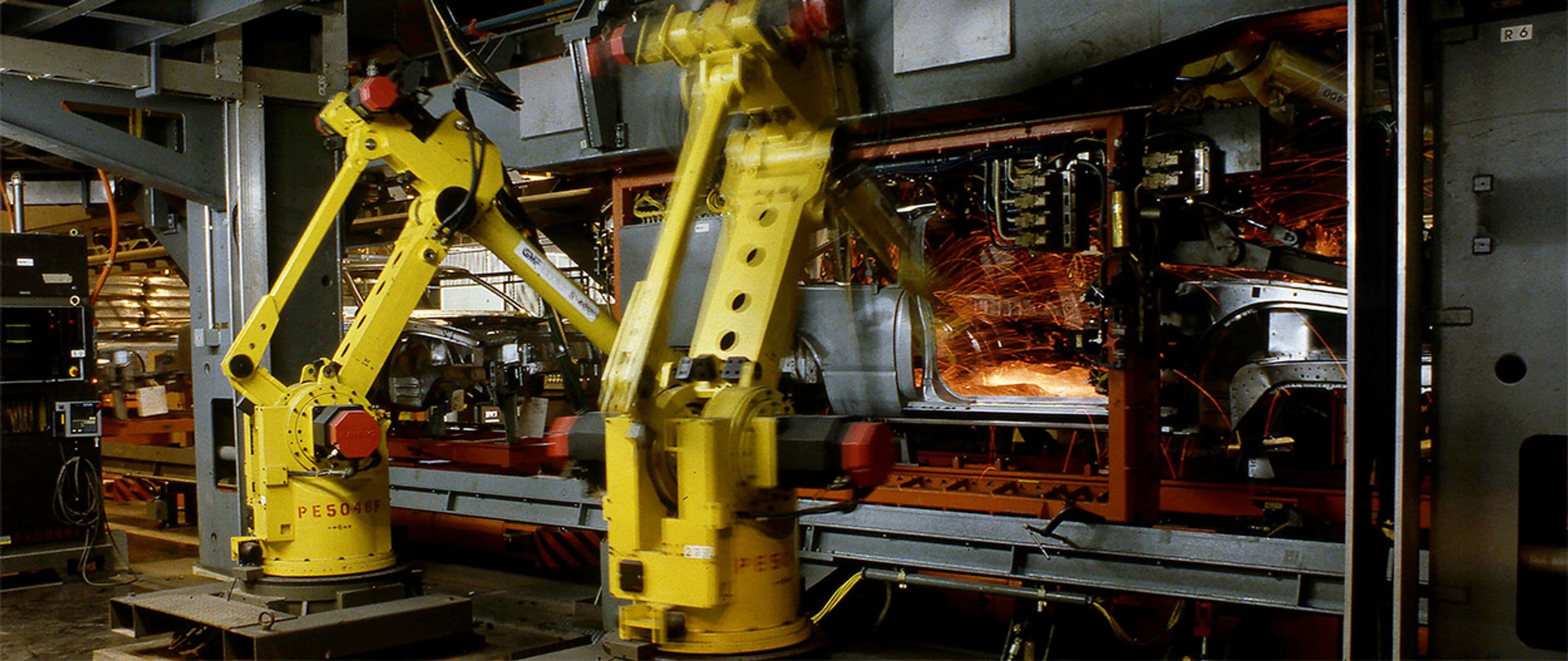
General Motors Doraville Automotive Facility
Client: General Motors Company
Location: Doraville, GA, U.S.
Business Segment: Urban Solutions
Industry: Manufacturing

Executive Summary
Fluor was initially selected to provide construction management services for this new three-story, 12 million square foot paint shop facility and related operations. Prior to completion of the paint shop, General Motors moved its GM-10 modernization program for production of the 'W" car to the Doraville facility.
We were selected to provide design, construction management, start-up and other support services for this project. Upon project completion, the Doraville plant exceeded its planned, acceleration schedule for production during the first six months after start-up.
