&w=3840&q=75)
Loy Yang Power Station and Mine Maintenance
Client: Loy Yang Power
Location: La Trobe Valley, Victoria, Australia
Business Segments: Energy SolutionsUrban Solutions
Industries: Mining & MetalsPower
Services: Maintenance

Executive Summary
The Victorian government created Generation Victoria to run the power stations formerly operated by the State Electricity Commission. Generation Victoria soon had evidence of how Fluor could increase plant availability at Loy Yang, Victoria's biggest power station.
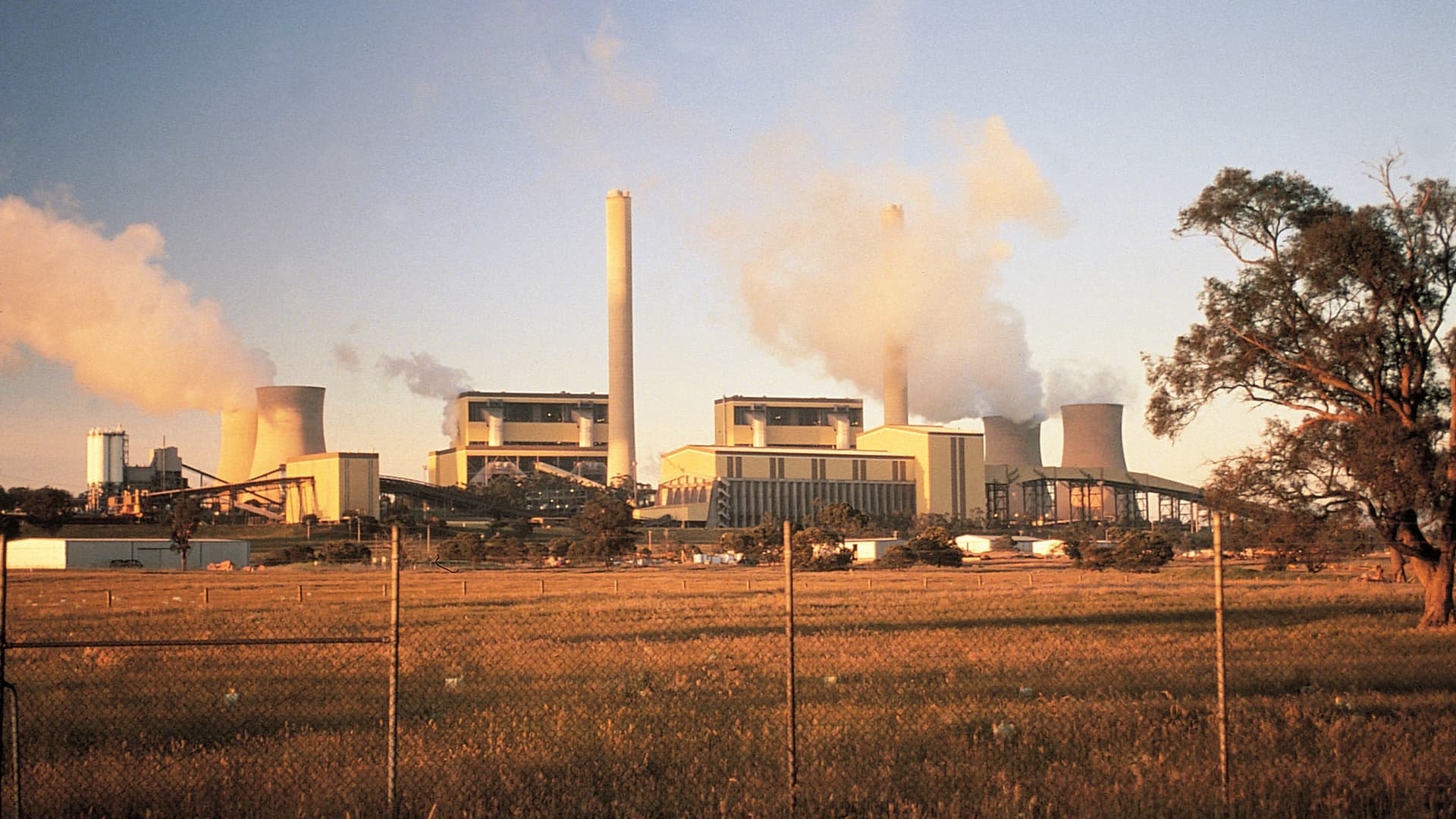
Client's Challenge
At Loy Yang, nothing has such an effect on profits as plant availability, having generators actually online and producing power when the market is buying it.
