&w=3840&q=75)
Mill Creek Units 1 & 2 Retrofitting Services
Client: Louisville Gas and Electric Company
Location: Kosmosdale, KY, U.S.
Business Segment: Energy Solutions
Industry: Infrastructure

Executive Summary
Fluor was selected by Louisville Gas and Electric Company to provide retrofitting services for Mill Creek Units 1 & 2 in Kosmosdale, Kentucky.
We were responsible for engineering and procurement, including the development of specifications, bidding, analysis of proposals, purchase recommendation, placement of orders, expediting and shop inspection for all project equipment, systems and materials.
&w=3840&q=75)
Client's Challenge
Louisville Gas and Electric Company wanted to retrofit dual reagent capability lime or limestone flue gas desulfurization (FGD) systems for two high-sulfur, coal-fired units, each of which was 330 MW.
The addition included absorbers, reaction tanks and large recycle pumps, conventional thickeners and sludge fixation using vacuum filters, fly ash mixing and lime addition. Design included provisions for water retention and reuse.
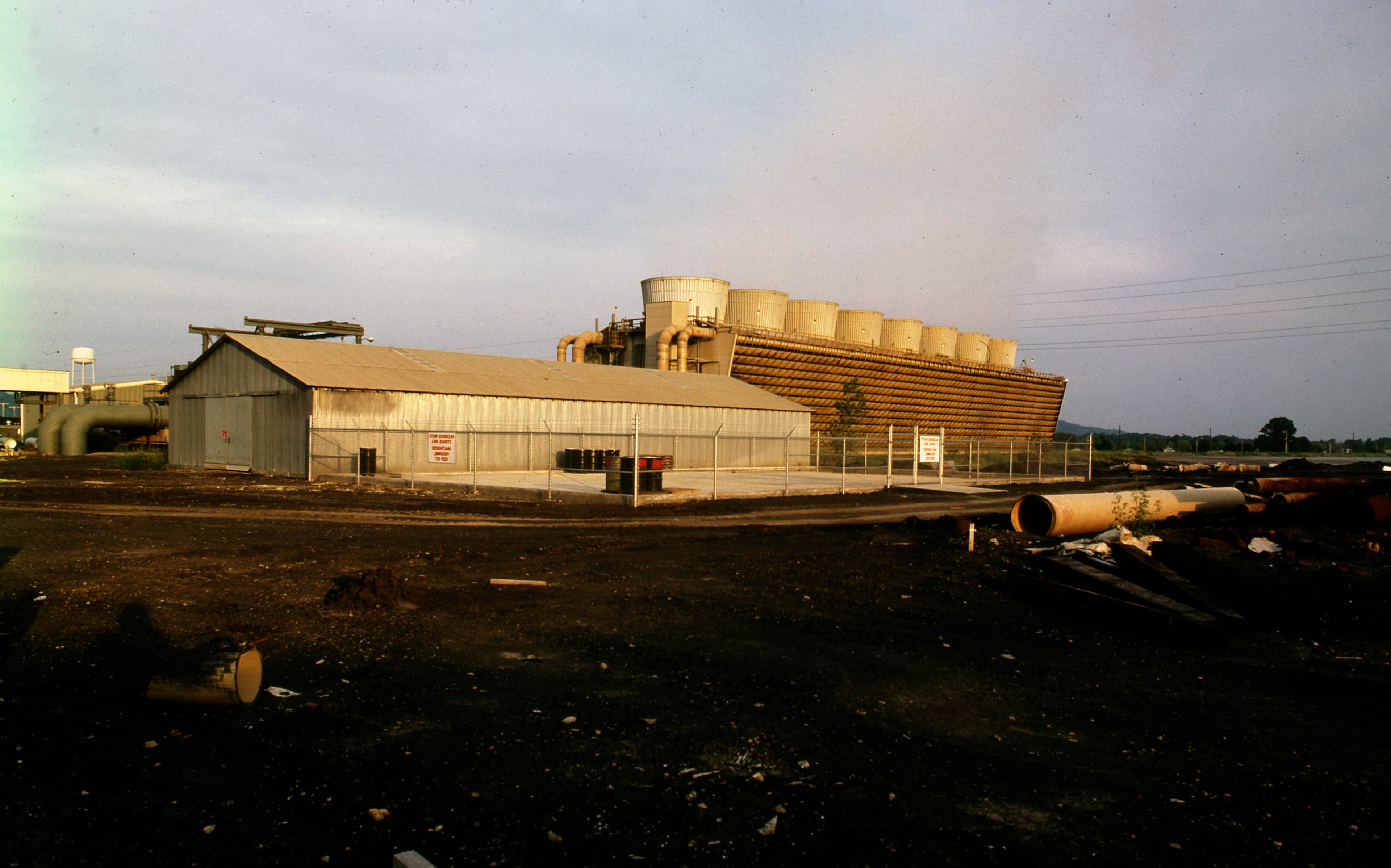
Fluor's Solution
We provided equipment arrangements and designed all foundations and the unique service building, which was critical to accommodate all the equipment in the confines of the available space. We also designed and procured the reagent storage and supply system and piping systems for the sludge circulating between the boiler heat exchanger and the flue gas reheater, as well as ash supplies to the sludge fixation plant, for the glycol and steam supply to the reheater sootblowers.
