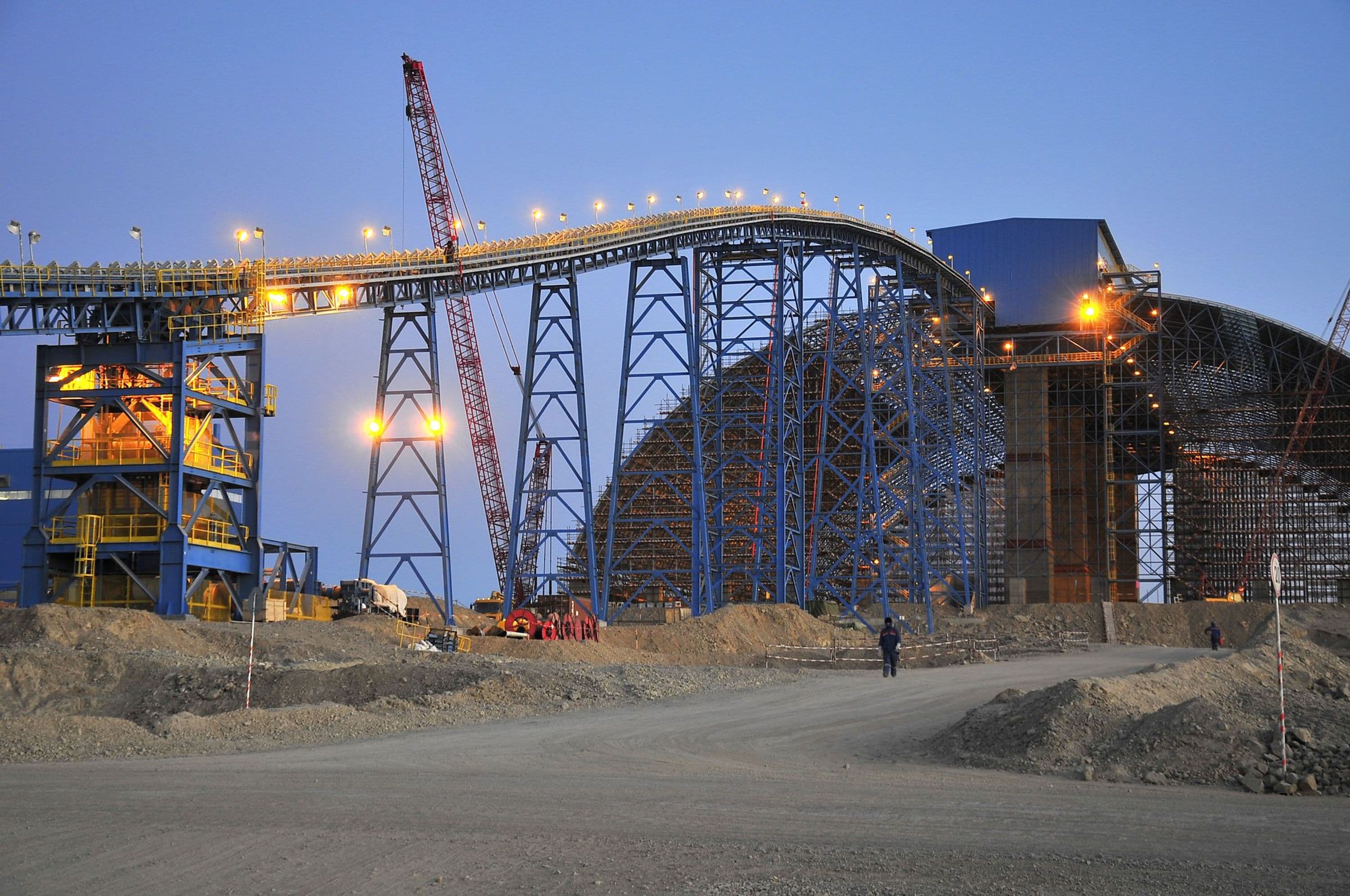
Ivanhoe Mines Oyu Tolgoi Copper Mine Construction
Client: Ivanhoe Mines Ltd.
Location: Gobi Desert, Mongolia
Business Segment: Urban Solutions
Industry: Mining & Metals
Services: Maintenance

Executive Summary
In the arid, very remote Gobi Desert in Mongolia, Fluor provided program and construction management to Ivanhoe Mines Ltd. on their $6 billion Oyu Tolgoi copper mine. This mine represented the largest and perhaps most challenging engineering-construction project in Mongolia and became one of the world's largest copper mines when it commenced operations in 2013.
Ivanhoe Mines and Rio Tinto, two of the world's leading mining companies, and the Mongolian Government formed a strategic partnership for construction and operation of the Oyu Tolgoi project. The project consisted of open-pit and underground mines, a copper concentrator and supporting infrastructure to produce high-quality copper-gold concentrate.
Client's Challenge
The name Oyu Tolgoi means "Turquoise Hill" in Mongolian. Challenges facing the project team at Oyu Tolgoi included operating at 3,800 feet, extreme weather and limited access to essential utilities and services. The Gobi Desert presented a brutally harsh environment, with temperatures ranging from -40° C to +45° C. The country is landlocked, with limited access via roads or rail.
The opportunity to positively impact an entire nation for decades to come made the project a rewarding one for all personnel working to build the mine.
The project was co-led by an integrated program management team composed of Fluor and Ivanhoe Mines personnel. This team oversaw all engineering, procurement and construction management services. Multiple Fluor offices supported the project, including those in Vancouver and Shanghai.
