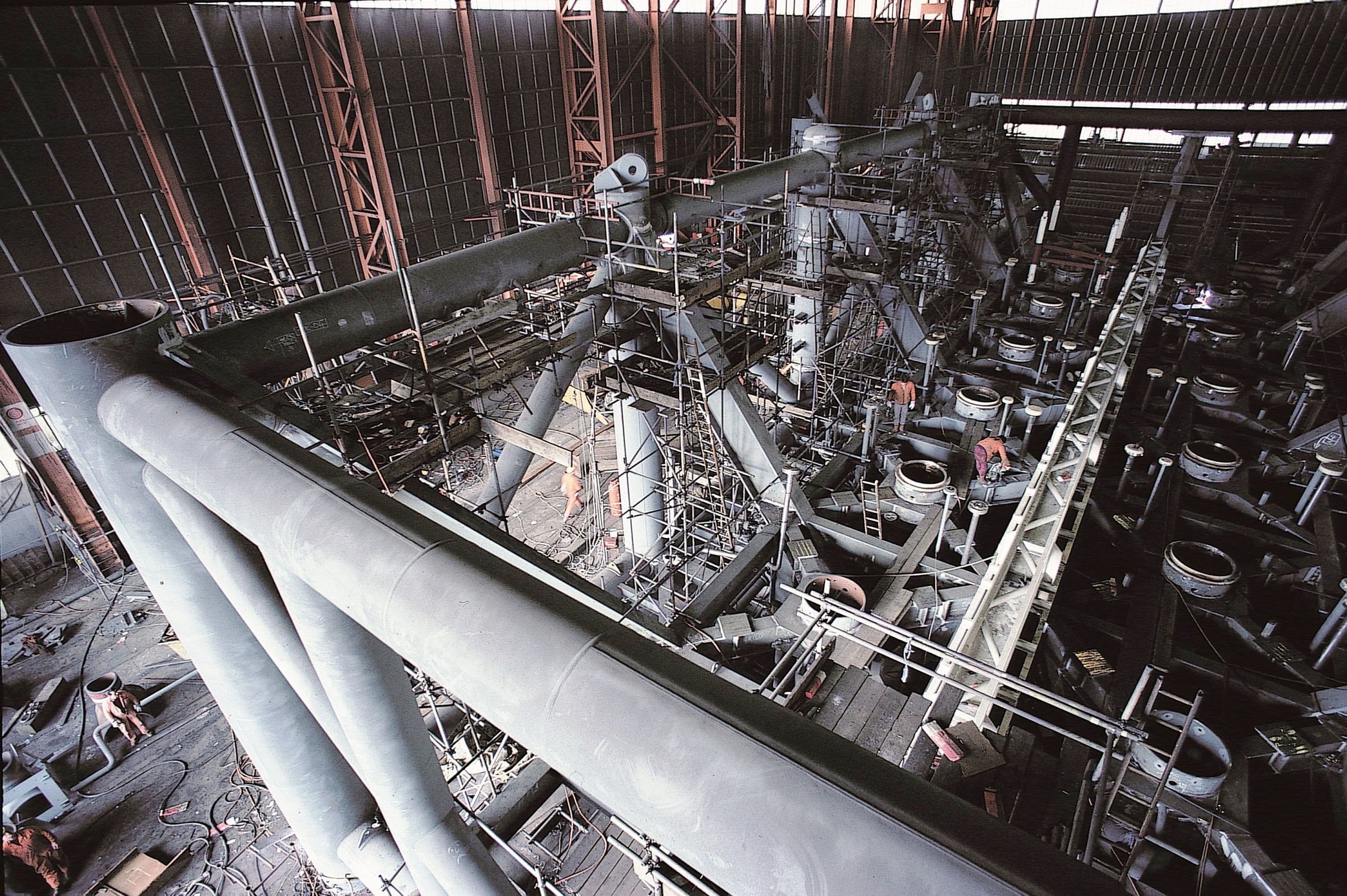
Highlander Field Development
Client: Texaco
Location: North Sea, United Kingdom
Business Segment: Energy Solutions
Industry: Fuels

Executive Summary
Texaco's Highlander Field development was a breakthrough in subsea technology that included universal trees and modular flowline connection concepts, a subsea slug catcher, retrievable pig launchers and receivers and diver-friendly designs for the 420-foot water depth.