Electrical substations and motor control centers were added to supply power to the new loads. A full-capacity distributed computer control system was provided to allow monitoring and control of the FGD systems by the boiler operators and to minimize operator requirements while ensuring redundancy for outage avoidance. We designed automated start-up/shutdown logic and all control circuits and control wiring.
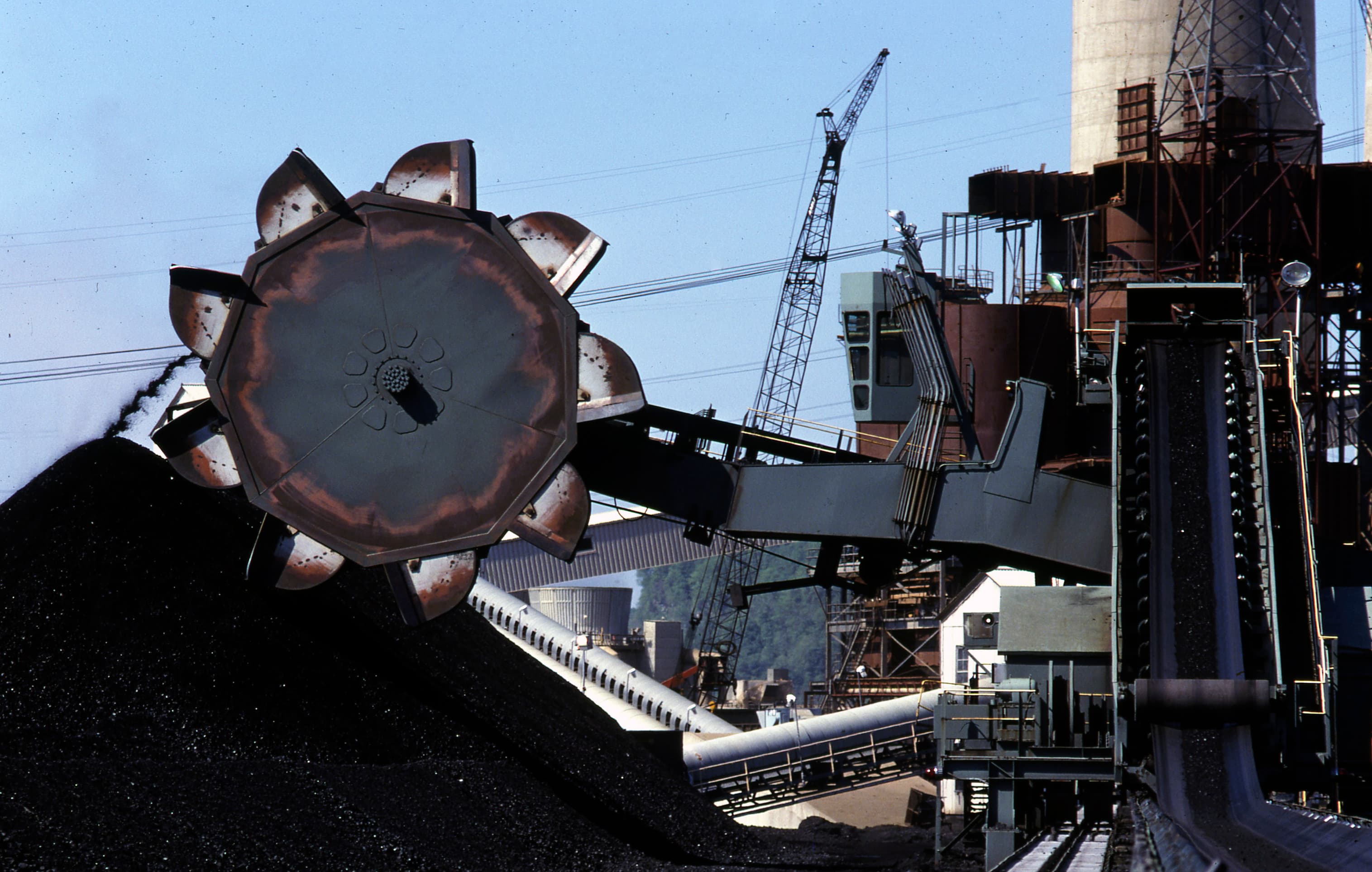
The owner, Louisville Gas and Electric Company, was the constructor of this project. We tailored the engineering to constructability. The small work area required special staging and sequencing of work to accomplish the erection tasks. A plan was developed during the engineering phase jointly with the construction engineers. Design of the ductwork and service building required particular skill and imagination. Delivery of equipment and materials, laydown space and sequence of erection were factored into the overall design of the FGD system. Tight work space prevented modularization and shipment of large shop assemblies to the field. Construction time was 18 months.
