&w=3840&q=75)
Echo Bay Mines Materials Handling System
Client: Echo May Mines Ltd.
Location: Round Mountain, NV, U.S.
Business Segment: Urban Solutions
Industry: Mining & Metals

Executive Summary
Echo Bay Mines' expansion of its existing heap leach operation to 35,000 tons per day (tpd) involved a large infrastructure scope of work including a new townsite, airstrip, material handling, gold concentrator and process facility. We performed the detail design, equipment procurement, contract specification and commissioning for the material handling.
We also performed detail engineering and procurement for an 8,000-tpd gold concentrator. The process included primary crushing, single stage SAG milling, two-stage high frequency screening and three stages of spiral gravity concentration followed by two stages of shaking table gravity concentration. Key aspects of the design included integration of the concentrator into the existing heap leach operating facilities.
Client's Challenge
Echo Bay Mines had sanctioned the investment for a significant capital expansion and infrastructure for its Round Mountain gold mine to increase the capacity and productivity of the operation.
The new, moveable 60/89 crushing plant was designed to produce minus 8 inch crushed ore at a rate of 5,000 tph. To support the increased gold operation output, the expansion also incorporated physical infrastructure for the town and air transportation facilities
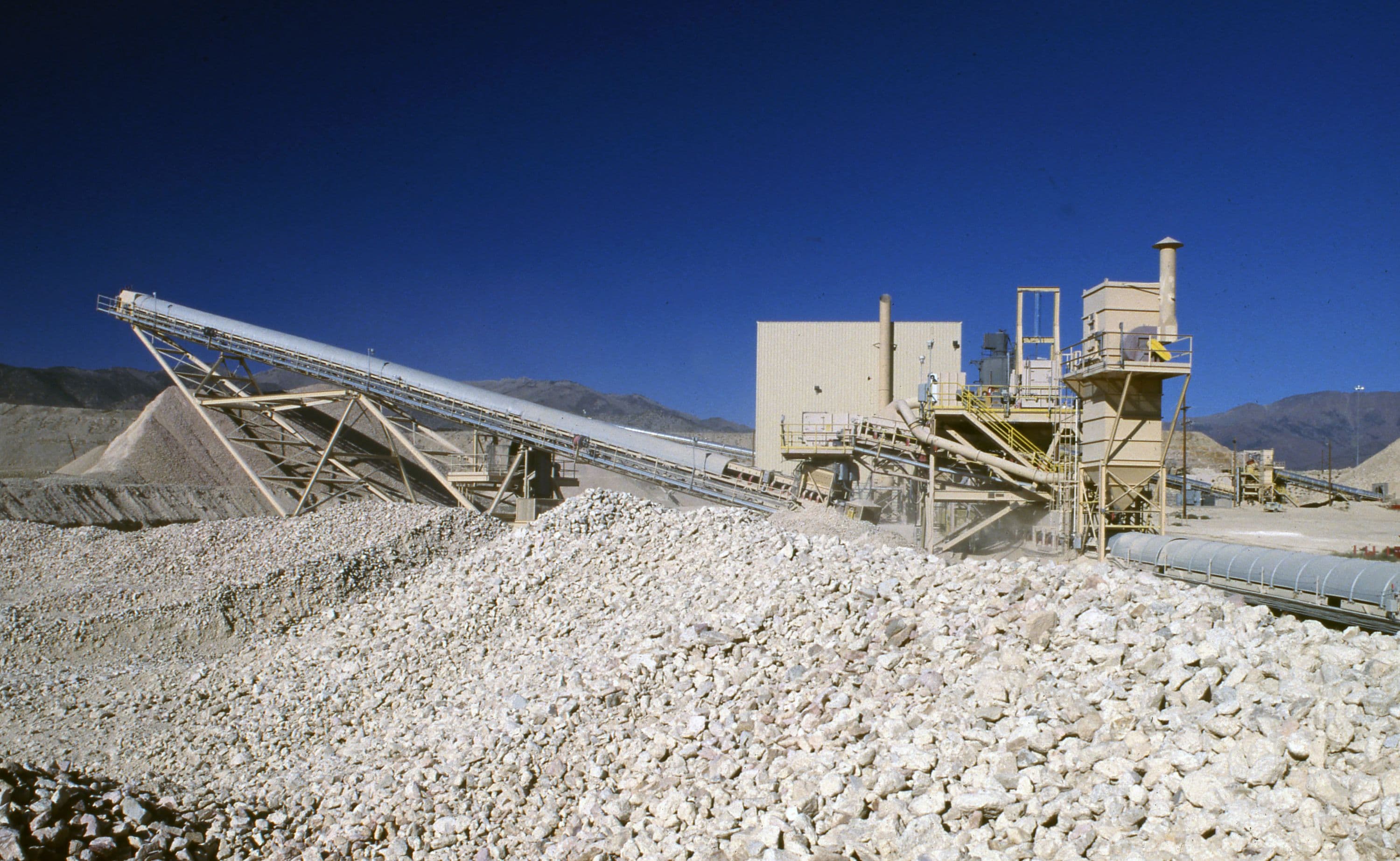
Fluor's Solution
Fluor's responsibilities included:
Detailed design of the system from primary crusher to deposition of material on the reusable leach pads
For the new 8,000 tpd gold concentrator, the spiral middlings stream was treated through a cyanide leach/CIP circuit
Technical consulting services for the moveable 60/89 gyratory crushing plant contract
Assistance during evaluation of contract packages
Equipment procurement
Commissioning assistance
The primary crushed ore was stockpiled on a kidney-shaped stockpile by a radial, luffing stacker. Reclaim was by four apron feeders to conveyors, which transported the material to the crushing and screening plant.