Subsea development of the marginal (15 million BBL) oil field included a 1,200-ton, 12-slot subsea template with remote wells, five pipelines, umbilicals, subsea slug catcher, riser systems and topside modifications. Highlander's remote controlled subsea production system combines all of the functions of well test, gas lift, water injection, and chemical treatment.
Fluor performed conceptual and detailed engineering, procurement and construction planning for the development of the Highlander Field oil and gas subsea production facilities.
This development, which consisted of a remote subsea system linked back to Texaco's existing Tartan "A" platform, was the first in the UK to use both water injection and gas lift.
The project required the development of conceptual and detailed designs for first-of-a-kind systems in areas of subsea level control, subsea slug catchers, retrievable pig launchers/receivers and pump risers.
We also used extensive modeling of pipeline hydraulics in development of the optimum interconnection design. A 12-slot template was installed and recoverable estimates are put at more than 30 million barrels with output projections of 30,000 b/d.
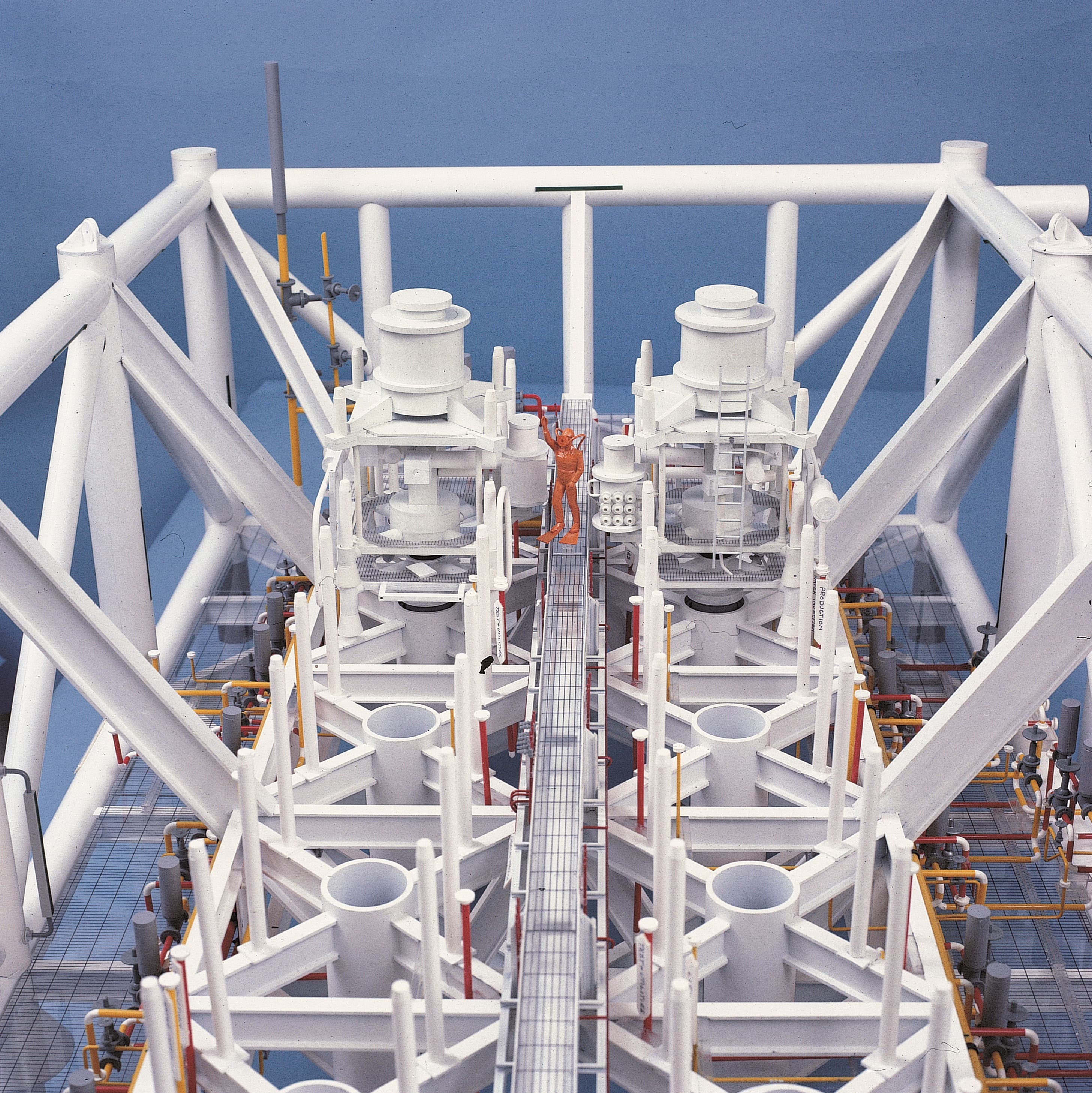
