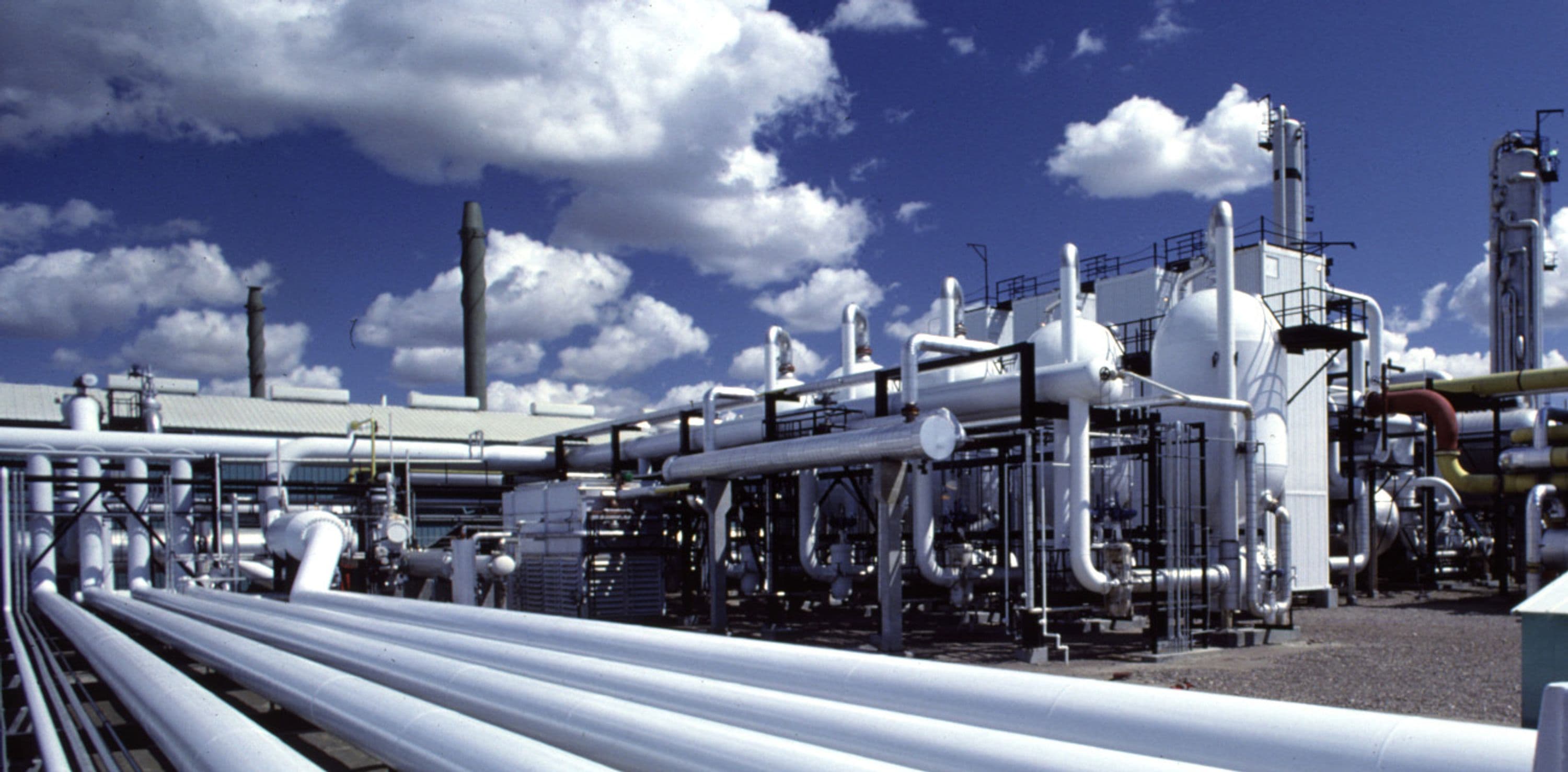
Dome Petroleum Electric Conversion - Design and Procurement
Client: Dome Petroleum Limited
Location: Empress, Alberta, Canada
Business Segment: Energy Solutions
Industry: Fuels

Executive Summary
Fluor was asked by client Dome Petroleum to increase the energy efficiency of a natural gas liquids extraction plant in Empress, Alberta, Canada. To do so, we undertook a replacement of the plant's original natural gas-fired engines with two electric motors that were at the time of the project's completion in 1981 the largest of their kind in Canada.
