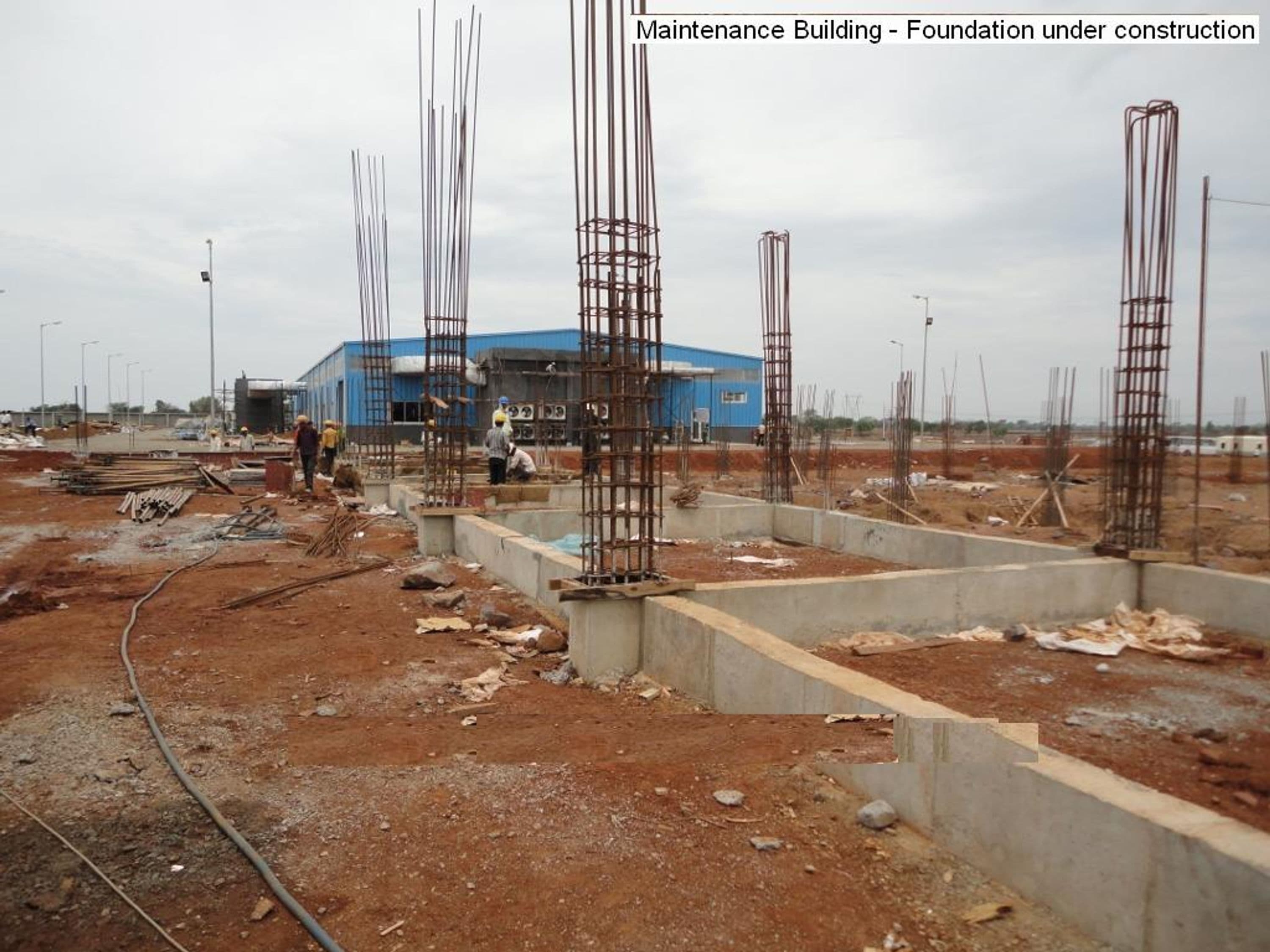
Lanco Solar 1500 TPA Polysilicon Plant - Engineering
Client: Lanco Solar Private Ltd.
Location: Rajnandgaon, Chhattisgarh, India
Business Segments: Energy SolutionsUrban Solutions
Industries: ChemicalsTechnology

Executive Summary
Fluor was the engineering integrator for process, utilities, infrastructure and offsites and provided detailed engineering services as well as procurement and field engineering support for the Lanco Solar 1500 TPA Polysilicon Plant. The Lanco greenfield plant will manufacture 1500 TPA of 99.9999999% pure polysilicon from manufacturing-grade silica using hydrochlorination technology.
