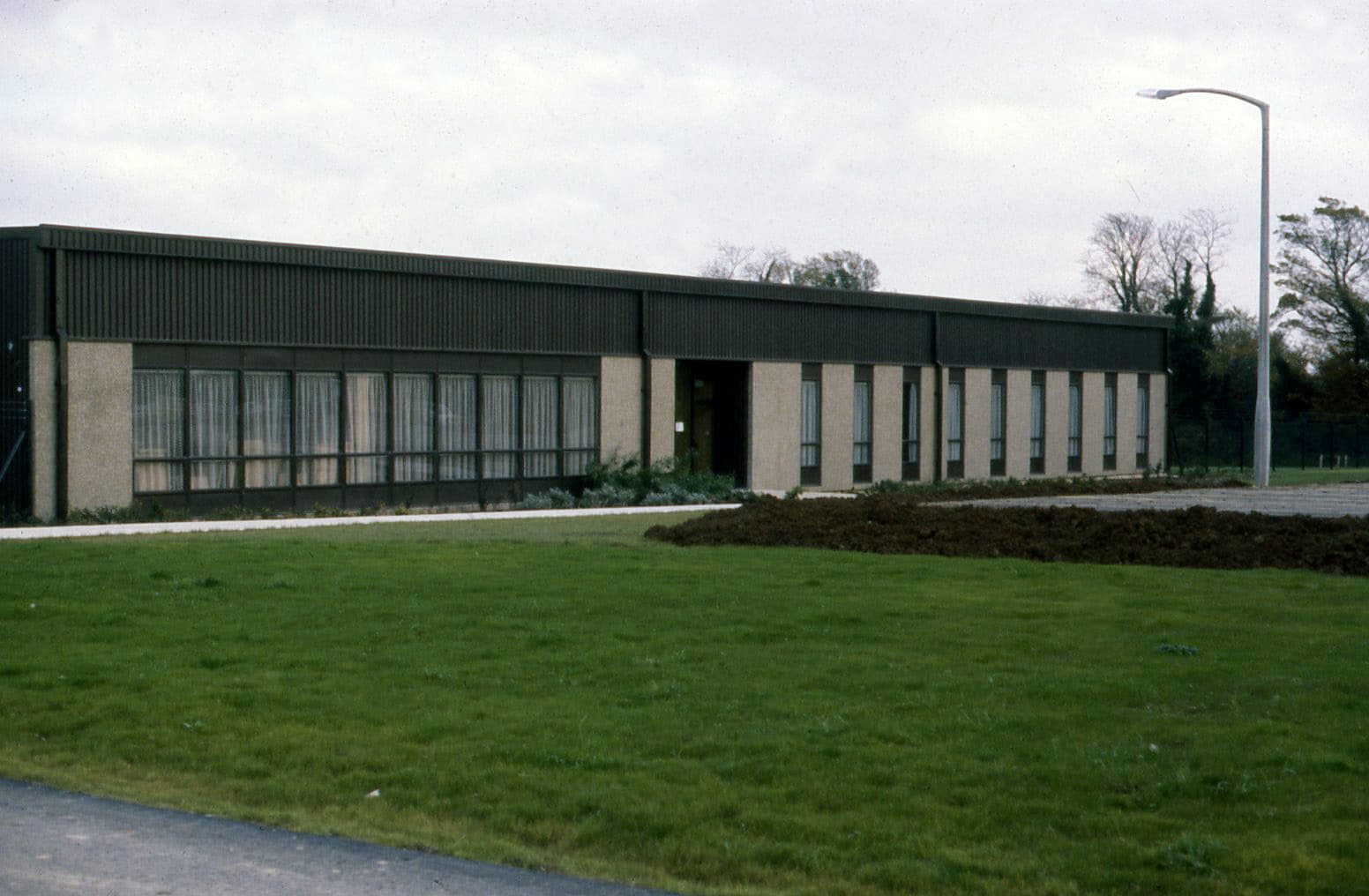
Fluor completed the design and construction of a grass-roots multipurpose bulk pharmaceutical facility for the production of various antibiotics (chemical synthesis of cephalosporin derivatives) and herbicides. The intermediates production area consisted of four separate process lines, including GLS reactors, vacuum receivers, and extractor crystallizers. Also included in the multipurpose process area were rotary vacuum filters, pressure plate filters, centrifuges, vacuum dryers, and blenders. The wastewater disposal involved an underground pipeline running six miles from the plant to the sea. The overall production processes were largely computer controlled. Design, procurement and construction was accomplished within a 30-month schedule.
1990
Henkel KGaA TAED plant commissioning begins 15 months after the start of construction
1990: Henkel KGaA TAED plant commissioning begins 15 months after the start of construction
Fluor provided detailed engineering, procurement and construction management services for Henkel's TAED plant in Cork, Ireland. The plant produces the bleach activator tetraacetylethylenediamine (TAED) as a granulated crystal by the two-stage reaction of ethylene diamine with acetic acid and acetic anhydride. The plant consists of a five-story building of two parts: an open-steel structure which houses the liquids processing function, and a closed reinforced concrete section containing the solids processing area. All process facilities are fully automated. Fluor completed the design and construction of the plant and handed over to the client in 19 months.
1991
Bristol-Myers Squibb's innovative bulk pharmaceutical finishing facility improves speed to market
&w=3840&q=75)
1991: Bristol-Myers Squibb's innovative bulk pharmaceutical finishing facility improves speed to market
&w=3840&q=75)
Fluor worked closely with Bristol-Myers Squibb in the design of one of the most automated pharmaceutical plants in the world in 1991. The 230,000 square foot finishing facility processes bulk product from other locations into final dosage forms of tablets, capsules, powders and injectable. At the time, this process was innovative and changed the pharmaceutical manufacturing industry.
Conceived as a means of improving market position while retaining product quality and competitive costs, the plant had an innovative and sophisticated materials handling process. Fluor designed the facility to use bar codes to track the lifecycle of plant materials. Materials were moved throughout the facility using automatic guided vehicles, conveyors and elevators. Operators received instructions from the computer in carrying out finishing operations. Glass-walled production rooms provide visual access to inspectors, supervisors and visitors without contaminating the product.
1991
Grassroots pacemaker manufacturing facility built in Dorado, Puerto Rico
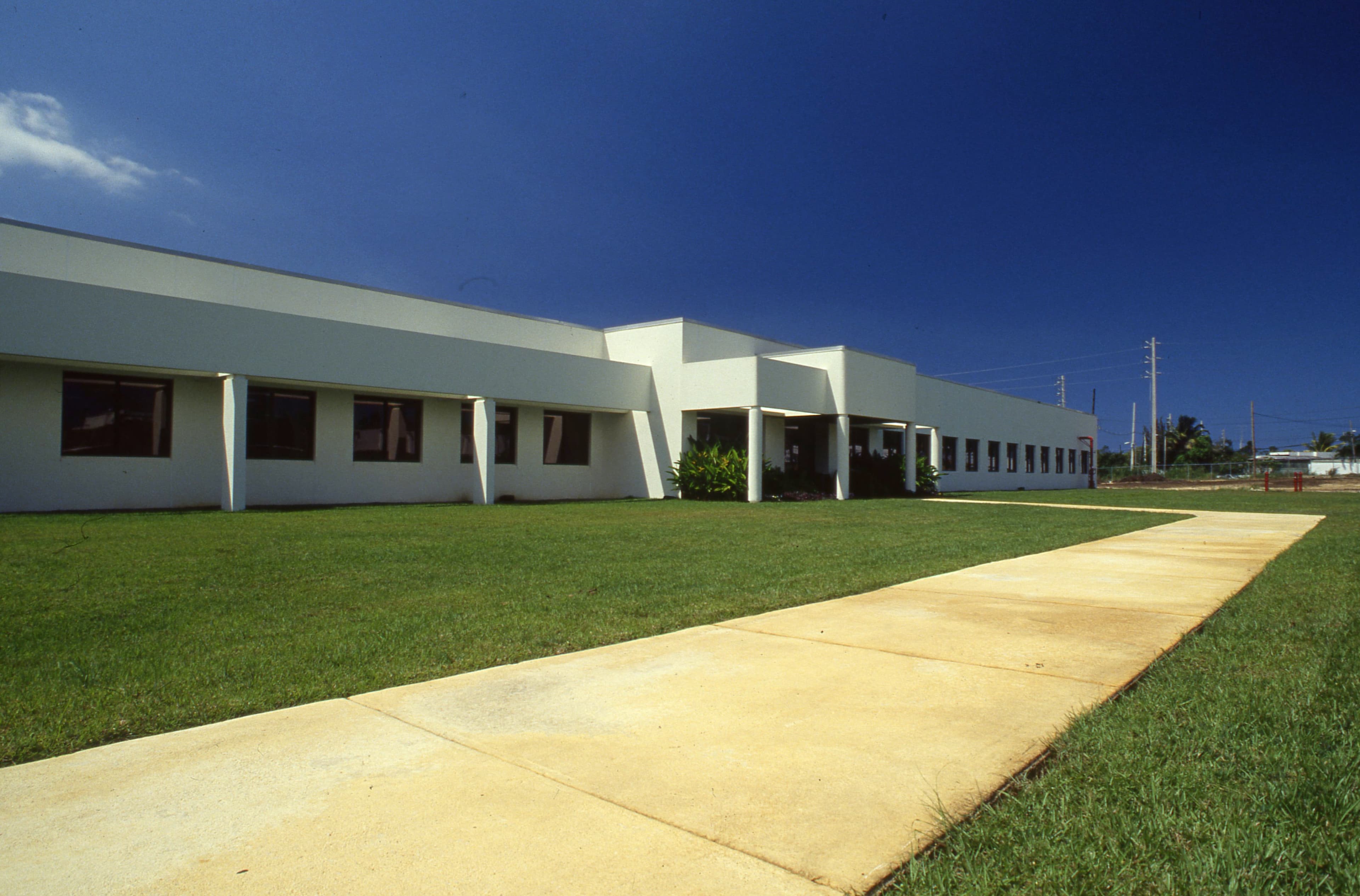
1991: Grassroots pacemaker manufacturing facility built in Dorado, Puerto Rico
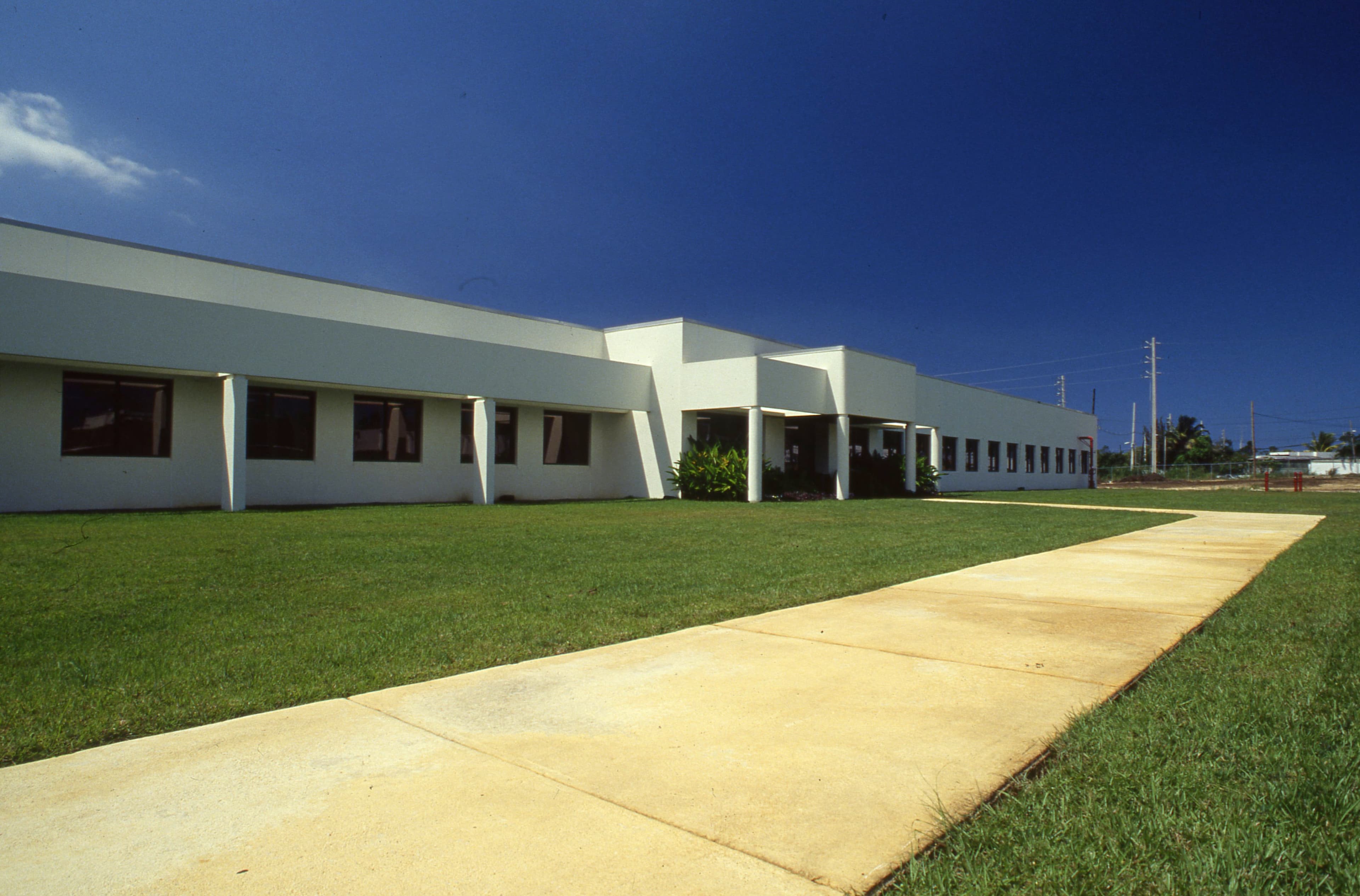
Fluor designed and built Cardiac Pacemaker Inc.'s 53,000 square foot facility in Dorado, Puerto Rico. The project focused on speed to market for this greenfield manufacturing plant.
1992
Biochemie Bioprocessing Plant, the world's largest commercial biotech plant, licensed and commissioned in Austria
&w=3840&q=75)
1992: Biochemie Bioprocessing Plant, the world's largest commercial biotech plant, licensed and commissioned in Austria
&w=3840&q=75)
Fluor successfully completed the engineering, procurement, design and construction of the production facilities for this bioprocessing plant. The facility included process utilities and other process steps like solution preparation, isolation, purification, ultrafiltration, sterile drying, filling and formulating. The batch process was fully computer controlled including several clean-in-place systems. Utilities are computer monitored. This facility employed gene splicing and recombinant technology and was considered the largest commercial biotechnical plant in the world at the time.
1992
Innovative production facility design and construction completed for Synergen
&w=3840&q=75)
1992: Innovative production facility design and construction completed for Synergen
&w=3840&q=75)
Fluor designed and constructed a first-of-its-kind production facility for Synergen in Boulder, Colorado. The plant produced IL-1 receptor antagonist, at the time a new drug for the treatment of rheumatoid arthritis and septic shock.
