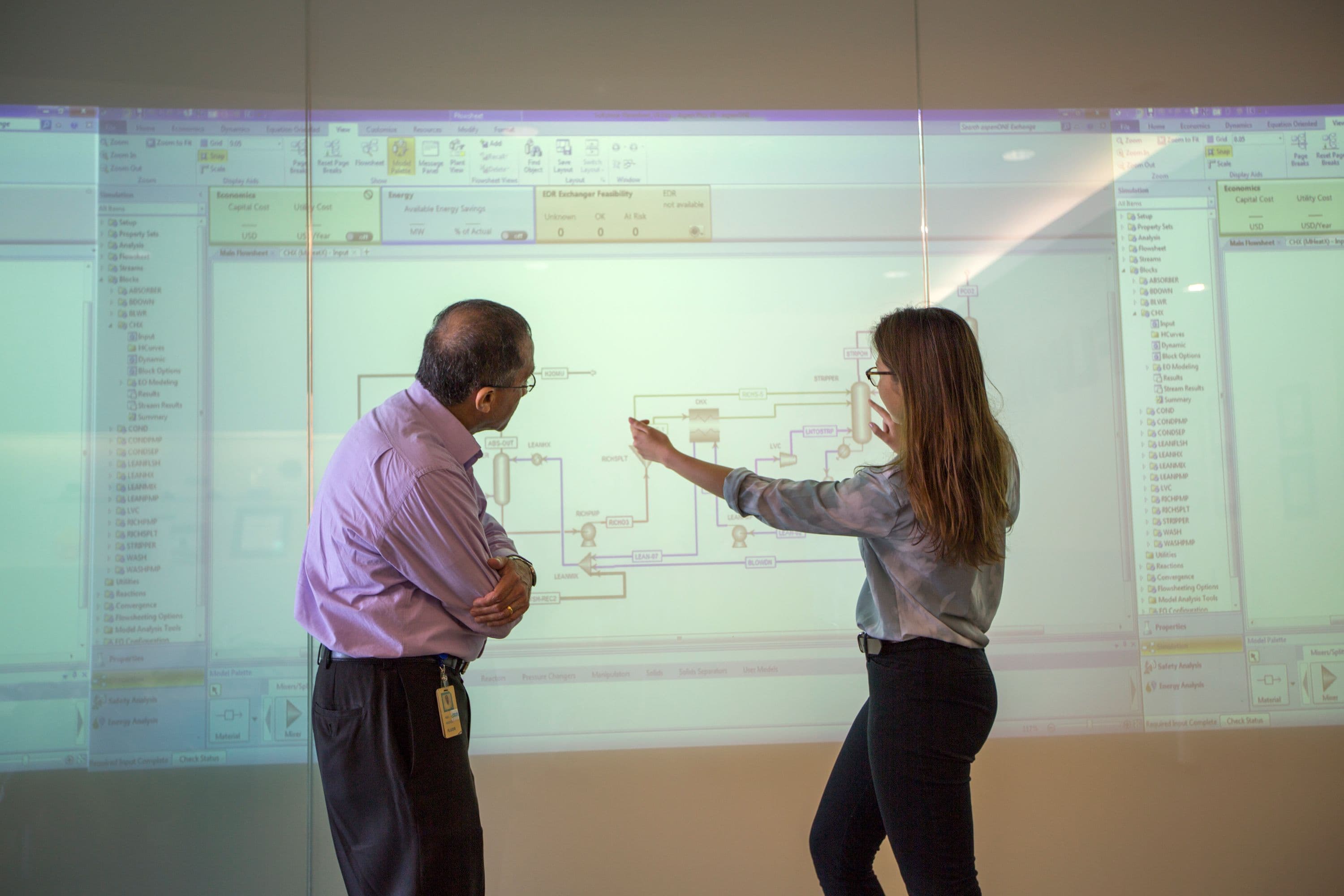
Fixed-Bed Reactor Scale-up Study

Executive Summary
Fluor was selected by a global chemical company to conduct a fixed-bed reactor scale-up study for the production of ethanol using basic hydrocarbon feedstocks. We were retained to assist with scale-up and design of the reactor, to develop kinetic models and to perform hydraulic investigations.