Client's Challenge
Lanco Infratech Limited is one of the fastest growing business conglomerates in India. Its portfolio includes EPC, Power, Infrastructure, Solar and Natural Resources. Lanco Solar is a 100% subsidiary of Lanco Infratech Limited. As a part of its integrated "Sand to Power" strategy, it has established India’s first integrated solar manufacturing Special Economic Zone at Chhattisgarh for manufacture of polysilicon, ingots, wafers and modules.
This facility is the first composite polysilicon plant in India to use manufacturing-grade silica to produce not only solar-grade polysilicon but also other products that comprise solar power modules.
Lanco brought together a core group with polysilicon experience who understand the issues surrounding fabrication quality, construction quality and start up. Lanco also evaluated the qualifications of vendors to support this project.
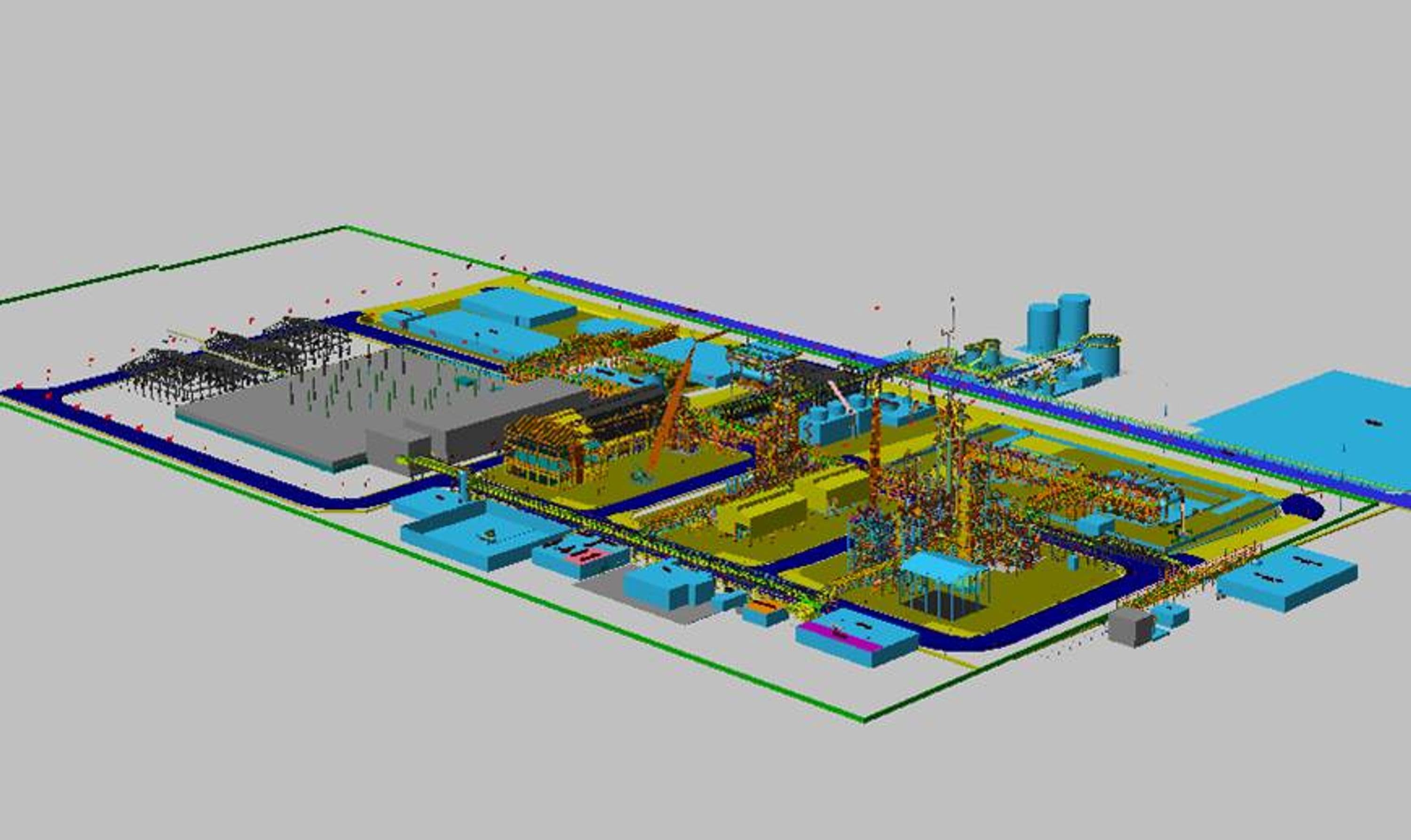
Fluor's Solution
Fluor provided detailed engineering for the polysilicon manufacturing process, technical support for procurement and field support. Having carried out previous polysilicon plant projects, we have experts in offices around the world with project execution experience using similar technologies and technology providers. These experts, as well as site employees, supported Lanco in this venture.
