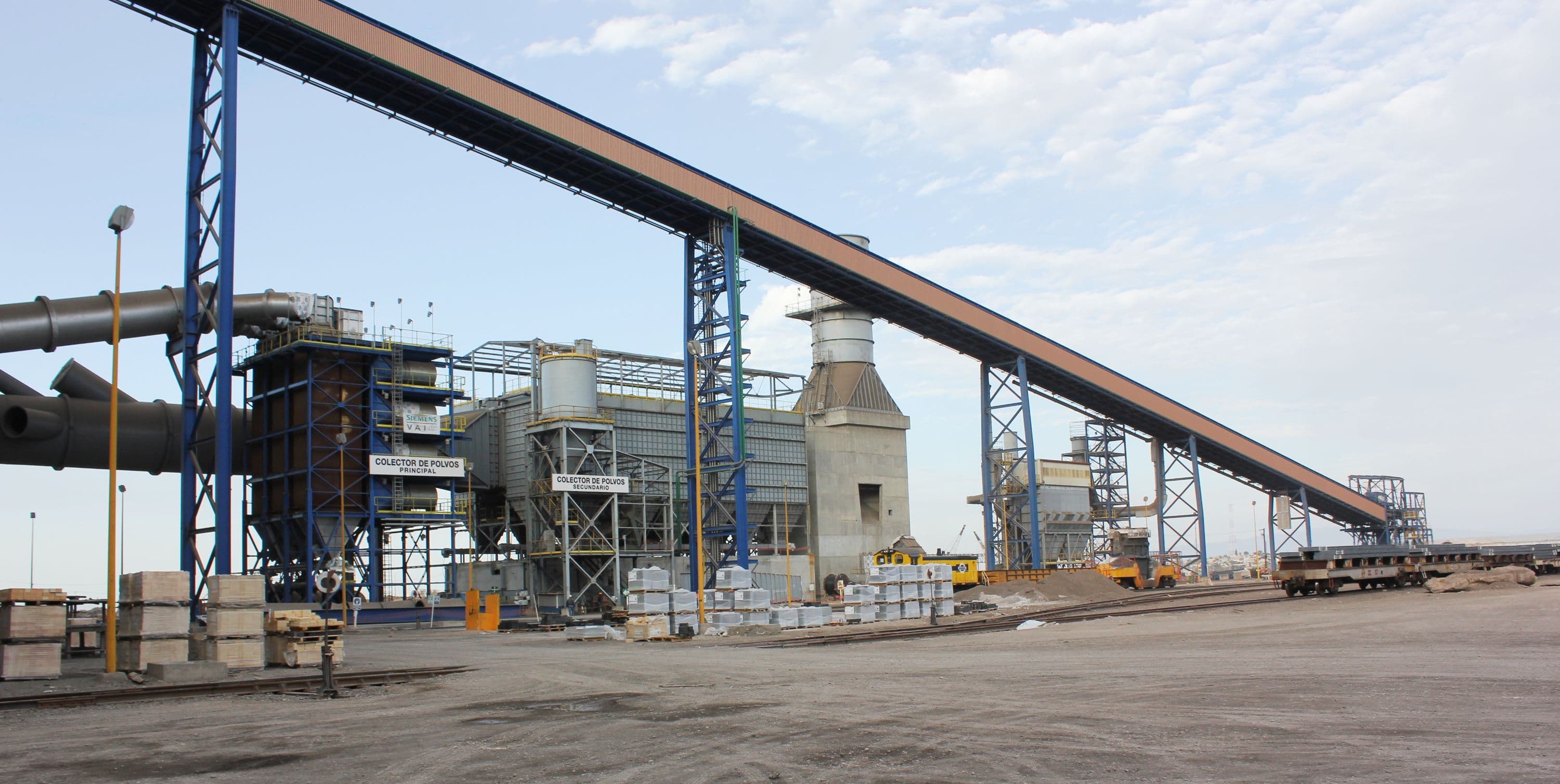
Fenix Steel Plant and Hot Mill
Client: Altos Hornos de Mexico S.A. de C.V. (AHMSA)
Location: Monclova, Coahuila, Mexico
Business Segment: Urban Solutions
Industry: Mining & Metals

Executive Summary
Altos Hornos de Mexico S.A. de C.V. (AHMSA) sought to increase its steel production by 40%. ICA Fluor, a Fluor joint venture, began the Fenix project by determining the project definitions and scope, developing a ROM estimate for each plant, and supplying all equipment and most of the bulk materials to support this goal.
Engineering, procurement and construction scopes for the new plant were awarded later.
Client's Challenge
Already the largest integrated iron and steel production company in Mexico, AHMSA produced 3.6 million tons per year. The company decided to increase production capacity by 40% with a new steel plant, hot mill plant, blast furnace and oxygen plant near its major iron and coal mining operation in Baja California Sur.
One of the many challenges at the site was the steel plant location: next to a rail line for incoming trains that carried melted steel at 1,600° C (2,912° F). The steel plant area was small and congested with pipe racks, rail tracks and electrical works. The steel plant was to contain a ladle furnace, electric arc furnace and wide and thick slab caster, with a capacity of 1.2 million tons of steel slabs per year.
