&w=3840&q=75)
L-Bar Uranium Mine & Mill Complex
Client: Sohio Petroleum Co and Reserve Oil & Mineral Corp
Location: Albuquerque, NM, U.S.
Business Segment: Urban Solutions
Industry: Mining & Metals

Executive Summary
Sohio and Reserve selected Fluor because of our extensive experience in second generation uranium processing mills including; Rabbit Lake, Saskatchewan; Shirley Basin, Wyoming; and Highland, Wyoming.
We performed the early feasibility studies and ultimately took overall responsibility for engineering, procurement and construction of the L-Bar underground mine, laboratory and mill complex, which includes semi-autogenous grinding, acid leaching and counter-current washing.
L-Bar uses a second-generation process more efficient and economical than the earlier 1950s technology. The second-generation process utilizes an eight-step processing sequence, which involves acid leaching, clarification, solvent extraction and precipitation resulting in dry, crushed yellow cake.
Work began on the $25 million mine and processing mill in late 1973. It progressed through one of the worst winters in New Mexico's history, yet concluded on schedule. The L-Bar mine was designed to handle 1,500 tons per day of uranium bearing ore.
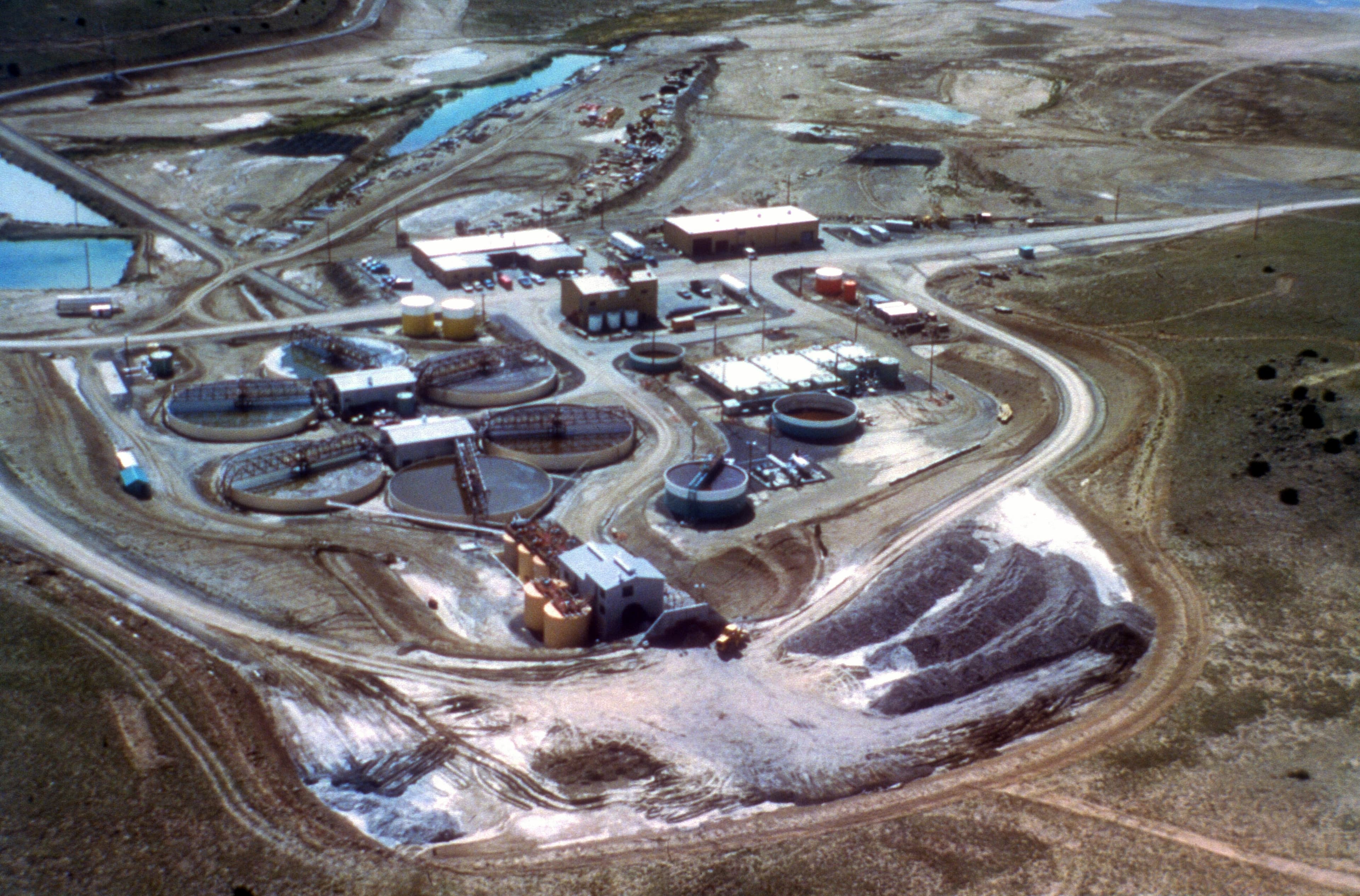
Client's Challenge
The L-Bar Ranch covers 120,000 acres on the rolling high mesa about 45 miles west of Albuquerque. In early studies of the L-Bar Ranch prospects, analysis of the exploratory drilling results indicated the perimeters of three sizeable ore bodies. Although geologists located the ore and recognized its value, the question of how and where to process it remained.
With each 0.1% uranium ore, for example, each ton contained 1,998 pounds of waste rock. It was determined to build a local mill to avoid steep transportation costs of the 99.9% waste material.
However, water in the semi-arid mesa was a concern. Sohio test wells found an aquifer that could supply the 720,000 gallons per day needed to operate the mill.
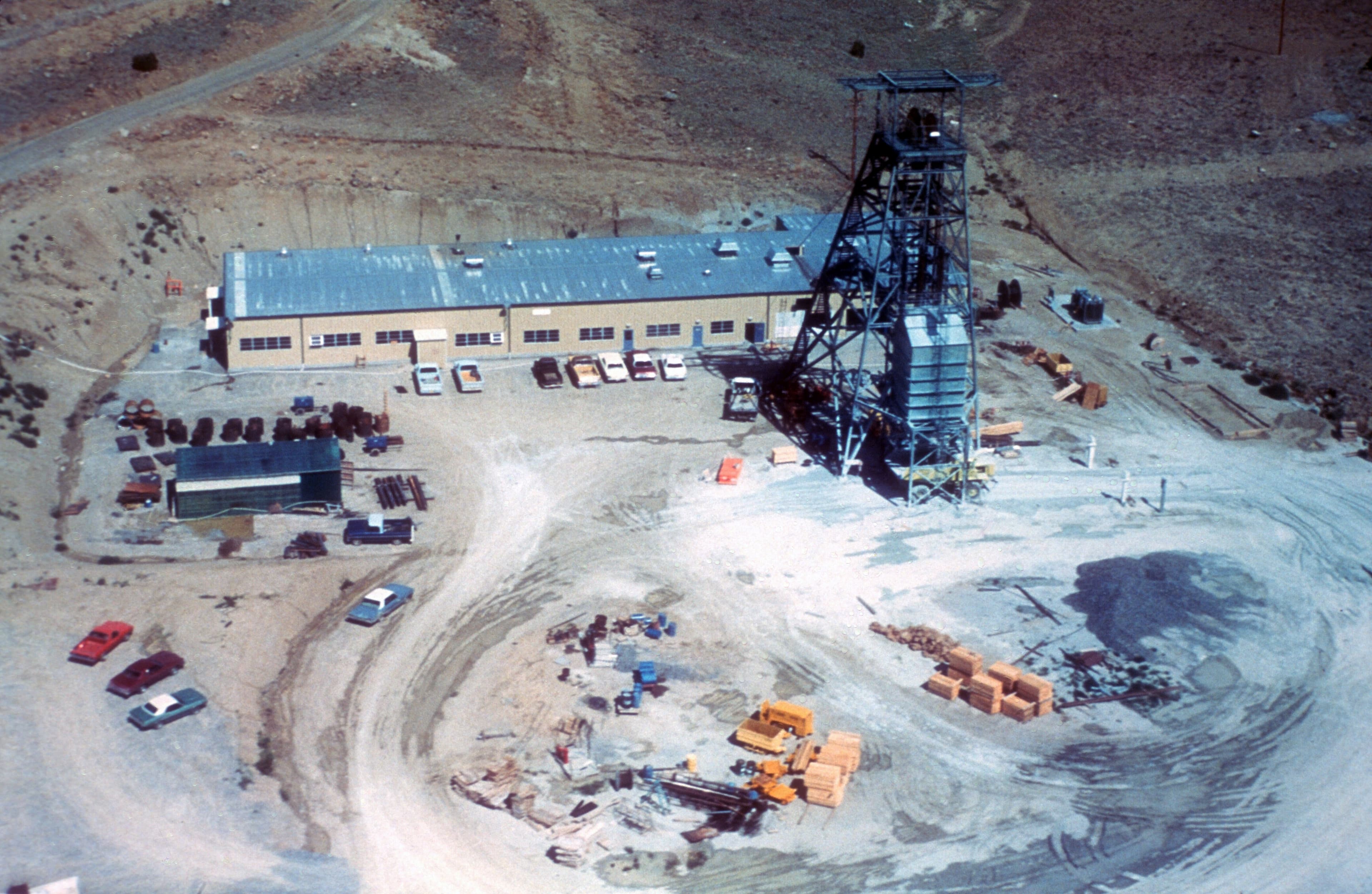
Plant operational efficiency was also designed into the yellow cake controls. Only four personnel plus a shift supervisor are needed to run this semi-automatic plant.