A design conference held in the early stages of the project included technology providers, our experts and client personnel, who put forward design solutions accepted by all key stakeholders. We conducted safety studies with Lanco and contributed to a solution for chemical vapor deposition reactor cooling that realized a cost savings for the client.
We also helped to select vendors who knew the requirements of polysilicon facilities and were able to deliver in a timely manner. In addition, we shared our experiences in supplier quality surveillance, and a similar approach was used on the project. At the client's request, we shared our experience in construction management and quality assurance with client personnel, adding to their understanding of the building requirements for this particular chemical facility.
The plant comprises a hydrochlorination plant, trichlorosilane vaporizer, chemical vapor deposition reactors, vent gas recovery, chunk and filament preparation and a host of infrastructure, offsite and utilities, including steam boilers, electric substation and water and waste treatment facilities. Hydrochlorination process technology for converting manufacturing grade silica to solar or photo voltaic grade silicon was provided by GT Solar and Chemical Design Inc., both U.S. companies.
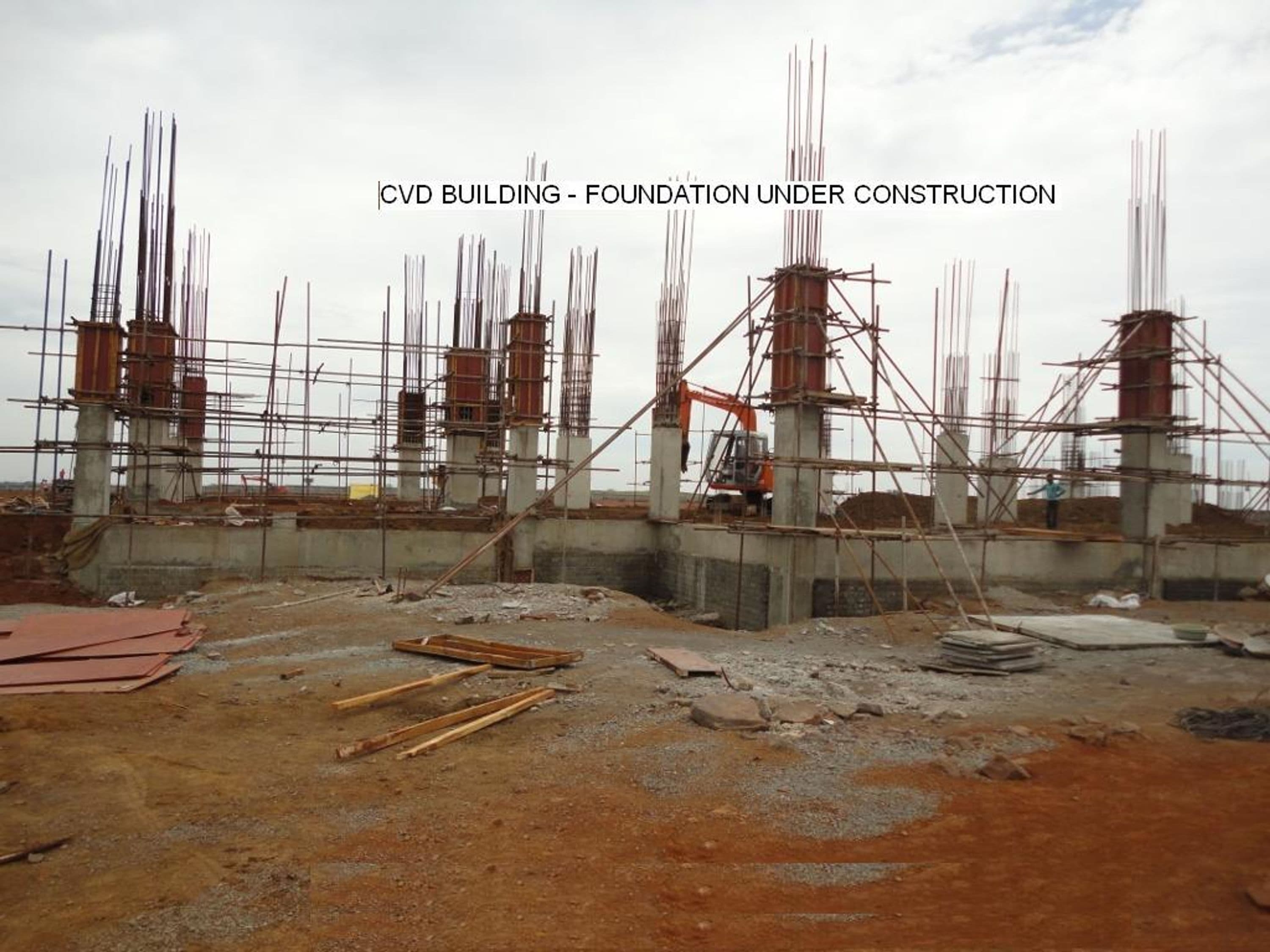
Conclusion
Lanco's new 1500 TPA polysilicon plant was successfully completed in December 2014. The Chhattisgarh project generated employment for over 250 locals and increased economic development for this formerly impoverished region.
