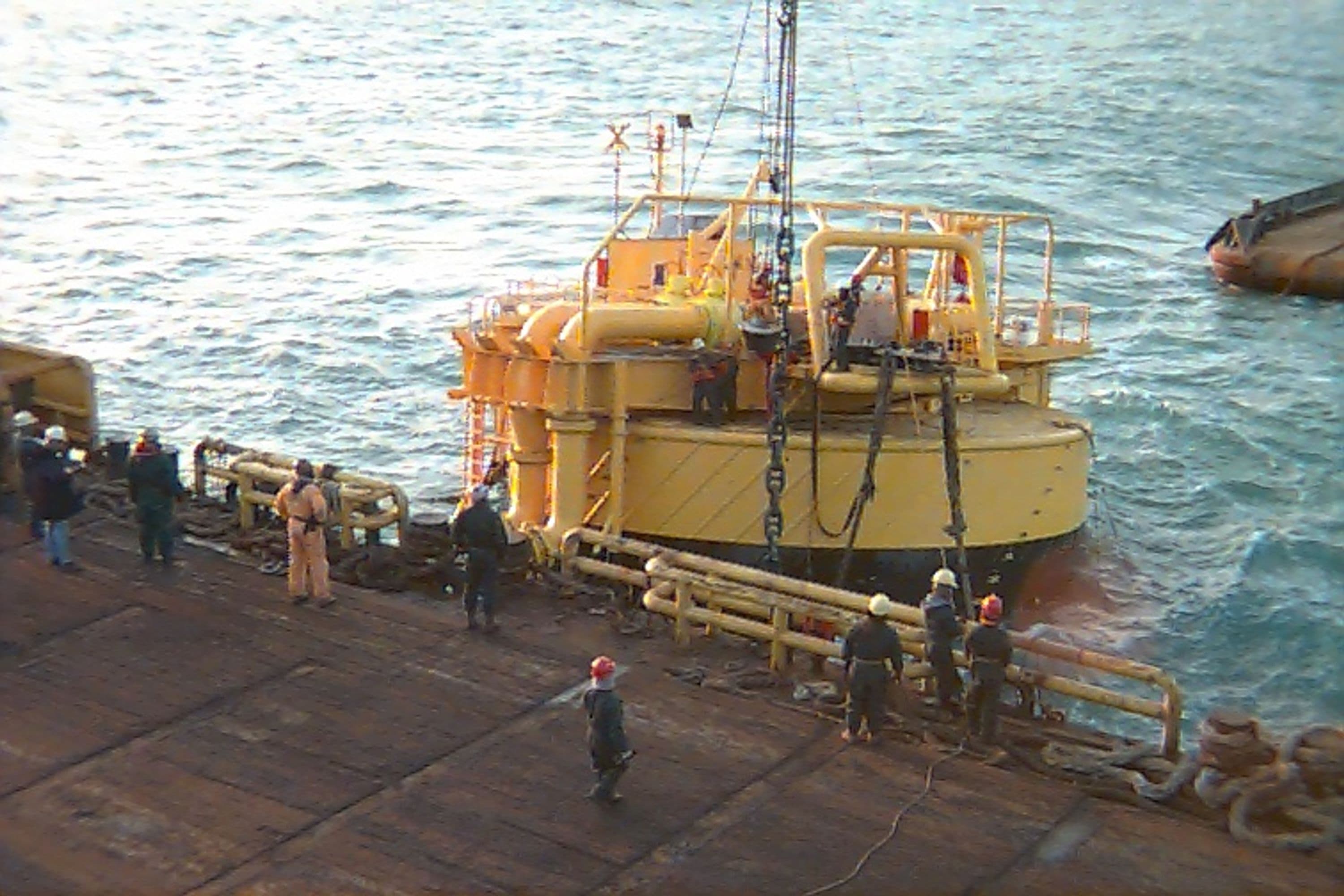
Submarine Pipeline
Client: Yukong Limited
Location: Ulsan, South Korea
Business Segment: Energy Solutions
Industry: Fuels

Executive Summary
Yukong Limited awarded us the contract to expand its Ulsan refinery capacity to 800,000 barrels per day. We worked on the expansion of three separate projects: the FCC project that added 300,000 barrels per day of refining capacity, the Paraxylene project that utilized part of the increased project output and the Submarine Pipeline project that increased Yukong's crude import capacity.
For the fast-track project, we performed overall project management, detailed pipeline design, management of the Single-Point Mooring (SPM)/Pipeline End Manifold (PLEM) design, technical input for procurement and construction management on the 42-in - 4.5 km submarine pipeline for Yukong.
Client's Challenge
Yukong Limited, Korea's largest refiner of petroleum products, contracted with us to increase its crude import capacity. Yukong's refinery is located on the southeast coast of Korea at the industrial port of Ulsan. The Submarine Pipeline project facilities included the installation of a third new Yukong-supplied single point mooring (SPM) buoy upon which a seabed PLEM was piled in place. The SPM accommodates tankers up to 325,000 deadweight tons.
Fluor's Solution
From the PLEM, a 42-inch diameter, 0.688-inch-thick wall, API5L-grade B pipeline coated with fusion bond epoxy and 3.5 inches of 190 pounds-per-cubic-foot density concrete for conveying crude oil was attached to an existing booster station onshore.
The 42-inch-diameter pipeline, 4.5 kilometers in length, was installed to cross a shipping fairway, a 2-meter-diameter sewer outfall, traverse about one kilometer of rocky shore and 0.5 kilometer onshore to end at the booster station.
At the booster station, two 45 degree fabricated bends make the transition from underground to aboveground piping. The booster station network consists of five 36-inch valves and piping to allow operators to fill crude oil storage tanks either by direct offloading from the tanker or through either one of two booster pumps.
The SPM buoy and pipeline accommodate tankers up to 325,000 deadweight tons. The pipeline system's capacity is about 58,000 barrels-per-hour, which enables tankers to unload in about 36 hours.
Facilities for the SPM consist of a six-anchor leg system held by 12-17 ton Mag anchors, two 24-inch / 16-inch floating and tail hose strings and a hydraulic valve operator system for subsea valves on the PLEM.
The PLEM consists of a structural steel frame with mud mats to support the 42-inch pipeline connection, two 24-inch check valves, two 24-inch hydraulically operated ball valves, blind flanges for pig launching capability and two 24-inch under-buoy hoses connected to the SPM.
Conclusion
We delivered the fast-track project ahead of schedule, beating the planned 18 month Yukong Submarine Pipeline reached mechanical completion only 51 weeks from receipt of the Letter of Intent.
The Yukong submarine pipeline project was awarded the Hugh Coble award for project excellence and the Fluor Daniel Excellence Award for 1996. Our team was also recognized with the Fluor Tri-Star Safety award for 442,000 work hours without a recordable incident.