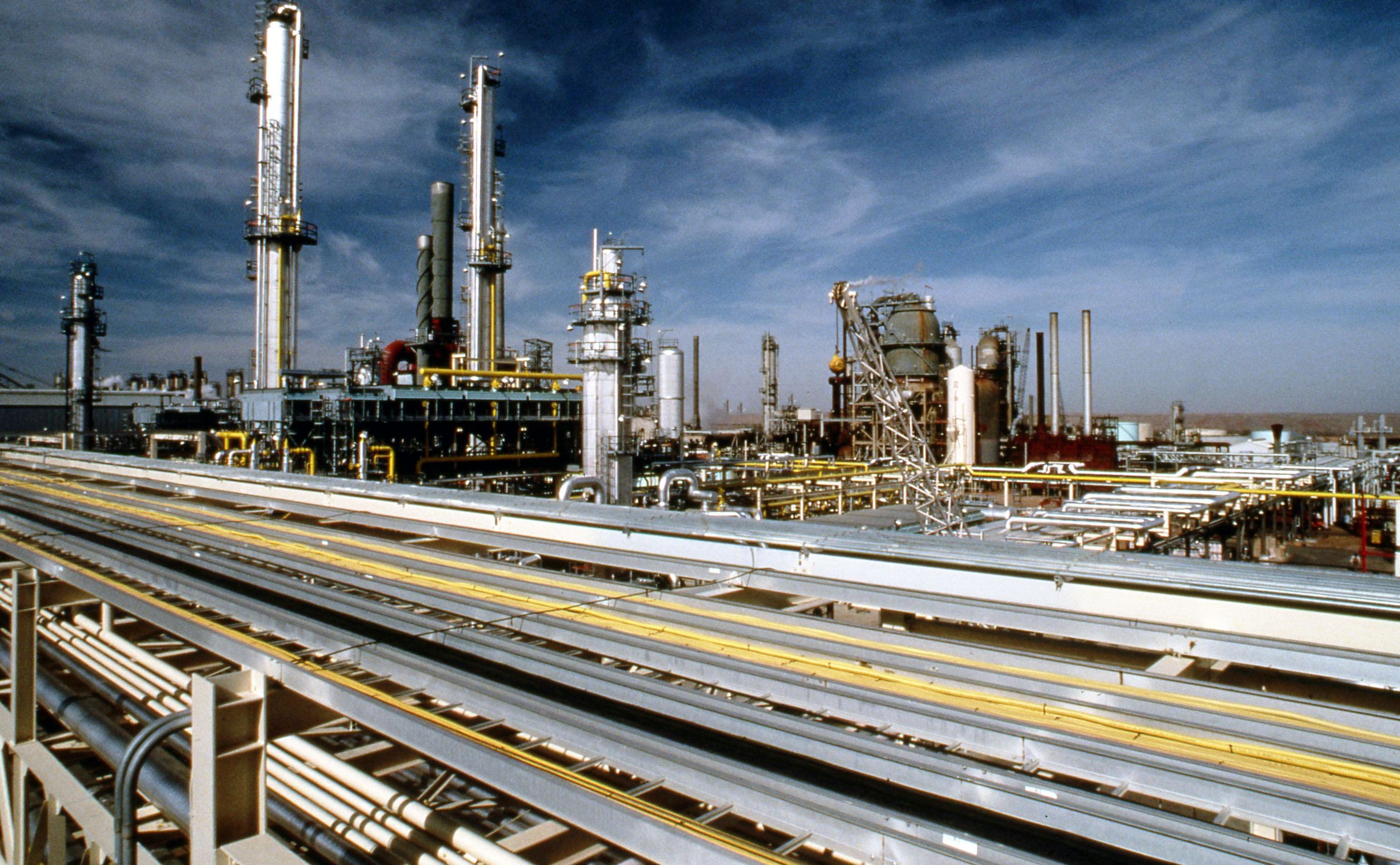
Phillips Refinery Expansion/Modernization Program
Client: Phillips Petroleum Company
Location: Borger, TX, U.S.
Business Segment: Energy Solutions
Industry: Fuels

Executive Summary
Fluor was awarded total engineering, procurement and construction management responsibility for an addition at the Phillips plant in Borger, Texas. This modernization program increased Phillips' capacity to process heavy crude.