The plate mill would contain a set of reheating furnaces, a Steckel mill (also known as a reversible finishing mill), cooling systems, cutting machines and ancillaries, with a capacity of 1 million tons/year of rolled and flat plate. It was designed to have all piping and electrical cables underground.
Finally, the local workforce was trained mostly in mechanical work, and training was needed for civil work and steel fabrication.

Fluor's Solution
ICA Fluor was founded in 1993 as a joint venture of Empresas ICA, S.A.B. de C.V., and Fluor to provide engineering, procurement and construction services in Mexico. The company began the Fenix project by determining the project definitions and scope, developing a ROM estimate for each plant, and supplying all equipment and most of the bulk materials.
Engineering, procurement and construction scope was awarded later.
Major obstacles were overcome in constructing plants at an operating steel site. For example, to avoid interference between the construction work and the trains feeding the operating steel shop, workers were moved a safe distance from the rail tracks whenever the trains came in, every 45 minutes.
More than 600 tons of pig iron were buried underground. Some pieces weighed more than 30 tons and had to be cut into pieces to be moved. In addition, the tracks had to be moved several times to accommodate excavations.
Structural steel was designed and fabricated in six shops, where management and craft were trained in Fluor procedures and standards and welders were qualified to the specifications required. More than 600 craft workers were trained.
Civil workers were housed in nearby camps.
The peak workforce was 4,500.
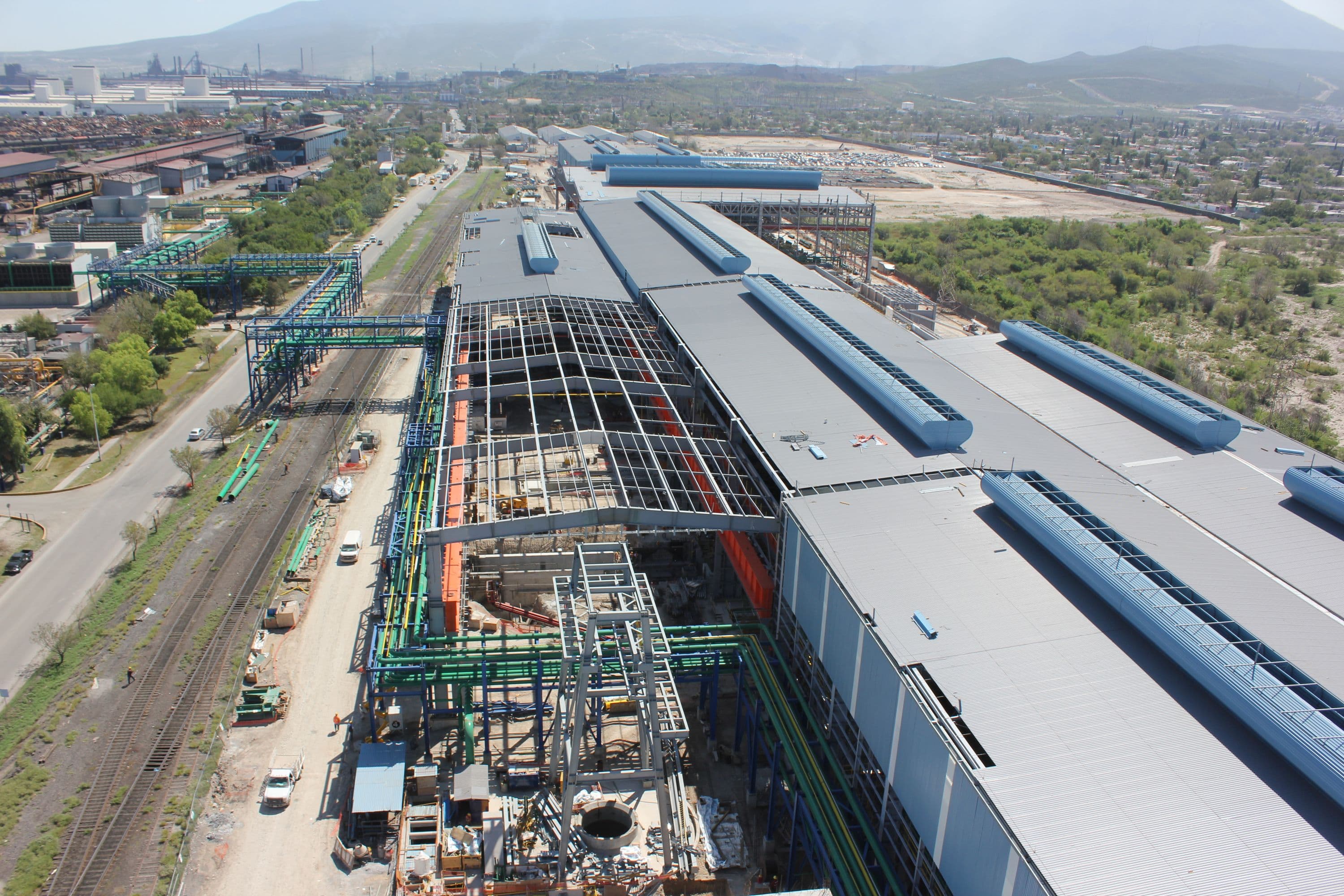
Conclusion
AHMSA's $1 billion investment would increase its annual production to 55 million tons per year. ICA Fluor fabricated and installed 30,000 tons of structural steel and 15,000 tons of rebar; poured 80,000 cubic meters of concrete; and constructed 29,000 square meters of buildings and installed 1,200,000 meters of electric wire. The most difficult work was the foundation of the Steckel mill, which required 10,000 cubic meters of high-resistance concrete, with rebar densities of 350 kilograms per cubic meter.
