&w=3840&q=75)
Shirley Basin Uranium Mill
Client: Utah International
Location: Wyoming, U.S.
Business Segment: Urban Solutions
Industry: Mining & Metals

Executive Summary
In 1959, Utah International started underground mining operations at Shirley Basin mine in Wyoming to meet the increasing needs of the United States Atomic Energy Commission.
By 1968, open-pit mining operations had begun. At the same time, to overcome the burden of shipping the ore 145 miles to another Utah facility for processing, it was decided to build a new uranium-processing mill at Shirley Basin.
Utah International awarded Fluor the engineering, procurement and construction of a second-generation uranium plant, the Shirley Basin mill. Shirley Basin was originally designed to handle 1,200 tons per day of uranium-bearing ore.
At Shirley Basin, we introduced the industry innovation of using semi-autogenous grinding in a uranium plant, eliminating the need for crushing.
With severe winter weather at Shirley Basin, we developed a schedule for completion of most external work on the processing mill before the winter weather could hinder construction. The design features an automated central control room that allows a single operator to remotely manage the processing units, minimizing manpower and operator exposure to the winter conditions.
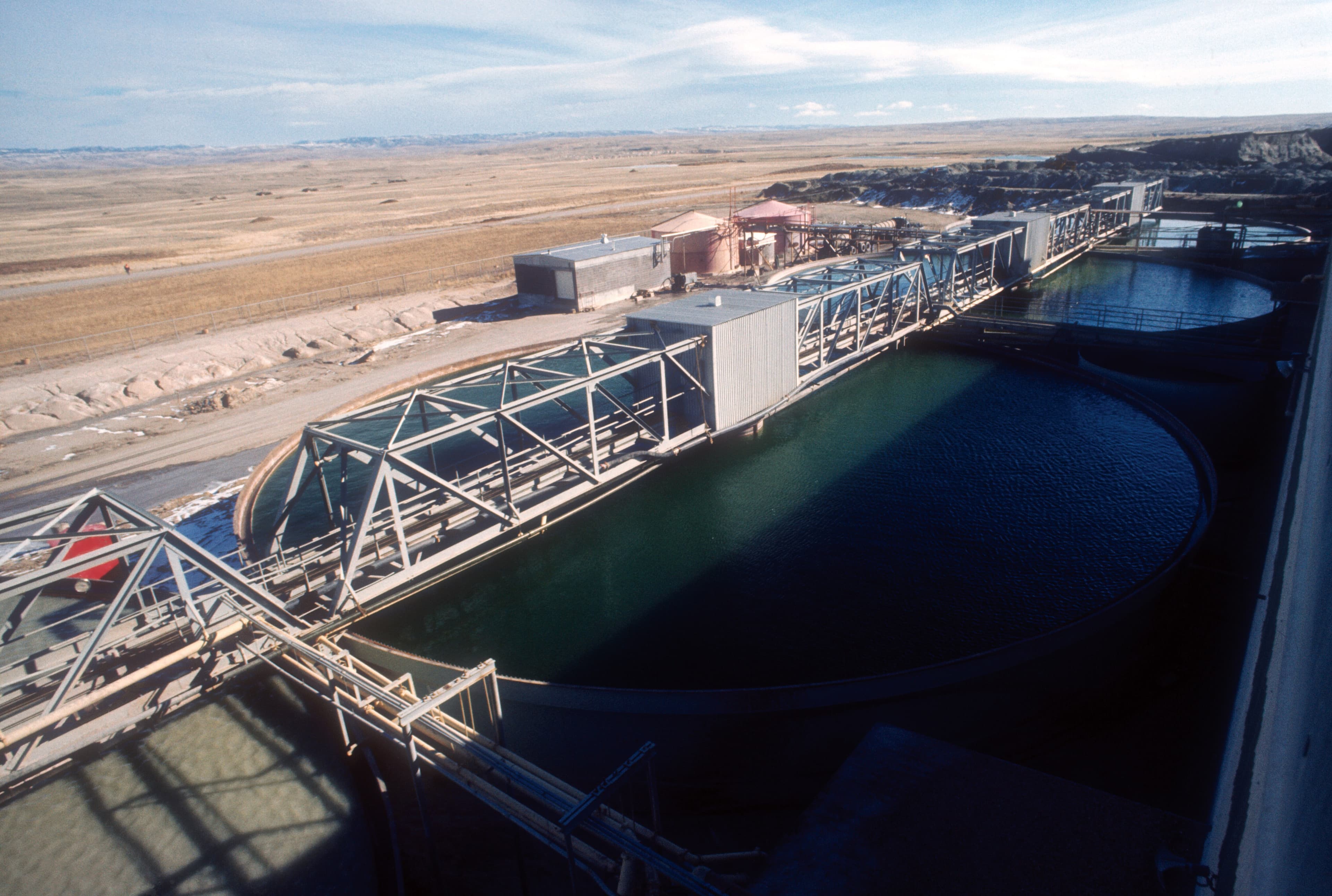
Client's Challenge
Shirley Basin, located 68 miles south of Casper, Wyoming, had been a quiet grazing land before the discovery of uranium in the area.