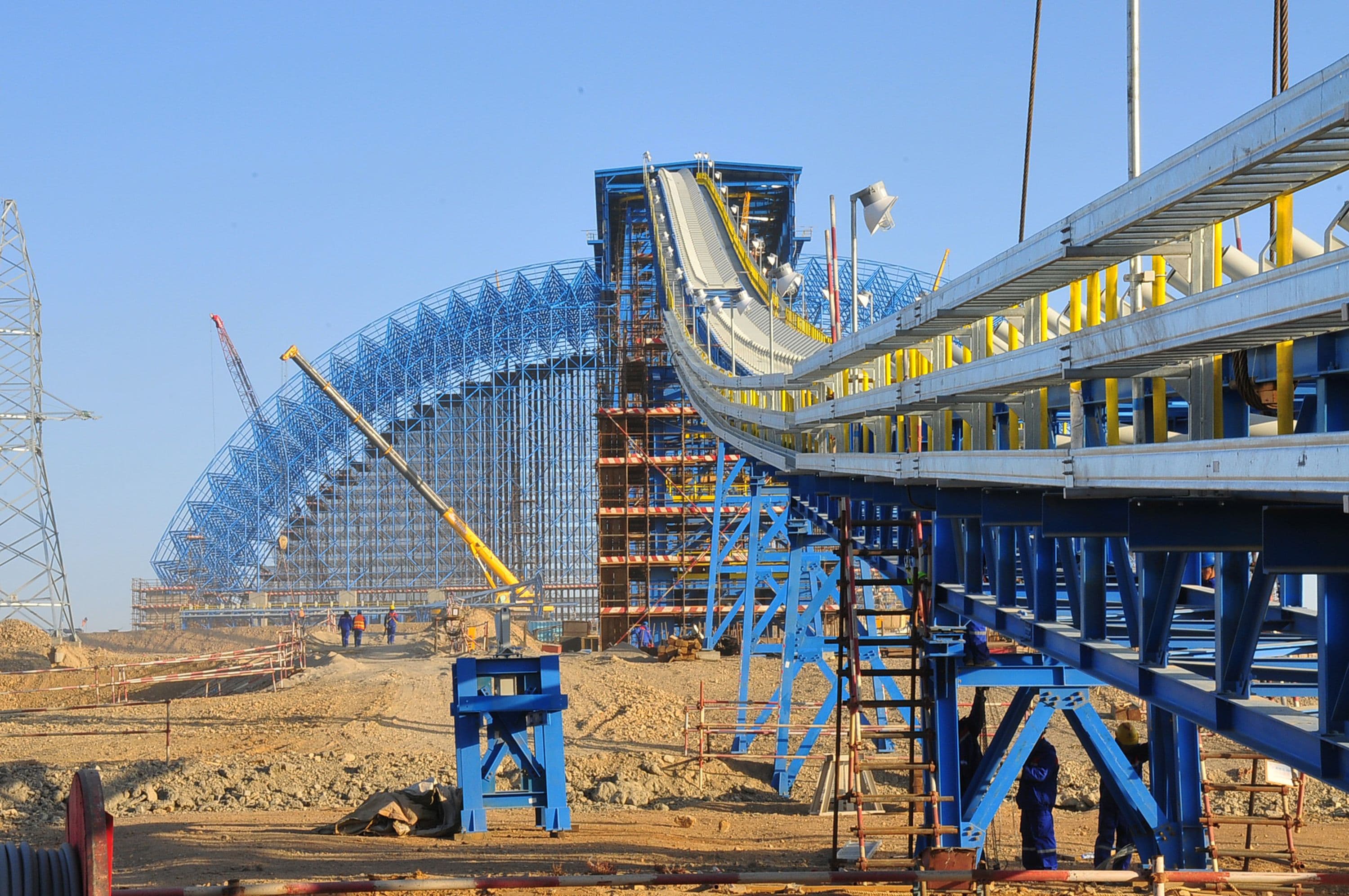
Fluor's Solution
In addition to program and construction management, we provided selected design and procurement services to build the copper concentrator, associated infrastructure, Shaft 2 headframe and related facilities.
To meet the challenges posed by the remoteness of the site, we applied our proven