In addition to financial justification, the client was stringent to minimize any environmental disturbance to the mesa. We employed advanced environmental techniques and designed the plant to have zero water emissions and the absolute minimum air emission. For example, in the acid leaching area, the tanks vent through wet scrubbers that capture 99.9% of the sulfur dioxide fumes. Considerable measures to protect the environment were taken. The entire drainage from the surrounding plant area, including the mine, was channeled to the tailings dam.
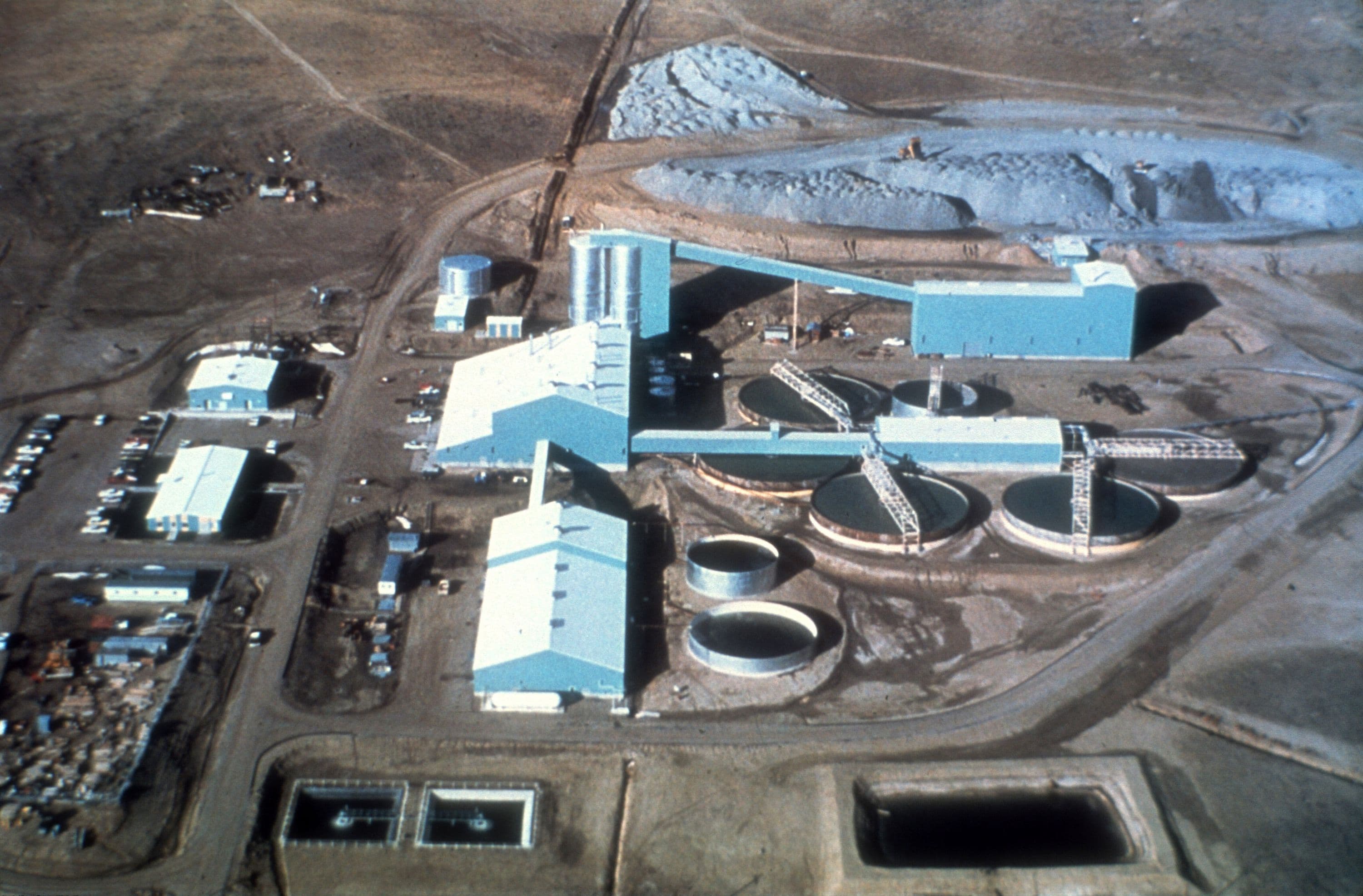
Fluor's Solution
We performed the early feasibility studies for the preliminary mine development including the shaft sinking and ultimately took overall responsibility for engineering, procurement and construction of the L-Bar underground mine, laboratory and mill complex. We were responsible for the design and installation of the mine surface facilities and the underground permanent facilities for the L-Bar mine, including the head frame, the hoist house, offices and the change rooms.
Powered by a 250-horsepower mill, semi-autogenous grinding is used in this process. The uranium bearing ore is crushed and ground and then after cycloning, is pumped into two slurry storage tanks, then into the mechanically agitated leach tanks. All of these tanks are insulated to assist in temperature control. Leaching is followed by solid-liquid separation, which takes place in six counter-current thickeners. The process continues to the solvent extraction units and yellow cake drier and drum filling.
The Sohio counter-current washing thickener circuit has two pump stations, versus the typical central design concept. A tunnel for pipework, constructed from corrugated steel conduit with a concrete-filled base walkway, connects the two pump houses. The thickener tunnels use a similar design, which is considerably more economical than the conventional concrete arch and allows for easy maintenance.
&w=3840&q=75)
Another design savings is the plant automation. With three control consoles, one for the grinding, one for the counter-current washing and one for the solvent extraction and yellow cake handling combined, the Sohio plant requires only four operators.
Our stringent focus on construction safety efforts netted 56 awards for the zero lost-time accidents performance.
The large endemic rattlesnake population was unique to this project and required snakebite kits in all the site trucks. No snakebites were recorded.
