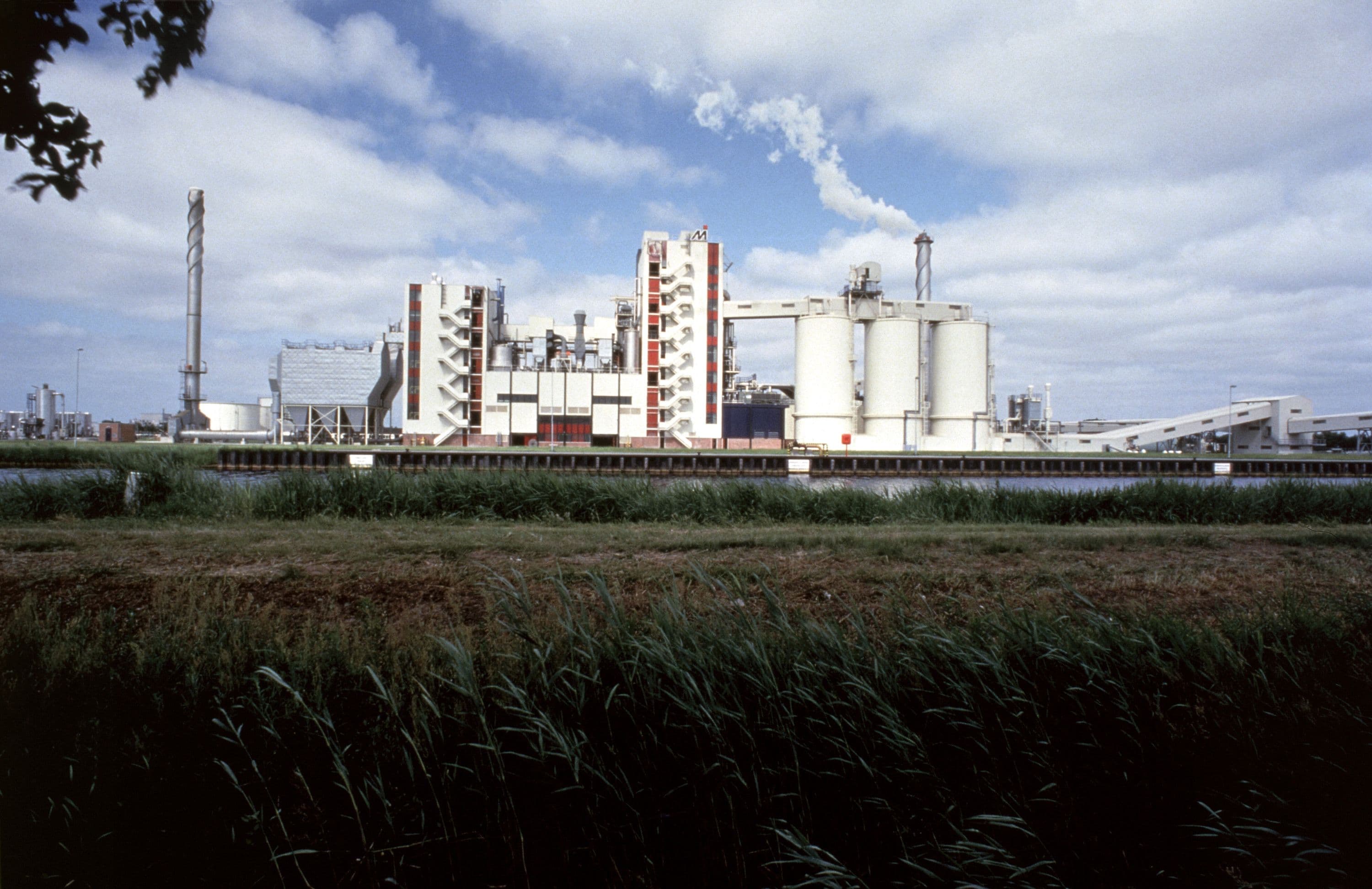
Magnesium Oxide Plant
Client: Billiton Nederland and N.V. Northern Development JV
Location: Veendam, The Netherlands
Business Segment: Urban Solutions
Industry: Mining & Metals

Executive Summary
In 1978, the client partnership selected Fluor to undertake engineering, procurement and construction for the $100 million, 100,000-metric-tons-per-year magnesium plant and the $25 million brine-solution mining facilities.
The scope of work included two main processing facilities, four 40-meter-wide (132-foot) separation tanks, the brine plant (located 15 miles from the chemical plant), a pipeline connecting the two plants and loading/unloading facilities.
Successfully completed in 1981, the magnesium oxide and brine-solution facilities provided over 150 permanent jobs and created a new economic resource base for the Northern Holland region.