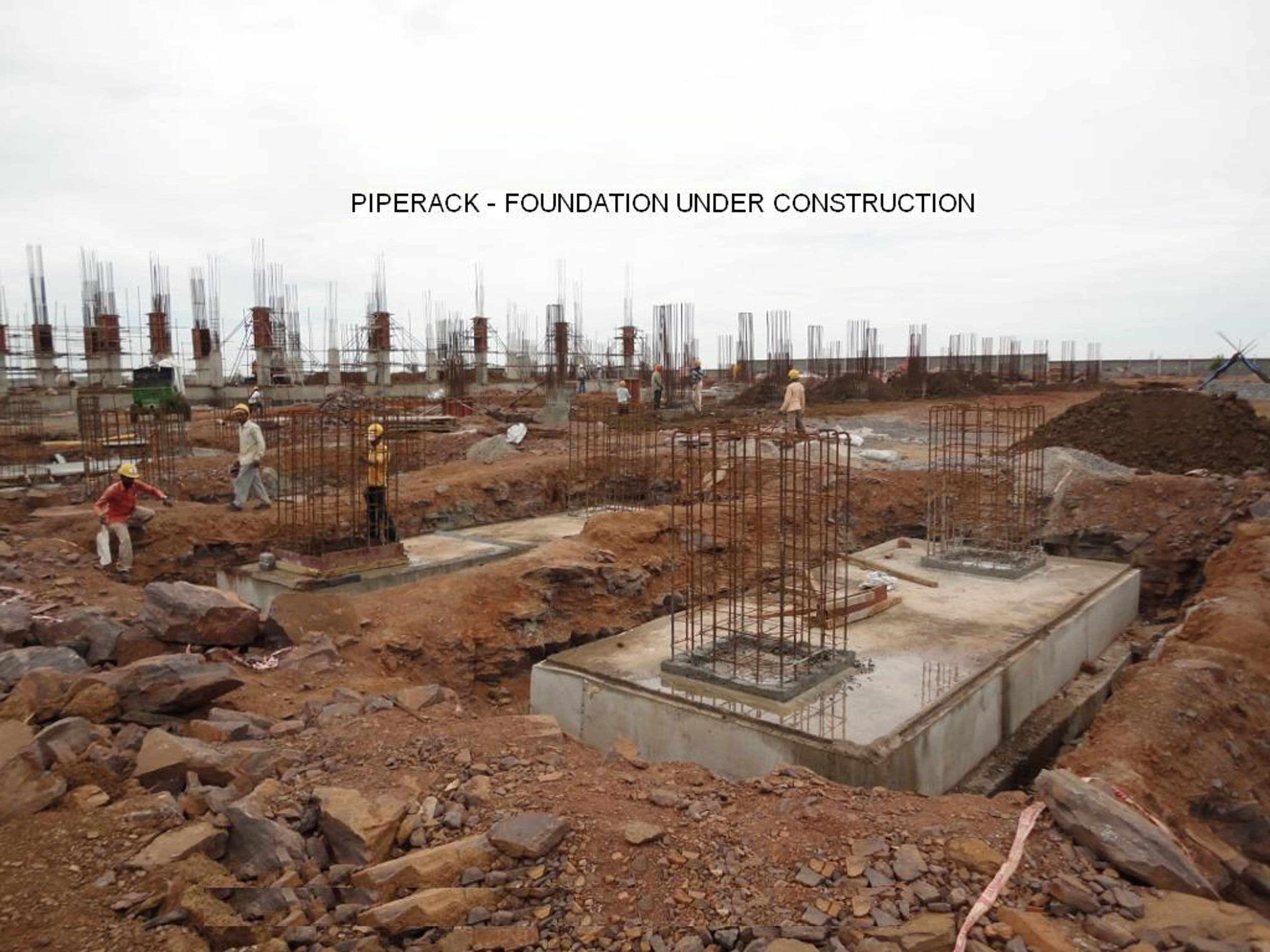