At Shirley Basin, the ore averages from 0.25% to 0.30% uranium. At that yield, a very large amount of ore had to be processed to produce the highly concentrated final product of uranium oxide, known as yellow cake.
The blended ore is crushed into fine sand and combined with water. This slurry is leached with sulfuric acid to produce a solution containing uranium and other impurities. After leaching and thickening, the uranium is extracted from solution using fixed bed ion exchange where the impurities are removed. The resin ion exchange circuit is entirely controlled from this one location by a single operator. Next, the pure uranium-bearing solution is centrifuged to separate the uranium from the solution and dried into concentrated yellowcake. After filtration, the yellowcake is dried and shipped in 50-liter drums.
The weather at Shirley Basin is severe. There is usually a constant wind, which, combined with snow and the winter temperatures often reaching -40° F, can cause many construction problems.
Workers and employees to Shirley Basin commute daily, typically a 75-minute drive from their homes in Casper, Wyoming.
We were tasked to design and automate the processing operations to minimize manpower requirements.
Lastly, prior to processing any ore in the new mill, 300 feet of overburden had to be removed to reach the uranium deposits in the open-pit mine. This stripping required removal of more than 22 million cubic feet of earth.
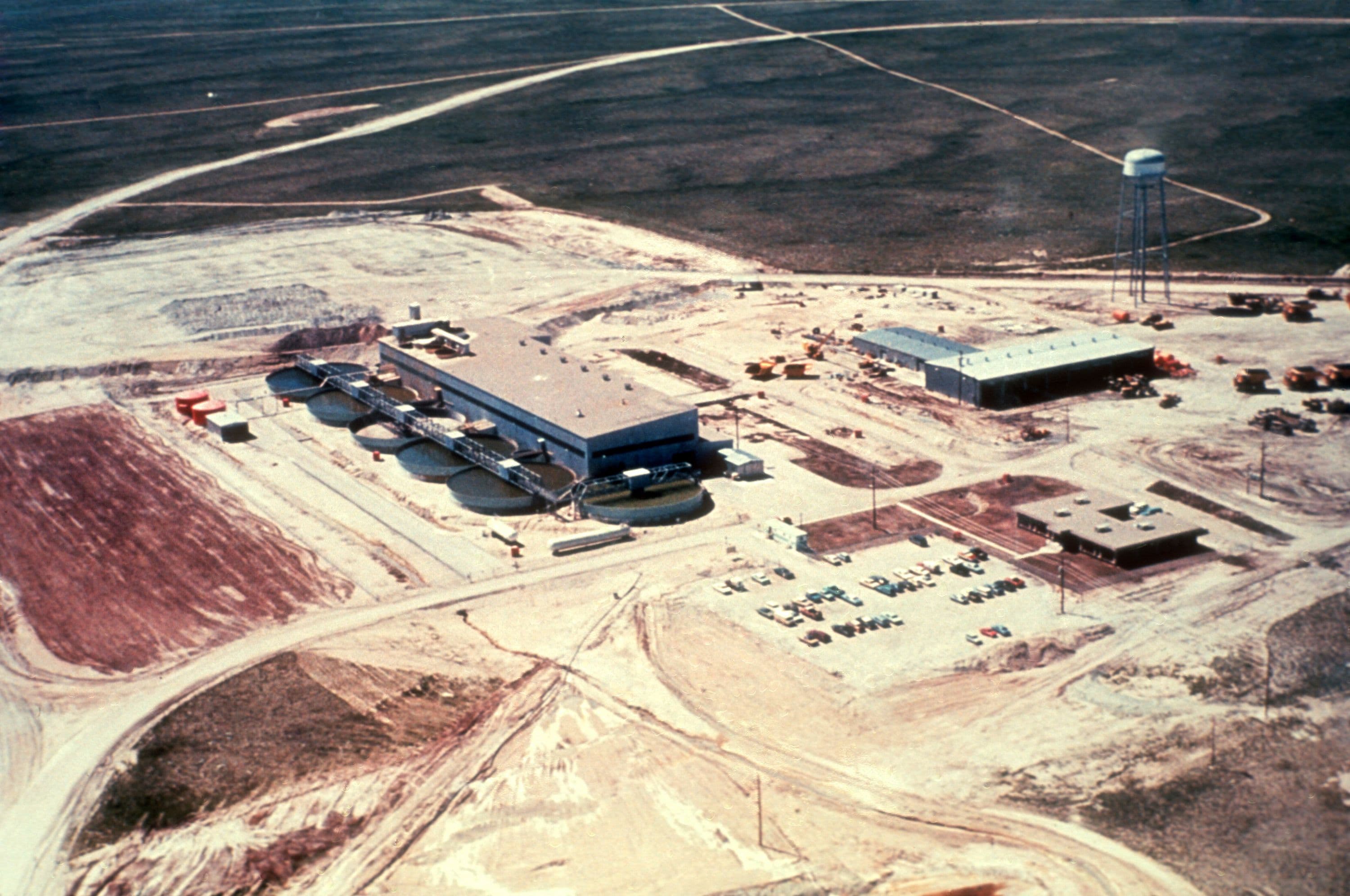
Fluor's Solution