Approximately 1,000 jobs were directly generated by the project, along with others in the area that supplied goods and services, and 5,000 indirect jobs.
The project received three annual ICA Fluor safety awards and the Group ICA “Best Project” award.
The AHMSA Fenix project received Fluor's 2014 Hugh Coble Award for Project Excellence. The award is based on outstanding performance in several areas, including safety, value creation and client and community relations.
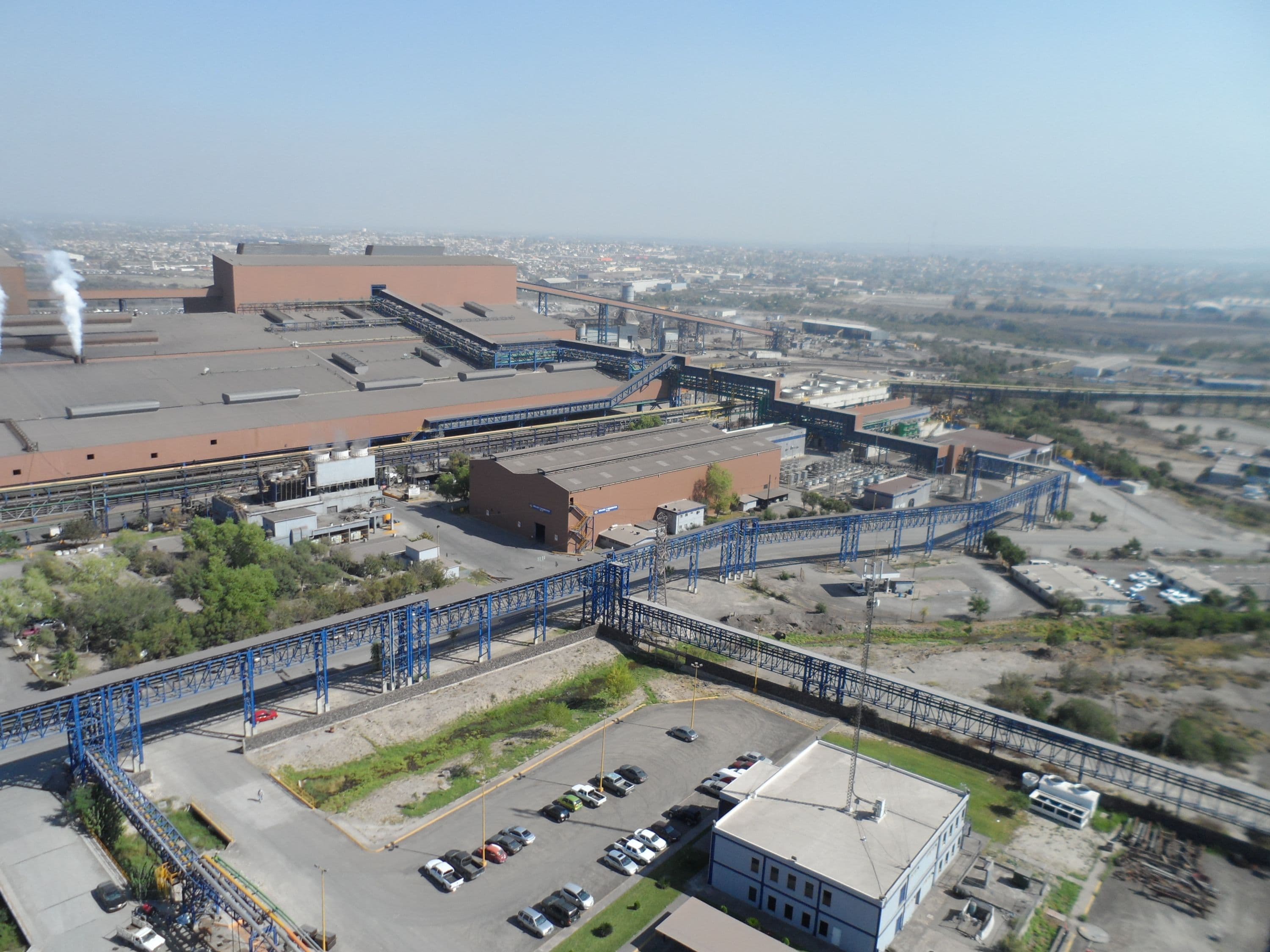
Project Gallery
