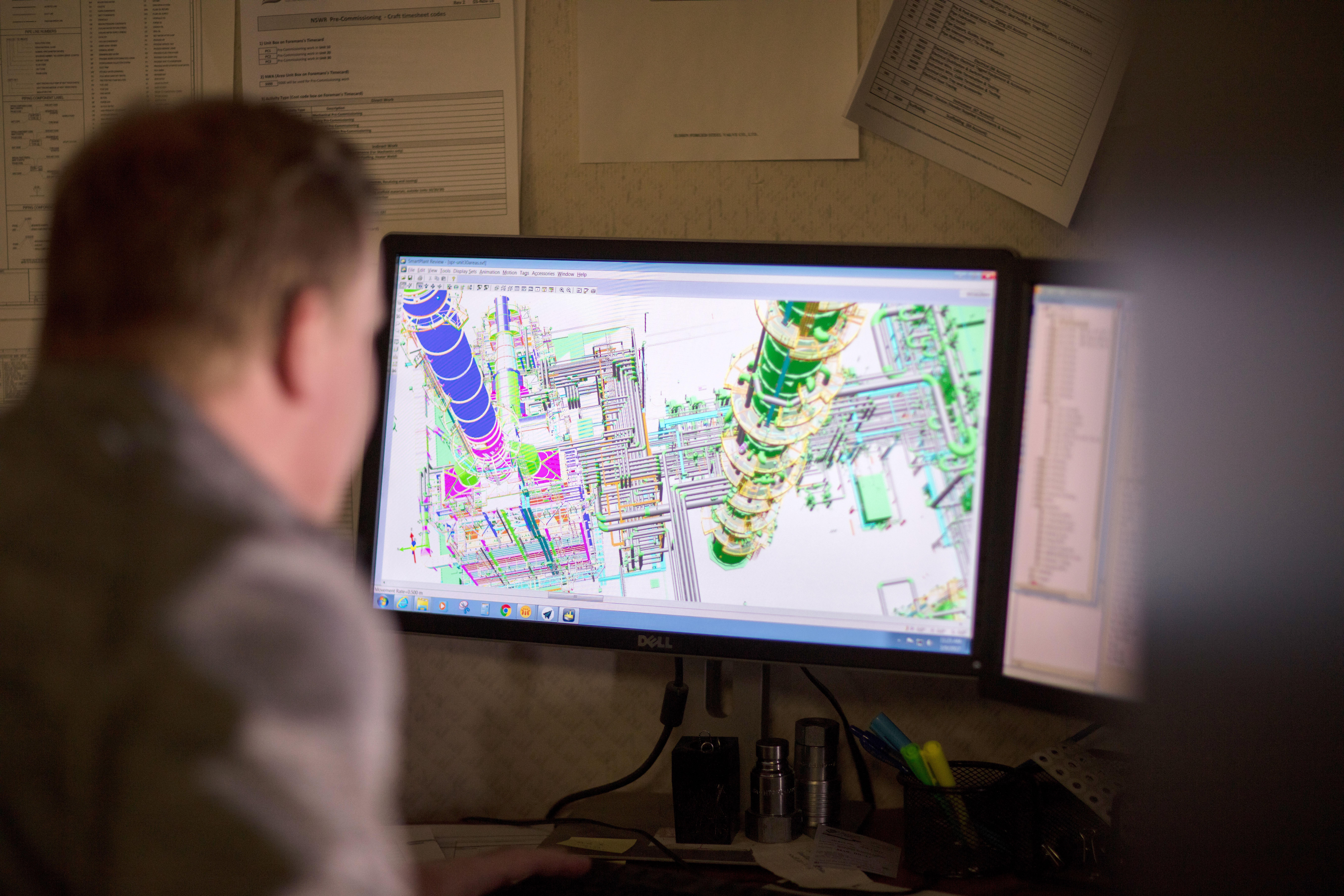
Discrete Event Simulation
- Home/
- Services and Expertise/
- Innovation and Expertise/
- Technologies & Processes/
- Discrete Event Simulation
Discrete Event Simulation
Abstract
Uncertainty caused by the randomness of events adds to the risk of every management and engineering decision. Traditional methods are ill-equipped to access the influence of randomness on design, schedule and cost. The problem is that an average value is typically applied to unknown conditions; however, an average is a poor choice because it lacks the capability to describe the variability associated with conditions found in everyday life. Compounding the problem is that a contingency factor is often added to offset unknowns such as strikes, power loss, shipping delays and equipment failures. This is a costly approach. An overly conservative design almost always results.
Discrete Event Simulation (DES) can better characterize randomness and should be part of every project's toolkit in order to assess the effects of design variability. Fluor's expertise in DES provides clients with a quantitative assessment of a plant's performance before financial resources are committed. DES entails building a mathematical-logical description that fully describes the major operational functions, storage characteristics, material transport and schedule as well as random outages. The model accounts for the volatility of real life through the incorporation of statistical functions or distributions that consider a range of values along with a probability of occurrence. Process imbalances, demand fluctuation and multiple breakdown/repair profiles are readily defined and adjusted within simulation models. Competitive organizations worldwide have proven they can reduce the risks associated with outages and other system disturbances by applying DES.
Client Benefits
Fluor's Discrete Event Simulation provides clients a cost-efficient mechanism to manage the risk of every management and engineering decision. The system simulation makes solving complex real-world problems surprisingly quick and easy, addressing problems that range from storage capacity to transportation system requirements to pipeline capacity, plant availability and plant layout and design.
Benefits of using DES include:
Allocating storage capacity to offset shipping constraints, weather disruptions or plant outages
Establishing transportation system requirements including ship, rail or truck movement and related loading/unloading operations to meet supply/demand fluctuations
Determining pipeline capacity and cycle frequency to meet varying demand schedules
Deciding plant availability to implement the most advantageous maintenance strategy and spare parts allocation to reduce the effect of equipment outages
Discerning plant layout, configuration, train capacity and sparing to maintain the required performance