skills in safety, craft training, baseline-focused project controls and quality management. Our Shanghai, China office supplied some 60% of the technical and support personnel.
Other project infrastructure included upgrading a 104-kilometer road from the Chinese border to the site; building a 1,000-liters-per-second pipeline from a borefield 80 kilometers from the site; setting up housing facilities for more than 10,000 workers; and establishing 80 square kilometers of site development, including an airstrip, roads, concrete batch plants, water distribution systems, associated electrical power distribution and two mining shafts 1,800 meters each in depth.
The harsh environment demanded adaptation for typical project tasks. For example, in applying 145,000 cubic meters of concrete for the concentrator, the team used cold-weather techniques in order to pour concrete when it was -30° C. These techniques included fabricating tented structures with diesel-fired heaters to keep the formwork and rebar at an acceptable temperature and to keep the freshly poured concrete from freezing.
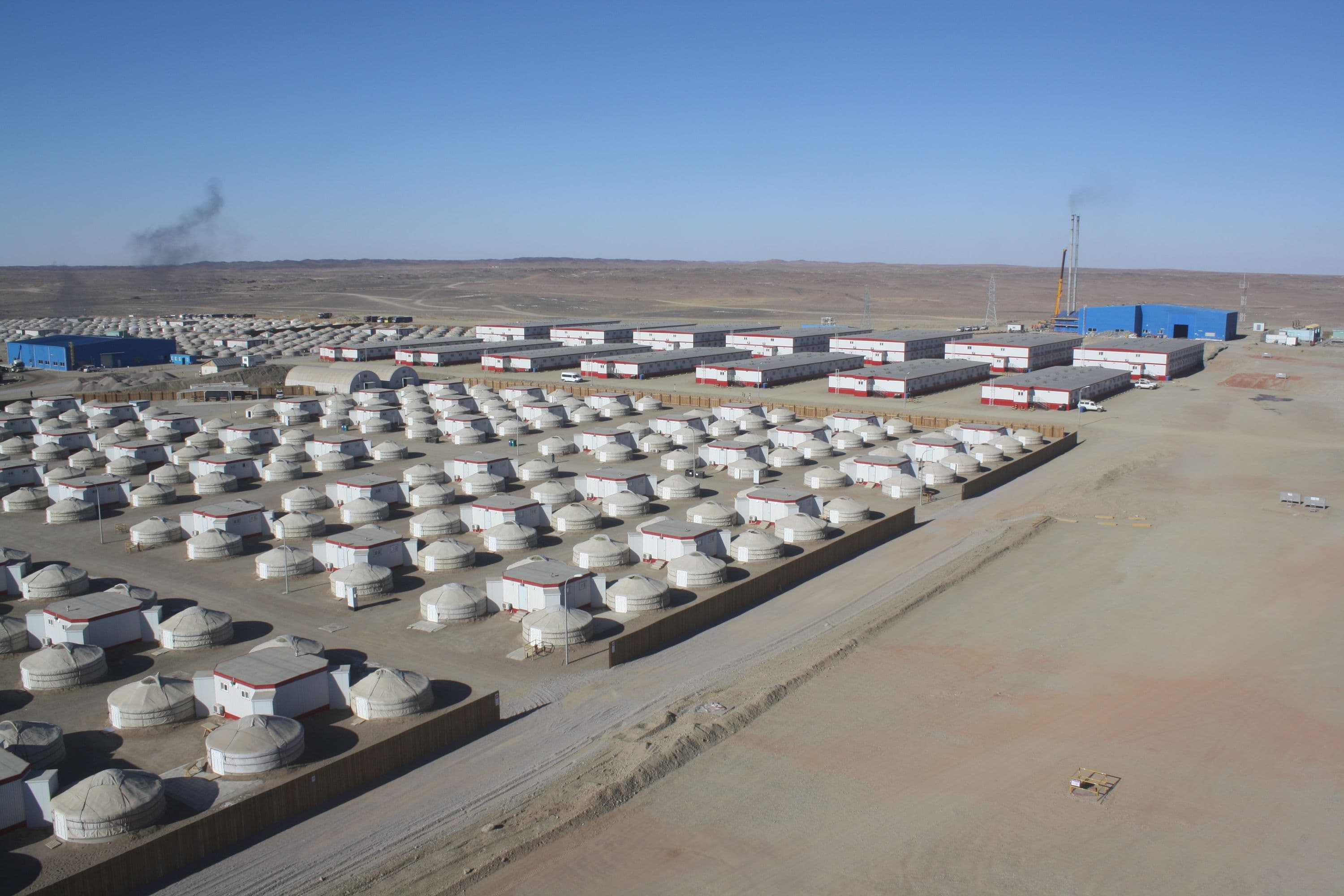
Conclusion
Using Mongolian labor with an infusion of Fluor's safety culture, plus an intern and leadership program in health, safety, environment and sustainability, the project achieved 10 million construction work hours without a lost-time incident.