Client's Challenge
We designed and built the existing turbo-expander facility at Empress, which went on-stream fall 1971. The facility processed 1.5 billion standard cubic feet of gas per day. At the time, it was the largest such plant in the world.
Dome Petroleum awarded Fluor a follow-on plant expansion in 1978 to increase the ethane recovery. The ethane product of the expanded plant served as feedstock for a planned petrochemical complex near Joffre, Alberta. With the demonstrated project success, Dome Petroleum contracted us to make the Empress facility more energy-efficient. We were tasked to make major changes with both the motors and the plant's internal systems.
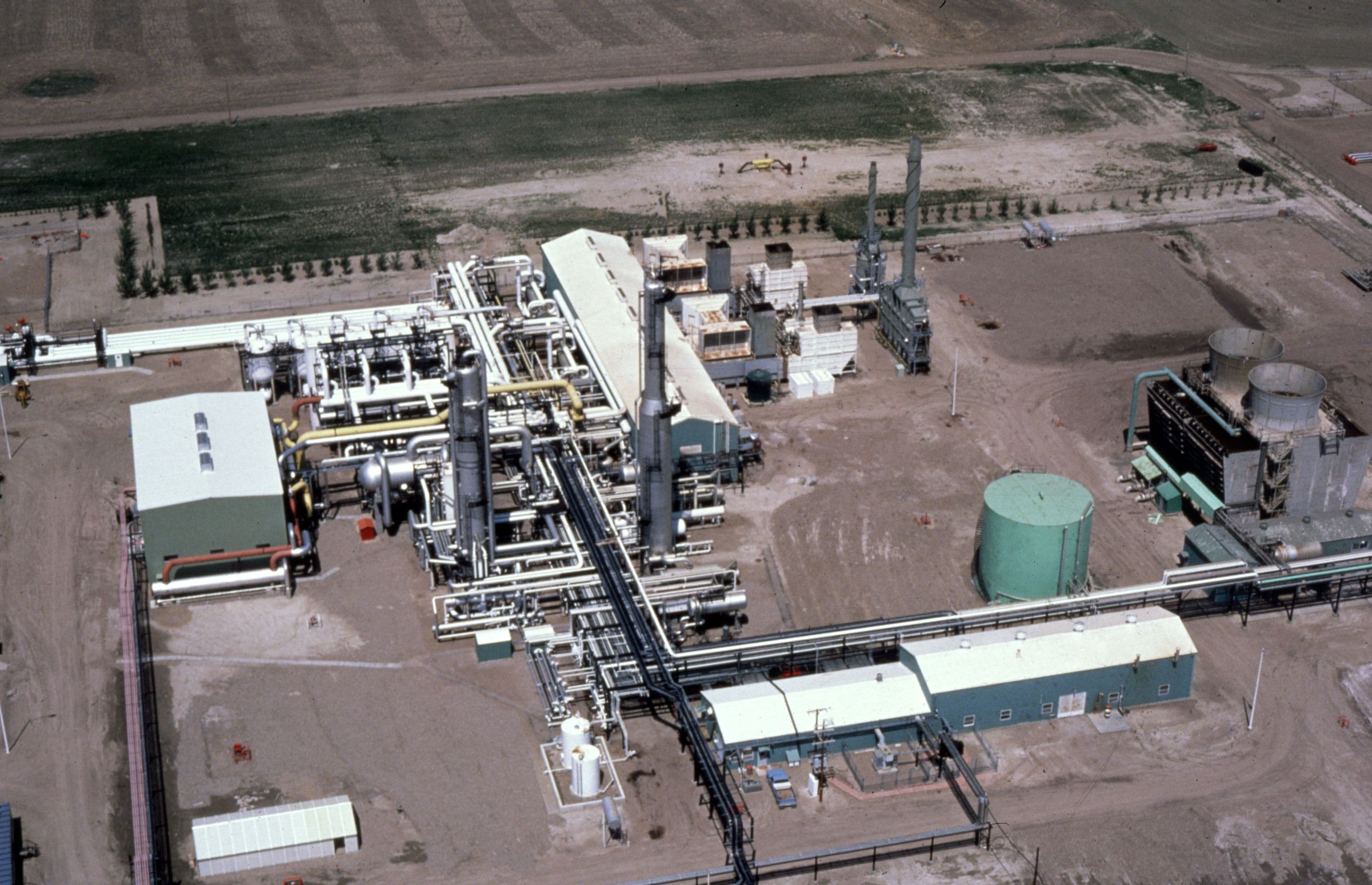
Fluor's Solution
We procured two new 25,000 brake horsepower (BHP) synchronous electric motors to replace the existing turbines. Weighing 28 tons each, they would be the largest engines in Canada when the project was completed.
