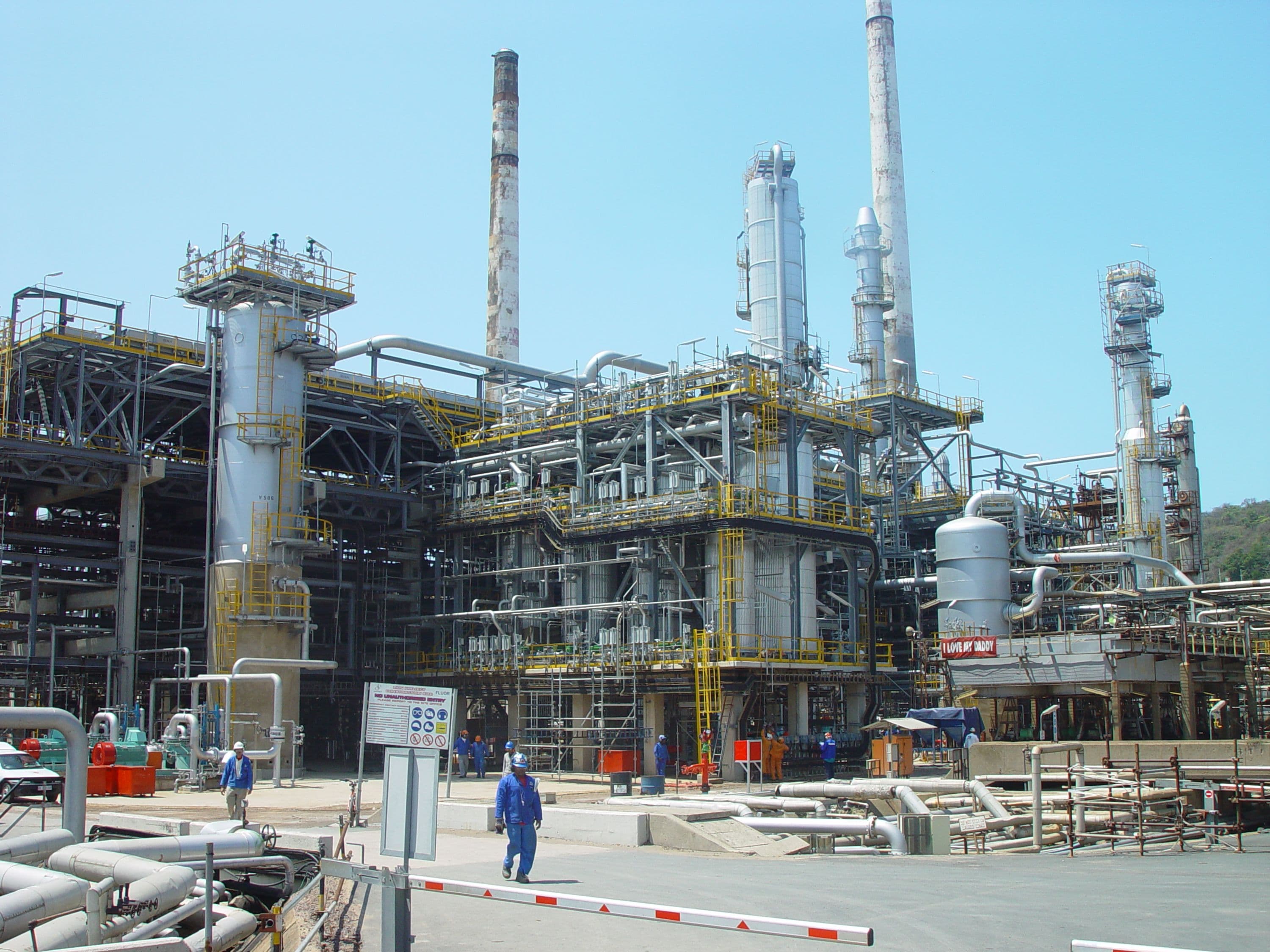
Project Lion Cleaner Fuels

Executive Summary
In 2002, the South African government announced a clean fuels initiative to remove lead from petroleum and reduce sulfur levels of petrol and diesel fuels. That initiative marked the largest collective investment period in the history of the South African fuel industry. SAPREF announced a 700 million rand investment to upgrade the refinery at Durban and selected Fluor for the engineering, procurement, construction and commissioning.