1993
Boots-Hoechst Celanese ibuprofen manufacturing facility receives prestigious Kirkpatrick Achievement Award
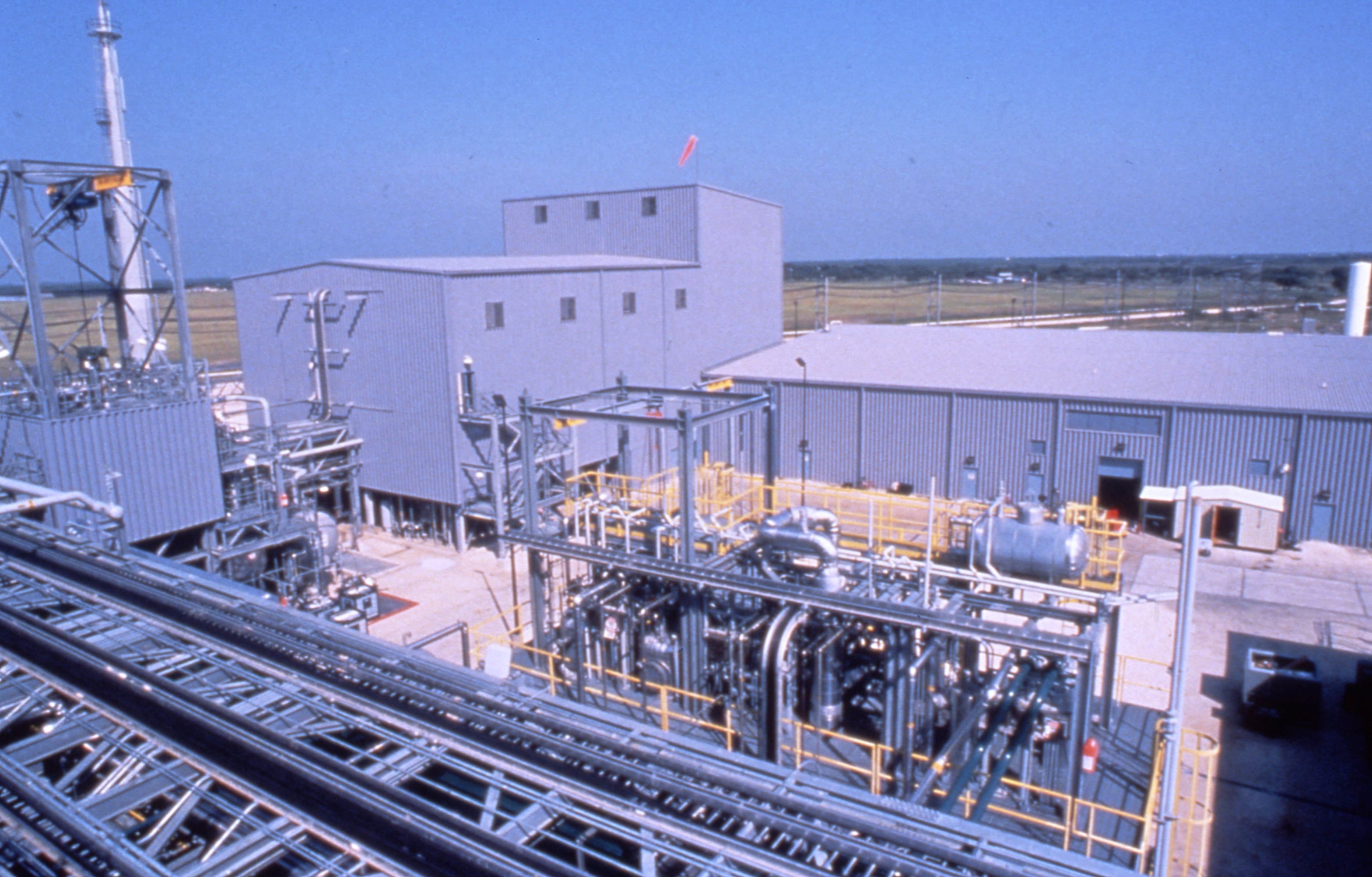
1993: Boots-Hoechst Celanese ibuprofen manufacturing facility receives prestigious Kirkpatrick Achievement Award
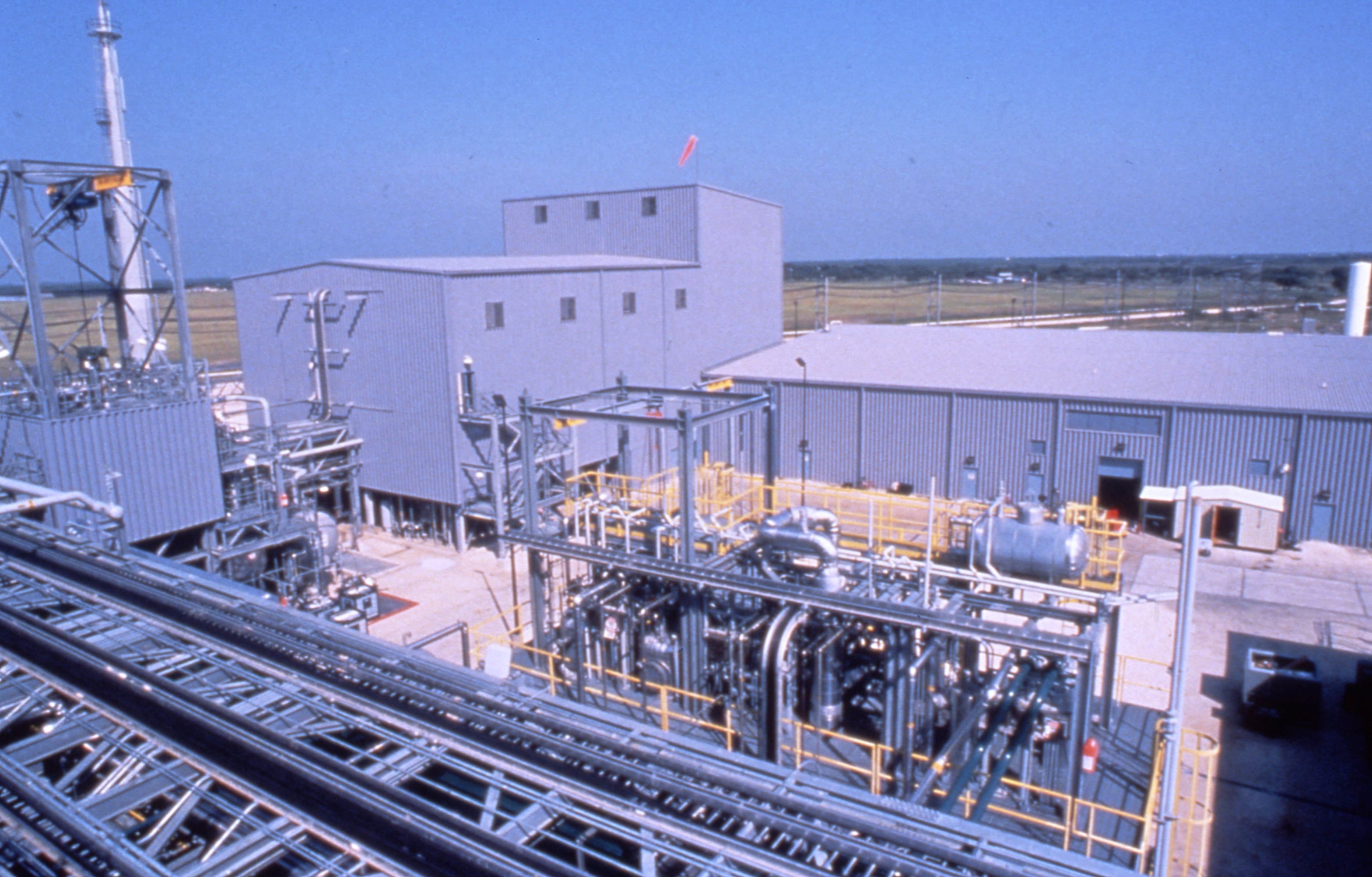
Fluor carried out preliminary engineering, detailed design, procurement and construction of this Bishop, Texas facility for the bulk synthesis of Ibuprofen. At start-up, this facility was the largest ibuprofen facility in the world, producing 3,500 metric tons per year of ibuprofen. The $86 million facility was honored with the prestigious Kirkpatrick Achievement Award because it employed a new process that reduced the six-step, non-catalytic process usually used for ibuprofen production to a three-step, catalytic synthesis. Benefits from the new process included lowered operating costs by avoiding the need for reagents; decreased waste-treatment costs; and lowered costs for compliance with environmental regulations.
1993
Fluor engineers grassroots facility for Gaeleo
1993: Fluor engineers grassroots facility for Gaeleo
Fluor worked on a series of projects for Gaeleo at its High Quality Bulk Pharmaceuticals Facility in Cork, Ireland. During the 1990s, Fluor provided engineering services for a grassroots, multiproduct bulk pharmaceutical facility.
1994
Licensing for Chiron Fill and Finish facility in Puerto Rico successful
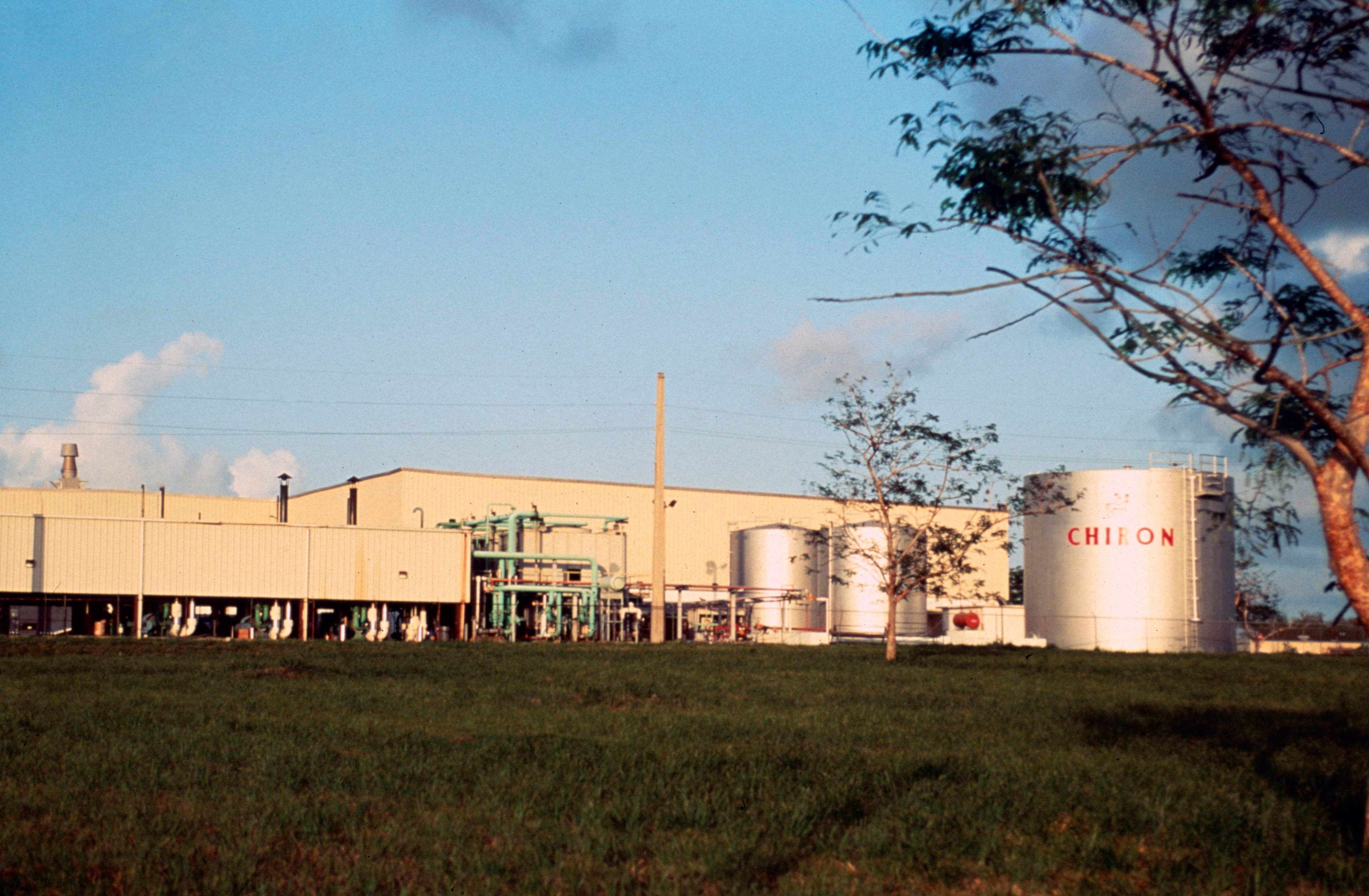
1994: Licensing for Chiron Fill and Finish facility in Puerto Rico successful
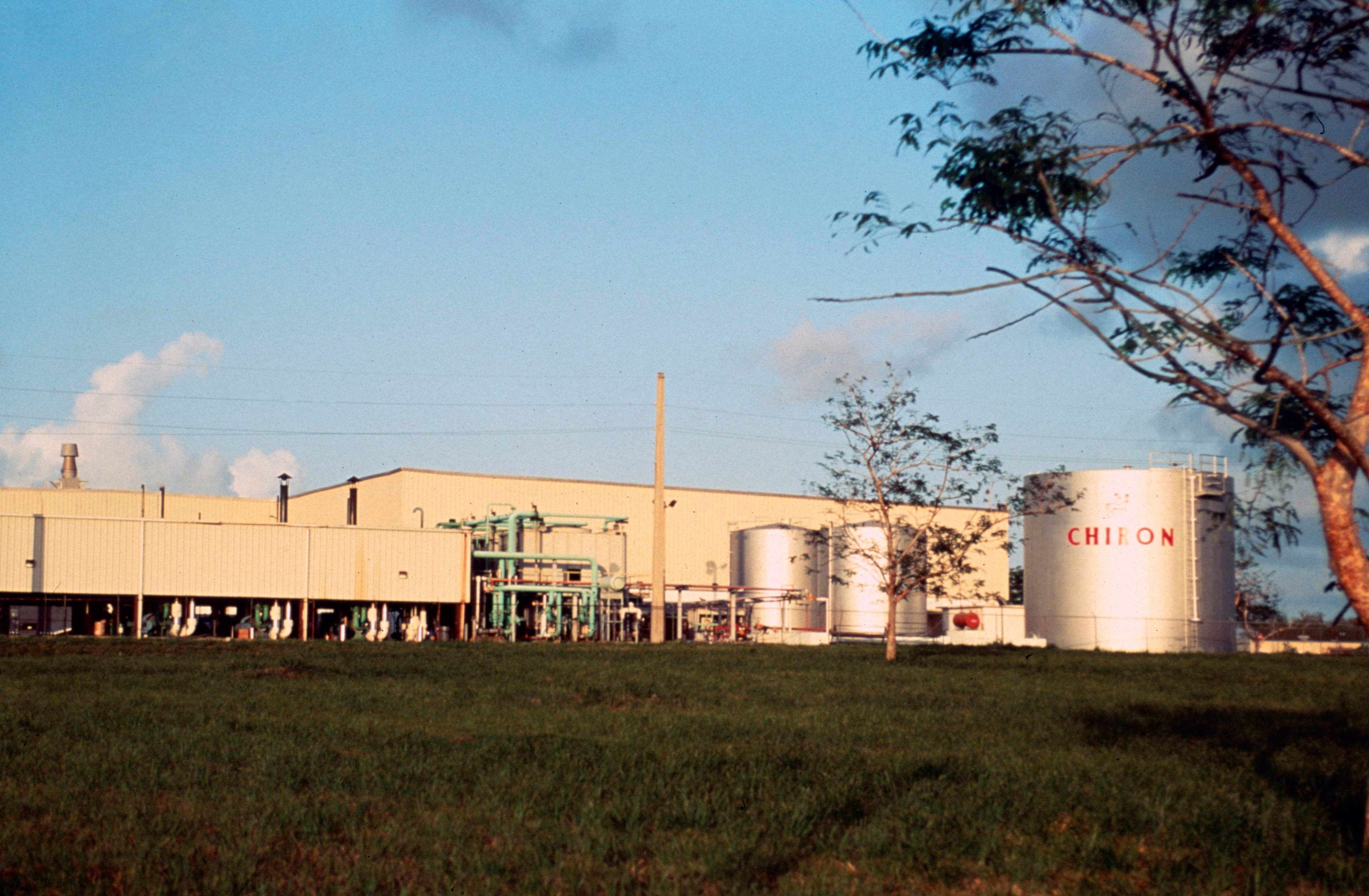
Fluor engineered, procured, constructed and assisted with the licensing of Chiron's Fill and Finish Area for beta interferon.
1996
Biogen Manufacturing Facility validated
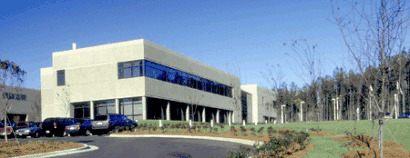
1996: Biogen Manufacturing Facility validated
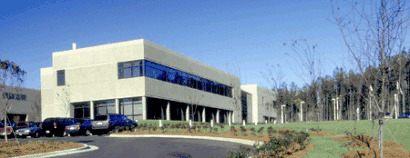
Fluor provided complete project services for Biogen's $57 million biologics manufacturing facility in North Carolina. The aseptic facility manufactured AVONEX® (Interferon beta-1a) for treatment of relapsing forms of multiple sclerosis. The 64,800-square-foot facility, on a 17-acre plot, is a structural steel frame with precast exterior skin.
1996
Freeport, Texas beta-carotene plant upgrade engineered
&w=3840&q=75)
1996: Freeport, Texas beta-carotene plant upgrade engineered
&w=3840&q=75)
Fluor was contracted in 1996 to provide engineering support for Hoffman-La Roche's Phase 1 Beta-carotene Retrofit project. Subsequently, Fluor was awarded the procurement and construction management of the plant upgrade. The revamp was completed in 1998.