Client's Challenge
Based on the scope of work to be performed and the tight schedule, planning and packaging the construction was critically important to avoid interference with the operating plant and to provide a clear division of responsibilities among the various contractors.
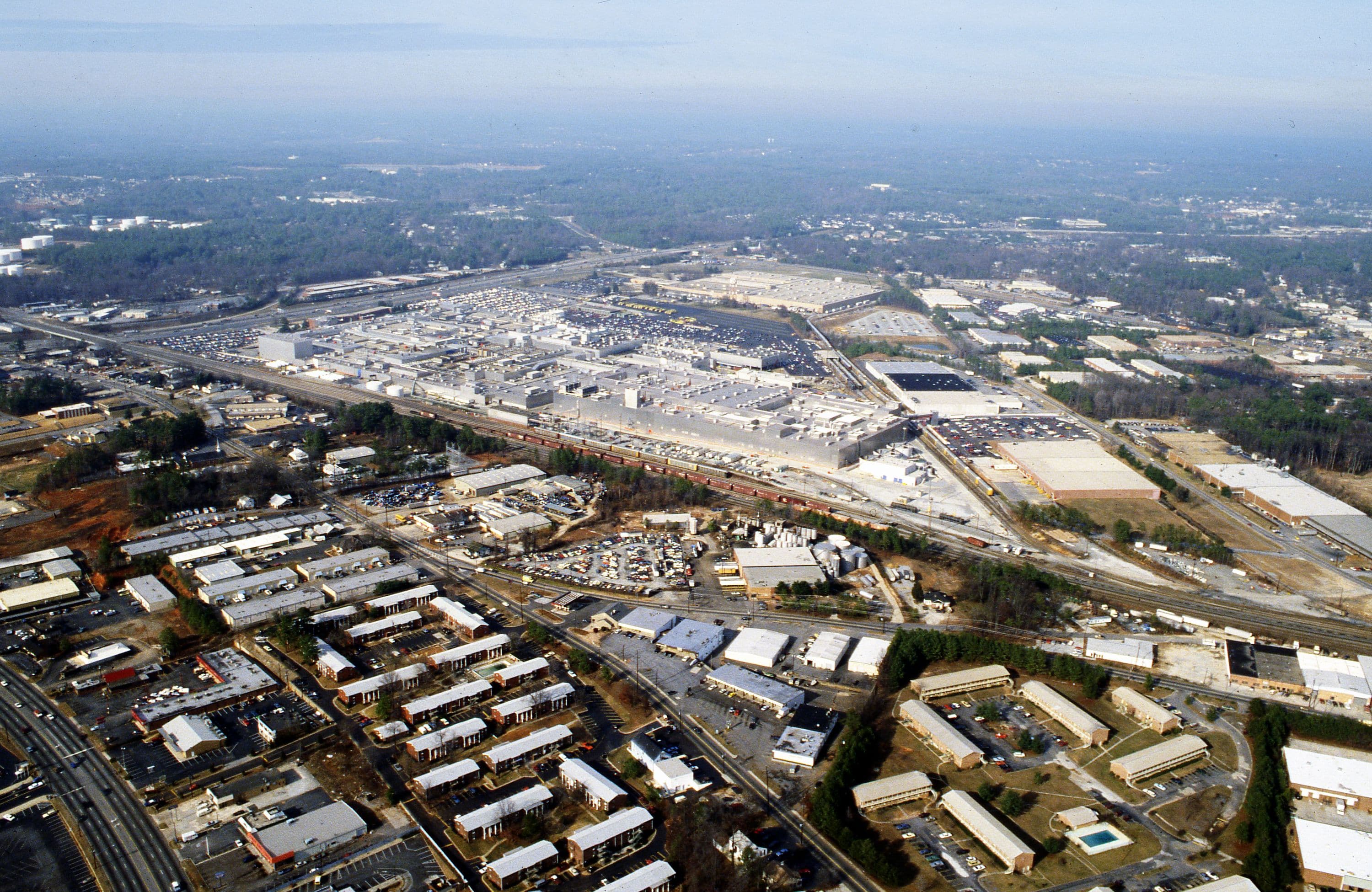
Fluor's Solution
The design portion of the project involved more than 250,000 man-hours of engineering, including the design of an 81,000 square-foot addition to the existing building, a new paint shop entrance bridge, conveyor enclosures, paving, fencing, rail relocation, cooling towers, switch gear sections, fire alarm systems, high bay lighting, ventilation rework, welder water system, compressed air systems and utilities distribution.