We executed the project from three international offices: Haarlem, Netherlands; Gliwice, Poland; and Durban, South Africa. The project met schedule and budget requirements and achieved a world-class safety achievement of 1,800,000 safe work hours.
Client's Challenge
SAPREF is a joint venture between Shell SA Refining and BP Southern Africa. In 2002, the South African government announced clean fuels specifications for refineries to remove lead from petroleum and reduce sulfur levels of petrol and diesel fuels.
SAPREF, Shell, BP and the South African government were committed to leading sustainable development in the refining industry. SAPREF made a 700 million rand investment to upgrade the Durban Refinery.
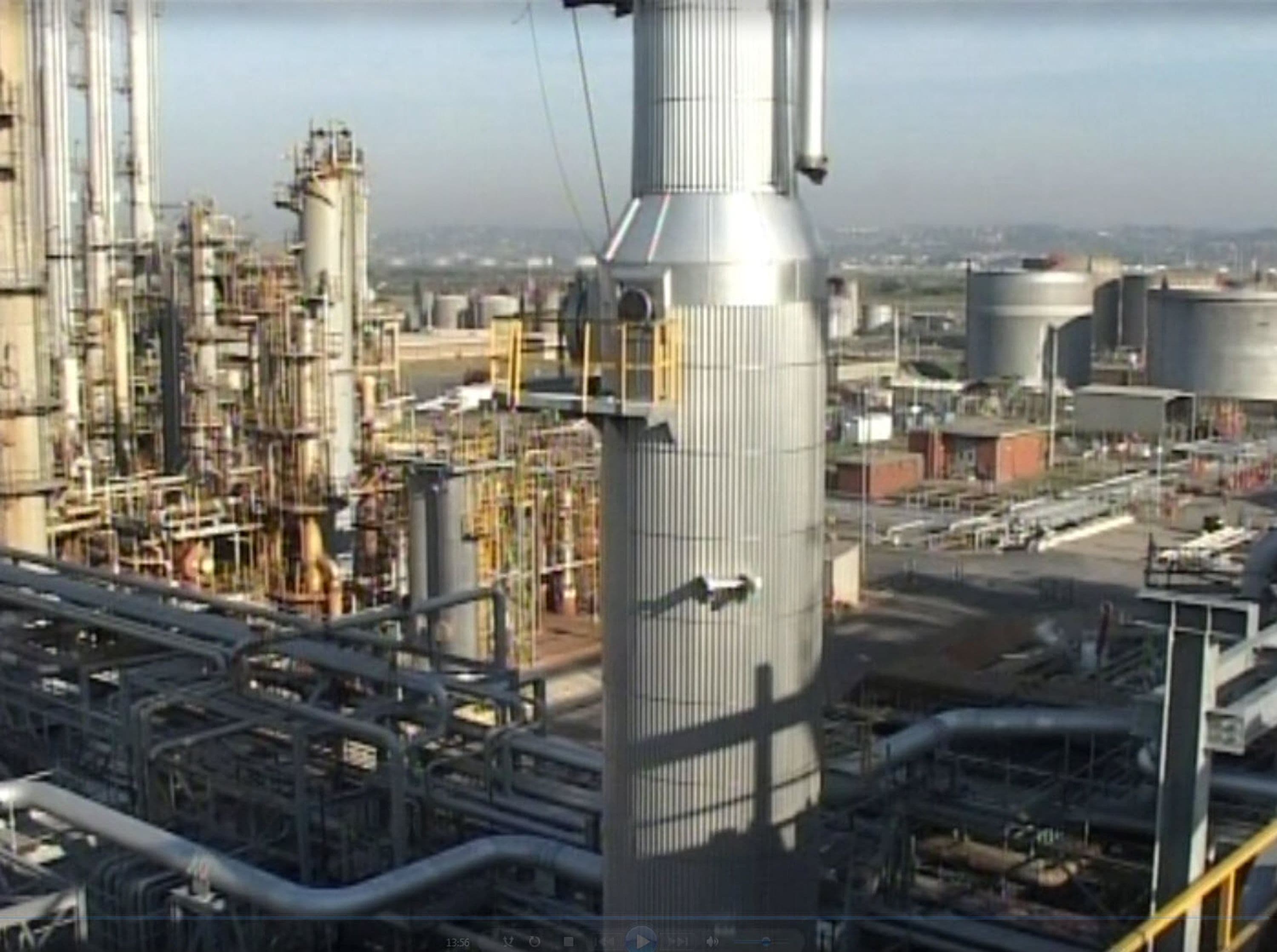
Due to the complex nature of the project at a working refinery, SAPREF needed a company that understood the new regulatory requirements and that had experience with refineries and the local knowledge to execute the project.
