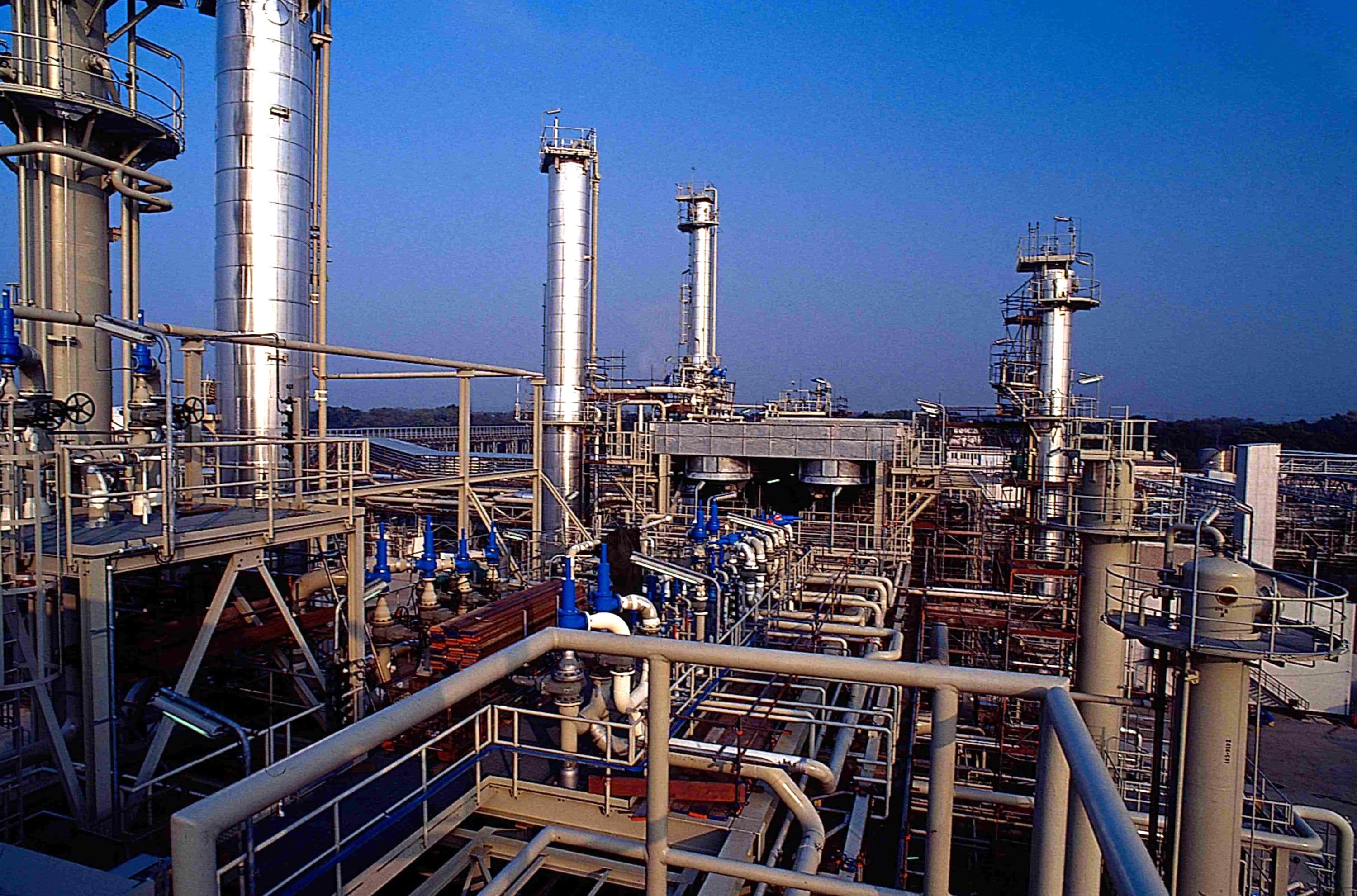
Česká rafinérská FCC Plant
Client: Česká rafinérská CRC
Location: Czech Republic
Business Segment: Energy Solutions
Industry: Fuels

Executive Summary
Fluor performed engineering, procurement, construction and project management for the Česká rafinérská FCC Plant addition on a lump sum contract. The FCC Plant comprised a new integrated resid conversion complex added to the existing Kralupy Refinery.
We completed the project two months ahead of the contractual schedule.
Client's Challenge
Česká rafinérská is the largest crude oil processing company and largest producer of oil products in the Czech Republic. The company operates refineries in Litvínov and Kralupy.