Construction was preceded by demolition of 2 million square feet of the facility's existing interiors. A major portion of existing tooling was tagged, saved and subsequently shipped for use in other GM plants. The demolition/construction schedule was set for 18 weeks.
At the end of 12 weeks, equipment installation was completed. The remaining six weeks were dedicated to equipment checkout, debugging and start-up. More than 700,000 square feet of concrete was poured, with half of the pour specified as super-flat to accommodate automatic guided vehicles in the body shop. The plant also included a maintenance monitoring automation system, computerized control conveyance systems and approximately 350 robots.
In addition to engineering and construction services, we also provided more than 40 upgrade training courses to assist operators and maintenance personnel on the new automated equipment.
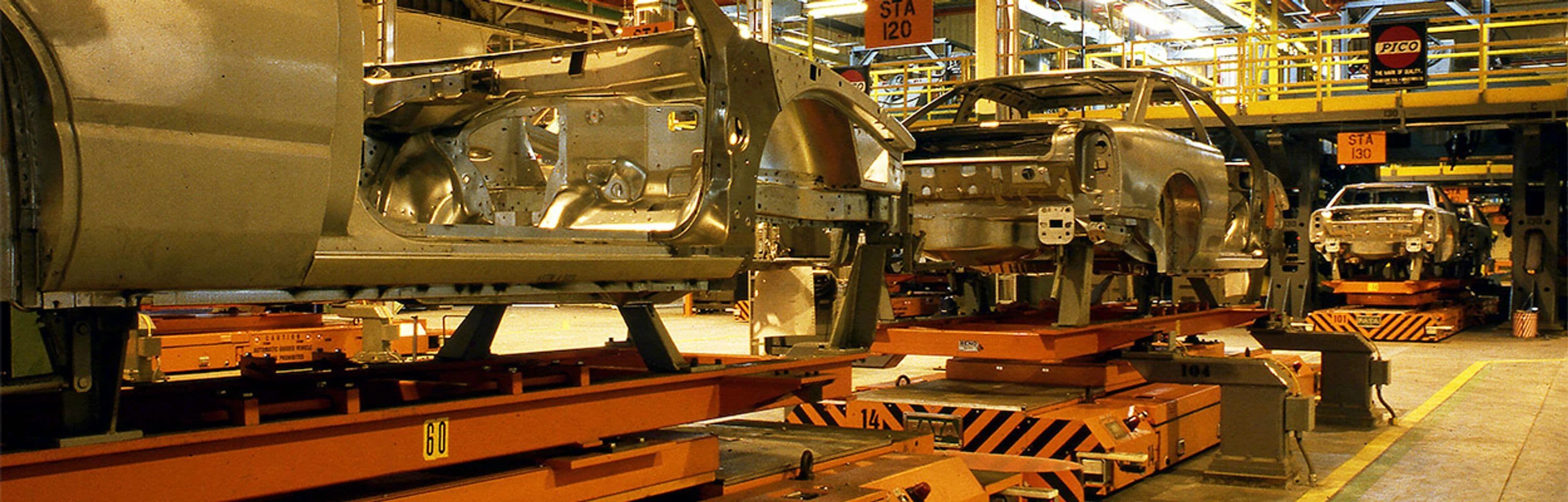
Conclusion
Engineering and construction were completed ahead of schedule and under the approved budget.
