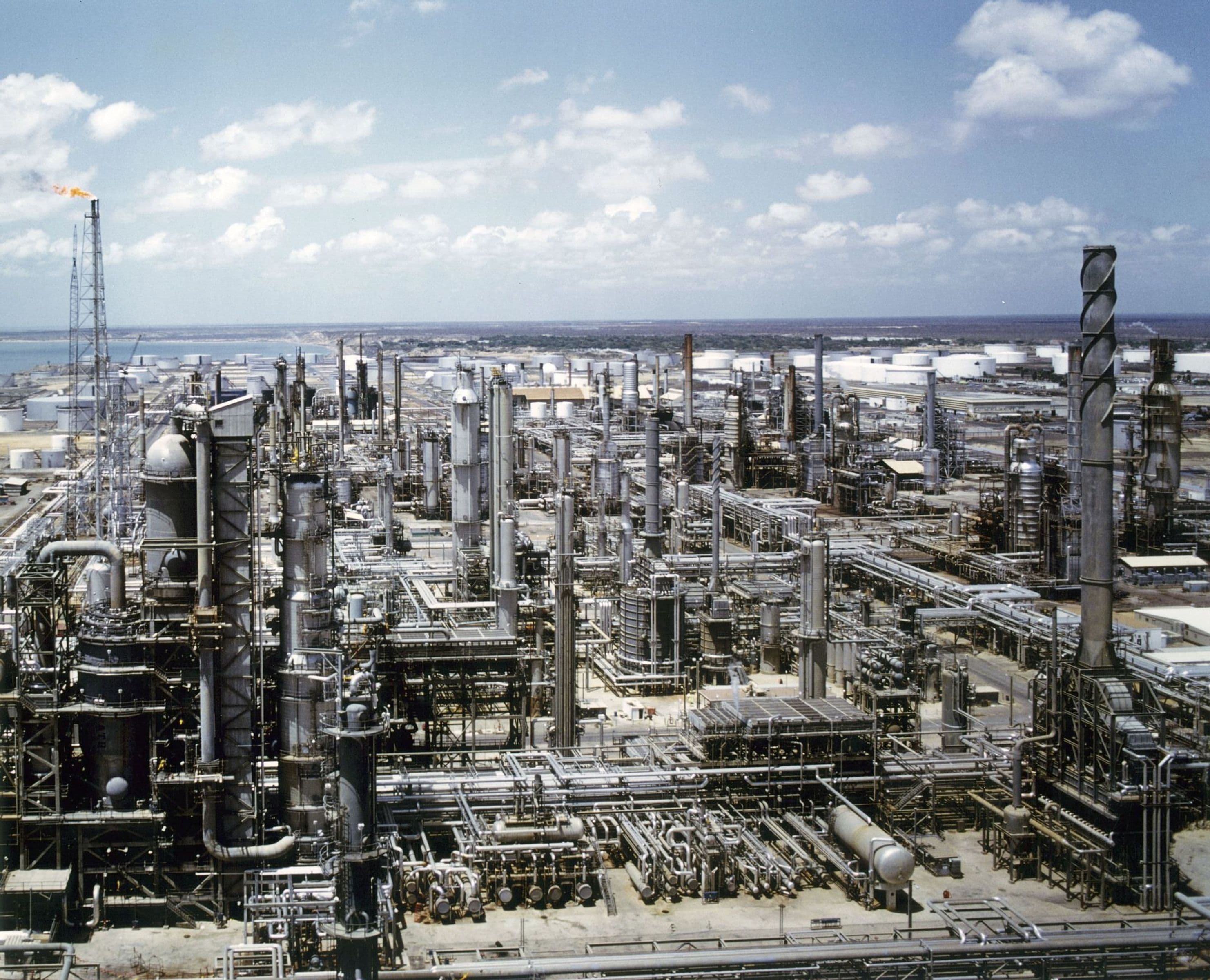
Lagoven Refinery Upgrade and Expansion - EPC
Client: Lagoven S.A.
Location: Amuay, Venezuela
Business Segment: Energy Solutions
Industry: Fuels

Executive Summary
Fluor provided engineering, procurement and construction services to Lagoven, S.A. for a massive upgrading and expansion project at the Amuay Refinery in Venezuela, making the facility one of the most modern and sophisticated complexes of its type in the world.
Client's Challenge
Lagoven wanted flexibility in coping with fluctuations in the residual fuels market by refining additional heavy crudes and increasing gasoline production capacity. Just like Canada and the United States at that time, Venezuela was running low on supplies of light, easy-to-refine crude oils when consumption of gasoline and other light products was rising. In order to keep pace with demand, Lagoven intended to produce more gasoline and less high-sulfur and residual oils.
