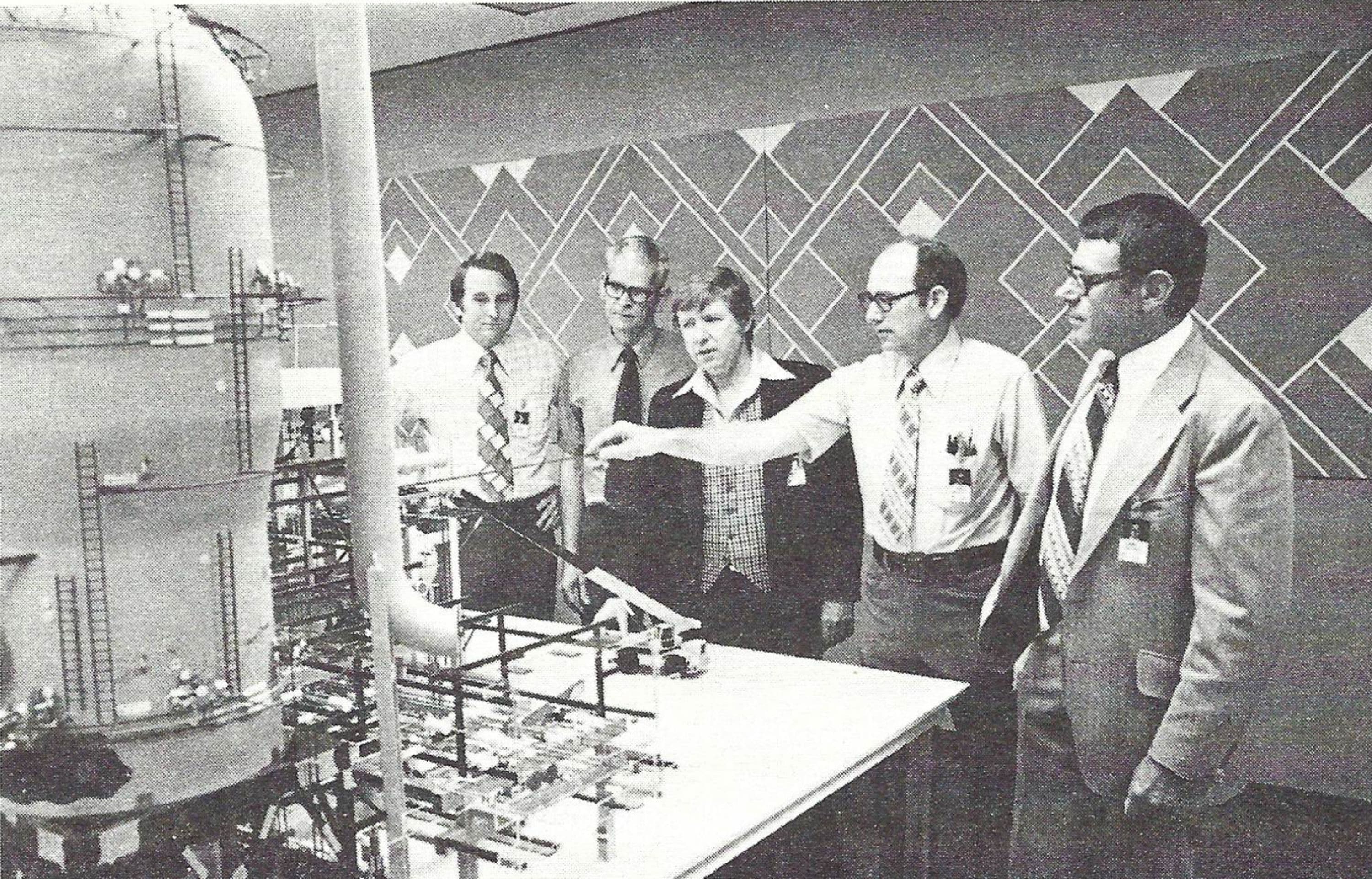
Marathon Garyville Oil Refinery Expansion - FEED, Engineering, Construction

Executive Summary
Fluor performed front-end engineering and design (FEED), engineering and design, procurement and construction management for Marathon Oil Corporation's Garyville Major Expansion (GME) project in Louisiana. With the GME in operation, Garyville can refine virtually any crude oil available on the market enabling the most cost-effective crude slate decisions. The expansion is essentially a new refinery adjacent to Marathon's existing facility. The original refinery, completed in 1976, now holds the distinction of being the last grassroots refinery constructed in the U.S. Previously the country's 18th largest, the Garyville refinery is now the United States' fourth largest.
Client's Challenge
The expansion project, which included a new crude/vacuum unit, hydrocracker, coker, NHT, CCR, KHT, sat gas and sulfur block (sulfur, amine, SWS, tail gas), increased Marathon's Garyville plant refining capacity from 256,000 bpd to 436,000 bpd and the total seven-plant refining capacity from 1,008,000 bpd to 1,188,000 bpd. Adding crude capacity with a second coker minimized Marathon's dependence on outside purchased gas oil without increasing the bunker fuel or asphalt.
From the onset, Marathon's key objective was to safely construct an energy-efficient facility with a mechanical completion on or before the end of 2009. This project was undertaken while at the same time the world engineering and construction market was facing nearly unparalleled growth in major project activity, material escalation and fabrication backlog. In order to meet this challenge, effective engineering, fabrication and construction execution along with significant resources were required.
Fluor's Solution
The GME project included the addition of a second crude processing train with associated downstream units. The second train added 180,000 bpd of capacity, with full conversion of bottoms via the addition of a maximum-sized two-drum coker.
To execute engineering for this major project, we leveraged 1,100 engineers at peak through global resources and local partners. Engineering and procurement was led by the Houston office and work shared with ICA Fluor in Mexico City, Fluor offices in Manila and New Delhi and a local engineering firm. Over 71,000 engineering drawings and documents were produced, including more than 27,000 isometrics. During critical production, we issued an average of more than 1,000 isometrics/week, reaching a single week peak of 1,400. Engineering data, vendor data and drawings were shared across the world, with the client and ultimately with the construction forces utilizing Fluor's Projects OnLine℠ web-based data management system.
Purchasing power was increased through the use of blanket commodity orders, Fluor key supplier agreements and Marathon Alliance vendors with strategic sourcing initiatives designed to secure fabrication resources ahead of the anticipated market growth. Major materials and equipment were sourced from 12 countries resulting in 7,700 truckloads and 50 separate barge loads delivered to the site.
We provided field construction management for 81 subcontracts, which ultimately resulted in an average workforce of 3,800 direct field craft workers with approximately 6,800 workers at peak (over 9,600 total craft and staff at peak). Material receiving, warehousing and issuing were controlled through the use of Fluor's MaterialManager® materials management system. Material laydown for the facility covered 70 acres with 114,000 separate material requisitions filled by the Fluor warehouse organization.
Conclusion
In addition to providing 7.5 million gallons of additional clean transportation fuels each day to the marketplace, Marathon's major expansion project provides significant benefits to the state of Louisiana. The completed expansion added approximately 200 new full-time employees and more than 70 new full-time contract workers. Moreover, state and local economies benefited from the approximately $60 million in taxes and economic activities associated with the project.
By leveraging vast experience in the petroleum refining industry and program management, the Fluor and Marathon team turned over the new facilities at the Garyville refinery on schedule, enabling Marathon to achieve corporate goals established five years earlier.