1998
MedImmune's Frederick Manufacturing Facility combines biologic and biotechnology processes in one facility
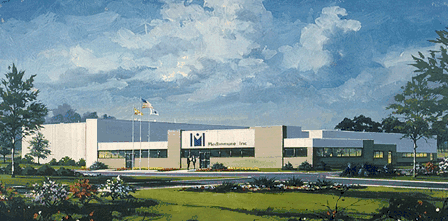
1998: MedImmune's Frederick Manufacturing Facility combines biologic and biotechnology processes in one facility
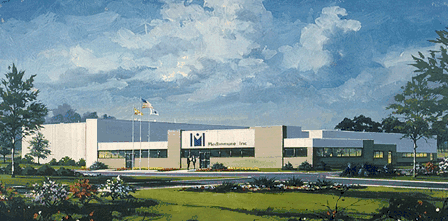
Fluor provided total project services for this multiproduct greenfield facility. The facility housed both biologic and biotechnology processes not normally found under one roof. Fluor performed engineering, procurement, construction management, validation and start-up services. The scope included a mezzanine, a filling and packaging area, clean utilities, a quality control area, a warehouse and offices. The facility included a biologics process train with dual centrifuges to fractionate blood plasma for production of immunoglobulins of interest and to recover albumin to be sold as bulk. The plasma fractionation process incorporated four 5,000-gallon Carr P-18 centrifuges that were the first of that size to be installed in a manufacturing facility.
1998
Eisai of America Vitamin E Manufacturing Plant Bay City, Texas
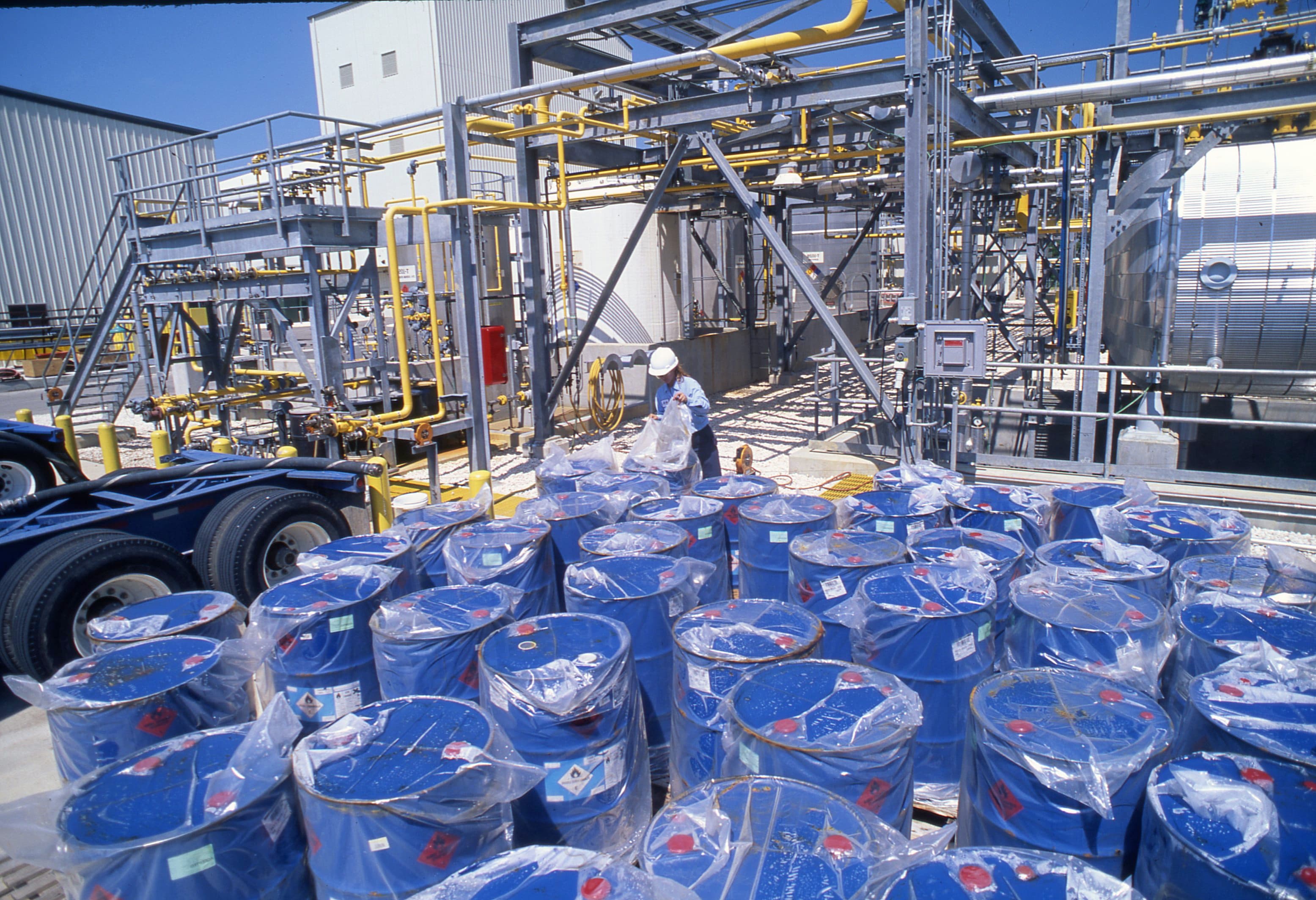
1998: Eisai of America Vitamin E Manufacturing Plant Bay City, Texas
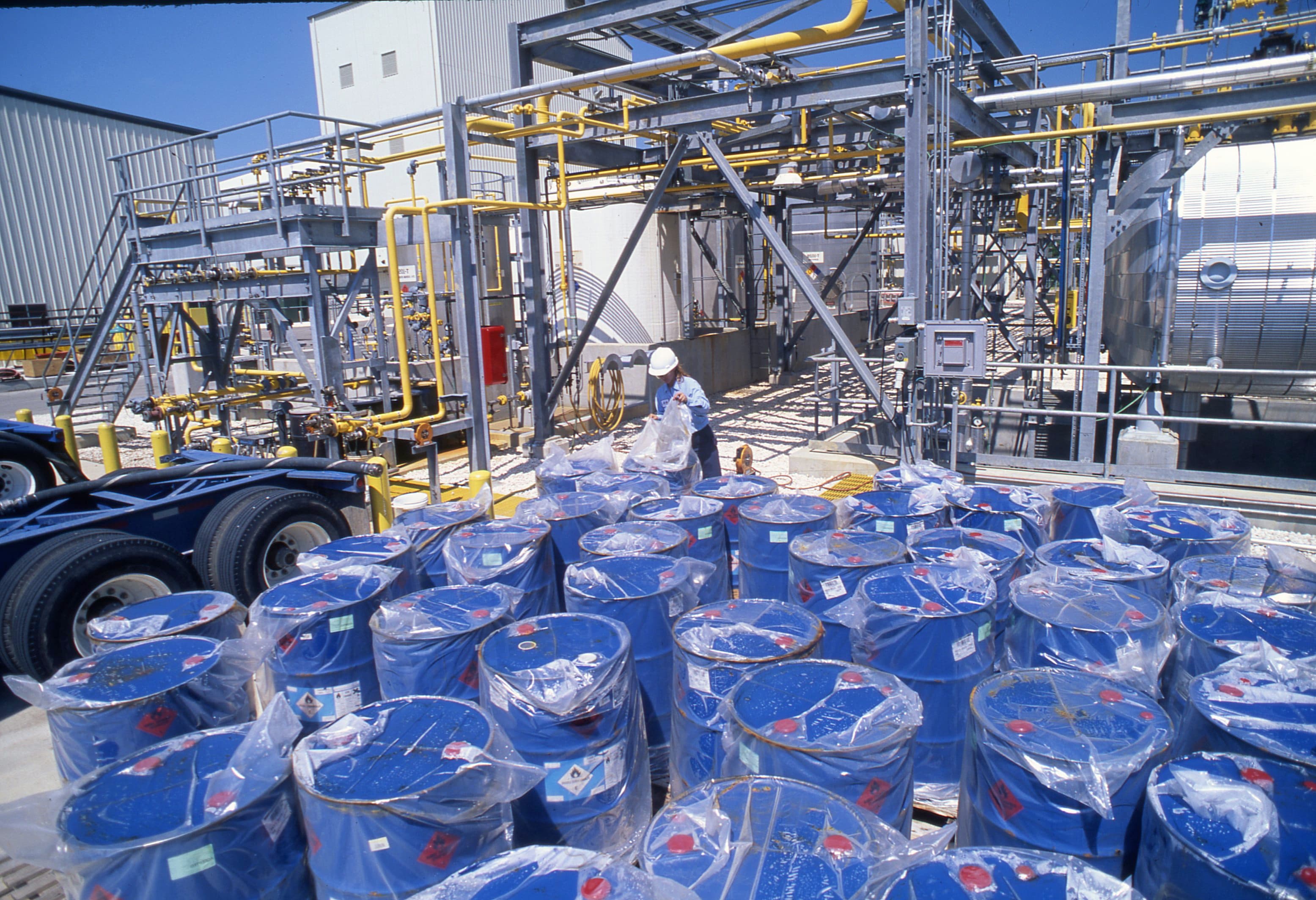
Fluor provided engineering and construction services for a 4-story, $36 million vitamin E manufacturing complex. The 70-acre greenfield site included a manufacturing facility, a warehouse, a maintenance building, administration offices, labs and cleanrooms in the packing areas. Fluor developed a quarter of the site. Vitamin E will be manufactured for human and animal consumption. Because of the extensive use of flammables and irritants, life safety and hazard reduction were especially critical. Production runs started in April 1998.
1998
Liquids Secondary Manufacturing Facility engineering commences
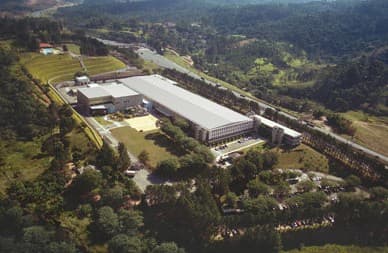
1998: Liquids Secondary Manufacturing Facility engineering commences
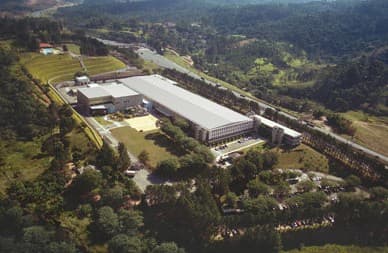
Wyeth and its affiliate Laboratorios Wyeth Whitehall relocated their secondary manufacturing facility for liquids, creams and tablets to a new site in São Paulo. A Fluor team performed the engineering to refurbish the existing facility and construct an additional building.
1999
Contract awarded for Abbott Bioresearch Facility in Worcester, Massachusetts
&w=3840&q=75)
1999: Contract awarded for Abbott Bioresearch Facility in Worcester, Massachusetts
&w=3840&q=75)
To facilitate the production of D2E7, a breakthrough monoclonal for the treatment of arthritis, Fluor delivered to Abbott this $35 million expansion, including an 8,000 square-foot warehouse. The 37,000 square-foot manufacturing facility was retrofitted into an existing shell, with Fluor providing multiple levels of engineering services, including process engineering for cell culture, harvest and purification.
1999
Gaeleo produces cytotoxically active products used in cancer treatment
&w=3840&q=75)
1999: Gaeleo produces cytotoxically active products used in cancer treatment
&w=3840&q=75)
Fluor has worked on a series of projects for Gaeleo, a subsidiary of Leo Pharmaceuticals in Sweden, at its High Quality Bulk Pharmaceuticals Facility in Cork, Ireland. These projects include an evaluation of a planned pilot plant facility during the development of a site master plan. Following the successful completion of the study work, Fluor performed front end design and engineering for the pilot plant and multiproduct small volume production unit for cytotoxically active products used in cancer treatment.
2000s
Fluor engineers, procures and constructs biopharmaceutical plants worldwide.
2000
Biologics Pilot Plant plays a critical role in the development of biologics-based products in the Merck pipeline
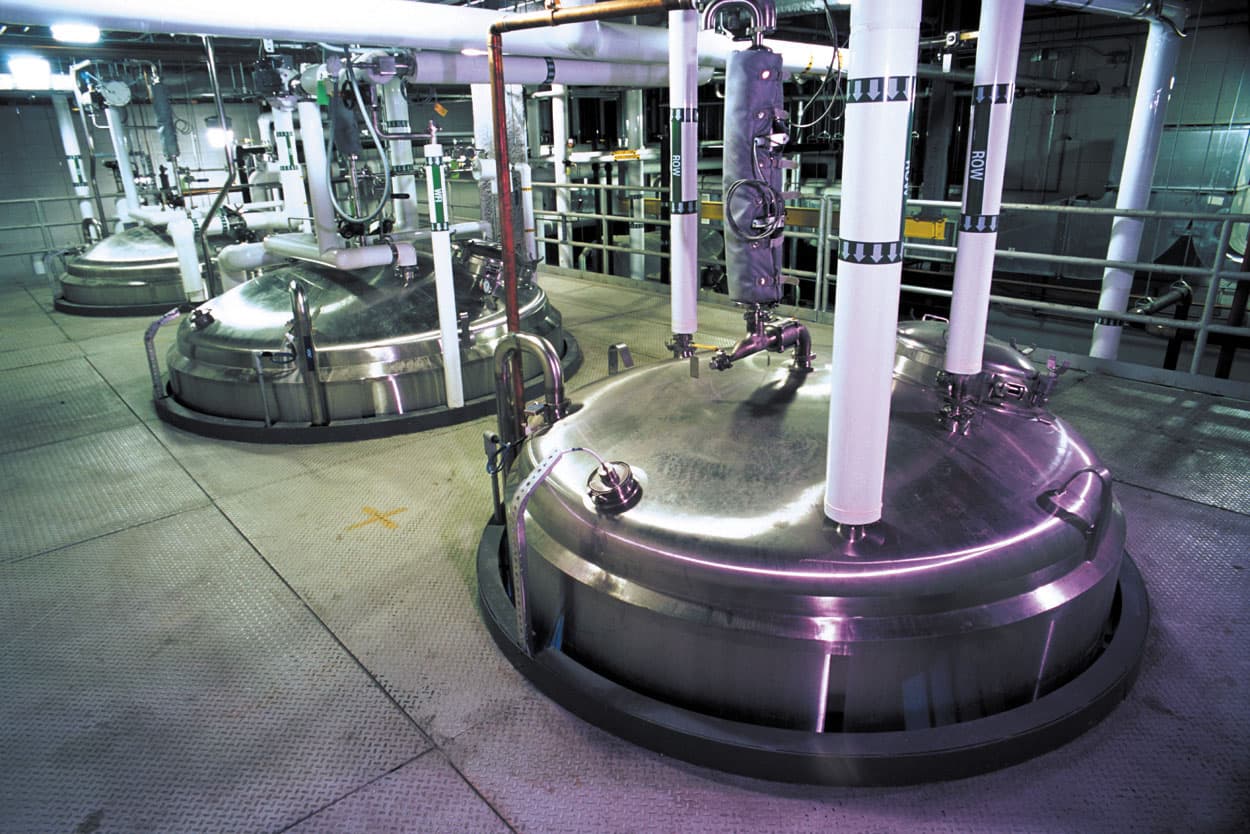
2000: Biologics Pilot Plant plays a critical role in the development of biologics-based products in the Merck pipeline
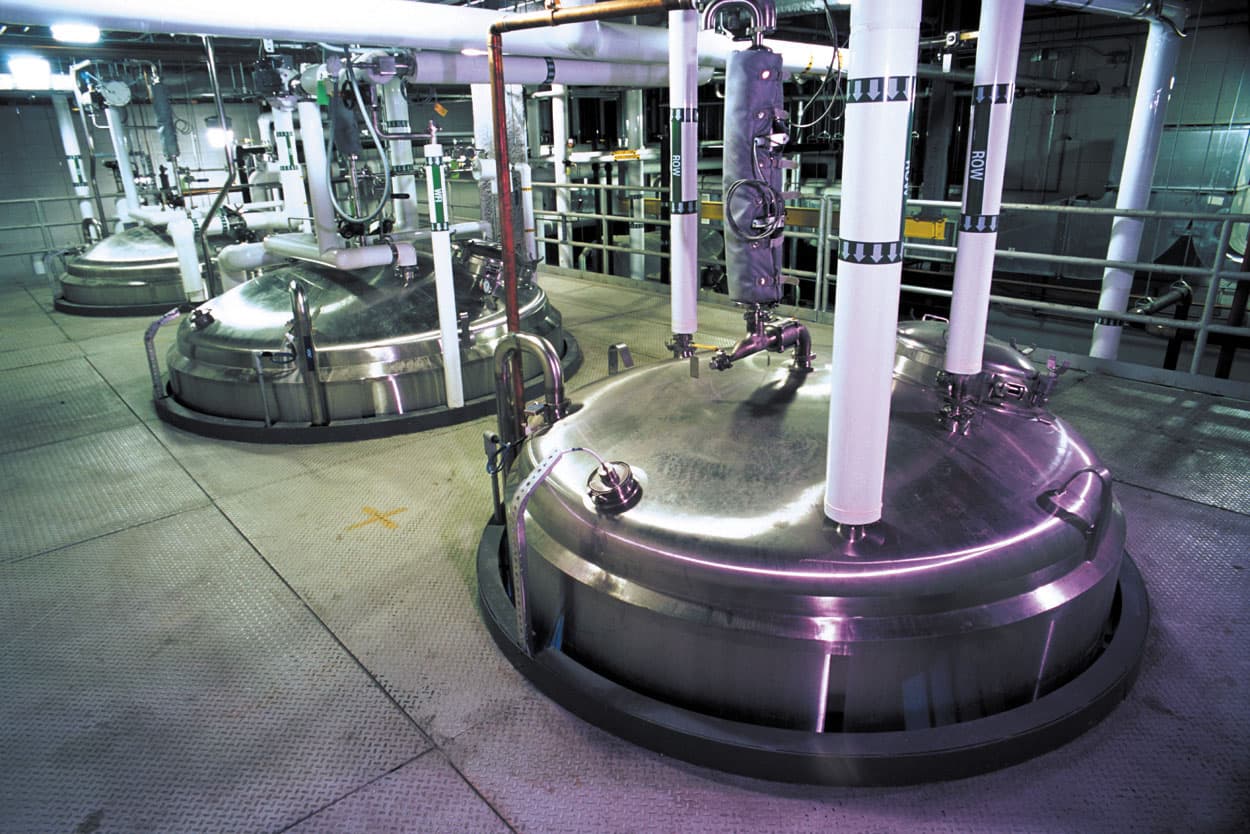
The 260,000-square-foot standalone facility, designed and built by Fluor, provided Merck with state-of-the-art bioprocess research and development capabilities. The architecturally striking facility was a four-story, steel-frame structure with three stories for pilot plant suites and a fourth story for R&D laboratories and offices.