The new units at Amuay included a 52,000 barrel-per-day Exxon-patented FLEXICOKER (the largest of three in existence at the time), a 74,000 barrel-per-day FLEXICRACKER (Latin America's largest), a 14,200 barrel-per-day alkylation unit, a 7,500 barrel-per-day isomerizer and six Merox units needed to desulfurize naphthas and gases from the light-ends recovery section.
These components were crucial to process a greater proportion of heavy oils, to reduce the volume of high sulfur residual fuel oil production and to substantially increase gasoline production.
FLEXICOKING converted the heaviest and highest metals-content residuals to naphthas and distillates. It also yielded large volumes of easy-to-handle byproduct gas that could be used as fuel instead of being flared wastefully.
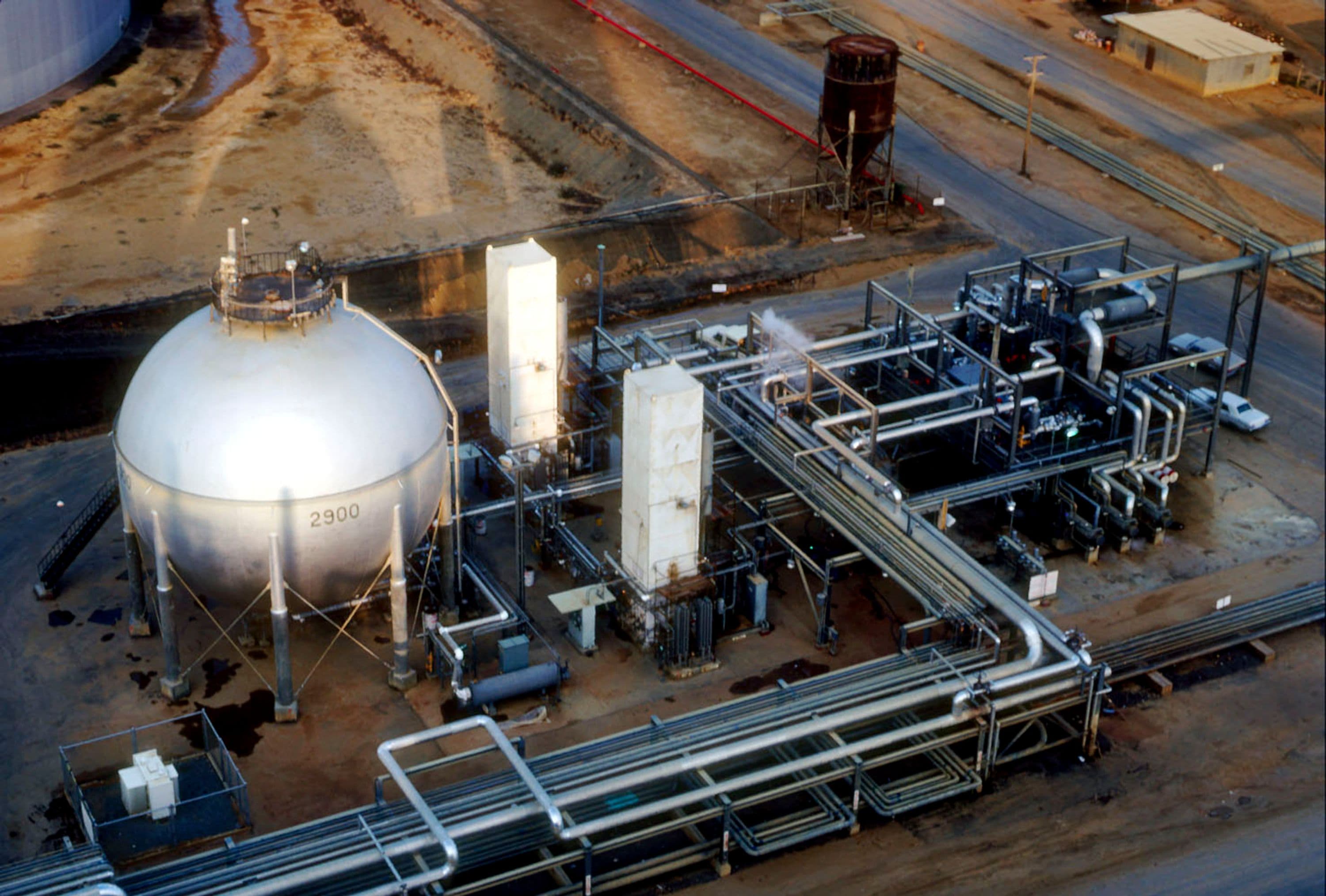
Fluor's Solution
Fluor's scope was engineering, procurement and field construction of four new facilities/units: a FLEXICRACKER, Exxon's patented FLEXICOKER, new light-ends and liquid propane gas recovery and HF alkylation and butane isomerization.