At Shirley Basin, we introduced the industry innovation of using semi-autogenous grinding in a uranium plant. Semi-autogenous grinding eliminates the need for crushing. This achieves in one step a size reduction from run of mine ore, top size typically 600mm, to the twenty-eight mesh, roughly ½-1 mm.
Semi-autogenous grinding allows the plant to handle a large variation in feed size and moisture content, to alleviate problems of sticky frozen ore in the winter and minimize the fine ore particulate and material handling storage, to significantly reduce operator exposure to such safety hazards as fine dust and radon gas.
The severity of the Wyoming climate required a minimum of operator exposure. Construction crews completed the main warehouse early in the project to house much of the shop, materials and back-up equipment. Our engineers developed a schedule that assured completion of most of the external work on the processing mill before the winter weather could hinder construction.
The 1,800 TPD acid leach plant with ion exchange was housed in one large process building surrounded by six counter-current thickener tanks.
Due to the inclement winter weather, all the process equipment was centrally housed. To reduce operator exposure to the harsh winter conditions, all maintenance was carried out inside the main building, with large drive-through aisles designed for accessibility.
Inside the process building were ion exchange tanks easily accessible for maintenance by a mobile crane, offering the client cost savings by eliminating expensive structures for overhead permanent building cranes. In addition, the automated central control room provided a panoramic view of the whole plant and allowed a single operator to load/unload the ion exchange units remotely and minimize staff requirements.