The company added a new FCC Plant to the existing refinery at Kralupy.
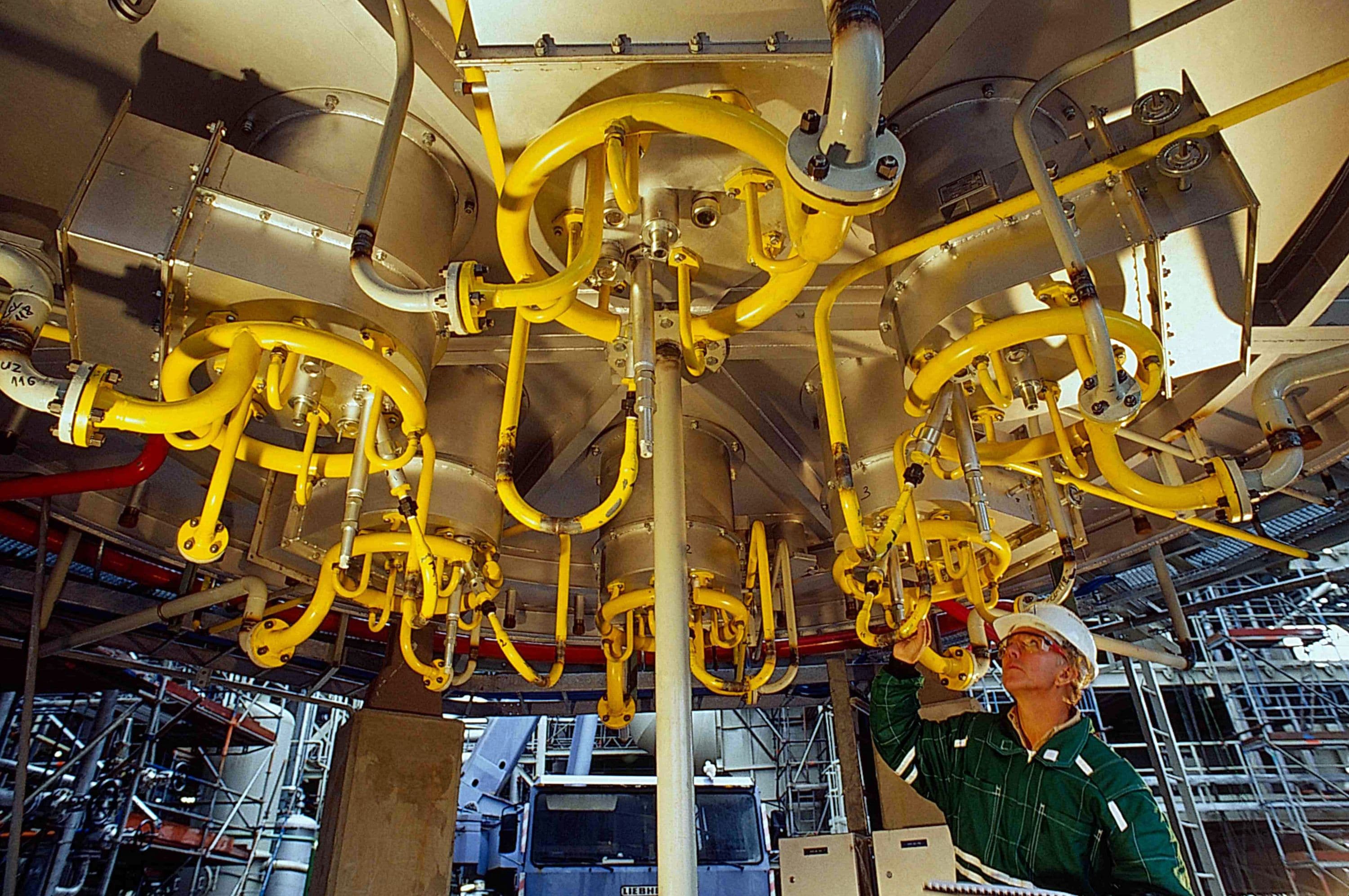
Fluor's Solution
We executed a lump-sum contract for engineering, procurement, construction and project management on the FCC plant addition project at the Kralupy Refinery in the Czech Republic.
The FCC plant included a new integrated resid conversion complex being added to the existing Ceska Kralupy Refinery. This resid conversion complex was based on an upgraded UOP Combustor-Style FCC reactor-regenerator, able to effectively charge and convert a low-sulfur resid mix of medium heaviness. Safety studies were performed for the Kralupy and Litvinov refineries.
