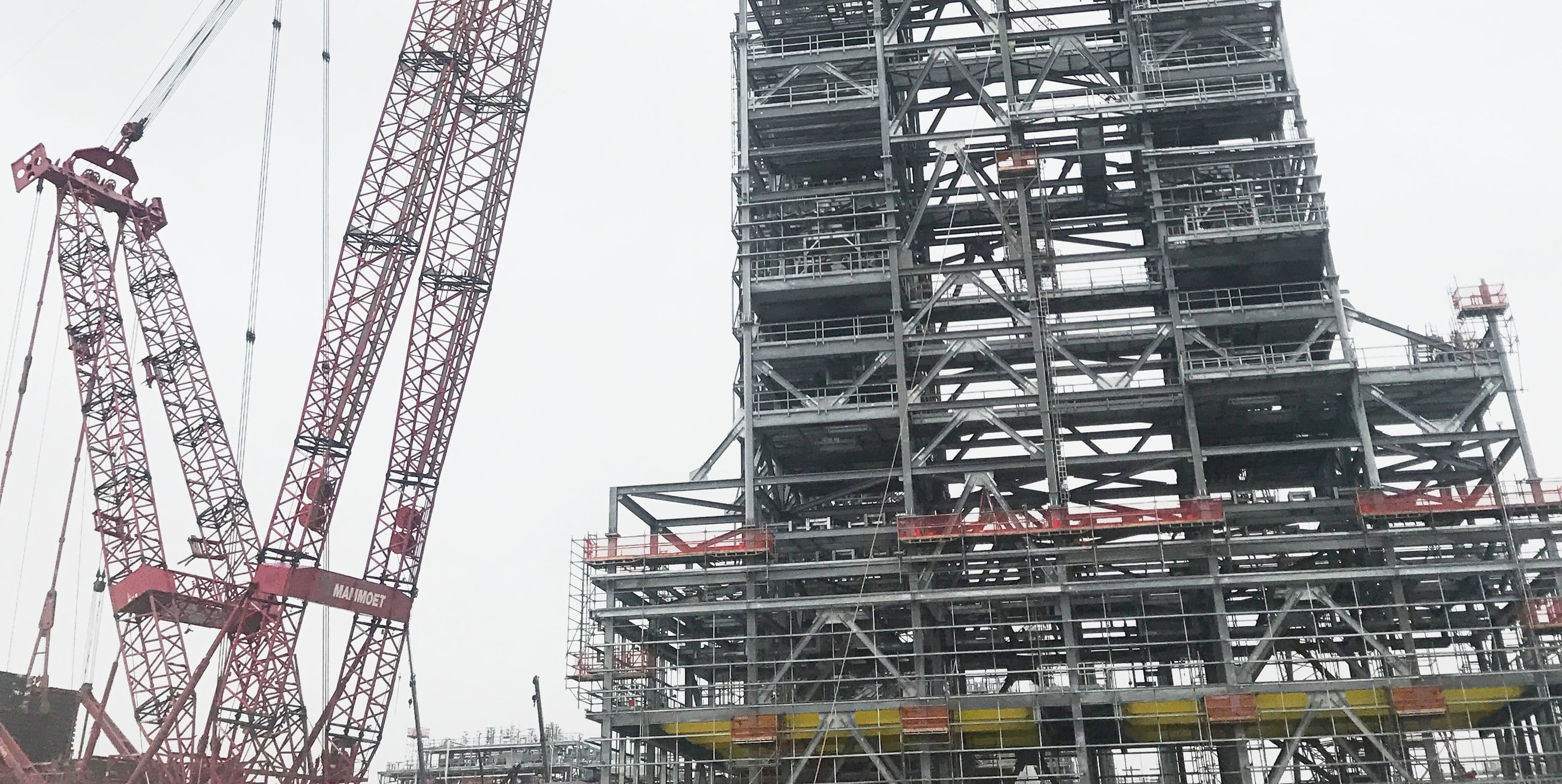
Dow Gulfstream Poly-6 Project
Client: The Dow Chemical Company
Location: Freeport, TX, U.S.
Business Segment: Energy Solutions
Industry: Chemicals

Executive Summary
Fluor provided mechanical construction services for The Dow Chemical Company's Gulfstream Poly-6 project, a new ethylene derivative facility in Freeport, Texas. The facility will manufacture polyolefin elastomers for applications in packaging, transportation, infrastructure and consumer markets.
Our mechanical construction scope included setting precast and steel structures, piping, equipment, painting and insulation for the unit.
Client's Challenge
This was the latest project in Dow's Freeport complex, the largest integrated chemical manufacturing complex in the Western hemisphere.
The new polymers unit was designed for the production of high melt index polymers such as AFFINITY™ GA polyolefin elastomers for hot melt adhesives, along with broad capability to produce conventional ENGAGE™ polyolefin elastomers and AFFINITY™ polyolefin plastomers.
Fluor's Solution
Fluor completed mechanical construction work on Dow's ethylene production facility in Freeport safely and several weeks ahead of schedule. This follow-on capital investment leveraged our local resources, best practices and expertise.
More than 500 craft professionals performed the mechanical construction, with Dow and Fluor managing the project together as an integrated project team.