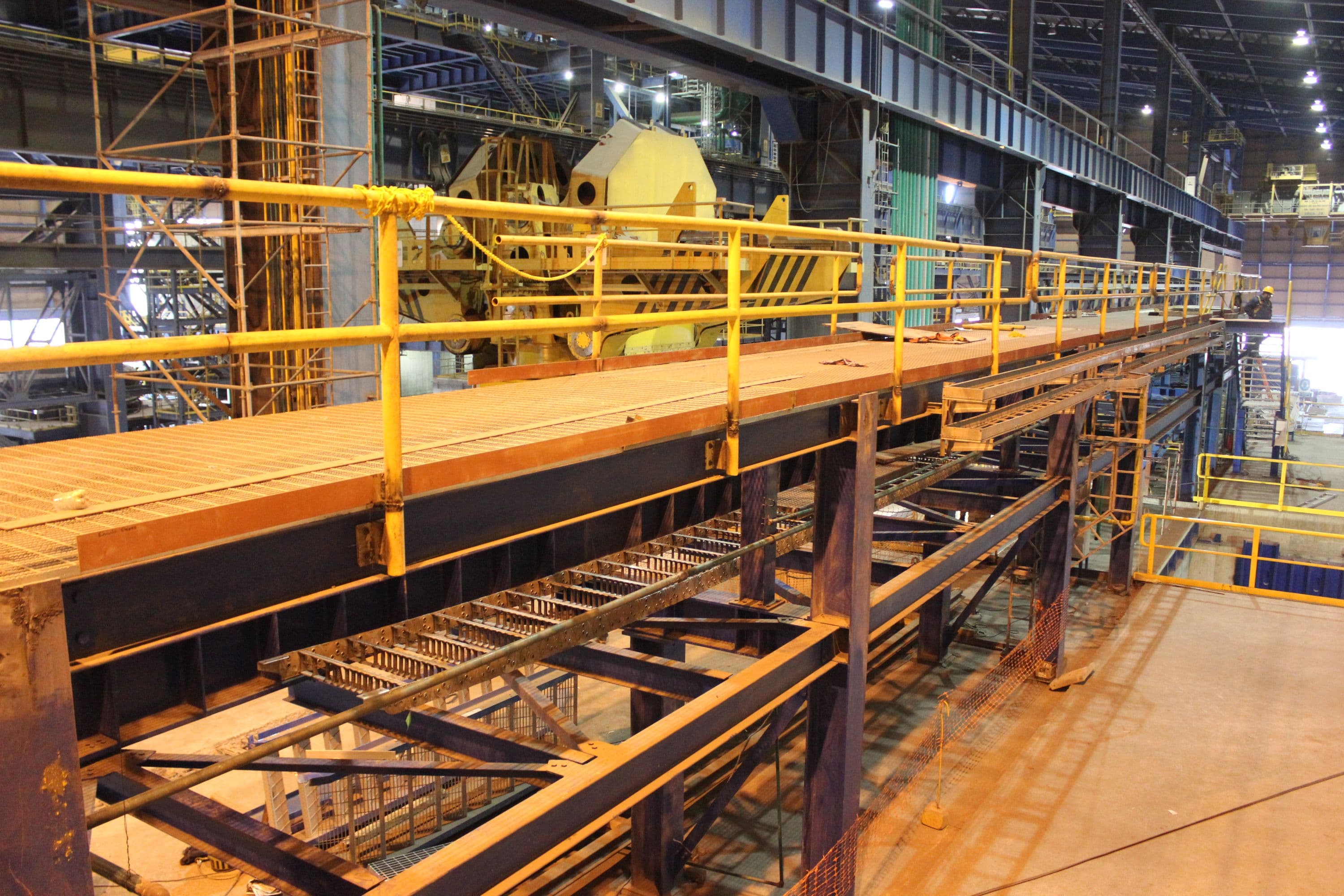
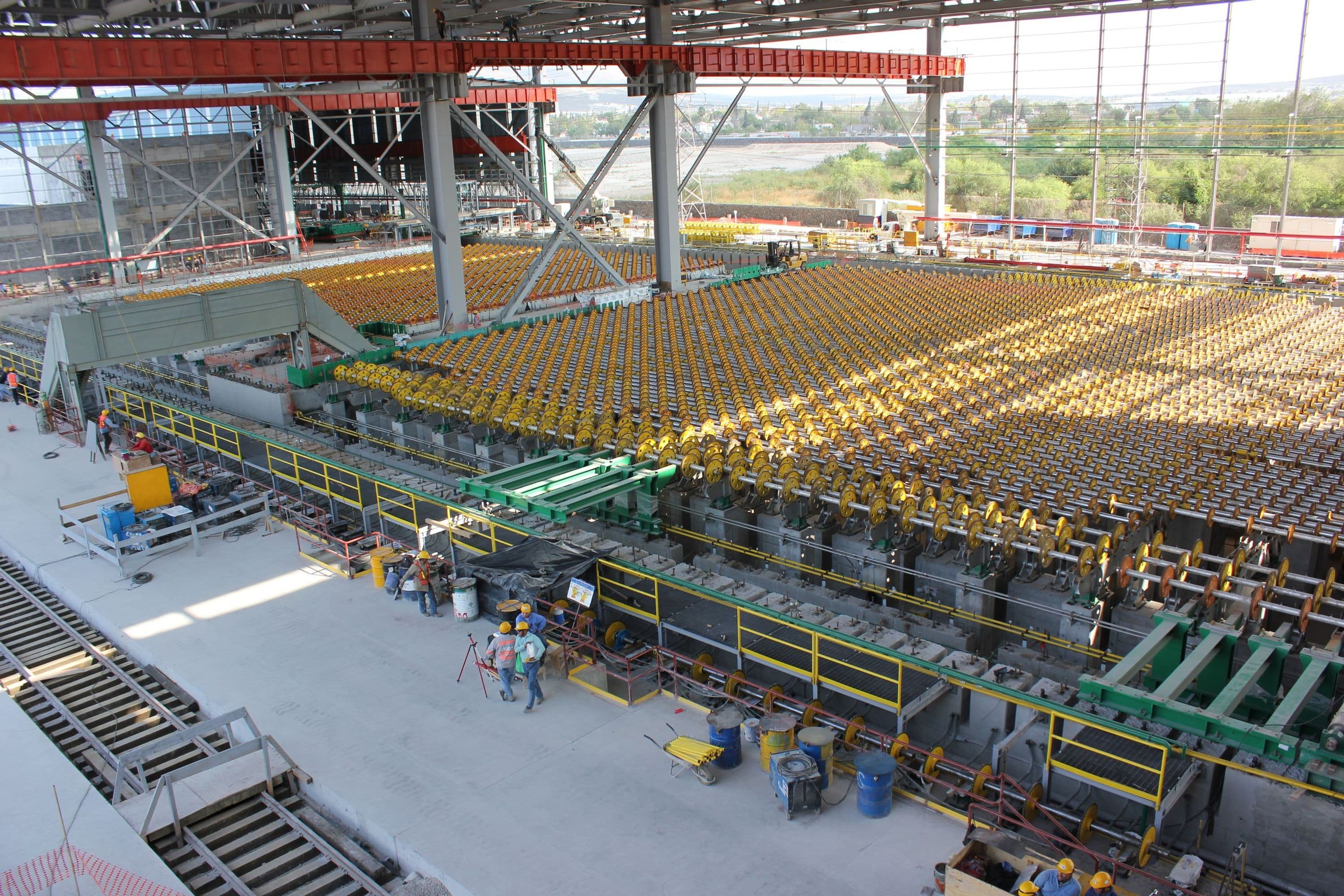
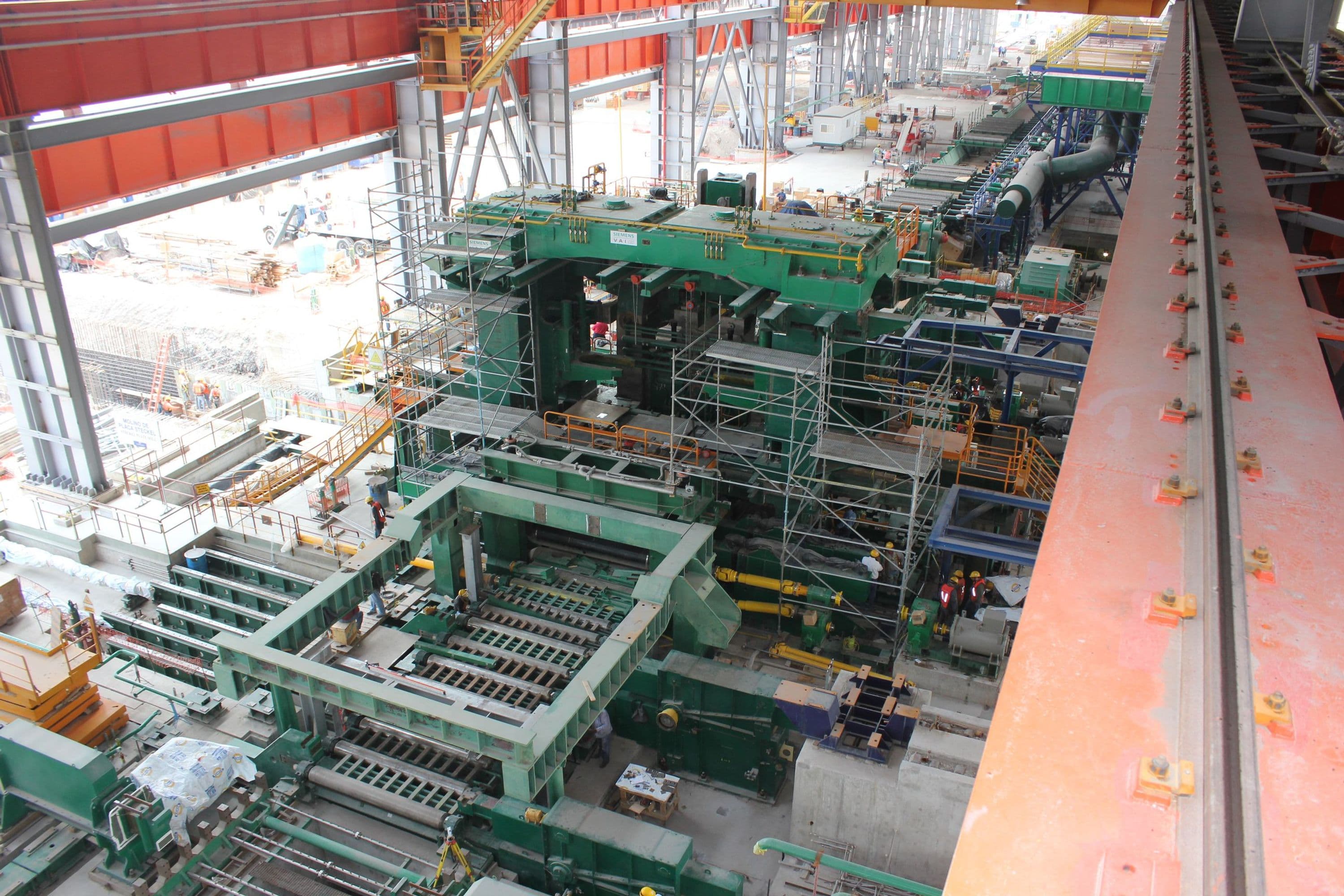
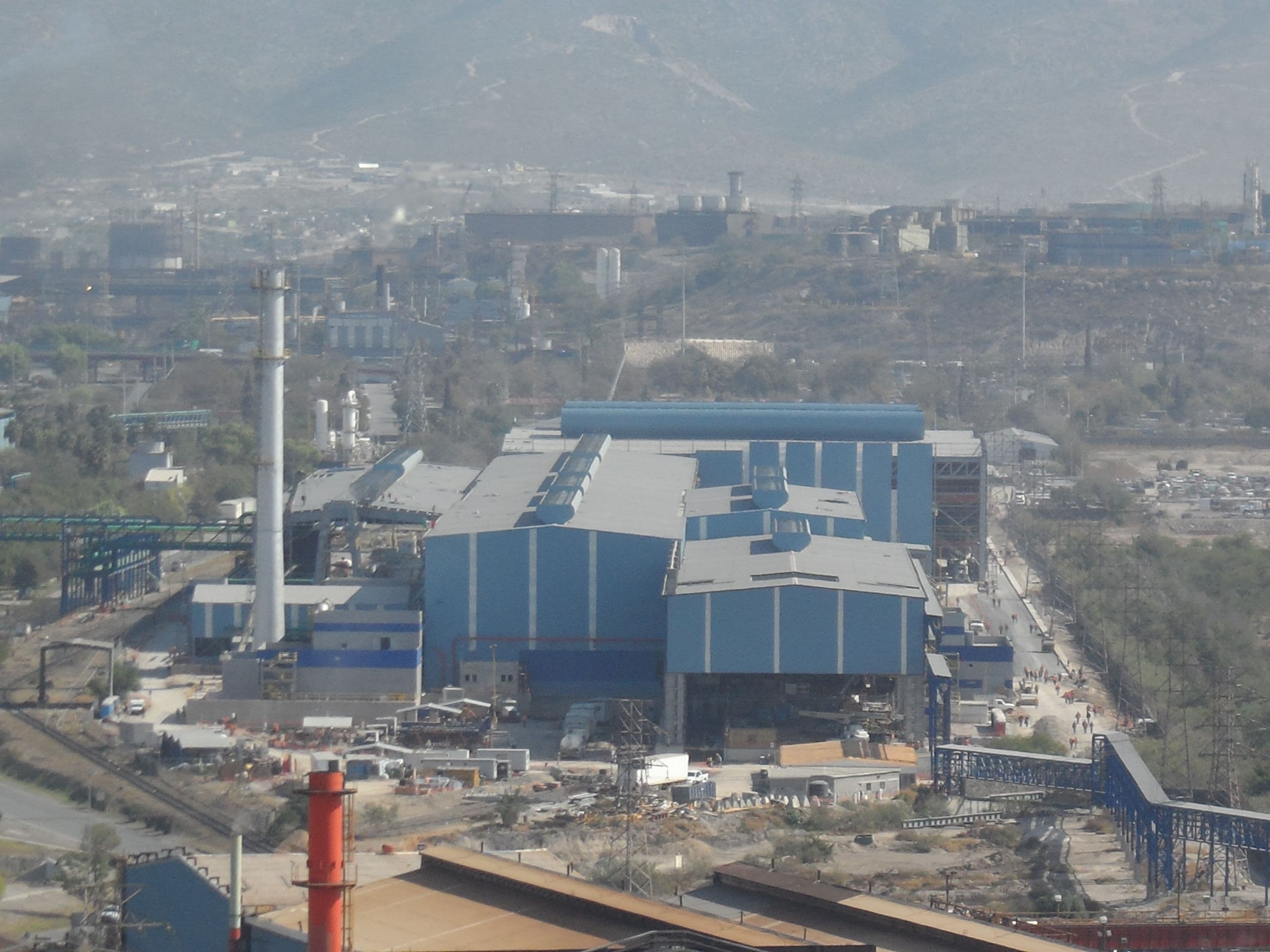