The huge scope of the project was addressed by supplementing the limited Mongolian craft labor availability with thousands of Chinese craft workers.
The project, highlighted by the large-scale (100,000 tons per day) copper concentrator, is a significant driver of the Mongolian economy. Production began in 2013.
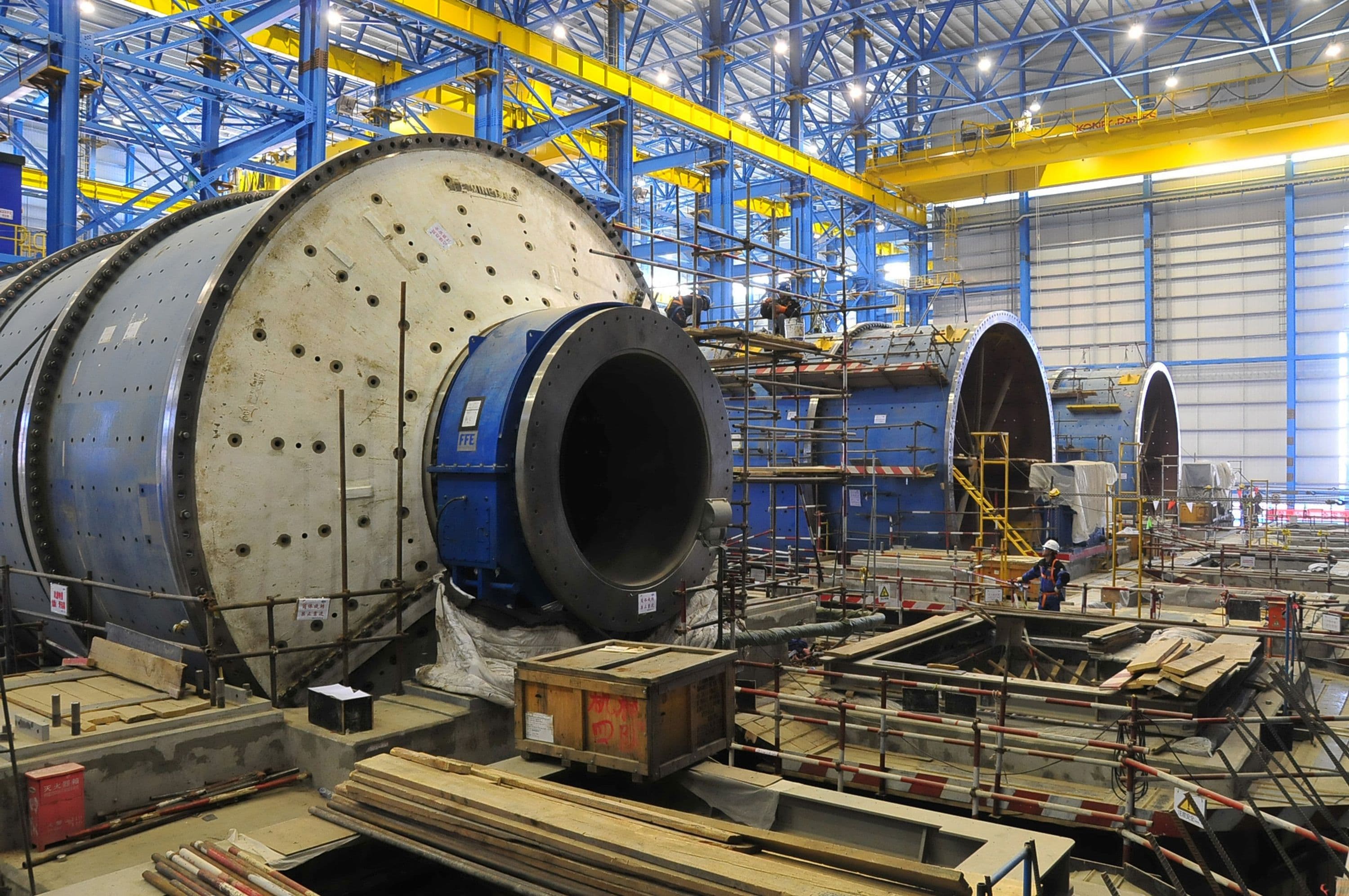