We also designed new systems for interacting with these engines and attaining the efficiency goals Dome Petroleum sought.
The complete conversion process included adding electric motor-drive compressor trains and auxiliary facilities, refrigeration and ethane product compressors and drivers, modifications to offsites and utilities and instillation of major electrical ancillary equipment. Two fired heaters were also used to replace the existing gas turbine waste heat recovery system.
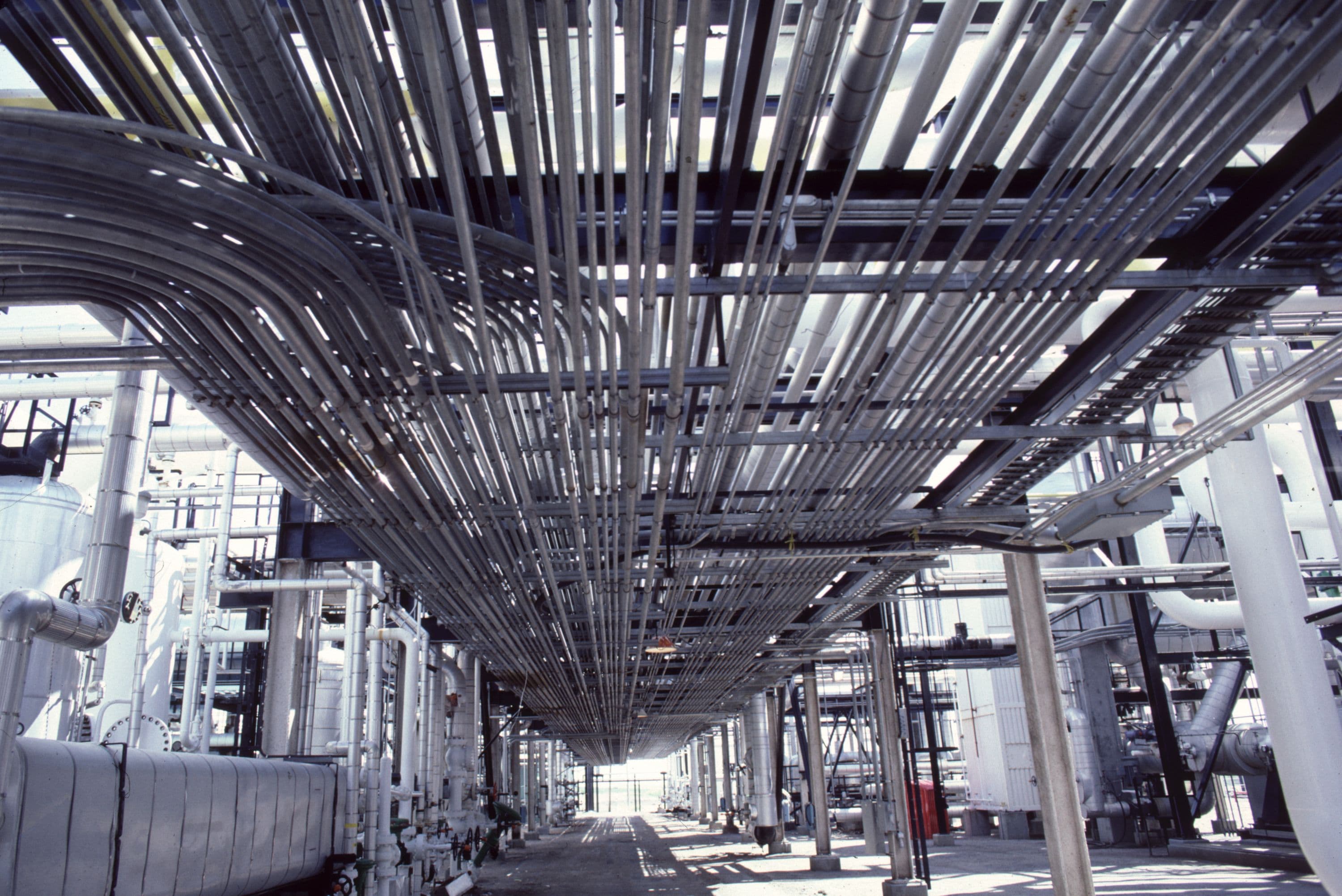
Conclusion
Early completion of piping and mechanical work allowed the conversion shutdown to occur two weeks ahead of schedule. This resulted in quicker demobilization of staff and some material savings. The entire project was completed successfully in 1981 and was a model for other electric conversions of its kind.