Over a two-week period in March 2018, the Dow and Fluor team safely erected two structures, both over 280 feet tall, making up portions of the facility. The two structures total almost 5,000 tons of steel, the equivalent of 3,000 average-sized cars, and were initially assembled into 12 different components at the site.
This pre-assembly phase reduced the schedule by enabling the components to be assembled simultaneously. In addition, it improved safety by reducing the level of elevated work and minimizing site congestion. The components were transported to their final location by self-propelled module transporters, and through 12 lifts, connected together like building blocks.
The project team also applied several best-practice construction approaches that were new to the region and industry. To control costs, we only used lattice boom cranes and reconfigured them as needed, rather than adding costly mobile cranes to the project. We also installed a large cooling fan in place, rather than pre-building the unit on the ground. This approach eliminated the need for costly specialized rigging and eliminated unnecessary congestion on the site.
The project was executed to the highest quality standards. The welding team completed work with an industry-leading weld reject rate of 0.52%, with all craft maintaining best-in-class productivity standards.
The Dow and Fluor project team simultaneously worked to give back to the community; for example, renovating a home for a deserving family in the Freeport area.
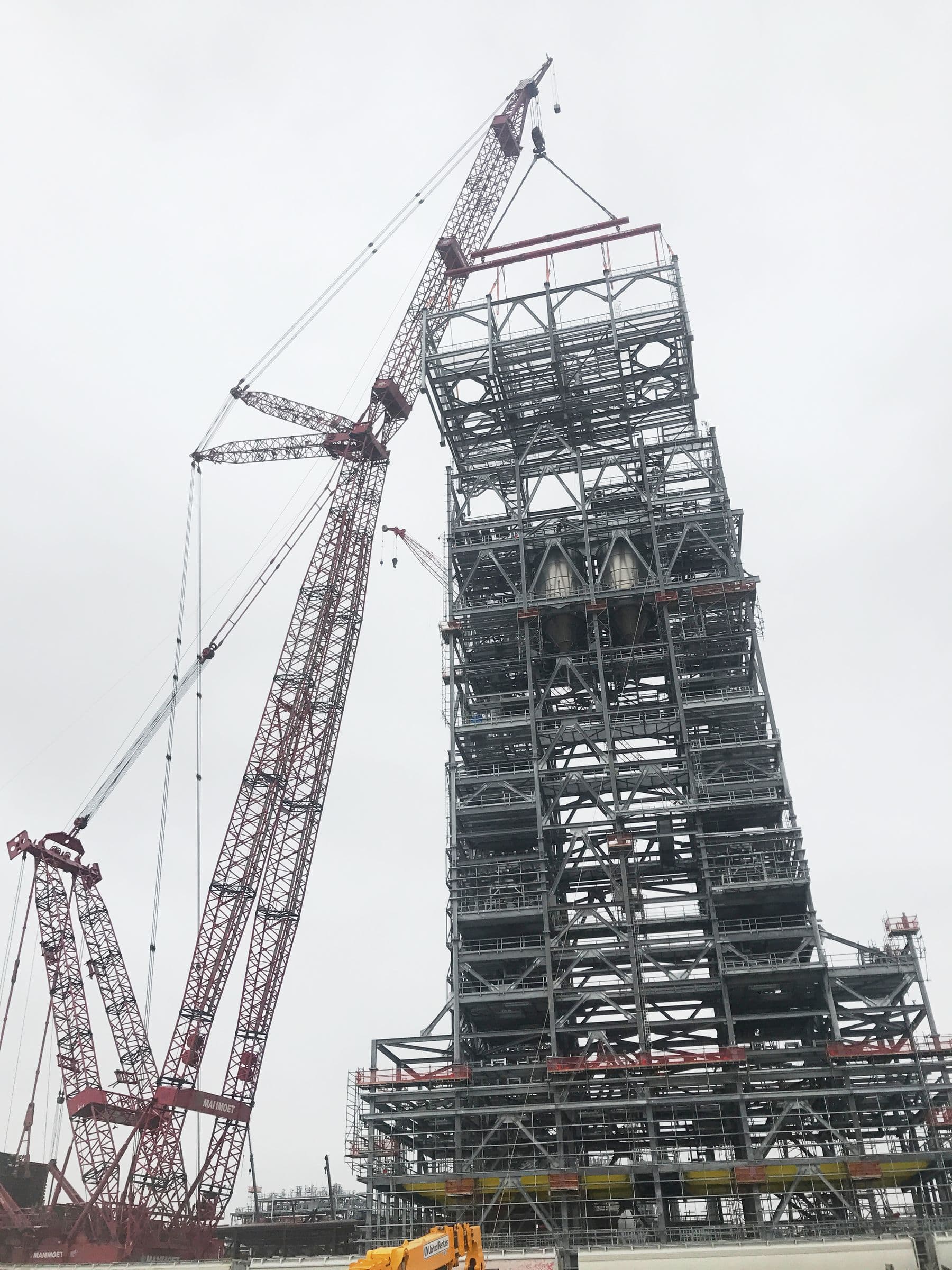
Conclusion
Fluor provided excellent mechanical construction services for Dow’s Gulfstream Poly-6 project, the latest in Dow’s Freeport complex. The project was named a finalist for Construction Project of the Year for the S&P Global Platts Global Energy Awards in 2019. It also received Fluor's HSE Three-Star Award.