Soon after Generation Victoria took over the plant, availability was at 79%. Another challenge was keeping lost-time accidents down, which had been running at 50 to 60 per million work hours.
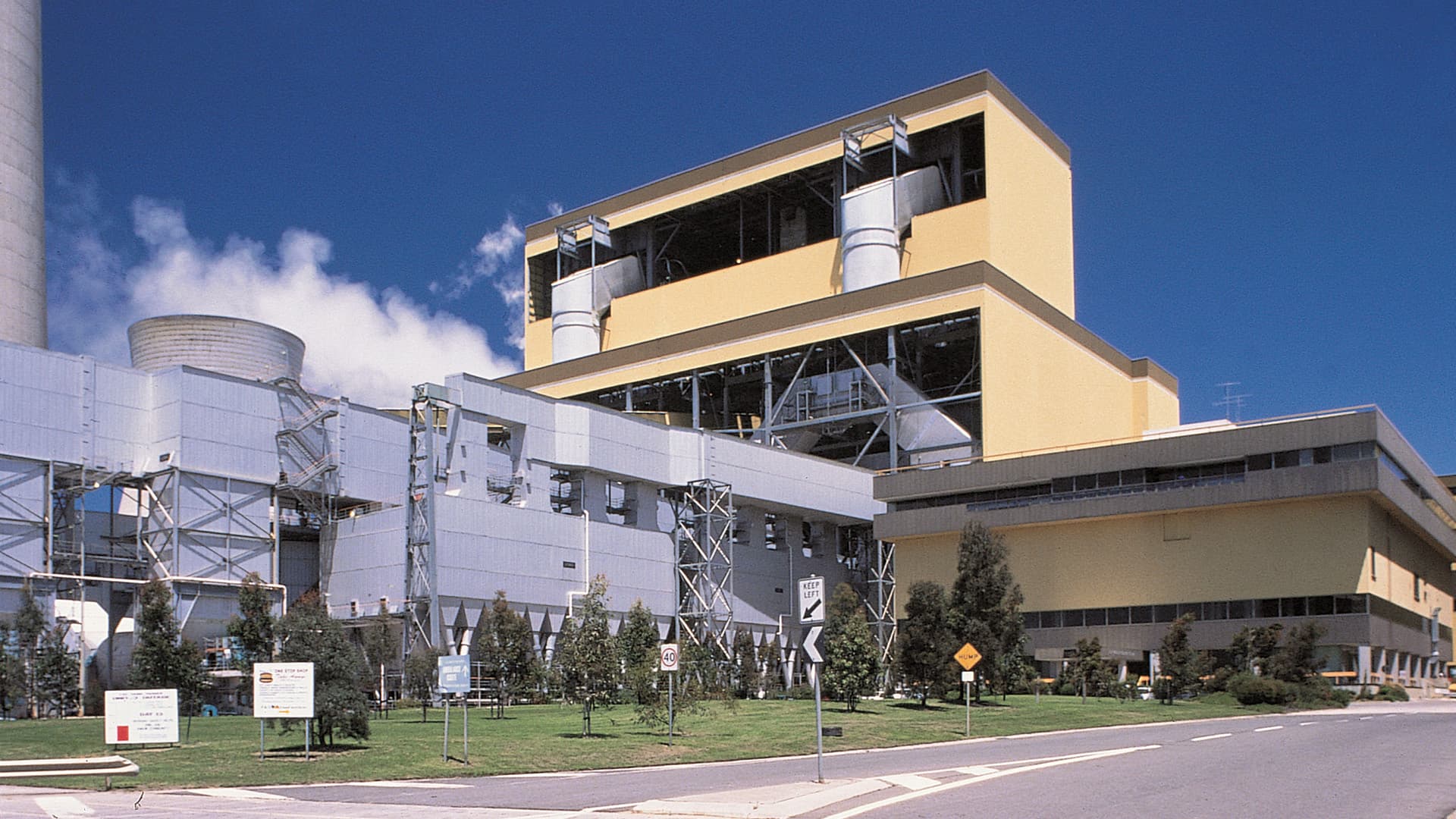
Fluor's Solution
Fluor managed the planned outage of the 500-megawatt Unit 3 boiler and turbo-generator, which usually took seven to eight weeks. We had the unit back online in less than four weeks, assigning 250 tradespeople to the project to get through the 70,000 hours of work. Boiler cleaning that had previously taken 2,250 worker hours over five or six days took us 1,200 worker hours in two days.