To support Lagoven's desire to keep at home as much of its huge investment as possible, Fluor established a project office in Caracas, subcontracting 140,000 hours of engineering and purchasing the majority of project materials and equipment in Venezuela. Of the peak construction workforce, more than 7,500, or 96%, were Venezuelan. In addition, we established a craft training center at the site, where the skills of more than 1,800 Venezuelans were upgraded. They were trained as welders, iron workers, pipe fitters, millwrights, boilermakers and electricians.
The 52,000 barrel-per-day FLEXICOKER was the third, and by far the largest, unit of its type of construction at the time. Its massive size, complexity and vibration and temperature considerations made it a challenge to design and build.
Our first project at the Amuay refinery had been in 1968. The upgrade was in 1982. Other refinery projects continued into the 1990s.
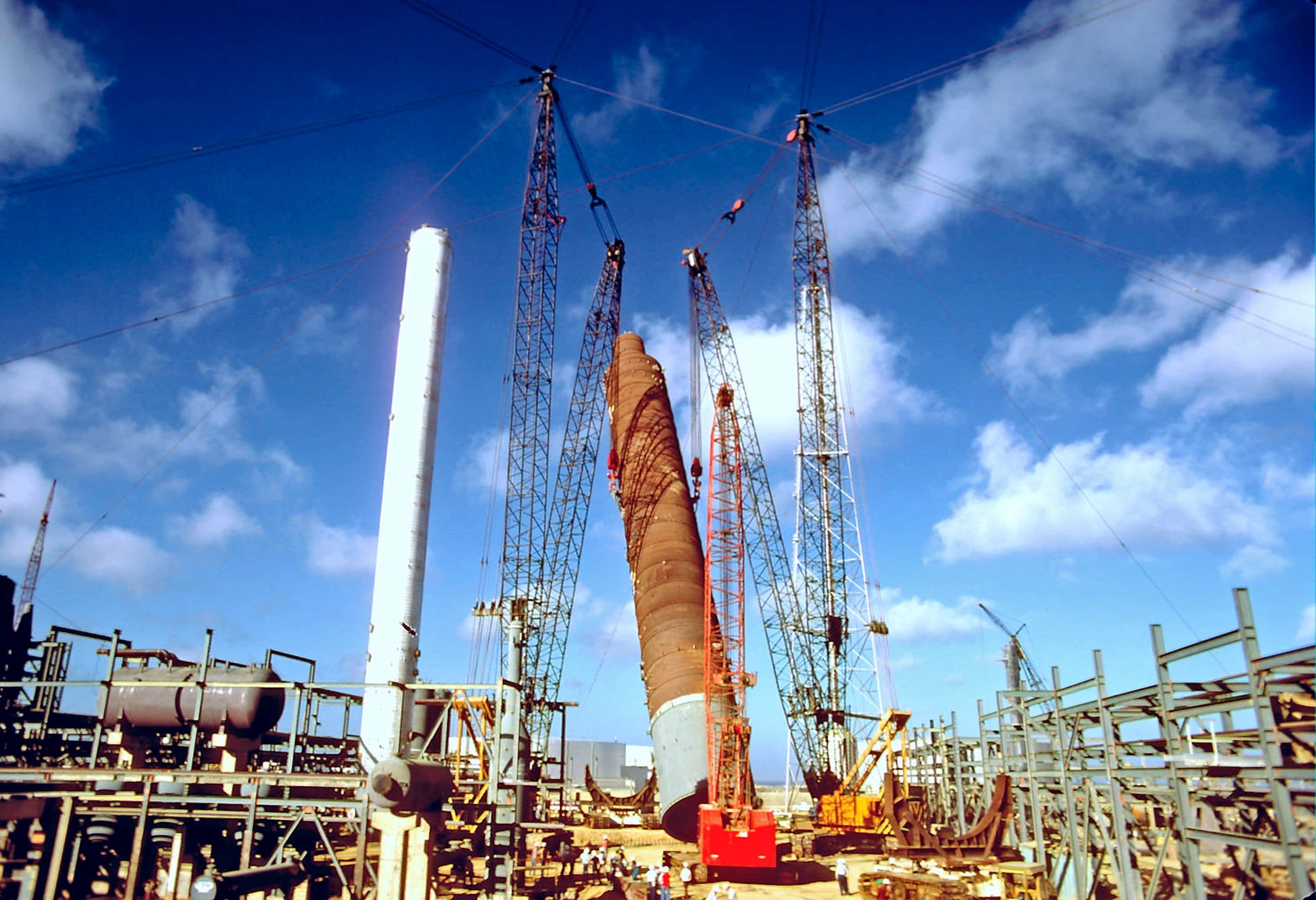
Conclusion
The project had an outstanding safety record in spite of the relatively low experience and skill level of much of the labor force and lower-level supervision. In addition, personnel from Lagoven, Exxon and Fluor who were involved in the latter phases of field work agreed that the plants started up smoothly and operated well.