2000
Pfizer Warner/Lambert Pharmaceutical Operations Expansion includes 5 major projects
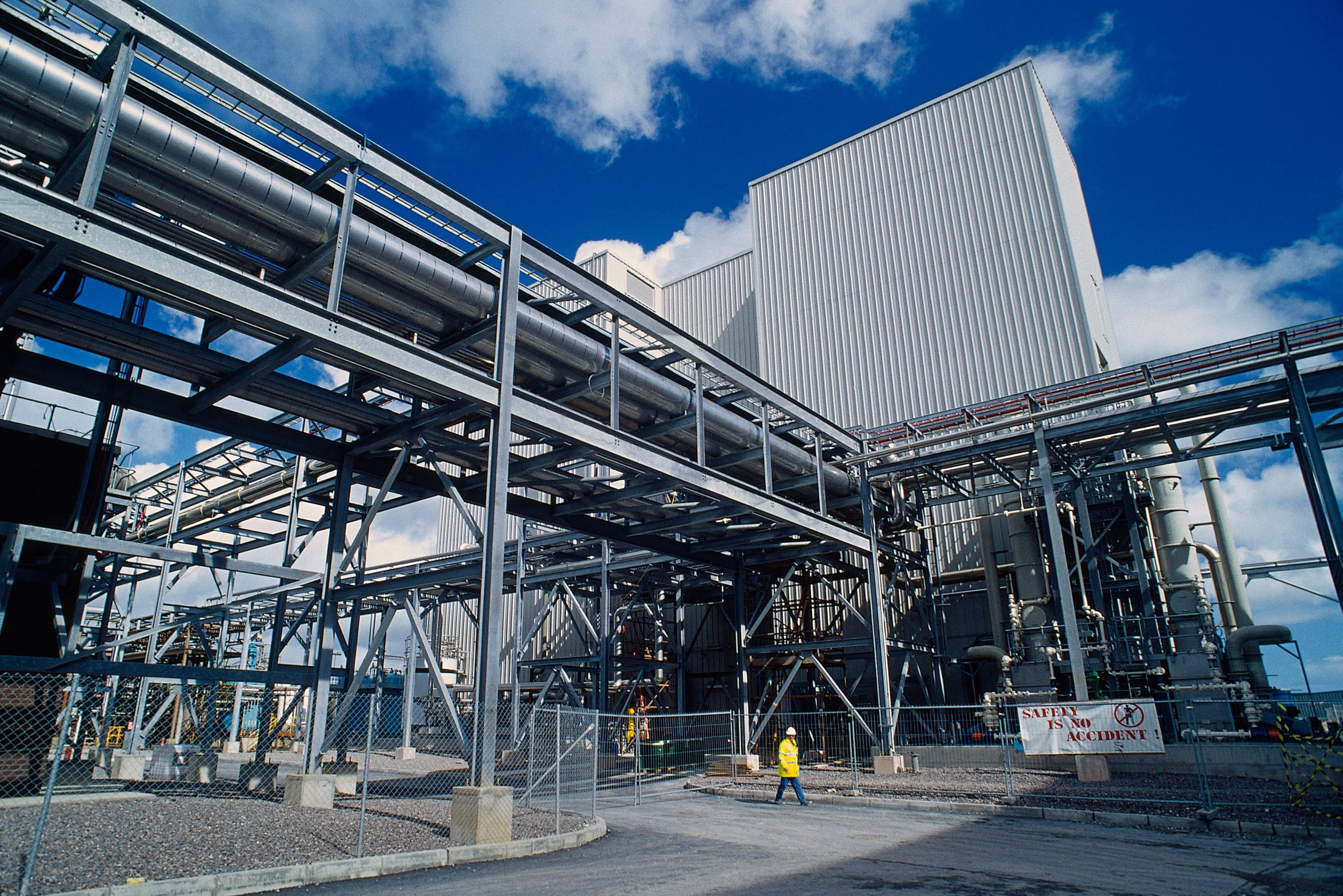
2000: Pfizer Warner/Lambert Pharmaceutical Operations Expansion includes 5 major projects
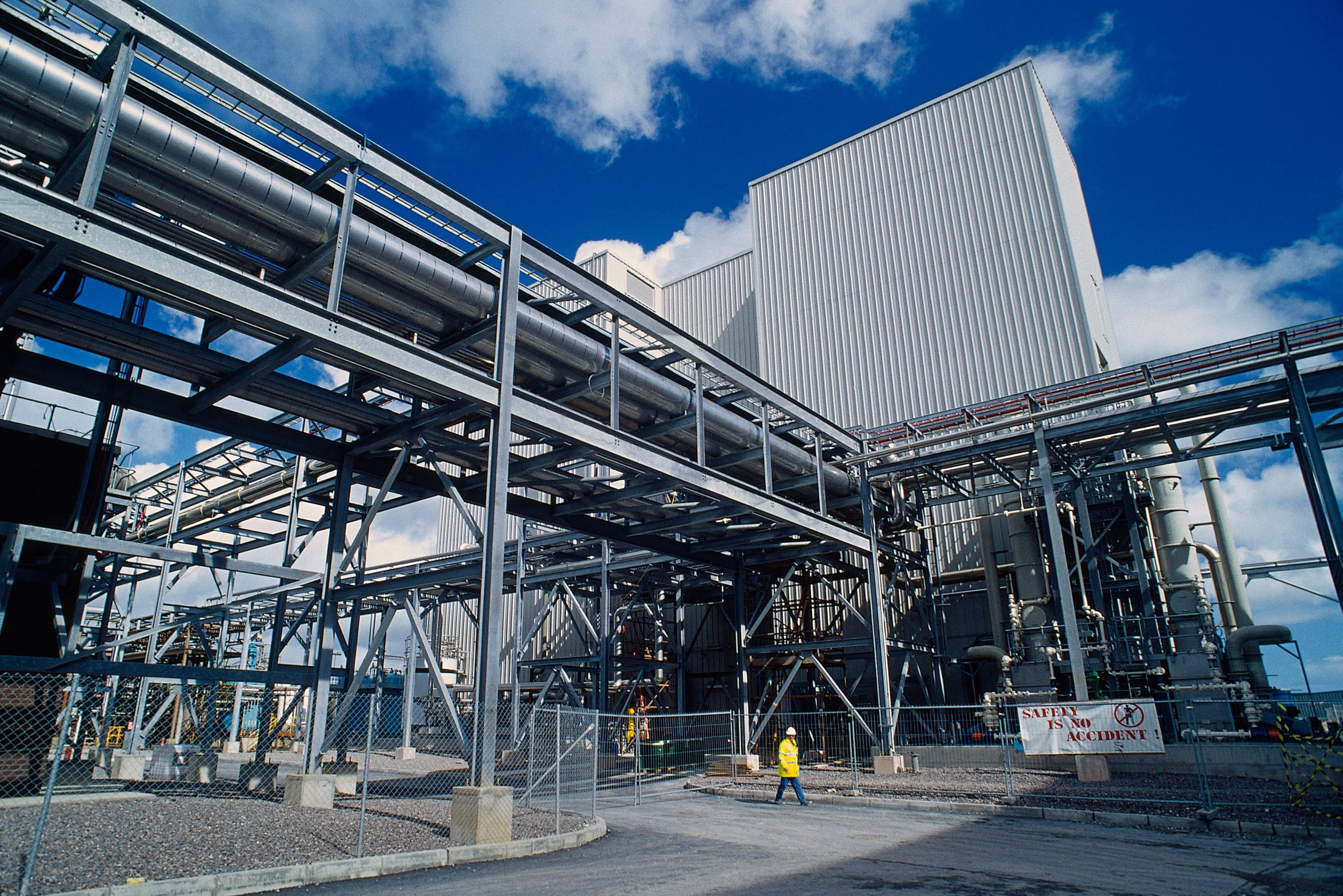
Pfizer is one of Ireland's largest pharmaceutical multinationals and leading pharmaceutical sector investor. Fluor provided EPCM and validation services for a $365 million pharmaceutical operations expansion program that included 5 major projects. The projects were a bulk-finishing facility, a multiproduct batch organic synthesis facility, two related organic synthesis facilities, and a central utility building. The Little Island, Cork, Ireland expansion program spanned four years, completing in 2000. The bulk pharmaceutical manufacturing complex produces Lipitor® (atorvastatin), the cholesterol-lowering compound that has become one of the most successful pharmaceutical products ever launched.
2001
Oceanside Manufacturing Complex preliminary design performed
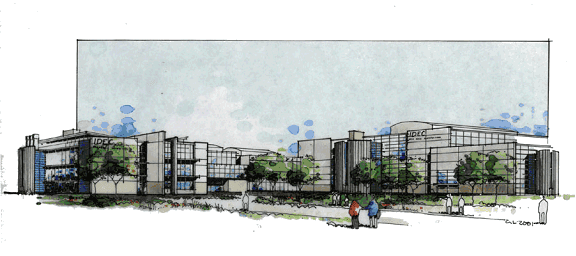
2001: Oceanside Manufacturing Complex preliminary design performed
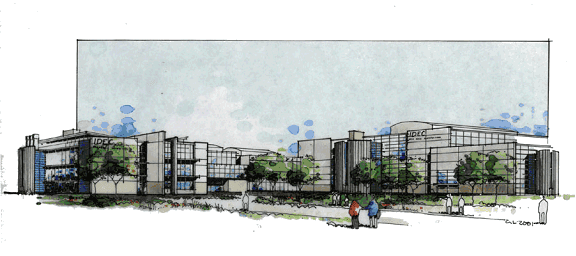
IDEC Pharmaceuticals selected Fluor to perform conceptual and preliminary design for the first phase of its new drug-manufacturing campus. Fluor provided engineering services for the main manufacturing building. The facility was a multiproduct current good manufacturing practices manufacturing facility designed to manufacture and purify mammalian cell culture-derived proteins for worldwide sale. The project consisted of three buildings: New IDEC Manufacturing Operations Building, lab/office building and warehouse.
2001
Biogen's Idec's Large Scale Manufacturing Facility delivered under budget and ahead of schedule
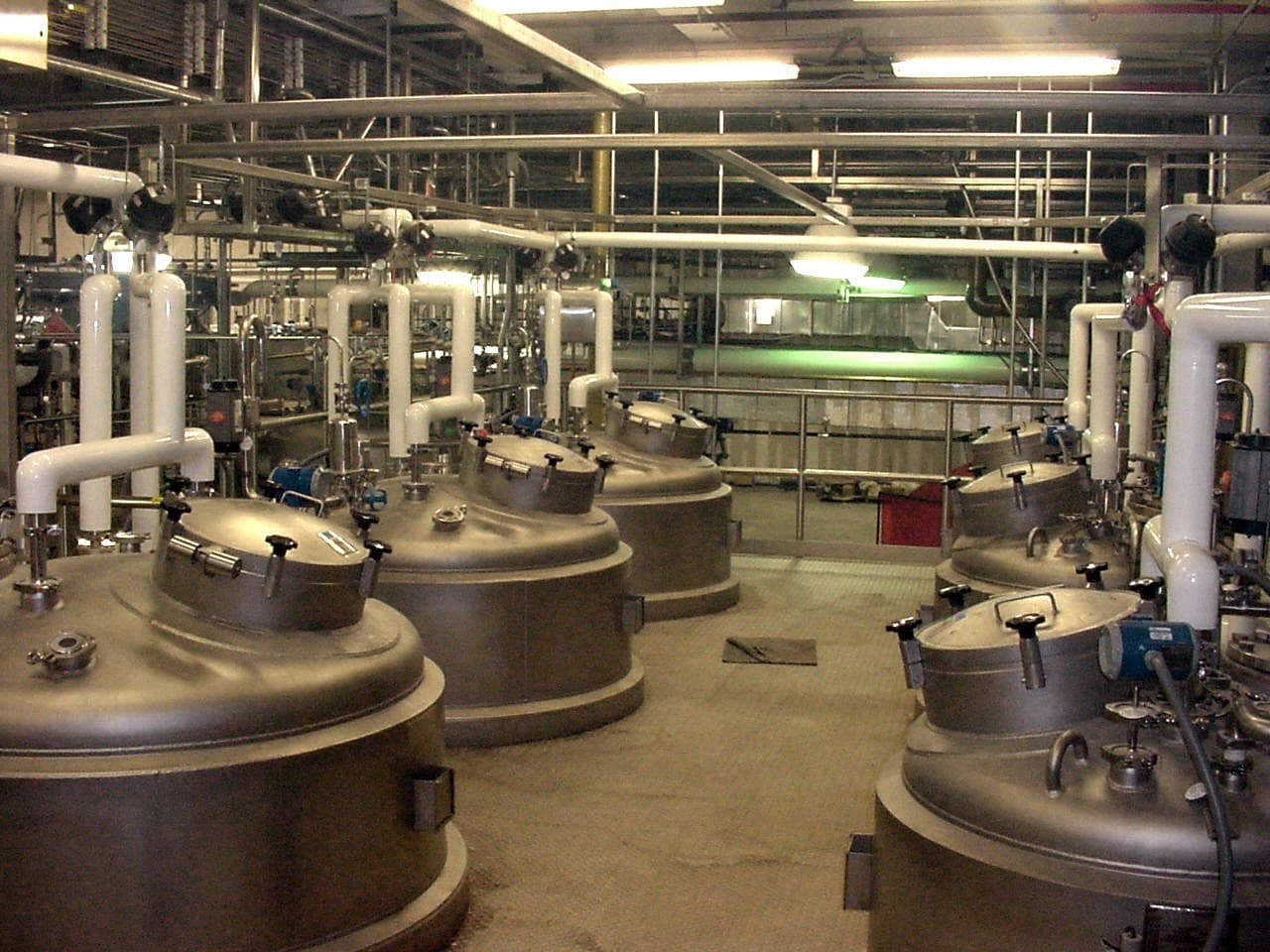
2001: Biogen's Idec's Large Scale Manufacturing Facility delivered under budget and ahead of schedule
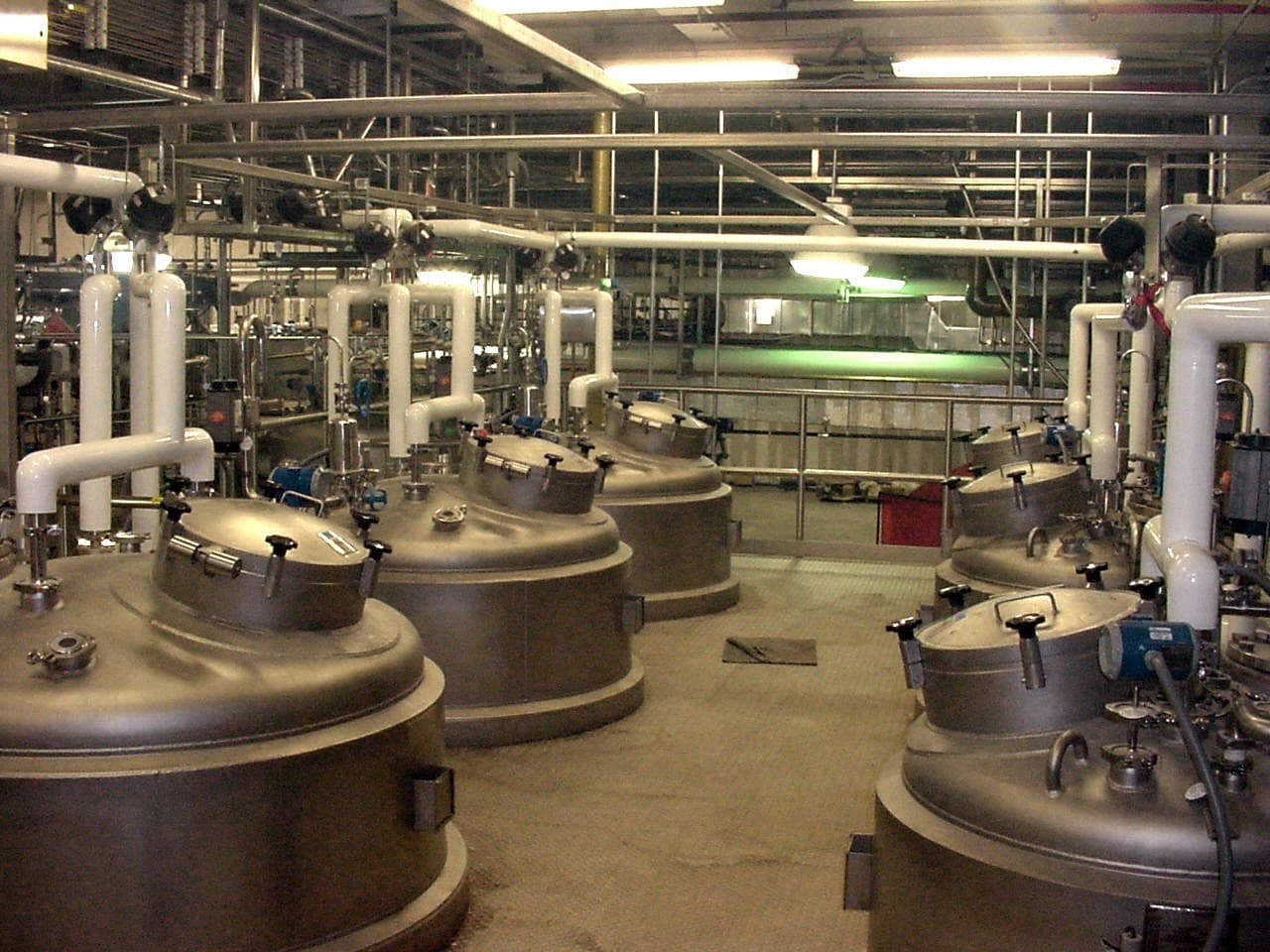
Fluor provided conceptual design, engineering, procurement, construction management and validation services to Biogen Idec for the company’s Large Scale Manufacturing facility in Research Triangle Park, North Carolina. Biogen Idec contracted with Fluor to design, build and validate a 250,000-square-foot LSM plant with the capability to run up to 120,000 liters of bioreactor capacity. At the time, it was one of the largest cell culture manufacturing facilities in the world.