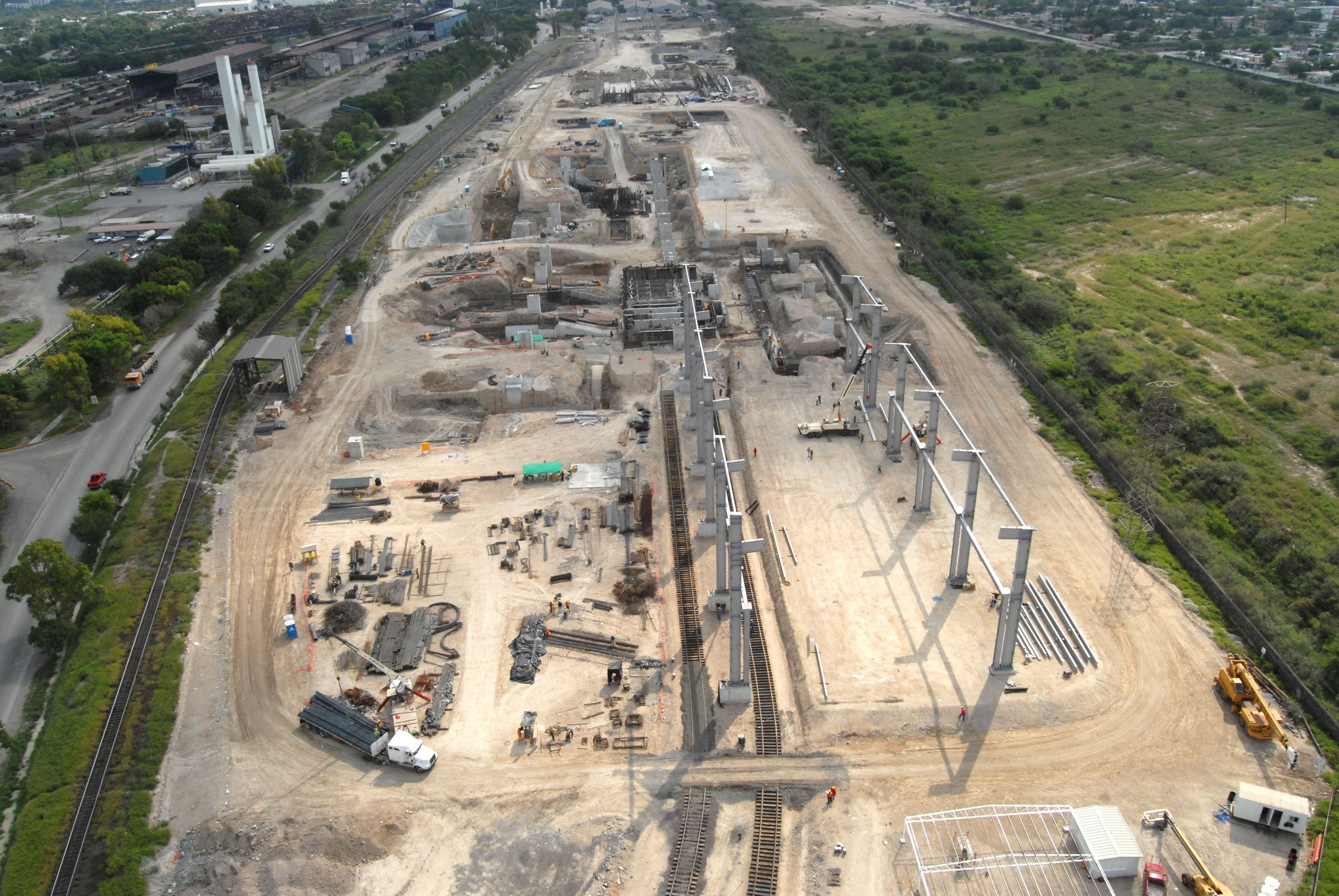
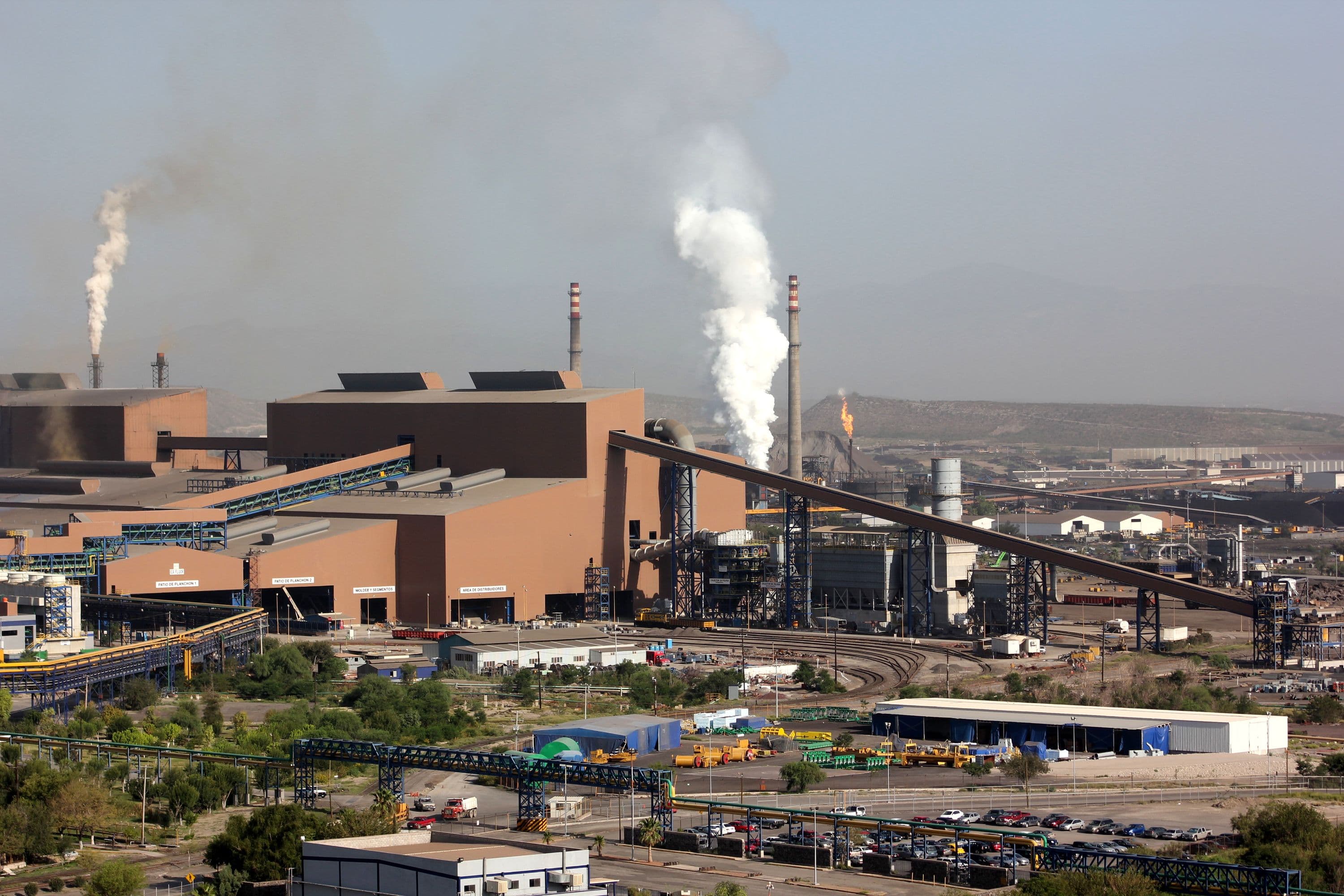
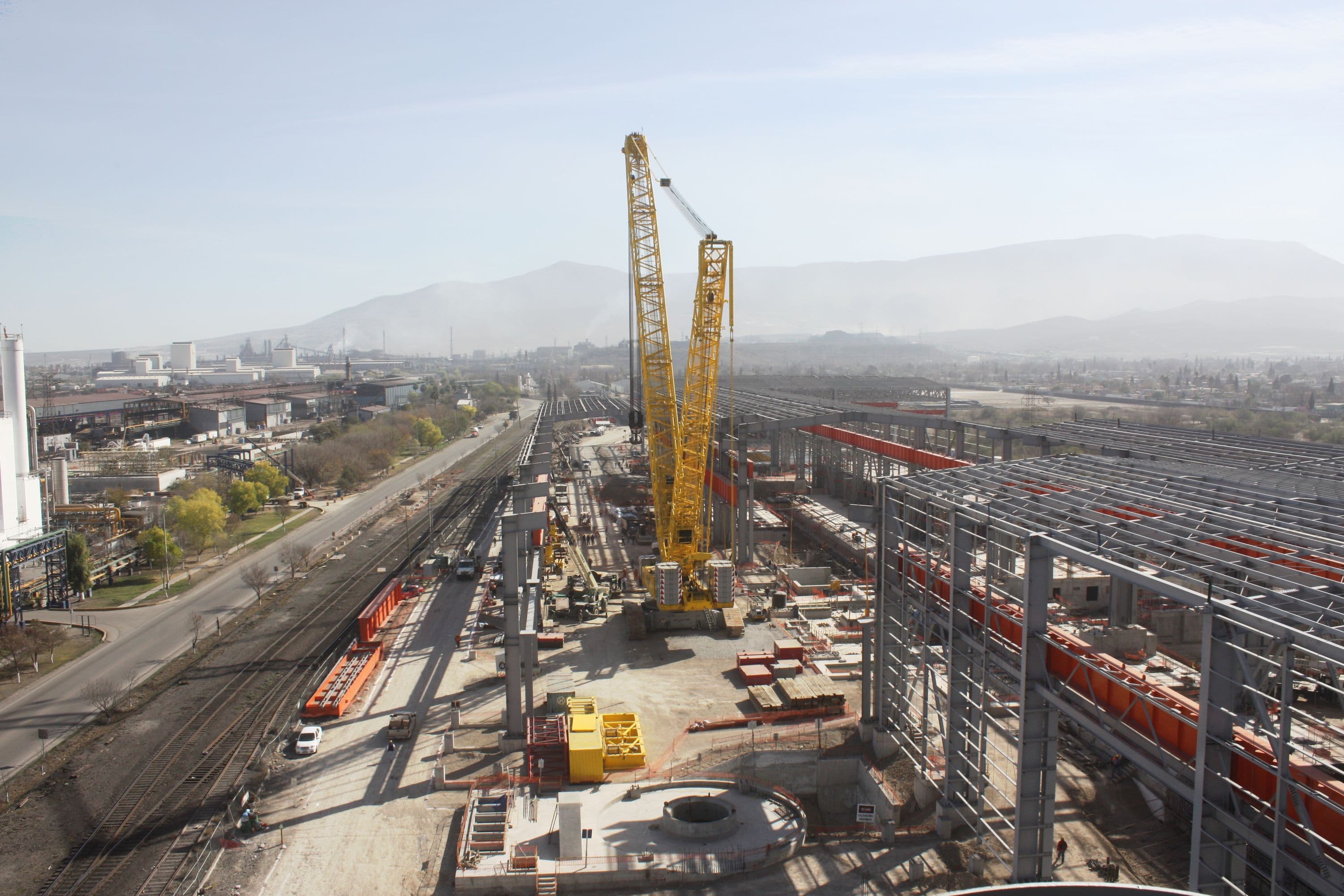