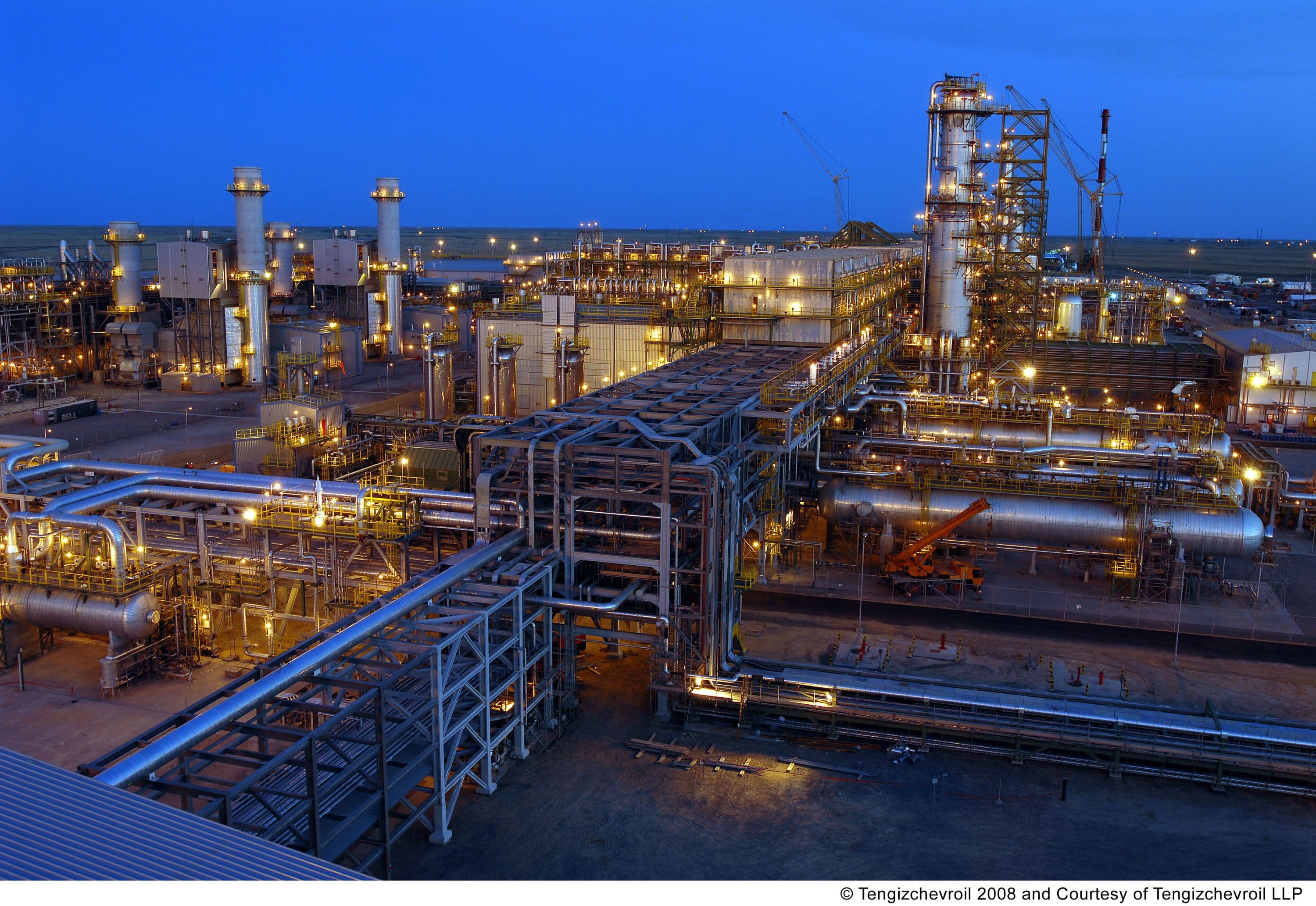
Tengizchevroil SGI/SGP Onshore Oil and Gas Projects - Project Management & Engineering

Executive Summary
Fluor and its joint venture partner provided engineering, procurement and construction management services to Tengizchevroil (TCO) for the Asset Development Project, one of the largest and most complex projects undertaken in the oil & gas industry.
The Asset Development Project was a combination of the Sour Gas Injection (SGI) and the Second Generation Plant (SGP) Projects at the giant Tengiz and Korolev Fields, located on the northeastern shore of the Caspian Sea.
The Fluor JV also provided engineering, procurement and construction management services for a power plant at the TCO project site.
The Fluor JV was subsequently awarded another contract by TCO for its Wellhead Pressure Management Project in Kazakhstan.
The Fluor-led JV had been providing services to TCO for 10 years, and the new project would create many opportunities for further development of the Kazakhstani oil and gas infrastructure, workforce and local companies. The JV trained the local workforce, enhancing skills with a high priority on safety, to create a long-term sustainable workforce in the region.
Client's Challenge
TCO (a joint venture comprising Chevron, ExxonMobil, KazMunaiGaz and LUKArco) undertook the $6.9 billion world-class expansion of its oil and gas production facilities in western Kazakhstan.
The SGI/SGP Projects increased the production potential from 13 million tonnes to over 25 million tonnes per annum. The projects counted a number of firsts, including:
the largest single-train oil/gas separation facility
the world's largest single-train sulfur recovery unit
a first-of-its-kind high-pressure/high H2S gas re-injection facility
The projects also required an extensive infrastructure upgrade with 435 miles of railway.