Our scope of work also included cost control, planning, scheduling, quality control and field engineering. The project scope required four reactors of more than 500 tons each that we sourced off-site and fabricated to take advantage of modular construction.
Client's Challenge
This facility is a heavy crude oil refinery that includes a desulphurization unit, a hydrogenation unit, and sour water and tail gas treatment units. The capital expansion and modernization investment generated increased heavy crude processing capacity at the Borger refinery.
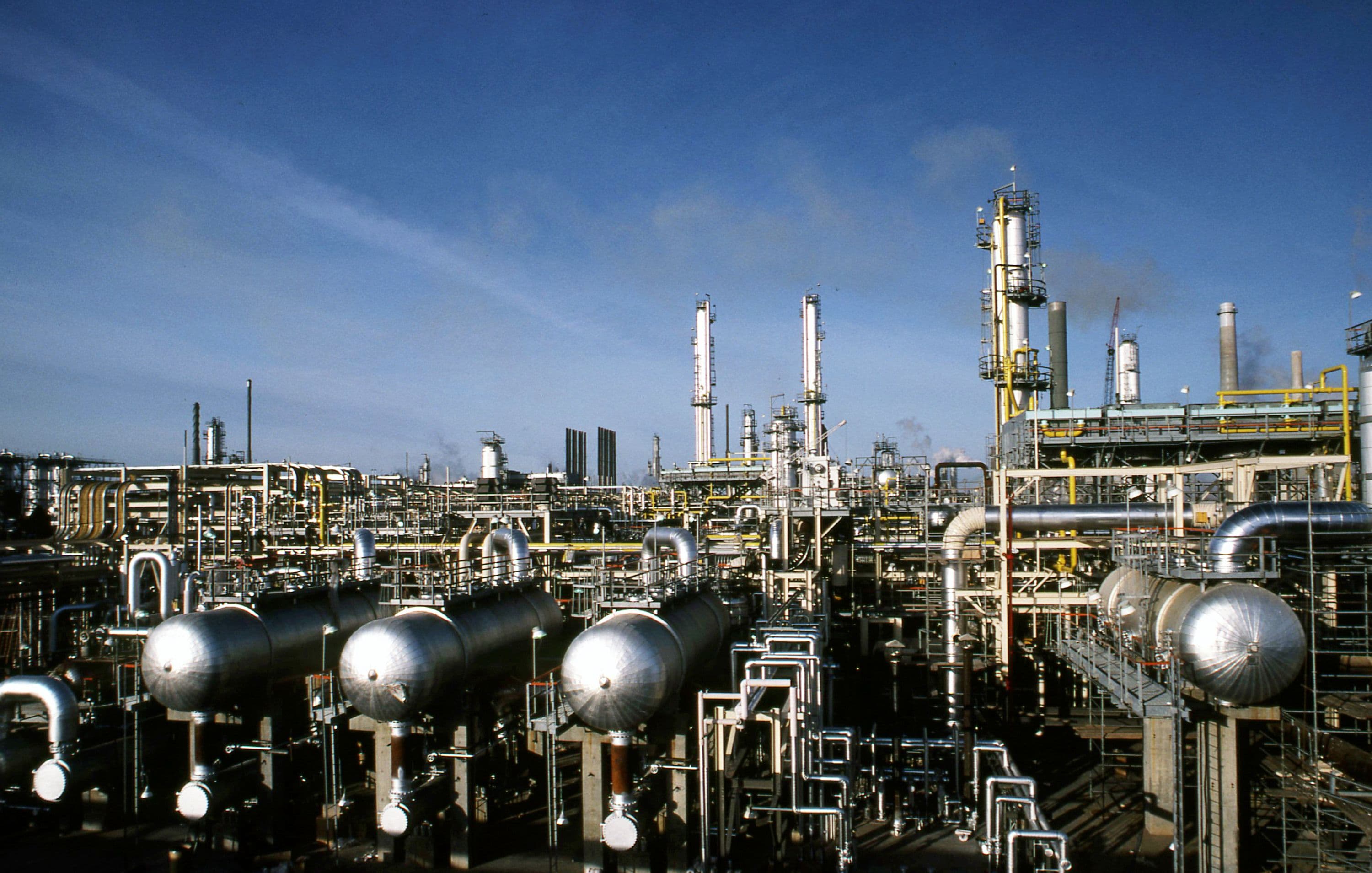
Fluor's Solution
The following units were added:
50,000-barrels-per-day atmospheric residue desulfurization
50-million-standard-cubic-feet-per-day hydrogen unit
New amine treater
New sour water stripper
300-tons-per-day sulfur recovery unit
Offsites and utilities
Fabricated in Japan, each of the four 550-ton, 75-foot reactors was shipped to the Greens Bayou terminal. These were the heaviest ever received at the Greens port. Special 600,000-pound capacity, 12-axle heavy duty rail cars were made to transport the vessels on the 700-mile rail journey to West Texas. We also supplied a special lifting rig consisting of a pair of 1,000-ton-capacity Manitowoc compression poles.