This plant consisted of two secondary crushers, four tertiary crushers and four double deck screens. A series of overland belt conveyors transported the 3/8 inch leach pad feed to two reusable leach pads which were 4,000 feet long by 350 feet wide by 40 feet high. The material was deposited by a series of trippers and stackers and a crawler-mounted bridge conveyor.
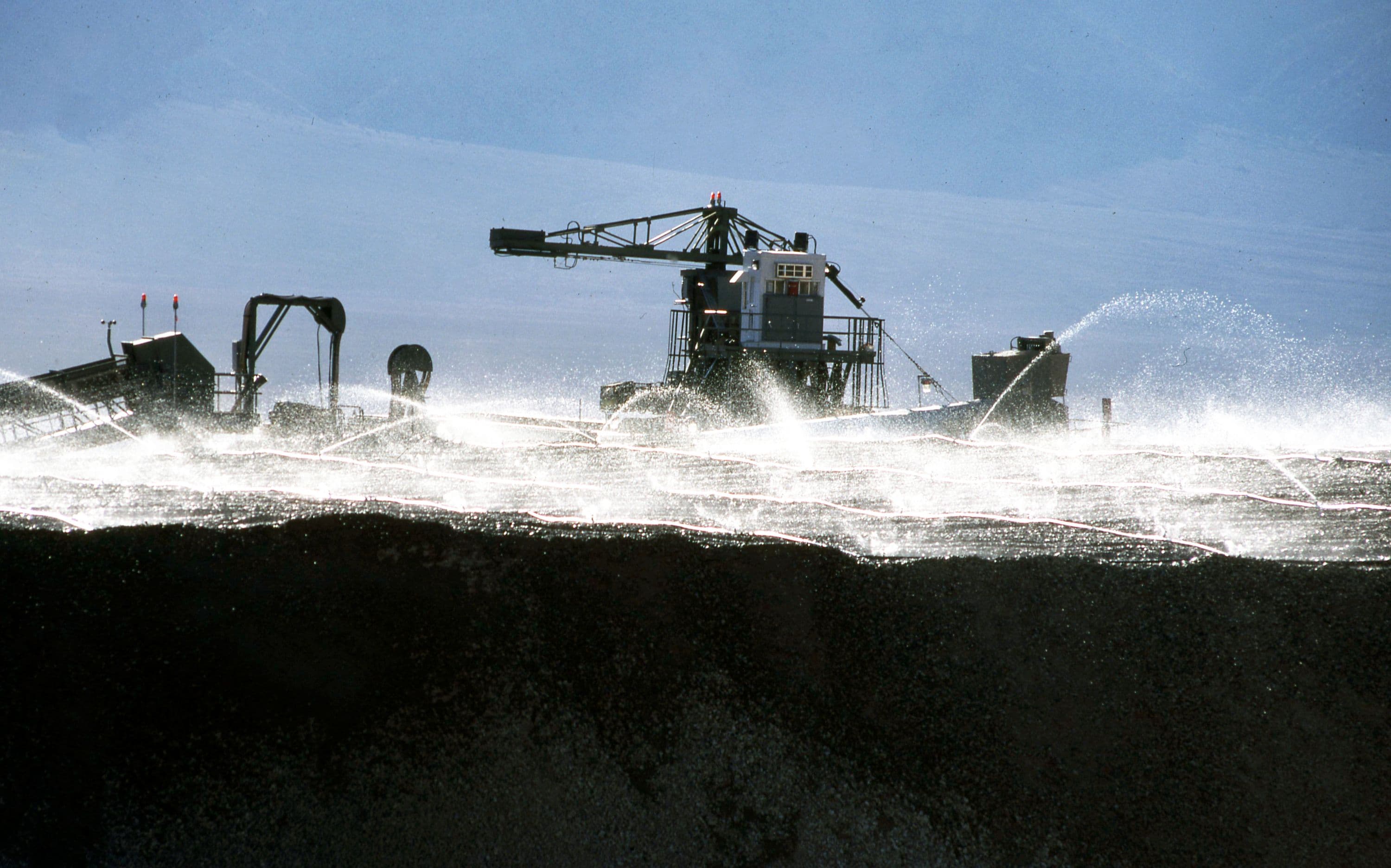
Conclusion
A sophisticated series of programmable logic control systems monitored and controlled the entire operation. The project was completed on schedule and under budget.