The refinery at Durban is South Africa's largest crude oil refinery, with about 30 percent of the country's refining capacity that equates to 180,000 barrels of crude per day or 8.5 million tons per year. Other petroleum products include diesel, paraffin, aviation fuel, liquid petroleum gas and marine fuel oil. SAPREF's facilities comprise a single buoy mooring, storage facility at the Durban harbor, joint bunkering services and the refinery.
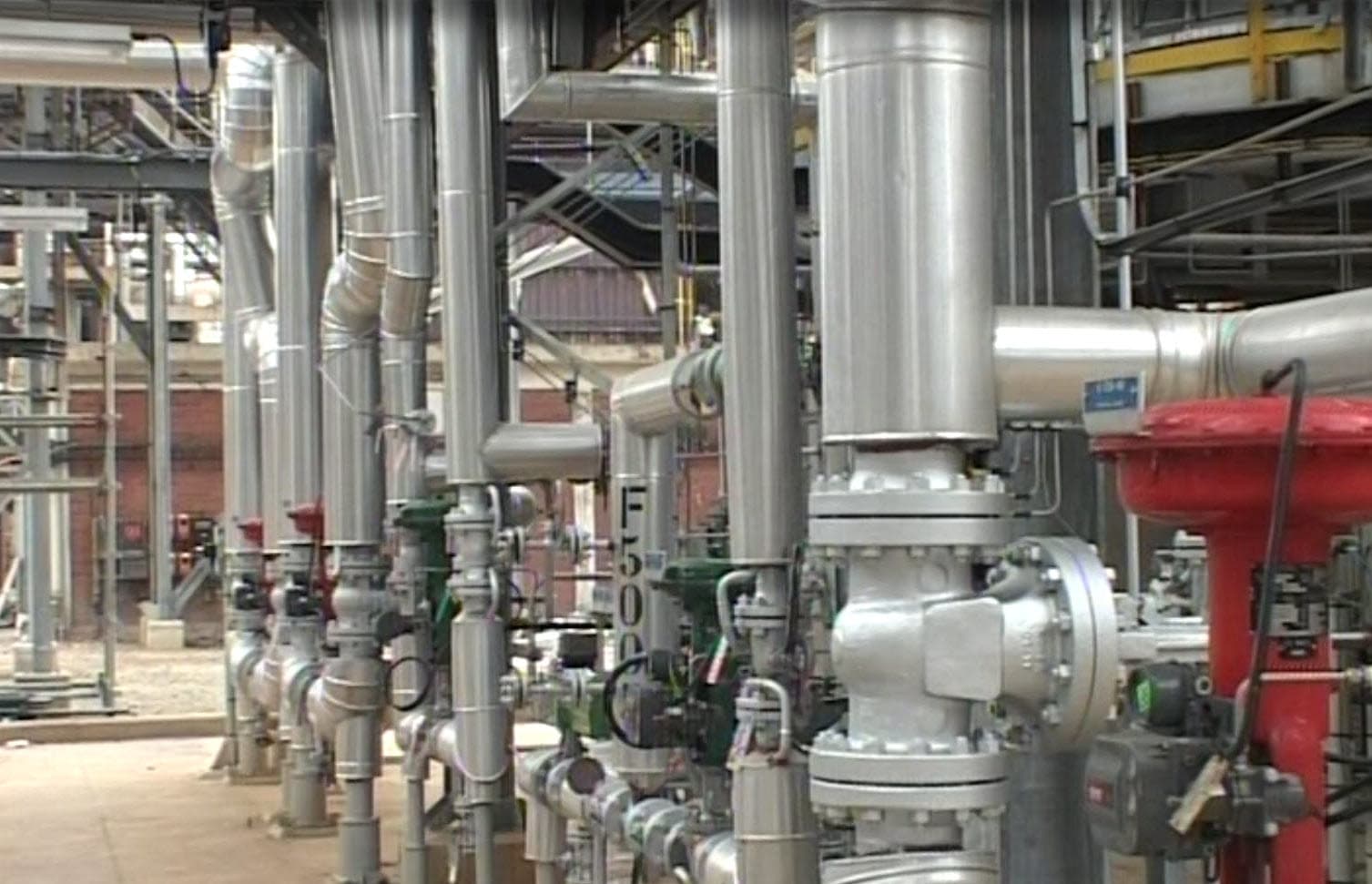
Fluor's Solution
Fluor was selected for Project Lion to perform engineering, procurement, construction and commissioning services.
We executed the work in three different offices. The office in Haarlem, Netherlands performed the basic engineering because of the office's conceptual engineering skills and experience with