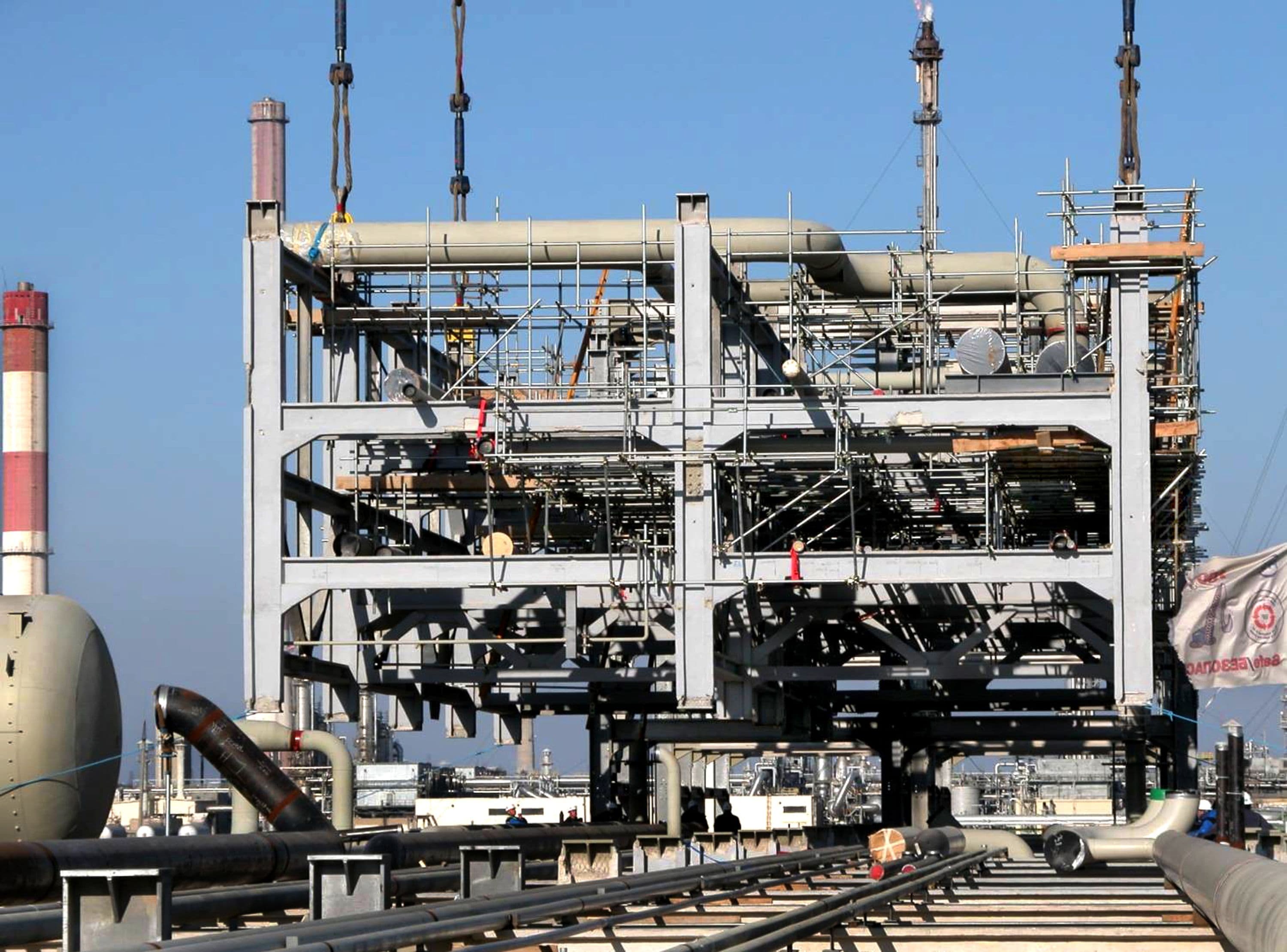
Fluor's Solution
The project team headquartered in Fluor's UK office provided engineering, procurement and construction management services to TCO for both the SGI and SGP Projects. The scale of the undertaking called for engineering to be performed 24 hours a day at project offices located in different time zones around the world. Construction also presented challenges, with a multinational workforce from 61 countries performing construction under hostile climatic conditions. The site's extreme weather conditions included temperatures ranging from 40° Celsius in summer to below -40° Celsius in winter.
SGI – The SGI project was divided into two stages:
Stage 1 was performed to inject sweet gas from the processing facilities into the reservoir to prove the operation of the compressor and validate the predicted response of the reservoir.
Stage 2 expanded the installation, permitting injection of high pressure sour gas (17% H2S) from SGP and providing the opportunity to process an additional 3 million tonnes of oil within the oil/gas separation area of SGP.
Key to the success of the project was pioneering a compressor and associated piping systems capable of delivering sour gas into the reservoir at 10,000 PSI in a way that is both safe and dependable.
SGP – The SGP project included a one-year front-end engineering and design (FEED) followed by detailed design and construction with the SGP greenfield facilities, including new production wells and associated gathering system together with crude stabilization, crude desalting, sour gas dehydration, gas processing, sulfur recovery, crude oil export systems, LPG processing, storage and loading, as well as offsites and utilities.
The Fluor JV also provided engineering, procurement and construction management services for a power plant at the TCO project site. The scope of facilities included two Frame 9E GE gas turbine generators, each with a nominal rating of 123 MWe, including all associated electrical, control and instrumentation equipment, and two supplementary-fired heat recovery steam generators (HRSGs). Each HRSG is capable of generating a maximum of 450 tons per hour of steam at 370° C and a pressure of 72 bar, using gas turbine exhaust gas and full supplementary firing.
In addition to the major power plant equipment, the Fluor JV was responsible for all associated piping and support racking necessary, electrical and control equipment and BOP equipment within the Power Island battery limits.
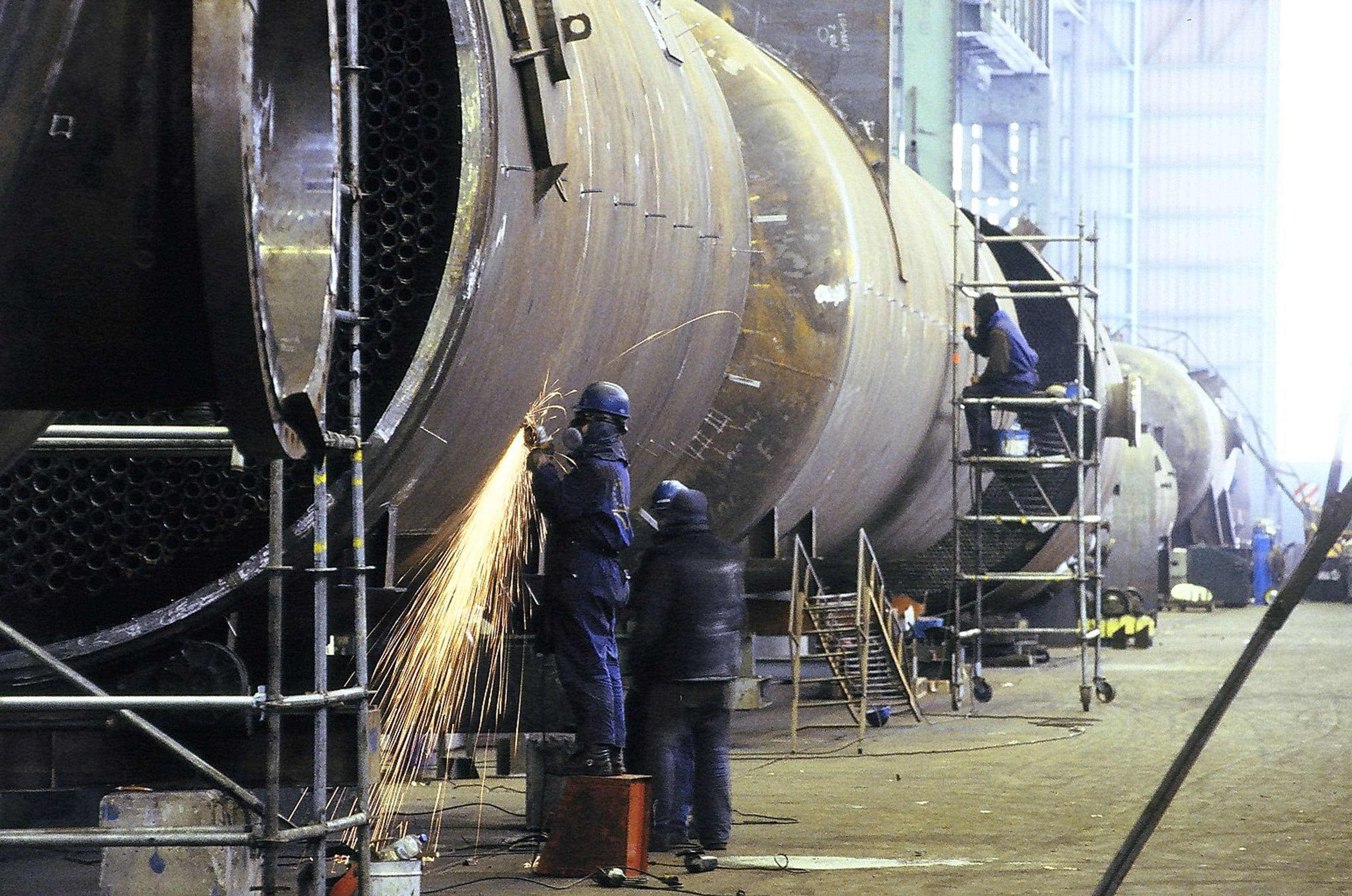
Conclusion
The project team successfully delivered the world-scale $6.9 billion expansion of the oil and gas facilities for TCO in 2008.