Based on the successful start-up of the Doraville Plant, Fluor was awarded a subsequent contract for the 4-door "W" car model production.
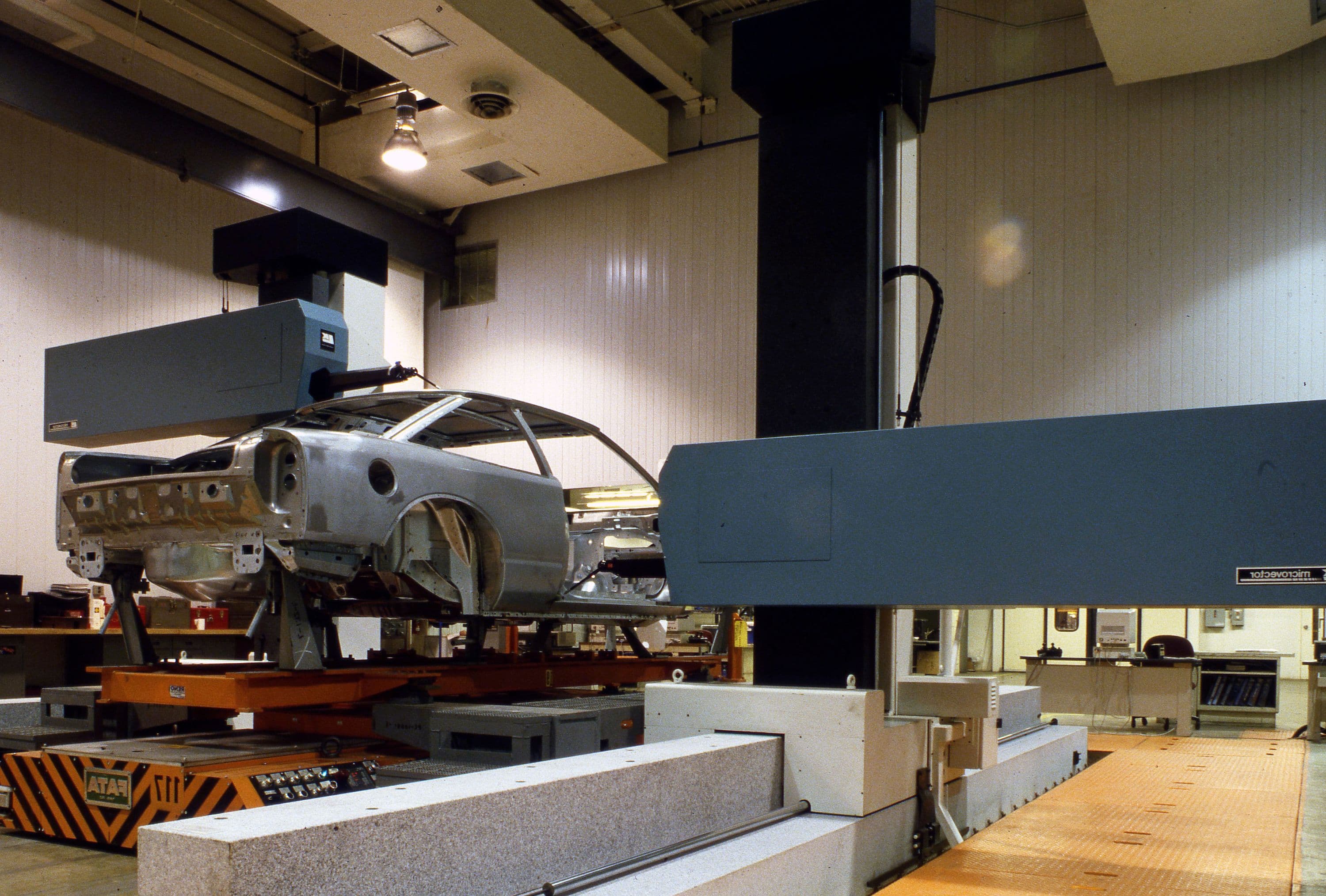