Client's Challenge
Survey work established the existence of significant magnesium-bearing salt layers at a depth of 1,500 to 2,000 meters (about 6,000 feet) beneath the surface in the Veendam area. The deposit, which provided at least 40 years' reserve, was part of a large, evaporate-salts basin stretching from Scotland to the south of Poland.
Demand for magnesium oxide had climbed steadily with the need for better and more consistent quality steel produced at higher temperatures. Magnesium oxide is used in a brick form as a refractory lining. The material can resist temperatures as high as 1,900° C.
After promising pilot-plant production of magnesium oxide, Billiton reached agreement with the Northern Development Company (NOM) to jointly create companies to mine and manufacture the mineral in the Veendam area.
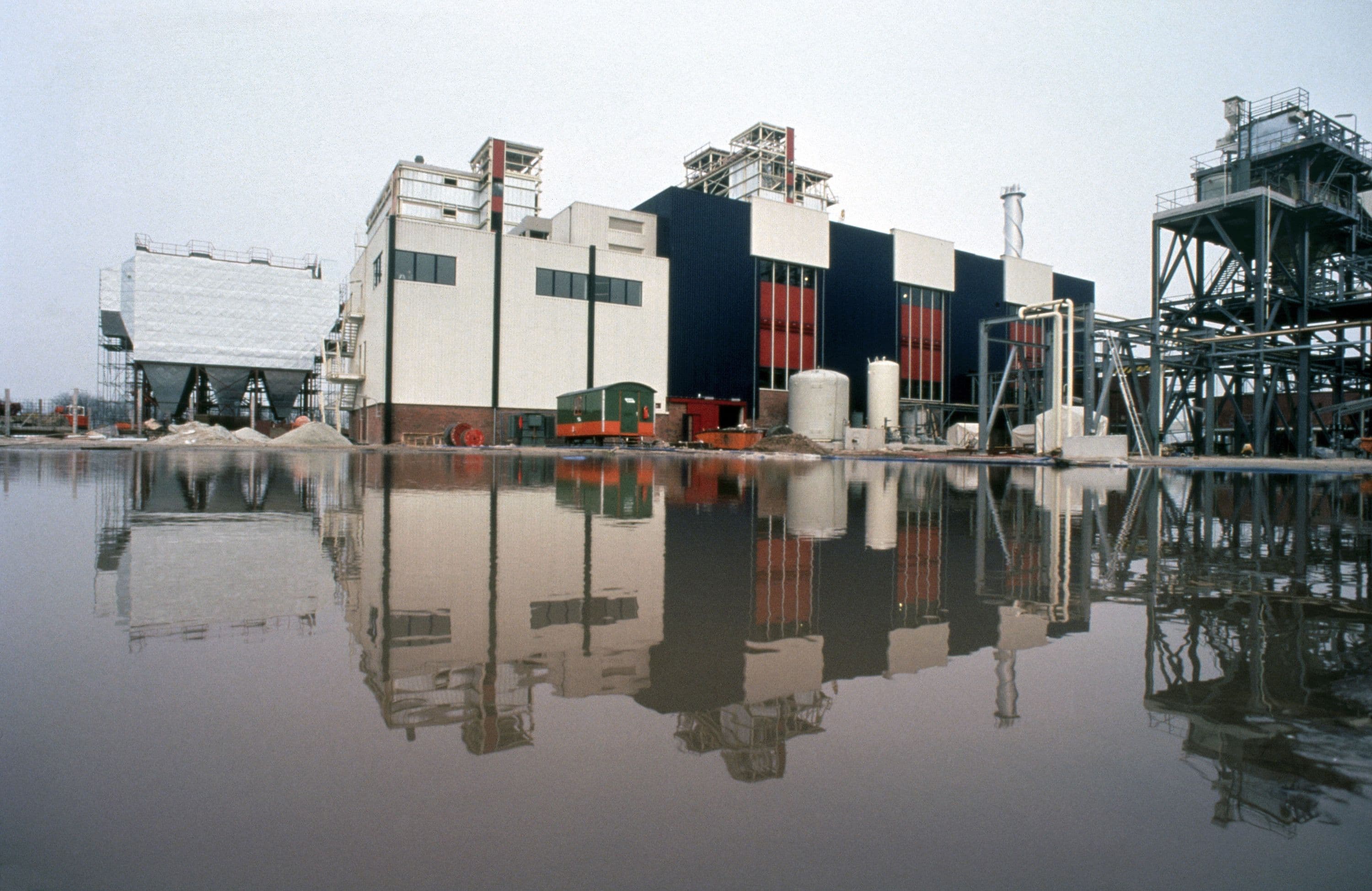
Fluor's Solution
In 1978, the client partnership selected Fluor to undertake engineering, procurement and construction for the $100 million, 100,000-metric-tons-per-year magnesium plant and the $25 million brine-solution mining facilities.