2001
Fast-track AstraZeneca pharmaceutical facility project completed
&w=3840&q=75)
2001: Fast-track AstraZeneca pharmaceutical facility project completed
&w=3840&q=75)
Fluor provided a full range of EPCM services for a new bulk pharmaceutical purification facility for AstraZeneca. The Bristol, United Kingdom facility was designed to meet both the needs of a particular product and general-purpose future needs. The project scope included a filter dryer, a purified water generation and distribution system, and a new chilled glycol system.
2002
Fluor manages construction for Large Scale Cell Culture Manufacturing project in Rhode Island
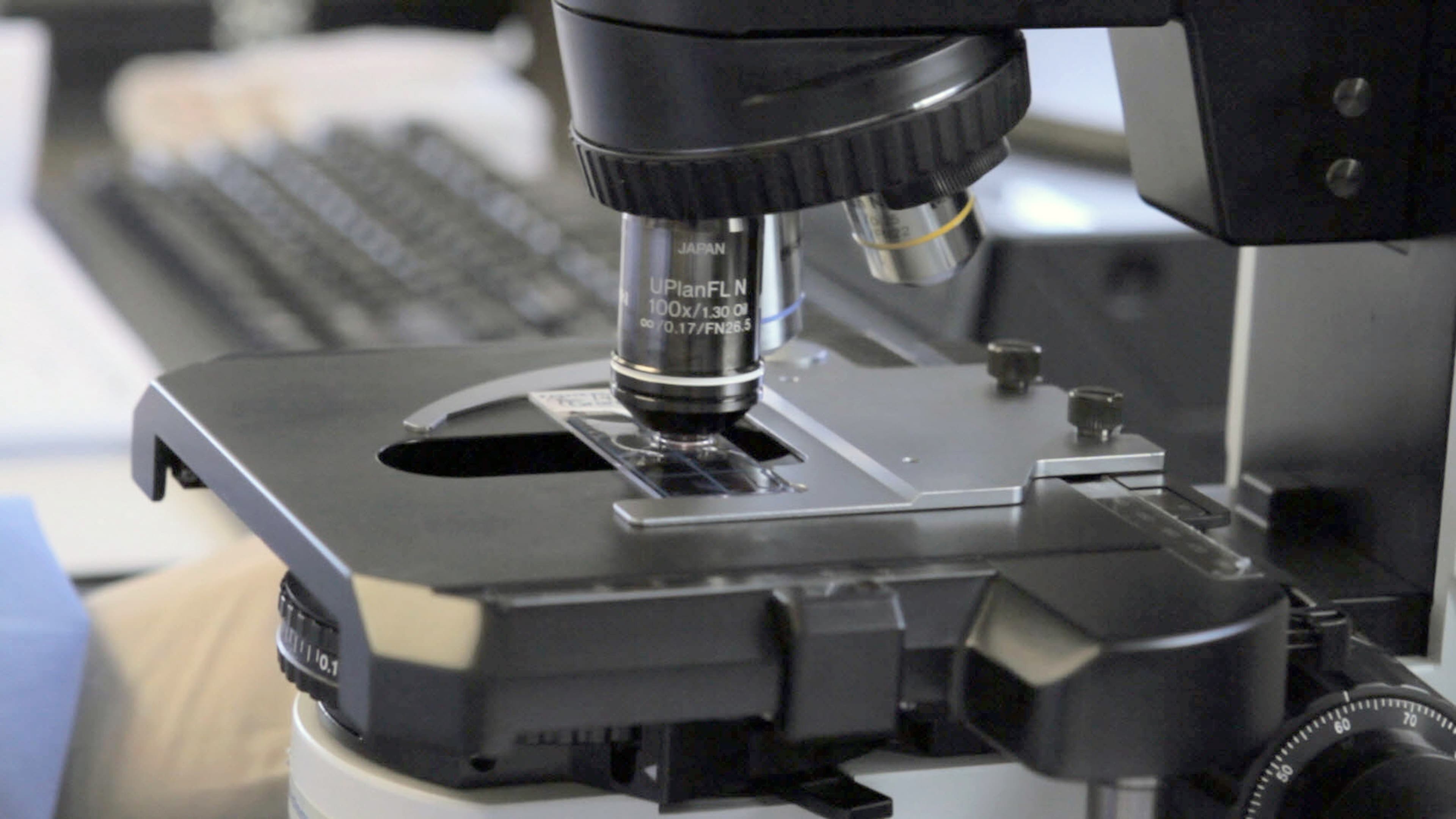
2002: Fluor manages construction for Large Scale Cell Culture Manufacturing project in Rhode Island
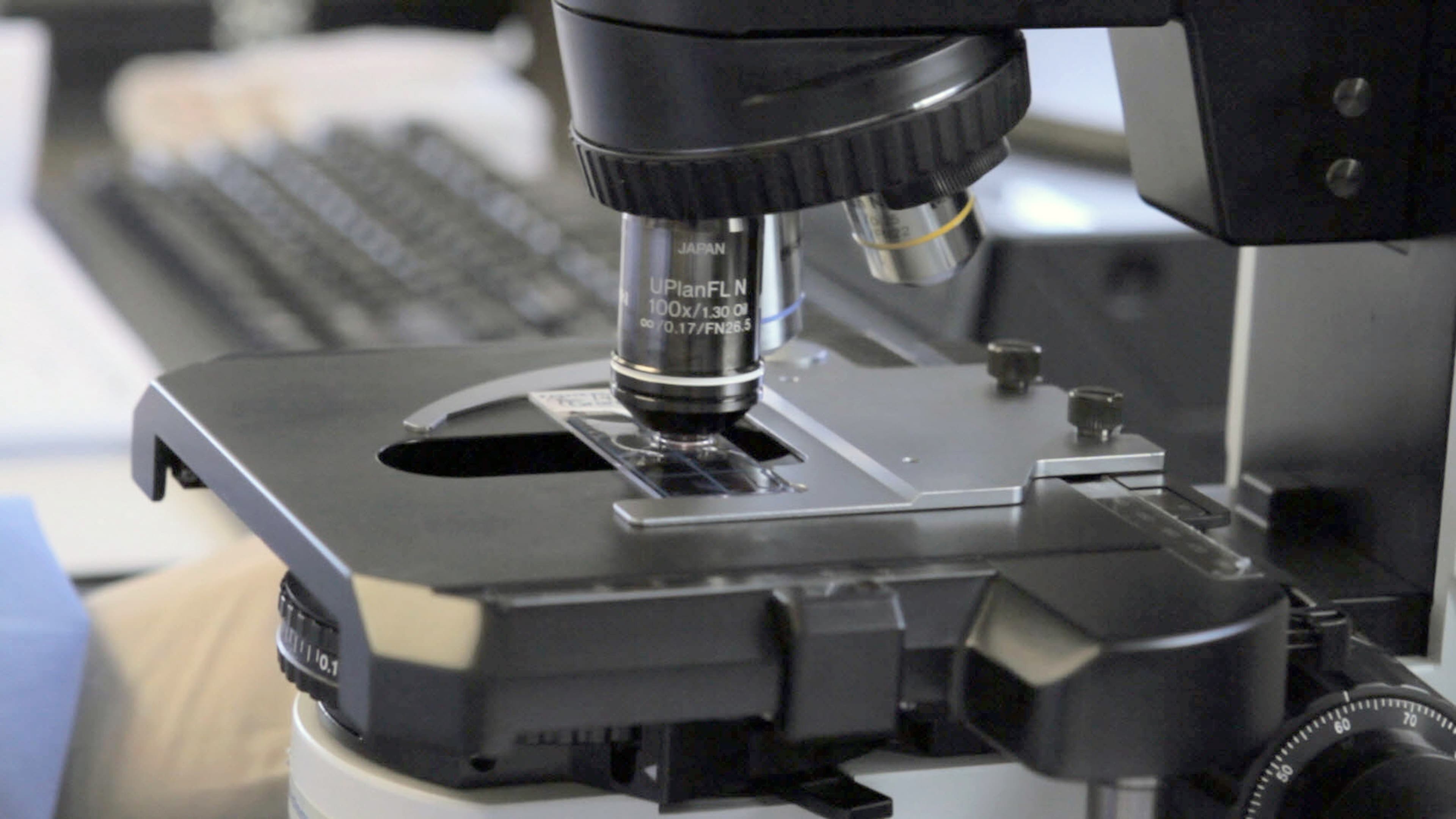
Fluor provided construction management services on this large-scale cell culture manufacturing facility. The project included the completion of construction and process work on a campus that provided the production capabilities to supply product to thousands of patients worldwide.
2003
BMS Cruiserath bulk manufacturing facility produces active pharmaceutical ingredients for a range of healthcare treatments
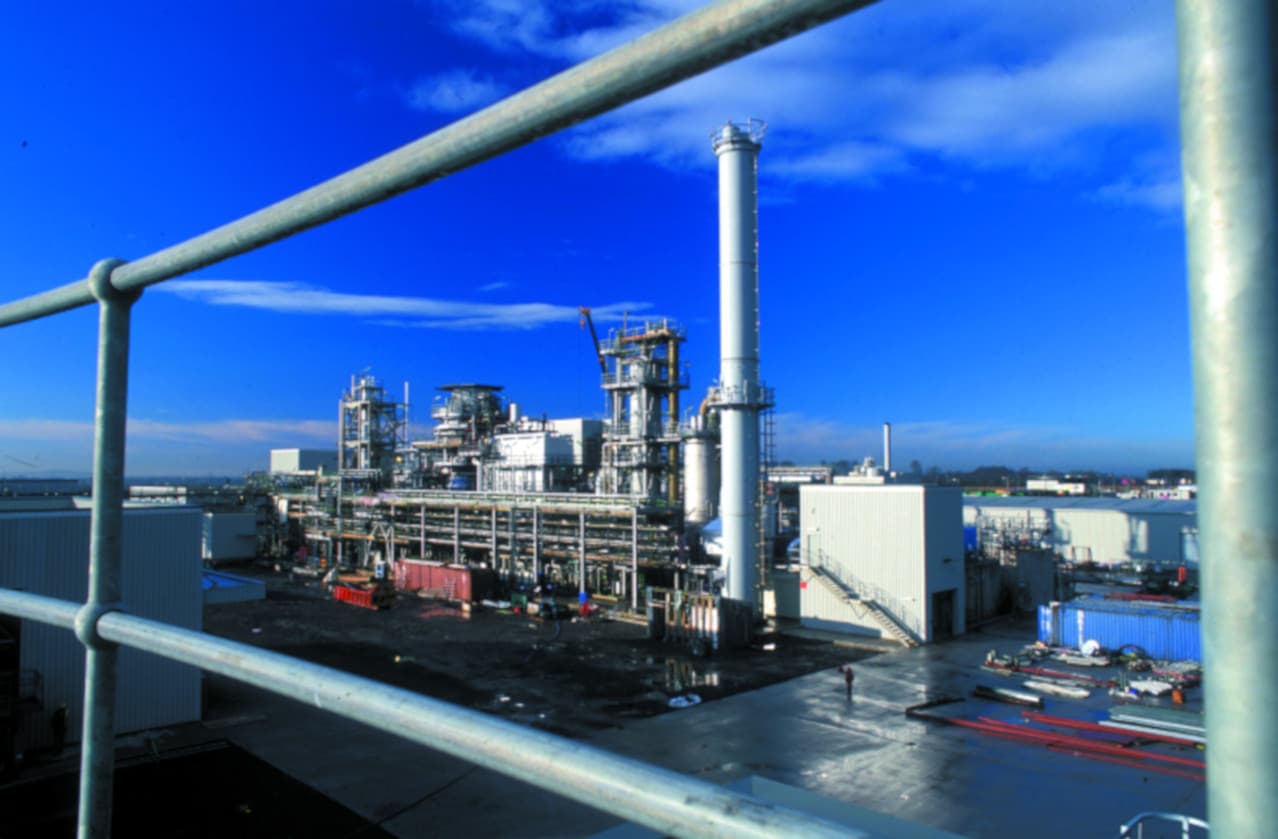
2003: BMS Cruiserath bulk manufacturing facility produces active pharmaceutical ingredients for a range of healthcare treatments
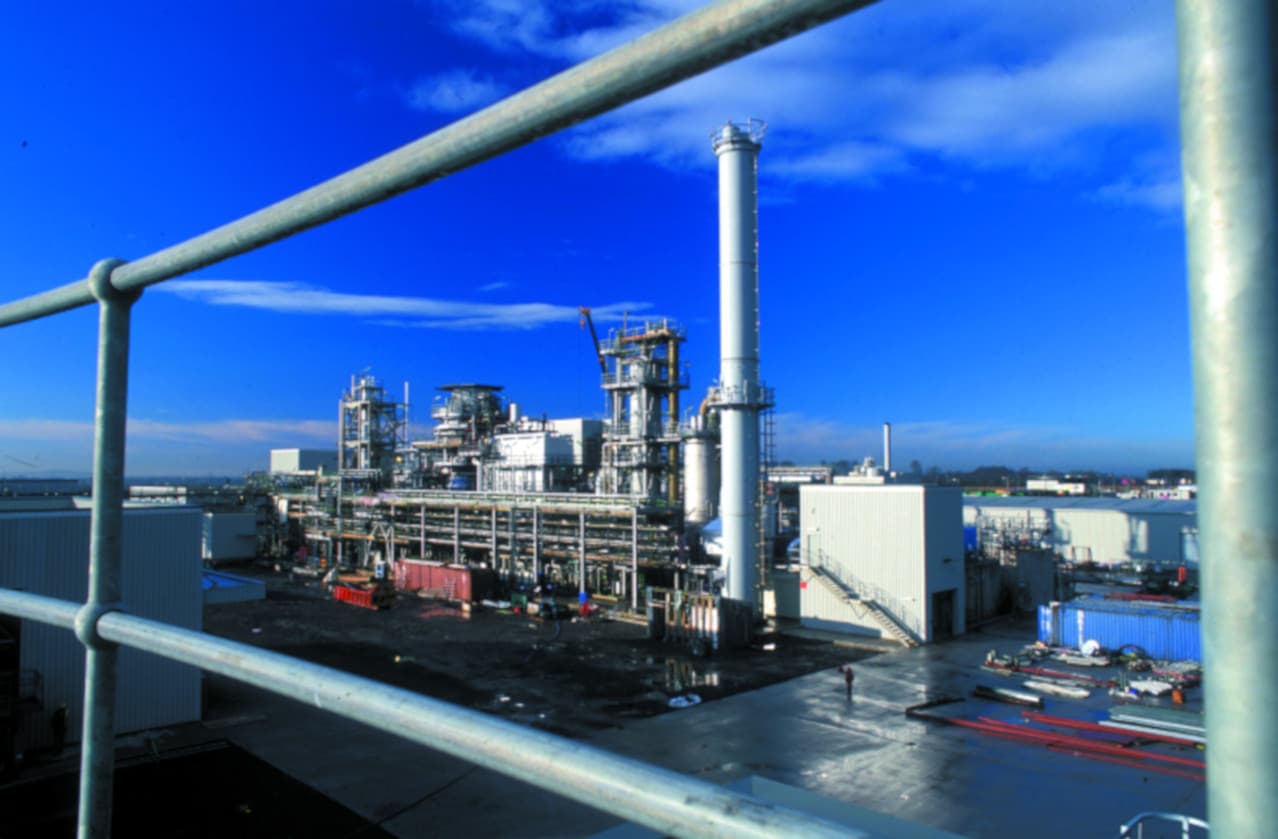
Bristol-Myers Squibb (BMS) is the Number 1 provider in anticancer therapies and a leader in development of cancer, heart disease, HIV/AIDS and mental illness treatments. This expansive $500 million greenfield project in Dublin, Ireland is one of the largest bulk operations in the world. In addition to being the construction management lead, BMS also selected Fluor to provide operational qualification, validation, start-up, and commissioning services. A distinct value for BMS was Fluor’s ability to deliver certainty to cost and schedule performance.