Client's Challenge
Faced with the challenge of a small reservoir located in 420 feet of water eight miles distant from the existing Tartan "A" Platform in the UK sector of the North Sea, Texaco selected a subsea development plan to achieve both early production and full field development, paving the way to exploit 90-odd marginal fields known to exist in the North Sea.
With an innovative subsea design using gas lift and water injection manifolding in one template, electrical submersible pumps in the riser and flexible flow lines, this ended up being the world's first subsea tie-back with a subsea separator and slug catcher, which is still working today and which has been the model for current subsea separation in deep water until now.
Detailed weight control involving removals as well as new design kept overall weight/space additions to a minimum. Careful planning of tie-ins and temporary re-allocations of production facilities allowed Tartan 'A' production to remain largely uninterrupted throughout the process. Close control of construction operations allowed the limited spare bed space on the platform to be used for construction personnel avoiding the expense of bringing Flotel equipment alongside.
The end result was not only one platform capable of handling two fiscally separate oil fields, but a thoroughly modernized computer controlled process facility as well.
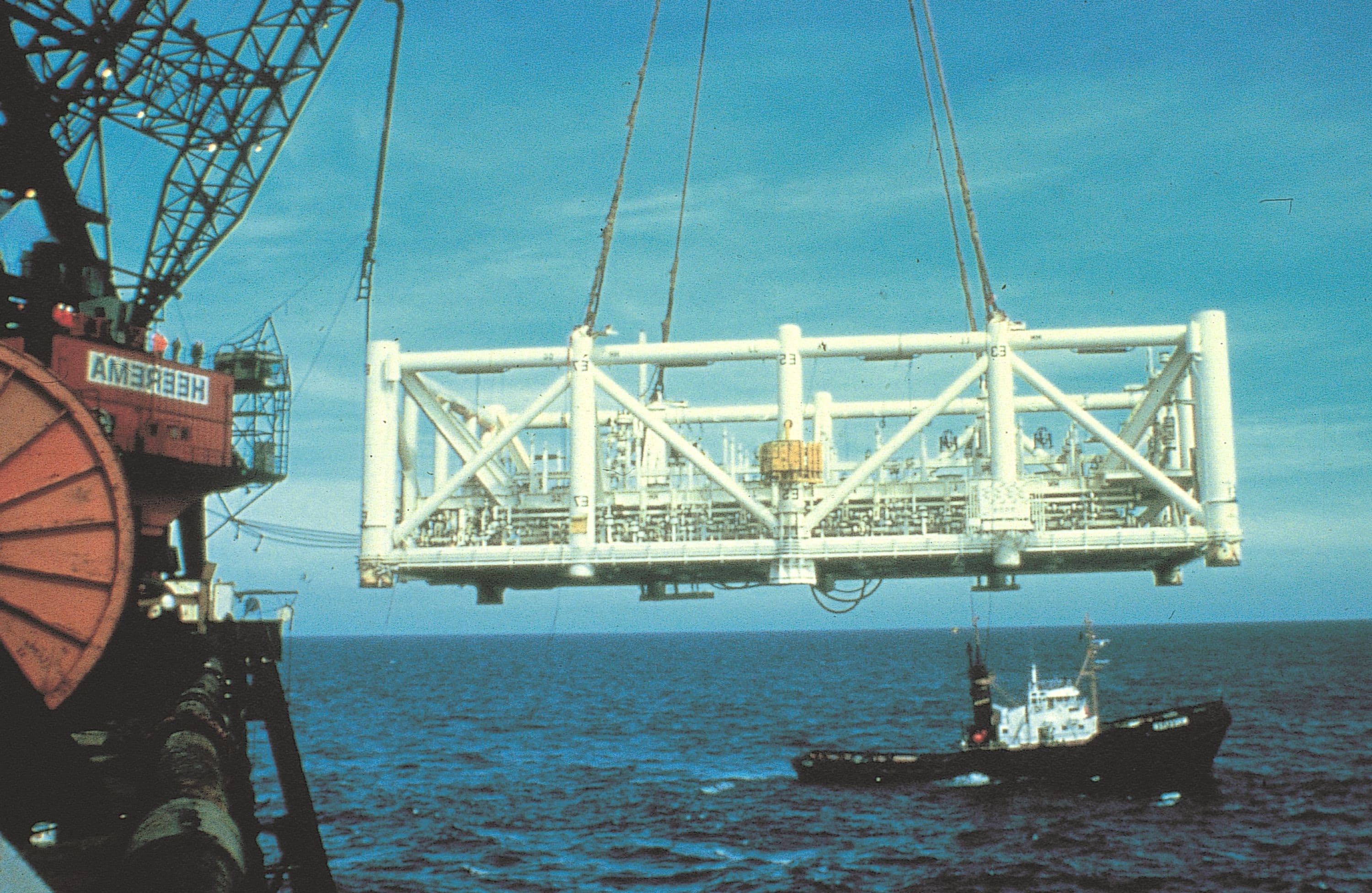
Fluor's Solution
Texaco's Highlander project in the UK sector of the North Sea helped pioneer the commercial viability of developing smaller oil fields. Fluor confirmed the concept and performed the engineering and detailed design. We also provided procurement and construction assistance.
Several new innovations were developed providing for significant subsea technologies:
Universal trees and flowline connection module concept
Incorporation of both gas lift and water injection manifolding in one template
Production and control eight miles from topsides facilities
Subsea retrievable pig launchers and receivers
Subsea slug catchers
Unique riser designs
Use of downhole pumps for bulk crude lift
Diver-friendly designs at 420 feet water depth
We structured activities to maximize local content and to establish early field production within 15 months of starting work. Full facilities were completed on schedule and within budget six months later.