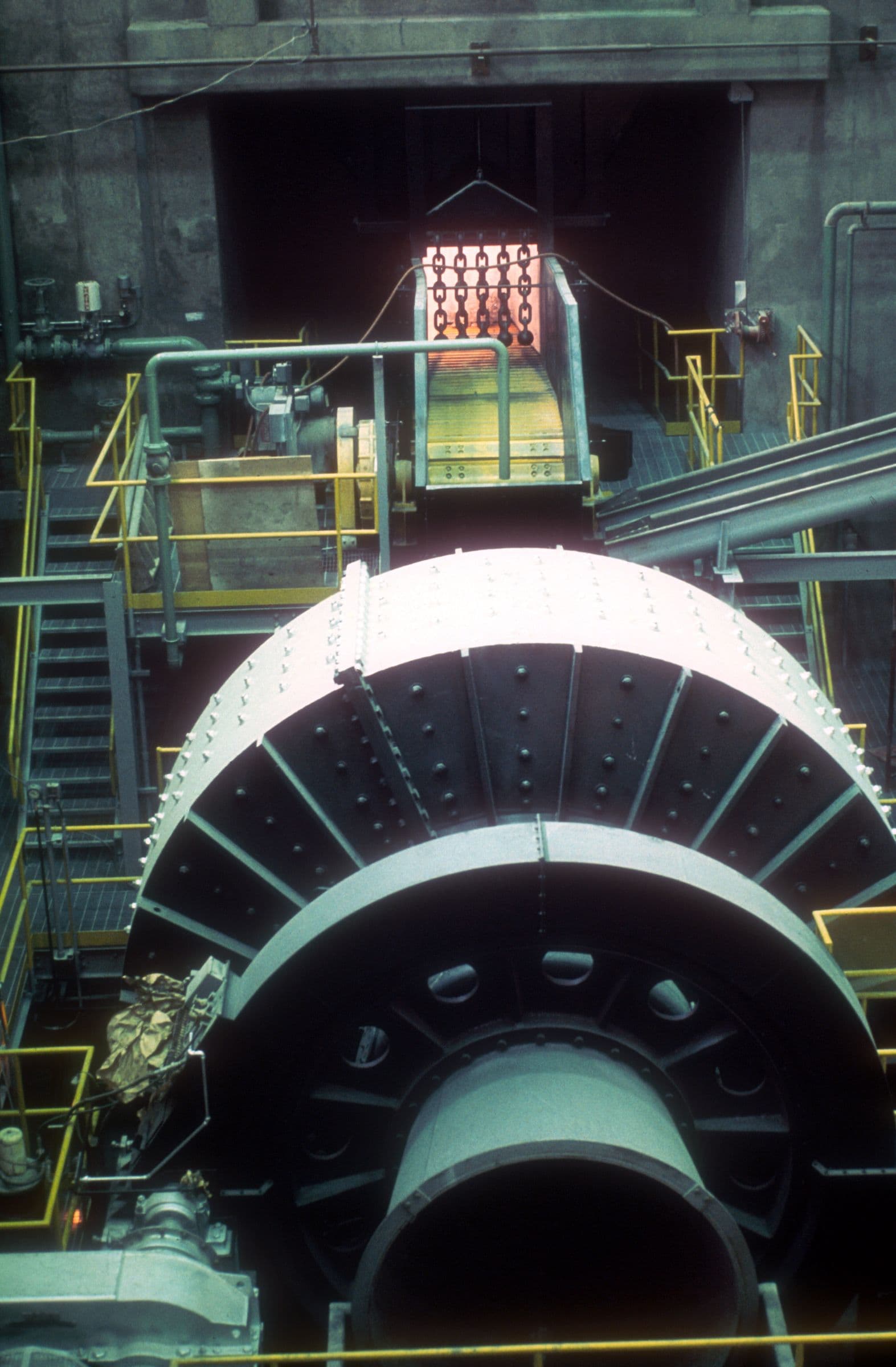
Conclusion
The new plant was the most advanced mill of its kind at the time. The compact design, placing most of the processing units within one area, incorporated many features used for the first time in the uranium processing industry.
The yellowcake shipped in 50-gallon drums to the customer, where it was further processed to form the fuel for nuclear reactors.
Plans called for the Shirley Basin mill to produce 2.25 million pounds of uranium oxide annually, a formidable step to meet the demands for uranium as a nuclear fuel.