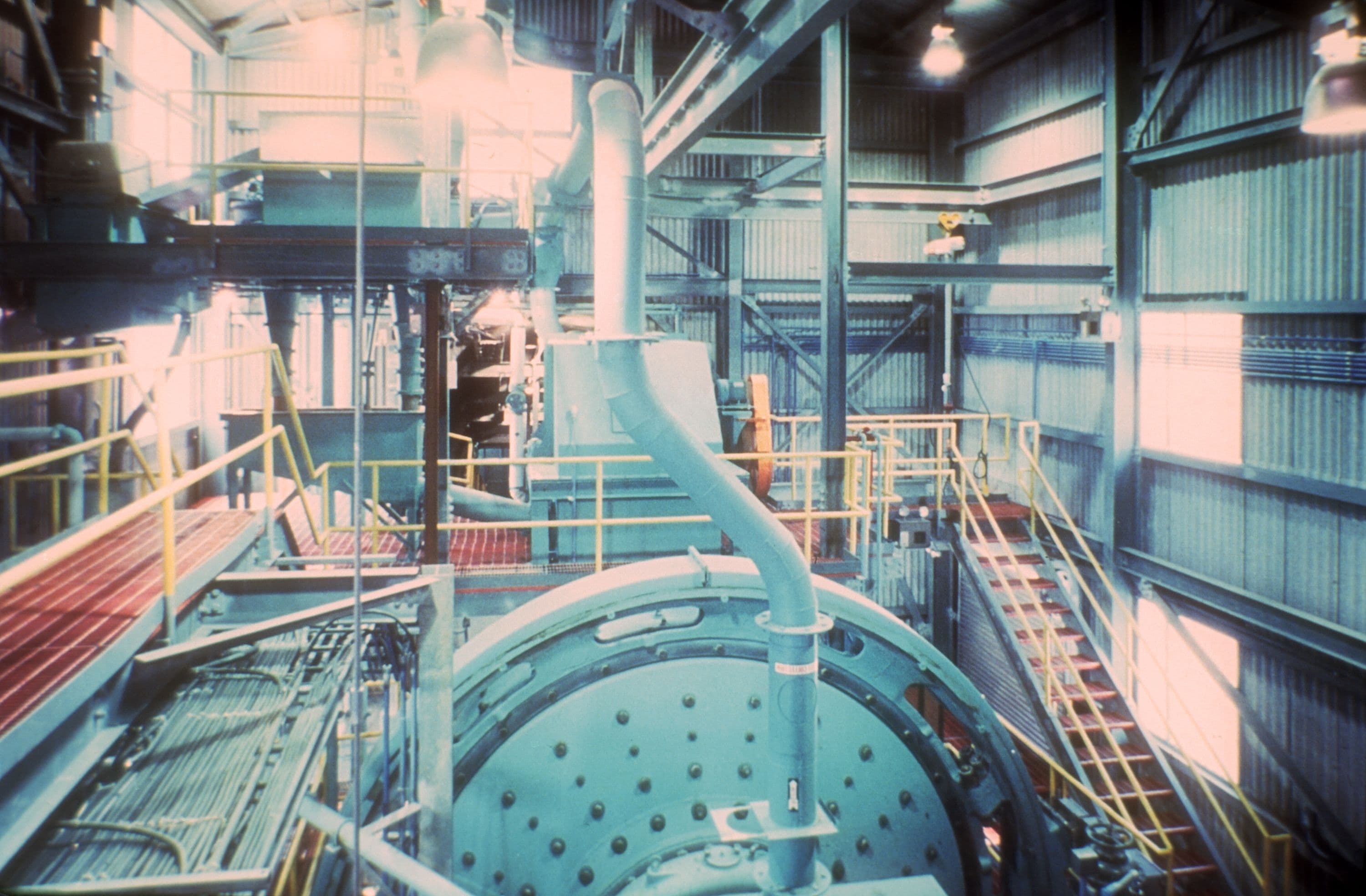
Conclusion
Each day, the miners broke approximately 1,000 tons of mineral from the bedrock and hauled it to the surface of the J.J No.1 Mine at the L-Bar Ranch.
In full operation, the uranium mill produces over 6,000 pounds of yellow cake daily.