We utilized advanced process modeling to complete the scope of the study, which included kinetic model development and validation using laboratory data, investigation of catalyst properties relevant to process scale-up, assessment of viable commercial reactor configurations and design of the technical demonstration plant and commercial-scale reactors. The scope also included development of the heat integration and process control scheme.
Client's Challenge
The global chemical company developed a chemical process to produce ethanol with high selectivity. Together, we collaborated on the scale-up study, evaluating laboratory data to assess the decision to proceed with the capacity plant.
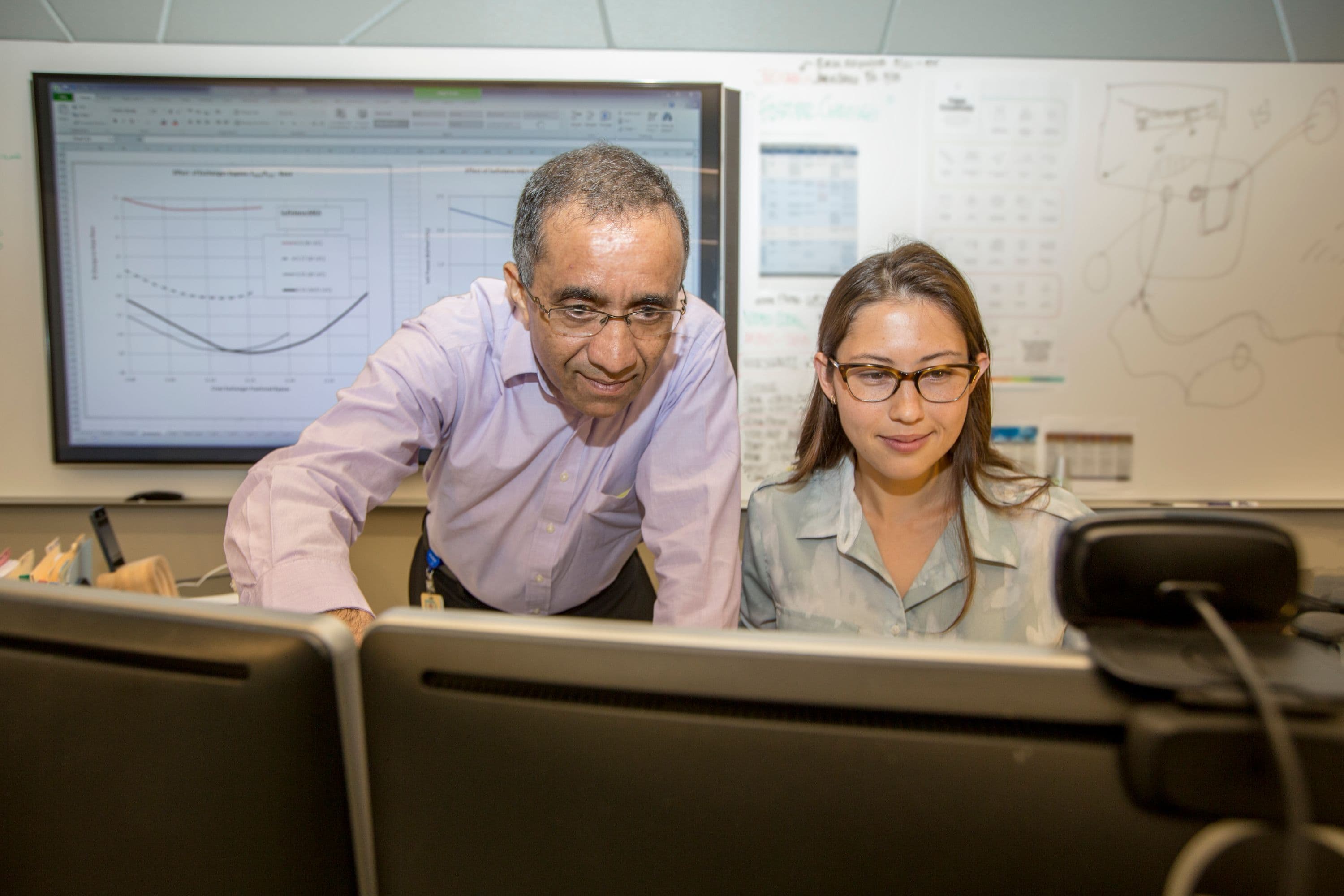
Fluor's Solution
We utilized advanced process modeling in developing kinetic models and designing the reactor.