international technology licensors, including Shell Global Solutions, which also served as the project manager on Project Lion. The Gliwice, Poland office was selected to perform detailed engineering due to CAD expertise and competitive hourly rates. The Durban, South Africa office was responsible for integrating the new facilities into the existing refinery because of its knowledge of local conditions. By using modern communication and design tools, the integrated team functioned as one unit, meeting the requirements of SAPREF.
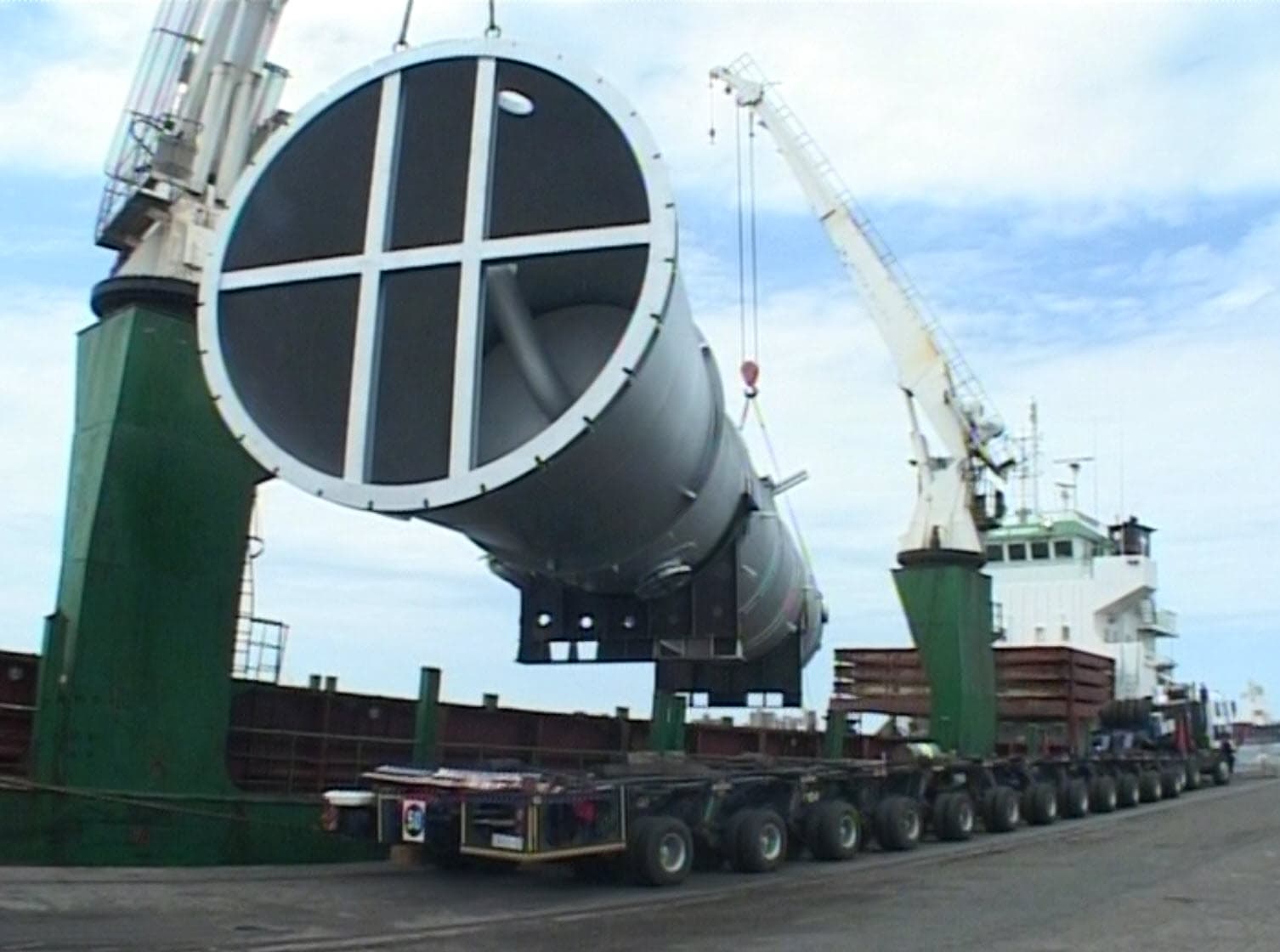
Our scope of facilities at the refinery included:
Installing 1,500-tons-per-day Penex/DIH isomerization unit
Installing a fourth reactor to existing semi-regen platformer
Installing hydrogen purification unit
We used international procurement specialists in Malaysia, Italy and Korea to obtain competitive pricing on the purification units and columns that would be needed at the refinery. When a devastating tsunami hit Southeast Asia in December 2004, cargo for Project Lion was already loaded onto seagoing vessels moored in that region for transport to South Africa. The cargo was unaffected, and ships soon began the journey to the port in Durban. Once at the Durban port, the equipment was loaded onto trucks for the journey to the project site.
When construction at the refinery started, we committed to using local labor from the neighboring communities, and more than 1,400 local residents were hired. Thirty percent of the contracts in South Africa were awarded to Black Economic Empowerment companies, exceeding the stated goals of SAPREF.