Among the project's major accomplishments was outstanding safety performance. Following implementation of an Incident and Injury Free (IIF) safety program, the project accumulated more than 163 million work hours and at its peak had an active work force of 25,000 personnel.
Throughout the project, the team was committed to sending every worker home to their families unhurt and achieved this by the dedicated application of a strong people-centered safety culture.
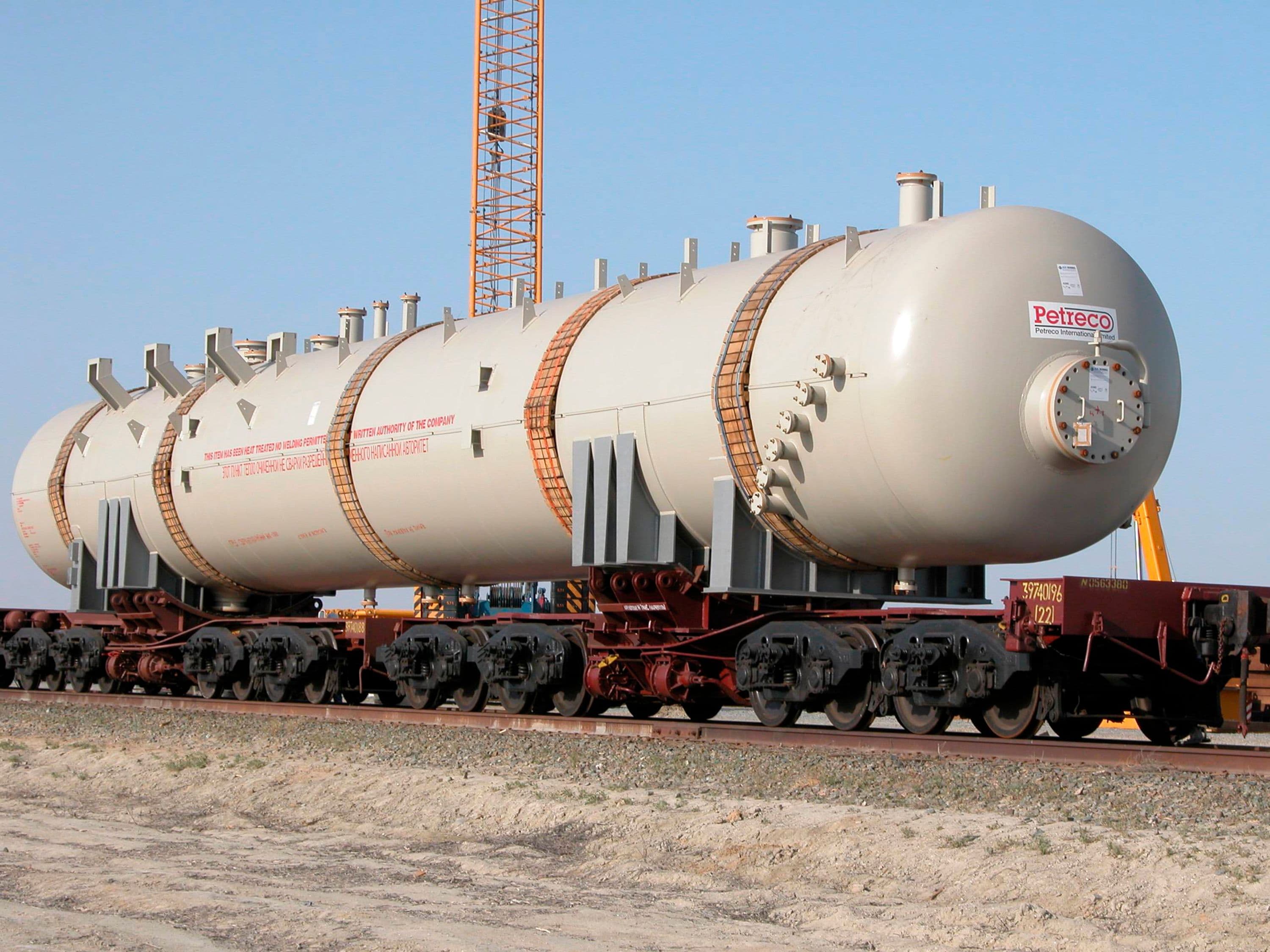
Project Gallery
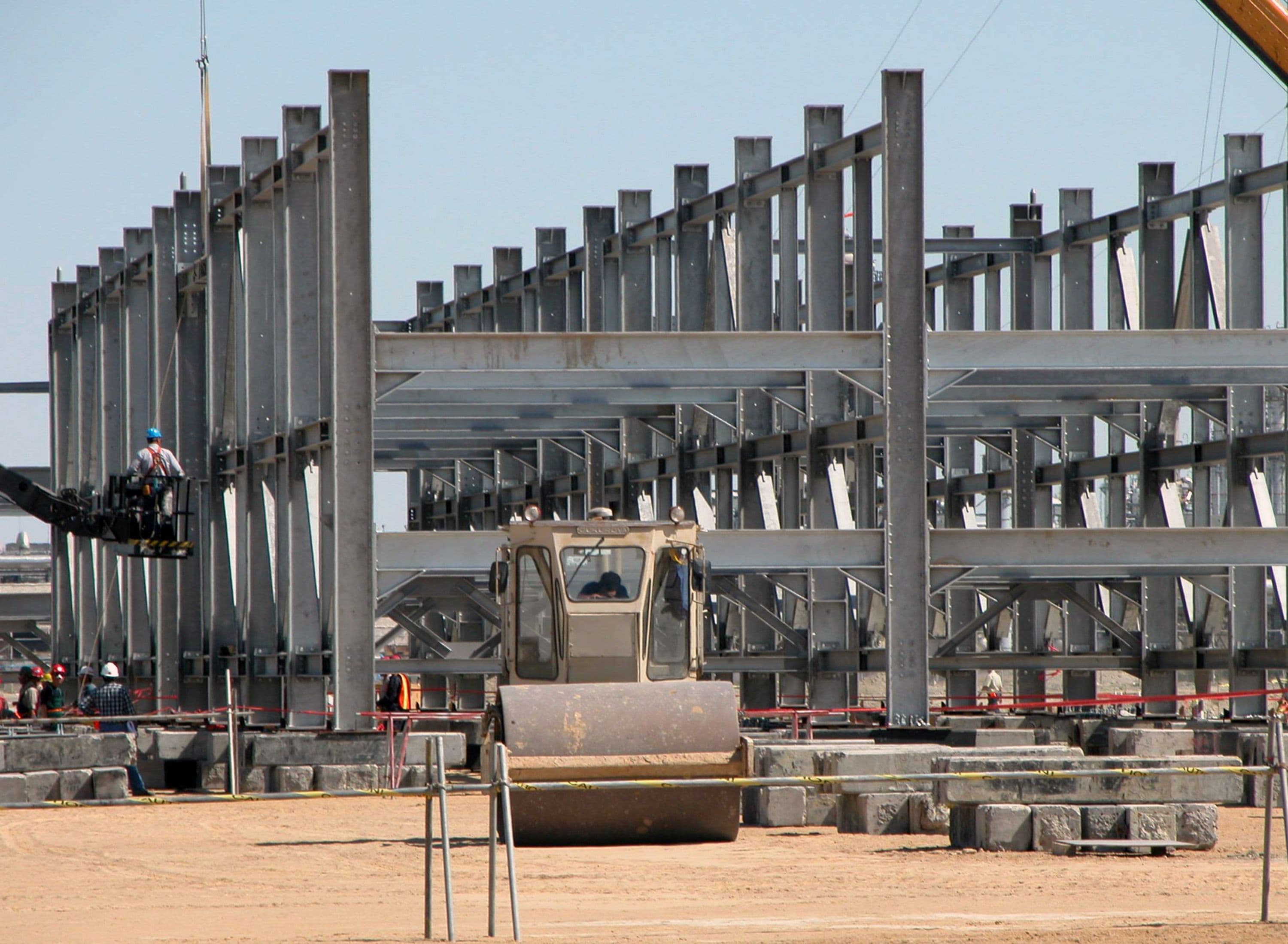
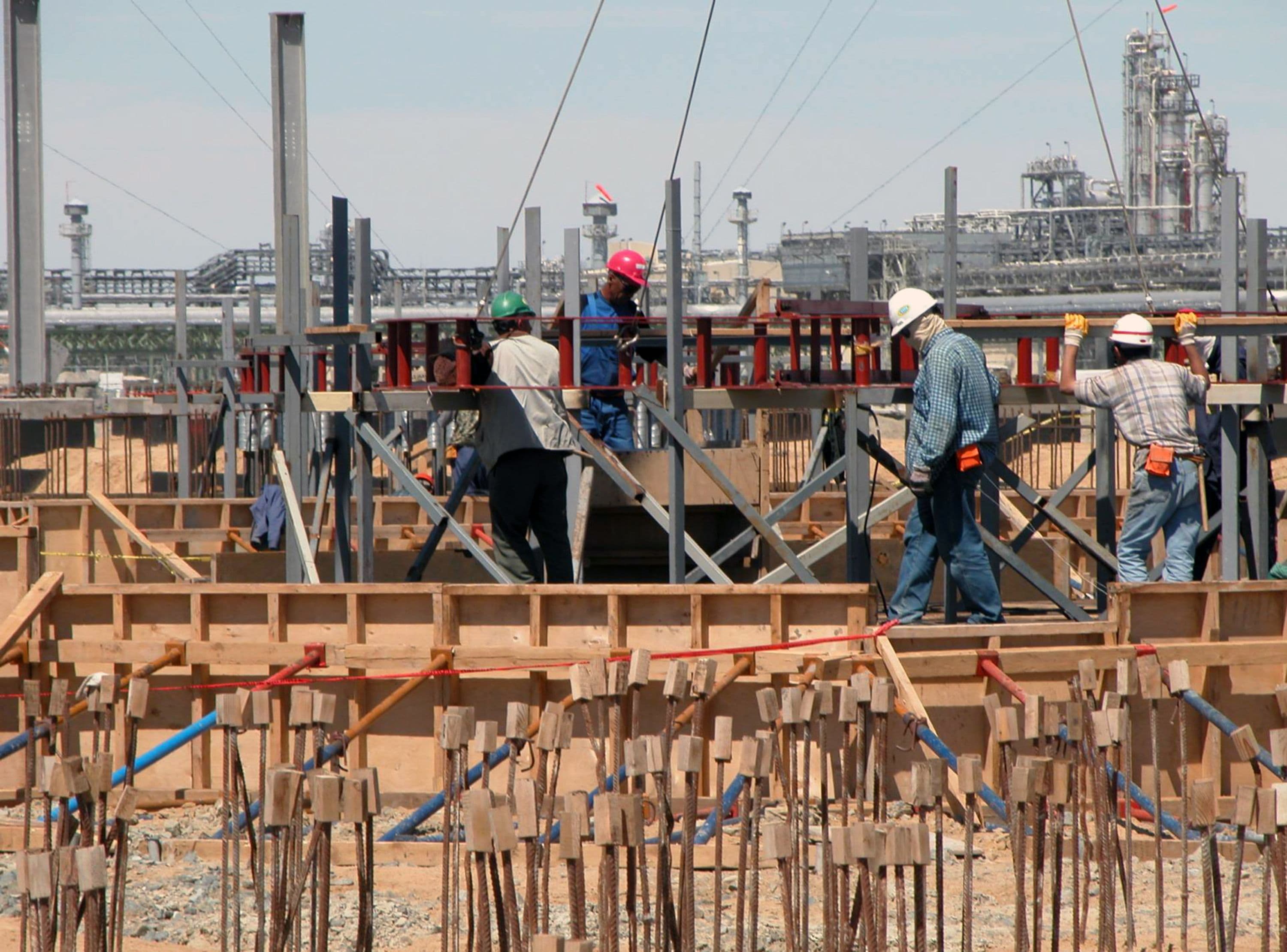