2003
Fluor selected to build one of the world's largest cell culture manufacturing facilities in Denmark
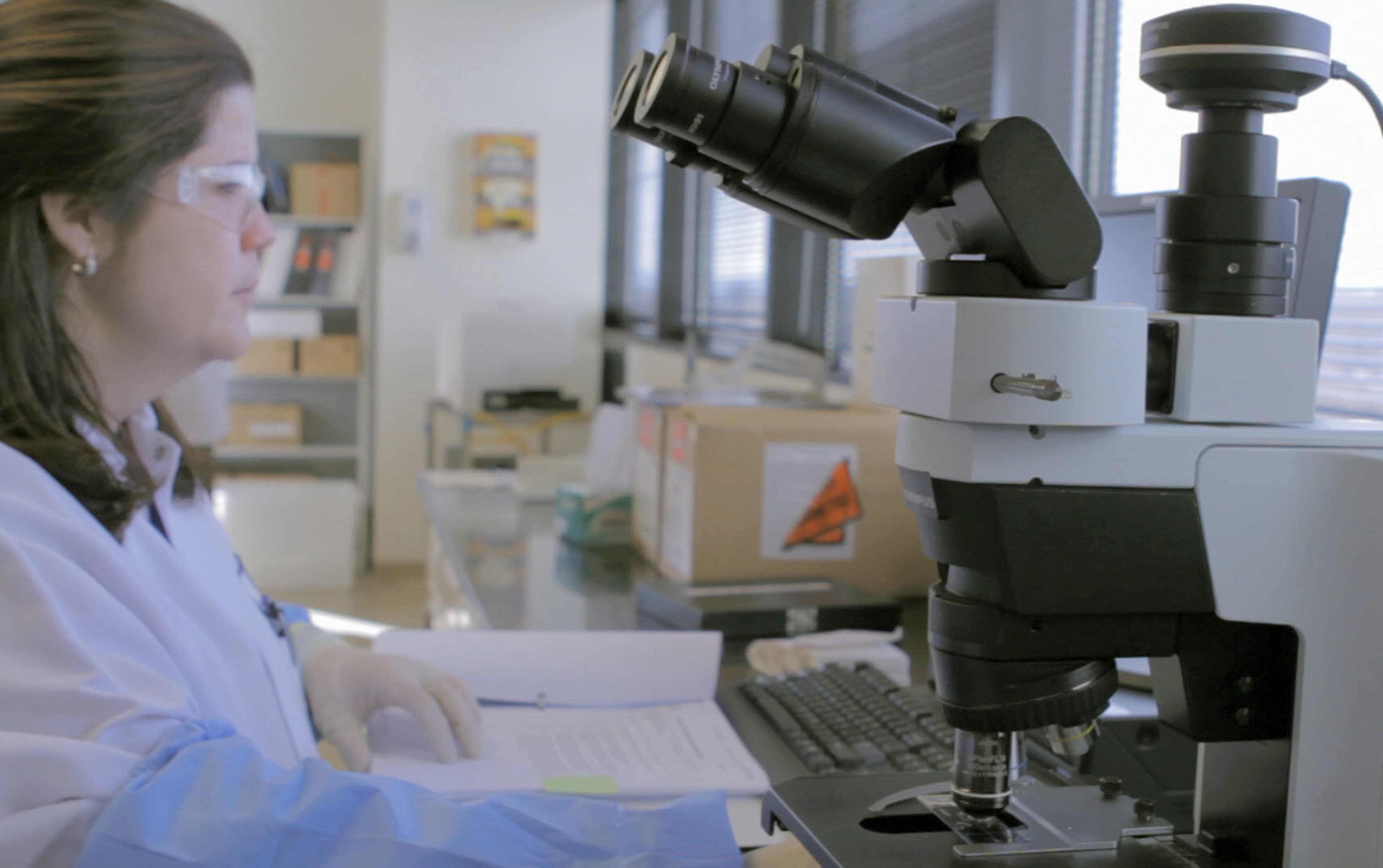
2003: Fluor selected to build one of the world's largest cell culture manufacturing facilities in Denmark
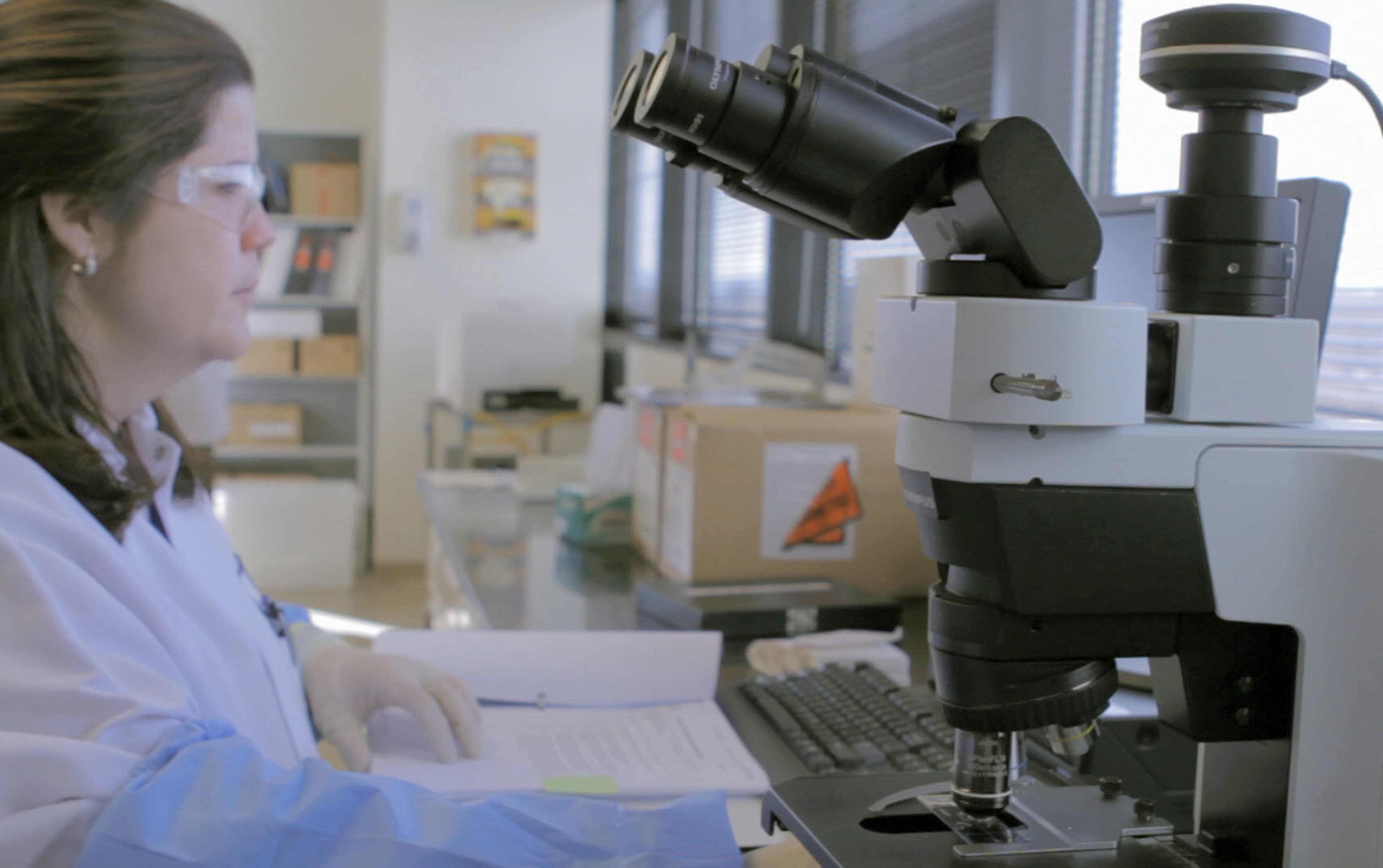
Fluor was selected by Biogen Inc., to build one of the world's largest cell culture manufacturing facilities in Hillerod, Denmark. Fluor performed program and construction management services for the large-scale manufacturing facility, which included a laboratory, administrative offices, warehouse and utility facilities.
2004
PDL BioPharma Commercial-Scale Biotech Manufacturing Facility commences production
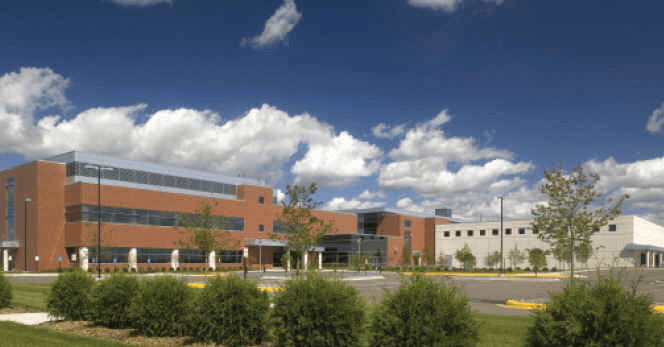
2004: PDL BioPharma Commercial-Scale Biotech Manufacturing Facility commences production
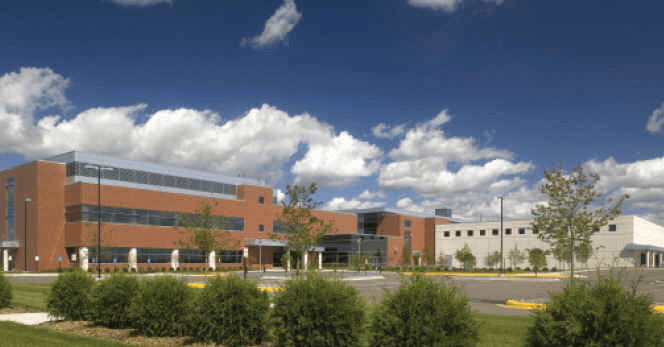
Fluor was chosen by PDL BioPharma to engineer a biotech manufacturing facility in Brooklyn Park, Minnesota. The large-scale facility was to produce antibody-based therapeutic drugs that treat autoimmune diseases, inflammatory conditions, and certain forms of cancer. Fluor provided front-end engineering, detailed design, procurement, automation, commissioning and validation for PDL's first commercial biotech manufacturing facility.
2005
Abbott ABL Cell Culture Manufacturing Plant validated in Barceloneta, Puerto Rico
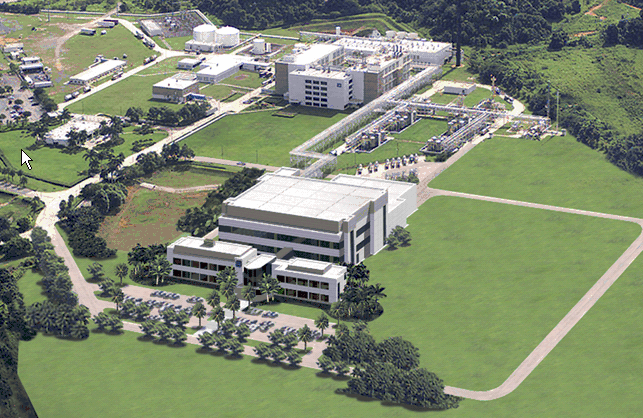
2005: Abbott ABL Cell Culture Manufacturing Plant validated in Barceloneta, Puerto Rico
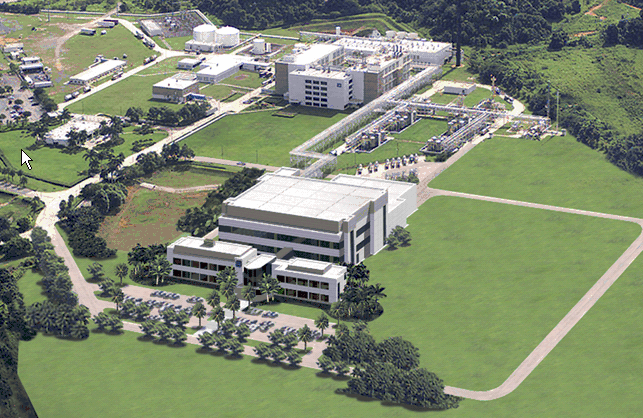
Fluor provided conceptual design, preliminary engineering, commissioning and validation for Abbott's ABL cell culture manufacturing plant. This fast-track project included a cell culture manufacturing building with two 12,000-liter fermenters, laboratory and office, warehouse and site utilities on a greenfield site.
2007
Genentech Cell Culture Plant named McGraw Hill Construction Best of '07, Best Industrial / Manufacturing project
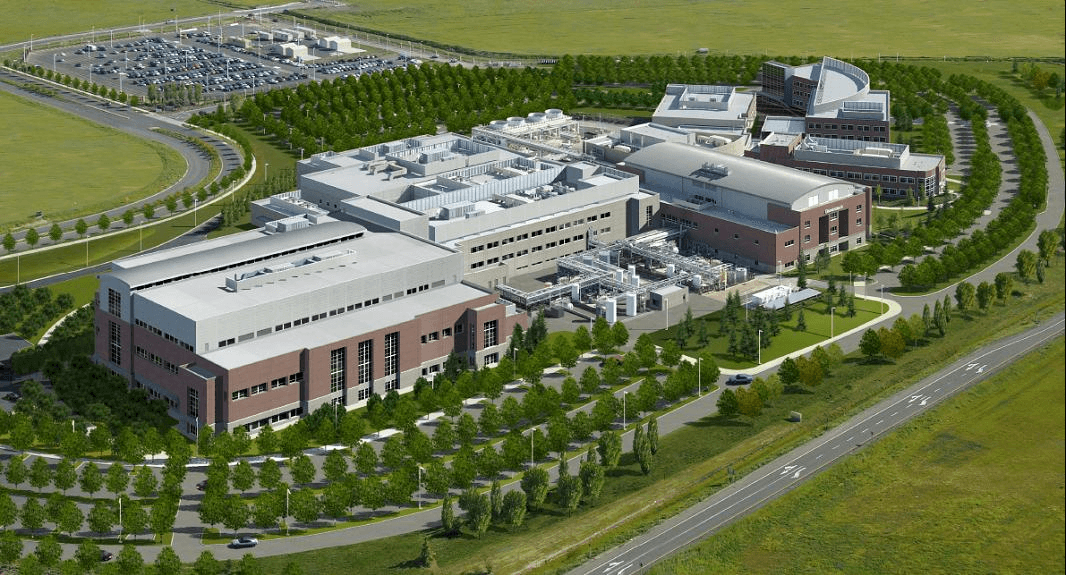
2007: Genentech Cell Culture Plant named McGraw Hill Construction Best of '07, Best Industrial / Manufacturing project
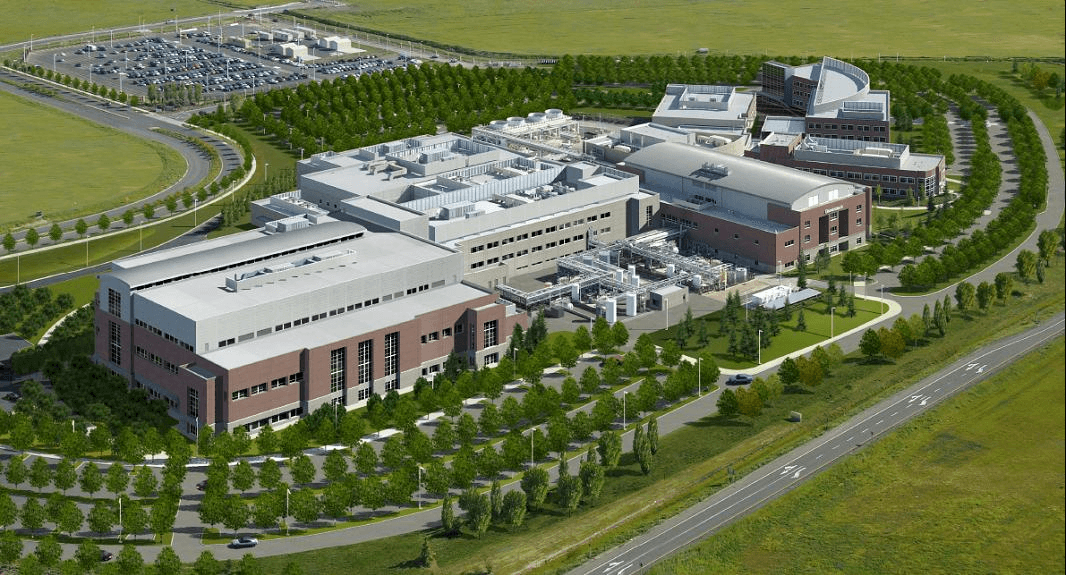
Fluor provided integrated engineering, procurement and validation for this large-scale cell culture manufacturing facility. The process design was based on Genentech’s CCP2 Greenfield Rituxan Manufacturing Process Requirements, Process Description for C2B8, 12K and rhuMAb VEGF G7 Cell Culture Process Description.