We designed the system with ease of operation and maintenance in mind. Large pumps and motors were designed to be removed by overhead crane. Overhead trolley beams were provided for other equipment. Obstruction-free aisles were reserved for fork lift truck access.
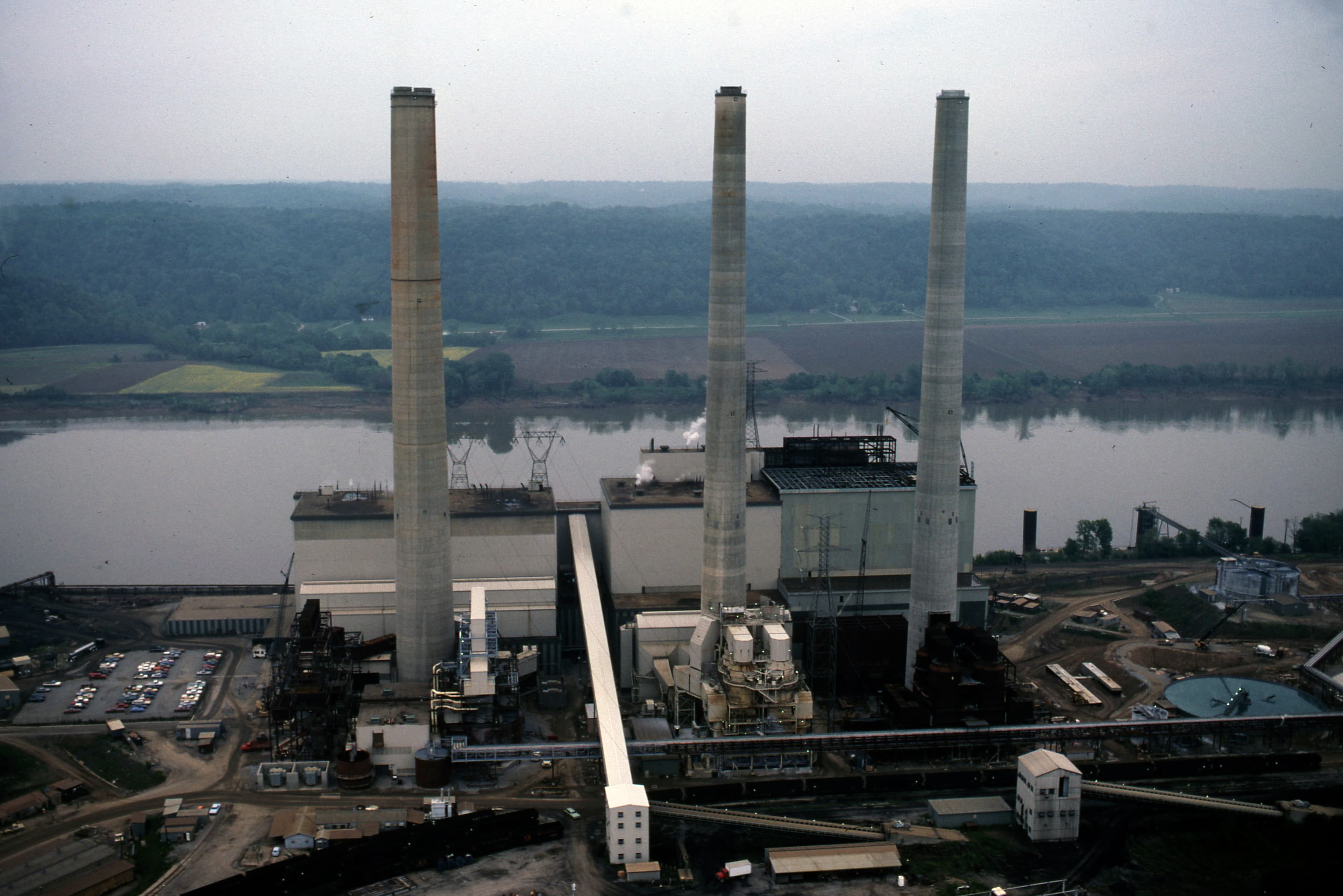
Conclusion
We provided engineering and procurement services for the retrofitting of Mill Creek Units 1 & 2. Commercial operation for the two units began in December 1982.