Our contribution to the project was expertise in thermodynamic properties, optimizing kinetic models through the capabilities provided by the Aspen Plus™ process simulator, specifically, Data-Fit, and flowsheet development to control reactor performance over the life of the catalyst.
We worked with the company's research & development team to develop and validate a kinetic model using data generated from two types of laboratory-scale reactors. These efforts were aided by Aspen Plus capability such as flexible kinetic models and Data-Fit to regress laboratory data.
We investigated catalyst properties relevant to process scale-up, assessed viable commercial reactor configurations and developed heat integration and process control scheme. We subsequently performed a technology assessment for the entire plant.
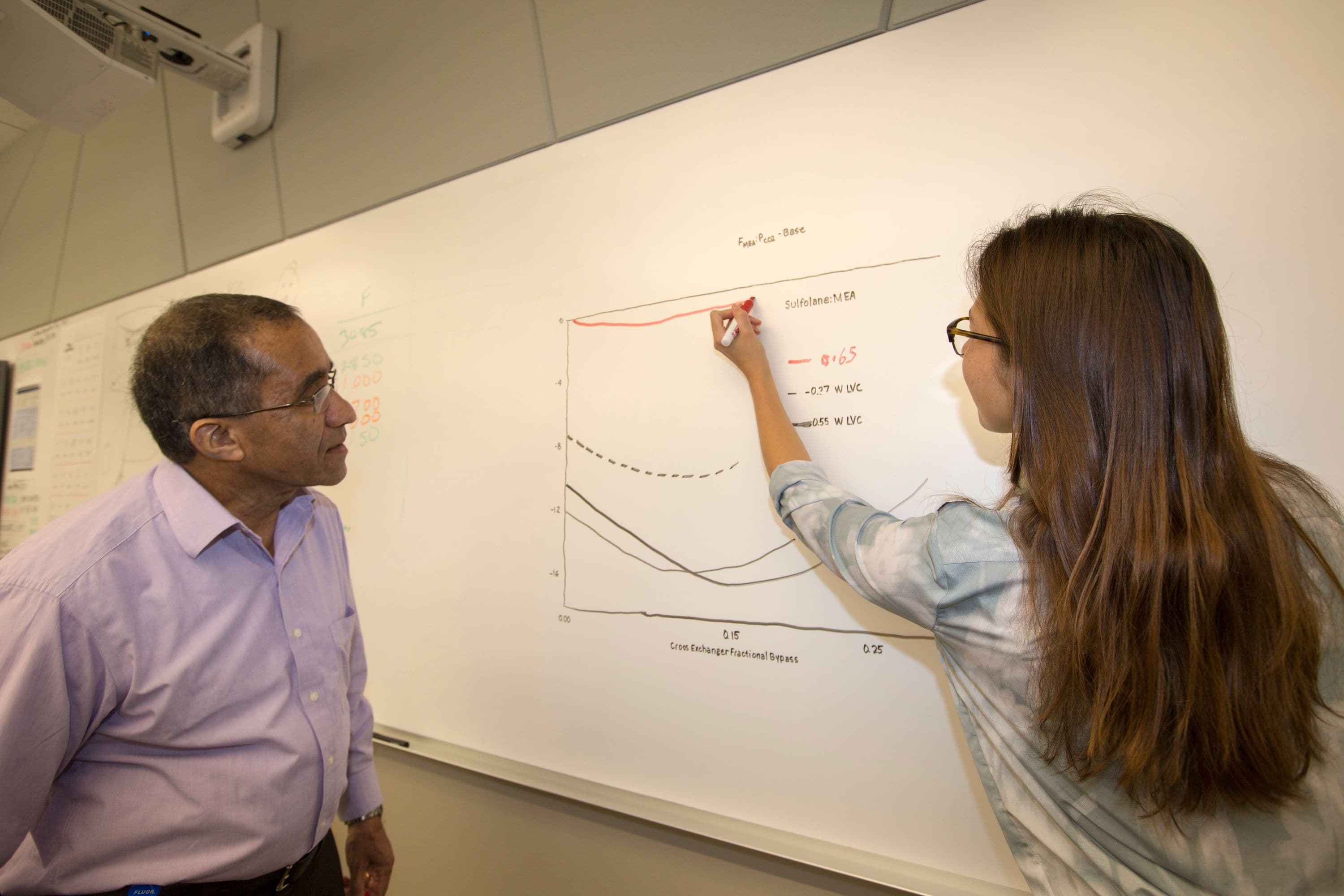
Conclusion
As a result of close collaboration, technical uncertainties were sufficiently mitigated to support the decision to proceed from a laboratory scale directly to designing a world-class capacity plant.