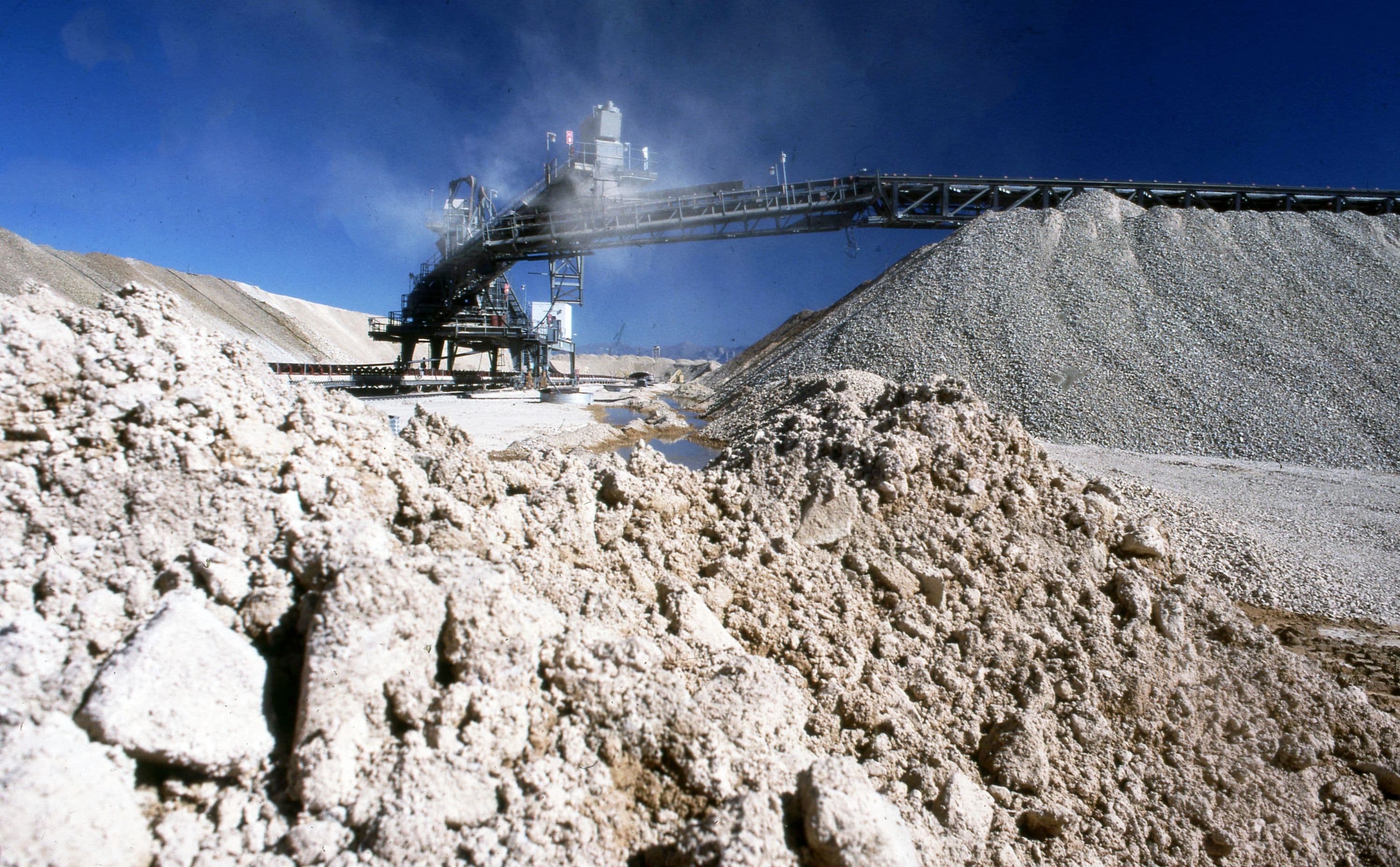