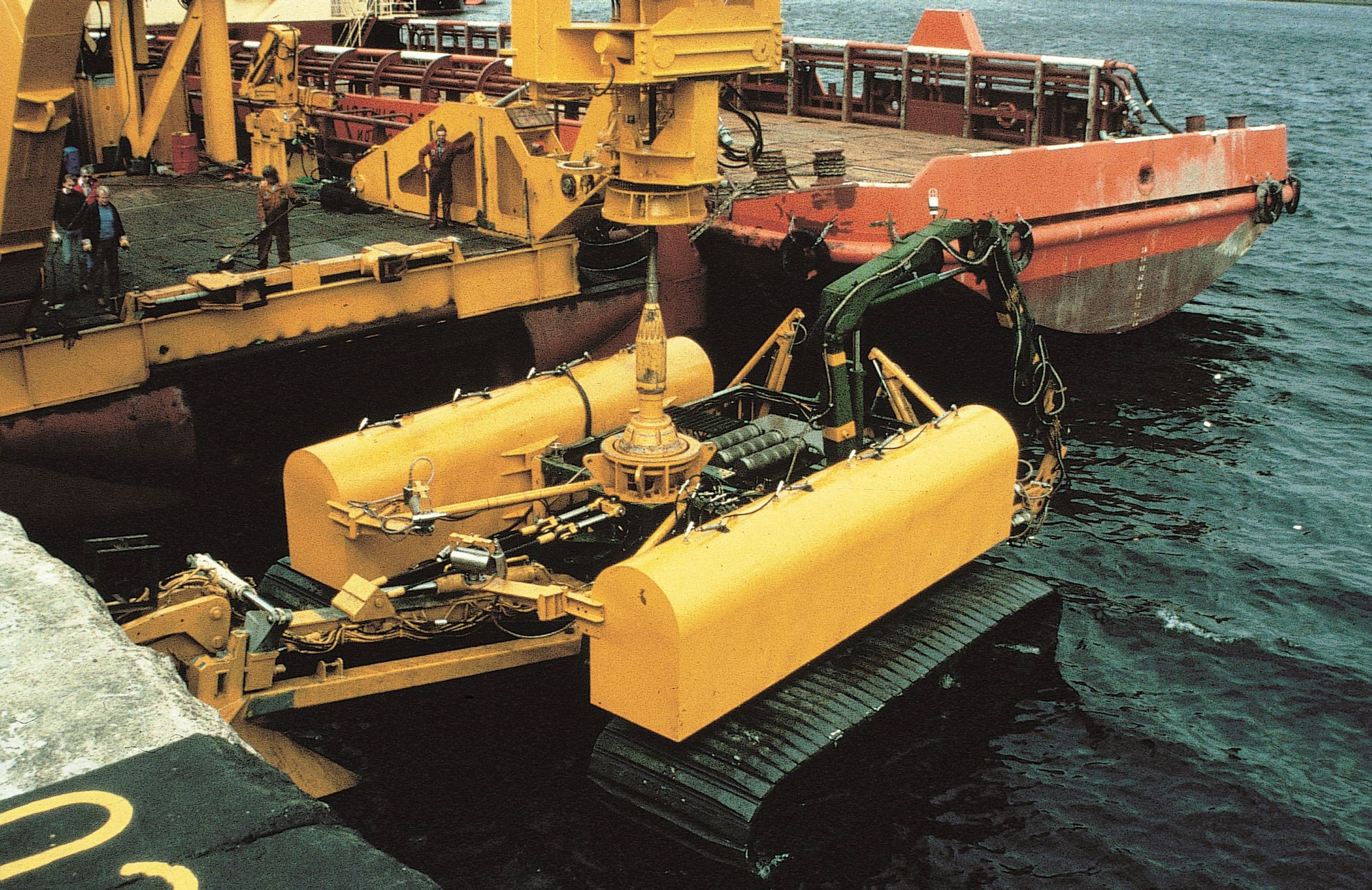
Conclusion
The Texaco Highlander Field Development project set a new standard for subsea production. Notable achievements include:
Early production was achieved, slightly exceeding the final design capacity of the system, within 15 months of detailed engineering kickoff.
Trouble-free operation of the early production scheme equipment, which included most of the key system components incorporated in the full production scheme.
Full production facilities on schedule for installation and commissioning in less than two years from start of detailed design and procurement.
Development costs kept within original budget restraints, demonstrating the economic viability of developing so-called marginal fields in the UK North Sea, utilizing subsea production techniques.
Innovation of significant new subsea technology.
Universal trees and flowline connection module concept.
Incorporation of both gas lift and water injection manifolding in one template.
Production and control eight miles from topsides facilities.
Subsea retrievable pig launchers and receivers.
Subsea slug catchers.
Unique riser designs.
Use of downhole pumps for bulk crude lift.
Diver-friendly designs at 420 feet water depth.
Nearly 30 years after installation, the facility was owned by Talisman and still working.