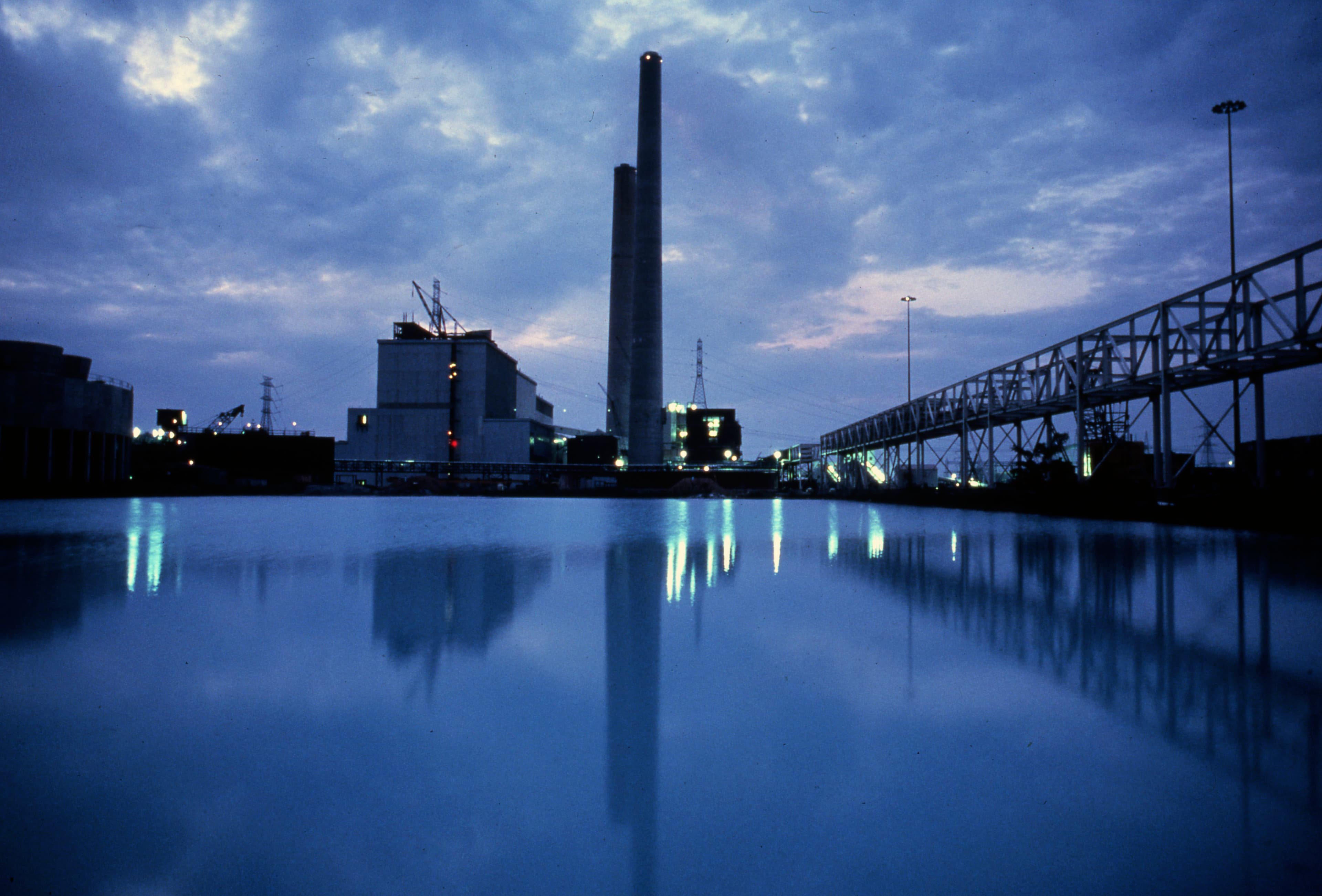