The facility is designed to process 25,000-liter batches of harvested cell culture fluid at six to seven recoveries per week (maximum). Built on unique seismic base isolators, all process support operations were designed in modular equipment arrays to secure the schedule.
2008
Pfizer facility produces cell culture-derived proteins for clinical testing and product launch
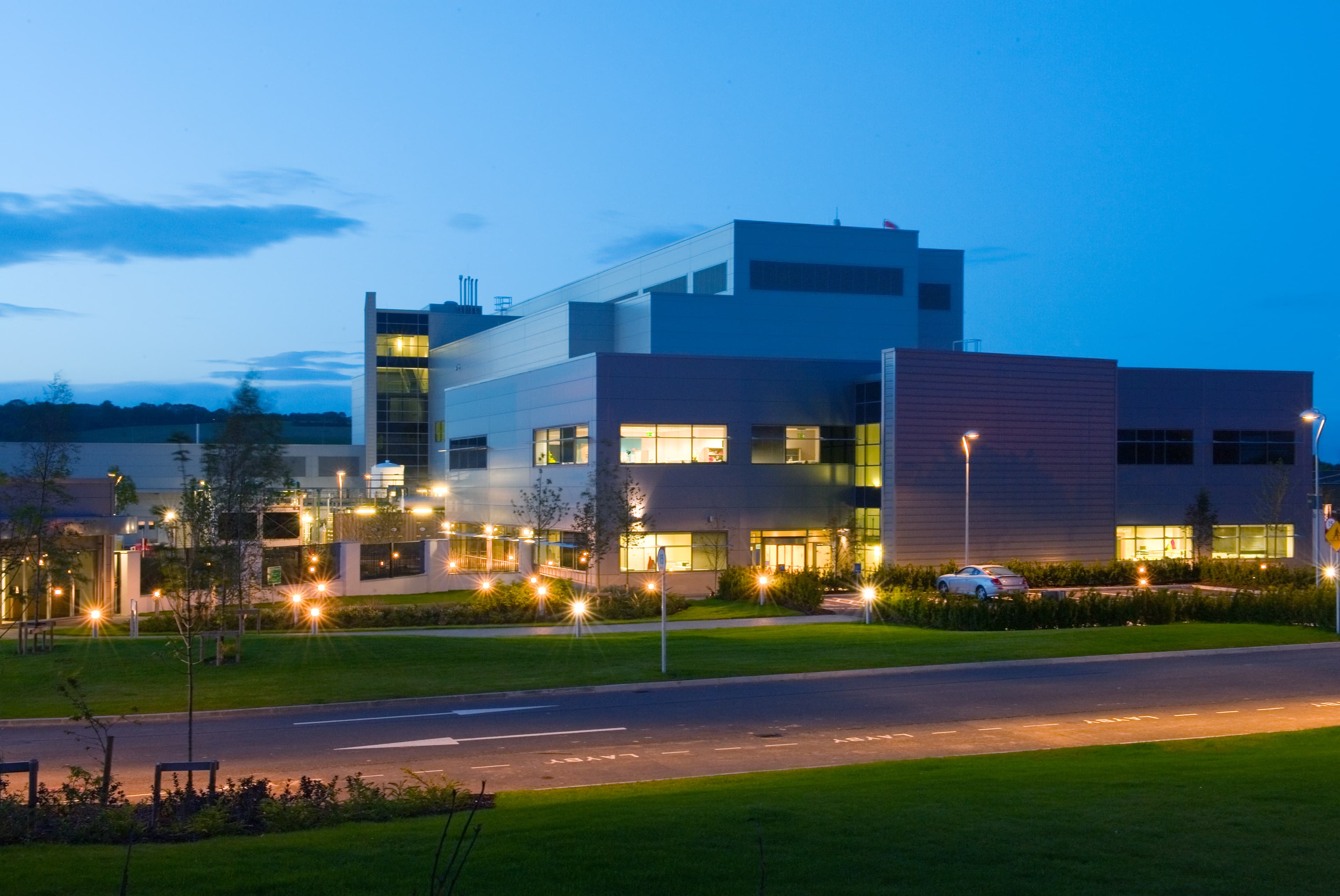
2008: Pfizer facility produces cell culture-derived proteins for clinical testing and product launch
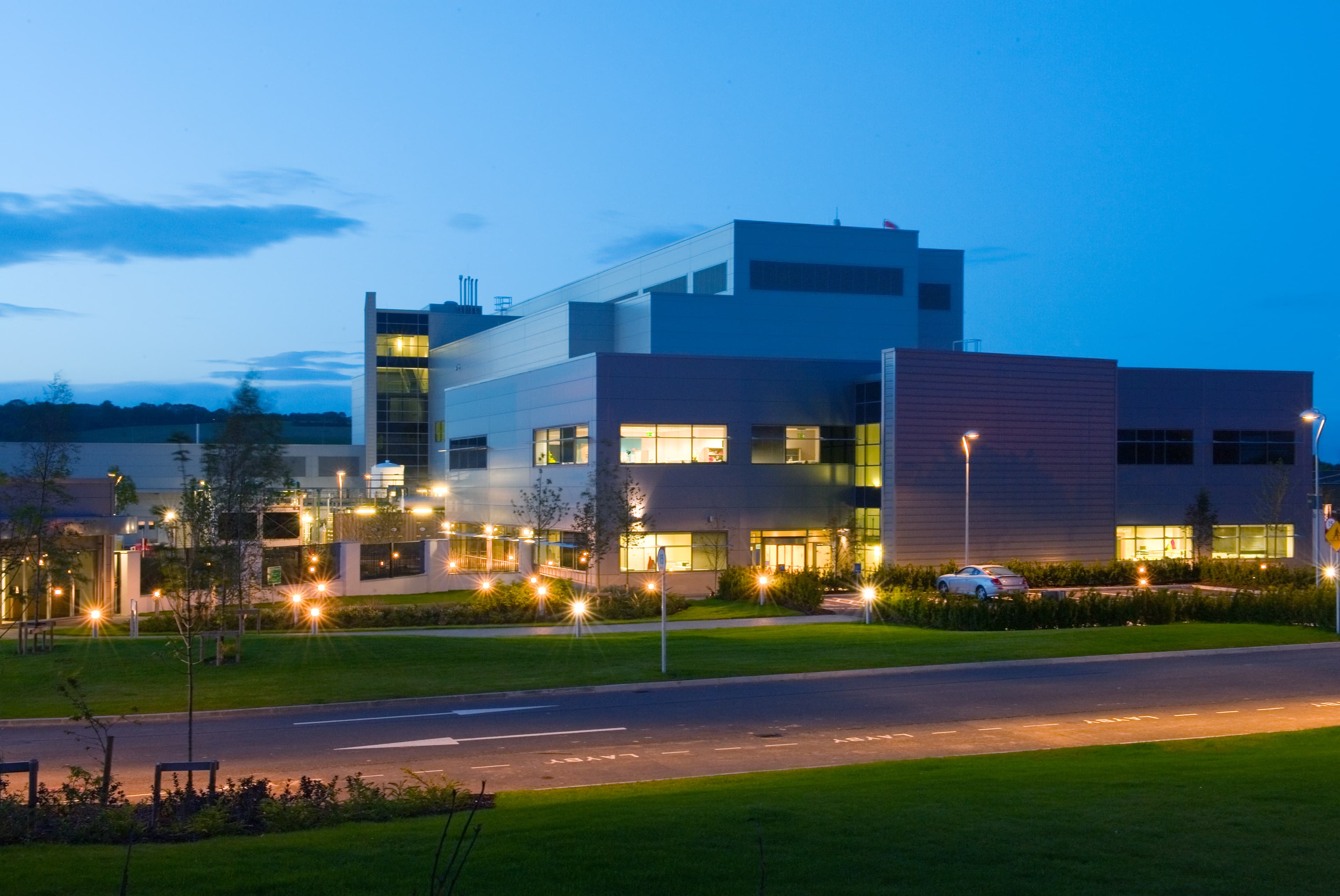
Fluor provided a study, engineering, and procurement services to Pfizer for the company's Small-Scale MAbs Facility in Shanbally, Ireland. Pfizer's MAbs SSF is a Phase III clinical trial and initial product launch facility to manufacture, purify, formulate and bulk fill mammalian cell culture-derived protein. The design of the facility provides for maximum flexibility, using disposable bag technology. Fluor implemented value engineering on the project, and Pfizer accepted ideas totaling $4.6 million in savings, a 2.3 percent reduction in total installed cost. Pfizer was awarded the ISPE Facility of the Year Award for Sustainability in 2010.
2010s
Fluor recognized by ISPE for design and build expertise.
2011
ISPE recognizes MedImmune Frederick Manufacturing Center Biotech Expansion
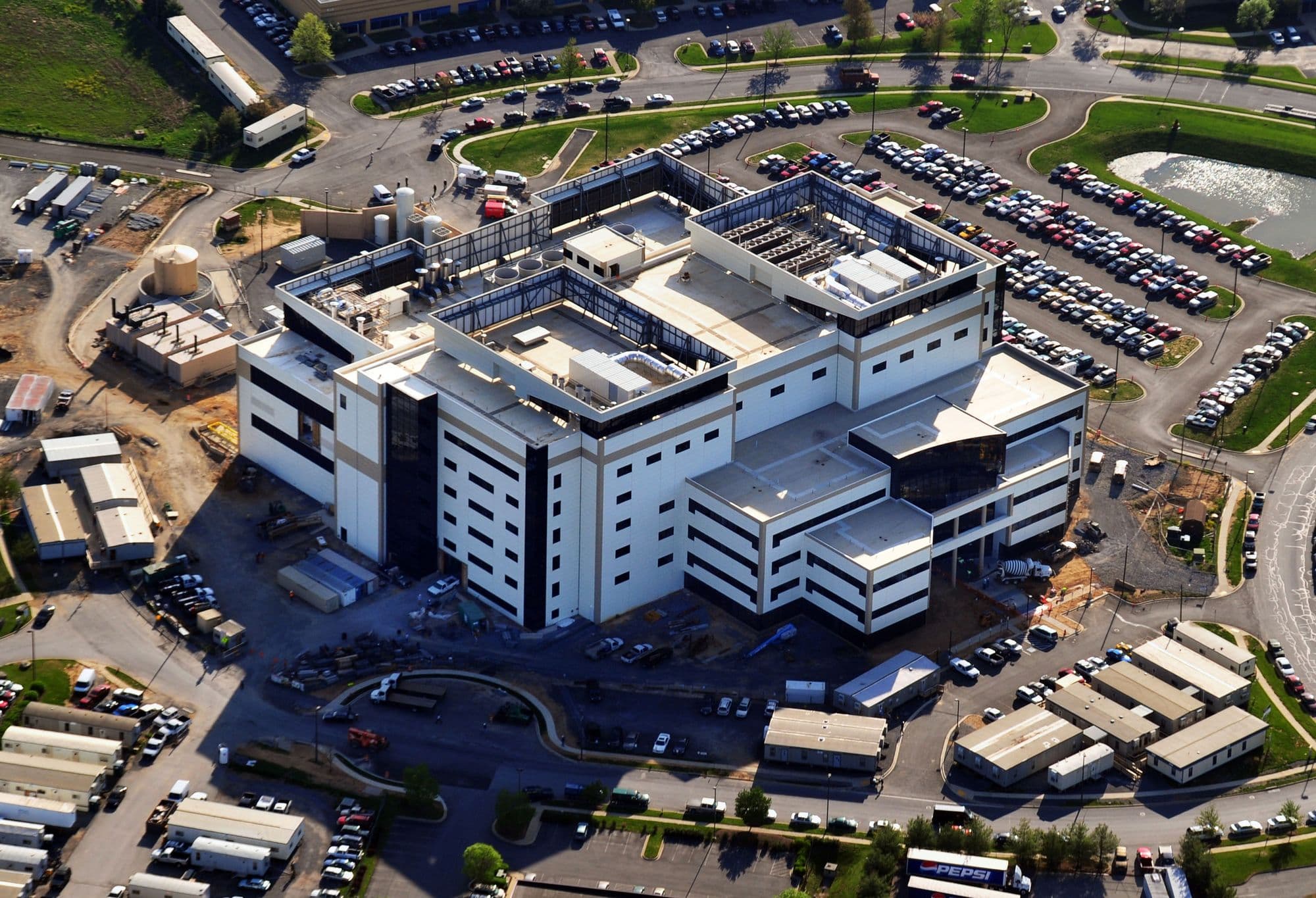
2011: ISPE recognizes MedImmune Frederick Manufacturing Center Biotech Expansion
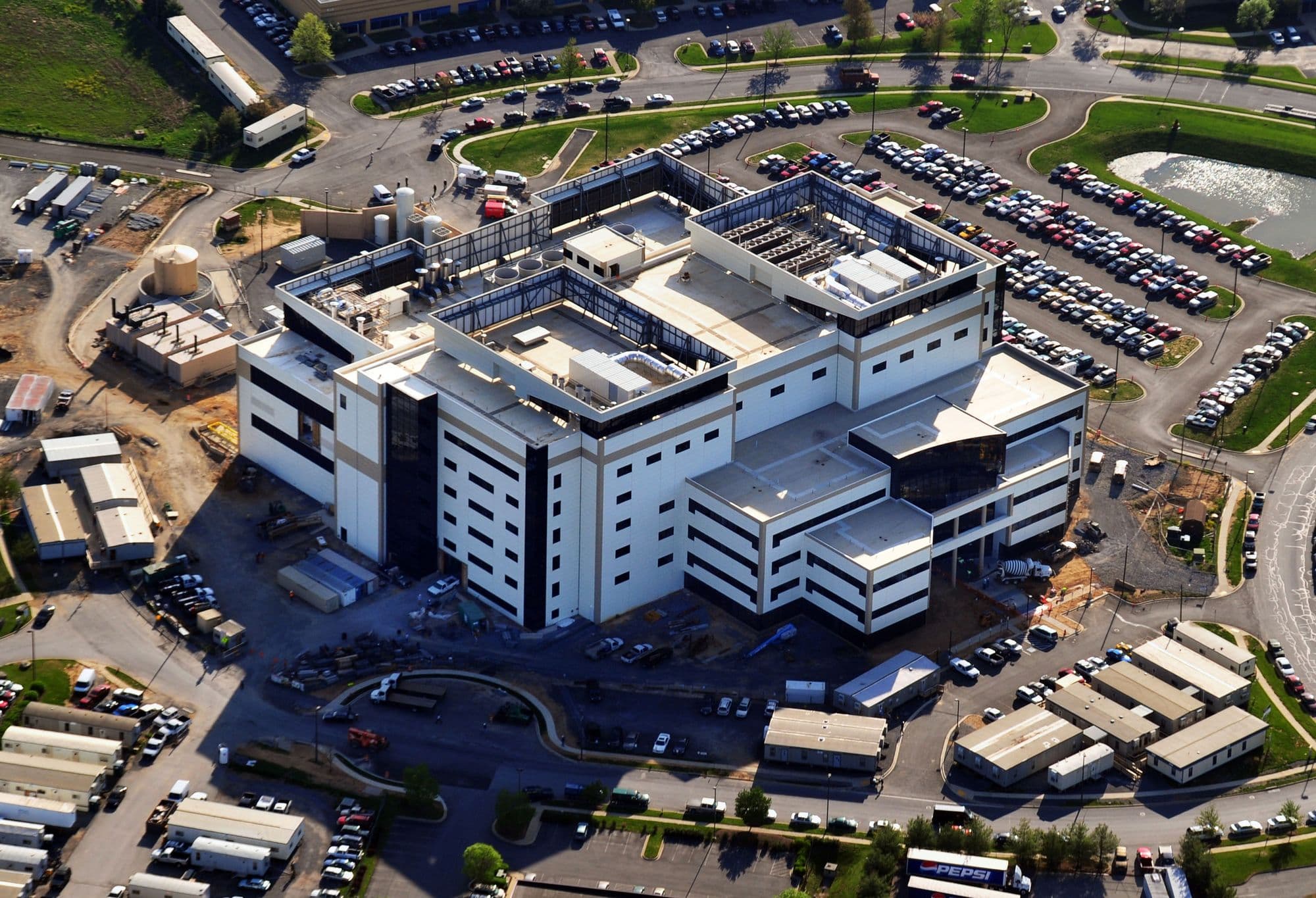
MedImmune is a leading biotechnology company and operates as a wholly owned subsidiary of AstraZeneca. The Frederick Manufacturing Center (FMC) is a large-scale mammalian cell culture manufacturing facility. Fluor provided construction management, start-up, commissioning and qualification services for MedImmune’s FMC Expansion Project. The project was recognized in 2011 with two awards by International Society for Pharmaceutical Engineering (ISPE): Overall ISPE Facility of the Year Awards Overall Winner and Facility of the Year for Project Execution.
