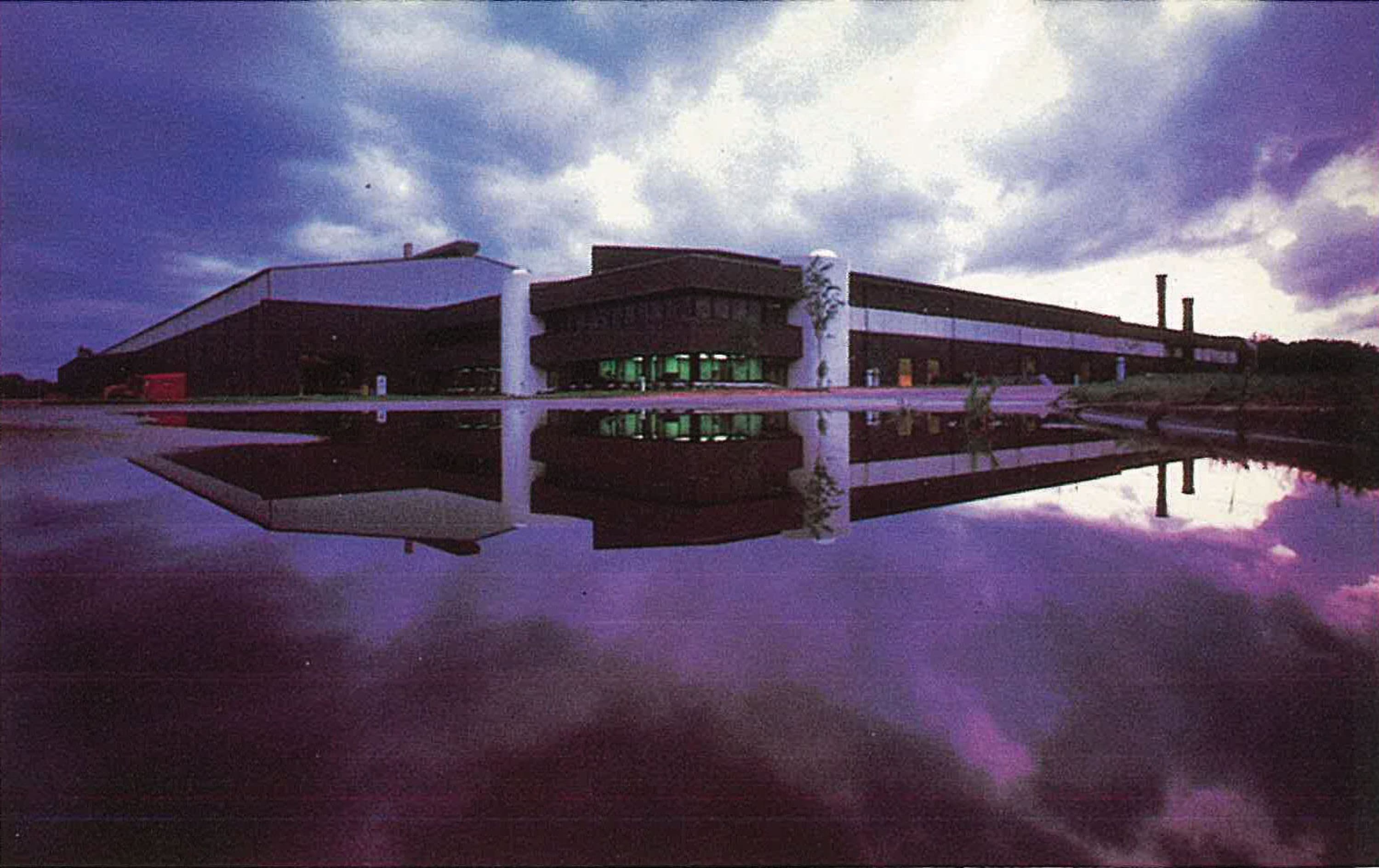
Reynolds Metals Aluminum Sheet Casting and Rolling Mill
Client: Reynolds Metals Company
Location: Hot Springs County, AR, U.S.
Business Segment: Urban Solutions
Industry: Mining & Metals

Executive Summary
Fluor provided design and construction services for this 273,750-square-foot, grassroots aluminum continuous casting and cold rolling mill.
Our scope of work comprised complete engineering services, including architectural and process design, equipment specifications, instrumentation and environmental engineering along with building and equipment installation.
Client's Challenge
The 273,750-square-foot facility converted molten aluminum to coiled, cold-rolled aluminum sheet for shipment to Reynolds Metals Company foil plants. The 18-month, two-phase project included construction of a main plant building and support facilities on a 240-acre greenfield site.
Fluor's Solution
Phase 1 consisted of approximately 153,000 square feet of the main plant, a railroad spur, water supply system, fuel oil storage facility, compressed air system, a recirculating cooling water system, electrical supply and distribution system, process gas systems, dross facility, parking lot and roads. The main building included the cast house with three casting lines, cold rolling mill with motor and coolant rooms, roll grinder, coil storage, maintenance shop and offices.
In Phase 2, the area of the main building was increased by 120,750 square feet to a total of 273,750 square feet. The additional building area housed five additional continuous caster lines, a melting furnace and additional coil storage area, which enabled the plant to double the rolling mill speed. The capacity of the utility systems was also increased.
The cast house had eight lines for continuous casting of coiled aluminum sheet. The melting furnaces were 90,000-pound capacity, tilting reverberatory furnaces that were charged with molten metal and internally generated aluminum scrap. The 90,000-pound-capacity holding furnaces provided a continuous flow of alloyed molten aluminum to the roll sheet casters at a rate of 4,000 to 12,000 pounds per hour. After cooling, the aluminum coil was delivered to the single-stand, four-high cold rolling mill by a hydraulically actuated walking beam conveyor.
The number of craft workers was 555 at peak.
Conclusion
Construction for both Phase 1 and 2 was successfully completed in the 18-month schedule, which included construction of a main plant building, support facilities and infrastructure for the grassroots mill.