The Amuay project increased production of motor gasoline and greatly reduced production of heavy fuel oils, making it one of the most modern and sophisticated refineries in the world.
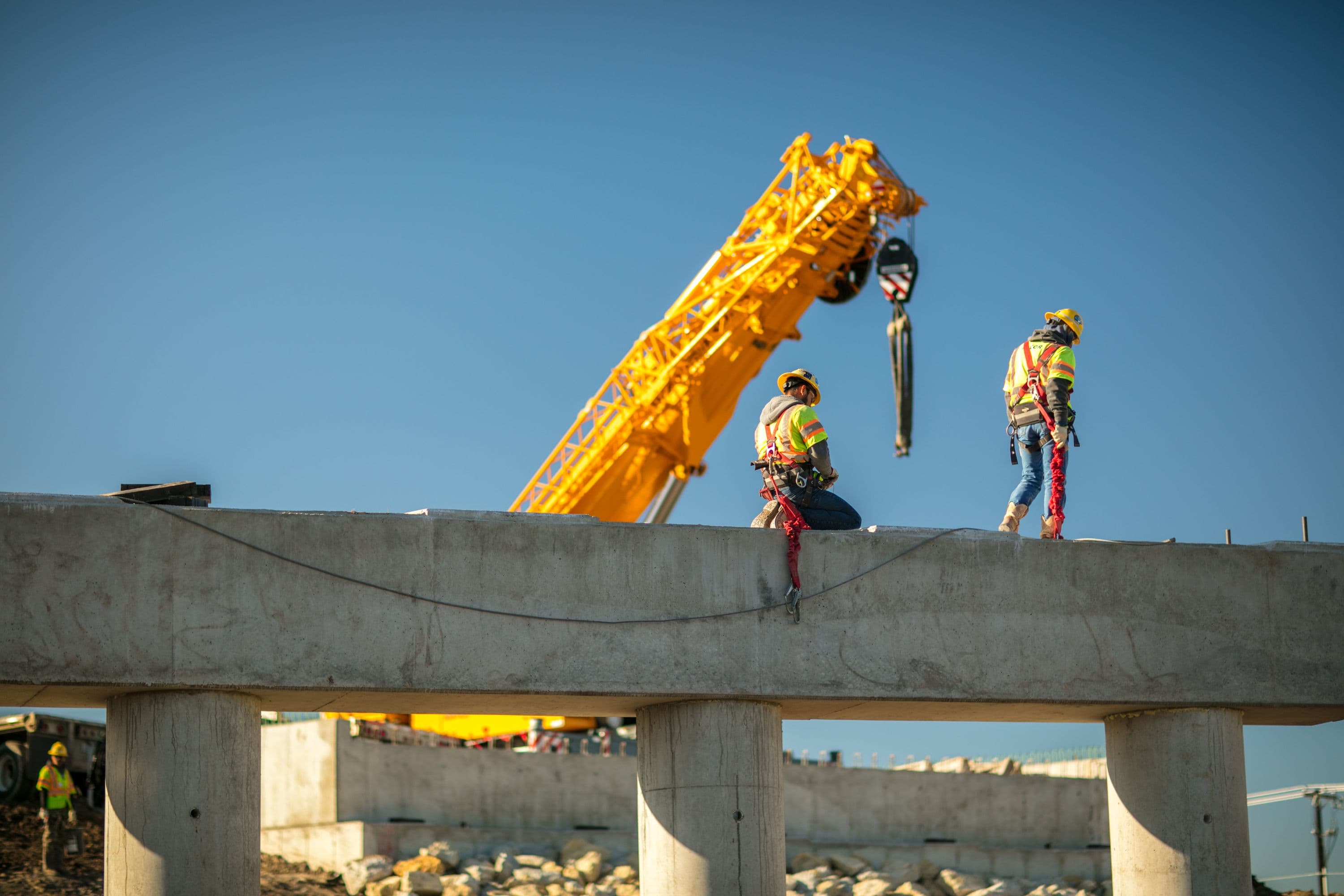