The Fluor team self-performed more than 90% of the work and constructed the project on an open-shop basis. The project workforce peaked at 1,850 craft personnel.
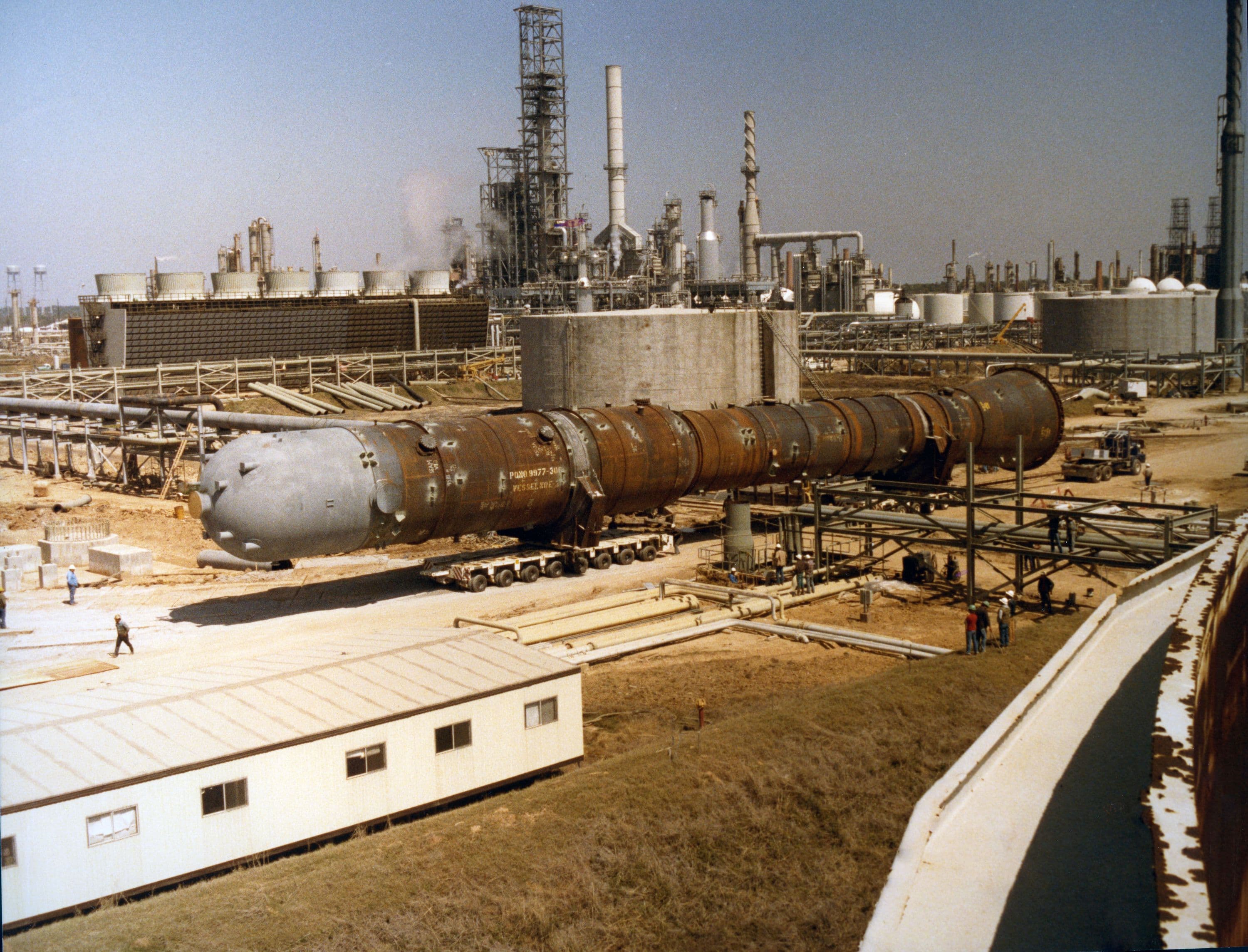
Conclusion
This project was completed on schedule and successfully reached 1,300,000 work hours without a lost-time accident.