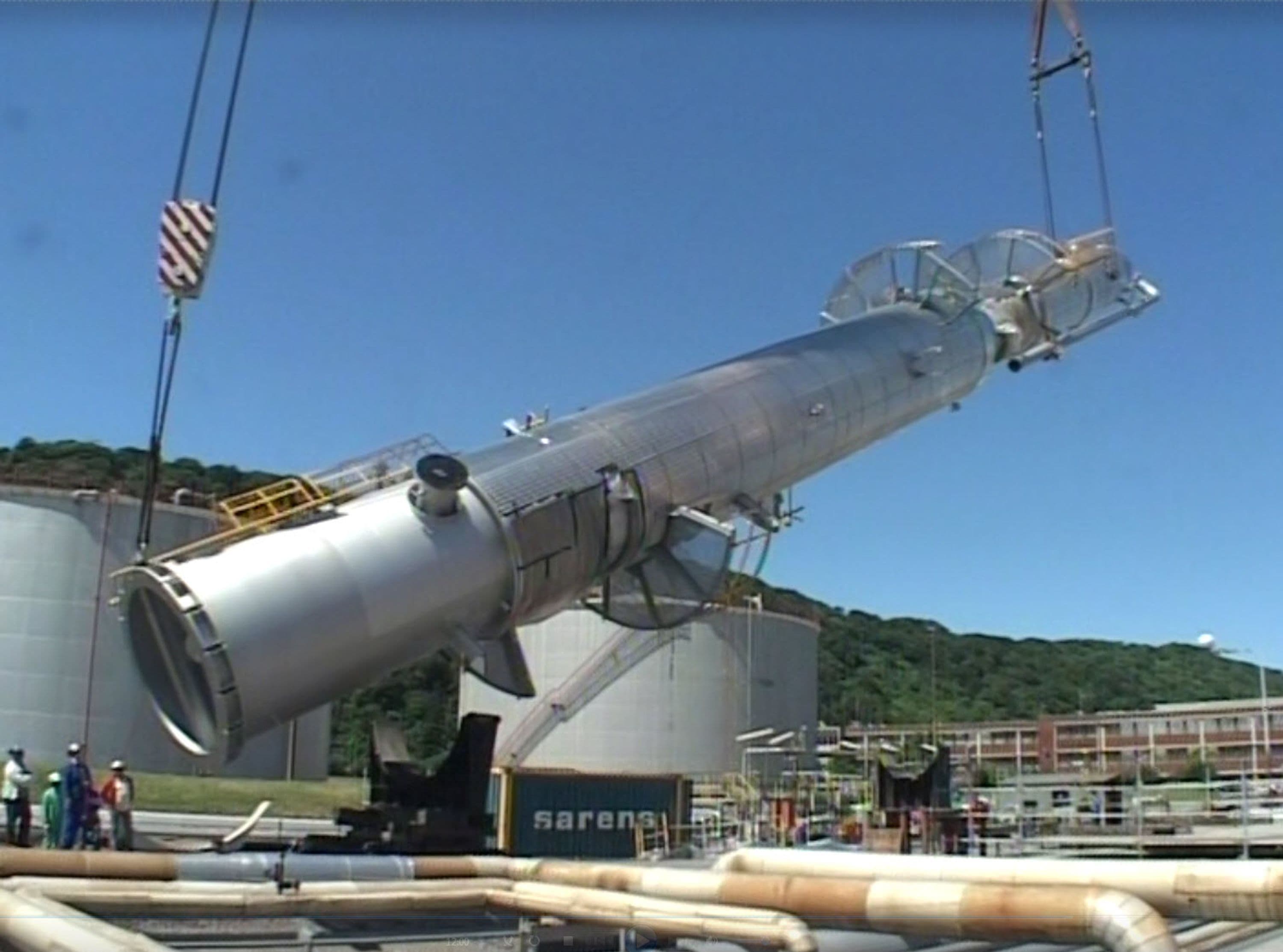
The scale of the project was massive and required close coordination and scheduling.
Several underground foundations were demolished while protecting underground cables. Because of the sandy soil at the Durban site, 311 pilings were cast to support the new process equipment. Distillation towers were shipped from Malaysia to Durban harbor and transported by truck to the refinery site. Cranes to lift the towers were booked more than a year in advance, and computer models were used to simulate the lifts. International specialists were employed to check the loads before and during the lifts.
At 119 tons, the platformer reactor was the largest piece of installed equipment, and the fit had to be precise. After careful planning, checking and installation, the fit was perfect.
The hydrogen purification unit was shipped in preassembled pieces from Germany. This unit was required to increase the purity of the hydrogen supply to desulfuriser units used to remove sulfur from the diesel fuels. An additional fourth platformer reactor was installed to produce more octane barrels to offset the loss of octane experienced as a result of having to remove tetraethyllead (TEL) as a petrol blend component.