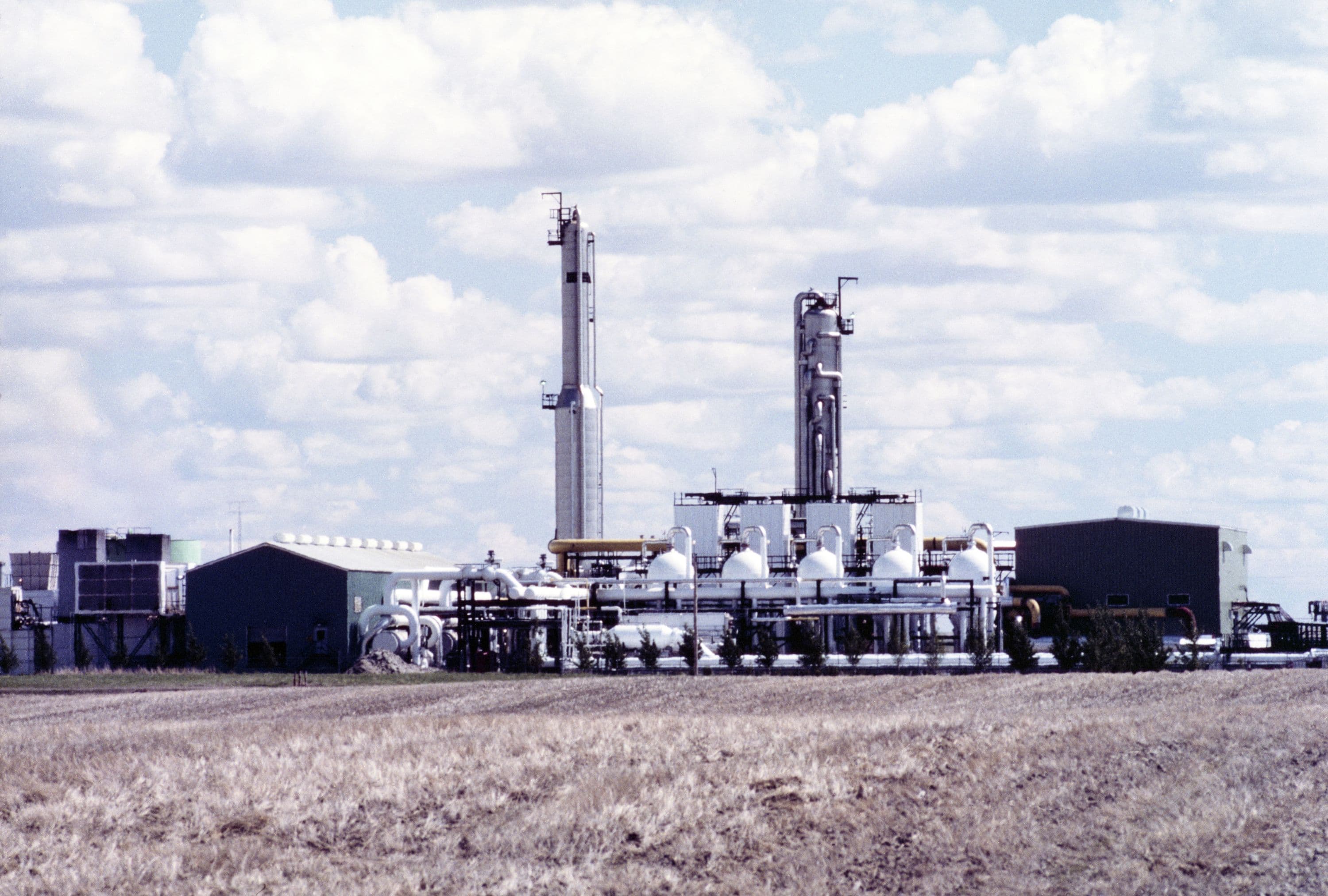