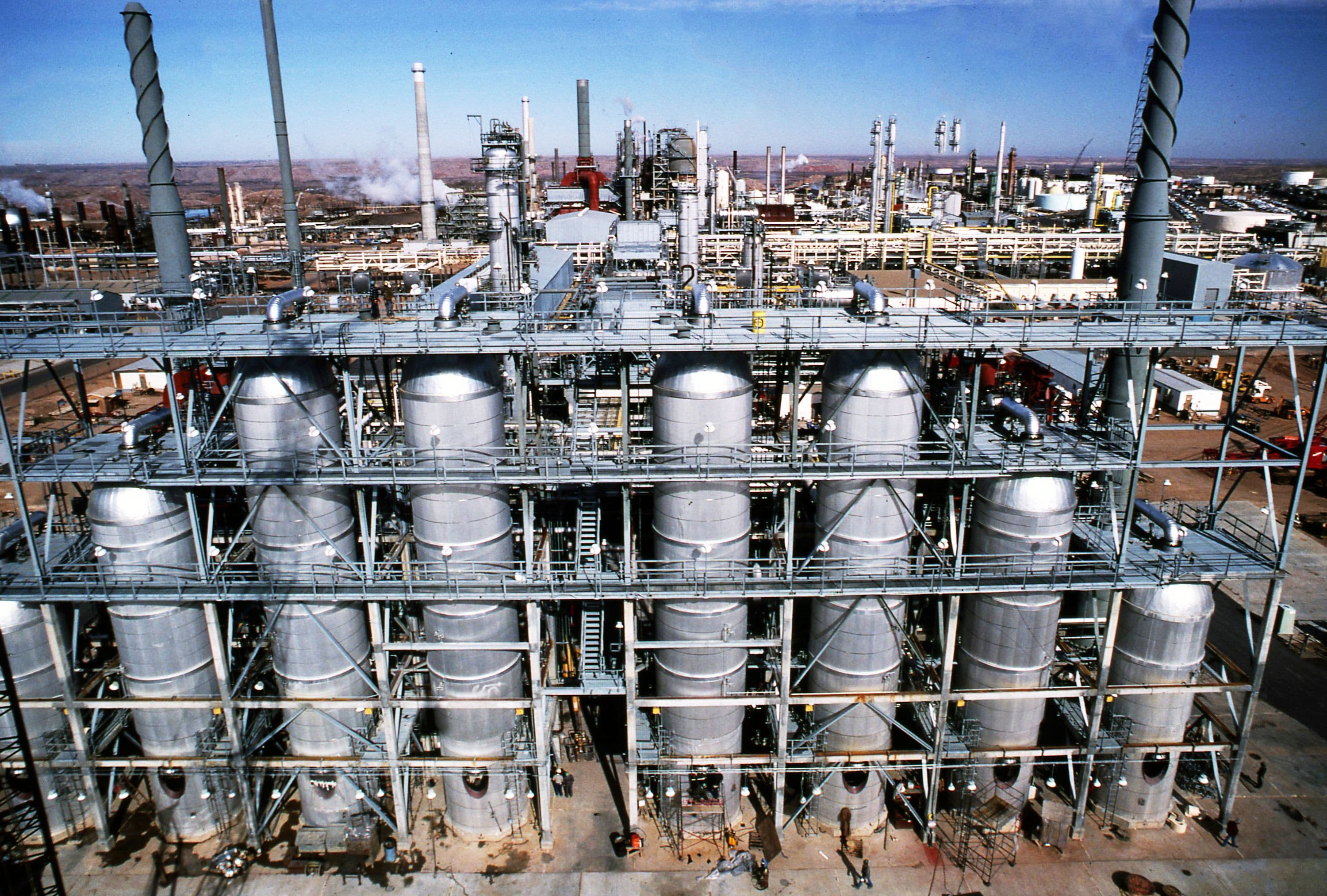