Our worldwide passion for safety also paid off at Loy Yang Power. Our maintenance activity soon had the lost-time accidents down to about six per million. With the improvement in safety performance, we were able to pass a major reduction in WorkCover premiums back to the client.
Where morale had once been rock bottom, workers now began to take an interest in better, faster, safer, cheaper ways of getting the job done. Over 100 maintenance suggestions were offered by the station's workers.
Our contract was extended by competitive tender to include the nearby brown-coal mine.
&w=3840&q=75)
Conclusion
After seven years of close co-operation between Loy Yang Power management and Fluor, the plant reached 98%. One unit at the facility was at 99%. The world's best practice for complex, coal-fired plants such as this at the time was 94 to 96%.
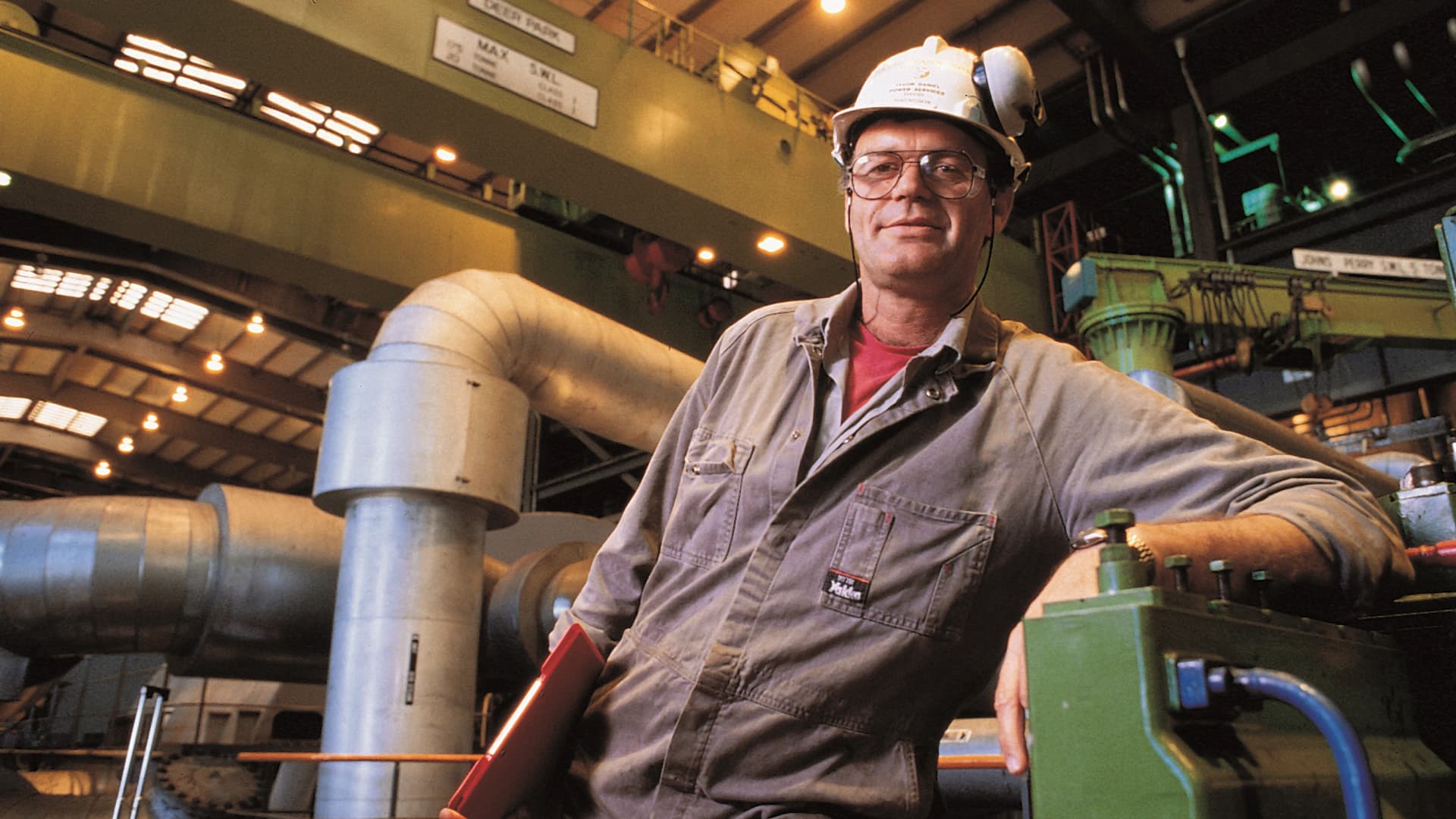