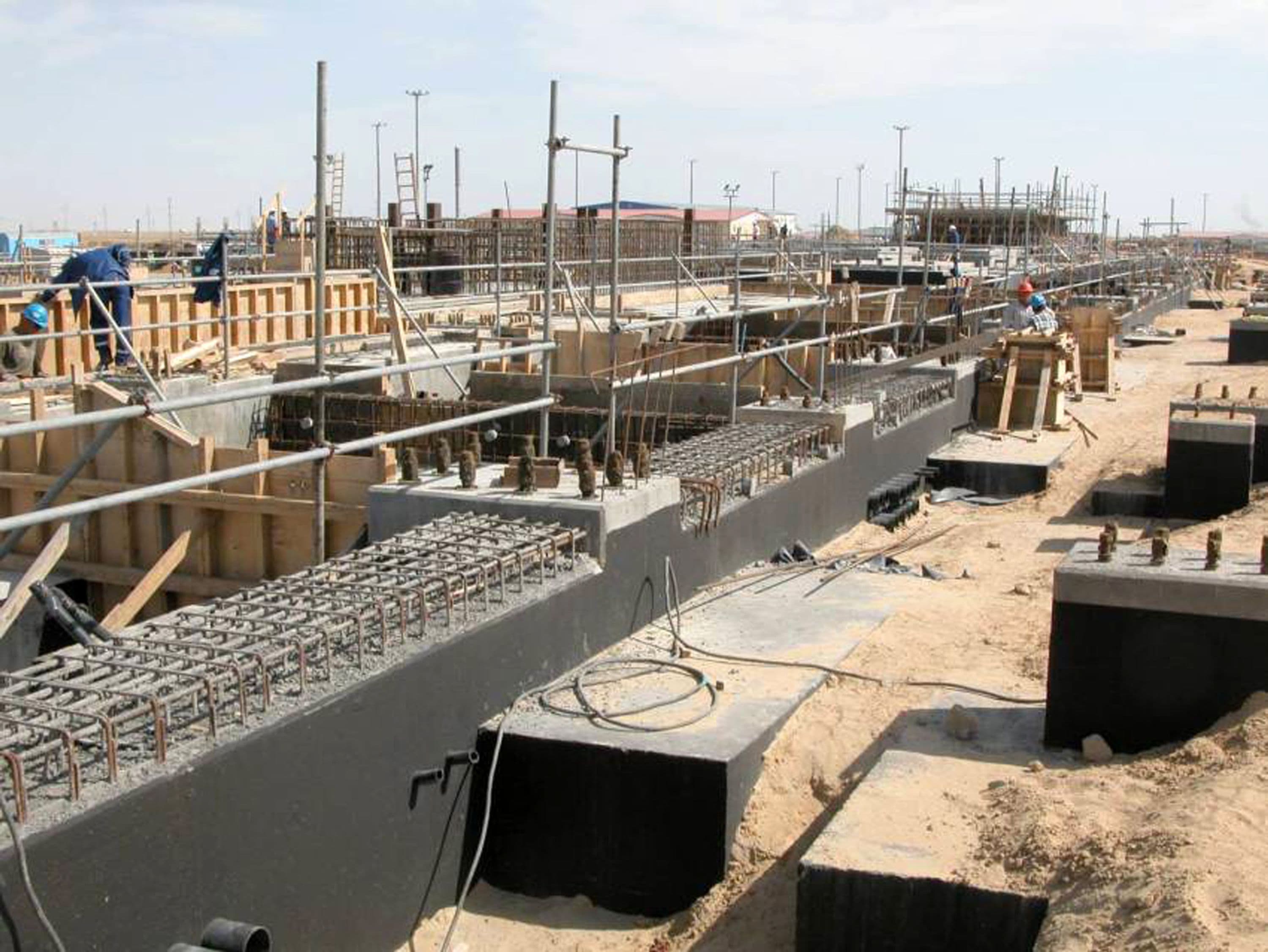
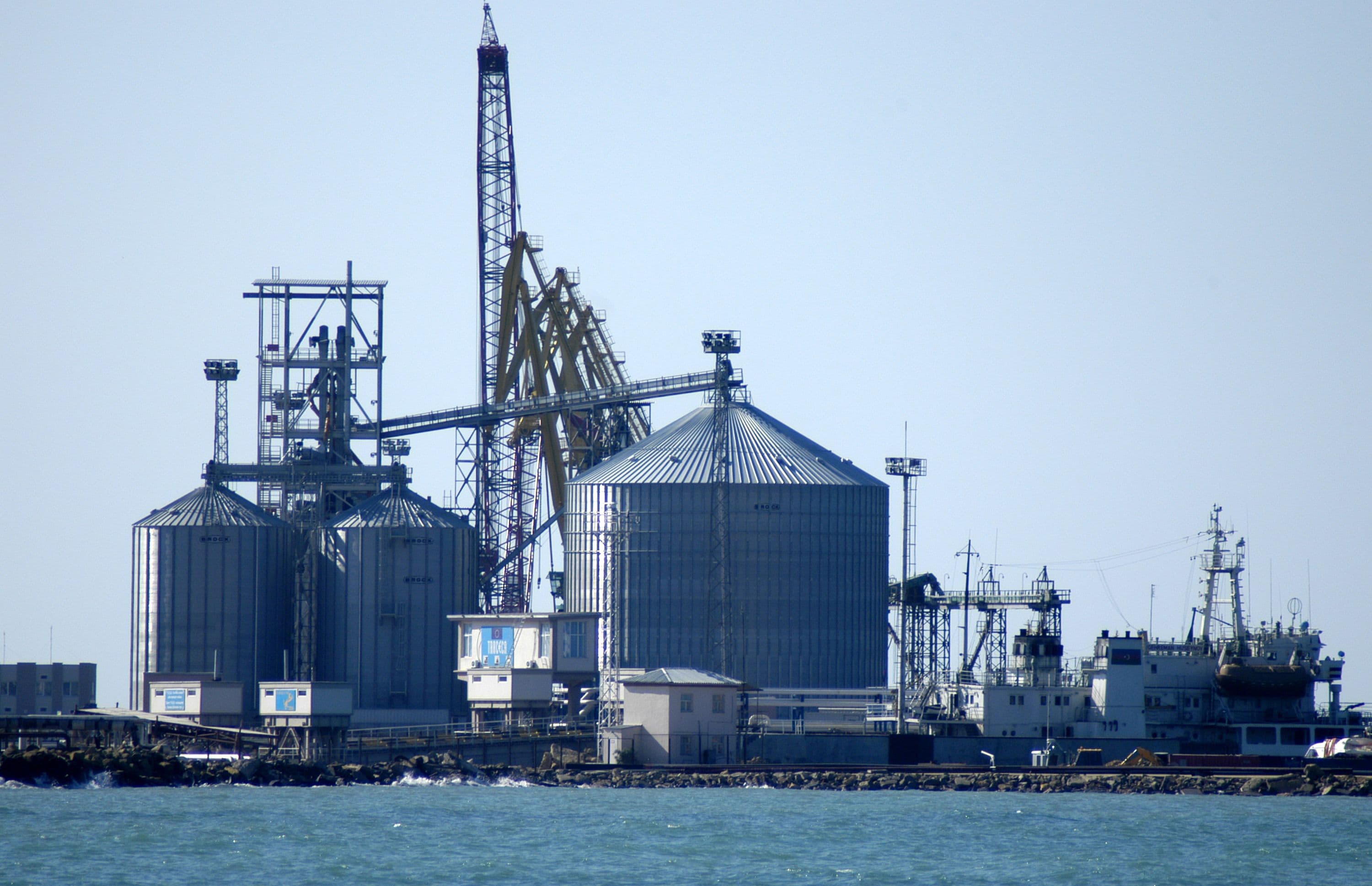
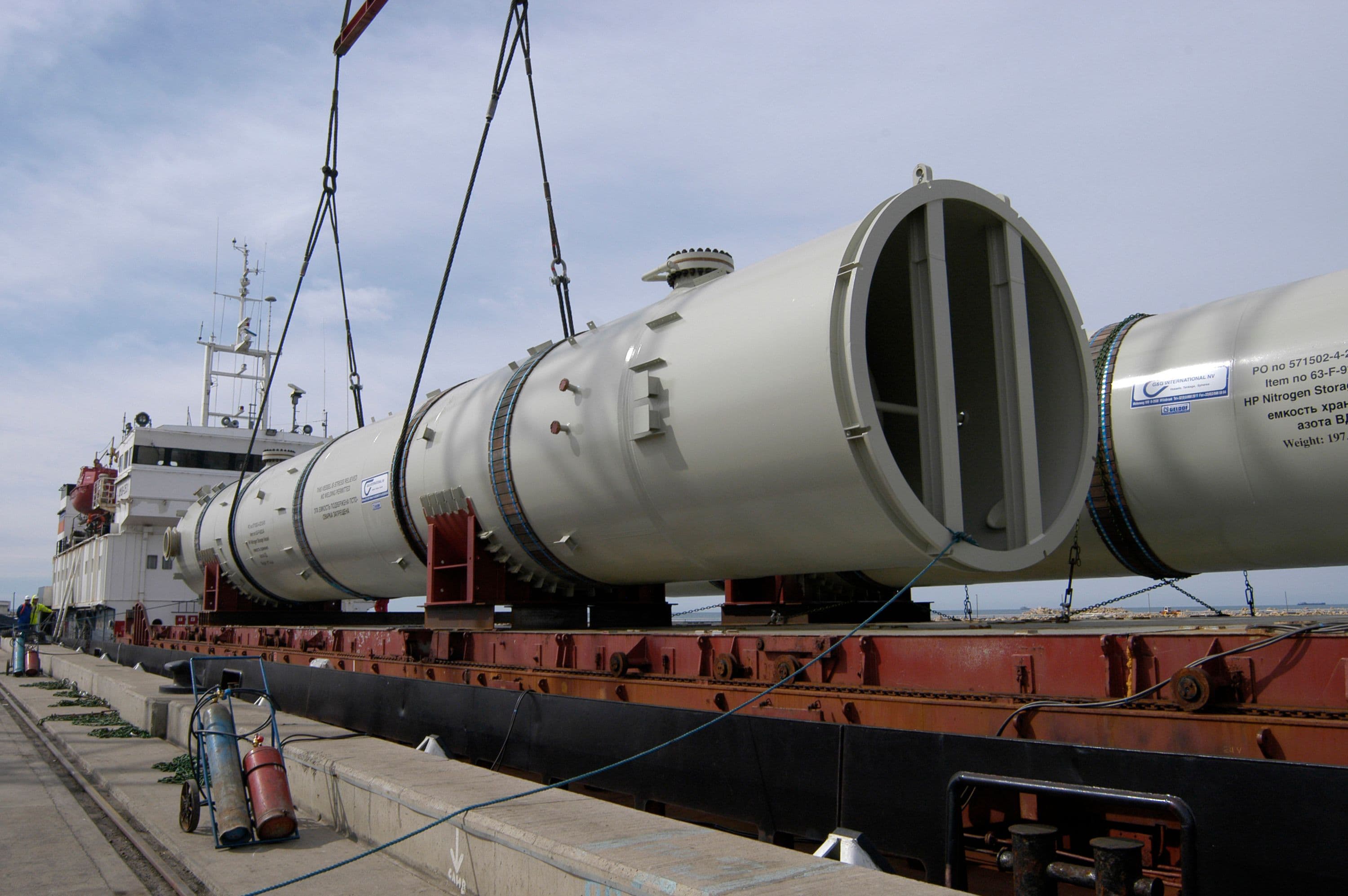
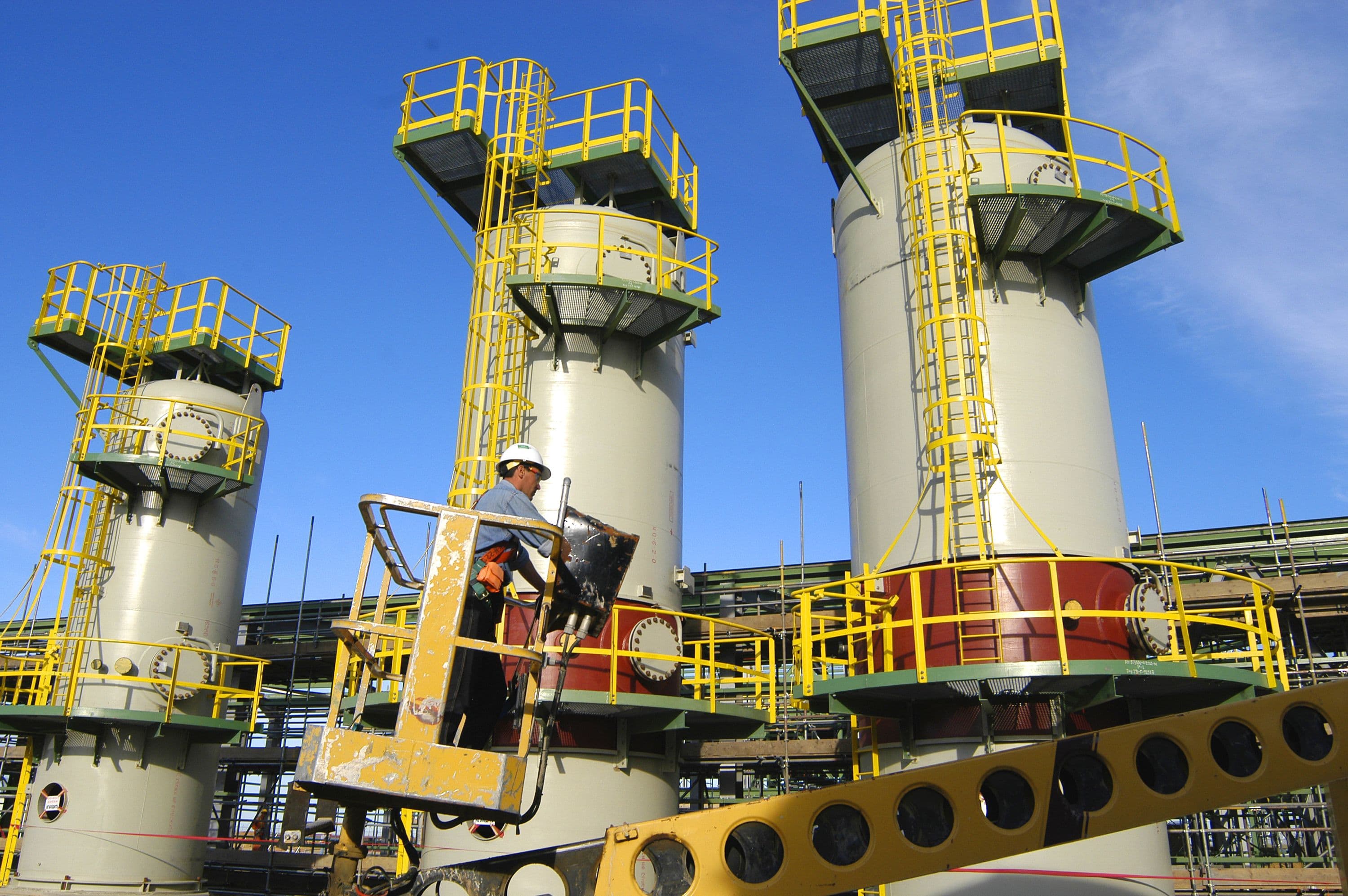
