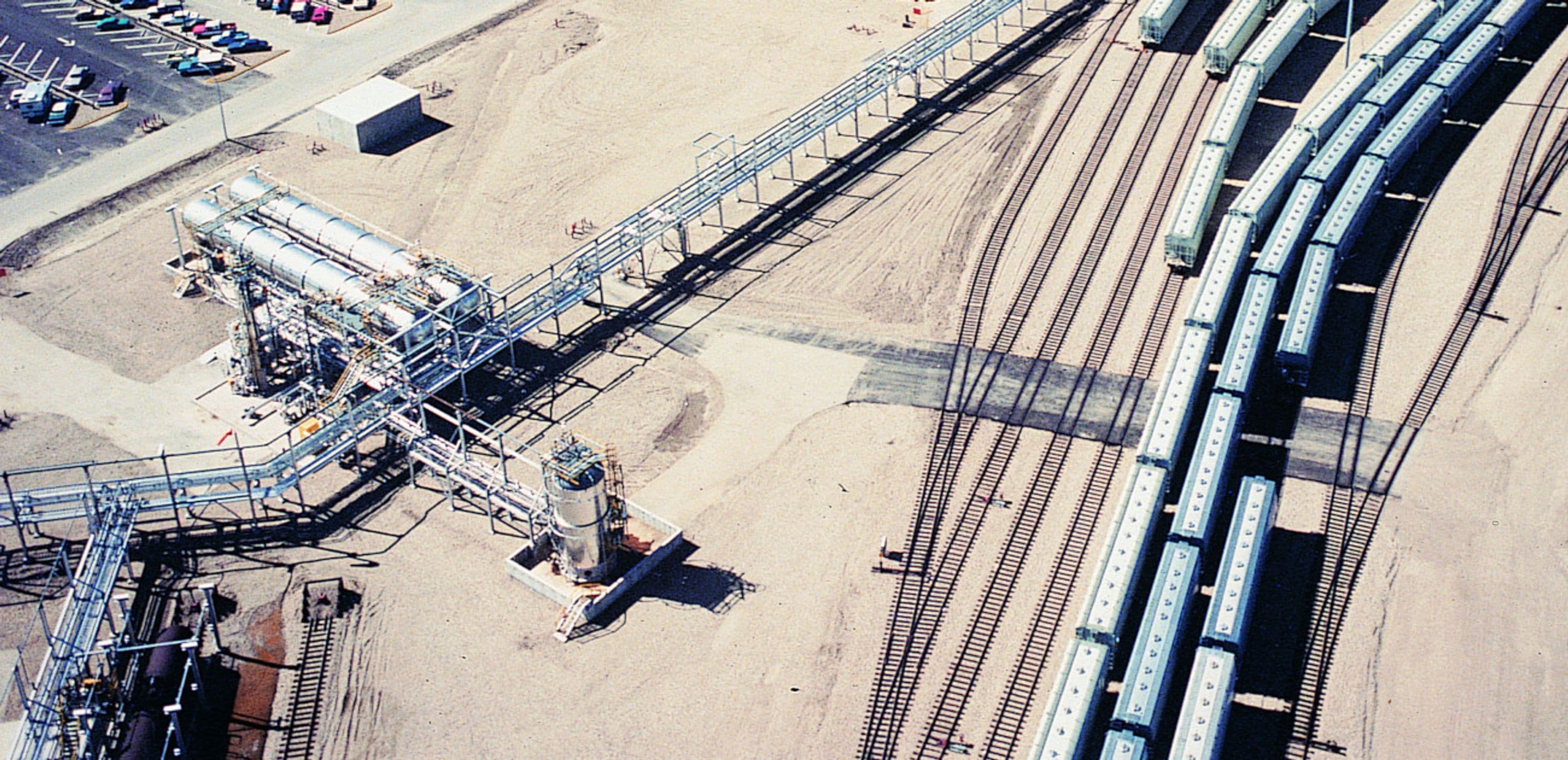
Novacor Rail Yard Design and Construction
Client: Novacor Chemicals, Ltd.
Location: Alberta, Canada
Business Segment: Urban Solutions
Industry: Infrastructure

Executive Summary
Fluor managed the construction of one of the largest privately owned, semiautomated rail yards in Canada as part of a total services contract for a 600-million-pound-per-year polyethylene plant.
We installed 11.7 miles of new track with 61 switches and upgraded an existing rail spur 2.8 miles long. The rail yard covered an area of approximately 65 acres. The rail yard consists of 33 tracks with a total length of 18 kilometers. It is one of the largest in Western Canada. We also participated in the development of a rail yard operation plan that included loading, unloading, car washing, switching, weighing, storage and transfers.
Client's Challenge
Novacor's rail yard operation included a sophisticated computer-controlled inventorying system. To reduce labor requirements, operated hydraulic car movers were used within the hopper car building to jostle cars underneath loading spouts every 15 minutes. The building, where all loading, unloading and hopper car washing took place, used over 4,100 cubic meters of concrete and 1,000 tons of steel.
All car movements on three tracks were computer interlocked through electric derailers, wheel detectors and switchlocks. The overall railroad system incorporated the latest developments at the time in inventory control, safety and operability.
Fluor's Solution
We conducted a major hydro-geologic survey and drainage study prior to starting the project, and as a result of the two studies the rail yard was designed to minimize the water table drainage requirement and yet achieve maximum operational efficiency. We also participated in a computer simulation study that assumed a random delivery of returned cars and product departures from the plant.
The simulation was used to determine the length and number of storage spurs required. A “herringbone” layout pattern was devised for the storage yard to store and ship multiple products with no bottlenecks. An automated scale model was used to test operability of the rail yard and to train operators.
Conclusion
We successfully performed engineering, procurement, and construction on Novacor's rail yard project. The overall railroad system incorporated the latest developments in inventory control, safety and operability. Other significant aspects of the project included major traffic control considerations, system communications, yard design and construction, logistical support, quality control and quality assurance programs, plus procurement, shipping, inspection and expediting responsibilities.
The first phase of the project allowed for 650 hopper cars, with future expansion capacity to 900 cars.