The scope of work included two main processing facilities, four 40-meter-wide (132-foot) separation tanks, the brine plant (located 15 miles from the chemical plant), a pipeline connecting the two plants and loading/unloading facilities.
The Wildervank Canal would be used to transport magnesium to Billiton's customers worldwide.
To mine the magnesium, a steel-casing pipe (in which two others were suspended) was sunk through a bore hole to the deposit. Water was injected downward, forcing brine to the surface where it was pumped via the pipeline to the plant. There, brine was combined with dolime, a material obtained by kiln-burning dolomite. In this wet-phase, the resulting magnesium hydroxide was thickened, washed and then filtered.
In the subsequent dry phase, workers heated the magnesium hydroxide to evaporate water content, leaving a white powder. To achieve the correct density and final product, the powder was compressed to form almond-shaped briquettes. These ware fired at 2,000° C.
Our project team worked closely with the client and government officials to plan for environmental safeguards, particularly to dampen noise and contain dust particle from the manufacturing operation. Computer calculations revealed that the plant's extensive mechanical conveyor operated less than 45 decibels at the perimeter boundary. Dust was controlled by enclosing the dry section and installing air conditioning.
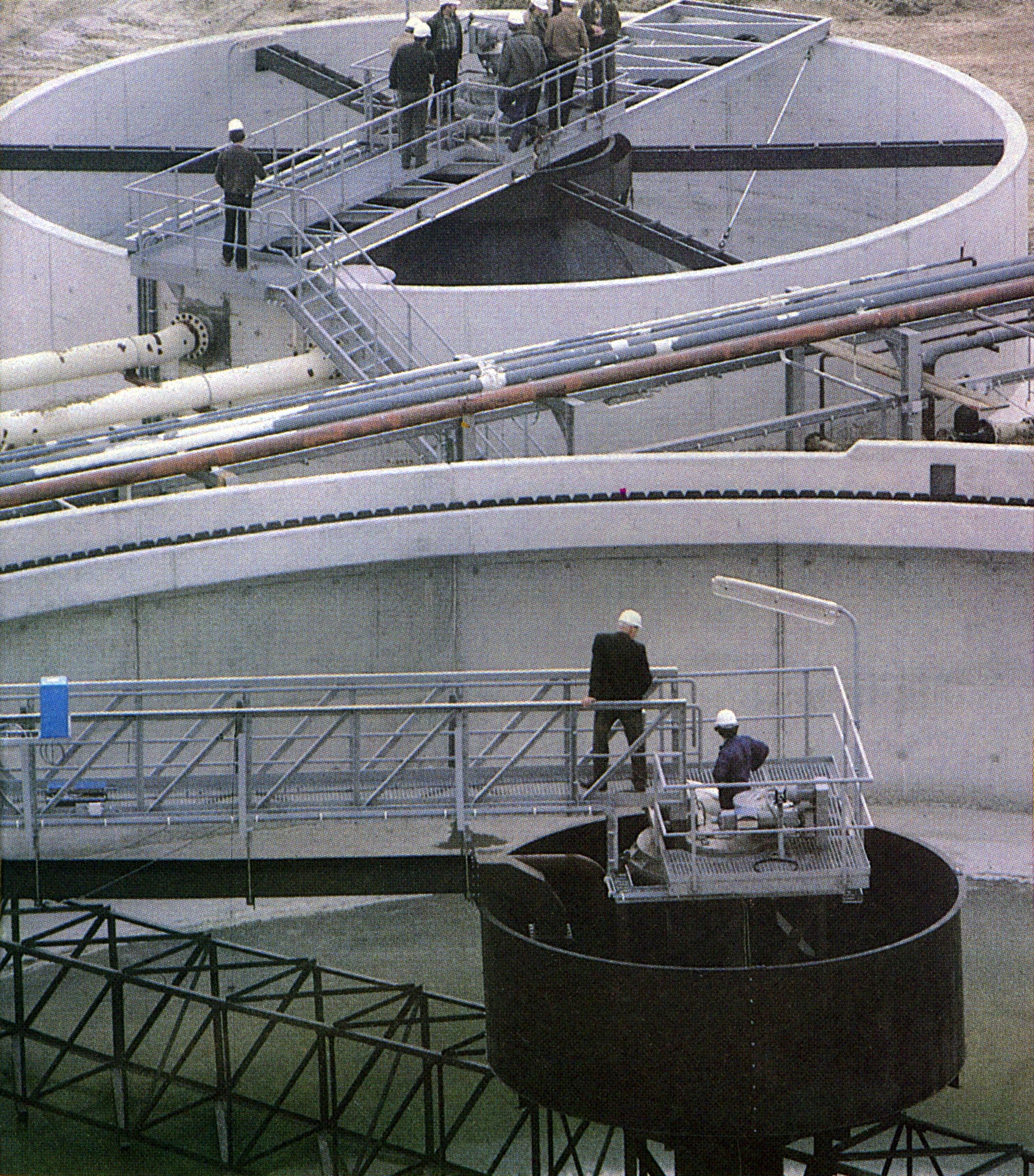
Conclusion
Successfully completed in 1981, the magnesium oxide and brine-solution facilities provided over 150 permanent jobs.