The Shirley Basin uranium mill became operational in 1969.
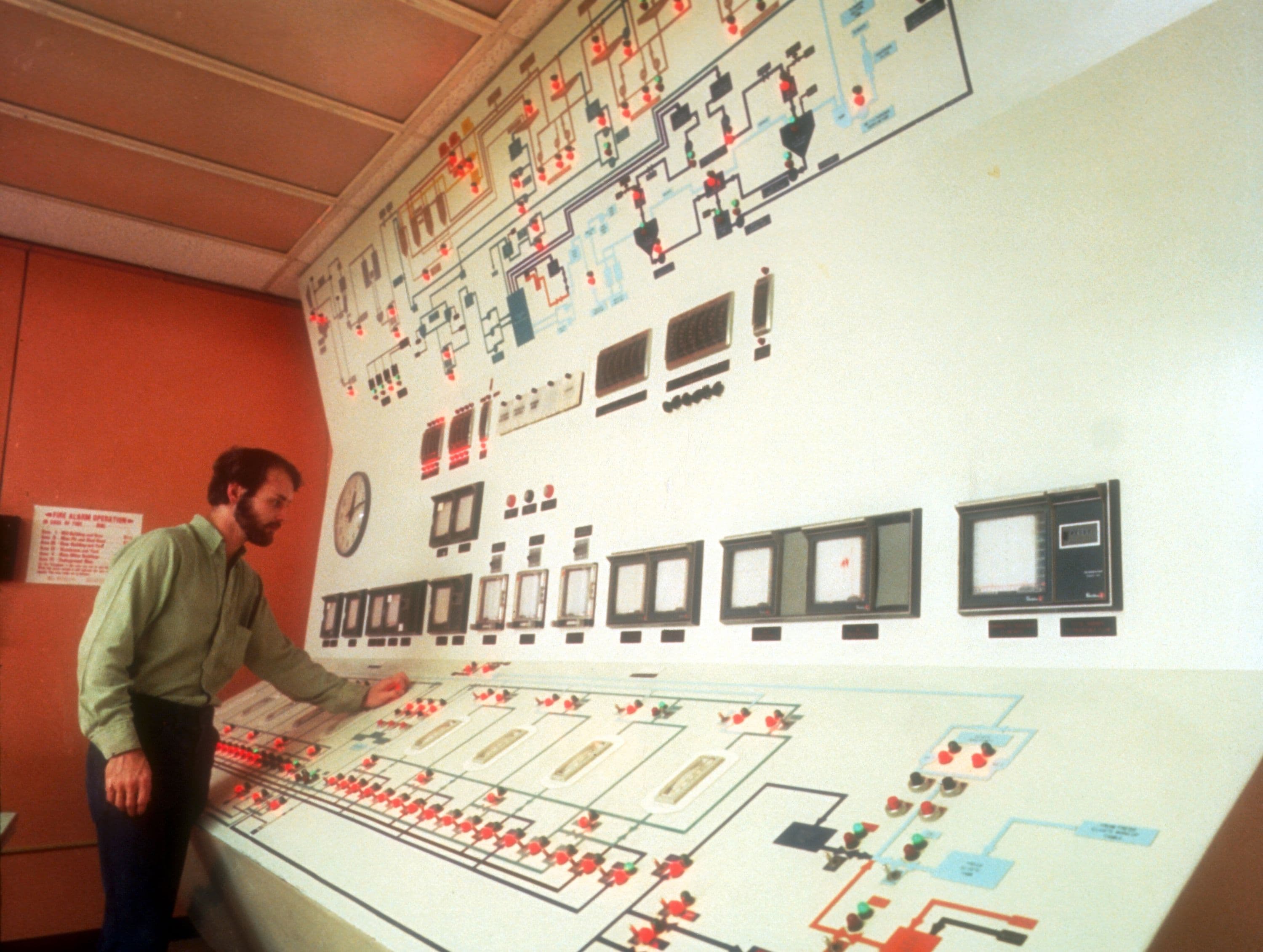