Project Gallery
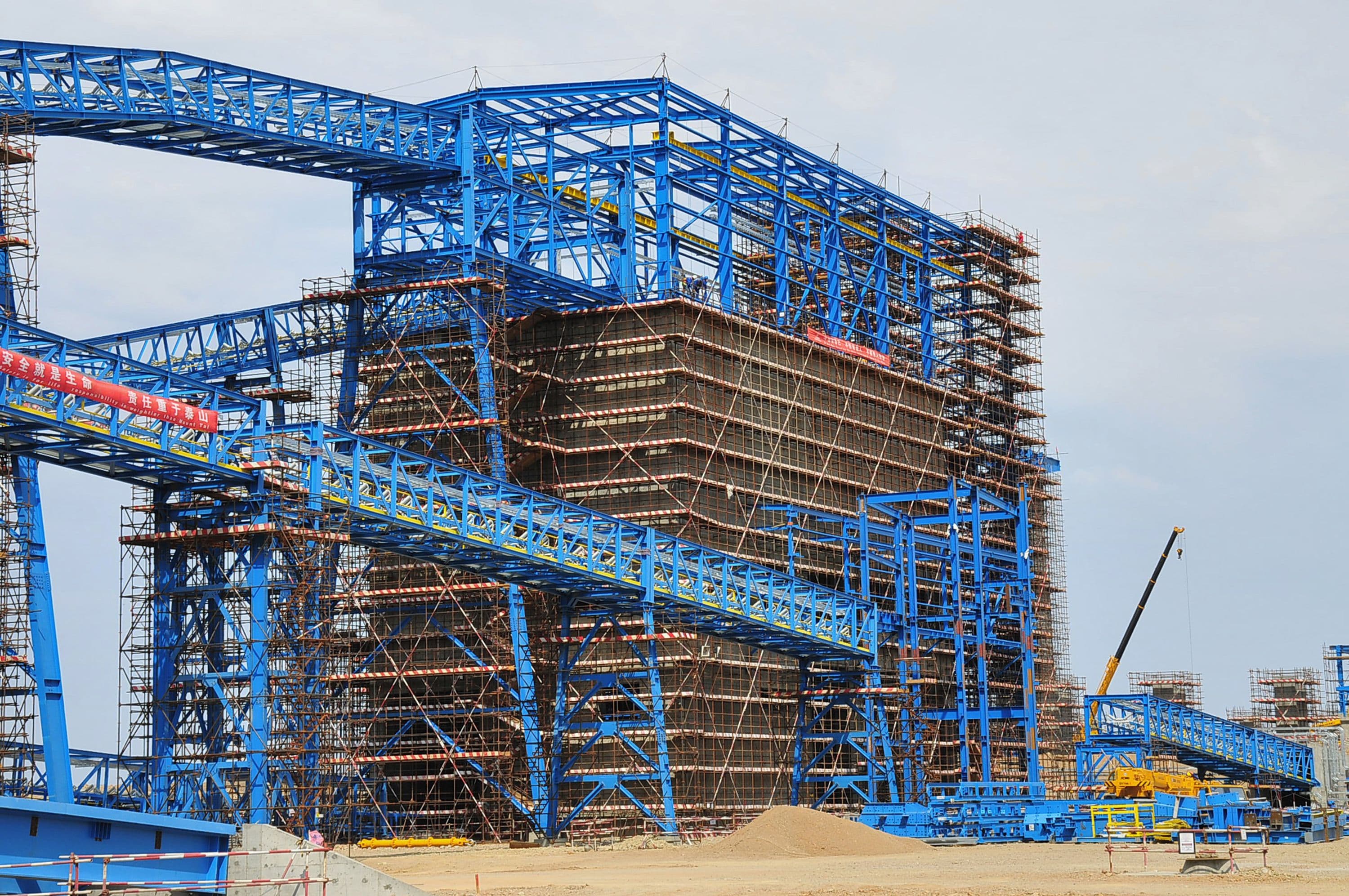
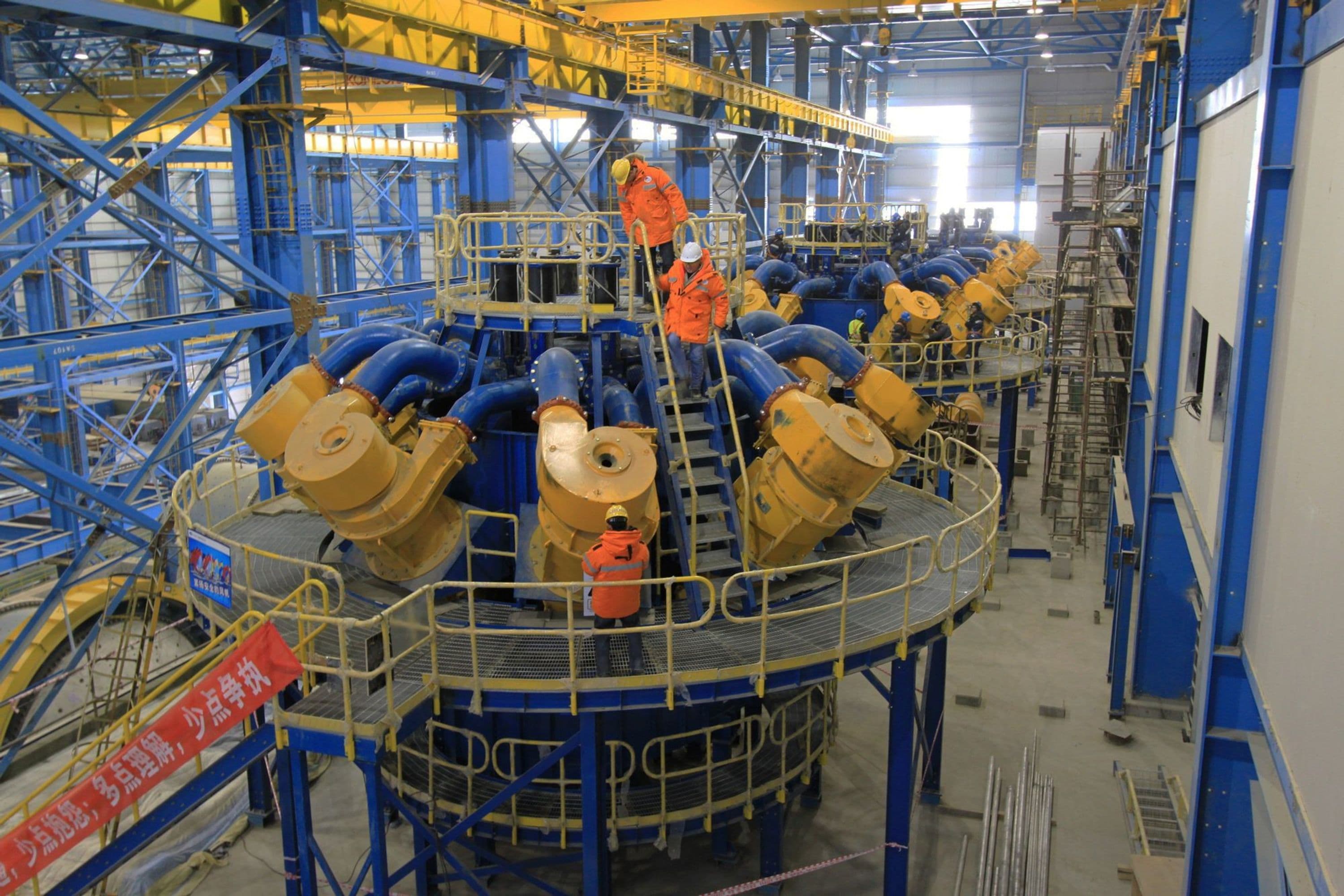
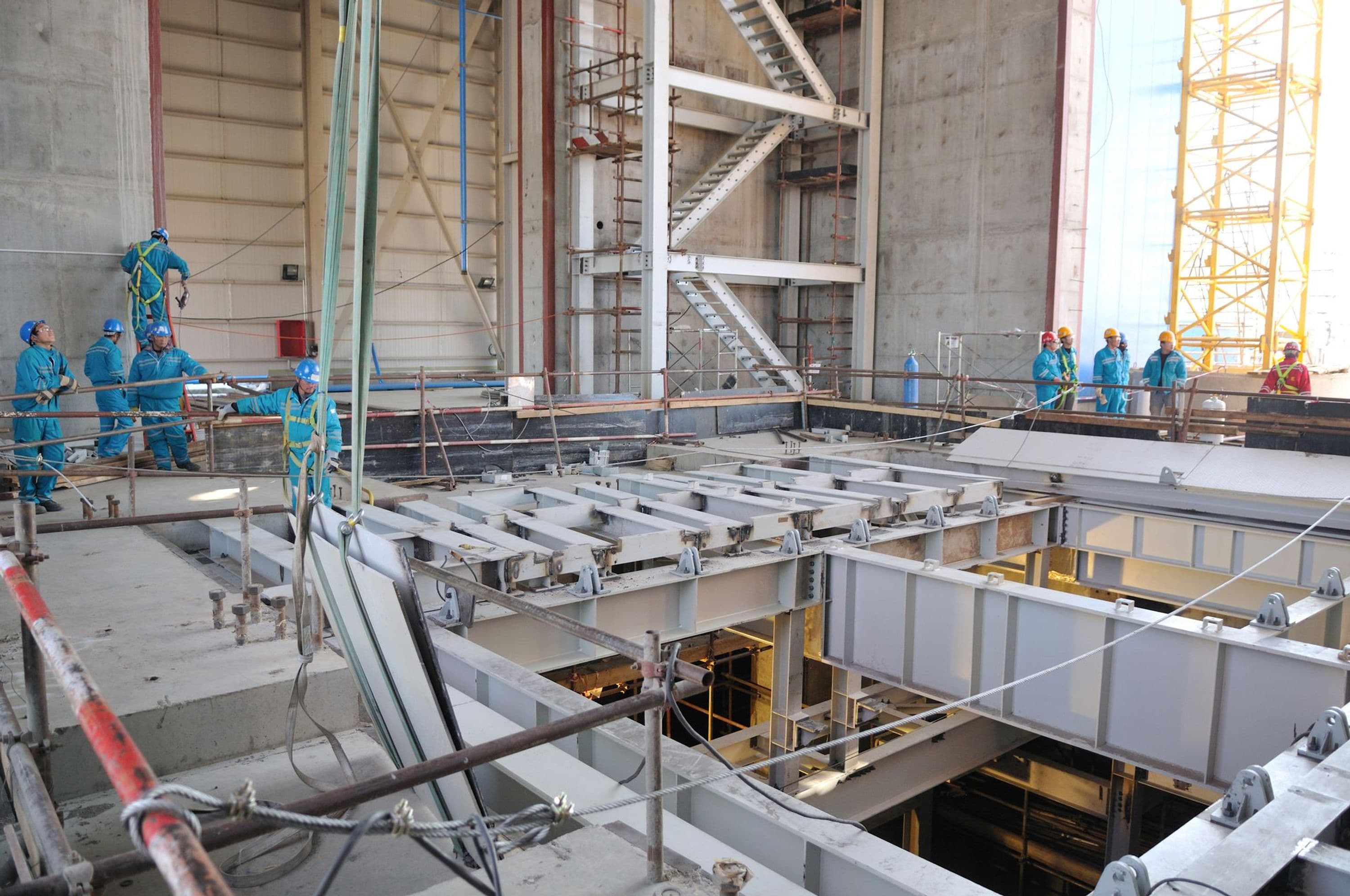
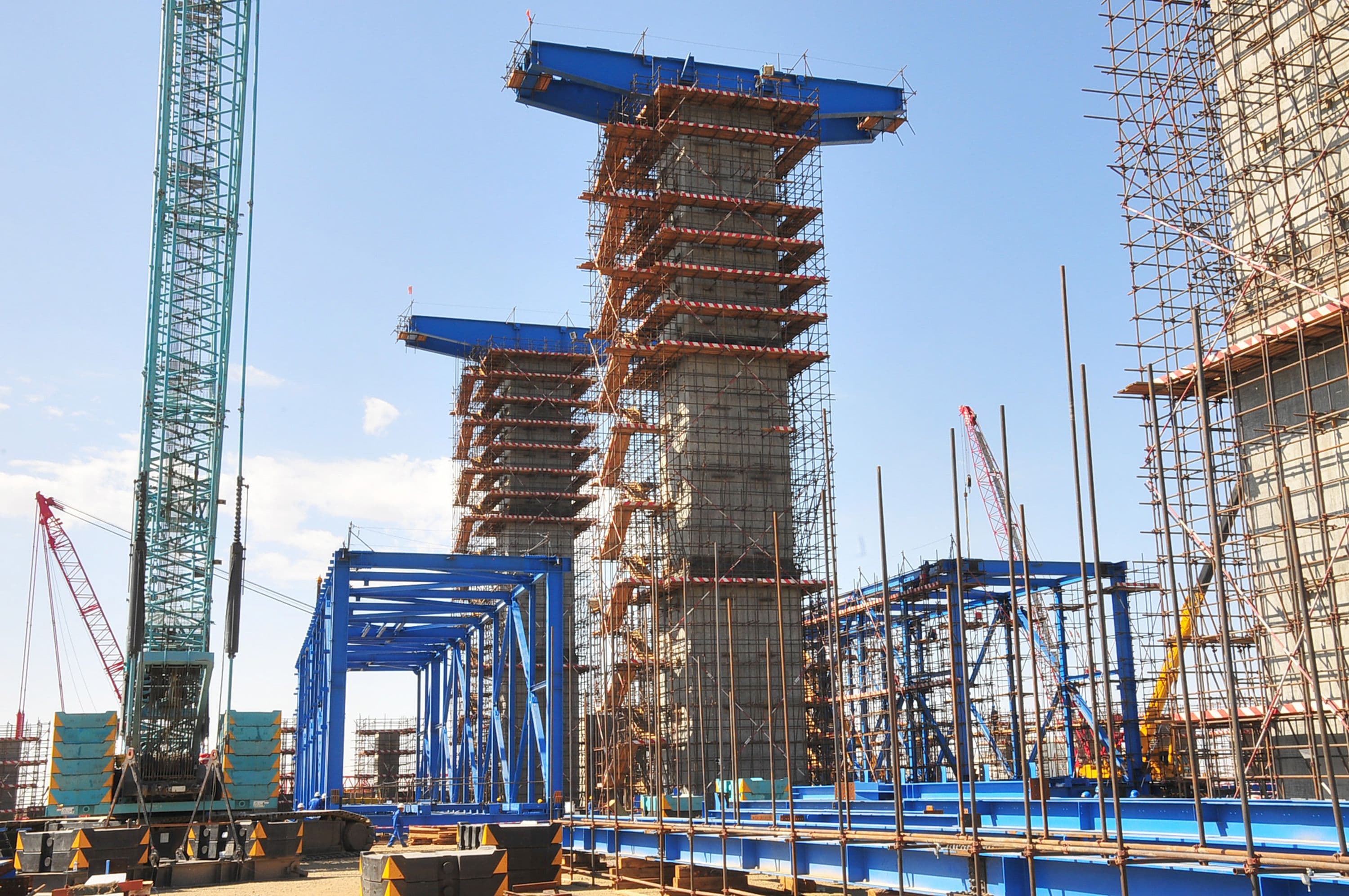
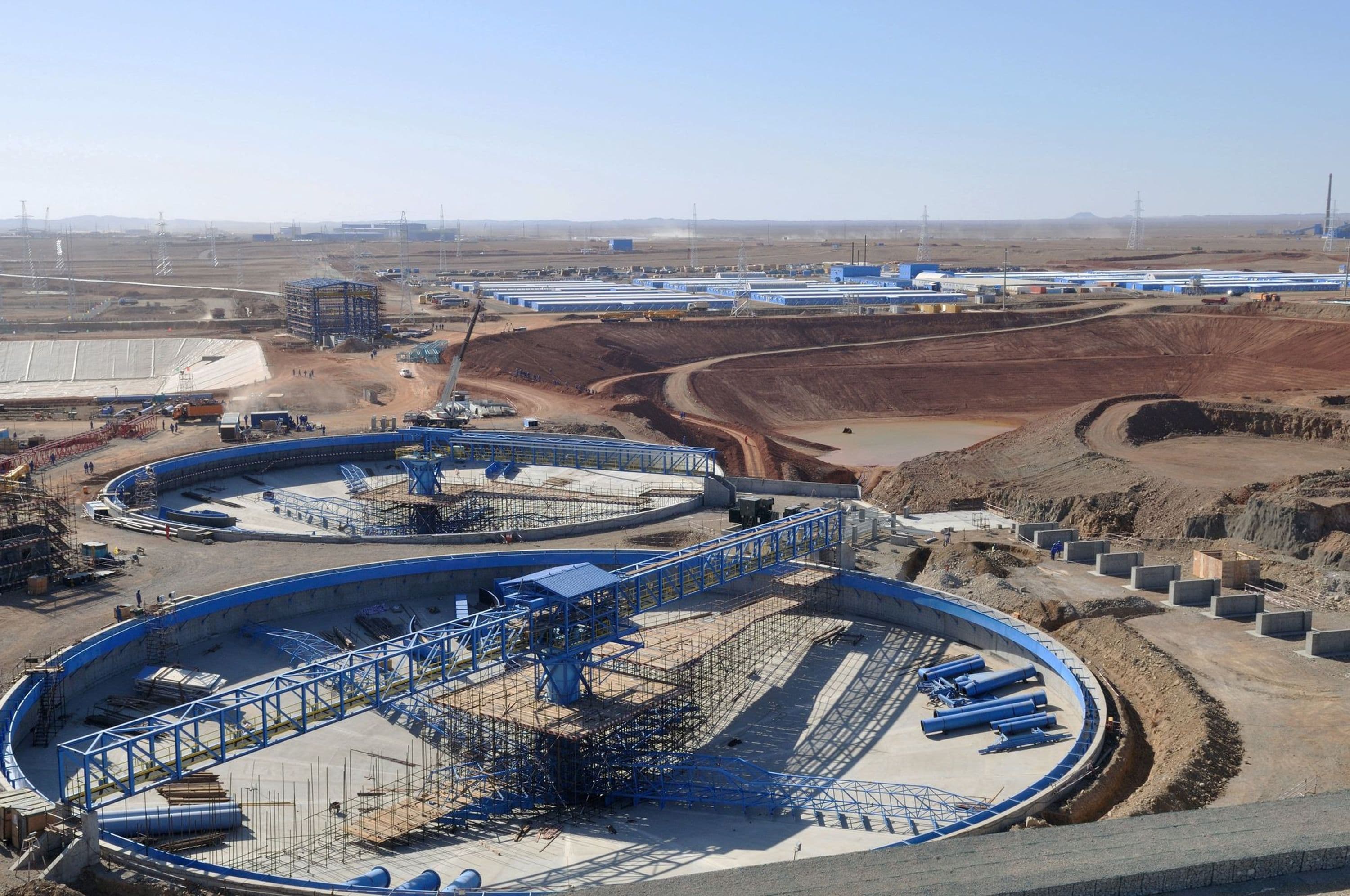
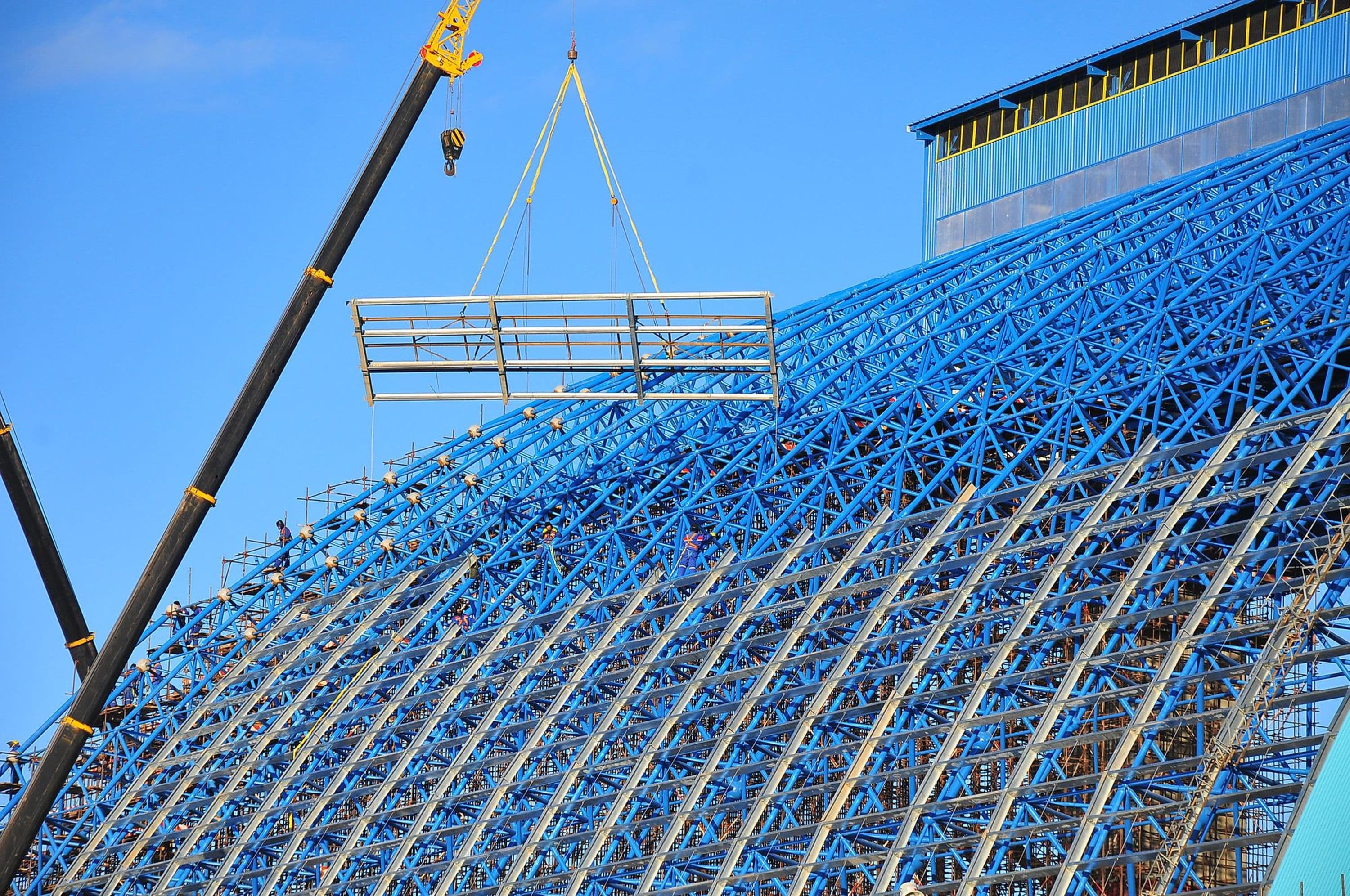
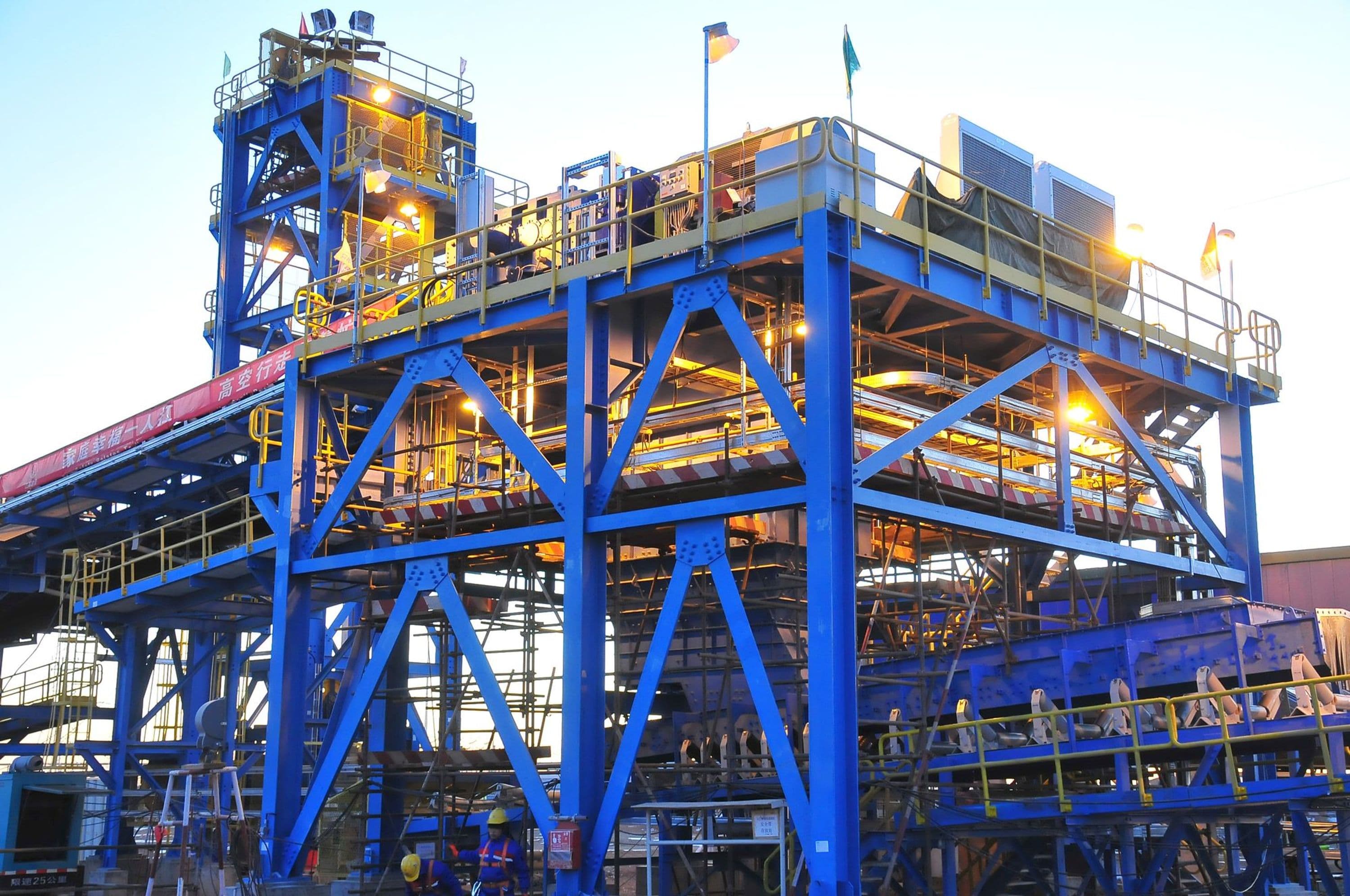
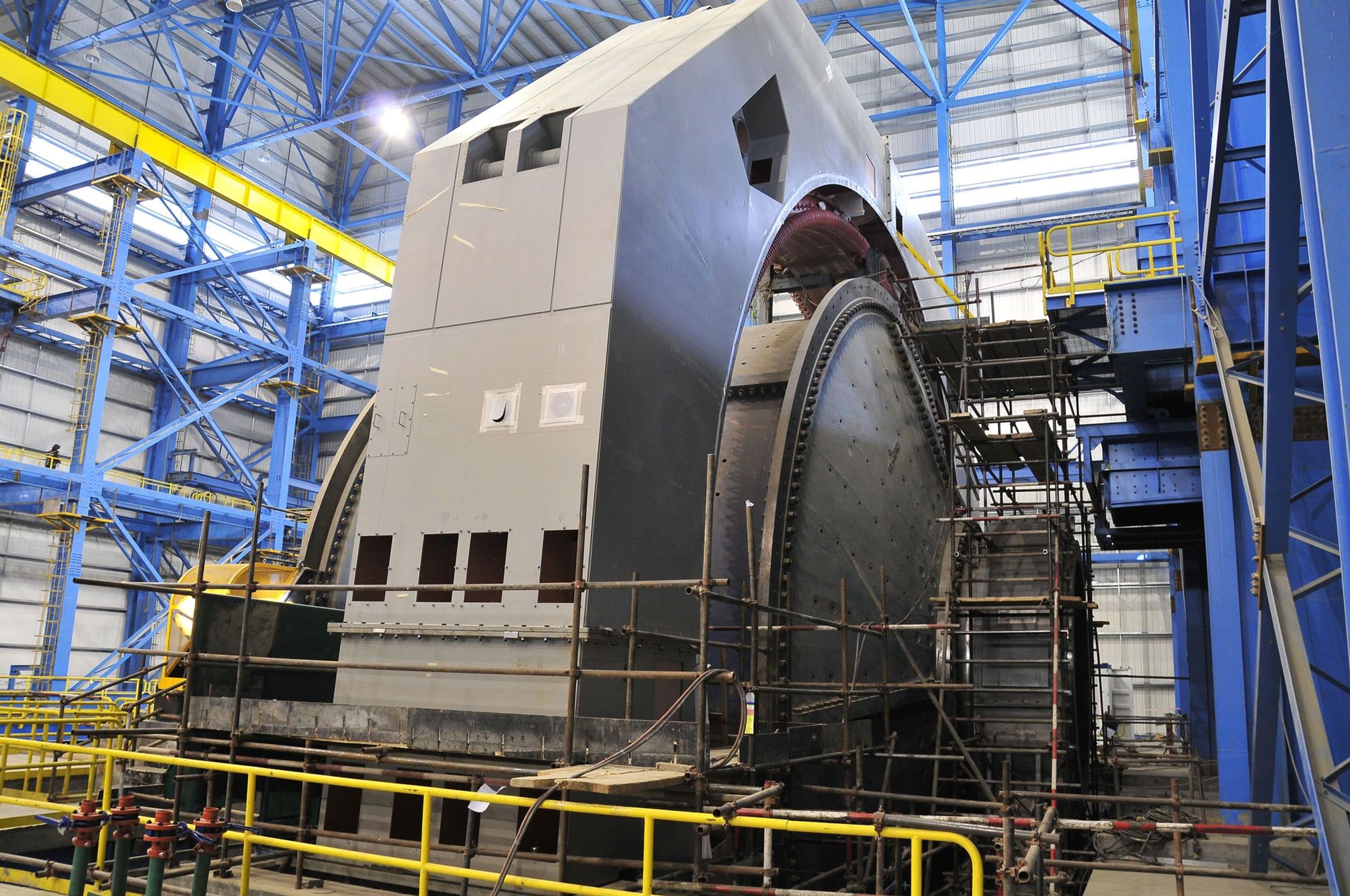