The core FCC reactor-regenerator is supported by a collection of carefully integrated units and systems:
FCC main fractionator, integrated heavy FCC gasoline desulfurizer reactor train and FCC gasoline merox (two-stage extractive concept)
FCC gas concentration plant
Dedicated amine system (using DEA amine) - dedicated sour water stripper system
High purity propylene plant (single MD tray tower and heat pump) - Olefinic C3 and C4 LPG Merox (extractive type)
HHP steam for export and letdown to HP steam system for "self-powering” of key blowers/compressors
Upstream vacuum distillation unit to provide flexibility in controlling qualities of the resid cat feed composite
DCS control system
The capacity of the FCC unit was 3,800 tonnes per day, and the capacity of the vacuum unit, 2,000 tonnes per day.
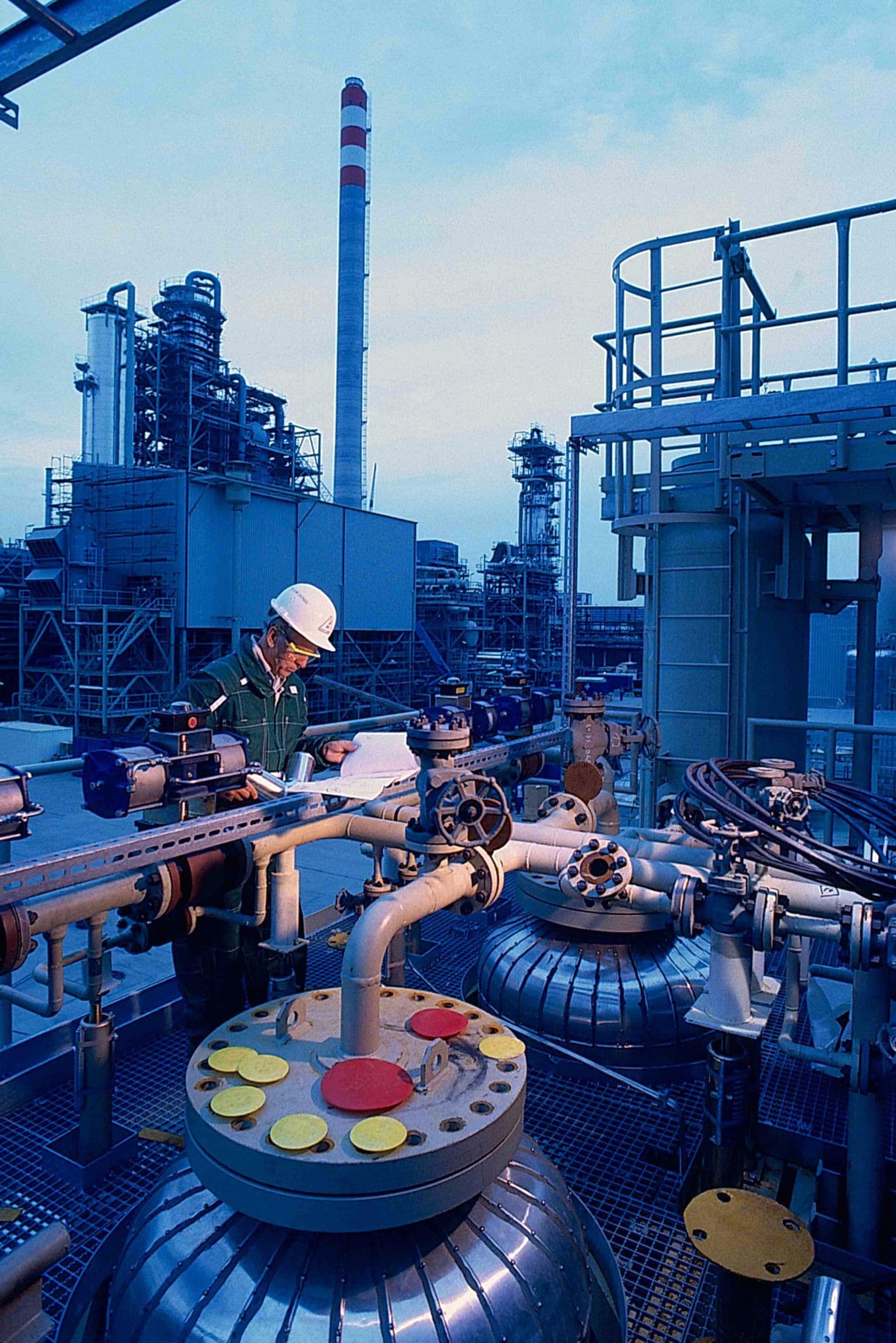
Conclusion
This lump sum turnkey project completed two months ahead of the contractual schedule of 29 months.