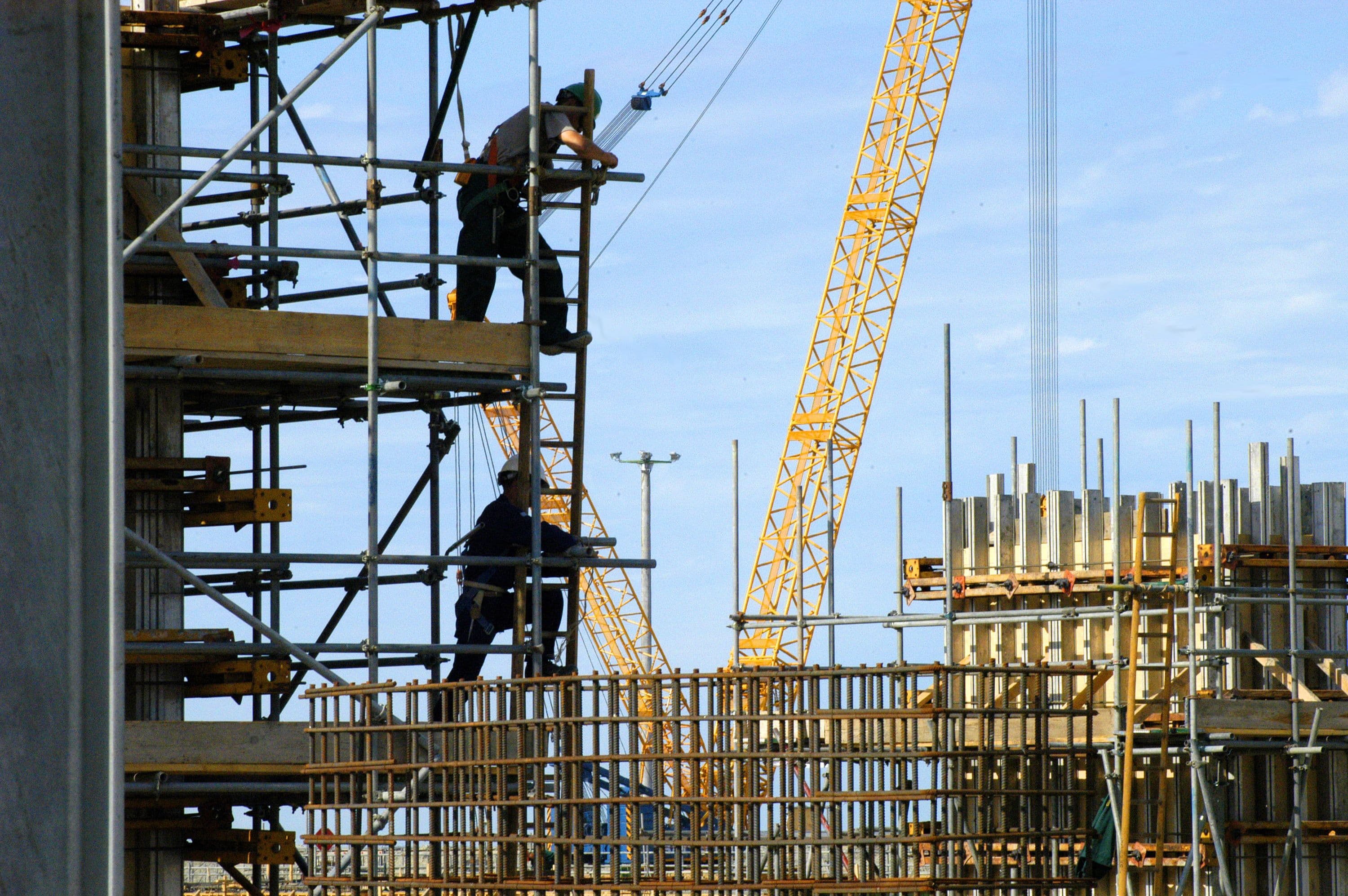
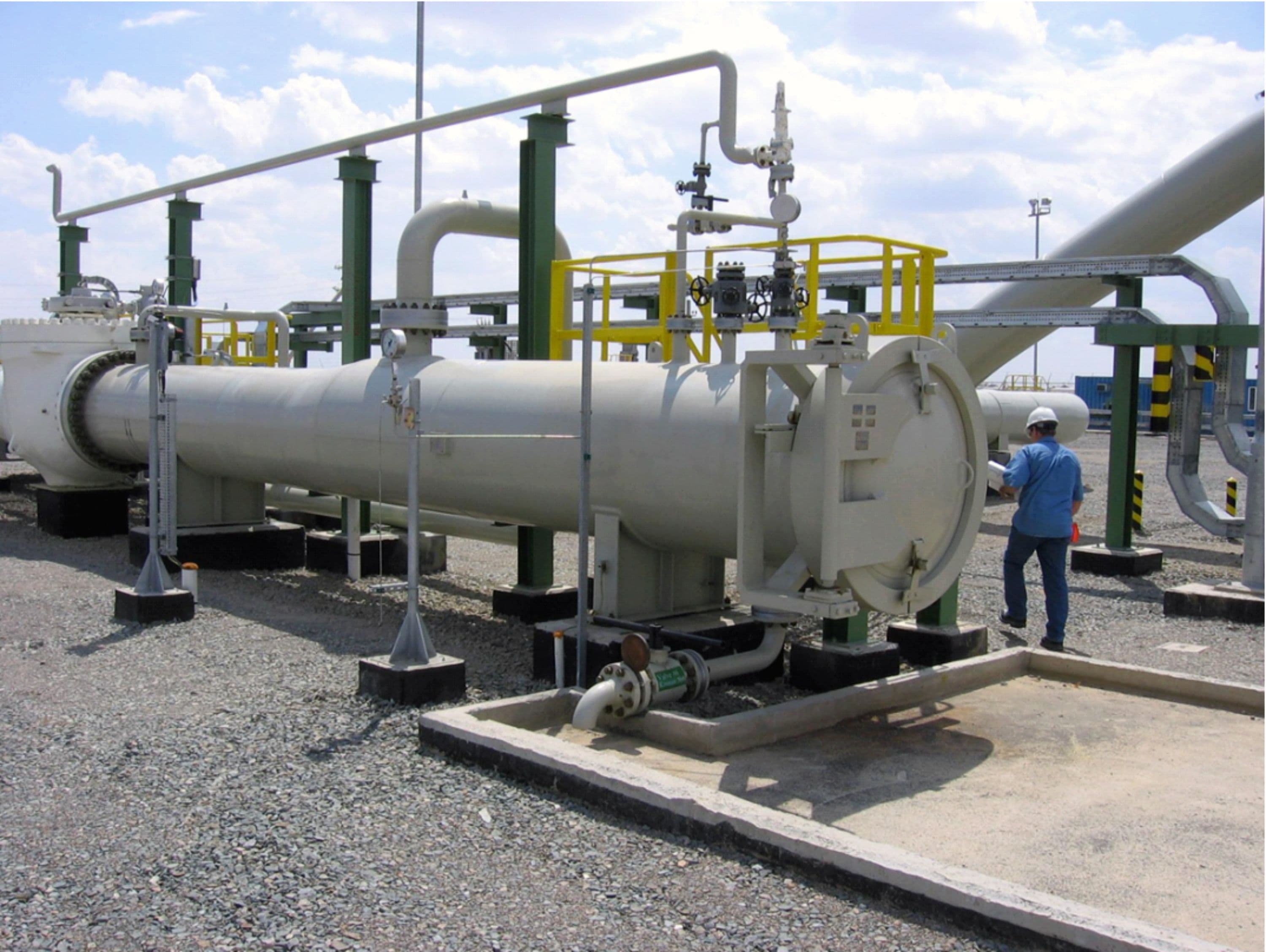
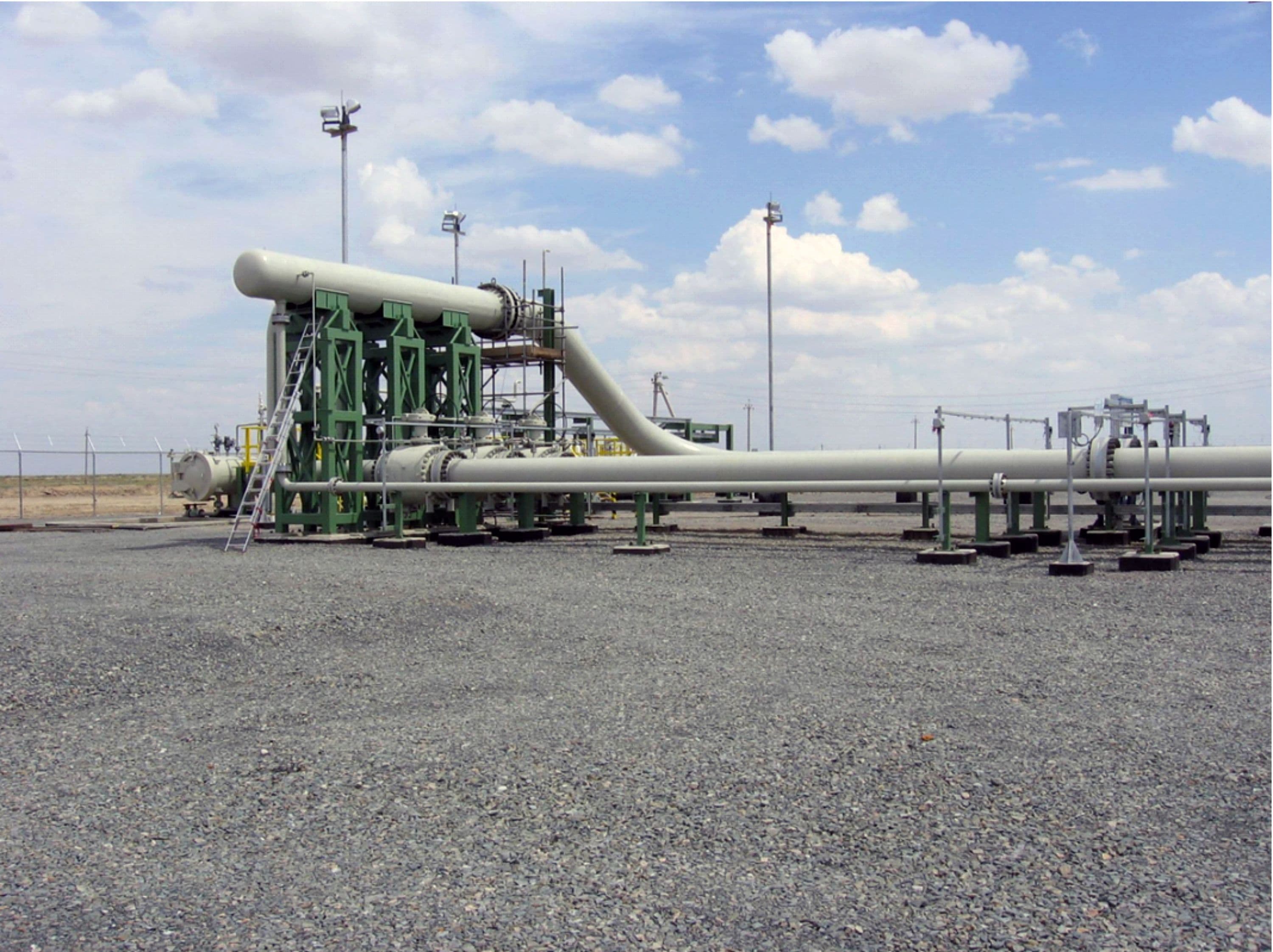
&w=3840&q=75)