2014
Grifols' North Fractionation Facility named ISPE Facility of the Year for Project Execution
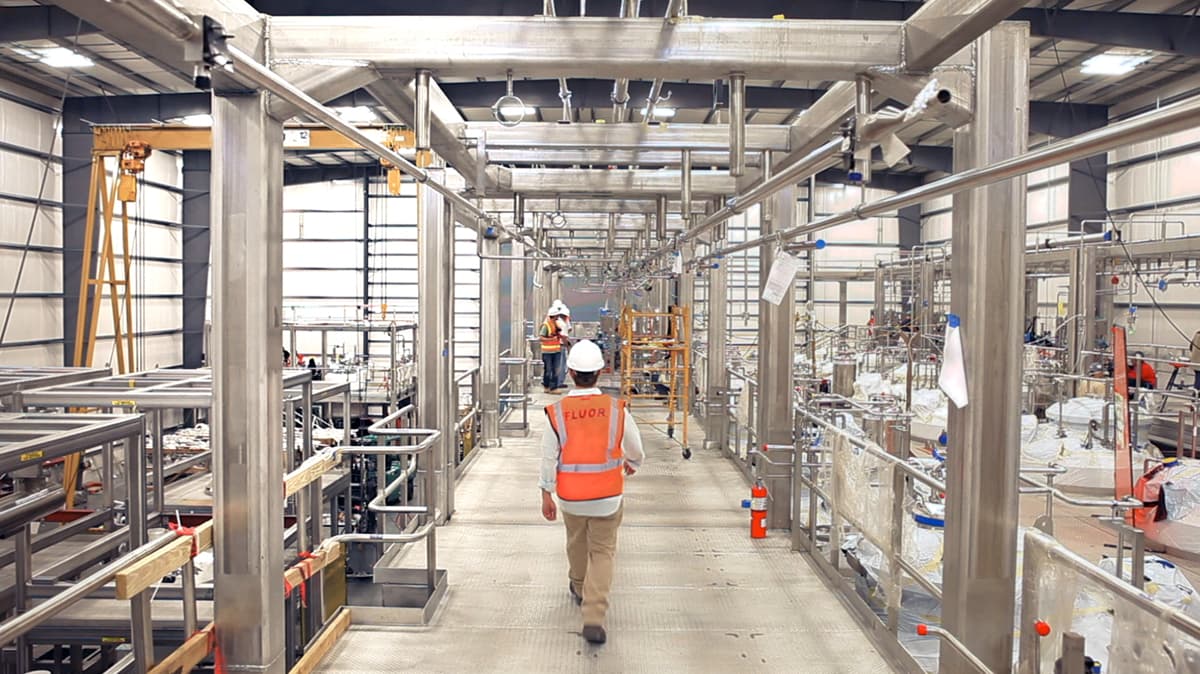
2014: Grifols' North Fractionation Facility named ISPE Facility of the Year for Project Execution
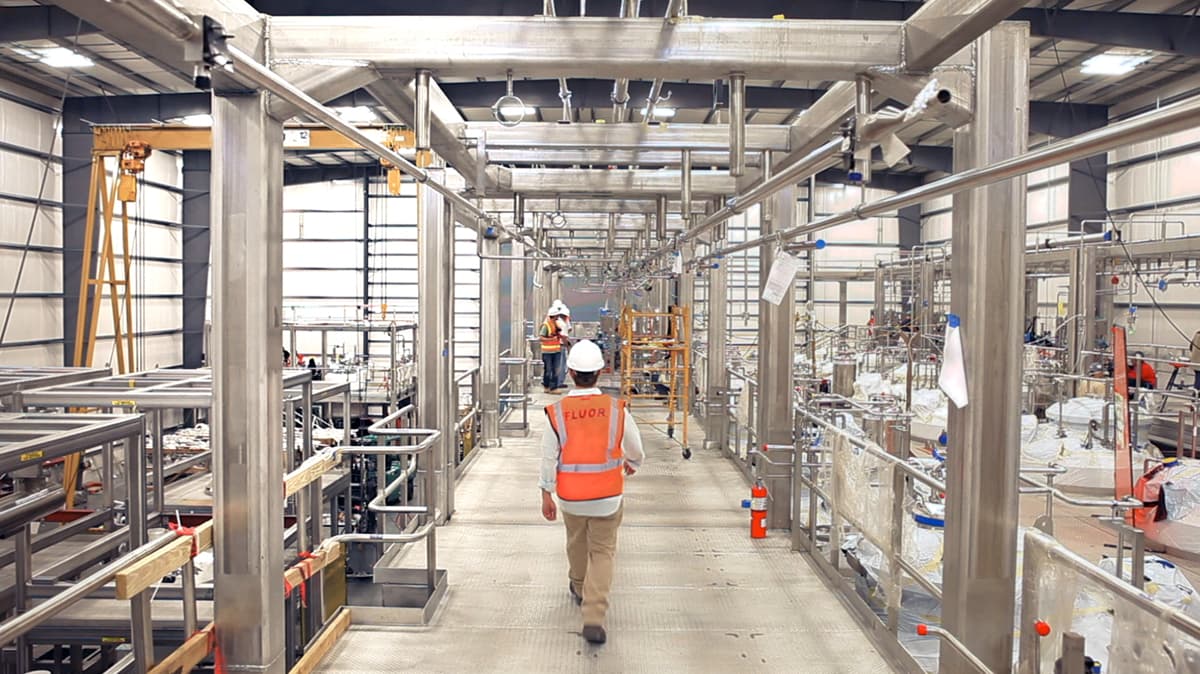
Grifols chose Fluor to be their partner on the engineering, procurement, construction management and commissioning of the North Fractionation Facility, or NFF project. Augmenting the existing Clayton facility in North Carolina, the NFF project includes a 160,000-square-foot fractionation expansion which allows Grifols a 43 percent increase over their previous plasma processing capacity. In 2014, Grifols' North Fractionation Facility was named the ISPE 2014 Facility of the Year for Project Execution.
2015
FLUOR IM℠ improves biotech clients' cost and schedule competitiveness through modular production spaces
&w=3840&q=75)
2015: FLUOR IM℠ improves biotech clients' cost and schedule competitiveness through modular production spaces
&w=3840&q=75)
Fluor's innovative Intelligent Modular Solutions, Fluor IM, provides clients with a cost-effective, highly flexible, and robust facility designed to provide clinical trial and initial product launch manufacturing capacity for single-use biopharmaceutical processes. Using Fluor IM, a facility is designed for rapid deployment and supports global regulatory compliance.
2016
Shire Biologics Facility manufactures life-sustaining therapies
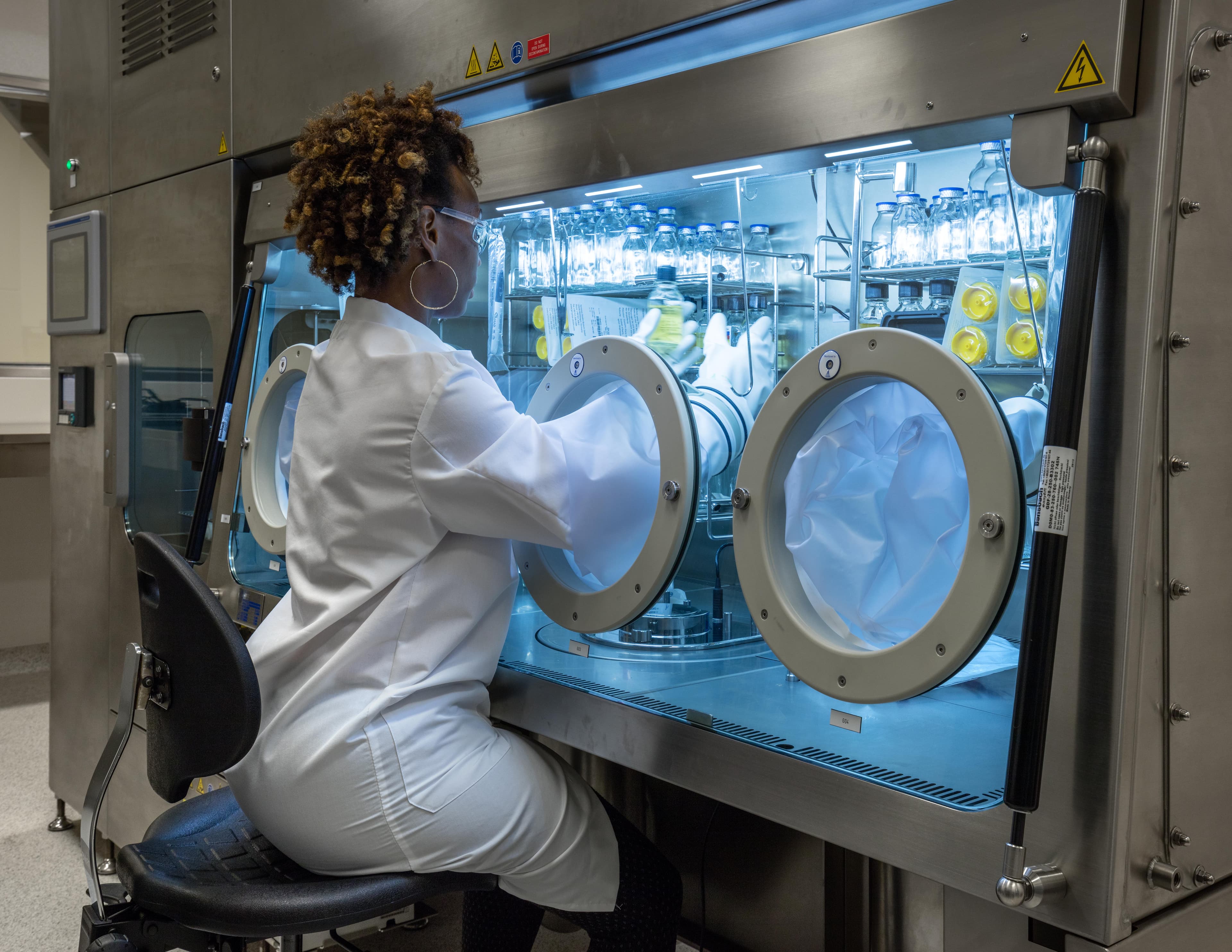
2016: Shire Biologics Facility manufactures life-sustaining therapies
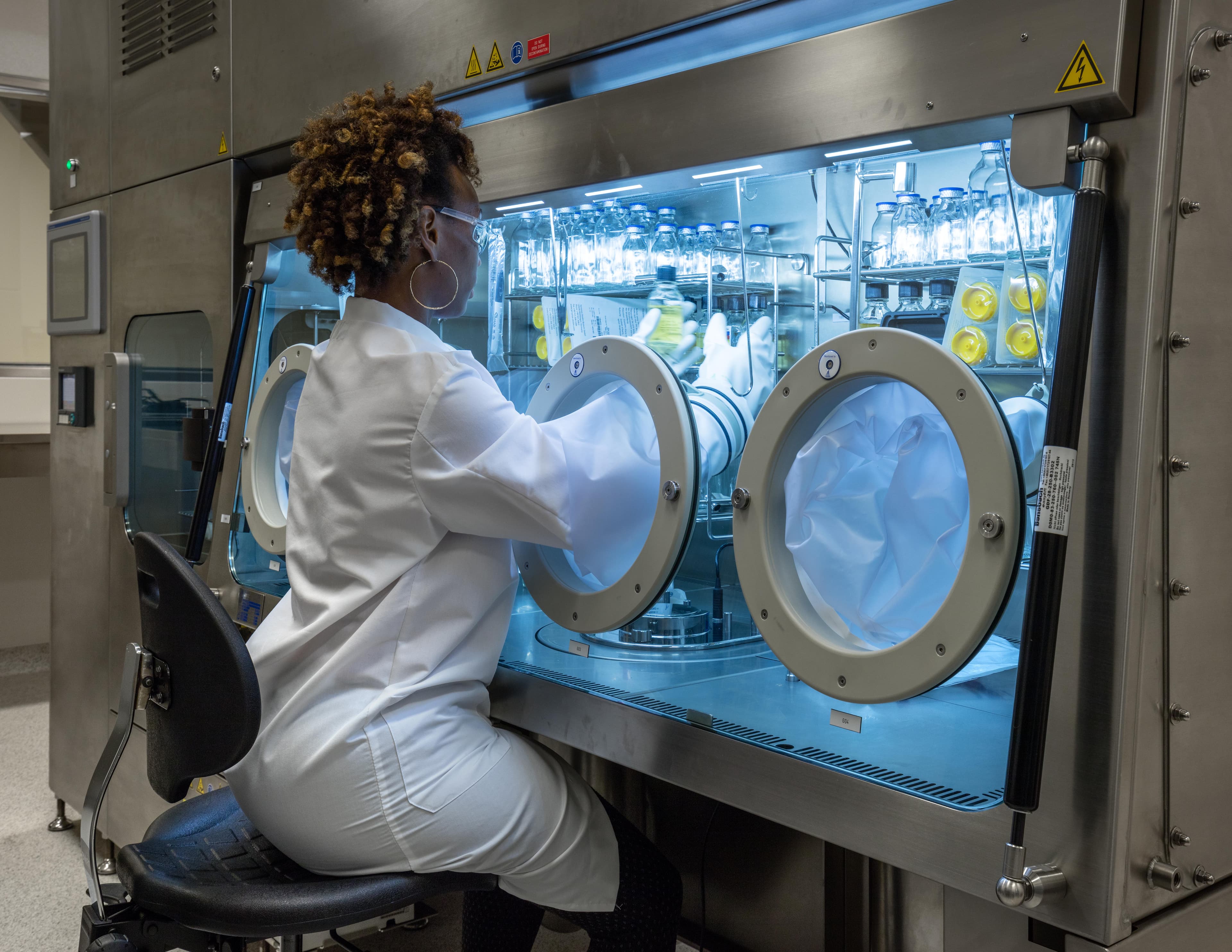
Shire (now a part of Takeda) built a 100-acre greenfield campus in Covington Georgia. The campus includes 1.2 million square feet of building space, including a wastewater treatment facility, manufacturing buildings, laboratory buildings, administrative buildings and a central utility building. The campus separates plasma components, purifies them and makes life-sustaining therapies used to treat burn victims and patients with immune disorders, hemophilia and other medical conditions.
2017
Fluor works on Novo Nordisk’s largest project
&w=3840&q=75)
2017: Fluor works on Novo Nordisk’s largest project
&w=3840&q=75)
Fluor is providing engineering, procurement, construction, construction management, commissioning and pre-qualification for Novo Nordisk’s Active Pharmaceutical Ingredients (API) manufacturing facility in North Carolina. The facility, which will produce pharmaceutical ingredients for diabetes medicines, is Novo Nordisk’s largest project and the single largest life sciences facility investment in North Carolina’s history.
2017
Fluor provides engineering services for CSL Behring
&w=3840&q=75)
2017: Fluor provides engineering services for CSL Behring
&w=3840&q=75)
Fluor provided engineering services for CSL Behring’s plasma fractionation facility expansion in Kankakee, Illinois. The expansion will increase the production of plasma intermediates, supporting the growing need for its life saving and life-improving therapies that are used to treat patients with rare and serious medical disorders around the world.
2019
Fluor breaks ground on Bayer cell culture technology center
&w=3840&q=75)
2019: Fluor breaks ground on Bayer cell culture technology center
&w=3840&q=75)
In May 2019, Fluor held a groundbreaking event for Bayer’s cell culture technology center in Berkeley, California. Fluor is providing a single point of responsibility for engineering, procurement, construction management, commissioning, qualification and validation for the project. The state-of-the-art Single Use Technology (SUT) biopharmaceutical development and manufacturing facility will produce oncology, cardiology and other therapeutics.