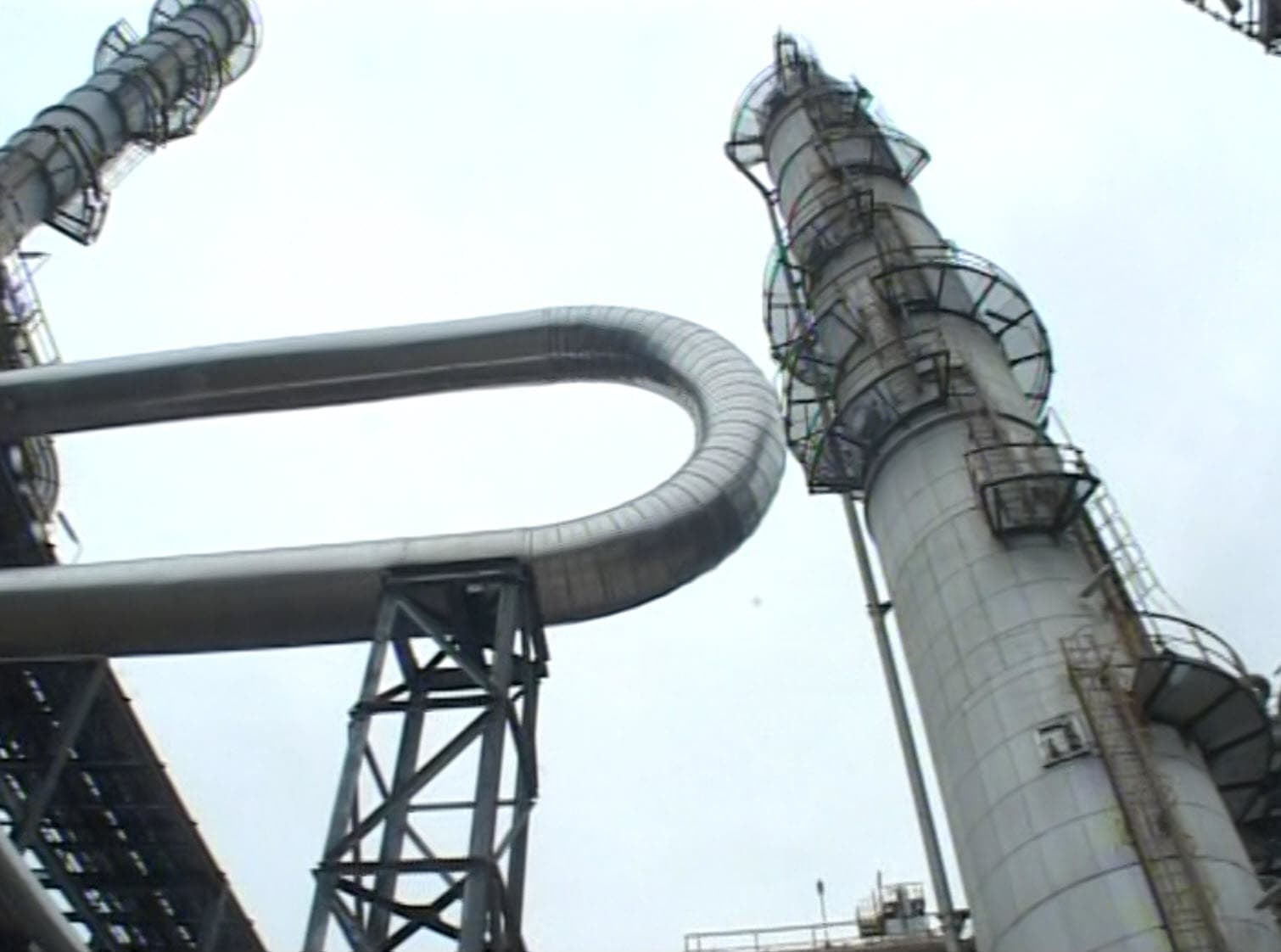
Conclusion
Project Lion was completed on schedule in 2006, living up to South Africa's commitment to producing cleaner fuels.
Fluor brought together an integrated, global team of engineers from three offices and used international procurement specialists to obtain competitive pricing on equipment sourced from five countries.
We hired more than 1,000 local workers for construction on the project and awarded 30% of the contracts in South Africa to Black Empowerment Companies.