A Fluor Safety Award was given to the project in recognition of three million safe recorded work hours.
The high optimization of capital cost investment degree-of-integration resulted in substantial reductions in initial investment cost.
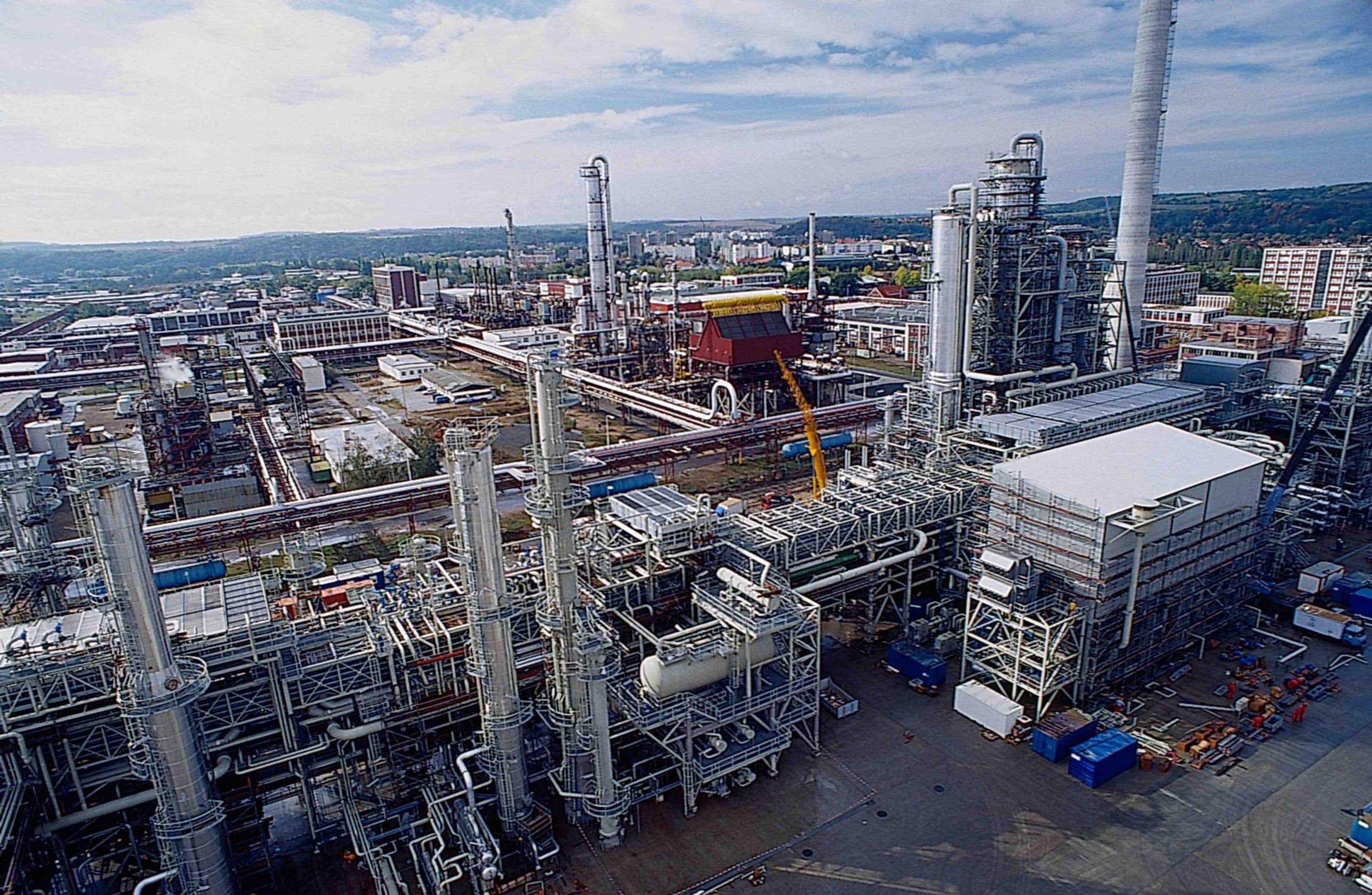