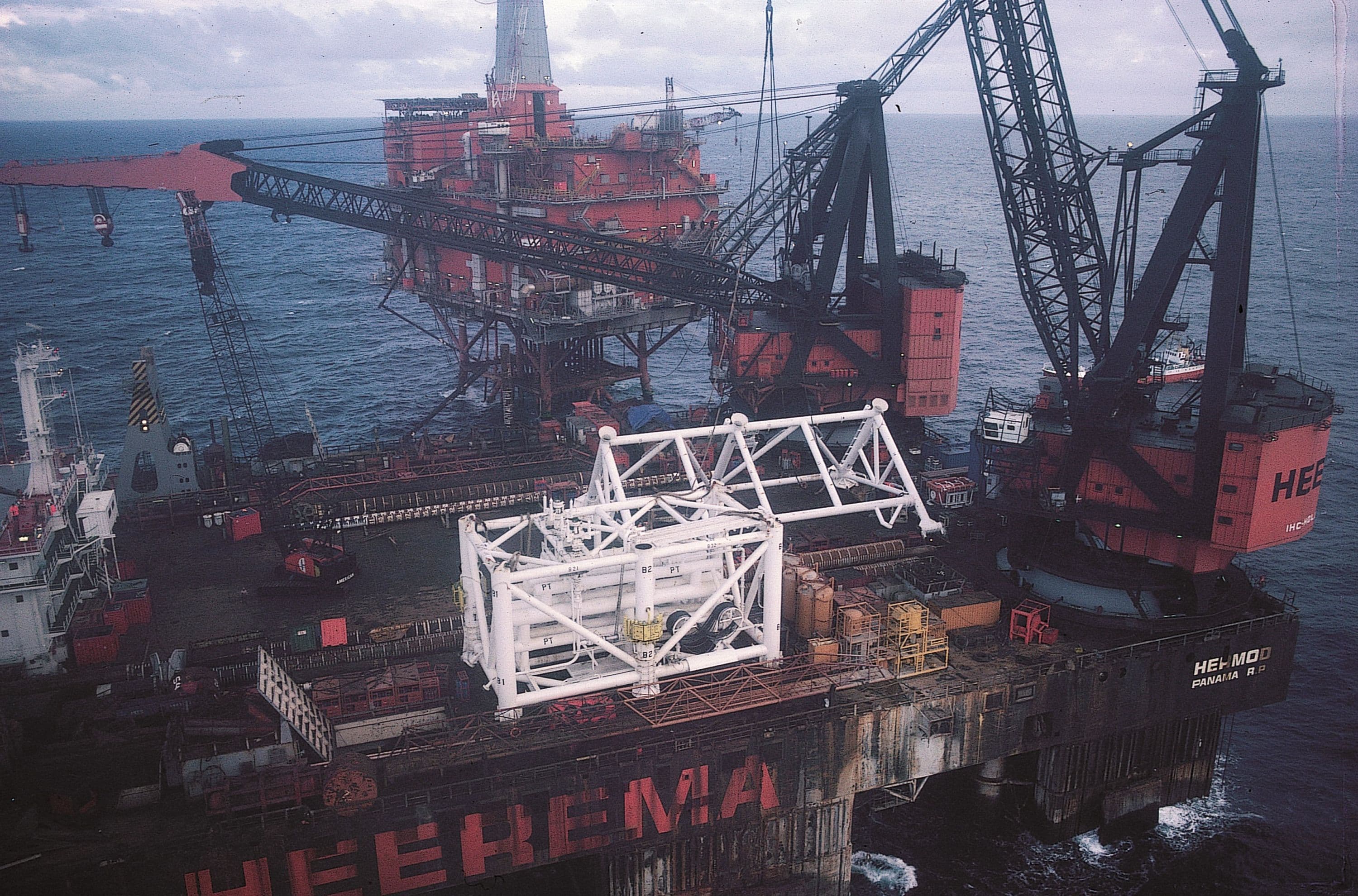