The project team achieved a world-class safety achievement of 1.8 million safe work hours.
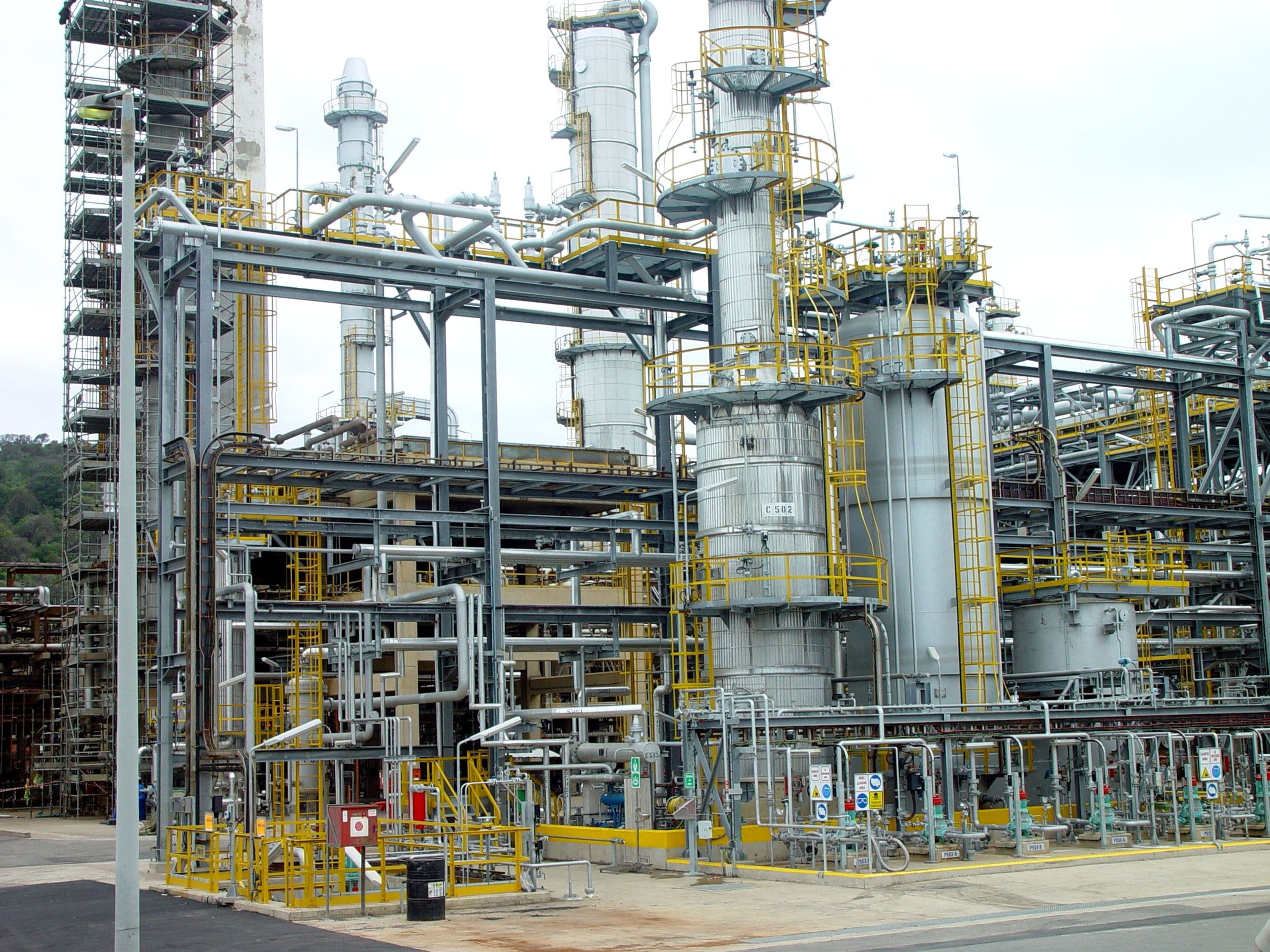