The L-Bar uranium mine and mill complex contributes fuel to provide power to the U.S. energy grid and reduces the country's reliance on foreign oil supply.
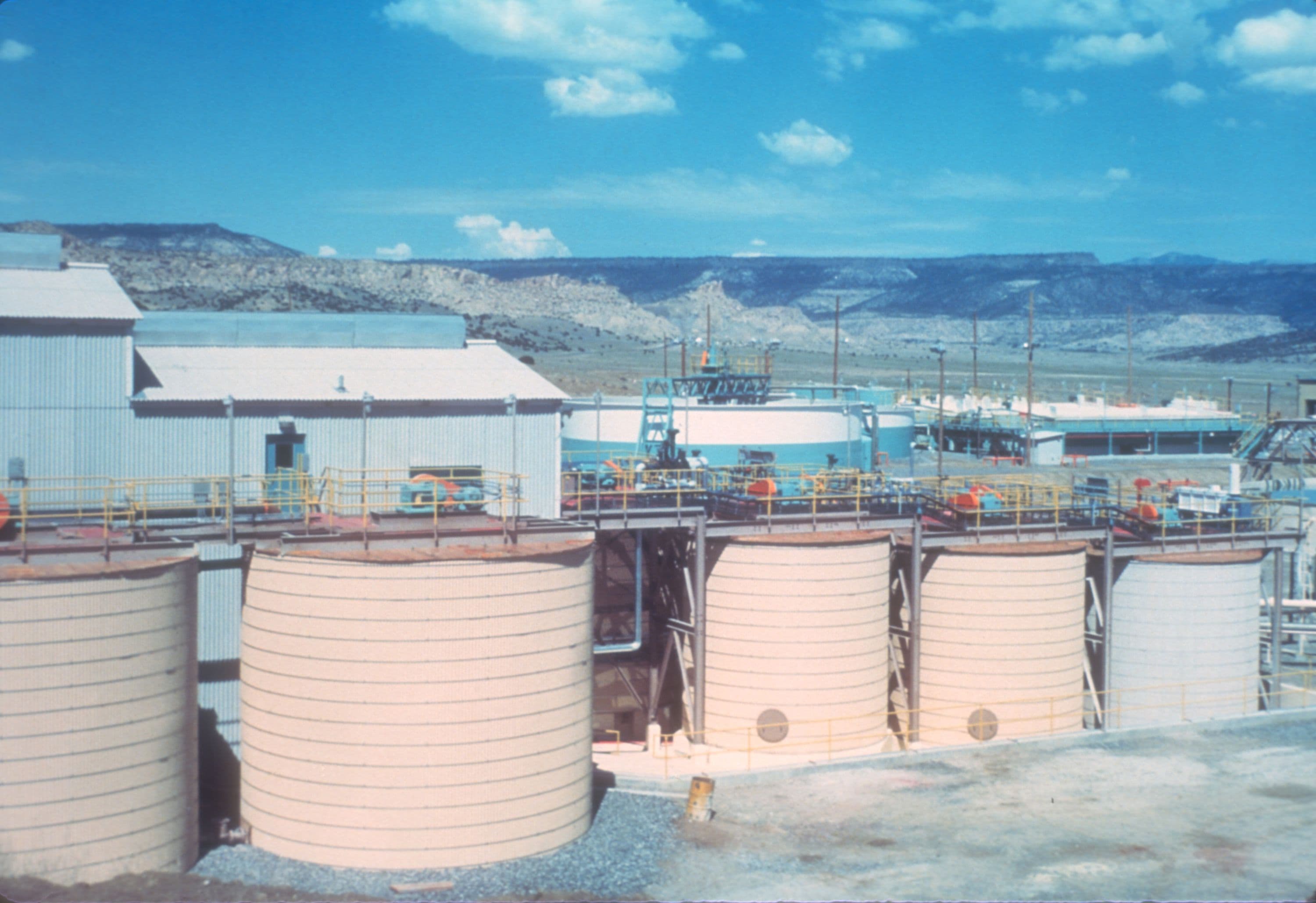