There was also a related local employment effect, such as increased rail work, shipping and maintenance, that engaged the local economy and community.
Billiton's capital investment created a new economic resource base for the Northern Holland region.
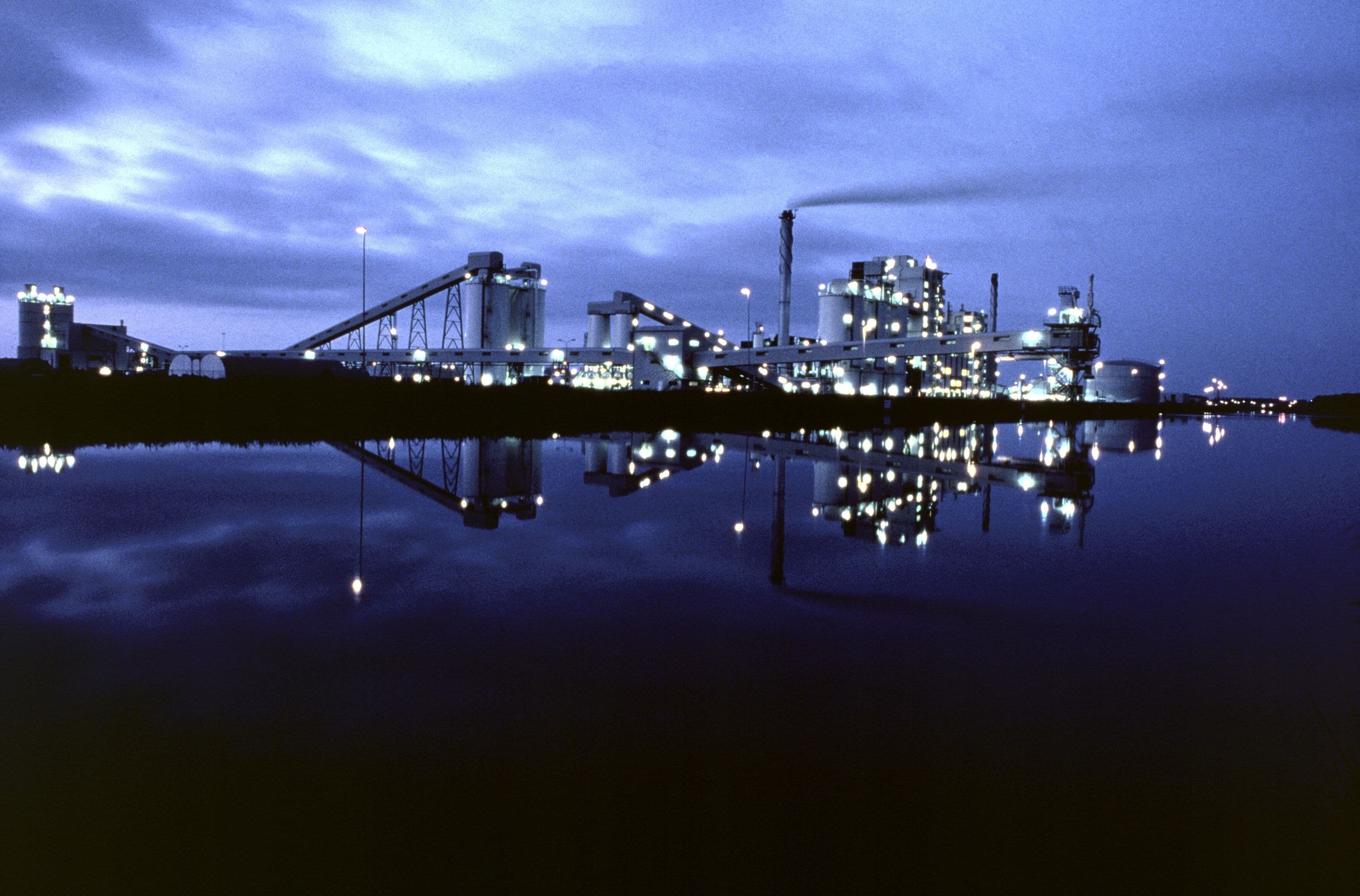