This study is an example of how our advanced process modeling capability assists clients in developing new technology through guidance on measuring and evaluating laboratory data and using these data to confidently implement validated process technology.
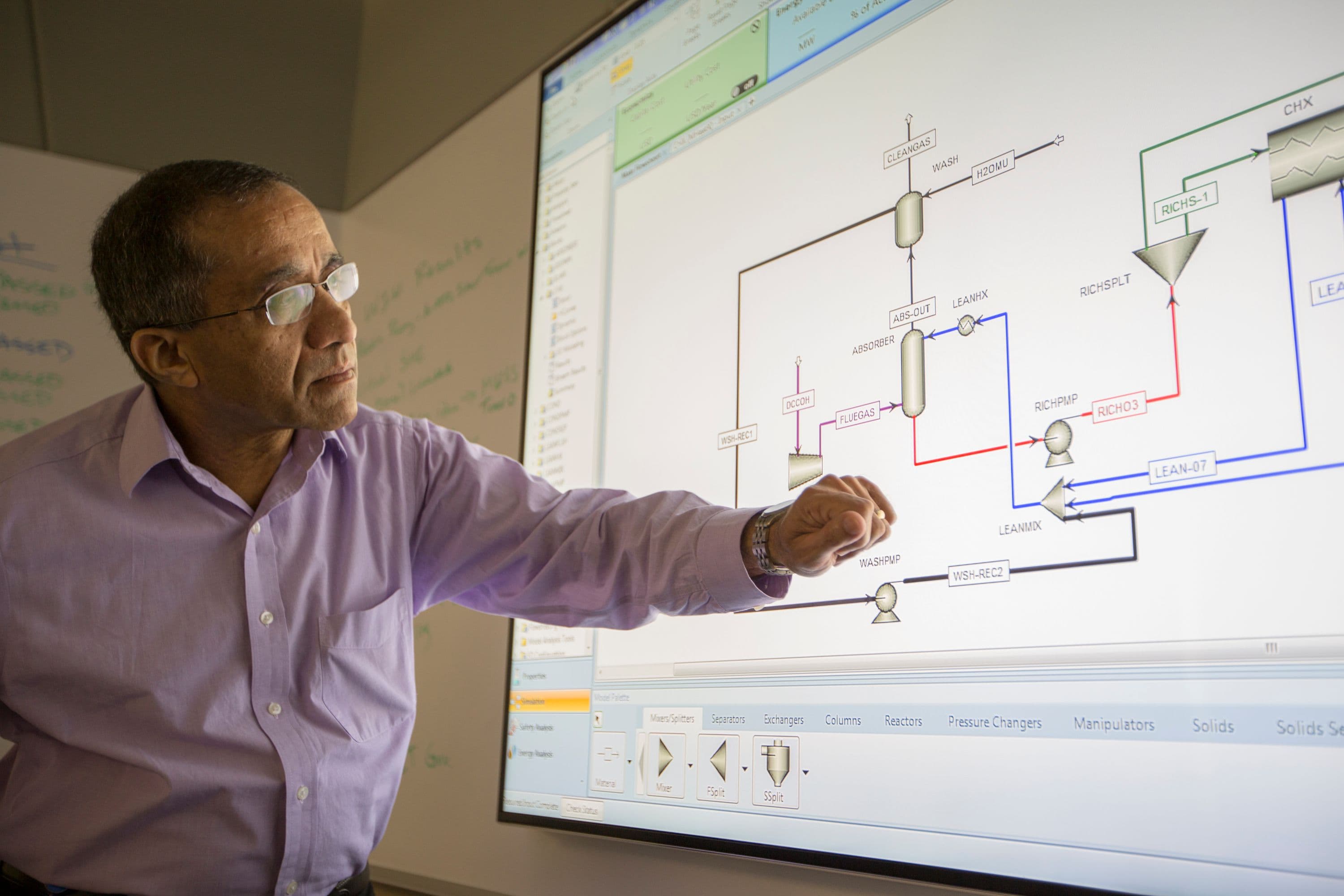